
Melnikov_V.B._i_dr._Tehnologicheskiy_raschet_adsorbcionnoy_osushki_prirodnogo_gaza
.pdfПриродный газ после осушки и очистки поступает для производства СПГ, например, из магистрального газопровода с параметрами P0, T0, W0 в блок 1 для его возможного охлаждения. Далее природный газ с параметрами PН, TН, WН идёт в блок адсорбционной осушки (2), где осушается до требуемого влагосодержания (температуры точки росы по влаге) и выходит с параметрами PК, TК, WК. После осушки газ попадает в теплообменник 3 для предварительного охлаждения до минус 30 – минус 40 С. Если в составе газа присутствуют (в значительном количестве) пропан– бутановая фракция и этан, то они отделяются и направляются на фракционирование (блоки сепарации и фракционирования про- пан–бутановой фракции на рисунке не показаны). После предварительного охлаждения природный газ доохлаждается в основном криогенном теплообменнике 4 и далее дросселируется. В результате дросселирования получается сжиженный природный газ с давлением чуть выше атмосферного и температурой минус 162С. Газовая фаза, образовавшаяся в результате дросселирования, отделяется в сепараторе и чаще всего используется в циклах охлаждения природного газа.
Для предотвращения образования твердой фазы (гидратов) в теплообменниках установки производства СПГ необходимо чтобы влагоемкость поступающего газа была не больше минимальной равновесной влагоемкости газового потока. Таким образом, допустимое количество влаги в природном газе определится из условия:
WК ≤ W5. |
(3) |
Природный газ чаще всего сжижается при давлении 3,5 4,6 МПа, а температура при этом колеблется от минус 91,5 С до минус 83,3 С (рис. 4).
Серьезное влияние на эффективность адсорбционной осушки оказывает температура (рис. 5).
21
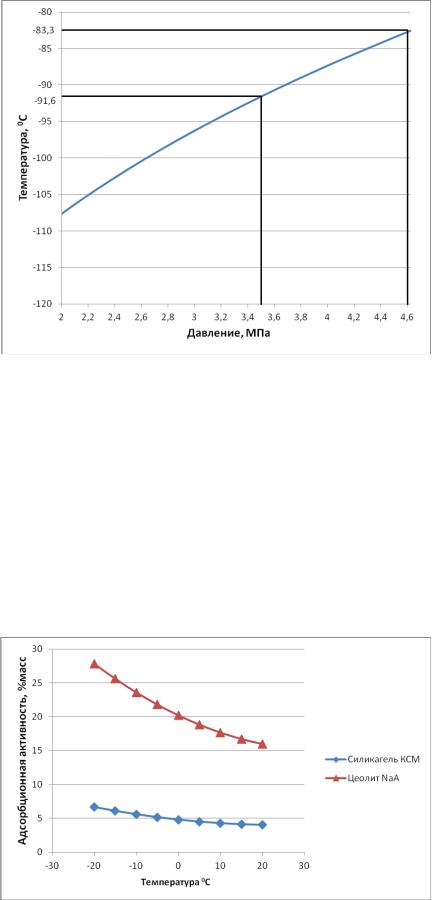
Рис. 4. Фазовая диаграмма для метана, рассчитанная в программном комплексе Aspen HYSYS
Таблица 4
Равновесная влагоемкость метана при термобарических условиях в точке 5
Т, C |
P, МПа |
W5, мг/ст.м3 |
83,5 |
4,5 |
0,0726 |
|
|
|
87,3 |
4 |
0,0709 |
|
|
|
91,6 |
3,5 |
0,0665 |
|
|
|
Рис. 5. Зависимость равновесной адсорбционной активности адсорбентов по влаге от температуры при давлении 4,5 МПа
22
Понижая её, можно добиться значительного увеличения адсорбционной активности сорбента, поэтому для качественной осушки газа потребуется меньше адсорбента.
5) Определение необходимого количества выбранного адсорбента для достижения заданной степени влагосодержания газа в расчете на производительность адсорбера.
Количество адсорбента в первом приближении можно рассчитать по формуле:
gА = W ∙ QГ ∙ τС / A, |
(4) |
где gА – количество адсорбента, кг; W – количество влаги которое необходимо извлечь, кг/нм3; QГ – производительность адсор-
бера, нм3/ч; τС – продолжительность цикла сорбции, ч; |
A – рав- |
новесная активность адсорбента, % масс. |
|
QГ = М ∙ 1000 / ρгну , |
(5) |
M – производительность установки, т/ч; ρгну – плотность газа при нормальных условиях, кг/м3.
Объем адсорбента будет таким:
VА = gА / ρна, |
(6) |
ρна – насыпная масса адсорбента, кг/м3.
6) Определение основных размеров адсорбера.
При известном значении часового объемного расхода газа при рабочих условиях адсорбционной осушки внутренний диаметр
адсорбера (Dвн) определяют по формуле: |
|
Dвн = {4Qгр / (π∙wгр)}1/2, |
(7) |
здесь Dвн – внутренний диаметр адсорбера, м; Qгр – объемный расход газа при рабочих условиях процесса м3/с; wгр – средняя допустимая скорость газа, м/с.
Среднюю допустимую скорость газа, например, для силикагеля с размером гранул 4–8 мм, обычно выбирают в пределах 9
23
13 м/мин, давление от 7,5 до 3,5 МПа и температуру адсорбции
25–30 С.
При известных значениях Dвн и wгр рассчитывают скорость газа в свободном сечении адсорбера.
Определить объемный расход газа при рабочих условиях можно так:
Qгр=М/(3,6∙ ρр), |
(8) |
в формуле M – производительность установки, т/ч; ρр – плотность газа при рабочих условиях, кг/м3; Qгр – объемный расход газа при рабочих условиях, м3/с.
Плотность газа при рабочих условиях можно рассчитать с использованием ГОСТ 30319.1-96 «Газ природный. Методы расчета физических свойств. Определение физических свойств природного газа, его компонентов и продуктов его переработки. Межгосударственный стандарт» или программного комплекса
Aspen HYSYS. |
|
|
Высоту слоя адсорбента можно определить по формуле |
|
|
Ha = 4Va /(π∙ D2 |
), |
(9) |
вн |
|
|
где Ha – высота слоя адсорбента, м; Dвн – внутренний диаметр адсорбера, м; Va – количество адсорбента, м3.
Высота цилиндрической части адсорбера будет составлять:
H = 1,2 Ha. |
(10) |
Толщину стенки цилиндрической обечайки адсорбера можно |
|
определить по формулам: |
|
so ≥ sp + c |
(11) |
spo = (Pрасч ∙ Dвн)/(2σдоп – Pрасч) |
(12) |
здесь so – исполнительная толщина стенки, мм; sp – расчетная толщина стенки, мм; c – прибавка на компенсацию коррозии; Dвн – внутренний диаметр цилиндрической части адсорбера, мм;
24
– допускаемые напряжения для материала адсорбера при расчетной температуре, МПа; Pрасч – расчетное давление, МПа.
Допускаемые напряжения для материала адсорбера при расчетной температуре и давлении обосновываются выбором марки стали для изготовления сварных сосудов, работающих под внутренним избыточным давлением.
Тип и параметры днища для внутренних диаметров и толщину стенки выбирают по нормативным документам.
При расчете массы аппарата принимают, что все внутренние устройства и приварные части составляют 20% от массы корпуса:
Мап = 1,2∙(Мо + 2Мд), |
(13) |
где Мап – масса аппарата-адсорбера, кг; Мо – масса цилиндрической обечайки, кг; Мд – масса днища, кг.
Мо = π∙[(Dвн |
+ 2sо)2 – D2 |
]∙ρст /4, |
(14) |
|
вн |
|
|
ρст – плотность выбранной марки стали; 7) Определение объемов газов регенерации и охлаждения.
Количество теплоты, необходимое для нагрева системы,
определяют по уравнению теплового баланса: |
|
Qт = Q1 + Q2, |
(15) |
здесь Qт – необходимое количество теплоты для нагрева системы, Дж/цикл; Q1 – количество теплоты для нагрева базовой части (адсорбера, адсорбента, теплоизоляции), Дж/цикл; Q2 – количество теплоты для нагрева десорбированных компонентов (т.к. десорбция молекул происходит с поглощением теплоты), кДж/цикл.
Q1 = (gк ∙ ск + gи ∙ си + gад ∙ сад) ∙ (t2 t1). |
(16) |
в формуле gк, gи, gад – масса адсорбера, теплоизоляции и адсорбента соответственно, кг; ск, си, сад – средняя удельная теплоемкость материала колонны, теплоизоляции и адсорбента в интер-
25
вале температур t1 t2, кДж/(кг∙ С); t1, t2 – начальная и конечная температуры процесса регенерации; С.
Принимают значения: ск = кДж/(кг∙ С) сад = кДж/(кг∙ С).
Температура t1 равна рабочей температуре адсорбции. Регенерация осуществляется сухим газом, подогретым до 150–350 С, в зависимости от типа адсорбента. Адсорбент прогревают так: прекращают ввод горячего газа в адсорбер с температурой 350 С, когда температура на выходе достигнет 140–150 С. Предполагают, что полное удаление сорбированных молекул воды из последнего слоя адсорбента произойдет в результате перемещения тепла из прогретых слоев потоком газа, вводимого в адсорбер на стадии охлаждения. Средняя конечная температура на стадии регенерации будет равна:
t2 = (150 + 350) / 2 = 250 С.
Так как количество теплоты, необходимое для нагрева теплоизоляции, невелико по сравнению необходимой для нагрева материала колонны и адсорбента до теплового режима регенерации адсорбента, то им можно пренебречь. Тогда количество теплоты, необходимое для нагрева десорбированных компонентов, будет таким:
Q2 = mв ∙ cв ∙ (t2 – t1), |
(17) |
где mв – |
количество поглощенной воды, кг/цикл; cв – средняя |
|
удельная |
теплоемкость воды в интервале |
температур t1 t2, |
кДж/(кг∙ С); |
|
|
|
mв = ∆W ∙ Qг ∙ τс |
(18) |
∆W – количество поглощенной воды, кг/нм3; |
Qг – производи- |
тельность установки, нм3/ч; τс – продолжительность цикла адсорбции, ч.
Принимаем cв = кДж/(кг∙ С).
26
Расход теплоты для десорбции поглощенных компонентов
Qп = mв ∙qад, |
(19) |
здесь mв – количество поглощенной воды, кг/цикл; qад – теплота сорбции воды адсорбентом, кДж/кг (например, для цеолита mв =
4,2 МДж/кг).
Расход газа регенерации определяют по уравнению матери-
ально-теплового баланса: |
|
|
Gрег = (Qн Qп )/[cрег (t |
t ) (t1′ t2′)], |
(20) |
1 |
2 |
|
в формуле Gрег – расход газа регенерации, кг/цикл; Qн |
– количе- |
ство теплоты необходимое для нагрева системы, кДж/цикл; Qп – количество теплоты необходимое для десорбции поглощенных компонентов, кДж/цикл; cрег – средняя удельная теплоемкость газа регенерации в интервале температур t1 t2 кДж/(кг∙ С); t1, t2 – температура газа регенерации на входе и выходе из адсорбера соответственно, С.
t1 = 350 С.
Температура газа на выходе из адсорбера меняется в течение цикла,: в начале она должна быть равна температуре адсорбции (tад), а при осушке газа в конце 150 С. Средняя температура га-
за на выходе из адсорбера при регенерации будет такой: |
|
|
t2 = (tад + 150) / 2. |
(21) |
|
Далее определяем cрег среднюю удельную теплоемкость газа |
||
регенерации в интервале температур t |
t , считая, что газ состо- |
|
1 |
2 |
|
ит из метана, а концентрацией паров влаги можно пренебречь ввиду их незначительного содержания.
Принимают значение cрег = кДж/(кг∙ С).
Расход газа на цикл охлаждения адсорбента определяют по уравнению материально-теплового баланса:
27
Gохл |
= Q1′ / [cохл (t t ) ], |
(22) |
|
|
1 |
2 |
|
где Gохл – расход газа охлаждения, кг/цикл; Q1 – количество теплоты необходимое для охлаждения аппарата и адсорбента, кДж/цикл; cохл – средняя удельная теплоемкость газа охлаждения
в интервале температур t t , кДж/(кг∙ С); |
t t |
– температура |
||
1 |
2 |
1 |
2 |
|
газа охлаждения на входе и выходе из адсорбера соответственно,
С.
Температура газа охлаждения на входе в адсорбер равна рабочей температуре сорбции влаги из газа.
Температура газа охлаждения на выходе из адсорбера изменяется в течение цикла: вначале выходит газ с температурой 150 ºС, затем газ с температурой 350 ºС, а в конце поступавший на охлаждение (tр). Расчет таких сложных кривых затруднителен, и обычно принимают среднюю температуру на выходе равной средней температуре слоя к концу стадии нагрева, т.е. 250 ºС, т.е.
t = (tр + 250)/2.
2
Затем определяем массовую долю природного газа, идущего на регенерацию и охлаждение адсорбента по следующей формуле:
φ = (Gрег + Gохл)∙100% /(M ∙ τс), |
(23) |
где φ – доля природного газа идущего на регенерацию и охлаждение адсорбента, % масс.; Gрег – расход газа регенерации, кг/цикл; Gохл – расход газа охлаждения, кг/цикл; M – производительность установки, кг/ч; τс – время цикла сорбции, ч.
Продолжительность циклов регенерации и охлаждения адсорбента определяют из условия постоянства расходов осушенного газа:
Gрег / Gохл = τр / τо. |
(24) |
При использовании технологической |
схемы адсорбционной |
осушки газа, состоящей из двух аппаратов-адсорберов, должно
28
выполняться следующее условие: τс ≥ τр + τо. Тогда при известном значении τс необходимо определить величины τр и τо.
Определение тепловой нагрузки печи
Тепловую нагрузку печи вычисляют по уравнению матери-
ально-теплового баланса: |
|
Qп = Gрег ∙ τр ∙ cг ∙(t2 t1), |
(25) |
где Qп – тепловая нагрузка печи, кВт; Gрег – расход газа регенерации, кг/цикл; τр – время цикла регенерации, ч; cг – средняя удельная теплоемкость газа в интервале температур t2 t1, кДж/(кг∙ С); t2, t1 – температура газа на выходе и входе в печь соответственно.
Принимаем: cг = кДж/(кг∙ С).
Количество топливного газа, подаваемого в печь, определяют по выражению:
Vг = 3600 ∙ Qп /(qт ∙ η), |
(26) |
где Vг – расход топливного газа, кг/ч; Qп – тепловая нагрузка печи, МВт; η – коэффициент полезного действия печи; qт – теплотворная способность топливного газа, кДж/кг.
Для трубчатых печей значение КПД лежит в пределах 0,65- 0,85.
Принимаем η = 0,75.
В качестве топливного газа, например, на заводах по его сжижению, чаще всего используется газ, образовавшийся при дросселировании СПГ. Он практически полностью состоит из метана.
Теплотворная способность метана qт = 50100 кДж/кг.
По полученным результатам также следует:
1)уточнить линейную скорость газа в свободном сечении адсорбера при рабочих условиях;
2)определить внутренний диаметр адсорбера при уточненной линейной скорости газа в свободном сечении адсорбера при рабочих условиях;
29
3)вычислить длину адсорбционной массообменной зоны в адсорбере;
4)выяснить динамическую влагоемкость слоя выбранного адсорбента;
5)определить минимально необходимую высоту слоя адсорбента;
6)проверить продолжительность работы слоя до проскока влаги. Если оно значительно отличается от принятой продолжительности цикла адсорбции, то расчет повторяется.
Из проведенных расчетов необходимо сделать вывод о запасе скорости газа в адсорбере и влагоемкости адсорбента.
30