
Энерготехнология химических производств
..pdf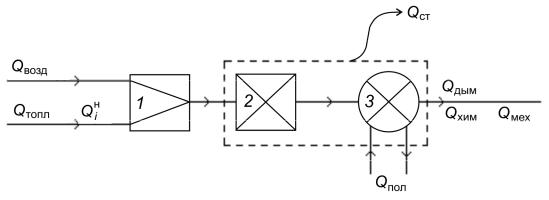
В зависимости от типа оборудования, параметров вырабатываемой тепловой энергии и текущего состояния и параметров эксплуатации оборудования на единицу вырабатываемой теплоты расходуется различное количество топлива (расходная норма). Более того, даже для однотипного оборудования, работающего на одинаковом топливе и вырабатывающего тепловую энергию одинаковых параметров, расходная норма будет различная, так как текущее состояние оборудования в каждом конкретном случае будет различным. Именно поэтому для каждого энерготехнологического агрегата составляется тепловой баланс, регламентирующий нормы полезно использующейся энергии и нормы ее потери. Иными словами, тепловые балансы численно определяют степень преобразования топлива в полезную энергию и, соответственно, совершенство энерготехнологического агрегата. При любой конструктивной модернизации агрегата или смене технологического режима они будут изменяться. Так как составление тепловых балансов относится к одной из основных задач заводского технолога, то рассмотрим порядок составления тепловых балансов для энерготехнологических агрегатов более подробно.
Из ранее пройденных технологических курсов известно, что в общем случае тепловой баланс любой технологической установки составляется путем уравнивания сумм потоков входящей и выходящей теплоты. Схема тепловых потоков энерготехнологической установки представлена на рис. 2.2.
Рис. 2.2. Тепловые потоки энерготехнологической установки: 1 – смеситель топки; 2 – топка (химический реактор); 3 – котел (теплообменник); Qтопл – физическая теплота потока топлива; Qвозд – физическая теплота потока воздуха; QiН – низшая теплота
горения топлива; Qпол – полезно используемая теплота; Qдым – физическая теплота дымовых газов; Qст – потери теплоты
через стенки установки; Qхим – потери теплоты с химическим недожогом; Qмех – потери теплоты с механическим недожогом
61
Таким образом, уравнение теплового баланса имеет вид
QН + Q |
+ Q |
= Q |
+ Q |
+ Q + Q |
+ Q . |
(2.26) |
i топл |
возд |
пол |
дым |
ст хим |
мех |
|
Условно разделим члены этого уравнения на группы и проведем их анализ.
К первой группе отнесем члены уравнения, величина которых определяется физической теплотой или энтальпиями потоков, а следовательно, их температурой. К этой группе относятся Qтопл,
Qвозд и Qдым.
Для их расчета можно использовать уравнение расчета физической теплоты потока (для изобарных условий)
Q = HG ≈ GСРТ. |
(2.27) |
Из уравнения теплового баланса видно, что положительными членами являются Qтопл и Qвозд, а отрицательным – Qдым. Таким образом, для улучшения показателей работы агрегата необходимо, чтобы потоки топлива и воздуха подавались в топку с максимально возможной температурой, а дымовые газы выбрасывались с минимально возможной температурой.
Ко второй группе отнесем «отрицательные» члены уравнения теплового баланса, определяющие потери тепла из-за несовершенства конструкции агрегата: Qст, Qхим и Qмех.
Для определения путей снижения потерь тепла через стенку аппарата (Qст) проведем анализ основного уравнения теплопередачи
Qст = КтрF tср, |
(2.28) |
где Ктр – коэффициент теплопередачи от дымовых газов в окружающую среду, определяемый коэффициентами теплоотдачи от дымовых газов к стенке котла (αдым–ст) и от стенки котла в окружающую среду (αст–о.с), теплопроводностью (λст) и толщиной стенки (δст):
Ктр = |
|
|
|
1 |
|
|
|
; |
(2.29) |
|
1 |
+ |
δст |
+ |
1 |
|
|||
|
|
|
|
|
|||||
|
|
αдым−ст |
|
λст |
|
αст−о.с |
|
|
|
F – площадь теплопередачи или наружная поверхность энерготехнологического агрегата;
62
tср – движущая сила теплопередачи, которая при условном постоянстве температуры дымовых газов и окружающей среды может быть рассчитана упрощенно:
tср = tдым – tо.с. |
(2.30) |
Таким образом, для снижения потерь тепла через стенку аппарата (Qст) необходимо:
–снизить коэффициент теплопередачи путем увеличения толщины теплоизоляции и за счет использования изоляционного материала с минимальной теплопрододностью;
–максимально защитить внутренние стенки котла от контакта
сдымовыми газами (снижение конвективной составляющей) и инфракрасного излучения зоны горения (уменьшение излучающей составляющей);
–уменьшить площадь теплопередачи путем максимального снижения размеров высокотемпературной зоны и модернизации наружной обмуровки агрегата на максимально более гладкую;
–снизить движущую силу теплопередачи за счет снижения температуры в пристенном пространстве топки.
Потери тепла с недожогами – химическим Qхим (содержание сажи, СО, Н2 и СН4 в дымовых газах) и механическим Qмех (содержание горючих элементов в золе или шлаке), – характеризующих степень совершенства горелок, как правило, определяются большим числом параметров (от состава топлива и типа горелок до коэффициента избытка воздуха) и носят нелинейный характер. В связи с этим такие потери тепла определяются пусконаладочными организациями и изображаются в виде графиков для определенного состава топлива в соответствии с режимной картой агрегата.
К третьей группе отнесем оставшиеся члены уравнения теп-
лового баланса: QiН и Qпол.
Низшая теплота сжигания топлива (QiН) определяется составом топлива и является «положительным» членом. Полезно используемая теплота (Qпол) определяется как конструкцией энерготехнологического агрегата, параметрами теплоносителя, так и технологическими параметрами работы агрегата. Анализ зависимости (Qпол) от текущих технологических параметров можно провести, также используя основное уравнение теплопередачи (как при анализе Qст). Однако выводы в данном случае будут противоположные, т.е необходимо:
63
–увеличить коэффициент теплопередачи путем уменьшения толщины стенок труб и за счет использования материала труб с максимальной теплопрододностью и прочностью;
–максимально турбулизовать поток дымовых газов и улучшить омывание ими теплопередающих поверхностей (увеличение конвективной составляющей) и активизировать теплоотдачу за счет инфракрасного излучения зоны горения (увеличение излучающей составляющей);
–увеличить удельную площадь теплопередачи (оребренные трубы, трубы меньшего диаметра и т.д.);
–увеличить движущую силу теплопередачи за счет увеличения температуры дымовых газов и снижения температуры теплоносителя.
Одним из наиболее важных параметров, характеризующих полноту использования располагаемой теплоты, является КПД-брутто энерготехнологического агрегата, т.е. КПД без учета затрат энергии на собственные нужды, который равен отношению полезно используемой теплоты к располагаемой теплоте (сумме низшей теплоты сжигания топлива и физической теплоты топлива). Для типичного агрегата, работающего на газовом топливе, величина КПД-брутто имеет значение 85–94 %.
Следует помнить: так как в России при расчетах КПД энерготехнологического агрегата используется низшая теплота сжигания топлива, то температура дымовых газов не должна быть меньше или равна температуре их точки росы. Таким образом, низшая теплота сжигания топлива будет использоваться на 100 %, в случае когда температура дымовых газов будет равна температуре точки росы,
или 55–60 °С. Если энерготехнологический агрегат предусматривает более сильное охлаждение дымовых газов с конденсацией водяных паров из дымовых газов, то в расчетах необходимо использовать высшую теплоту сжигания, так как стандартный расчет с низшей теплотой сжигания будет давать значение КПД более 100 %. Иными словами, при изменении исходных данных может возникнуть необходимость в смене «идеальных» параметров, по которым определяется степень совершенства процесса преобразования тепла, на другие – более строгие. Кроме того, необходимо быть очень внимательным при сравнении эффективности работы отечественного и импортного оборудования по их КПД.
Указанное особенно важно учитывать для вновь проектирующихся агрегатов, так как в связи с повышающейся стоимостью топлива возникает необходимость более полного использования тепло-
64

ты, и в первую очередь теплоты дымовых газов, которая из совокупности потерь энерготехнологического агрегата имеет наибольшее абсолютное значение. Однако в этом случае возникают другие проблемы, связанные с коррозией поверхностей нагрева (содержащиеся в дымовых газах SO2 и NOx, растворившись в конденсате, образуют кислоту) или с экологией (холодные дымовые газы, содержащие SO2 и NOx, плохо рассеиваются в атмосфере), которые необходимо будет решить.
2.6. Особенности сжигания газового топлива
Ранее было показано, что топливо может быть в трех агрегатных состояниях: твердом, жидком и газообразном. Наиболее используемым является газовое топливо, поэтому рассмотрим процесс его сжигания более подробно.
Существуют два способа подачи газового топлива на сжигание: оно может подаваться в топку (химический реактор) (реакции глубокого окисления) либо отдельно от воздуха (смешение происходит в топке), либо предварительно смешиваясь с ним. Если топливо предварительно смешано с воздухом, то горючая смесь уже готова для сжигания, поэтому процесс горения будет определяться скоростью химической реакции (кинетикой). В данном случае он называ-
ется кинетическим.
Как известно из курса общей химической технологии, скорость химической реакции зависит от концентрации реагентов и температуры процесса, причем скорость процесса возрастает с увеличением температуры по экспоненциальному закону:
− Eакт |
N M |
|
|
r = k0e RT |
(2.31) |
||
CтоплCO2 . |
Если учесть, что процесс является экзотермическим, то скорость горения будет увеличиваться с ростом температуры по экспоненциальному закону, поэтому процесс будет самоускоряться, что может привести даже к взрыву. Экспериментально доказано, что процесс гомогенного горения водорода и углеводородов протекает по радикальному механизму (рис. 2.3), изменение скорости которого во времени показано на рис. 2.4.
Как видно из графика на рис. 2.4, сначала при прохождении экзотермической химической реакции происходит «накачка» системы энергией с увеличением количества радикалов (скорость их образо-
65
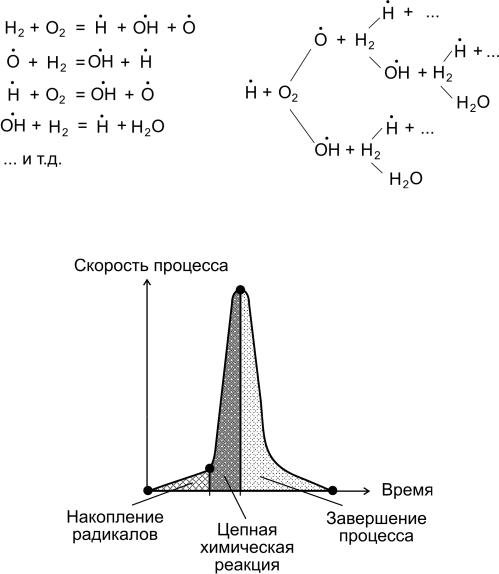
вания несколько превышает скорость их расходования) до тех пор, пока не будет достигнут некий уровень энергии системы, при котором становится возможным цепной механизм протекания реакции.
Рис. 2.3. Схема радикального (цепного) механизма горения водорода
Рис. 2.4. Изменение скорости радикального процесса во времени
При протекании реакции по цепному механизму радикалы образуются лавинообразно, что приводит к еще большему увеличению скорости процесса и «накачке» системы энергией, что способствует образованию других радикалов. Этот процесс может завершиться лишь только тогда, когда израсходуются исходные реагенты.
Так как время протекания химической реакции по цепному радикальному механизму ничтожно мало, а в этот промежуток времени выделяется все тепло химической реакции (адиабатное горение), то при таком способе сжигания можно достичь очень высоких тем-
66
ператур. С одной стороны, это играет положительную роль, так как известно, что с увеличением температуры движущая сила процесса теплопередачи будет увеличиваться, а с другой – отрицательную, поскольку для материала теплопередающего оборудования существуют ограничения, связанные с его термостойкостью и теплонапряженностью. По данным причинам кинетическое горение применяется только в особых случаях: в двигателях внутреннего сгорания, газовых резаках для металла и т.п.
Если в топку подавать топливо и воздух раздельно, то процесс горения будет определяться скоростью смешения этих потоков. Так как скорость смешения двух газовых потоков достаточно мала
иопределяется скоростью молекулярной диффузии, а процесс окисления протекает практически мгновенно, то данный способ сжигания топлива называется в соответствии с лимитирующей стадией процесса диффузионным. В промышленности он используется достаточно широко, так как, во-первых, исключается необходимость в транспортировке взрывоопасной смеси, а, во-вторых, для более равномерного нагрева поверхности необходимо увеличить площадь излучения (т.е. размер факела) и т.п.
Из курса общей химической технологии известно, что для проведения химической реакции в реакторе (топке) с определенным заданным объемом необходимо соблюдать соответствующие концентрационные и температурные условия, определяющие скорость химической реакции. Так как в большинстве существующих энерготехнологических установок используются «огневые» топки, или плазмохимические реакторы, то для стабильного существования пламени (плазмы) необходимо выдерживать достаточно жесткие концентрационные и температурные пределы.
Для газового топлива заданного состава существуют низший
ивысший концентрационные пределы горения топлива, которые совпадают с концентрационными пределами взрываемости, т.е. вне этих пределов стабильное существование пламени (плазмы) невозможно. В качестве примера в табл. 2.2 даны концентрационные пределы различных видов топлив в воздухе.
Если концентрация топлива в воздухе ниже или выше соответствующего концентрационного предела, то такая смесь считается пожаро- и взрывобезопасной. Однако следует обратить внимание на то, что за счет макроэффектов перемешивания при смешении высококонцентрированных газовых смесей или чистых газов даже с большим количеством воздуха могут возникнуть отдельные очаги
67
взрывоопасной концентрации. При этом стехиометрическая смесь может загореться (химическая реакция) лишь в том случае, когда энергия молекул превысит энергетический барьер начала химической реакции. Так как энергия молекул зависит от температуры, то необходимо, чтобы температура смеси превысила температуру самовоспламенения. Для различных топлив эта температура будет разная: для СН4 − 650–750 °С, С2Н2 − 406–440 °С, Н2 − 580–590 °С, СО − 644–658 °С.
Таблица 2 . 2 Концентрационные пределы горения некоторых веществ
Характеристика |
|
|
|
Топливо |
|
|
|
|
|
|
Коксовый |
Пары |
|
смеси |
CH4 |
C3H8 |
H2 |
CO |
||
|
|
|
|
|
газ |
бензина |
Нижний предел (избыток воздуха, α > 1) |
5 |
2 |
4,1 |
12,5 |
5,6 |
≈2,4 |
Стехиометрическая смесь (α = 1) |
9,5 |
4 |
29,6 |
29,6 |
18,8 |
– |
Верхний предел (недостаток воздуха, α < 1) |
15 |
9,5 |
75 |
75 |
30,8 |
≈4,9 |
Таким образом, для существования пламени необходимо одновременное выполнение двух условий:
1)концентрация топлива в воздухе должна быть выше нижнего концентрационного предела и ниже верхнего концентрационного предела;
2)температура топливовоздушной смеси должна быть выше температуры самовоспламенения.
При этом совсем не обязательно, чтобы температура горючей смеси была выше температуры самовоспламенения во всем объеме. Поскольку реакции окисления топлива кислородом воздуха являются экзотермическими, то достаточно инициации процесса в любой точке объема, так как после начала химической реакции горения экзотермический процесс может идти автотермически. В связи
сэтим даже малейшая искра может вызвать взрыв.
Кроме «огневых», существуют «беспламенные» топки (реакторы глубокого каталитического окисления), которые работают практически при любом соотношении реагентов, но при температуре большей, чем температура зажигания катализатора (300–600 °С), и меньшей, чем температура его деструктурирования (900–1200 °С). Данный тип топок является достаточно перспективным, так как катализатор позволяет управляемо проводить процесс глубокого окисления газового топлива без угрозы взрыва и побочных химических реакций образования сажи, СО и т.п. и даже «сжигать» топливные смеси вне концентрационных
68
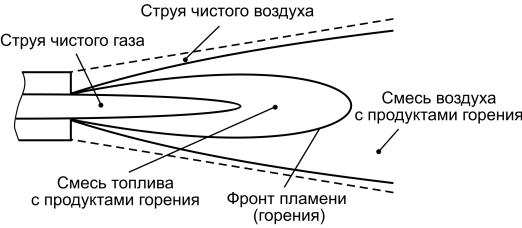
пределов, поскольку при этом способе пламя отсутствует. Однако для этого способа требуются специальные катализаторы, имеющие широкий температурный интервал работы и надежные автоматические системы управления процессом (чтобы не вывести катализатор из строя). В настоящее время этот способ начинает применяться, например, для стационарных газовых турбин и т.д. Тем не менее сейчас в промышленности наиболее распространенным остается «огневой» способ сжигания топлива, поэтому рассмотрим его более подробно.
Ранее было указано, что при раздельной подаче в топку топлива и воздуха скорость процесса будет определяться молекулярной диффузией. В зависимости от режима движения газового потока различают ламинарную и турбулентную диффузию. В свою очередь, при низких скоростях потоков топлива и воздуха режим их движения ламинарный (Re < 2300), т.е. в них отсутствуют турбулентные вихри, и скорость горения определяется исключительно молекулярной диффузией. Длина факела в данном случае будет максимальная. При увеличении скорости потоков (Re > 2300) в них образуются турбулентные вихри, которые улучшают перемешивание и уменьшают длину факела. Схема факела при горении газового топлива представлена на рис. 2.5.
Рис. 2.5. Схема факела при горении газового топлива
На рис. 2.5 видно, что потоки чистого газа и чистого воздуха раздельно подаются в топку, где происходит:
1)их смешение с образованием горючей смеси;
2)подогрев горючей смеси при смешении с продуктами горения до температуры самовоспламенения;
3)горение горючей смеси (фронт пламени);
4)удаление дымовых газов из топки.
69
Как следует из механизма сжигания топлива, который состоит из последовательных стадий, плохие смешение и подогрев смеси или низкая скорость истечения могут привести либо к потуханию факела, либо к хлопкам, приводящим к разрушению горелок или топки. Таким образом, горелки должны обеспечивать хорошее перемешивание горючего с воздухом и надежное горение факела без погасаний и пульсаций.
2.7.Горелки для сжигания газового топлива
игазофазных отходов
Наиболее широкое распространение в промышленности получили горелки для сжигания газового топлива. Однако до сих пор не установлена единая классификация горелочных устройств. Так, например, их можно классифицировать по теплопроизводительности, давлению газа, давлению воздуха, длине пламени, способам подачи горючего и окислителя, целям применения, закрученному или прямоточному потокам воздуха и газа, методу смешения и т.п. Классификация горелок также может производиться и по определяющим характеристикам, которые положены в основу физической сущности протекающих процессов. Внутри этой классификации горелки можно подразделить по давлению газа, характеру факела, длине пламени, теплопроизводительности и др. Кроме того, определяющим может быть относительное количество первичного воздуха и процесс его смешения с топливом (воздух, непосредственно подаваемый в газовые горелки, называется первичным, а поступающий из топочного пространства – вторичным).
Для сжигания газового топлива различают два основных типа горелок:
1)инжекционные (воздух поступает под действием разряжения, созданного газовыми струями и тягой в камере горения);
2)с принудительной подачей воздуха.
К горелкам первого типа относят горелки:
–диффузионного типа, низкого и среднего давления (αперв. возд = 0);
–атмосферного типа (αперв. возд = 0,3–0,7);
–эжекционного типа, среднего и высокого давления (αперв. возд > 1).
Горелки второго типа бывают низкого и среднего давления
(αперв. возд > 1).
Рассмотрим эти горелки более подробно.
70