
Учебное пособие 800481
.pdfли при освещении литой детали параллельными лучами в направлении, перпендикулярном к плоскости разъема формы, появляются теневые участки, это свидетельствует о несовершенстве ее конструкции. Такую конструкцию необходимо пересмотреть, в противном случае трудоемкость ее изготовления значительно увеличится за счет необходимости применения формы с отъемными частями.
Наиболее существенное влияние на массу детали оказывает толщина стенок, ребер, фланцев и других конструктивных элементов.
Однако уменьшение толщины конструктивных элементов отливки допустимо только в определенных пределах, ограниченных условиями прочности, литейными свойствами сплавов и возможностями выбранного способа литья. Практикой установлены оптимальные значения толщины стенок, ребер и других конструктивных элементов отливок в зависимости от литейных свойств сплавов, средней массы отливки и характера производства. В литературе даны конкретные рекомендации для определения толщины стенок литых деталей, которые в основном сводятся к следующему.
Толщину стенок литых деталей определяют в зависимости от механических и технологических свойств сплава, конфигурации и габаритных размеров детали, способа ее получения. Правильно выбранная толщина стенок обеспечивает необходимые жесткость, герметичность и является одним из важнейших условий получения годных отливок с высоким коэффициентом использования металла. Чрезмерно толстые стенки увеличивают массу детали, вызывают появление усадочной рыхлости и пористости, снижают прочность изделий. Очень тонкие стенки при литье получить практически невозможно из-за большого брака по незаполнению формы, трещинам и прочим дефектам.
При конструировании литых деталей необходимо стремиться по возможности к одинаковой толщине стенок по всему сечению, избегать локального скопления металла, так называемых горячих мест или термических узлов. Термический
81
узел — место локального скопления металла, которое дольше остается горячим, дольше затвердевает и где больше вероятность образования усадочных рыхлости и раковин.
Наименьшую толщину стенки литых деталей можно определить в зависимости от сплава по графикам (рис. 2.8). Для деталей прямоугольной формы приведенный габаритный размер N определяется по формуле
N = (2L + B + H)/4
где L, В и Н — соответственно длина, ширина, высота детали. Для стальных и чугунных литых деталей при N 8 тол-
щину стенок принимают соответственно 40 и 30 мм. Для медных и алюминиевых сплавов с приведенным габаритным размером N 0,1 минимальную толщину стенок можно принять: 4 мм для безоловянных сплавов; 2,5 мм для оловянных сплавов; до 2 мм для алюминиевых сплавов.
Толщина стенок чугунных литых деталей, габаритные размеры которых меньше 0,5 м, может быть принята 1,5…2,0 мм, стальных — 4…5 мм. Учитывая более низкую жидкотекучесть высокопрочного и модифицированного чугунов, толщину стенок литых деталей из них следует увеличивать на 15…20 % по сравнению с серыми чугунами. Толщину внутренних стенок принимают равной: для чугунных и алюминиевых отливок на 10…20 % меньше толщины наружных, для стальных — на 20…30 %, для медных сплавов - на 15…20 %. Толщину стенок литых деталей из легированных сталей принимают на 20…30 % меньше, чем однотипных деталей из углеродистых сталей.
Толщину краев стенок крупногабаритных литых деталей рекомендуется увеличивать для выравнивания температуры по сечению при охлаждении и уменьшения остаточных напряжений.
Прочность следует повышать не за счет увеличения толщины стенок, а приданием стенкам коробчатого, U- образного или ребристого профиля, что упрощает литейную
82
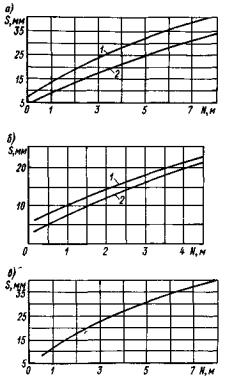
технологию и снижает соответственно себестоимость отливки.
Рис. 2.8. Графики для определения толщины стенок отливок: а - из углеродистых сталей (1), чугуна (2);
б- из медных безоловянных сплавов (1), оловянных сплавов (2); в - из алюминиевых сплавов
Кбраку может привести значительная разница в толщинах сопрягаемых стенок.
В литых деталях со стенками разной толщины, с резкими и неправильно выполненными переходами между сечениями, с большими скоплениями металла возникают значи-
83
тельные внутренние напряжения, приводящие к короблению и трещинам, усадочным раковинам и пористости.
Очень важно при конструировании литой детали осуществить правильное сопряжение стенок отливки. Отливка должна иметь (по возможности) плавно изменяющуюся толщину стенки, ибо в местах резкого их утолщения могут возникать дефекты усадочного характера (пористость, трещины, усадочные раковины). Сопряжения стенок различной толщины выполняются плавными переходами, при этом толщины стенок не должны отличаться более чем в 4 раза. Если сопрягаемые стенки отличаются по толщине менее чем в 2 раза, то переход между ними выполняют в виде галтели с определенным радиусом. Сопряжение же стенок с толщинами, отличающимися друг от друга более чем в 2 раза, выполняют в виде клина с галтелями.
Радиусы галтелей в отливках при литье в песчаные и оболочковые формы, а также в формы, изготовленные по выплавляемым моделям, выполняют равными примерно половине толщины сопрягаемых стенок (при небольшой их толщине), но не менее 1…2 мм; при литье в кокиль — равными полусумме толщин; при литье под давлением — 1/3 суммы толщин сопрягаемых стенок.
Требования к пересечениям ребер жесткости и стенок отливок. Необходимые для упрочнения конструкции ребра жесткости вызывают местные скопления металла, приводящие к образованию усадочных дефектов. Разгрузку узлов скопления металла в данном случае осуществляют применением различного типа сопряжении, в том числе шахматного и кольцевого пересечений ребер.
Выполнение пазов, полостей, отверстий. Направленное затвердевание отливок исключает возможность образования усадочных раковин и пористости. Этот процесс реализуется, если отливки конструируют с учетом правила вписанных окружностей. Предупредить образование усадочных раковин изза местного скопления металла можно также путем выравнивания толщин стенок, формирования в отливках специ-
84
альных полостей, пазов, отверстий. Допускаемые размеры отверстий, получаемых в отливке, определяются типом отверстий (сквозное или глухое), составом сплава и способом литья. Минимальный диаметр литого отверстия d возрастает с увеличением его глубины h.
Окантовки (буртики), перемычки, выступы, бобышки выполняются по краям окон и отверстий для их усиления и исключения появления в отливках трещин. Ширина перемычек между окнами зависит от размеров отливок.
Форма отверстий в отливках (наличие скругленных кромок, бобышек) существенно влияет на их прочность.
Уклоны (конусность) на отливках необходимы для облегчения съема полуформ. Их задают в градусах, миллиметрах или процентах от толщины вертикальной стенки отливки.
Правильный выбор состава литейного сплава, режимов и метода литья приводит к увеличению точности отливки, а также повышению ее механических и специальных свойств.
2.4.13. Выбор способов литья
Разработка процесса изготовления отливки начинается с анализа технологичности конструкции детали. При выборе способа изготовления отливки определяющими факторами являются как технические требования, предъявляемые к изделию, так и технико-экономические показатели (КИМ, себестоимость детали в изготовлении, экономически оправданная серийность и др.), учитывающие расход металла, стоимость оборудования и технологической оснастки. Важную роль при выборе способа литья играет серийность производства. В единичном, мелкосерийном и серийном производствах отливки часто изготавливаются литьем в песчаные формы, по выплавляемым моделям. В крупносерийном и массовом производствах применяют литье под давлением, в кокиль, в оболочковые формы, центробежное литье, литье в сырые песчаные формы, изготавливаемые на формовочных машинах или автоматических линиях, и др.
85
Выбор способа литья проводится в зависимости от требований к отливкам (габариты отливок, точность их размеров, чистота поверхности), а также возможностей способа литья (серийность производства, коэффициент использования металла, процент выхода годных изделий, себестоимость процесса литья). При выборе способа литья надо обязательно учитывать его возможности по обеспечению нужной конфигурации отливки, требуемого качества структуры металла и уровня механических и специальных эксплуатационных свойств. Важно, чтобы способ литья мог обеспечить качественное литье из выбранного конструктором сплава, а также проведения (если есть необходимость) последующей термической обработки отливок.
Трудность выбора способа литья вызвана тем, что нередко отливка может быть изготовлена сразу несколькими способами, которые обеспечивают требуемые свойства литой детали. В этом случае решающими факторами, обусловливающими выбор рационального способа литья, являются серийность производства и экономичность процесса. Эти факторы, наряду с техническими характеристиками способа литья, могут помочь правильно выбрать технологический процесс литья.
3. ОБРАБОТКА МЕТАЛЛОВ ДАВЛЕНИЕМ
Формообразование обработкой давлением основано на способности заготовок из металлов и других материалов изменять свою форму без разрушения под действием внешних сил. Обработка давлением — один из прогрессивных, экономичных и высокопроизводительных способов производства заготовок в машино- и приборостроении. Почти 90% всей выплавляемой стали и 60% цветных металлов и сплавов подвергают тем или иным способам обработки давлением — прокатке, прессованию, волочению, ковке, объемной или листовой штамповке.
86
3.1. Понятие о механизме пластического деформирования при обработке давлением
Обработкой давлением могут быть получены заготовки или детали из материалов, обладающих пластичностью, т. е. способностью необратимо деформироваться без разрушения под действием внешних сил.
Установлено, что в монокристаллах пластическая деформация происходит под действием касательных напряжений, вызывающих скольжение атомарных плоскостей друг относительно друга — явление сдвига. Плоскости скольжения характеризуются наиболее плотной упаковкой атомов в направлениях, по которым межатомные расстояния минимальны. Поэтому сдвиг атомов в этих плоскостях приводит к минимальным нарушениям правильности их расположения, а, следовательно, смещение может быть осуществлено при наименьших напряжениях. Чем больше таких плоскостей в кристаллитах, тем более пластичен металл. Одной из главных причин, определяющих плоскости скольжения, является наличие в них дислокаций. Перемещаясь под действием сил вдоль плоскости скольжения последовательно за счет единичных перемещений атомов, дислокации способствуют снижению напряжений, при которых начинается процесс пластического деформирования, и, кроме того, существенно увеличивают пластичность металла. После окончания процесса скольжения по одной или нескольким плоскостям, что означает, как правило, выход дислокации, расположенных в этих плоскостях, за границу кристаллита, начинается процесс скольжения в других плоскостях, где сопротивление было более высоким. Усилие деформирования будет возрастать по мере включения в процесс скольжения новых плоскостей со все более высоким уровнем сопротивления движению дислокации.
Таким образом, механизм пластического деформирования скольжением при обработке давлением можно предста-
87
вить как лавинообразный процесс движения дислокации вдоль плоскостей скольжения под влиянием сдвиговых напряжений.
Другой механизм пластической деформации — двойникование, или двойниковый сдвиг — чаще всего встречается в металлах и сплавах, имеющих гексагональную или объемноцентрированную кубическую решетку. В отличие от обычного сдвига двойниковый совершается только раз и не приводит к значительным пластическим деформациям. Однако вместе с ним появляются дополнительные очаги сдвиговой деформации по механизму обычного скольжения.
Именно возможностью сочетания двойникования и сдвига объясняется высокая пластичность меди, аустенита, серебра, α-латуни, цинка, магния и др.
Процессы, происходящие при деформировании поликристаллических тел, в которых кристаллиты разделены границами и имеют плоскости скольжения, различно ориентированные в пространстве, значительно более сложны, так как в поликристаллическом теле деформация одного, отдельно взятого зерна практически невозможна. Любое перемещение атомов в результате скольжения или двойникования обязательно вызывает соответствующие групповые перемещения по границам зерен или в самих соседних зернах.
Механизм деформирования поликристаллического тела при обработке давлением можно представить в такой последовательности. Вначале под действием приложенных сил начинается сдвиговая пластическая деформация в зернах, плоскости скольжения которых совпадают или близки вектору максимальных касательных напряжений (рис. 3.1, а), а также по плоскостям, плотность дислокации в которых максимальна. Затем последовательно в процесс включаются плоскости, сопротивление сдвигу которых более высокое. Одновременно происходит смещение и поворот соседних зерен, т. е. переориентация их в пространстве и по отношению к действующим силам (рис. 3.1, б). Зерна, переориентированные в положения, благоприятные для деформирования, включаются в этот процесс, вызывая поворот других, соседних с ними зерен, и т. д.
88
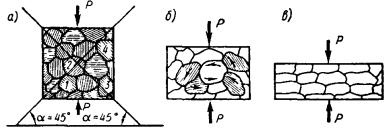
Рис. 3.1. Схема развития пластической деформации поликристалла: а — деформация зерен 1, 2, 3, 4, плоскости скольжения которых ориентированы под углом 45° к направлению усилия; б — поворот
и скольжение новых зерен в положение, благоприятное для деформирования; в — зерна, вытянутые в направлении интенсивного течения металла
Одновременно со сдвигом протекают и процессы двойникования. В результате структура металла, подвергнутого значительным пластическим деформациям, характеризуется вытянутыми зернами, ориентированными в направлении интенсивного течения металла (рис. 3.1, в).
При обработке металла давлением различают деформацию внутрикристаллитную, т. е. протекающую внутри зерна, и межкристаллитную, протекающую по границам зерен. Межкристаллитная деформация (рис. 3.1, б) осуществляется путем взаимного поворота и перемещения скольжением одних зерен относительно других.
В процессе обработки металлов давлением оба вида деформаций протекают одновременно. Однако какой из видов деформации является преобладающим, определяется соотношением прочности зерен и их границ при данном состоянии металла или сплава.
При холодной обработке давлением, осуществляемой обычно при комнатной температуре, преобладает внутрикристаллитная деформация, а при горячей обработке — межкристаллитная. Объясняется это тем, что металл в нагретом со-
89
стоянии имеет зерна более прочные и менее пластичные, чем их границы.
3.2. Нагрев металла для обработки давлением
Металлы и сплавы перед обработкой давлением нагревают до определенной температуры для повышения их пластичности и уменьшения сопротивления деформации. Эту температуру называют температурой начала горячей обработки давлением. Однако в процессе обработки температура металла понижается. Минимальная температура, при которой можно производить обработку, называется температурой окончания обработки давлением. Область температур между началом и окончанием обработки, в которой металл или сплав обладает наилучшей пластичностью, наименьшей склонностью к росту зерна и минимальным сопротивлением деформации, называют температурным интервалом горячей обработки давлением.
Температурный интервал обработки давлением выбирают с учетом диаграммы состояния сплава. Желательно, чтобы в этом температурном интервале металл находился в однофазном состоянии. В двухили многофазном состоянии при низкой пластичности одной из фаз возможно разрушение металла. Исключение представляют доэвтектоидные стали (рис. 3.2), которые при температурах двухфазного состояния между линиями GS и PS обладают достаточной пластичностью. Достаточную пластичность имеют и заэвтектоидные стали выше 750 °С, в которых между линиями ES и SK фиксируется двухфазная структура из аустенита со вторичным цементитом.
Цементит располагается в виде сетки по границам зерен и снижает пластичность стали. Однако после разрушения этой сетки методом обработки давлением сталь восстанавливает свои пластические свойства.
Температурный интервал обработки сплавов зависит от их химического состава. Так из диаграммы железо-углерод видно, что с увеличением количества углерода в стали темпе-
90