
4327
.pdf21
|
|
|
|
Таблица 3.1 |
|
|
Составы огнеупорных покрытий (красок) кокилей |
||||
Назначение |
№ |
Компоненты |
содержимое |
|
Коэфф. теп – |
|
состава |
|
по массе, % |
|
лопроводнос- |
|
|
|
|
|
ти, Вт/(м·к) |
|
|
|
|
|
|
Для отливок из |
|
Окись цинка |
15 |
|
|
алюминиевого |
1 |
Асбест прокаленный |
5 |
|
0,41 |
сплава |
|
Жидкое стекло |
3 |
|
|
|
|
Вода |
77 |
|
|
|
|
|
|
|
|
|
|
Тальк |
18 |
|
|
|
2 |
Борная кислота |
25 |
|
0,39 |
|
|
Жидкое стекло |
25 |
|
|
|
|
Вода |
77 |
|
|
|
|
|
|
|
|
Полностью разбирают кокиль после охлаждения до температуры 300…400°С, т.е. через 2…3 мин. Из песчаной формы отливку можно выбивать через 3…5 мин. Отливки после выбивки показаны на рис.3.5 а, б. После очистки и обрубки литниковой системы произвести осмотр отливок, сравнить их качество (наличие усадочных раковин, газовых раковин, трещин
ит.д.). Сопоставить размеры литниковых систем.
3.11Содержание отчета
3.11.1Описать модельный комплект и технологию изготовления песчаной формы. Выполнить следующие эскизы: модели, стержневого ящика, стержня, собранной формы в разрезе, отливки с литниковой системой
иотливки, совмещенной с готовой деталью.
3.11.2Описать устройство кокиля, подготовку его к заливке жидкого металла. Выполнить эскизы: кокиля в разрезе, отливки с литниковой системой.
3.11.3Обосновать выбор температуры заливки сплава в кокиль и в песчаную форму.
3.11.4Сравнить качество отливок, полученных в кокиле и в песчаной
форме.
3.12Контрольные вопросы
3.12.1Что такое модельный комплект, что в него входит?
3.12.2Перечислите основные свойства формовочных и стержневых
смесей и дайте им определения.
3.12.3Изложите порядок изготовления песчаной формы.
3.12.4Что такое кокиль и как он устроен?
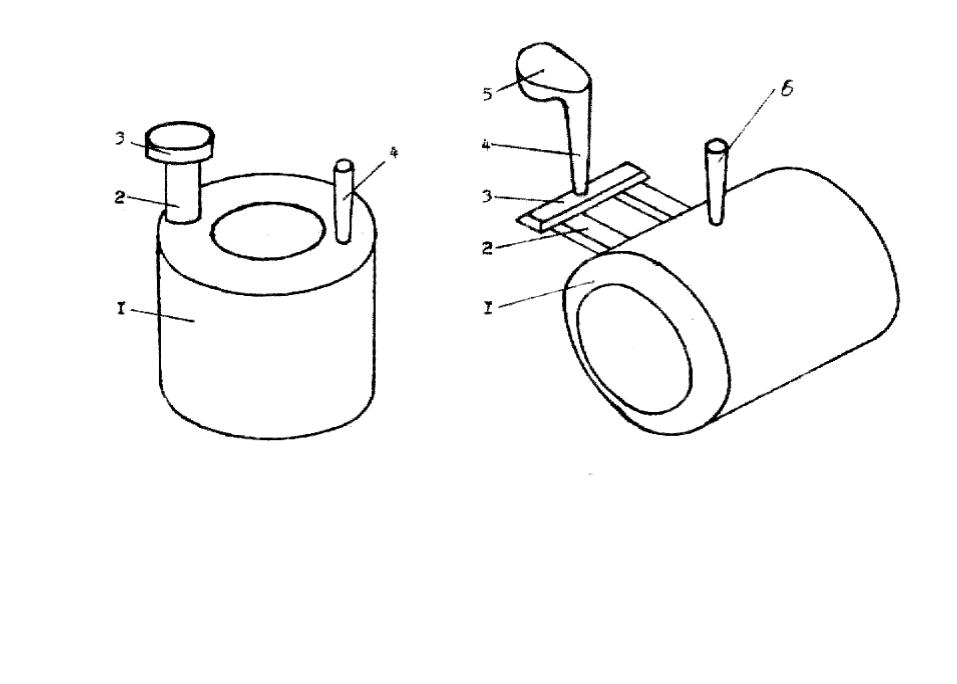
22
Рис. 3.5 а Отливка, полученная литьем |
Рис.3.5 б Отливка, полученная литьем |
в кокиль (после выбивки): |
песчянную форму (после выбивки): |
1 – отливка; 2 – литниковый стояк; 3 – |
1 – отливка в; 2 – питатель; 3 –шлакоуло- |
литниковая чаша; 4 – выпор |
витель; 4 – литниковый стояк; 5 – литни- |
|
|
23
3.12.5Какие основные этапы подготовки кокиля к заливке жидкого сплава?
3.12.6На сколько градусов температура заливки жидкого сплава должно превышать температуру его плавления и почему?
3.12.7Какие виды брака отливок возможны при литье в песчаные формы
ив
кокиль?
4 ЛАБОРАТОРНАЯ РАБОТА № 3
РАЗРАБОТКА ТЕХНОЛОГИИ ПОЛУЧЕНИЯ ОТЛИВКИ В ПЕСЧАНОЙ ФОРМЕ
4.1 Цель и содержание работы
Целью настоящей работы является приобретение студентом навыков самостоятельной разработки технологии получения отливки в песчаной форме методом ручной формовки.
Процесс разработки технологии получения отливки включает в себя следующие этапы:
4.1.1Знакомство с чертежом детали, ее технологичностью, серийностью производства, материалом детали.
4.1.2Технологическую проработку чертежей отливки, модели, стержня и стержневого ящика, формы в сборе.
4.1.3Расчет сечений элементов литниковой системы, массы отливки, технико-экономических показателей.
4.2Последовательность выполнения задания
4.2.1Выполнить чертеж детали в соответствии с вариантом задания.
4.2.2Разработать чертеж отливки.
4.2.3Рассчитать размеры стержня и выполнить его чертеж.
4.2.4Разработать чертеж модели, предварительно выбрав материал для
ееизготовления.
4.2.5Выбрать размеры опок.
4.2.6Выполнить расчет литниковой системы.
4.2.7Разработать чертеж литейной формы в разрезе.
4.2.8. Определить технико-экономические показатели.
4.3 Выполнение чертежа детали Чертеж детали, как и другие чертежи выполнить на формате А4 (формат 11).
Количество проекций должно давать полное представление о форме и размерах
24
детали. Обрабатываемые поверхности в соответствия с функциональным
назначением должны иметь знак обработки ( ) с указанием шероховатости, а размеры с указанием точности обработки. О том, что остальные поверхности
не обрабатываются, укажет знак ( )в правом верхнем углу чертежа. В
основной надписи указать материал, из которого должна быть изготовлена отливка. В технических условиях указать серию отливаемых деталей.
4.4 Разработка чертежа отливки
Основой для разработки чертежа отливки является чертеж детали. Разработку начинать с анализа технологичности отливки, требований к наиболее ответственным ее частям, свойств используемого сплава и т.д.
Технологичность получения отливки определяется правильностью выбора плоскости разъема. Разъем литейной формы целесообразно совместить с разъемом модели. При этом следует учесть удобство формовки и извлечения модели из формы. Наиболее ответственные поверхности отливки целесообразно располагать в нижней части формы или вертикально, так как в верхней части формы скапливаются газы, неметаллические включения, что способствует снижению качества отливки -появлению газовых раковин, шлаковых включений. Кроме того, по возможности, следует стараться расположить отливку или хотя бы ее базовые поверхности для механической обработки в одной нижней полуформе, что позволит предотвратить перекосы и смещения. Отливки цилиндрической формы, поверхности которых подвергаются механической обработке резанием, желательно при заливке располагать вертикально.
Если модель состоит из двух неравных частей, то большую по габаритам часть модели целесообразно установить в нижней полуформе. На чертеже отливки разъем будущей модели показывают отрезком или ломаной штрихпунктирной линией, заканчивающейся знаками "Х- • - X", а направление разъема - сплошной основной линией (со стрелками), перпендикулярной линии разъема. При совпадении плоскости разъема модели и формы над этой линией слева проставляют буквенное обозначение МФ (разъем модели и формы), а положение отливки в форме при заливке обозначают буквами В (верх) и Н (низ). При неразъемной модели указывают только разъем формы - Ф.
Припуски на механическую обработку наносят на чертеж отливки там, где
стоят знаки механической обработки ( ).
Величина припуска зависит от материала детали, точности размеров обрабатываемой поверхности, способа изготовления и размеров отливки, а также от положения обрабатываемой поверхности в форме при заливке ее металлом.
25
Припуски наносят на чертеж отливки сплошными тонкими линиями и штрихуют только в плоскости разреза (допускается выполнять линии припуска красным карандашом).
Величину припусков для отливок из серого чугуна выбирают по табл. 4.1, для стальных отливок по табл. 4.2 и для отливок из цветных сплавов по табл. 4.3. При выборе припусков следует учитывать возможное коробление отливки, класс ее точности. Припуски на нижние и боковые поверхности имеют одинаковые значения, на верхние поверхности припуски увеличены из-за неметаллических включений, пузырьков газа, всплывающих на поверхность жидкого металла.
Минимальная толщина стенки, которая может быть получена данным способом литья, зависит от жидкотекучести металла и габаритных размеров отливки. Поэтому минимальную конструктивную толщину стенки детали необходимо по табл. 4.4 проверить на минимальную допустимую толщину стенки отливки S, которая при литье в песчаную форму зависит от заливаемого металла и некоторого параметра N, учитывающего габаритные размеры отливки. Параметр N определяется по формуле
N = |
2l + b + h |
, м, |
(4.1) |
|
3 |
||||
|
|
|||
|
|
|
где l - наибольший габаритный размер отливки;,
b и h - соответственно ширина и высота отливки, м.
Если полученная расчетным путем толщина стенки отливки оказалась больше конструктивной, то последнюю следует увеличить, если меньше - то конструктивную толщину стенки можно оставить без изменения.
Сопряжения стенок отливки, так же как и модели, долины быть плавными, т.е. скругленными. Округления внутренних углов называют галтелями, наружных - закруглениями. Галтели и закругления облегчают извлечение модели из формы, уменьшают возможность появления трещин и усадочных раковин в отливках. Величину радиуса галтели (закругления) определяют по формуле
|
1 |
|
1 |
S1 |
+ S2 |
|
|
|
r = |
|
/ |
|
|
|
|
, мм, |
(4.2) |
3 |
5 |
|
2 |
|||||
|
|
|
|
|
где S1 и S2 -толщины сопрягаемых стенок отливки в мм.
26
Округление расчетной величины радиуса производят в большую сторону до рекомендуемых значений: I, 2, 3, 5, 8, 10, 15, 20, 25, 30 и 40 мм.
Формовочные уклоны назначают в тех случаях, когда деталь не имеет конструктивных уклонов, обеспечивающих свободное извлечение модели из формы. Существует три возможных варианта выполнения уклонов: путем увеличения размеров отливки ("в плюс") на обрабатываемых поверхностях сверх припусков на механическую обработку или на необрабатываемых при толщине стенки меньше минимально допустимой величины; путем одновременного увеличения и уменьшения размеров отливки ("в плюсминус") на необрабатываемых поверхностях, которые не сопрягаются с другими деталями, или при толщинах стенок от 8 до 12 мм; путем уменьшения размеров отливки ("в минус") на необрабатываемых поверхностях, сопрягаемых с другими деталями, или при толщинах стенок более 12 мм.
Величины минимальных уклонов моделей и стержневых ящиков зависят от измеряемой высоты поверхности и находятся из табл. 4.5.
4.5 Разработка чертежа стержня
Стержни служат для образования в отливках отверстий и внутренних полостей. В процессе заливки формы стержни окружены со всех сторон расплавленным металлом, испытывают значительные термические и механические воздействия, поэтому должны обладать высокой прочностью, газопроницаемостью, хорошей податливостью и выбиваемостью. В единичном мелкосерийном производстве литейные стержни изготовляют в стержневых ящиках ручным способом.
К основным элементам конструкции литейного стержня относят знаковые части, которые служат для установки стержня в форме, обеспечивают его устойчивость и точную фиксацию положения в форме, а также вывод газов, выделяющихся из стержня при заливке жидкого металла. Для улучшения вывода газов накалывают иглами вентиляционные каналы.
Размеры стержня выполняют с учетом линейной усадки заливаемого сплава (табл. 4.6). Место расположения стержня должно быть такое, чтобы исключить разностенность отливки. Точность установки стержня обеспечивается формой знаковых частей, их размерами, которые назначают по таблице 4.7 а, б с учетом размеров стержня и его положения в форме (рис. 4.1). Высоту верхних вертикальных знаков h1 (рис. 4.1) принимают не менее 0,5 h. Формовочные уклоны на знаковых частях стержня принимают в пределах от 6 до 10°. Зазоры S между знаковыми поверхностями форм и стержней в зависимости от их размеров берут в пределах от 0,3 до 1,5 мм и указывают на чертежах только в случае отклонения от рекомендуемых величин. Контуры стержней изображают сплошной тонкой лини-ей (допускается синим цветом). Стержни в разрезе штрихуют только у контурных
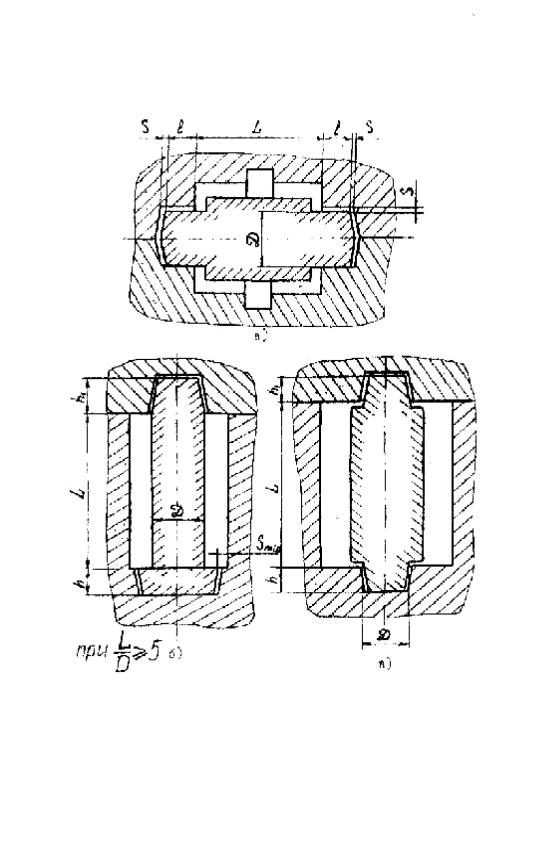
27
Рис. 4.1 Положение стержней в литейной форме: а) – горизонтальное; б), в) - вертикальное
28
линий и обозначают буквами "Ст" с указанием порядкового номера, например. Ст1, Ст2.
4.6 Разработка чертежа модели
Литейная модель - это приспособление, при помощи которого в формовочной смеси получают полость с формой и размерами, близкими к размерам отливки. Поэтому при разработке чертежа модели за основу принимают форму и размеры отливки и увеличивают на величину линейной усадки заливаемого сплава (см. табл. 4.6).
Для изготовления моделей используют различные материалы. Наиболее часто применяют древесину различных пород. Деревянные модели значительно дешевле других и широко применяются не только для индивидуального и мелкосерийного производства, но и для серийного производства крупногабаритных отливок.
Комбинированные модели - деревянные с металлическими частями используют для серийного производства.
Гипсовые и цементные смеси используют для изготовления простых моделей при мелкосерийном и серийном производстве.
Металлические модели применяют в серийном, крупносерийном и массовом производстве. Их основные преимущества — долговечность, точность размеров и чистота поверхности. В качестве материала для изготовления металлических моделей используют в основном алюминиевые сплавы, иногда серый чугун или бронзу. Металлические модели с целью облегчения делают полыми и тонкостенными. Толщина стенки должна быть не меньше указанной в табл. 4.8. В последние годы нашли применение модели из пластических масс. Они легче и дешевле металлических, однако уступают им по стойкости. Деревянные модели окрашивают:
-для чугунных отливок - в красный цвет;
-для стальных отливок - в синий цвет;
-для отливок из цветных сплавов - в желтый цвет. Стержневые знаки на
моделях окрашивают в черный цвет.
4.7 Выбор размеров опок
Применяемые в литейных цехах опоки изготовляют из стали, чугуна, алюминиевых сплавов и в некоторых случаях в условиях индивидуального производства - из древесины. По конструкции опоки делят на цельнолитые, свертные и сварные. По форме они бывают прямоугольные, квадратные, фасонные и круглые.
Прежде чем выбрать, размеры опок, следует определить место расположения литниковой системы и согласно табл. 4.9 принять расстояния
29
(не менее допустимых) между элементами модели, литниковой системой и стенками опок. Полученные размеры опок округлить и из табл. 4.10 выбрать внутренние размеры опок.
4.8 Расчет литниковой системы
Литниковая система - это система каналов, предназначенная для подвода расплавленного металла в полость литейной формы и питания отливок при затвердевании.
Основными элементами литниковой системы является литниковая чаша или воронка, стояк, шлакоуловитель, питатель, выпор и при необходимости прибыль.
Литниковая чаша предназначена для приема жидкого металла из ковша и удержания шлака, попавшего вместе с металлом в чашу. Стенки чаши выполняются под углом, близким к 45°, а дно перед входом в стояк имеет возвышение (порожек).
Литниковая воронка представляет собой расширение верхней части стояка и предназначена для приема жидкого металла.
Литниковый стояк - вертикальный канал для подачи жидкого металла из чаши к другим элементам литниковой системы. Стояк выполняют в верхней полуформе с конусностью до 5°.
Шлакоуловитель служит для распределения металла из стояка по питателям и улавливания шлаков, движущихся вместе с жидким металлом. Это, как правило, горизонтальный канал трапецеидального профиля, расположенный в верхней полу форме.
Питатель - это литниковый канал, предназначенный для подвода жидкого металла к полости формы. Питатель выполняют по разъему в нижней полуформе сечением в виде трапеции с переходом в месте сопряжения с отливкой в широкий прямоугольник (для облегчении отламывания). Количество питателей выбирают исходя из необходимости равномерного заполнения всей формы.
Выпор предназначен для выхода газов из полости формы, питания отливки при затвердевании и облегчения контроля заполнения формы. Количество выпоров зависит от размеров и конфигурации отливки, а устанавливают их в самых высоких точках верхней полуформы. Выпор имеет конусность до 5° с сечением у основания 1/2 - 1/4 сечения стенки отливки.
Прибыль является добавочной частью отливки, служащей для ее питания в процессе затвердевания и для предотвращения появления в отливке усадочных раковин. Остальные функции прибыли те же, что и выпора.
Литниковая система оказывает существенное влияние на качество отливки и расход металла. Следует стремиться к тому, чтобы при обеспечении необходимого качества отливки расход металла на литниковую систему был минимальным.
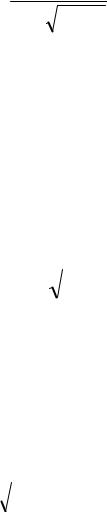
30
Для расчета размеров элементов литниковой системы необходимо определить массу отливки Q в кг по формуле
Q=Vp, кг, |
(4.3) |
где V - объем отливки, м3;
р - плотность металла, кг/м² (см. табл. 4.6).
Вначале рассчитывается наиболее узкое сечение литниковой системы. Для сужающейся системы, наиболее часто используемой при литье в песчаные формы, узким сечением является питатель, суммарная площадь которого ∑Fmin в мм2 определяется по следующей эмпирической формуле
∑F min= Q 106 , мм2 , (4.4)
ρτµ 2gHp
где τ - продолжительность заливки, с;
µ- коэффициент расхода металла: для чугунного литья 0,27… 0,55; для стального литья 0,3…0,4; для цветного литья " 0,6…0,7;
g- ускорение свободного падения, м/с2 ( g = 9,83 м/с2); Нр - расчетный статистический напор, м.
Продолжительность заливки формы τ , с, для отливки массой до 450 кг определяют по формуле
|
|
τ = К |
|
|
|
|
||
|
|
|
Q , c, |
(4.5) |
||||
где К - коэффициент, учитывающий (преобладающую или среднею) |
||||||||
толщину стенки отливки S, мм: |
|
|
|
|
||||
S, MM |
2,5…3,5 |
3,5…6,0 |
|
|
8…15 , |
|
||
K, |
1,68 |
1,85 |
|
|
2,2 |
|
||
Для отливок массой до 1000 кг |
|
|
|
|
||||
|
|
|
|
|
|
|
|
|
|
|
τ = К 3 SQ |
, с, |
(4.6) |
||||
|
|
1 |
|
|
||||
где K - коэффициент, зависящий от толщины стенки отливки S, мм. |
||||||||
S, мм |
до 10 |
20 |
|
|
40 |
до 80 и более |
||
К, |
1,0 |
1,35 |
|
1,5 |
1,7 |
Расчетный напор Нр зависит от размеров отливки, верхней опоки,