
Наукоемкие химические технологии учебное пособие
..pdfплота парообразования, тем меньше потребуется жидкости. Жидкость с высокой теплопроводностью сведет к минимуму перепад температур между стенкой и поверхностью испарения (тем меньше вероятность возникновения пузырькового кипения на границе фитиля со стенкой корпуса). Чем меньше вязкость жидкости, тем меньше гидравлическое сопротивление ее течению.
Капиллярно-пористый материал (фитиль) – обеспечи-
вает создание капиллярного напора для перемещения жидкости из конденсатора в испаритель и равномерного распределения ее по всей зоне испарения.
К материалу предъявляются противоречивые требования:
• он должен быть мелкопористым для создания максимального напора, и он должен быть крупнопористым для увеличения проницаемости (по жидкости); в связи с этим в условиях работы против сил гравитации практически не используется ТТ длиной более 1 м;
• слой КПМ вдоль стенок должен быть толстым для увеличения расхода жидкости (увеличение теплопередачи) и должен быть тонким для уменьшения термического сопротивления фитиля в радиальном направлении (с целью увеличения плотности теплового потока в испарителе).
Наиболее часто используют металлические сетки, металлические ткани саржевого плетения, спеченные металлические порошки, металлический войлок. Металлы: медь, никель, титан, фосфористая бронза, нержавеющая сталь.
Функция, основные свойства и области работы ТТ
Классическая ТТ имеет одну главную полезную функцию (ГПФ) – теплопередача в осевом направлении между двумя разделенными в пространстве точками.
Для нормальной работы ТТ необходимо, чтобы режимы работы всех ее элементов не достигали критических величии.
Подвод тепла может осуществляться любым известным способом (открытым пламенем, теплообменом с нагретым
91
телом, электрическим током, ИК-лучами, электронной бомбардировкой и др.). При этом из-за термического сопротивления стенки будет обычный перепад температур между источником тепла и рабочей жидкостью. Температурный предел зависит только от термо- (хладо)стойкости материала корпуса.
Зона испарения. Плотность теплового потока не должна превышать некоторого значения, при котором может наступить кризис теплоотдачи (осушение фитиля, когда КПМ не успевает подавать новые порции жидкости в зону испарения).
Зона конденсации. Существует два типа конденсации – капельная или, чаще, пленочная. Обычно пар конденсируется на поверхности пленки жидкости. Между этой поверхностью и наружной поверхностью стенки существует небольшой перепад температур (т.е. температура стенки ненамного отличается от температуры пара). Поверхность ТТ в зоне конденсации обладает интересным свойством – изотермичностью, так как эта поверхность работает, можно сказать, при постоянной температуре (близкой к температуре фазового перехода пар–жидкость). Если на каком-то участке возникает местный тепловой сток, то количество конденсирующегося в этом месте пара увеличивается и температура поддерживается на прежнем уровне.
Зона транспорта пара. В зоне испарения создается избыточное давление насыщения пара, которое расходуется на разгон пара до осевой скорости, на преодоление силы трения парового потока на поверхности фитиля и на преодоление сил вязкости пара. Вследствие этого давление по длине ТТ от зоны испарения падает. В среднем участке трубы давление стабилизируется (адиабатный участок). В зоне конденсации давление восстанавливается почти до величины давления в зоне испарения. Можно сказать, потери давления в простых ТТ связаны только с преодолением вязкостных сил.
92
Некоторые явления, ограничивающие область работы ТТ
•Срыв жидкости. Направления движения пара и жидкости в ТТ противоположны. Поэтому на поверхности раздела фитиль – паровой поток на жидкость действуют касательные напряжения – возможен срыв капель. Унос капель жидкости наступит тогда, когда скоростной напор пара превысит силы поверхностного натяжения жидкости. Установлено, что чем тоньше сетка (чем меньше шаг проволочек), тем менее вероятен унос капель.
•Ограничение мощности ТТ по вязкости. При низких
температурах преобладающими являются силы вязкости
впаровом потоке: чем они выше, тем меньше скорость пара и мощность теплопередачи. Установлено, что для увеличения скорости пара достаточно снизить давление (в идеале до нуля)
взоне конденсации, т.е. снизить температуру этого конца ТТ.
•Звуковой предел. Снижение давления (температуры)
взоне конденсации и повышение температуры в зоне испарения повышает «разность потенциалов» между концами ТТ и тем самым – скорость движения пара. Однако существует физический предел – скорость звука, при достижении кото-
рого уже никакое увеличение «разности потенциалов» не приводит к увеличению скорости пара. Достигается состояние, которое носит название «запирание» канала ТТ. При этом если продолжать и далее уменьшать температуру в зоне конденсации, то ТТ потеряет свойство изотермичности – по ее длине будет наблюдаться значительный градиент температур.
• Капиллярное ограничение (ограничение по смачива-
нию фитиля). При возрастании теплового потока в зоне испарения должен возрастать приток жидкости по фитилю. Предельная величина притока жидкости зависит от типа конструкции фитиля.
93
• Кризис теплоотдачи. Для неметаллических жидкостей характерно возникновение пузырькового кипения в фитиле зоны испарения. Это затрудняет отвод образующегося на греющей поверхности пара через толщу фитиля, а следовательно, ограничивает мощность теплопередачи (например, предел мощности для воды – 130 кВт/м2, для калия –
315 кВт/м2.
Конструктивные особенности тепловых труб
Для подъема жидкости в тепловой трубе на высоту h приходится применять более мелкие поры. В этом случае гидравлические сопротивления трения ( Рж) значительно возрастают, и не только из-за уменьшения диаметров капиллярных каналов, но еще и за счет увеличения длины фитиля. Дальнейшее уменьшение диаметров капиллярных каналов при тех же размерах (длине) фитиля почти не приводит к увеличению мощности тепловой трубы. Причина заключается в том, что увеличение напора Рmах при уменьшении этих диаметров происходит значительно медленнее, чем увеличение гидравлического сопротивления фитиля Рж – разность капиллярных давлений обратно пропорциональна диаметрам пор, а гидравлическое сопротивление трения при ламинарном течении жидкости по фитилю обратно пропорционально более чем второй степени этих диаметров.
Но тем не менее увеличение длины тепловых труб, передающих теплоту по направлению поля тяжести, все же возможно. Но для этого должна быть изменена их конструкция. Поскольку гидростатические потери давления уменьшать нельзя, то конструкция тепловой трубы должна быть такой, при которой увеличение длины тепловой трубы, передающей теплоту по направлению поля тяжести при той же ее мощности или увеличение мощности при той же длине тепловой трубы, осуществлялось за счет увеличения разности максимального капиллярного напора Рmах и гидравлических потерь в жидкости Рж, т.е. путем увеличения величины
94
Рmах – Рж. Это может быть достигнуто при одновременном увеличении как разности капиллярных давлений Рmах, так и при уменьшении Рж. Увеличение Рmах на той же рабочей жидкости возможно только путем уменьшения диаметров капиллярных каналов, а уменьшение потерь на трение Рж (при таком же уменьшении диаметров этих каналов и при том же поперечном сечении фитиля) возможно только при значительном уменьшении длины фитиля. Очевидно, что последнее в тепловых трубах первого поколения без уменьшения их длины просто невозможно.
Таким образом, задача передачи тепла по направлению поля силы тяжести приводит к такой конструкции тепловой трубы, в которой мелкопористый фитиль, создающий необходимый и достаточно большой капиллярный напор, обладает малым гидравлическим сопротивлением по жидкости, т.е. имеет небольшую длину (толщину), а следовательно, находится только в испарителе.
Конструкции таких тепловых труб были разработаны на кафедре молекулярной физики физико-технического факультета Уральского политехнического института им. С.М. Кирова (ныне Уральского государственного технического университета) в городе Свердловске (ныне Екатеринбурге).
Это тепловые трубы с раздельными каналами для пара и жидкости. Один из вариантов такой конструкции представлен на рис. 26. Тепловая труба состоит из герметичного корпуса, содержащего испаритель 1, к которому присоединяется источник тепла, конденсатор 2, который подключается к приемнику тепла. Испаритель и конденсатор соединены между собой паропроводом 3 и конденсатопроводом 4. Обычно паровой канал 3 и жидкостный канал 4 – это пустотелые трубки небольшого диаметра. Мелкопористый фитиль 5 имеется только в испарителе. Он плотно посажен в корпус последнего. Откачка воздуха и заполнение трубы теплоносителем осуществляется через штуцер 6. Фитиль имеет пароотводные микроканалы 7, расположенные ради-
95
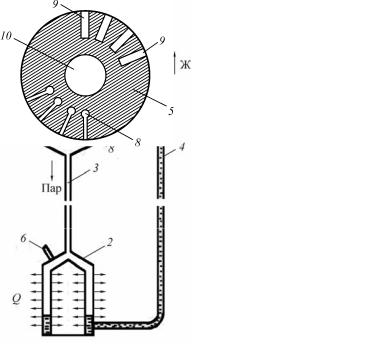
|
|
а |
б |
Рис. 26. Тепловая труба с раздельными каналами для пара и жидкости: а – общий вид; б – поперечное сечение испарителя
ально и паросборные каналы 8, расположенные вдоль испарителя. Продольные паросборные каналы могут быть выполнены в виде пазов 9 между ребер на внешней поверхности фитиля. Для приема жидкости во время работы имеется компенсационная полость 10. Количество рабочей жидкости, заправляемой в трубу, таково, что при пропитанном фитиле она при вертикальном положении трубы находится на уровне А–А. Это исключает вероятность отрыва жидкости от фитиля.
При подводе тепла к испарителю давлением пара паровой канал и конденсатор освобождаются от жидкости, кото-
96
рая поступает в компенсаторную полость. Объем компенсаторной полости и прилегающих к ней деталей таков, что она может полностью принимать эту жидкость.
Было разработано и испытано на различных жидкостях более десяти конструктивных вариантов таких тепловых труб. При этом изменялась длина тепловых труб, размеры испарителя, размеры и форма конденсаторов. Иногда их внешняя сторона делалась оребренной. В ряде конструкций компенсационная полость размещалась в «нижней» части испарителя, стенки этой полости и конденсатора иногда покрывались крупнопористым материалом, в ряде случаев к основному мелкопористому фитилю присоединялся небольшой крупнопористый фитиль, последнее позволяло несколько уменьшить объем заправляемой жидкости.
Но в основном эти изменения касались испарителя: изменялось количество и размеры как микроканалов, так и каналов для сбора пара, а также толщина запорной стенки фитилей. Изменялась пористость и структура самой массы фитилей, а следовательно, их проницаемость. При этом полная длина тепловых труб составляла 60–150 см, диаметр парового канала был 5–6 мм, а жидкостного около 3 мм. Диаметр испарителей изменился от 15 до 30 мм, а их длина от 60 до 120 мм. В зависимости от длины тепловых труб, теплоносителя и передаваемой мощности разность температур между испарителем и конденсатором колебалась от нескольких десятков до нескольких градусов. Опыт показал, что длина таких тепловых труб при работе в горизонтальном положении может составлять несколько метров.
Фитили изготовлялись из карбонильных порошков никеля путем прессования в цилиндрических пресс-формах при давлениях 800–900 кг/см. Используемые порошки имели 80 % частиц размером от 1 до 20 мкм. Карбонильные порошки имеют форму частиц, близкую к овальной, в отличие от никелевых электролитических порошков, у которых форма частиц
97
папоротниковообразная и которые после пресссования дают более высокую закрытую объемную пористость, а следовательно, более высокое гидравлическое сопротивление.
В шихту карбонильных порошков в качестве наполнителя добавлялась мочевина CO(NH2)2 в количестве от 10 до 40 % со средним размером частиц около 30 мкм. Температура плавления мочевины около 133 °С. Применение мочевины позволяло изменять открытую пористость фитилей в широких пределах: от 40 до 75 %. К тому же мочевина является хорошей смазкой, уменьшающей трение между стенкой пресс-формы и деталью. Это облегчает как само прессование, так и извлечение этой детали из пресс-формы.
Спекание фитилей производилось в кварцевой капсуле, которая подключалась к насосу через фильтр. В течение 4–5 часов температура медленно поднималась до 800–900 °С. Во время спекания мочевина испаряется и до температуры 500 °С среда в капсуле является восстановительной. Эту среду создают такие продукты разложения мочевины, как водород и окись углерода. Поэтому в значительной степени спекание порошка происходит по чистому металлу.
Спеченные заготовки фитилей являются достаточно прочными: они обтачиваются на токарном станке и в них выполняются необходимые отверстия. После охлаждения
вжидком азоте изготовленные фитили плотно вставляются
вкорпус испарителя.
Втаких конструкциях тепловых труб не только увеличивается длина теплопереноса и уменьшается длина фитилей, но благодаря наличию компенсационной полости и тонкой запорной стенки, отделяющей пар от жидкости, последовательное питание фитилей жидкостью заменяется на питание, близкое к параллельному.
Кроме этого, из-за малых размеров фитилей упрощается технология их изготовления и монтаж в корпус тепловой трубы.
98
Наличие раздельных каналов позволяет исключить тормозящее действие пара на встречный поток жидкости и нежелательный ее обогрев паром. Последнее уменьшает величину бесполезного обогрева жидкости, который и без того возникает из-за потерь давления в ней.
Наличие разделительных каналов позволяет в случае необходимости охлаждать жидкость после ее конденсации, регулировать мощность тепловой трубы с помощью вентиля, который можно устанавливать на паровом канале.
Такая конструкция также позволяет придавать испарителю и конденсатору желаемую форму, обеспечивает возможность изгибания тепловой трубы при ее изготовлении, монтаже и эксплуатации, позволяет ослаблять передачу вибрации от одного ее конца к другому, если какую-то часть этих каналов выполнять в виде змеевиков.
Раздельные каналы могут быть выполнены из диэлектрического материала, позволяющего электрически изолировать испаритель и конденсатор. Окончательное отключение тепловых труб (отпайка штуцера 6) от заправочного стенда производилась после ее работы в течение нескольких часов. Все детали труб, за исключением фитилей, были выполнены из нержавеющей стали.
Примеры применения тепловых труб. Применение технологии тепловых труб в производстве серной кислоты
Типовая теплотехнологическая схема производства серной кислоты способом ДК-ДА мощностью 1515 т моногидрата в сутки имеет существенный недостаток – низкую степень использования теплоты технологических процессов (не более 55 %). Анализ отдельных стадий этого производства позволил выявить структуру потерь эксергии: 1 % – в отделении комовой серы (вызваны разностью температур между твердой серой и паром, идущим на ее нагрев, т.е. связаны
99
с паровым обогревом сборников серы и серопроводов); 4 % – в узле подготовки питательной воды (при теплообмене); 14 % – в узле контактирования (связаны с процессом окисления сернистого ангидрида SО2 в серный ангидрид SО3 и с потерями при теплообмене); 14 % – в котле-утилизаторе (обусловлены разностью температур в несколько сотен градусов); 40 % – при охлаждении кислоты в моногидратных абсорберах (связаны со сбросом теплоты в окружающую среду через водооборотный цикл).
Более высокая степень использования теплоты процесса получения серной кислоты может быть достигнута, если проводить процесс абсорбции при высоких температурах («горячая» абсорбция). Возможно получение серной кислоты путем образования ее паров с последующей их конденсацией на поверхностях тепловых труб (термосифонов). Теплота конденсации и охлаждения серной кислоты используется для выработки насыщенного пара (Р = 0,6 МПа, t = 158 °С, G = = 9,08 кг/с), который целесообразно направлять как в технологические схемы, так и внешнему потребителю.
Другим вариантом поддержания необходимого температурного уровня серной кислоты в случае проведения процесса абсорбции при высоких температурах является охлаждение ее после моногидратного абсорбера в теплотехнологическом аппарате на основе тепловых труб (термосифонов) с получением насыщенного пара (Р = 0,6 МПа, t = 158 °C, G = 13,4 кг/c). Схема такого аппарата приведена на рис. 28. Это – теплообменное устройство, в кожухе которого установлены вертикально тепловые трубы (термосифоны).
Термосифон представляет собой герметически замкнутый объем, часть которого заполнена жидким теплоносителем (в данном случае – водой). Тепловой поток подводится к нижней части термосифона, отводится от верхней. При подводе теплоты к промежуточному теплоносителю в зоне нагрева происходит процесс испарения или кипения жидко-
100