
3901
.pdf21
Таблица 3.1
Наименование подшипника |
Условное |
d, |
|
|
D, |
В, |
Грузоподъем- |
|
|||||
|
|
обозначе- |
мм |
|
|
мм |
мм |
ность Н |
|
|
|||
|
|
ние |
|
|
|
|
|
|
|
дина- |
стати- |
|
|
|
|
|
|
|
|
|
|
|
|
|
миче- |
ческая, |
|
|
|
|
|
|
|
|
|
|
|
|
ская, С |
С0 |
|
Шарикоподшипник |
ради- |
208 |
|
40 |
|
80 |
18 |
25600 |
13900 |
|
|||
альный однорядный легкой |
|
|
|
|
|
|
|
|
|
|
|
|
|
серии |
|
|
|
|
|
|
|
|
|
|
|
|
|
Шарикоподшипник |
ради- |
308 |
|
40 |
|
90 |
23 |
31900 |
22700 |
|
|||
альный однорядный |
сред- |
|
|
|
|
|
|
|
|
|
|
|
|
ней серии |
|
|
|
|
|
|
|
|
|
|
|
|
|
Шарикоподшипник |
ради- |
1208 |
|
40 |
|
80 |
18 |
15100 |
8720 |
|
|||
альный сферический |
двух- |
|
|
|
|
|
|
|
|
|
|
|
|
рядный легкой серии |
|
|
|
|
|
|
|
|
|
|
|
|
|
Роликоподшипник кониче- |
7208 |
|
40 |
|
80 |
20 |
42400 |
32700 |
|
||||
ский легкой серии |
|
|
|
|
|
|
|
|
|
|
|
|
|
|
|
Fr |
= F /2 |
|
|
|
|
|
(3.2) |
||||
Момент трения, получаемый на всех четырех подшипниках |
|
|
|||||||||||
|
|
Т |
|
= 4Frf |
|
d |
|
|
|
|
|||
|
|
Т |
пр |
2 |
|
|
|
(3.3) |
|||||
|
|
|
|
|
|
|
|
||||||
|
|
|
|
|
|
|
|
|
|
|
|
||
или после подстановки значения Fr |
|
|
|
|
|
|
|
|
|
|
|||
|
|
ТТ = Fdfпр |
|
|
|
|
|
(3.4) |
|||||
Из формулы (3.4) можно определить условный, приведенный к валу ко- |
|||||||||||||
эффициент трения |
|
|
|
|
|
|
|
|
|
|
|
|
|
|
|
fпр |
= ТТ / Fd |
|
|
(3.5) |
5Порядок выполнения работы
5.1Установить на вал предназначенную для испытаний головку (по указанию преподавателя). Проверить надежность фиксации головки.
5.2Снять заднюю крышку и перебросить ремень на шкивы, соответствующие частоте вращения, равной 970 мин-1.
5.3Убедившись, что масла в подшипнике нет, включить электродвигатель и дать поработать 2…5 мин, создав нагрузку 2000…3000 Н.
5.4Включив электродвигатель, создать винтом нагружения ряд нагрузок на подшипники: 2500; 5000; 7500; 10000 Н, используя тарировочный
22
график и индикатор динамометра. На каждой ступени нагружения включить установку и по шкале замерить момент трения.
5.5Затем установить 1880 и 2860 мин-1 и произвести испытания в том
же порядке.
5.6Следующее испытание произвести с заполнением подшипника маслом до центра нижнего шарика при тех же нагрузках и тех же скоростях.
5.7Заполнить подшипник до погружения в масло нижней части внутреннего и в той же последовательности произвести испытания.
Испытания в пунктах 5.6 - 5.7 проводить по возможности при установившейся (постоянной) температуре масла.
5.8Данные испытаний занести в табл. 3.2.
5.9По формуле (3.5) вычислить условный коэффициент трения и тоже занесите в табл. 3.2.
5.10Используя данные табл. 3.2, построить графики зависимости момента трения и условного коэффициента трения от нагрузки и частоты вращения при различных уровнях смазки.
6Оформление отчета
6.1Схема установки, краткое описание устройства и работы.
6.2Данные по подшипникам, установленным для испытания.
6.3Расчетные зависимости.
6.4Результаты испытаний (табл. 3.2).
6.5 Графики зависимостей ТТ = ϕ(F) fпр = ϕ(F) при различном уровне масла в подшипнике.
7Контрольные вопросы
7.1Как изменяется момент трения с изменением нагрузки и частоты
вращения?
7.2Как изменяется условный коэффициент трения с изменением нагрузки и частоты вращения?
7.3Как влияет на момент трения и на условный коэффициент трения заполнение подшипника маслом?
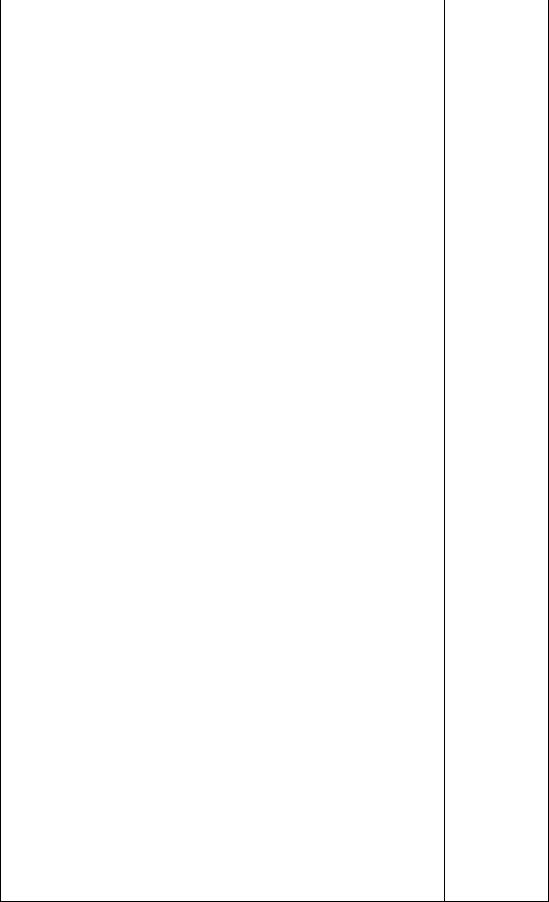
|
|
|
|
23 |
|
|
|
|
|
|
|
|
|
|
|
По внутреннему кольцу |
|
|
|
|
|
|
|
|
|
об/минn=12860 |
пр |
По центру нижнего шарика |
|
3.2Таблица |
Нм, f |
|
|||
Без смазки |
|||||
|
|
|
|
||
|
|
|
|
|
|
|
|
|
|
По внутреннему кольцу |
|
|
|
|
|
|
|
|
|
|
|
По центру нижнего шарика |
|
|
|
|
Т |
|
|
|
|
|
Т |
|
|
|
|
|
Без смазки |
||
|
|
|
|
||
|
|
|
|
|
|
|
подшипник |
|
|
По внутреннему кольцу |
|
|
об/мин |
f |
|
||
|
По центру нижнего шарика |
||||
|
|
|
пр |
||
|
|
|
|
|
|
|
|
|
|
Без смазки |
|
|
Испытуемый |
n=1880 |
|
|
|
|
Т |
По внутреннему кольцу |
|||
|
|
|
|
||
|
|
|
Нм |
|
|
|
|
|
По центру нижнего шарика |
||
|
|
|
, |
|
|
|
|
|
Т |
|
|
|
|
|
|
|
|
|
|
|
|
Без смазки |
|
|
|
|
|
|
|
|
|
|
|
По внутреннему кольцу |
|
|
|
|
|
|
|
|
|
об/мин |
пр |
По центру нижнего шарика |
|
|
|
f |
|
||
|
|
|
Без смазки |
||
|
|
|
|
||
|
|
|
|
|
|
|
|
n=970 |
|
По внутреннему кольцу |
|
|
|
Нм |
|
||
|
|
По центру нижнего шарика |
|||
|
|
|
, |
|
|
|
|
|
Т |
|
|
|
|
|
Т |
|
|
|
|
|
Без смазки |
||
|
|
|
|
||
|
|
|
|
|
Нагрузка, Н
2500 |
5000 |
7500 |
10000 |
24
ЛАБОРАТОРНАЯ РАБОТА №4
ИЗУЧЕНИЕ ПОСАДОК ДЕТАЛЕЙ МАШИН
1 Цель работы
Ознакомление с рекомендациями по выбору посадок зубчатых колес, шкивов ременных передач, звездочек цепных передач и подшипников качения.
2Общие сведения
Вмашинах и механизмах соединяемые между собой детали должны иметь в зависимости от условий работы различную свободу относительного перемещения, определяемую степенью сопротивления их взаимного смещения. Например, соединение зубчатого колеса с валом должно обеспечить неподвижность, а соединение подшипника скольжения с валом – свободное вращение. Выполнение указанных требований осуществляется применением той или иной посадки. Посадки разделяют на три группы:
- с натягом (для неподвижных соединений); - с зазором (для подвижных соединений);
- переходные (возможна подвижность при приложении небольшого усилия).
Приведём понятия по терминологии единой системы допусков и посадок. Вал – термин, применяемый для обозначения наружных (охватываемых)
элементов деталей.
Отверстие – термин, применяемый для обозначения внутренних (охватывающих) элементов деталей.
Номинальный размер – основной размер, который определяется расчетом на прочность или по конструктивным соображениям, он служит началом отсчета отклонений. Номинальные размеры округляются в соответствии с нормальным рядом чисел по ГОСТу.
Действительный размер – это размер, полученный в результате измерения с допустимой погрешностью.
Предельными размерами называют максимальное и минимальное значения размера, между которыми должен находиться действительный размер детали. Большее из них – наибольший предельный размер, меньшее – наименьший предельный размер.
Отклонение размера – алгебраическая разность между действительным размером и его номинальным значением.
Верхнее предельное отклонение – алгебраическая разность между наибольшим предельным размером и номинальным.
Нижнее предельное отклонение – разность между наименьшим предельным размером и номинальным.

25
Допуском размера называют разность между наибольшим и наименьшим предельными размерами. Допуск диаметра отверстия δD = Dmax − Dmin ,
допуск диаметра вала δd = dmax − dmin , где Dmax и Dmin – наиболее и наименее допустимые диаметры отверстий; dmax и dmin – наиболее и наименее допустимые диаметры вала.
Поле допуска – совокупность всех возможных отклонений в пределах допуска.
Зазор – разность действительных размеров отверстия и вала, если размер отверстия больше размера вала.
Натяг – разность размеров вала и отверстия до сборки, если размер вала больше размера отверстия.
Различают посадки в системе отверстия – это такие посадки, при которых наименьший предельный размер отверстия равен номинальному (нижнее отклонение равно нулю), и посадки в системе вала, у которых наибольший предельный размер вала равен номинальному (верхнее отклонение равно нулю). Например, в системе отверстия: отверстие 50+0,5, вал 50+−00,,0301 ; в систе-
ме вала: отверстие 50+−00,,0502 , вал 50-0,02. Всегда верхнее отклонение записы-
вается выше, нижнее – ниже номинального размера, справа от него. В нашей стране в основном принята система отверстия.
Для краткости на чертежах размеры и положенные поля допуска, определяющие характер соединения, обозначают буквой латинского алфавита – прописной (заглавной) А, В, С…Z для отверстий и строчной (малой) а, в, с…z для валов (табл. 4.1).
|
|
|
Таблица 4.1 |
|
|
|
|
Основное |
Посадки с зазором |
Переходные |
Посадки с натягом |
отклоне- |
|
посадки |
|
ние |
|
|
|
Отверстие |
A, B, C, D, E, F, G, H |
Js, K, M, N |
P, R, S, T, U, V, X, Y, Z |
|
|
|
|
Вал |
a, b, c, d, e, f, g, h |
Js, k, m, n |
p, r, t, u, v, x, y, z |
|
|
|
|
На чертежах предельное отклонение указывается следующим образом:
-условными обозначениями, например отверстие 50Н7, вал 55q6;
-числовыми значениями в мм, например отверстие 50+0,05, вал50−−0,0320,059;
-комбинированным способом, например отверстие 18Н7+0,018, вал
12е8 −− 00,,032059 .
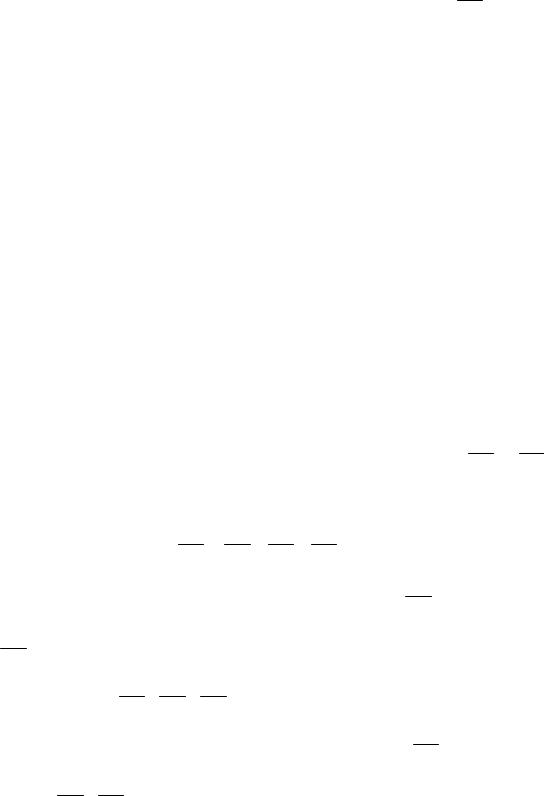
26
На сборочных чертежах посадки указывают в виде дроби, в числителе –
для отверстия, в знаменателе - для валов. Например, 50 Н7 . g6
Цифра справа от буквенного обозначения посадки характеризует степень точности (степень качества) соединения, или квалитет (табл. 4.2)
|
|
|
|
|
|
|
|
|
|
|
|
|
|
|
|
|
|
|
|
Таблица 4.2 |
|
|
|
|
|
|
|
|
|
|
|
|
|
|
|
|
|
|
|
|
|
|
|
|
|
Точные |
|
|
|
|
|
Средние |
|
|
|
Грубые |
|
|
|||||||
01 |
0 |
|
1 |
2 |
|
3 |
4 |
5 |
6 |
7 |
|
8 |
9 |
10 |
11 |
13 |
14 |
15 |
16 |
17 |
|
В машинах и механизмах общего назначения обычно применяют средние квалитеты.
3 Рекомендации по выбору посадок
3.1 Посадки зубчатых и червячных колес
Посадка зубчатых и червячных колес на вал, как правило, выполняется в системе отверстия. При выборе типа посадки учитывают условия работы и величину передаваемой нагрузки.
Для неподвижных соединений колес с валом, которые требуют периодической разборки, применяют переходные посадки Нn67 и Hk67 (первая –
для небольших нагрузок, вторая – для средних, при мощности двигателя до 5 кВт). Для зубчатых и червячных редукторов общего назначения обычно
используют посадки Нr67 , Hs67 , Hp67 , mH76 . Для цилиндрических зубчатых и червячных колес наиболее употребима посадка Hp67 , для конических колес mH76 . Для подвижных блоков шестерен коробок передач по шпонкам применяют посадки Нh67 , Hf 67 , He87 . Посадку зубчатого вала на ступицу червячного колеса осуществляют при сплошной нагрузке по Hp67 , при умеренных толчках по Hr67 , Нn67 .

27
3.2 Посадка шкивов и звездочек
Рекомендуемые посадки шкивов ременных передач и звездочек цепных передач – переходные: при спокойной нагрузке Нк67 , при умеренных толчках
mН76 , Hn67 (если шкивы и звездочки установлены на шпонках).
3.3 Посадки подшипников качения
Посадки подшипников качения в корпус и на вал производятся в зависимости от режима работы в табл. 4.3.
|
|
Таблица 4.3 |
|
|
|
Посадка |
Режим работы |
Рекомендуемая по- |
|
|
садка |
В корпус |
Легкий или нормальный |
Js7 |
На вал |
Легкий или нормальный |
js6, k6 |
В корпус |
Нормальный или тяжелый |
H7, K6 |
|
|
|
На вал |
Нормальный или тяжелый |
k6, m6 |
|
|
|
4 Соединения с натягом (прессовые соединения)
В последнее время для передачи момента со ступицы детали на вал все чаще стали применять соединения с натягом (без шпонок и шлицевых соединений).
Исходными данными являются: вращающий момент на ступице Т, Нмм; диаметр соединения d, мм; диаметр отверстия пустотелого вала d1, мм (для сплошного вала d1=0); диаметр (условный) ступицы d2, мм; длина сопряжения
l, мм.
Выбор посадок осуществляют в следующем порядке. |
|
||
Определяют среднее контактное давление, МПа |
|
||
р = |
2Тk |
, |
(4.1) |
|
|||
|
πd2lf |
|
где k – коэффициент запаса сцепления (муфты соединительные k=3, штифты ременных передач k=4, звездочки цепных передач k=3,5, зубчатые колеса k=4,5);
f – коэффициент трения (табл.4.4).
28
|
|
|
|
|
|
|
|
|
|
Таблица 4.4 |
|
|
|
|
|
|
|
|
|
|
|
|
|
Материал соединительных дета- |
|
|
|
|
|
Сборка |
|
|
|||
лей |
|
|
прессованием |
Нагревом |
|
||||||
Сталь-чугун |
|
|
|
0,08 |
|
0,14 |
|
||||
Сталь-сталь |
|
|
|
0,08 |
|
0,14 |
|
||||
Сталь-бронза, латунь |
|
|
|
0,05 |
|
0,07 |
|
||||
Чугун-бронза, латунь |
|
|
|
0,05 |
|
0,07 |
|
||||
Находят деформацию деталей, мм, |
|
|
|
|
|
|
|||||
|
|
|
|
C2 |
|
|
|
|
|||
|
|
|
C1 |
+ |
|
|
(4.2) |
||||
|
|
|
|||||||||
|
|
δ = рd |
|
, |
|
||||||
|
|
E1 |
|
E2 |
|
|
|
||||
где С1 и С2 – коэффициенты жесткости соединяемых деталей: |
|||||||||||
1+ (d1 /d)2 |
|
|
1+ (d/d2 )2 |
|
|
|
|||||
C1 = |
|
− µ ; |
|
C2 = |
|
+ µ2 . |
(4.3) |
||||
1− (d1 /d)2 |
|
1− (d/d2 )2 |
|||||||||
В приведенных формулах Е |
– |
модуль упругости: |
для стали – |
2,1.105МПа, для чугуна – 0,5.105МПа, для бронзы и латуни – 105МПа; µ - коэффициент Пуассона: для стали – 0,3, чугуна – 0,25, бронзы и латуни – 0,35.
Затем производят проверку на обмятие микронеровностей, мм,
(4.4) где Ra1 и Ra2 - средние арифметические отклонения профиля поверхностей (табл.4.5). Табличные значения перевести в мм.
|
|
|
|
|
|
|
|
Таблица 4.5 |
||
|
|
|
|
|
|
|
|
|
|
|
|
|
|
Отверстие |
|
|
Вал |
|
|
|
|
Интервалы разме- |
|
|
|
Квалитет |
|
|
|
|
||
|
ров, мм |
6, 7 |
|
8 |
9 |
6, 7 |
8 |
|
9 |
|
|
|
|
|
|
Ra, мкм |
|
|
|
|
|
Св. 18 |
до 50 |
0,8 |
|
1.6 |
3,2 |
0,8 |
0,8 |
|
1,6 |
|
Св. 50 |
до 120 |
1,6 |
|
1,6 |
3,2 |
0,8 |
1,6 |
|
1,6 |
|
Св. 120 до 500 |
1,6 |
|
3,2 |
3,2 |
1,6 |
3,2 |
|
3,2 |
Проводят проверку на температурную деформацию (обычно при подборе посадки зубчатых венцов червячных передач, которые нагреваются при работе передачи до высоких температур).
δt = d106 [(t2 − 200 )α2 − (t1 − 200 )α2 ], |
(4.5) |
29
где α - коэффициенты: для стали – 12.10-6, для чугуна – 10.10-6, для бронзы, латуни – 19.10-6;
t1 и t2 – средние объемные температуры соответственно обода центра и венца колеса.
Находят минимальный натяг (мм), который для передачи вращающего момента должен быть
[N]min ≥ δ + u + δt . |
(4.6) |
Определяют максимальный натяг (мм), допускаемый прочностью охватывающей детали
[N]max ≤ [δ]+ u , |
(4.7) |
где [δ]=[p]max δ/p, мм – максимальная деформация, допускаемая прочностью
охватывающей детали ([p]max = 0,5σT2 [1− (d/d2 )2 ], МПа –максимальное давление, допускаемое прочностью охватывающей детали, где σT2 - предел текуче-
сти материала охватывающей детали ,МПа).
Производят выбор посадки. По значениям [N]min и [N]max , переведя их размерности в мкм, выбирают из табл.4.6 одну из посадок.
|
|
|
|
|
|
Таблица 4.6 |
|
|
|
|
|
|
|
|
|
Интервалы |
Н7/р6 |
Н7/г6 |
Н8/s7 |
Н7/s6 |
Н7/s7 |
Н7/t6 |
|
диаметров, мм |
|
|
|
|
|
|
|
30…40 |
7/36 |
15/44 |
13/59 |
24/53 |
25/61 |
29/58 |
|
40…50 |
-//- |
-//- |
-//- |
-//- |
-//- |
35/64 |
|
50…65 |
9/44 |
18/53 |
18/72 |
30/65 |
32/74 |
43/78 |
|
65…80 |
-//- |
20/55 |
24/78 |
36/71 |
38/80 |
52/87 |
|
80…100 |
10/51 |
24/65 |
29/93 |
44/85 |
46/96 |
64/105 |
|
Интервалы |
Н8/n8 |
Н7/n7 |
Н8/x8 |
Н8/z8 |
Н8/Zа8 |
|
|
диаметров, мм |
|
|
|
|
|
|
|
30…40 |
32/88 |
42/88 |
52/108 |
84/140 |
120/175 |
|
|
40…50 |
42/98 |
52/88 |
69/125 |
108/164 |
152/207 |
|
|
50…65 |
55/119 |
66/109 |
90/154 |
140/204 |
193/258 |
|
|
65…80 |
70/134 |
81/123 |
114/178 |
178/242 |
241/309 |
|
|
80…100 |
86/162 |
99/149 |
149/216 |
220/294 |
297/373 |
|
|
5 Порядок выполнения работы
5.1Ознакомиться с терминологией единой системы допусков и посадок.
5.2Изучить систему обозначения посадок.
5.3Ознакомиться с рекомендациями по выбору посадок зубчатых и червячных колес.
30
5.4Ознакомиться с рекомендациями по выбору посадок шкивов и звез-
дочек.
5.5Ознакомиться с рекомендациями по выбору посадок подшипников
качения.
5.6Изучить методику расчета и выбора посадок для прессовых соеди-
нений.
6 Оформление отчета
6.1Привести наиболее употребимые посадки зубчатых и червячных колес, шкивов ременных передач, звездочек цепных передач и подшипников качения.
6.2Представить расчет по выбору посадки прессового соединения зубчатого колеса с валом по данным: передаваемый вращающий момент Т=200000 Нмм; диаметр соединения d=35 мм; вал сплошной, то есть d1=0;
диаметр ступицы колеса d2=50 мм; длина ступицы l=35 мм; материал вала – Сталь 45, материал колеса и его ступицы - Сталь 45. Предел текучести взять разным σT2 =500 МПа.
7 Контрольные вопросы
7.1Как понимать термин «посадка в системе отверстия»?
7.2Как понимать термин «посадка в системе вала»?
7.3Как обозначается посадка на сборочных чертежах и на чертежах деталей машин ?
7.4В чем суть методики расчета посадок прессовых соединений ?