
Методическое пособие 773
.pdf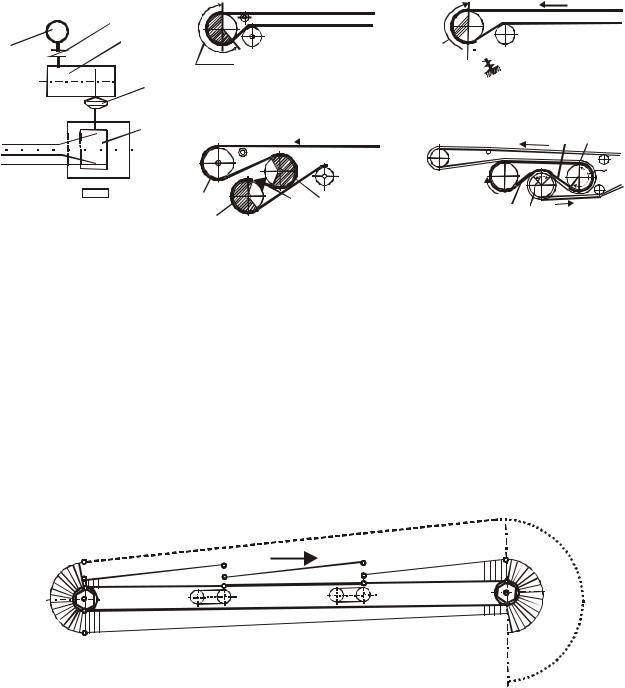
31
|
2 |
1 |
3 |
=220о |
|
4 |
б |
|
1
R
г
|
|
|
|
|
|
|
|
|
|
|
|
|
|
|
|
|
|
|
|
5 |
=480о |
|
|
|
|
|
|
|
|
||||||
|
|
|
|
|
|
|
|
|
|
|
|
|
|
|
|
|
|
|
|
|
|
|
|
|
|
|
|
||||||||
|
|
|
|
|
|
|
|
|
|
|
|
|
|
|
|
|
|
|
|||||||||||||||||
|
|
|
|
|
|
|
|
|
|
|
|
|
|
|
|
|
|
|
|
|
|
|
|
|
|
|
|||||||||
|
|
|
|
|
|
|
|
|
|
|
|
|
|
|
|
|
|
|
|
|
|
|
|
|
|
|
|
|
|
|
|||||
|
|
|
|
|
|
|
|
|
|
|
|
|
|
|
|
|
|
|
|
|
|
|
|
|
|
|
|
|
|
|
|
|
|
|
|
|
|
|
|
|
|
|
|
|
|
|
|
|
|
|
|
|
|
|
|
|
|
|
|
|
|
|
|
|
|
|
|
|
|
||
|
|
|
|
|
|
|
|
|
|
|
|
|
|
|
|
|
|||||||||||||||||||
|
|
|
|
|
|
|
|
|
|
|
|
|
|
|
|
||||||||||||||||||||
|
|
|
|
|
|
|
|
|
|
|
|
|
|
|
|
|
|
|
|
|
|
|
|
|
|
|
|
|
|
|
|
|
|
|
|
|
|
|
|
|
|
|
|
|
|
|
|
|
|
|
|
||||||||||||||||||||
|
|
|
|
3 |
|
|
|
Sпр 1 |
|
|
|
|
а |
2 |
|||||||||||||||||||||
|
|
|
|
|
|
|
|
|
|||||||||||||||||||||||||||
|
|
|
|
|
|
|
|
|
|
|
|
|
|
|
|
|
|
|
|
|
|
|
|
2 |
|
|
|
|
|
|
|
|
|
S‘ |
2 |
|
|
|
|
|
|
|
|
|
|
|
|
|
|
|
|
|
|
|
|
|
|
|
|
|
|
|
|
|
|
|
|
|
|
|
|
|
|
|
|
|
|
|
|
|
а |
|
|
|
в |
|
|
|
|
|
д |
S“а Sнб
|
1 |
1 |
Рис. 2.5. Приводы ленточных конвейеров: а - схема приводной |
||
станции; б – схема приводного барабана с увеличенным |
||
углом охвата; в |
– схема двухбарабанного |
привода; |
г – схема привода |
с прижимным роликом |
ленты; |
д – схема привода с прижимной лентой
Для снижения растягивающих усилий в ленте применяют установку промежуточных приводов (рис. 2.6). Эпюра натяжения тягового органа в этом случае (рис. 2.6 – пунктирная линия) имеет существенно меньшую амплитуду, чем эпюра натяжений без промежуточных приводов.
|
|
|
|
|
|
|
|
|
|
|
|
|
|
|
|
|
|
|
|
|
|
|
|
|
|
|
|
|
|
|
|
|
|
|
|
|
|
|
|
|
|
|
|
|
|
|
|
|
|
|
|
|
|
|
|
|
|
|
|
|
|
|
|
|
|
|
|
|
|
|
|
|
|
|
|
|
|
|
|
|
|
|
|
|
|
|
|
|
|
|
|
|
|
|
|
|
|
|
|
|
|
|
|
|
|
|
|
|
|
|
|
|
|
|
|
|
|
|
|
|
|
|
|
|
|
|
|
|
|
|
|
|
|
|
|
|
|
|
|
|
|
|
|
|
|
|
|
|
|
|
|
|
|
|
|
|
|
|
|
|
|
|
|
|
|
|
|
|
|
|
|
|
|
|
|
|
|
|
|
|
|
|
|
|
|
|
|
|
|
|
|
|
|
|
|
|
|
|
|
|
|
|
|
|
|
3 |
|
|
|
|
|
|
|
|
|
|
|
|
|
|
|
4 |
||
1 |
2 |
|
|
|
|
|
|
|
|
|
|
|
|
|
|
|
|
|
|
|
|
|
|
|
|
|
|
|
|
|
|
|
|
|
|
|
|
|
|
|
|
|
||||||||||||||||||||||||||||||||
|
|
|
|
|
|
|
|
|
|
|
|
|
|
|
|
|
|
|
|
|
|
|
|
|
|
|
|
|
|
|
|
|
|
|
|
|
|
|
|
|
|
|
|
|
|
|
|
|
|
|
|
|
|
|
|
|
|
|
|
|
|
|
|
|
|
|
|
|
|
|
|
|
|
|
|
|
|
|
|
|
|
|
|
|
|
|
|
|
|
|
|
|
|
|
|
|
|
|
|
|
|
|
|
|
|
|
|
|
|
|
|
|
|
|
|
|
|
|
|
|
|
|
|
|
|
|
|
|
|
|
|
|
|
|
|
|
|
|
|
|
|
|
|
|
|
|
|
|
|
Рис. 2.6. Эпюры натяжений ленты при установке промежуточных приводов
Для уменьшения возможности схода ленты с приводного и натяжного барабанов при небольшой непараллельности их осей барабанам придают бочкообразность со стрелой выпуклости образующих барабанов 3…5 мм. Долговечность ленты существенно зависит от радиуса изгиба ее на барабане. С этой целью принимают оптимальное соотношение диаметра барабана и толщины ленты Dб = (120…150) z, где z – количество слоев кордной ткани в ленте.
Натяжная станция предназначена для создания минимального натяжения ленты, при котором обеспечиваются устойчивое сцепление с тяговым барабаном и необходимая сила тяги для преодоления сопротивлений перемещению
32
ленты. В процессе эксплуатации конвейера натяжное устройство должно компенсировать вытяжку ленты без снижения силы тяги. Конструкции натяжных устройств разнообразны, но все они реализуют два способа устранения ослабления натяжения ленты: периодический и непрерывный. В первом случае используются винтовые, реечные, рычажно-пружинные и др. натяжные устройства. Во втором случае применяются грузовые и автоматические натяжные устройства с электрическим, гидравлическим или пневматическим приводами. Автоматические натяжные устройства могут увеличивать натяжение ленты в 1,3- 1,5 раза на период пуска конвейера для разгона вращающихся масс роликоопор и оптимизировать натяжение при установившемся режиме. Грузовые натяжные устройства обеспечивают постоянство необходимого расчетного натяжения ленты.
Кольцевая транспортирующая лента является наиболее ответственным и дорогостоящим элементом конвейера. Стоимость ленты составляет до 50% стоимости всего конвейера. Ленты подразделяются на резинотканевые, резинотросовые, цельнометаллические и специальные. В строительной индустрии наибольшее распространение получили резинотканевые ленты. Тяговый каркас такой ленты состоит из нескольких слоев ткани специального плетения, соединенных между собой тонкими резиновыми прослойками. Ткань может быть выполнена из хлопчатобумажных или синтетических нитей. С внешних сторон каркас защищен привулканизированными к нему эластичными обкладками. Прочность ленты на разрыв обусловлена прочностью нитей основы (продольных нитей) и числом слоев ткани в каркасе. Число слоев ткани влияет на жесткость и способность ленты образовывать желобчатость на роликоопорах. Жесткая лента будет плохо прилегать к роликам, интенсивно изнашиваться по краям, в местах перегиба наступает ее быстрое расслоение. В зависимости от условий эксплуатации конвейера лента должна обладать прочностью при растяжении и изгибе, малым упругим и остаточным удлинением, высоким сопротивлением абразивному износу, достаточной продольной и поперечной гибкостью, способностью противостоять старению и усталостному изнашиванию. Надежность работы конвейерной ленты в значительной степени зависит от качества соединения ее концов (стыка), которое должно отвечать тем же требованиям, что и сама лента. Стыки лент могут быть разъемными и неразъемными. Неразъемные стыки получают вулканизацией или с помощью заклепок. Разъемные стыки выполняют на петлях, на крючках, на болтах с пластинами.
Загрузочные устройства на конвейере должны обеспечивать его заданную производительность и долговечность ленты. Место загрузки является основным местом износа и повреждения ленты. Для устранения вредного воздействия груза на ленту (рис. 2.7) поток груза направляют сначала на наклонные стенки загрузочного бункера или колосники, которые пропускают мелкие фракции груза, а крупные куски скатываются по ним и гасят свою энергию.
Для снижении энергии удара падающих крупных фракций материала в местах загрузки устанавливают амортизирующие роликоопоры с меньшим шагом, чем рядовые.
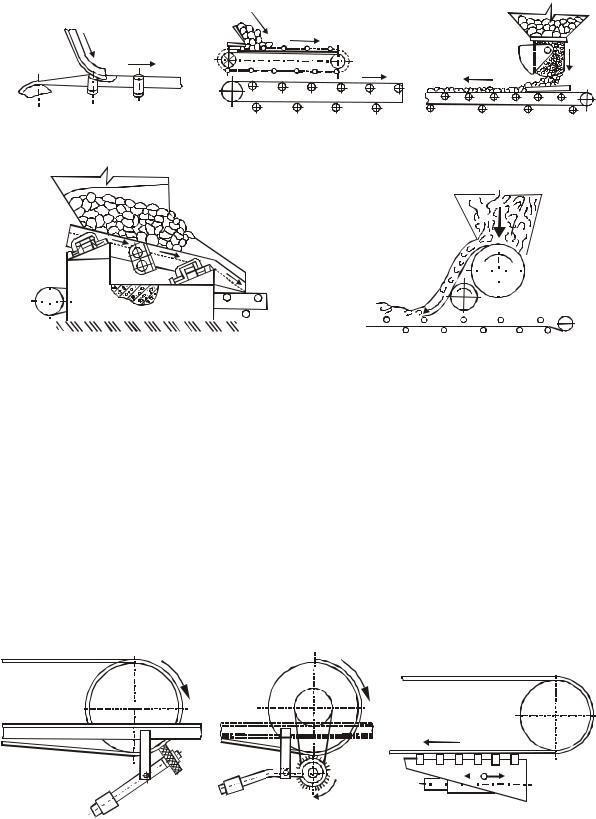
33
|
|
|
а |
|
|
|
|
|
|
б |
|
|
|
|
|
|
|
|
в |
|||||||||||||||||||||||||||||||||||||||||
|
|
|
|
|
|
|
|
|
|
|
|
|
|
|
|
|
|
|
|
|
|
|
|
|
|
|
|
|
|
|
|
|
|
|
|
|
|
|||||||||||||||||||||||
|
|
|
|
|
|
|
|
|
|
|
|
|
|
|
|
|
|
|
|
|
|
|
|
|
|
|
|
|
|
|
|
|
|
|
|
|
|
|
|
|
|
|
|
|
|
|
|
|
|
|
|
|
|
|
|
|
|
|
|
|
|
|
|
|
|
|
|
|
|
|
|
|
|
|
|
|
|
|
|
|
|
|
|
|
|
|
|
|
|
|
|
|
|
|
|
|
|
|
|
|
|
|
|
|
|
|
|
|
|
|
|
|
|
|
|
|
|
|
|
|
|
|
|
|
|
|
|
|
|
|
|
|
|
|
|
|
|
|
|
|
|
|
|
|
|
|
|
|
|
|
|
|
|
|
|
|
|
|
|
|
|
|
|
|
|
|
|
|
|
|
|
|
|
|
|
|
|
|
|
|
|
|
|
|
|
|
|
|
|
|
|
|
|
|
|
|
|
|
|
|
|
|
|
|
|
|
|
|
|
|
|
|
|
|
|
|
|
|
|
|
|
|
|
|
|
|
|
|
|
|
|
|
|
|
|
|
|
|
|
|
|
|
|
|
|
|
|
|
|
|
|
|
|
|
|
|
|
|
|
|
|
|
|
|
|
|
|
|
|
|
|
|
|
|
|
|
|
|
|
|
|
|
|
|
|
|
|
|
|
|
|
|
|
|
|
|
|
|
|
|
|
|
|
|
|
|
|
|
|
|
|
|
|
|
|
|
|
|
|
|
|
|
|
|
|
|
|
|
|
|
|
|
|
|
|
|
|
|
|
|
|
|
|
|
|
|
|
|
|
|
|
|
|
|
|
|
|
|
|
|
|
|
|
|
|
|
|
|
|
|
|
|
|
|
|
|
|
|
|
|
|
|
|
|
|
|
|
|
|
|
|
|
|
|
|
|
|
|
|
|
|
|
|
|
|
|
|
|
|
|
|
|
|
|
|
|
|
|
|
|
|
|
|
|
|
|
|
|
|
|
|
|
|
|
|
|
|
|
|
|
|
|
|
|
|
|
|
|
|
|
|
|
|
|
|
|
|
|
|
|
|
|
|
|
|
|
|
|
|
|
|
|
|
|
|
|
|
|
|
|
|
|
|
|
|
|
|
|
|
|
|
|
|
|
|
|
|
|
|
|
|
|
|
|
|
|
|
|
|
|
|
|
|
|
|
|
|
|
|
|
|
|
|
|
|
|
|
|
|
|
|
|
|
|
|
|
|
|
|
|
|
|
|
|
|
|
|
|
|
|
|
|
|
|
|
|
|
|
|
|
|
|
|
|
|
|
|
|
|
|
|
|
|
|
|
|
|
|
|
|
|
|
|
|
|
|
|
|
|
|
|
|
|
|
|
|
|
|
|
|
|
|
|
|
|
|
|
|
|
|
|
|
|
|
|
|
|
|
|
|
|
|
|
|
|
|
|
|
|
|
|
|
|
|
|
|
|
|
|
|
|
|
|
|
|
|
|
|
|
|
|
|
|
|
|
|
|
|
|
|
|
|
|
|
|
|
|
|
|
|
г |
д |
Рис. 2.7. Схемы загрузочных устройств: а – с наклонным лотком; б – с ленточным питателем; в – с загрузкой из бункера через виброплощадку; г – с вибрационным питателем; д – с барабанным питателем
Устройства очистки ленты предусмотрены для очистки от налипающего на нее материала, создания нормальных условий работы и повышения срока службы ленты конвейера. При плохой очистке ленты нарушается сцепление ее с барабаном, стабильность движения, повышается износ, затрудняется работа конвейера в целом. Очистные устройства (рис. 2.8) можно разделить на следующие типы: скребковые (рис. 2.8,а), щеточные (рис. 2.8,б), винто-лопастные (рис. 2.8,в), вибрационные, гидравлические и пневматические.
|
|
|
|
|
|
|
|
|
|
|
|
|
|
|
|
|
|
|
|
|
|
|
|
|
|
|
|
|
|
|
|
|
|
|
|
|
|
|
|
|
|
|
|
|
|
|
|
|
|
|
|
|
|
|
|
|
|
|
|
|
|
|
|
|
|
|
|
|
|
|
|
|
|
|
|
а |
|
|
|
|
|
|
|
|
|
|
|
|
|
|
в |
|||
б |
|
|
|
|
|
|
|
|
|
Рис. 2.8. Схемы очистных устройств: а – скребкового типа; б – щеточного типа; в – винтолопастного типа
Разгрузочные устройства позволяют принимать поток материала как с концевой ветви конвейера, так и в любой точке трассы. При разгрузке с конце-
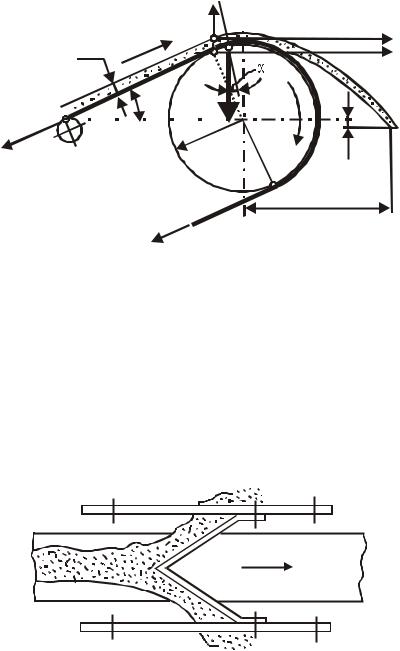
34
вого барабана (рис. 2.9) расположение устройства для приема материала должно учитывать траекторию движения и дальность полета отдельных кусков и струи груза в целом.
Sб н
|
|
|
|
|
|
|
|
|
y |
|
|
|
|
|
|
|
|
|
О1 |
hм |
|
V |
|
|
|
|
О |
||
|
|
|
|
|
|
|
|
|
|
|
|
|
|
|
|
|
|
G |
|
|
|
|
|
|
|
|
|
|
|
|
|
|
|
|
|
|
|
R |
Sсб
x1
x
1 Н
L3
Рис. 2.9. Схема разгрузки с концевого барабана
Промежуточная разгрузка насыпных и штучных грузов может производиться плужковыми сбрасывателями (рис. 2.10). Недостатки плужковых сбрасывателей (увеличение износа ленты, значительные местные сопротивления, ограничение скорости ленты) при их простоте устройства потребовали применения более сложных устройств для промежуточной разгрузки.
Рис. 2.10. Схема разгрузки плужковым сбрасывателем
Таковыми стали самоходные двухбарабанные разгрузочные тележки (рис. 2.11). Тележка перемещается по рельсовому пути на своих ходовых колесах с собственным приводом. При сходе ленты с верхнего барабана груз с нее поступает в приемный бункер, из которого с помощью шибера направляется в правую или левую разгрузочную воронку.
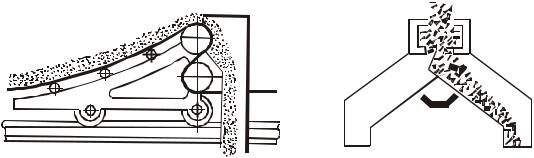
35
Рис. 2.11. Схема двухбарабанной разгрузочной тележки
Остановы применяют для предотвращения самопроизвольного движения ленты загруженного наклонного конвейера при отключении двигателя. Наиболее простую конструкцию имеют ленточные остановы, в которых закрепленная одним концом на раме стопорная лента затягивается самопроизвольно движущейся вниз лентой под барабан и останавливает конвейер. Недостатком такого останова является быстрый износ стопорной ленты. Надежными и долговечными являются храповые и роликовые остановы. Они сложнее по конструкции и требуют дополнительной защиты от загрязнения стопорных элементов.
Определение параметров конвейера производится при проектировании, ремонте или выборе необходимого типоразмера ленточного конвейера из серийно выпускаемых. Обычно требуется для заданной производительности П(т/час) при горизонтальной и вертикальной дальностях перемещения L(м) и Н(м) определенного груза рассчитать и выбрать параметры комплектующих элементов конвейера: ширину ленты Вл, число слоев корда в ленте z, диаметры барабанов D6 и роликоопор Dpo, мощность электродвигателя и частоту вращения вала, передаточное число и типоразмер редуктора. На практике возникает необходимость решать и обратную задачу: по известным параметрам комплектующих элементов конвейера определить его производительность для различных условий работы и вида транспортируемого материала.
Теоретическую производительность горизонтального конвейера П оп-
ределяют как произведение площади поперечного сечения потока материала на ленте Sл (м2) на ее скорость движения Vл (м/с):
П = 3600 Sл Vл |
, |
м3/ч, |
(2.7) |
или |
|
|
|
П = 3600 Sл Vл |
, |
т/ч, |
(2.8) |
где - насыпная плотность материала, т/м3.
При расчете производительности наклонного конвейера необходимо учитывать возможность ее уменьшения за счет некоторого ссыпания материала под уклон в зависимости от степени подвижности материала соответствующим коэффициентом [4].
Площадь сечения потока материала на ленте зависит от ширины лен-
ты Вл, типа роликоопор, угла наклона боковых роликов , угла естественного
36
откоса материала в движении и может быть вычислена по следующим формулам:
однороликовая опора:
|
|
Sл = 0,25 b2 tg , м2 ; |
|
(2.9) |
двухроликовая опора при угле наклона роликов : |
|
|
||
=15° |
|
Sл = b2 (0,062+0,230 tg ), м2 |
, |
(2.10) |
=20° |
|
Sл = b2 (0,125+0,125 tg ), м2 ; |
(2.11) |
трехроликовая опора при угле наклона боковых роликов :
=20° |
|
Sл = b2 |
(0,068+0,223 tg ), м2 , |
(2.12) |
=30° |
|
Sл = b2 |
(0,096+0,214 tg ), м2 , |
(2.13) |
=45° |
|
Sл = b2 (0,13+0,17 tg ), м2 . |
(2.14) |
|
Обозначив числовые коэффициенты и tg через коэффициент ks , полу- |
||||
чим общую формулу площади потока материала на ленте |
|
|||
|
|
S = ks b2, м2 , |
(2.15) |
где коэффициент ks зависит от угла естественного откоса материала в движении, количества и угла наклона роликов в роликоопоре.
Скорость движения ленты выбирается в зависимости от характеристики транспортируемого груза, его плотности и гранулометрического состава, сохранности груза, ширины и долговечности ленты, способа загрузки и разгрузки на ленте, производительности конвейера и условий его эксплуатации. Высокие скорости ленты позволяют обеспечить высокую производительность, уменьшить ширину ленты, при этом снижается линейная нагрузка на конвейер и уменьшается натяжение ленты конвейера. Все это ведет к снижению его стоимости. Но есть и недостатки: при больших скоростях ленты необходимо более высокое качество изготовления роликоопор; движение ленты менее устойчиво; наблюдается более интенсивное просыпание груза; возрастает опасность сбегания ленты с роликоопор; увеличивается износ ленты в местах загрузки; повышается опасность воспламенения ленты при пробуксовке ее на барабане или при трении о неподвижные предметы; может изменяться качество транспортируемого продукта; порошковые и пылевидные грузы могут интенсивно распыляться. Диапазон скоростей ленты при разгрузке через головной барабан, с учетом всего ранее сказанного, составляет 1…8 м/с. Большие значения скоростей лент назначают при транспортировании зернистых и мелкокусковых грузов и ширине лент 2000…3000 мм. Для узких лент (400…650 мм) скорости принимают 1,0…2,5 м/с соответственно.
Ширина ленты определяется по производительности конвейера и должна быть проверена по условию обеспечения минимальной ширины ленты в за-
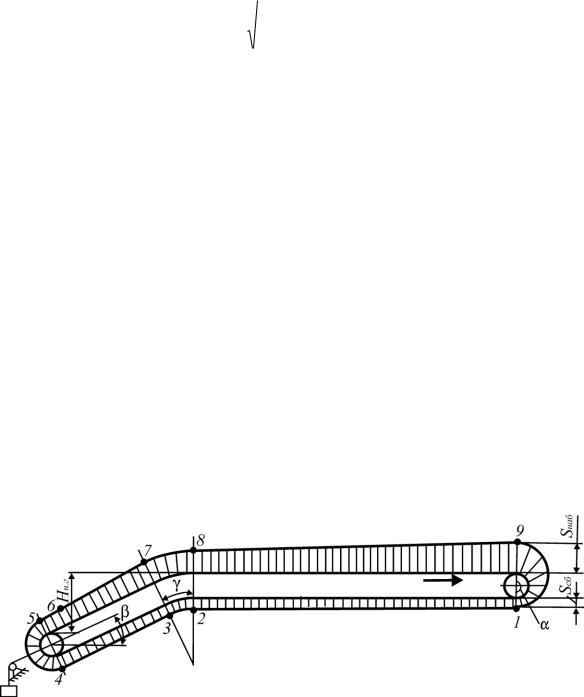
37
висимости от кусковатости груза. Рекомендуется минимальную ширину ленты для рядового груза принимать равной
Вл 2а + 200 , |
мм, |
(2.16) |
а для сортированного |
|
|
Вл 3,3а + 200 |
, мм, |
(2.17) |
где а - размер наибольшего куска.
Расчетная ширина ленты горизонтального конвейера может быть получена по формуле
|
|
|
|
|
|
|
|
|
|
|
|
|
|
|
П |
|
|
|
|
||
В |
л |
1,1 |
|
|
|
0,05 |
|
, мм. |
(2.18) |
|
|
||||||||||
|
|
|
3600 ksVл |
|
|
|
||||
|
|
|
|
|
|
|
|
|
Необходимая прочность ленты при известной ширине достигается за счет числа слоев корда z в ленте и рассчитывается по формуле
z |
Fмах |
n |
|
|
|
|
, |
(2.19) |
|
|
|
|||
|
Вл |
|
где Fmax - максимальное усилие натяжения ленты, Н; n - коэффициент запаса прочности для ленты общего назначения, который принимается равным 8…10; - предел прочности на разрыв 1 см ширины одного слоя корда. Его величина зависит от типа ткани кордного слоя. Так, для ленты БКНЛ – 100 прочность на разрыв = 1 кН/см; для БКНЛ – 150 - = 1,5 кН/см; для ТЛК –
200 - =2 кН/см.
Усилие натяжения ленты по ее периметру различно. Минимальное натяжение ленты будет на сбегающей с ведущего барабана ветви Fmin = Fсб. Величину этого натяжения обычно задают натяжным устройством по условию провисания ленты под действием собственного веса и веса находящегося на ней груза так, чтобы стрела прогиба ленты Ул = 0,03Lнpo (здесь Lнpo - шаг установки рядовых роликоопор). Эпюра натяжения ленты конвейера простой конфигурации показана на рис. 2.12. Изменение величины натяжения ленты при обходе ее по контуру обусловлено различными сопротивлениями, действующими при движении ленты.
Рис. 2.12. Эпюра натяжений ленты конвейера
38
Такими характерными сопротивлениями, создающими в ленте конвейера дополнительное натяжение, называют следующие (начиная от точки минимального натяжения - 1):
-сопротивление от перемещения ленты по роликоопорам на горизонтальном, прямолинейном участке 1 – 2 без груза;
-сопротивление на криволинейном выпуклом участке 2 – 3 без груза;
-сопротивление на наклонном прямолинейном участке 3 – 4 без груза;
-сопротивление на участке 4 – 5 от взаимодействия ленты с натяжным барабаном;
-сопротивление от взаимодействия ленты с грузом в момент загрузки (участок 5 – 6);
-сопротивление от перемещения ленты с грузом на наклонном прямолинейном участке 6 – 7;
-сопротивление на криволинейном участке 7 – 8 при движении ленты с грузом;
-сопротивление на горизонтальном прямолинейном участке 8 – 9 при
движении ленты с грузом.
Прибавляя к минимальному усилию натяжения ленты последовательно усилия сопротивления движению ленты, можно определить усилие натяжения ленты в любой ее точке. Максимальное усилие натяжения ленты (точка 9) Fmax определяет необходимое число слоев корда в ленте.
Условие нормальной работы конвейера предполагает надежную (без проскальзывания) передачу необходимого окружного усилия с барабана приводной станции на ленту. Это условие зависит не только от мощности двигателя, но и от тяговой способности приводного барабана. Требование к приводной станции конвейера состоит в том, чтобы в набегающей на барабан ленте создать усилие Fнб> Кзап· Fmax, где Кзап = 1,3. Способность барабана обеспечить это условие определяется его тяговым фактором:
Т = е , |
(2.20) |
где е - полный тяговый коэффициент приводного барабана, который обеспечивает его способность передавать тяговое усилие ленте без буксования; е - основание натурального логарифма; - коэффициент трения скольжения ленты по барабану; - угол охвата барабана лентой, рад.
При полном использовании силы сцепления между натяжениями в набегающей Fнаб и в сбегающей Fсб ветвях ленты существует зависимость
Fнб = Fсб е , Н. |
(2.21) |
Максимальное тяговое усилие, которое способен передать приводной барабан без пробуксовки ленты при известном натяжении в сбегающей ветви Fcб:
F |
F |
F |
F (е 0 1) |
, Н. |
(2.22) |
0 мах |
нб |
сб |
сб |
|
|
39
Для исключения возможности пробуксовки при всех режимах работы конвейера привод должен иметь коэффициент запаса сцепления kc = 1,3…1,4.
W ≤ Fокр = Fо мах / kс , Н, |
(2.23) |
где Fокр - рекомендуемое тяговое усилие привода, Н; W – сопротивления движению ленты.
Мощность приводного двигателя по допустимому тяговому усилию
рассчитывают по формуле |
|
|
|
Nдв = |
k з FокрVл |
, Вт, |
(2.24) |
|
|||
|
пр |
|
где Vл — скорость ленты, м/с; ηпр — КПД приводной станции; kз — коэффициент запаса установочной мощности, k3 = 1,0…1,2.
Более подробно теоретический материал по ленточным конвейерам изло-
жен в [3, с. 405…435; 4, с. 54…94].
2.5. ВИНТОВЫЕ КОНВЕЙЕРЫ
Винтовыми конвейерами называют машины непрерывного транспорта, в которых перемещение груза осуществляется по желобу шнеком - вращающимся валом, снабженным винтовой поверхностью обычной или специальной конфигурации. Винтовые конвейеры с обычной винтовой поверхностью широко применяются для транспортирования на небольшие расстояния (до 50 м) сыпучих пылевидных, зернистых и мелкокусковых грузов в строительной, химической, пищевой, сельскохозяйственной и других отраслях промышленности. Конвейеры со специальным шнеком могут использоваться для транспортирования тестообразных, вязких материалов на расстояние 5…10 м. В этом случае конвейер при его остановке необходимо освобождать от материала.
Винтовые конвейеры обладают такими положительными свойствами, как простота и надежность конструкции, компактность и возможность загрузки - разгрузки в любой точке трассы, возможность транспортирования экологически опасных грузов путем герметизации желоба, возможность транспортировать грузы по наклонным трассам вплоть до вертикальных, простота в эксплуатации. Эти конвейеры позволяют совмещать некоторые технологические операции (смешивание, дозирование) с перемещением грузов.
Недостатки винтовых конвейеров: повышенный расход энергии вследствие трения транспортируемого груза о желоб и шнек, интенсивный износ рабочих поверхностей конвейера при перемещении абразивных материалов, небольшая дальность транспортирования и сравнительно небольшая производительность. Винтовые конвейеры не рекомендуются для перемещения материа-
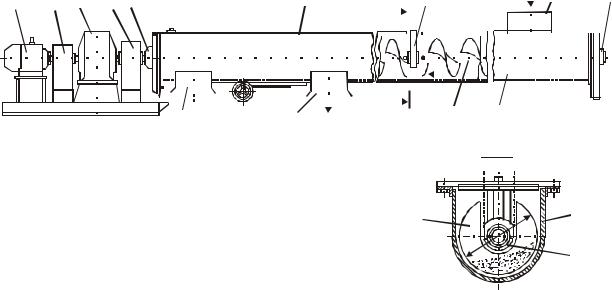
40
лов, которые легко крошатся и теряют при этом свои потребительские свойства.
Классификация винтовых конвейеров представлена в табл. 2.7
Таблица 2.7
Классификация винтовых конвейеров
ПРИЗНАК КЛАССИФИКАЦИИ |
ОПИСАНИЕ ПРИЗНАКА |
|
КЛАССИФИКАЦИИ |
||
|
||
|
Перемещение сыпучих, тестообраз- |
|
По назначению |
ных, опасных грузов |
|
Смешивание, дозирование, сушка |
||
|
||
|
грузов |
|
По виду трассы |
Горизонтальная, наклонная, верти- |
|
кальная |
||
|
||
|
Сплошной, лопастной, ленточный, |
|
По конструкции шнека |
фасонный, спиральный, многозаход- |
|
|
ный |
Устройство винтового конвейера серийного исполнения показано на рис. 2.13. Конвейер состоит из закрытого неподвижного желоба 1, внутри которого на опорах 2, 3, 4 размещен винт (шнек) 5. Шнек приводится во вращение через редуктор 6, муфты 7 и 8 - электродвигателем 9. Загрузка конвейера осуществляется через загрузочную воронку 10, разгрузка – через промежуточную 11 или концевую 12 воронки.
9 |
7 6 8 2 |
|
|
1 |
|
|
|
|
|
|
|
|
|
|
|
|
|
|
|
|
А |
|
3 |
|
|
|
|
|
|
|
10 |
|
|
|
|
|
|
4 |
|||||||||||||||||||||||||||||||||||||||||||||||||||||||||||||||||||||||
|
|
|
|
|
|
|
|
|
|
|
|
|
|
|
|
|
|
|
|
|
|
|
|
|
|
|
|
|
|
|
|
|
|
|
|
|
|
|
|||||||||||||||||||||||||||||||||||||||||||||||||||||||||||||||||||||||
|
|
|
|
|
|
|
|
|
|
|
|
|
|
|
|
|
|
|
|
|
|
|
|
|
|
|
|
|
|
|
|
|
|
|
|
|
|
|
|
|
|
|
|
|
|
|
|
|
|
|
|
|
|
|
|
|
|
|
|
|
|
|
|
|
|
||||||||||||||||||||||||||||||||||||||||||||
|
|
|
|
|
|
|
|
|
|
|
|
|
|
|
|
|
|
|
|
|
|
|
|
|
|
|
|
|
|
|
|
|
|
|
|
|
|
|
|
|
|
|
|
|
|
|
|
|
|
|
|
|
|
|
|
|
|
|
|
|
|
|
|
|
|
|
|
|
|
|
|
|
|
|
|
|
|
|
|
|
|
|
|
|
|
|
|
|
|
|
|
|
|
|
|
|
|
|
|
|
|
|
|
|
|
|
|
|
|
|
|
|
|
|
|
|
|
|
|
|
|
|
|
|
|
|
|
|
|
|
|
|
|
|
|
|
|
|
|
|
|
|
|
|
|
|
|
|
|
|
|
|
|
|
|
|
|
|
|
|
|
|
|
|
|
|
|
|
|
|
|
|
|
|
|
|
|
|
|
|
|
|
|
|
|
|
|
|
|
|
|
|
|
|
|
|
|
|
|
|
|
|
|
|
|
|
|
|
|
|
|
|
|
|
|
|
|
|
|
|
|
|
|
|
|
|
|
|
|
|
|
|
|
|
|
|
|
|
|
|
|
|
|
|
|
|
|
|
|
|
|
|
|
|
|
|
|
|
|
|
|
|
|
|
|
|
|
|
|
|
|
|
|
|
|
|
|
|
|
|
|
|
|
|
|
|
|
|
|
|
|
|
|
|
|
|
|
|
|
|
|
|
|
|
|
|
|
|
|
|
|
|
|
|
|
|
|
|
|
|
|
|
|
|
|
|
|
|
|
|
|
|
|
|
|
|
|
|
|
|
|
|
|
|
|
|
|
|
|
|
|
|
|
|
|
|
|
|
|
|
|
|
|
|
|
|
|
|
|
|
|
|
|
|
|
|
|
|
|
|
|
|
|
|
|
|
|
|
|
|
|
|
|
|
|
|
|
|
|
|
|
|
|
|
|
|
|
|
|
|
|
|
|
|
|
|
|
|
|
|
|
|
|
|
|
|
|
|
|
|
|
|
|
|
|
|
|
|
|
|
|
|
|
|
|
|
|
|
|
|
|
|
|
|
|
|
|
|
|
|
|
|
|
|
|
|
|
|
|
|
|
|
|
|
|
|
|
|
|
|
|
|
|
|
|
|
|
|
|
|
|
|
|
|
|
|
|
|
|
|
|
|
|
|
|
|
|
|
|
|
|
|
|
|
|
|
|
|
|
|
|
|
|
|
|
|
|
|
|
|
|
|
|
|
|
|
|
|
|
|
|
|
|
|
|
|
|
|
|
|
|
|
|
|
|
|
|
|
|
|
|
|
|
|
|
|
|
|
|
|
|
|
|
|
|
|
|
|
|
|
|
|
|
|
|
|
|
|
|
|
|
|
|
|
|
|
|
|
|
|
|
|
|
|
|
|
|
|
|
|
|
|
|
|
|
|
|
|
|
|
|
|
|
|
|
|
|
|
|
|
|
|
|
|
|
|
|
|
|
|
|
|
|
|
|
|
|
|
|
|
|
|
|
|
|
|
|
|
|
|
|
|
|
|
|
|
|
|
|
|
|
|
|
|
|
|
|
|
|
|
|
|
|
|
|
|
|
|
|
|
|
|
|
|
|
|
|
|
|
|
|
|
|
|
|
|
|
|
|
|
|
|
|
|
|
|
|
|
|
|
|
|
|
|
|
|
|
|
|
|
|
|
|
|
|
|
|
|
|
|
|
|
|
|
|
|
|
|
|
|
|
|
|
|
|
|
|
|
|
|
|
|
|
|
|
|
|
|
|
|
|
|
|
|
|
|
|
|
|
|
|
|
|
|
|
|
|
|
|
|
|
|
|
|
|
|
|
|
|
|
|
|
|
|
|
|
|
|
|
|
|
|
|
|
|
|
|
|
|
|
|
|
|
|
|
|
|
|
|
|
|
|
|
|
|
|
|
|
|
|
|
|
|
|
|
|
|
|
|
|
|
|
|
|
|
|
|
|
|
|
|
|
|
|
|
|
|
|
|
|
|
|
|
|
|
|
|
|
|
|
|
|
|
|
|
|
|
|
12 |
11 |
|
А |
5 |
1 |
|
|
|
|
|||||
|
|
|
|||||
|
|
|
|
|
|
|
А-А
5 |
|
1 |
|
ш |
|
|
D |
3 |
|
|
Рис. 2.13. Схема винтового конвейера
Желоб имеет форму полуцилиндра с увеличенными боковыми стенками, закрытого крышкой. Обычно желоб собирается из секций длиной по 2 – 3 м. В местах стыка секций устанавливаются для шнека подвесные опоры 3 с под-