
Учебное пособие 800508
.pdf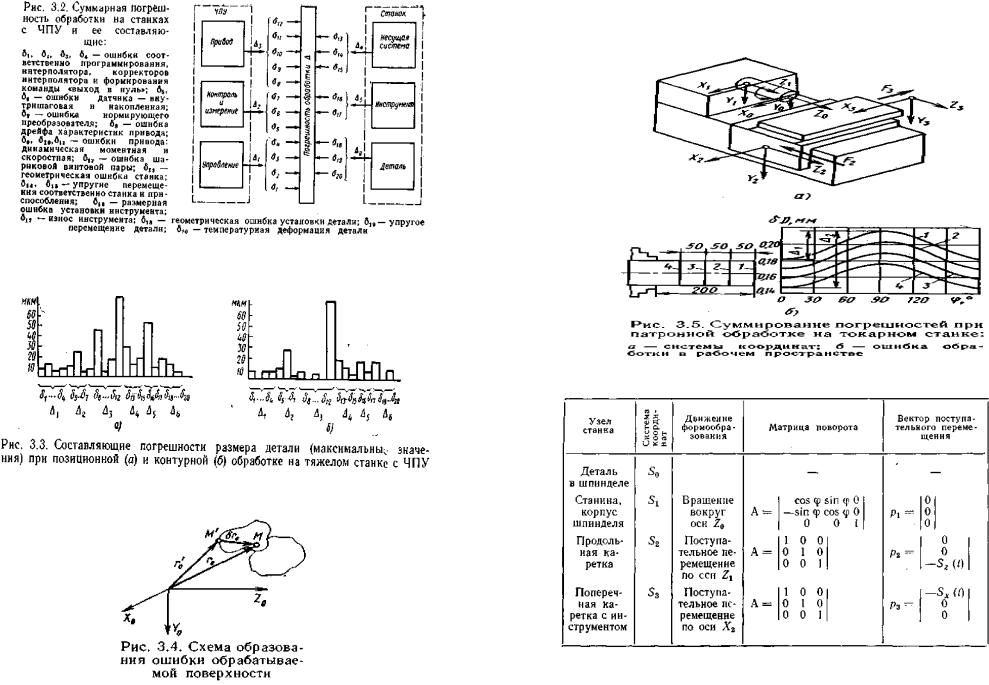
Системы координат узлов токарного станка Таблица 3.1
.
42
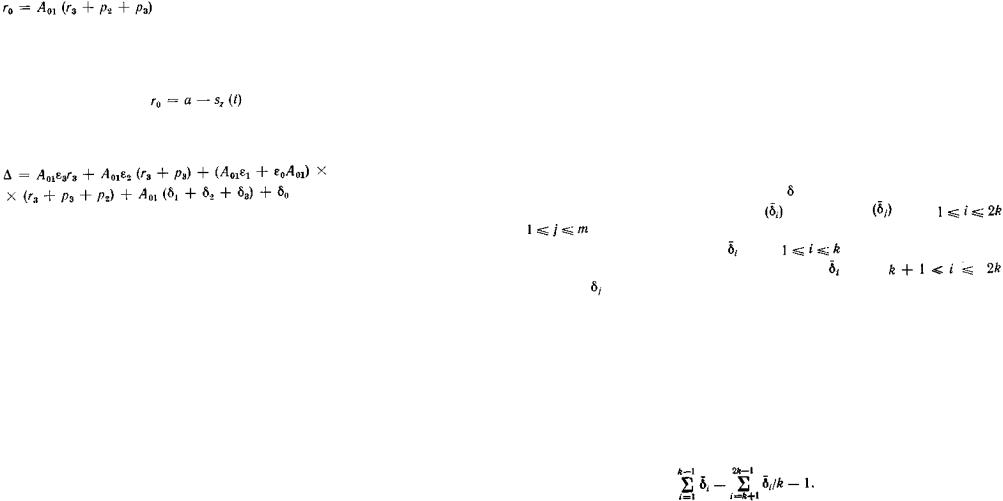
Применение изложенного метода суммированияпогрешностей поясняется примером токарного станка для патронной обработки (рис. 3.5, а). Закрепленная в шпинделе деталь характеризуется системой координат , а остальные узлы — системами координат, приведенными в табл. 3.1. При этом формула (3.2) для текущего значения вектора фактически обрабатываемой поверхности на токарном станке принимает вид
где— радиус-вектор формообразующей точки кромки режущего инструмента в системе координат
.
Для конкретного случая продольного обтачивания цилиндра диаметром D с продольной подачей
где а — координата правого торца по оси Z.
При этом текущее значение погрешности обработки
Выражение (3.3) может быть использовано для вероятностной оценки точности станка. В этом случае математическое ожидание и дисперсию ошибки определяют через математическое ожидание и дисперсию составляющих погрешностей по формулам для линейных функций от случайных величин. получается из формулы (3.3) при подстановке значений матриц, сведенных в табл. 3.2.
Результаты аналитического расчета суммарной погрешности при чистовой обработке в патроне цилиндрической детали диаметром 200 мм на станке нормальной точности приведены на рис. 3.5, б.
В станках с ЧПУ особую роль играет точность позиционирования, которая характеризуется ошибкой выхода в заданную координату. При одновременном проявлении систематических и случайных погрешностей точность позиционирования можно условно определять следующими частными показателями: 1) зоной рассеяния случайных ошибок положения подвижного узла при его подводе к заданной координатной точке с заданного направления (стабильность позиционирования); 2)
систематической составляющей перемещения подвижного узла из одной точки в другую при движении в заданном направлении (ошибка перемещения); 3) систематической разностью ошибок положения при подводе подвижного узла к заданной точке с разных сторон (зона нечувствительности); 4) изменение положения подвижного узла в систематическим изменением течение заданного периода времени (погрешность размерной настройки).
Точность позиционирования как важнейшая характеристика станка с ЧПУ часто снимается экспериментально и включается в его паспорт (рис. 3.6). Существуют различные методы экспериментальной проверкиточности позиционирования. В частности, указанные выше четыре показателя
— стабильность позиционирования, ошибка перемещения, зон нечувствительности и погрешность настройки могут быть получены по результатам одной серии испытаний. При этом произвольно выбранный пути перемещения по координате разбивают на k интервалов и перемещают подвижной узел по управляющей программе на основе случайной функции в каждую из k точек сначала в одном направлении, а затем в противоположном. Каждое испытание повторяютm раз, получая
таким образом 2km значений ошибки |
положения. Результаты можно |
||||||
свести в |
матрицу со столбцами |
и строками |
, где |
, |
|||
|
. Систематическая ошибка перемещения при прямом ходе |
||||||
характеризуется значениями |
при |
|
, а эта же ошибка при |
||||
обратном |
ходе |
определяется |
значениями |
при |
. |
||
Значения |
характеризуют изменение настройки во времени. |
|
|||||
Стабильность |
позиционирования |
и |
зону |
нечувствительности |
получают на основе допущения о том, что во всем рабочем пространстве их математическое ожидание не меняется. Стабильность позиционирования соответствует усредненным результатам по всем столбцам матрицы.
Закон распределения обычно близок к нормальному закону распределения, ограничивая поэтому поле рассеяния значением ; зону нечувствительности получаем в виде
43
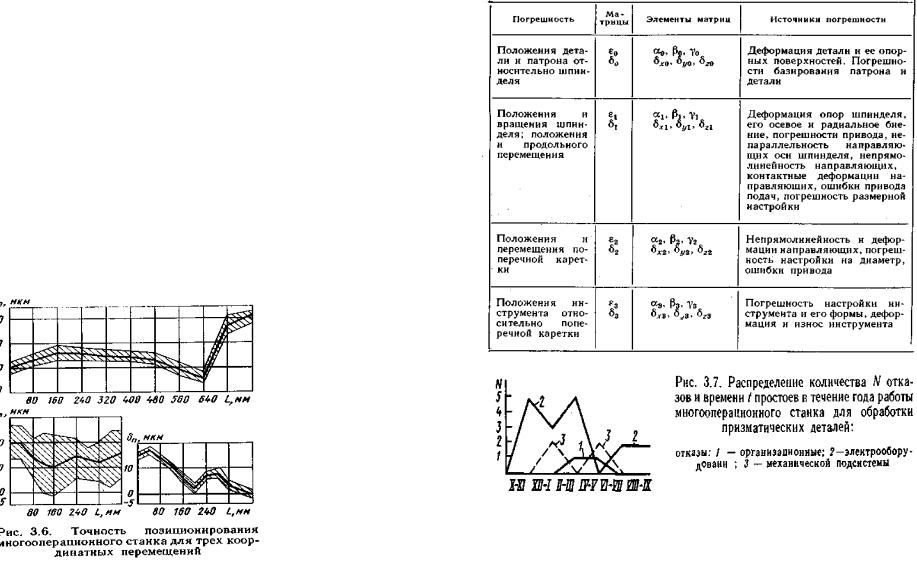
Известные для данного числа характеристики точности позиционирования могут быть учтены и скорректированы при составлении управляющей программы. Следует при этом иметь в виду взаимное влияние погрешностей. Так, геометрические ошибки станка существенно
влияют |
на |
фактическую |
точность |
позиционирования. |
Н а д е ж н о с т ь |
станков, работающих в |
общей автоматической |
системе, имеет особо важное значение. Эксплуатационная надежность, связанная с отказами различного характера, влияет на производительность и на экономическую эффективность системы.
Отказы деталей и механизмов станка имеют разнообразный характер, и для их описания принимают обычно трехпараметричеcкое распределение Вейбулла: , или иначе,
, где а, Ь, с, г =
— постоянные параметры распределения. Иногда в целях упрощения обработки экспериментальных данных принимают двухпараметрическое распределение Вейбулла, полагая
. В качестве примера на рис. 3.8 приве дены данные о надежности автоматической станочной системы для обработки призматических деталей, состоящей из четырех многооперационных станков.
.
Погрешности обработки
Т а б л и ц а 3.2
44
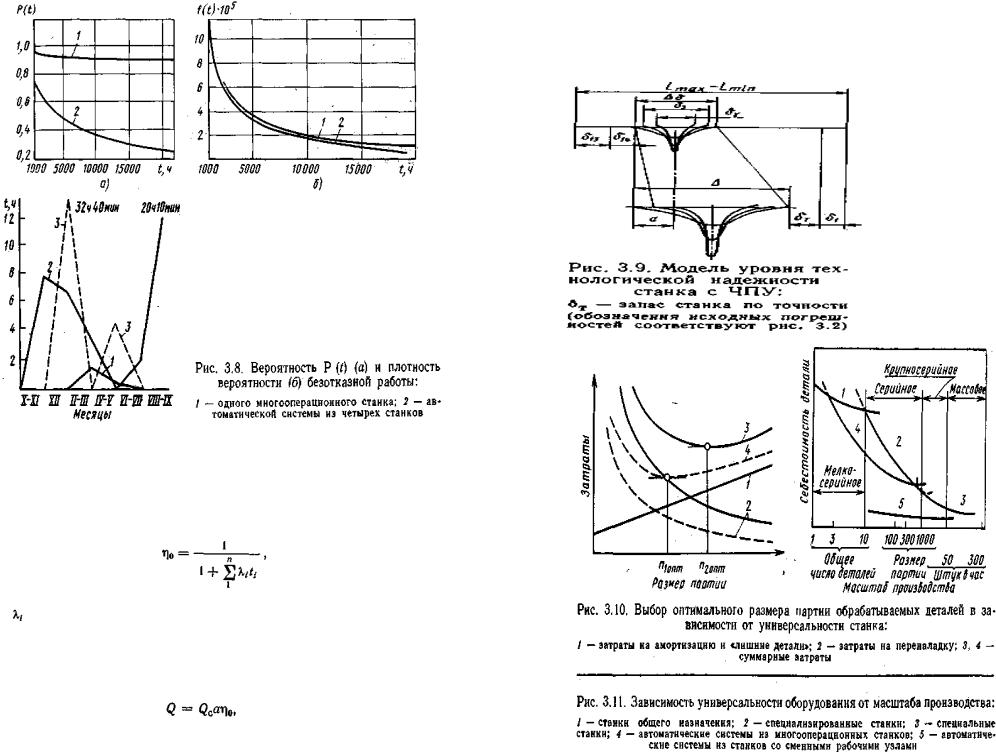
По мере совершенствования систем управления, перехода на микропроцессоры и бесконтактную автоматику значение отказов электрооборудования станков существенно снизилось (рис. 3.7).
Для оценки влияния надежности на производительность станка или станочной системы обычно вводят коэффициент технического использования
где п — число независимых элементов, подверженных отказам;
— интенсивность отказов i-го элемента; — среднее время на устранение отказа этого элемента.
С учетом коэффициента технического использования фактическая производительность автоматической системы принимает вид
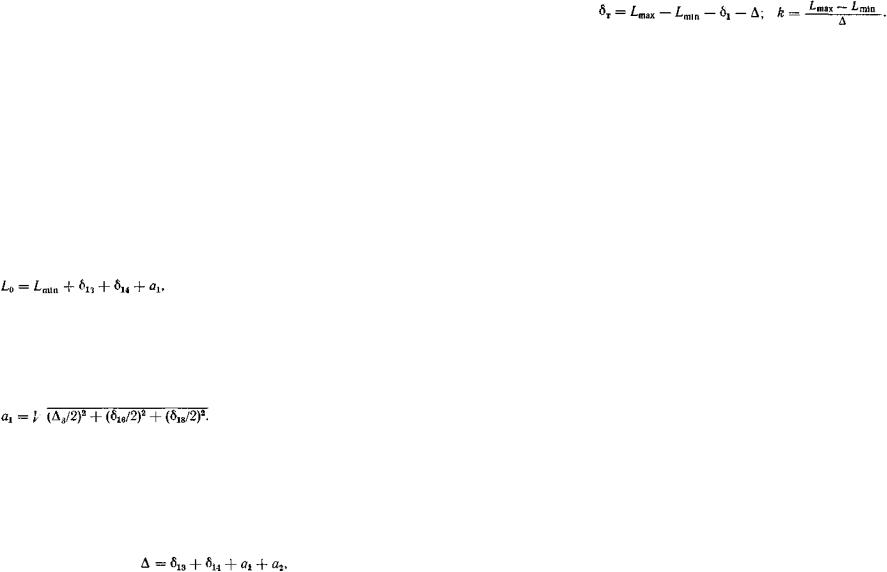
где — производительность многооперационного станка; а — среднее число одновременно обрабатываемых деталей.
Технологическая надежность станков с ЧПУ и автоматических станочных систем из этих станков как свойство сохранять во времени первоначальную точность оборудования и соответствующее качество обработки имеет важное значение в связи с большим сроком службы этого вида оборудования и интенсивной его эксплуатацией. В основе аналитических методов оценки технологической надежности станков с ЧПУ лежит разработка математической модели изменения точности обработки во времени. Если выбрать основные виды исходных погрешностей, наиболее существенно снижающих точность станков с ЧПУ во времени, то модель формирования суммарной ошибки можно привести к виду, изображенному на рис. 3.9.
Первичная настройка станка на величину контролируемого параметра осуществляется исходя из условия
где — минимально допустимое значение контролируемого параметра;
— систематические ошибки от геометрии и деформации станка;
—зона рассеяния от действия случайных ошибок при установке детали
, от привода позиционирования
i, при размерной установке инструмента
;
По мере работы станка под воздействием возмущений, имеющих характер случайных процессов, центр зоны рассеяния размера смещается на некоторую величину b (t), которую следует рассматривать как случайную функцию времени. Смещение происходит главным образом под воздействием температурных, износных и динамических факторов. К концу наладочного периода суммарная погрешность обработки достигает предельно допустимого значения
где — зона рассеяния случайных ошибок к концу периода настройки. Для оценки технологической надежности станка можно пользоваться запасом
по точности обработки или коэффициентом k запаса
точности:
Эффективным средством повышения надежности станков автоматической станочной системы является диагностика. При этом осуществляют направленный сбор текущей информации о состоянии станка и его важнейших узлов и элементов. Для сбора информации используют преобразователи, дающие сигнал по естественным для станка возмущениям или на основе специально возбуждаемых периодических воздействий. Поиск и диагностику ошибок, неисправностей, опасных отклонений от нормальной работы осуществляют различными методами. При использовании функциональной модели станок и отдельные его узлы (привод подачи, несущая система) разбивают на конечное число функциональных блоков с одним выходным контролируемым параметром. Совокупность выходных параметров, связанных в единую систему, служит основой модели всего узла или всего станка. Диагностирование ведут на основе алгебры логики; дефектное состояние функционального блока соответствует нулевому значению параметра, а нормальное состояние
соответствует булевскому значению «1». Конкретный набор булевских значений оценочных параметров характеризует определенный вид отказа и соответствующим образом кодируется. Для быстрого анализа ситуации и нахождения дефектного блока составляется диагностическая матрица и соответствующая программа для ЭВМ. При этом методе диагностика носит дискретный характер.
При непрерывном действии станка или его узла используют параметрический метод диагностики. В этом случае математическую модель станка составляют в виде системы дифференциальных уравнений, а параметры в уравнениях уточняют по экспериментальным данным. В соответствии с принятой целевой функцией для станка или его узла выбирают критерии оптимизации, по которым на основе текущей информации осуществляются непрерывное регулирование (адаптивное управление) и диагностика.
Иногда используют энергетическую модель, основу которой составляет диаграмма распределения энергетического потока при оптимальных условиях работы станка. Значения параметров уточняют экспериментально. Изменение распределения потоков энергии,
46
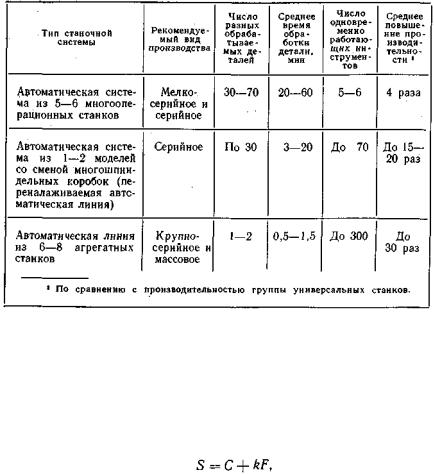
фиксируемое встроенными в станок датчиками, анализируется; оно является основой диагностического контроля..
У н и в е р с а л ь н о с т ь станочных систем определяется затратами на переход от обработки партии одних деталей к обработке партии других деталей. Для каждого вида оборудования существуют оптимальные условия эксплуатации, связанные с масштабом производства. Это относится и к отдельным станкам и к станочным системам разной универсальности. В зависимости от соотношения затрат на переналадку оборудования и затрат, связанных с изготовлением «лишних» деталей, существует оптимальный размер партии деталей для каждого конкретного оборудования (рис. 3.10).
Универсальность и производительность являются противоречивыми требованиями, поэтому с уменьшением универсальности станков и станочных систем их производительность может быть повышена за счет концентрации технологических операций, совмещения времени рабочих и вспомогательных операций, применения многоинструментальной обработки. Целесообразный уровень универсальности оборудования в зависимости от масштаба производства приведен для станков и станочных систем на рис. 3.11 и в табл. 3.3, которая обобщает некоторый опыт эксплуатации в различных условиях производства автоматических станочных систем для обработки корпусных деталей.
Э к о н о м и ч е с к а я э ф ф е к т и в н о с т ь является важнейшим параметром для оценки автоматической станочной системы, поскольку любой вид технологического оборудования направлен на снижение затрат труда в производстве.
Определение экономической эффективности осуществляют суммированием приведены затрат как при создании нового
Характеристики станочных систем Т а б л и ц а 3.3
оборудования (рис. 3.12), так и при его эксплуатации. Таким образом, приведенные затраты S представляют собой сумму годовой себестоимости С продукции и нормативных отчислений от капитальных вложений F в производственные фонды:
где k — нормативный коэффициент окупаемости капитальных вложений.
47
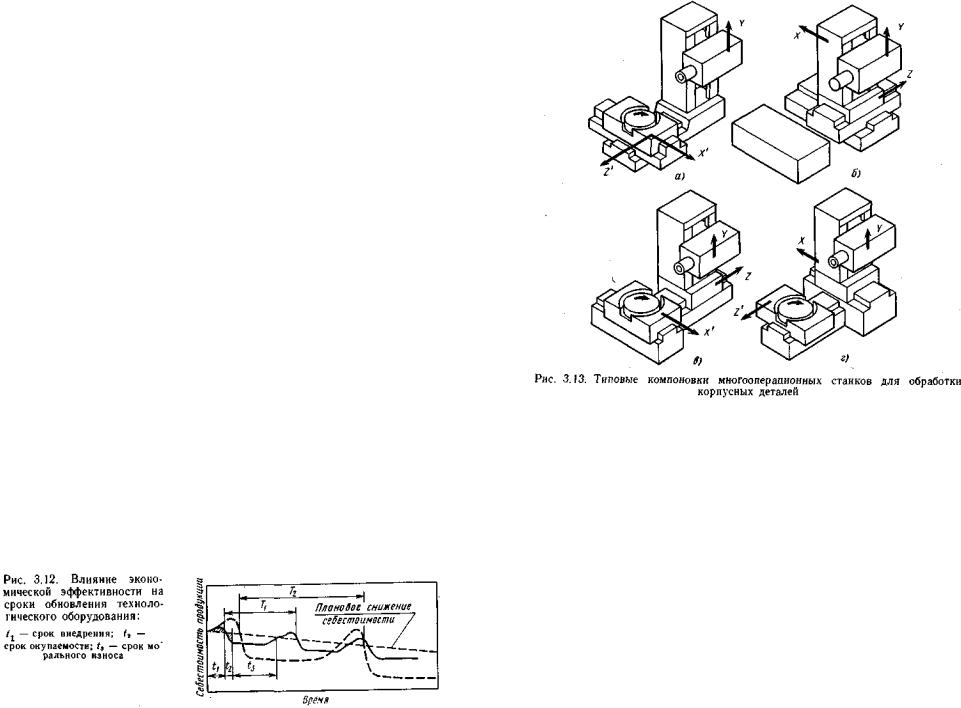
3.2. НЕСУЩАЯ СИСТЕМА СТАНКА
Несущая система станка как последовательность базовых деталей и их соединений в значительной мере определяет правильность взаимного расположения детали и инструмента и соответственно точность обработки. Шпиндельные узлы и направляющие, которые входят в состав несущей системы, рассмотрены отдельно; в данном разделе рассматриваются базовые детали .и их неподвижные соединения.
К несущей системе станка при его проектировании предъявляются следующие основные требования: 1) ограничение геометрических погрешностей при изготовлении и сборке, а также сохранение этих ограничений в течение требуемого срока эксплуатации станка; 2) ограничение упругих перемещений несущей системы под действием силовых факторов, возникающих в работающем станке;
3)ограничение амплитуды колебаний несущей системы при действии периодических возмущений во всем рабочем спектре частот;
4)ограничение температурных деформаций несущей системы как в стационарном, так и в нестационарном температурном режиме;
5)минимально возможные затраты материала и труда на изготовление и сборку при сохранении всех проектных ограничений. Выполнение проектных требований зависит как от правильности конструирования отдельных базовых деталей и их соединений, так и от компоновки всей несущей системы.
К о м п о н о в к а |
несущей |
системы станка подразумевает |
определенную последовательность |
расположения базовых деталей |
(шпиндельная бабка, стойка, станина, стол) между инструментом и обрабатываемой деталью и их ориентацию в пространстве. Среди всех базовых деталей одна должна
быть неподвижной (это обычно станина, основание), а ее расположение в цепочке базовых деталей несущей системы определяет ориентацию в пространстве и структурную компоновку станка. Число последовательно расположенных базовых деталей (узлов станка) на единицу больше числа необходимых относительных движений, . причем каждое движение требует направляющих подвижных соединений. Общее число возможных компоновок и их особенности могут быть выявлены на основе структурного анализа по методу Ю. Д. Врагова [7].
Формализация компоновок основана на том, что неподвижному узлу присваивают символ О, узлам, перемещаемым вдоль координатных осей, соответственно символы X, Y, Z, а узлам с относительным вращательным движением относительно этих осей — символы А, В, С. При записи формулы компоновки начинают с узла, несущего заготовку, и кончают узлом, несущим инструмент. Примеры соответствующих
48
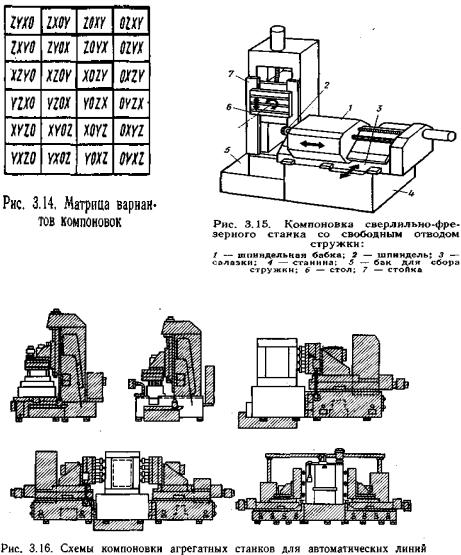
формализованных записей для наиболее распространенных компоновок многооперационных станков с горизонтальным шпинделем для обработки корпусных деталей приведены.на рис 3.13. Каждая из компоновок имеет свои преимущества и недостатки, которые предопределяют целесообразную область их применения. .Компоновка с крестовым столом (рис. 3.13, а) создает значительные трудности по обеспечению жесткости и соответственно точности обработки, особенно в тех случаях, когда на крестовом столе уже установлен и поворотный стол. Такая компоновка встречается главным образом в станках небольших и среднего размера, с шириной стола до 800 мм. Компоновки с разделением горизонтальных перемещений (рис. 3.13, в, г) между столом и стойкой обеспечивают более высокую жесткость и Точность координатных перемещений. Перемещение стола по оси X дает возможность беспрепятственно увеличивать длину стола, создавая размерный ряд станков. Подвижная стойка ведет к неизбежному усложнению устройств для автоматической смены инструмента. Последнее обстоятельство в еще большей мере относится к компоновке, при которой все координатные перемещения сосредоточены у инструмента, и стойка имеет крестовое перемещение по двум горизонтальным осям (рис. 3.13, б). Однако именно эта компоновка получает в последнее время все большее распространение как в тяжелых станках, так и в станках средних размеров. Важнейшими достоинствами этой компоновки являются удобство отвода и сброса стружки, резкое упрощение систем автоматической загрузки обрабатываемых деталей, независимость подсистемы станка и подсистемы транспорта в автоматической станочной системе и удобство реализации принципа агрегатирования. Рассмотренные четыре компоновки многооперационных станков с тремя координатными перемещениями не исчерпывают всех возможных вариантов, общее число которых определяется числом перестановок символов в записи и в данном конкретном случае составляет 24 варианта, сведенные в матрицу на рис. 3.14. В формализован ной записи отсутствуют вращательные движения шпинделя и стола, поскольку они зафиксированы за инструментом.
49
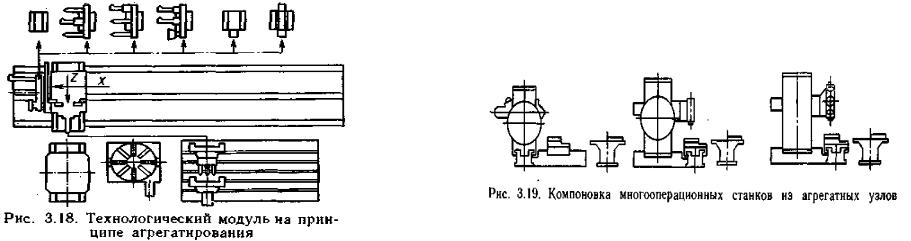
Для станков особо высокой производительности, например при обработке легких сплавов, важнейшим проектным критерием для выбора варианта компоновки может стать удобство сбора и отвода большого количества стружки. В этом случае лучшими будут иные компоновки (рис. 3.15), которые в ущерб другим проектным критериям обеспечивают свободное удаление стружки из рабочей зоны станка.
А г р е г а т и р о в а н и е является важной предпосылкой развития многооперационных станков, встраиваемых в автоматические станочные системы. Основными достоинствами агрегатирования, когда различные станки используют одинаковые узлы, выполняемые в виде отдельных независимых агрегатов, являются удешевление производства станков за счет повышения серийности, сокращение сроков их изготовления, повышение надежности, что особенно важно при их использовании в сложных и дорогих комплексных системах. Принцип агрегатирования используют при проектировании автоматических линий (рис. 3.16), а в последнее время при создании многооперационных станков. В стране разработаны принципы стандартизации узлов многооперационных станков с горизонтальным шпинделем для обработки корпусных деталей на автоматических станочных системах (рис. 3.17). Предусмотрено агрегатирование базовых деталей (станина, стойка, стол, приспособление-
спутник, шпиндельная бабка), привода шпиндельных узлов, инструментальных магазинов, устройств смены обрабатываемых
Реализация подобных принципов позволяет осуществить поузловую специализацию станкостроительных заводов и организовать централизованное производство комплектующих изделий и вспомогательных устройств.
Дальнейшим развитием принципов агрегатирования в автоматических станочных системах является создание технологических модулей, один из которых приведен на рис. 3.18. На основе комплекта агрегатных узлов предусмотрено большое число модификаций для использования в различных автоматических системах в зависимости от их служебного назначения. Набор агрегатных узлов включает два типа станин ( с двумя или с тремя направляющими), три типа стоек с различными по размеру направляющими, два варианта шпиндельной бабки (мощность И или 22 кВт), три варианта шпиндельного узла с различной частотойвращения и несколько типов столов для обрабатываемых деталей. Предусмотрен большой набор устройств для автоматической смены инструмента и для автоматической смены заготовок. Основой технологического модуля является стойка с крестовым перемещением по двум горизонтальным координатам, т. е. компоновка станка соответствует рис. 3.13, б..
Другой пример компоновки многооперационных станков для обработки корпусных деталей в рабочем пространстве 500x500x500 для трех вариантов с горизонтальным или вертикальным расположением шпинделя, а также с револьверной головкой, представлен на рис. 3.19.
50
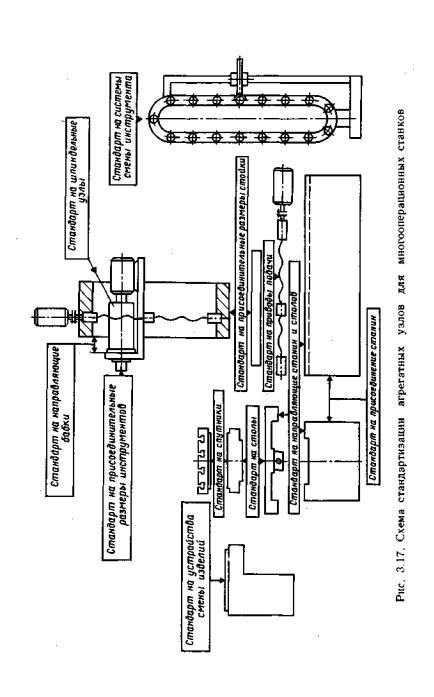
Б а з о в ы е д е т а л и станков, предназначенные для автоматических станочных систем, проектируют в соответствии с проверенными на практике рекомендациями по выбору материала и конструктивных форм. Основным материалом для литых конструкций является серый чугун, а для сварных конструкций, которые получают все большее распространение в условиях единичного и мелкосерийного производства, — листовая сталь.
Литые чугунные базовые детали выполняют, по возможности, замкнутой коробчатой формы, симметричной и простой в изготовлении конструкции. Во внутренних полостях нередко оставляется стержневая смесь (рис. 3.20), что обеспечивает полностью замкнутый профиль и соответственно высокую жесткость. Кроме того, сыпучий материал во внутренней полости повышает демпфирующие свойства несущей системы.
Сварные базовые детали позволяют при той же статической жесткости и при сохранении высоких динамических характеристик (рис. 3.21) затрачивать стали на 25—30 % меньше по массе, чем чугуна в литой конструкции. При этом, однако, надо иметь в виду более высокую стоимость стали. При проектировании сварных базовых деталей целесообразно сохранять простую прямоугольную коробчатую форму и ограничивать число сварных швов во избежание значительного разброса статической жесткости (до 20—50 %). Известны примеры (рис. 3.22) использования железобетонных базовых деталей в средних и тяжелых станках в целях экономии металла (до 30—40 %) и повышения демпфирующих свойств несущей системы. Существенным недостатком железобетонной конструкции является невозможность вторичного использования металла. Кроме того, возрастает общая масса несущей системы и всего станка, что усложняет его транспортирование.
Ж е с т к о с т ь несущей системы станка является важнейшим проектным критерием оценки качества конструкции. При этом особое значение имеет стохастический характер жесткости в зависимости от разброса геометрических параметров (толщина стенки, габаритные размеры) под влиянием технологии производства и от разброса характеристик материала.
51