
2419
.pdfПродолжение таблицы 2
1 |
2 |
3 |
4 |
5 |
6 |
7 |
8 |
Содержание |
|
|
75±2 |
73±2 |
66±2 |
66±2 |
|
сухих |
58 |
65 |
68-70 |
||||
веществ, % |
|
|
|
|
|
|
|
Содержание |
|
|
|
|
|
|
|
свободного |
|
|
|
|
|
|
|
формальдегид |
0,15 |
0,1 |
0,1 |
0,15 |
0,15 |
0,15 |
0,15 |
а, %, не более |
|
|
|
|
|
|
|
Время |
|
|
|
|
|
|
|
желатинизаци |
40…60 |
50…65 |
35…90 |
35…50 |
50…60 |
50…70 |
50…70 |
и при 100 0С, с |
|
|
|
|
|
|
|
Смешивание с |
не |
не |
не |
- |
не более |
1:2-1:10 |
1:2 |
водой, мас.ч. |
более |
более |
более |
|
1:1-1,5 |
|
|
|
1:4 |
1:2 |
1:2 |
|
|
|
|
Вязкость по |
|
|
|
|
|
|
|
ВЗ-4, с |
130 |
150…30 |
200 |
100…30 |
60…100 |
50…80 |
80…12 |
|
|
0 |
|
0 |
|
|
0 |
Концентрация |
|
|
|
|
|
|
|
водородных |
6,5…8,0 |
7,0…9, |
- |
7,0…7,8 |
7,5…8,5 |
|
|
ионов, (рН) |
|
|
0 |
|
|
|
|
Способ |
Поддон |
Бесподд |
Поддон |
Сетчаты |
Сетчатый |
Поддонн |
Беспод |
производства |
ный |
онный |
ный |
й |
|
ый, |
- |
ДСтП |
|
|
|
|
|
сетчатый |
донны |
|
|
|
|
|
|
|
й |
Класс плит с |
|
|
|
|
|
|
|
комплексным |
Е1 |
Е1 |
- |
- |
Е1 |
- |
- |
отвердителем |
|
|
|
|
|
|
|
Класс плит с |
|
|
|
|
|
|
|
отвердителем |
Е2 |
Е2 |
Е1 |
Е1 |
Е2 |
Е2, Е3 |
Е1 |
20%-ным |
|
|
|
|
|
|
|
NH4Cl |
|
|
|
|
|
|
|
Распыление производят центробежным, механическим или пневматическим способами. Получившийся мелкодисперсный гигроскопичный порошок упаковывают в герметически закрывающуюся тару. В таком виде он может хранится 2…3 года. Под влиянием тепла порошок переходит в комкообразное, а при избытке влаги – в жидкое состояние. Поэтому хранить его необходимо в сухом помещении при нормальной температуре.
Порошкообразные карбамидные смолы должны удовлетворять следующим основным требованиям:
Содержание влаги, % |
не более 5 |
Растворимость в воде при 18-20 0С |
полная |
11 |
|
рН водного раствора |
не ниже 7 |
Жизнеспособность водного |
|
раствора (без отвердителя), суток |
не менее 2 |
Продолжительность желатинизации |
|
клея при температуре 20 0С, ч |
не менее 2 |
Содержание свободного формальдегида, % |
0,7 |
Жидкую смолу приготавливают из порошка в мешалках, куда сначала заливают воду, а затем при непрерывном перемешивании постепенно засыпают порошок смолы. Перемешивание продолжается до получения однообразной жидкой массы без комков и сгустков.
Клеящие свойства порошкообразных смол не отличаются от свойств жидких смол с таким же содержанием сухого остатка. Однако изготовление этих смол сложно, что отражается на их стоимости, поэтому промышленное производство и использование порошкообразных смол в нашей стране не организовано, хотя за рубежом они получили определенное распространение.
Вопросы для контроля
1.Современные карбамидоформальдегидные смолы. Основные марки. Свойства КФС.
2.Порошкообразные КФС. Основные свойства. Область применения.
3.Технология получения порошкообразных КФС.
4.Приготовление клеев на порошкообразных КФС.
ЛАБОРАТОРНАЯ РАБОТА № 3
Определение основных свойств клеев – расплавов
Клей-расплав представляет собой термопластичный клей, в котором нет воды и растворителей, требующих удаления при отверждении. Это клеевые композиции, которые расплавляются при нагревании и становятся клейкими, а при охлаждении они затвердевают. В расплаве они имеют низкую вязкость и хорошую текучесть, стабильны на протяжении
12
длительного времени при относительно высокой температуре, представляют собой многокомпонентные композиции.
Клеи-расплавы используются в различных областях промышленности: мебельной, авиа- и судостроении, обувной, тарной и др.
Клеи-расплавы состоят из основного полимера, модификаторов, пластификатора, наполнителя и антиоксиданта. Основным полимером в них является сополимер этилена с винилацетатом, различающиеся степенью полимеризации и отношением этилена с винилацетатом. При содержании в сополимере винилацетатных групп более 28%; они приобретают хорошую адгезию ко многим материалам, легко совмещаются с различными смолами, полимерами, натуральными и синтетическими каучуками и т. д.
Вкачестве модификаторов используют полимеры, хорошо совмещающиеся с сополимером. Модификаторы имеют различное назначение: одни усиливают адгезионные свойства сополимера к склеиваемым материалам, другие изменяют упругие и релаксационные свойства клеевого соединения.
Вклеях-расплавах, используемых в мебельной промышленности, в качестве модификатора, используют канифоль или ее производные, инденкумароновую смолу, низкомолекулярные полиамиды и др. Эти вещества улучшают адгезионные свойства клея, уменьшают вязкость расплава, что способствуетповышениютекучестиклея.
Пластификаторы способствуют снижению вязкости расплава, уменьшают хрупкость клеевого соединения, повышают смачивающую способность клея.
Наполнители — это добавки, снижающие стоимость клея и улучшающие его свойства: повышается теплостойкость, сокращается время отверждения, увеличивается жесткость. Кроме того, эти добавки существенно влияют на реологические свойства расплава, препятствуют нитеобразованию при нанесении клея-расплава на склеиваемые поверхности.
В качестве наполнителей используют в основном минеральные вещества: кварцевую муку, тальк, мел, шпат и т. д.
Обязательным компонентом клея-расплава являются антиоксиданты — вещества, предохраняющие клей от термоокислительной деструкции. Обычно клеи-расплавы наносят в горячем состоянии при температуре от 120 до
13
220°С. В связи с этим клеи в расходной емкости оборудования постоянно находятся в виде расплава при высокой температуре. Для предотвращения разложения клея при продолжительном нагреве в его состав вводят вещества
— антиоксиданты.
Качество клеев-расплавов характеризуется адгезионной и когезионной прочностью, текучестью, скоростью отверждений, термостабильностью, водо- и теплостойкостью, стойкостью к старению.
Взависимости от способов применения клеи-расплавы на основе сополимеров этилена с винилацетатом выпускаются в виде порошка, гранул, прутков и пленок. Для мебельной промышленности их выпускают в виде гранул.
Внастоящее время отечественная промышленность выпускает несколько видов клеев-расплавов: КРУС-1 (ТУ 13— 936—86), КРУС-2 (ТУ
13-03-4-87).
Свойства клеев-расплавов должны соответствовать нормативным требованиям, представленным в табл. 3.
|
|
Таблица 3 |
Техническиетребованиякклеям-расплавам |
||
|
|
|
Наименование |
Марка клея |
|
показателей |
КРУС-1 |
КРУС-2 |
|
|
|
|
Однородный гранулированный |
Гранулы произвольной |
Внешний вид |
материал белого, светло- |
формы от белового до |
|
коричневого, красно- |
красно-коричневого цвета |
|
коричневого цвета |
|
Время открытого |
|
|
отверждения |
2…8 |
– |
клея, с |
|
|
Температура |
|
|
размягчения по методу |
85 |
85 |
«кольцо — шар», °С, не |
|
|
ниже |
|
|
Термостабильность, %, |
50 |
– |
не более |
|
|
Текучесть расплава при |
15…20 |
13…20 |
180 ... 190° С, г/10 мин |
|
|
Прочность клеевого |
2,0 |
2,5 |
соединения при |
|
|
сдвиге, МПа, не менее |
|
|
Прочность клеевого, |
|
|
соединения при |
2,0 |
– |
равномерном отрыве, |
|
|
МПа, не менее |
|
|
|
14 |
|
Цель работы: установление качества клея-расплава и рационального направления использования при склеивании древесных материалов.
Для этого необходимо определить следующие физико-химические и механические показатели:
внешний вид; текучесть расплава;
температура размягчения; прочность клеевого соединения при сдвиге.
Виды испытаний. Средства измерения, посуда и реактивы
Определение внешнего вида клея: а) стакан стеклянный емкостью 300 ...
400 см3 по (ГОСТ 25336—82); б) нож.
Определение текучести расплава: а) экструзионный пластомер
(рис. 5.1); б) приспособление для введения образцов в экструзионную камеру; в) инструмент для отсечения отрезков экструзируемого материала; г) стержни для чистки капилляра; д) ерш для чистки канала экструзионной
камеры; е) развертка; |
ж) уровень; |
з) секундомер; |
и) весы |
|
(ГОСТ 19491—74) с |
погрешностью |
измерения не |
более 0,0002 г; к) |
|
термометр с погрешностью измерения 0,1 °С. |
|
|
||
Определение |
температуры |
размягчения |
клея-расплава: |
а) аппарат для определения температуры размягчения битума (ГОСТ 1424— 57) или аппарат ЛТР, включающий: подвеску на 4 кольца с расстоянием между нижней плоскостью колец и контрольным диском основания аппарата (25,00 +0,28) мм; кольца латунные гладкие (без внутреннего выступа) с внутренним диаметром (15,70 + 0,24) мм и высотой 6,35 мм; кольца латунные ступенчатые с верхним внутренним диаметром (17,70 + 0,24) мм, нижним внутренним диаметром (15,70 + 0,24) мм и высотой 6,35 мм; шарики стальные (ГОСТ 3722—81) диаметром (9,50 + 0,05) мм, массой (3,50 ± 0,05) г каждый; или полуавтоматический лабораторный прибор, основные размеры рабочей части которого и условия проведения испытания соответствуют требованиям стандарта: пластинку полированную металлическую или стеклянную; баню или стеклянный стакан диаметром не менее 90 мм и высотой не менее 115 мм; термометр ртутный; сито с металлической сеткой № 07 (ГОСТ 3584-73); нож для срезания клея-
15
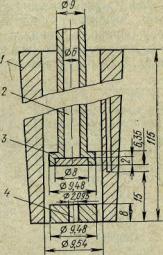
расплава; плитку электрическую с регулировкой нагрева; глицерин (ГОСТ
6823—77,6824—76, 6259—75); декстрин (ГОСТ 6034—74); тальк; пинцет.
Определение прочности склеивания при сдвиге:
а) полосы березового шпона размером 80х20х1,5 мм; б) разрывная машина со специальным устройством для зажима образца (максимальное усилие до 5000 Н); в) стеклянная палочка; г) груз для создания давления (30...
50 Н); д) электрическая плитка с регулировкой нагрева; е) термометр ртутный; ж) нож; з) стакан металлический диаметром не менее 90 мм, высотой не менее 60 мм и толщиной стенок около 1 мм.
камера; 2- стальной поршень; 3- направляющая головка; 4- капилляр
Рис.2 – Экструзионный пластомер:
Порядок выполнения работы
1.Определение внешнего вида клея-расплава.
Внешний вид клея определяется |
визуально. |
Цвет клея-расплава |
определяется на поперечном срезе гранулы |
клея. |
|
2.Определение текучести расплава.
Для испытания применяют образцы в виде гранул, порошка, пленки или другой формы, обеспечивающей его введение в отверстие экструзионной камеры.
Прибор устанавливают по уровню, нагревают без образца до соответствующей температуры испытаний и выдерживают его при этой температуре в течение 15 мин.
16
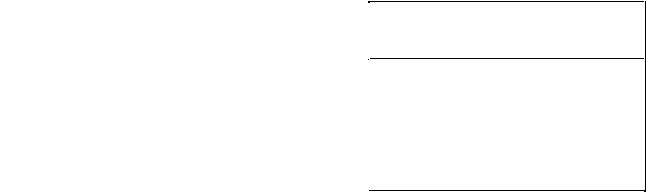
В капилляр вставляют плотно входящую медную развертку для предотвращения вытекания материала во время прогрева, вынимают поршень, загружают в экструзионную камеру образец материала массой от 4 до 8 г, в зависимости от предполагаемого значения показателя текучести расплава (табл. 4), и вручную уплотняют его.
Таблица 4
Показатель |
|
|
|
Интервалы времени между |
||
текучести расплава, |
Масса образца, г |
|
двумя отсечениями материала, |
|||
г/10 мин |
|
|
|
с |
|
|
До 0,5 |
4 |
5 |
|
|
|
|
|
|
240 |
||||
0,5 |
1,0 |
|
|
|
|
|
4. .. |
5 |
|
|
120 |
||
...1,0 |
3,5 |
. ..4 |
5 |
|
|
60 |
3,5 ... |
10,0 |
6... |
8 |
|
|
30 |
...10,0 |
25,0 |
.. .6 |
8 |
|
.10 |
..15 |
Свыше 25,0 |
6... |
8 |
|
5. |
..15 |
|
|
|
|
|
|
|
|
Чтобы исключить попадание воздуха в испытуемый материал, время загрузки его не должно превышать 1 мин.
В камеру вставляют поршень и помещают на втулку добавочный груз. После выдержки под давлением в течение времени, указанного в соответствующих стандартах и технических условиях на испытуемый материал, вынимают из капилляра развертку и дают полимеру течь.
Время предварительного прогрева материала под давлением не должно быть менее 4 мин.
Как только нижняя кольцевая метка штока поршня опустится до верхней кромки камеры, весь экструдированный материал срезают и в расчет его не принимают. Измерения показателя текучести расплава производят до тех пор, пока верхняя метка на поршне опустится до верхней кромки экструзионной камеры. Когда показатель текучести расплава меньше чем 3 г/10 мин, измерения производят в положении, когда верхняя кромка камеры находится между двумя средними метками.
Для измерения, показателя текучести расплава отбирают отрезки экструдирозанного материала, последовательно отсекаемые через интервалы времени.
Отрезки, имеющие пузырьки воздуха, отбрасывают.
17
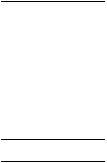
После охлаждения полученные отрезки взвешивают каждый в отдельности с погрешностью не более 0,001 г. Число их должно быть не менее трех. Масса отрезка определяется как среднее арифметическое результатов/ взвешивания всех отрезков.
После окончания измерений освобождают капилляр и удаляют из прибора остатки полимера. После каждого испытания камеру следует прочищать в горячем состоянии ветошью до зеркального блеска. Поршень вынимают и чистят в горячем состоянии тканью, смоченной в растворителе. Капилляр прочищают плотно входящим медным стержнем и при необходимости погружают в кипящий растворитель. При удалении остатков полимера или очистке прибора запрещается применять абразивные или другие подобные им материалы.
Показатель текучести расплава термопластов ПТР(г, Р) (г/10 мин) вычисляется по формуле
ПТР Т,Р
где T —температура испытания, К (°С); Р —нагрузка, Н (кгс);
t — стандартное время, с ;
m —средняя масса экструдируемых отрезков, г;
τ — интервал времени между двумя последовательными отсечениями отрезков, с.
Таблица 5 Условия определения показателя текучести расплава термопластов
Условия |
Внутренний |
Температура |
Коэффици- |
Стандартное |
Нагрузка, Н |
определения |
диаметр |
испытания, 0С |
ент, К |
время, с |
|
|
капилляра, |
|
|
|
|
|
мм |
|
|
|
|
|
|
|
|
|
|
|
|
|
|
|
|
|
|
|
|
|
|
|
|
|
|
|
|
* Для материалов с большим ПТР.
18
За результат испытания принимают среднее арифметическое двух определений на трех отрезках материала с допускаемым расхождением по массе между ними не более 5%,
3. Определение температуры размягчения клея-расплава.
Перед испытанием образец, клея-расплава при наличии влаги обезвоживают осторожным нагреванием до температуры 120 ... 180°С. Обезвоженный и расплавленный до подвижного состояния клей-расплав процеживают через сито и затем тщательно перемешивают до полного удаления пузырьков воздуха.
Для клеев-расплавов с температурой-размягчения свыше 80 °С используют два ступенчатых кольца, которые предварительно подогревают на электрической плитке до предполагаемой температуры размягчения.
Клей-расплав наливают с некоторым избытком в эти два ступенчатых кольца, помещенных на пластинку, покрытую смесью декстрина с глицерином (1:3) или талька с глицерином (1:3), при этом следует избегать образования пузырьков воздуха.
После охлаждения колец с клеем на воздухе в течение 20 мин при (25±10)°С избыток клея гладко срезают нагретым ножом вровень с краями колец.
Для клеев-расплавов с температурой размягчения от 80 до 110°С в баню наливают смесь воды с глицерином (1:2).
Кольца с клеем-расплавом помещают в отверстия на подвеске аппарата. В среднее отверстие подвески вставляют термометр так, чтобы нижняя точка ртутного резервуара была на одном уровне с нижней поверхностью клея в кольцах. Подвеску с кольцами и испытуемым клеем помещают в баню, наполненную глицерином с водой при (34±1)°С.
По истечении 10 мин подвеску вынимают из бани, на каждое кольцо в центре поверхности клея кладут пинцетом стальной шарик, нагретый в бане до (34±1)°С, и опускают подвеску обратно в баню, избегая появления пузырьков воздуха на поверхности клея.
Устанавливают баню на нагревательный прибор так, чтобы плоскость колец была строго горизонтальной. Температура воды с глицерином в бане после первых 3 мин подогрева должна подниматься со скоростью
(5,0±0,5)°С в минуту.
19

Для каждого кольца и шарика отмечают температуру, при которой выдавливаемый шариком клей-расплав коснется контрольного диска (основание) аппарата.
За температуру размягчения клея-расплава принимают среднее арифметическое значение двух параллельных определений.
Два результата определения признаются достоверными (при 95%-ной вероятности), если расхождение между ними не превышает значения, указанного в табл. 6
|
|
Таблица 6 |
|
Температура размягчения, |
Повторяемость |
Воспроизводимость, % |
|
0С |
|
|
|
До 80 |
1 |
10 от среднего значения |
|
|
|
||
Свыше 80 |
2 |
||
|
|||
|
|
|
5. Определение прочности клеевого соединения при сдвиге.
Для испытания изготавливают 20 полос березового шпона размером
80 х 20 х 1,5 мм.
Склеивание полос шпона осуществляют попарно. Для этого на каждую полосу шпона стеклянной палочкой наносят предварительно расплавленный при температуре 190 °С клей на длину нахлестки 20 мм, затем полосы соединяют и нагружают на 8 ... 10 мин грузом 30 ... 50 Н (3 ... 5 кгс).
Склеенный таким образом образец должен быть без перекосов и потеков клея. Излишки клея удаляют горячим "ножом. Для испытаний изготавливают 10 образцов.
Испытания проводят через 24 ч после склеивания на разрывной машине маятникового типа с нагрузкой до 5000 Н (500 кгс).
Образцы устанавливают таким образом, чтобы расстояние между зажимами составляло 70±2 мм. Испытания проводят со скоростью движения нижнего зажима 200 мм/мин до разрушения образца.
Предел прочности при сдвиге (а) в МПа вычисляют по формуле
·10
где Р — разрушающее усилие, Н;
S— площадь склеивания, м2.
20