
Методическое пособие 778
.pdfструкции, которые трудно или невозможно получить традиционными методами механической обработки.
Кроме этого, в последние годы наблюдается интеграция EDMоборудования и технологий в аддитивных комплексах и аддитивных процессов
вEDM-технологиях, создаются гибридные системы обработки, включающие как аддитивные, так и традиционные модули обработки заготовок. Последовательная обработка на таких станках происходит без смены технологических баз, что исключает погрешность базирования.
Так, ведущий мировой поставщик компонентов и комплексных решений для индустрии прецизионной обработки GF Machining Solutions (Швейцария) и ведущий мировой поставщик решений в АМ-технологиях и пионер в области 3D-печати 3D Systems (США) объединились для создания гибридной станочной системы, состоящей из трех модулей, сочетающей АМ-технологию производства 3D Systems с прецизионной обработкой GF, в частности, с EDM, и 5 - осевым фрезерным центром с 18-ти инструментальным магазином. В магазин включены не только инструменты для субтрактивной обработки, но и для передовой постобработки с помощью EDM. Система CUT AM 500 компании GF позволяет горизонтально расположенным проволочным электродом с высокой скоростью отделять 3D-напечатанные детали от сборочной платформы. Например, форсунки для впрыска топлива на сборочной платформе устанавливаются
врабочую зону CUT AM500 (рисунок 1), которая автоматически поворачивается на 1800, опускается в ванну и отрезается проволочным электродом. Процесс полностью автоматизирован. Гибридный комплекс позволяет более эффективно изготавливать сложные металлические детали с жесткими допусками и снизить эксплуатационные расходы [5].
Введение двух и более дополнительных воздействий: химических, тепловых, акустических, механических и др. способствовало повышению эффективности процесса эрозии и созданию более 800 комбинированных способов обработки. Однако в промышленности успешно внедрены не более 10-12 комбинированных методов. Большинство исследований и разработок в этой области принадлежит советским и российским ученым и инженерам [6-8].
При электроэрозионной обработке на копировально-прошивных станках до 40% времени от общего времени на технологический процесс изготовления детали уходит на изготовление электрода-инструмента.
При электроэрозионной обработке на копировально-прошивных станках до 40% времени от общего времени на технологический процесс изготовления детали уходит на изготовление электрода-инструмента. Аддитивные технологии позволяют кратно сократить время изготовление прототипов. Вопросы интеграции этих технологий успешно решаются в Воронежском ГТУ [9], ТулГУ [10], Пермском НИПУ [11] и др.
Аддитивные и традиционные технологии имеют вполне очевидные различия, но они часто играют взаимодополняющую роль в жизненном цикле производства изделий. Аддитивные процессы послойного выращивания деталей
70
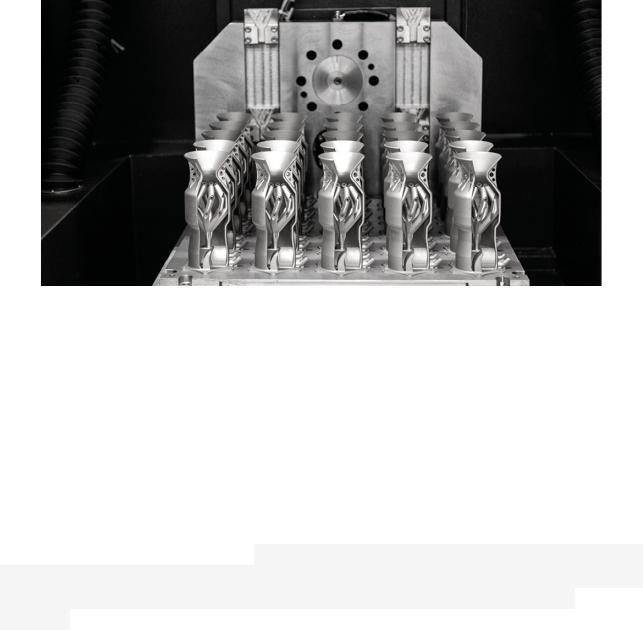
произвели технологическую революцию в создании прототипов и функциональных изделий. Вместе с тем их многие преимущества не «похоронили» субтрактивное производство, которое по-прежнему считается традиционным и более надежным методом для массового производства. Анализ развития технологий EDМ показывает, что эта технология также продолжает совершенствоваться по разным направлениям и вряд ли исчезнет в ближайшие десятилетия.
3D-напечатанные форсунки для впрыска топлива (по [5])
Литература
1.Саушкин Б.П. Обзор состояния и перспектив развития электроэрозионных технологий и оборудования // Металлоообработка. №2 (50). 2009. С. 20-27.
2.The Case For Additive Technology In EDM. Режим доступа: www.makino.com (дата обращения 21.09.2020).
3.Derek Korn. EDM and Additive Manufacturing Similarities. Режим доступа: www.mmsonline.com (дата обращения: 21.09.2020).
4.Степанова Е.Ю. Аддитивные технологии как прорывные инновации ресурсосбережения 21 века. В сб. «Энерго- и ресурсосбережение - XXI век»: Материалы XIII международной научно-практической интернет-конференции. ГУ «Орловский региональный центр Энергосбережения». 2015. С. 124-128.
5.3D Systems, GF Machining Solutions form partnership. Режим доступа: https://www.thefabricator.com/https://www.thefabricator.com/additivereport/news/ad ditive/3d-systems-gf-machining-solutions-form-partnership. (дата обращения: 23.07.2021.
6.Смоленцев В.П., Смоленцев Е.В. Состояние и перспективы развития комбинированных методов обработки // Вестник Рыбинской государственной
71

авиационной технологической академии им. П. А. Соловьева. 2017. № 2 (41). С.
5-9.
7.Смоленцев Е.В. Проектирование электрических и комбинированных методов обработки. М.: Машиностроение, 2005. 511 с.
8.Смоленцев В.П. Инновационные технологии комбинированных методов обработки //Наукоемкие технологии в машиностроении. 2017. №7 (73). С.
15-19.
9.Смоленцев В.П., Кузовкин А.В., Коптев И.Т., Золототрубов Ю.С. Разработка технологического процесса изготовления деталей электродоминструментом на основе цифрового прототипирования // Фундаментальные и прикладные проблемы техники и технологии. 2012. №2-3 (292). С. 74-7
10.Любимов В.В., Саломатников М.С. Электроды-инструменты с двухслойными медными покрытиями на полимерных прототипированных оправках для электрофизико-химического формообразования // Упрочняющие технологии и покрытия. 2015. № 3 (123). С. 30-36.
11.Абляз Т.Р., Шумков А.А. Изготовление сложнопрофильных электро- дов-инструментов с применением технологии быстрого прототипирования //ВЕСТНИК ПНИПУ. 2016. Машиностроение, материаловедение. Т. 18, № 2. С. 160-169. DOI: 10.15593/2222-9877/2016.2.12.
1Воронежский государственный технический университет г. Воронеж, Россия
2Орловский государственный университет им. И.С. Тургенева г. Орел, Россия
21.873.001.891.54
Г.В. Селиверстов, К.С. Коломиец, В.Ю. Анцев, Н.Н. Трушин
МЕТОДИКА ОПРЕДЕЛЕНИЯ ОСТАТОЧНОГО РЕСУРСА МЕТАЛЛОКОНСТРУКЦИЙ ГРУЗОПОДЪЕМНЫХ МАШИН В УСЛОВИЯХ КОРРОЗИОННОЙ УСТАЛОСТИ
В статье представлены результаты исследований процессов воздействия коррозии на элементы металлоконструкций грузоподъемных машин с точки зрения их учета при определении остаточного ресурса в условиях циклического нагружения. Получены модели, определяющие взаимосвязь между глубиной питтинга и величинами теоретической концентрации напряжений и изменения амплитуд напряжений по мере развития коррозии. Получены зависимости для определения остаточного ресурса металлоконструкций грузоподъемных машин в условиях коррозионной усталости
Ключевые слова: усталость, металлоконструкция, питтинг, коррозия, поврежденность, диагностирование, восстановление
72
В современном машиностроительном производстве при реализации производственного процесса важную роль играют грузоподъемные машины (ГПМ), выполняющие погрузочные и разгрузочные работы на складах и в цехах предприятий. Промышленная безопасность при эксплуатации грузоподъемных машин зависит от их технического состояния, а также от комплекса организа- ционно-технических мероприятий, направленных на предотвращение или минимизацию последствий аварий, инцидентов, с учетом индивидуального риска потери жизни и здоровья людей, участвующих в процессах монтажа (демонтажа), наладки, эксплуатации, в том числе ремонта, реконструкции, модернизации и утилизации ГПМ [1].
Наиболее важной и ответственной частью ГПМ является её металлическая конструкция, выполняющая несущую функцию. Наблюдались случаи разрушения ее отдельных элементов, которые приводили к аварийной ситуации. Необходимо отметить, что разрушение может являться следствием целого ряда факторов, из которых можно выделить усталость и влияние атмосферной коррозии. Существующий подход к анализу этих двух факторов обычно определяет независимость их друг от друга, что не совсем верно в современном рассмотрении данного вопроса [2]. Особенно это актуально при эксплуатации грузоподъемной машины, имеющей тяжелый или весьма тяжелый режим работы в условиях агрессивной и сильно агрессивной сред. Примером таких машин являются мостовые краны, эксплуатируемые в сталелитейных цехах. При этом можно отметить, что к коррозионному повреждению склонны не только конструкционные стали, применяемые в несущих металлоконструкциях ГПМ, но и алюминиевые сплавы, используемые в различных конструкциях военнотехнического назначения.
Воздействие коррозии необходимо учитывать тремя факторами: уменьшением несущего сечения элемента; влиянием адсорбционного понижения прочности поверхностного слоя; наличием питтингов. Уменьшение несущего сечения является постепенным процессом окисления поверхностного слоя, что ведет к увеличению действующих напряжений на поврежденный элемент. Адсорбционное понижение прочности наблюдается в поверхностном слое материала, и, с точки зрения статической прочности, существенного влияния не оказывает. Однако, работа конструкции в условиях циклического нагружения может приводить к появлению усталостной поврежденности, а ее накопление и развитие проявляется в первую очередь именно в поверхностном слое. Важным моментом для развития усталости будет условие превышения действующих амплитуд напряжений предела выносливости, который будет зависеть как от характеристик нагружения, так и от величин концентрации напряжений в элементе конструкции.
Питтингообразование, как проявление коррозионного процесса, представляет собой дефекты в виде язв, уходящие вглубь материала. Таким образом, каждый питтинг является локальным концентратором напряжений и местом ве-
73
роятного зарождения усталостной трещины. Для определения величины теоретического коэффициента концентрации напряжений, вызываемого питтингом, были построены конечно-элементные модели с дискретным шагом по глубине дефекта. Моделировался самый распространенный полусферический питтинг. Анализ модели показал, что величина концентрации напряжений меняется от значения 1,6 до значения 2,75. Изменение величины теоретического коэффициента концентрации напряжений ασ при этом предложено описывать математи-
ческой моделью
ασ =0,5ln xотн +2,8, |
(1) |
где xотн – относительная глубина питтинга.
Таким образом, принимая во внимание перечисленные факторы, в функциональной зависимости определения остаточного ресурса необходимо учитывать изменение напряженно-деформированного состояния элемента металлоконструкции для уточнения результатов его расчета на усталость. Изменение действующих амплитуд напряжений σ при заданных значениях агрессивности
среды предложено представлять в виде зависимости |
|
|
|
|
|
|
|||||||||||
|
|
|
|
|
σ=0,0001 N +125,77. |
|
|
|
|
|
(2) |
||||||
Используя полученные модели (1) и (2) можно представить известную |
|||||||||||||||||
формулу |
оценки |
|
|
|
расчета |
ресурса |
|
|
металлоконструкции |
||||||||
lgN = m (lgσRK −lgσ)+lgNБ [3] в виде: |
|
|
|
|
|
|
|
|
|||||||||
|
|
|
|
|
|
|
|
|
285 |
|
|
|
|
|
|
|
|
|
|
|
|
|
|
|
|
|
|
|
|
|
|
|
|
|
|
|
|
|
|
1+ q(0,5ln xотн +1,8) |
|
|
|
||||||||||
|
|
|
|
|
|
|
|
|
|
|
|
||||||
|
|
|
|
lg |
|
|
|
|
|
|
|
|
− |
|
|
|
|
|
lgN |
−6 |
|
0,7 + |
|
0,39 |
|
|
|
−6,301=0, |
(3) |
||||||
|
|
|
|
|
|
|
|
|
|
||||||||
|
|
1 |
+ q(0,5ln x |
+1,8) |
|
||||||||||||
|
|
|
|
|
|
|
|
|
отн |
|
|
|
|
|
|
||
|
|
|
|
|
−lg(0,0001N +125,77) |
|
|
|
|
|
|
|
|
||||
|
|
|
|
|
|
|
|
|
|
|
|
|
где q =1−υσ – коэффициент чувствительности металла к концентрации напряжений (υσ =0,2−0,0001 σВ [4], где σВ – предел прочности материала метал-
локонструкции, МПа). Например, для широко применяемого в металлоконструкциях кранов листового проката из стали 09Г2С σВ = 460 МПа.
Практическое использование предложенного подхода оценки остаточного ресурса металлоконструкций ГПМ предполагает внесение соответствующих изменений в существующую систему их технического обслуживания и ремонта. При этом необходимо уменьшить периодичность проведения диагностических мероприятий в зависимости от глубины имеющихся на металлоконструкции питтингов.
Разработаны алгоритм и реализующее его программное обеспечение, позволяющие определить оптимальные периодичность проведения диагностиче-
ских мероприятий и допустимую относительную глубину питтинга xотн.доп.,
при достижении которой необходимо проводить расчет остаточного ресурса металлоконструкции по зависимости (3) [5]. Данное программное обеспечение
74
было использовано при диагностике мостовых кранов тяжелого и весьма тяжелого режимов работы. При этом были предложены следующие изменения в существующую систему технического обслуживания и ремонта кранов: установить допустимое значение относительной глубины питтинга xотн.доп =0,4; на-
значить периодичность контрольных осмотров до возникновения питтинга – 2 года и 3 месяца; назначить периодичность контрольных осмотров после возникновения питтинга – 1 год и 4 месяца.
Результаты проведенных исследований и методика определения остаточного ресурса металлоконструкций ГПМ позволят повысить промышленную безопасность при эксплуатации грузоподъемных машин, имеющих тяжелый или весьма тяжелый режим работы в условиях агрессивной и сильно агрессивной сред.
Литература
1.Приказ Федеральной службы по экологическому, технологическому и атомному надзору от 26 ноября 2020 г. N 461 "Об утверждении федеральных норм и правил в области промышленной безопасности «Правила безопасности опасных производственных объектов, на которых используются подъемные сооружения».
2.Оценка поврежденности металлоконструкций грузоподъемных машин при совместном действии коррозии и усталости и оптимизация их диагностирования / Г. В. Селиверстов, В. Ю. Анцев, Н. В. Анцева, К. С. Коломиец // Черные металлы. – 2020. – № 3 (1059). – С. 52–57.
3.Гохберг, М. М. Справочник по кранам / М. М. Гохберг. – Т. 1 – Ленинград : Машиностроение, 1988. – 531 с.
4.ГОСТ 25.504–82. Методы расчета характеристик сопротивления усталости: межгосударственный стандарт : издание официальное : утвержден и введен в действие постановлением Государственного комитета СССР по стандартам от 18 мая 1982 г. № 1972 : введен впервые : дата введения 1983-01-07 / разработан Академией наук СССР, Государственным комитетом СССР по стандартам, Министерством высшего и среднего специального образования СССР, Министерством тракторного и сельскохозяйственного машиностроения. – Москва: Издательство стандартов, 1982. – 55 c.
5.Взаимосвязь усталостных и коррозионных процессов при оценке ресурса несущих металлоконструкций грузоподъемных машин / Г. В. Селиверстов, К. С. Коломиец В. Ю. Анцев, Н. В. Анцева // Известия Тульского государственного университета. Технические науки. – 2021. – Вып. 3. – С. 132-137.
Тульский государственный университет
75
УДК 621.9
В.П. Фёдоров, М.Н. Нагоркин, Е.В. Ковалева
ИССЛЕДОВАНИЕ ПРОЦЕССОВ ФОРМИРОВАНИЯ ПАРАМЕТРОВ ИЗНОСОСТОЙКОСТИ ПОВЕРХНОСТЕЙ ДЕТАЛЕЙ
В ТРИБОТЕХНОЛОГИЧЕСКИХ СИСТЕМАХ
Рассматриваются вопросы формирования геометрических параметров качества и параметров износостойкости поверхностей деталей в комбинированных системах обработки, объединяющих процессы лезвийной обработки, модификации поверхностей мягкими приработочными пленками, методы поверхностного пластического деформирования, а также в процессе последующего процесса приработки поверхностей трибоэлементов. Представлены примеры качественной и количественной оценки технологических возможностей исследуемой триботехнологической системы, модели формирования параметров износостойкости и эксплуатационной шероховатости поверхностей деталей
Ключевые слова: износостойкость, антифрикционные технологии, алмазное выглаживание, шероховатость, триботехнические характеристики, параметры процесса приработки, модели формирования, надежность
Эксплуатационные свойства поверхностей деталей машин являются важным компонентом обеспечения надёжности изделий машиностроения в целом за время активного периода их жизненного цикла. Они зависят от точности размеров и параметров качества поверхностного слоя детали – шероховатости, волнистости, макроотклонений, наклёпа и остаточных напряжений и др. Одним из лимитирующих эксплуатационных свойств поверхностей деталей является их износостойкость [1].
Для обеспечения показателей износостойкости широкое практическое применение получили методы антифрикционных технологий на основе использования твёрдых износостойких покрытий и мягких приработочных плёнок, получаемых различными способами. Формирование триботехнических характеристик поверхностей может осуществляться различными методами поверх- ностно-пластического деформирования, что позволяет повысить износостойкость, снизить коэффициент трения и величину начального износа, а также путь
ивремя приработки поверхностей деталей в соединениях трения скольжения.
Впериод приработки деталей трения скольжения происходит изменение параметров микропрофиля контактирующих поверхностей от технологических значений, полученных после обработки, до эксплуатационных, которые будут сохраняться на протяжении нормального цикла работы трибосопряжения.
Таким образом, при разработке технологических процессов изготовления деталей соединений трения скольжения требуется учитывать большое количество факторов, влияющих на формирование параметров износостойкости, начиная с этапов подготовки поверхностей под нанесение износостойких покрытий или пленок и после окончания процессов приработки соединений.
76
Множество вариантов комбинирования последовательности методов обработки для создания технологических процессов формирования параметров износостойкости определяет задачи выбора оптимальных технологий по критериям параметрической надежности технологических систем с учетом технологической наследственности [2].
Проводились исследования технологических систем (ТС) формирования параметров качества поверхностного слоя (ПКПС) и параметров эксплуатационных свойств (ПЭС) поверхностей деталей соединений трения-скольжения на основе комбинирования лезвийных, антифрикционных и упрочняющих технологий с учетом процессов приработки деталей соединений. Такой подход является эффективным при формировании эксплуатационных характеристик опорных шеек валов под подшипники скольжения [2, 3 и др.].
Для обработки поверхностей валов (стали 45 HRC 48…50) предложено применение комбинированных технологий на основе чистовой лезвийной (или абразивной) обработки инструментами, оснащёнными синтетическими сверхтвердыми материалами, модификации поверхностей мягкими приработочными плёнками и финишной обработки методами поверхностного пластического деформирования [2, 3 и др.].
В качестве одного из альтернативных вариантов рассматривается ТС обработки валов, включающая три последовательных этапа обработки:
1)чистовое точение поверхности детали, обеспечивающее требуемые значения параметров профиля шероховатости для последующего гарантированного нанесения материалов мягких приработочных плёнок;
2)нанесение на поверхности деталей материалов для получения мягкой приработочной плёнки: а) финишной антифрикционной безабразивной обработкой фрикционным латунированием (меднением и др.); б) химическим способом, включающим нанесение на поверхность химических растворов, вызывающих осаждение на ней плёнки мягкого вещества, например, меди;
3 – алмазное выглаживание поверхности вала, позволяющее сформировать микропрофиль, обеспечивающий, в свою очередь, требуемые показатели износостойкости [2, 3 и др.].
Чистовое точение осуществлялось на токарном станке стандартными резцовыми вставками из композита 10 при следующих режимах: скорость резания
VТ = 65…200 м/мин; подача инструмента SТ = 0,05…0,15 мм/об; глубина резания t = 0,1…0,25 мм; жёсткость технологической системы j = 2,5…16,2 кН/мм.
В процессе фрикционного латунирования в зоне контакта латунного стержня с поверхностью обработки создавалось давление 30 МПа. Подача инструмента составляла 0,05 мм/об, скорость обработки – 20 м/мин. Химическое меднение поверхности осуществлялась нанесением на обезжиренную поверхность образца раствора хлорной меди в смеси 70%-ной уксусной кислоты с глицерином.
Алмазное выглаживание (АВ) осуществлялось инструментом упругого действия с индентором, оснащённым алмазом синтетическим поликристалли-
77
ческим. Режимы АВ: сила выглаживания QАВ = 100…300 Н; скорость VАВ = 65…100 м/мин; подача инструмента SАВ = 0,075…0,15 мм/об. Радиус индентора r = 3,5 мм. Выглаживание проводилось при наличии смазки «И-20».
Требовалось установить взаимосвязь триботехнических параметров поверхностей деталей с управляющими технологическими факторами комбинированной антифрикционной обработки, к которым относятся режимы точения композитом 10 V, S, t; жёсткость j ТС; вид материала мягкой приработочной
пленки Мп; режимы АВ QАВ, VАВ, SАВ.
В качестве факторов, определяющих процессы износа поверхностей деталей в соединениях трения скольжения, исследовались скорость относительного скольжения поверхностей трибоэлементов Vс = 10…50 м/мин; величина номинальной погонной нагрузки на трибосопряжение в процессе приработки P = 30…50 Н/мм; интервал изменения значения номинальной погонной нагрузки на трибосопряжение в процессе приработки при моделировании динамических условий эксплуатации ∆P = ± (15…25) %; материал вкладыша соединения Mвкл – антифрикционный чугун АЧС-1 или бронза БрОЦС 5-5-5 [2, 3 и др.].
Исследование эксплуатационных свойств поверхностей деталей осуществлялось на компьютеризированном стенде для триботехнических испытаний пар трения-скольжения при изменяющихся нагрузках [2].
Измерение параметров качества поверхностного слоя осуществлялось компьютеризированными измерительными системами, разработанными на основе оригинальных блоков аппаратно-программного интерфейса [3].
Таким образом, в исследуемой триботехнической системе учитывались двенадцать управляющих факторов. Матрица планирования в виде регулярной дробной реплики типа 212–8 представляла собой комплексный план исследований триботехнологической системы по схеме активного эксперимента, включающего факторы комбинированной антифрикционной обработки и факторы процесса приработки.
По результатам экспериментов требовалось построить модели формирования следующих характеристик: f1, f0 – коэффициентов трения в начале и в конце приработки; h01, h02 – величин начального износа поверхностей вала и вкладыша, мкм; L01, L02 – величин пути приработки для вала и вкладыша, м; I1, I0 – значений интенсивности изнашивания поверхностей вала и вкладыша.
Оценивалась степень влияния технологических факторов обработки на формирование эксплуатационных показателей поверхностей деталей соединений трения скольжения, работающих в установившемся режиме.
Анализировался процесс изменения коэффициента трения f в процессе приработки (рис. 1). При дозированной подаче смазки в зону трения (т. 6, 7, 8, 9) наблюдалось кратковременное увеличение значения коэффициента f. Через некоторое время значение f уменьшалось. При изменении нагрузки с постоянной на пульсирующую (t = 16…17 мин.) картина не меняется.
78
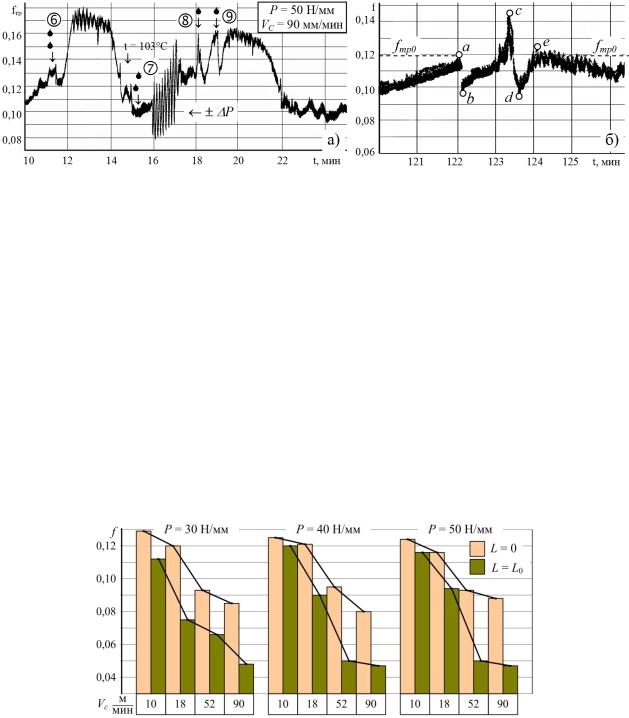
Рис. 1. Изменение коэффициента трения f при дозированной подаче смазки в зону контакта поверхностей (а) и без вмешательства в процесс приработки (б)
Установлено возникновение бифуркаций на стадии завершения приработки без внешнего вмешательства в работу трибосистемы – разрывных недифференцируемых скачков коэффициента трения (участок а – b, рис. 1б) и резкого его повышения с дальнейшим спадом и стабилизацией (b – c – d – e, рис. 1б). Участок (участок а – e) по времени длился около 2 мин, а путь трения для вкладыша составил 180 м.
Результаты экспериментов показывают (рис. 2), что коэффициент трения f снижается с ростом скорости Vc относительного скольжения. До конца приработки он снижается, при этом интенсивность снижения его значения увеличивается к концу приработки. Например, при нагрузке P = 50 Н/мм на поверхность для скорости Vc = 10 м/мин коэффициент трения снижается в 1,07 раза, а для скорости Vc = 90 м/мин он снижается в 1,83 раза.
Рис. 2. Величина коэффициента трения f при изменении скорости Vc относительного скольжения для различных величин нагрузки P на сопряжение в начале (L = 0) и в конце (L = L0) процесса приработки [2]
На рис. 3 представлены графики зависимости линейного износа h01 поверхностей валов и коэффициента трения f от длины пути трения L01 для различных условий проведения экспериментов. Здесь же указаны границы для 80 % доверительных интервалов. На микрофотографиях поверхностей валов до и после приработки по цветовым оттенкам видно, что мягкая приработочная
79