
Оборудование для подготовки материалов
..pdf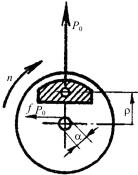
действием силы равной P0, тогда а = |
Р0 |
и K = |
Р0 |
= |
G0n2ρ |
; но |
||||||
4K |
4а |
|
||||||||||
|
|
|
|
|
|
|
|
3600a |
||||
т. к. K = |
Gn2 |
, отсюда |
|
|
|
|
|
|
|
|
|
|
|
|
|
|
|
|
|
|
|
|
|
||
3600 |
|
|
|
|
|
|
|
|
|
|
|
|
|
|
G0 |
= |
Ga |
|
|
|
|
|
|||
|
|
|
|
|
|
|
|
|
||||
|
|
ρ |
|
|
|
|
|
|
|
|||
или |
|
|
|
|
|
|
|
|
|
|
|
|
|
|
G ρ = |
3600aK |
. |
|
|
|
|
|
|||
|
|
0 |
|
n2 |
|
|
|
|
|
Приближенно считаем, что при работе сита при резонансе мощность расходуется только на преодоление трения в подшипниках, тогда:
N |
|
= |
P0 f π dn |
= |
G0 fn3ρ d |
л. с., |
|
|
|
||||
|
тр |
|
60 75 129 104 |
|
где f — коэффициент трения; d — диаметр вала.
При работе сита без резонанса (в случае перегрузки сита), когда tc ≠ tв
все соотношения, рассмотренные ранее, остаются в силе, но при этом необходимо затратить дополнительную
мощность на сообщение ситу колебания с амплитудой ± a. Эта мощность
NK = 2 |
mυ 2max |
n |
л. с., |
||
2 |
|
60 75 |
|||
где множитель 2 введен потому, |
что максимальная скорость |
( υ max ) сообщается ситу дважды за один оборот вала; υ max= 2υ ср ;
71
средняя скорость ( υ ср ) колебания равна пути (4a), деленному на
время полного оборота |
60 |
. |
|
|
|
|
|
|
||||||
|
|
|
|
|
|
|
|
|||||||
|
|
|
|
|
|
п |
|
|
|
|
|
|
||
Тогда |
|
|
|
|
|
|
|
|
|
|
|
|
|
|
|
= 2 |
1 |
2 4ап 2 |
п |
|
= |
Gn3a2 |
|
л. с. |
|||||
NK |
|
|
|
|
|
|
|
|
|
|
|
|||
2 |
|
60 |
|
60 |
|
248 10 |
4 |
|||||||
|
|
|
|
|
75 |
|
|
Суммарная мощность, затрачиваемая при колебании сита без резонанса,
N= Nтр + N K .
1.2.2.3.Барабанные сита
Барабанное сито представляет собой цилиндрический или конический барабан с сетчатой боковой поверхностью, вращающийся около горизонтальной или слегка наклонной оси (рис. 1.37). Внутрь барабана с одного конца непрерывно загружают материал, который при вращении барабана просеивается через его сетку. Крупные части (отсев) проходят всю длину барабана и выходят из него сдругогоконца, переваливаясь через край.
Цилиндрические сита (рис. 1.37, а) делают с наклонной осью и монтируют на валу либо на бандажах, вращающихся на роликах. Большие цилиндрические сита делают с регулируемым углом наклона оси для изменения скорости движения материала вдоль сита, в зависимости от способности его просеиваться.
Конические сита ставят на горизонтальной оси с питанием в узкий конец барабана (рис. 1.37, б) либо на наклонной оси с питанием в широкий конец (рис. 1.37, в). Последняя схема рациональнее, так как через широкий конец барабана проходит наибольший поток материала, и использование просеивающей поверхности сита наилучшее. При заданной производительности диаметр сита, представленного на рис. 1.37, в, должен быть меньше, чем диаметр сита, представленного на рис. 1.37, б.
72
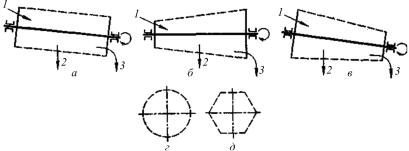
Рис. 1.37. Барабанные сита: 1 — загрузка материала; 2 — выход продукта; 3 — отсев
В сечении барабанные сита бывают круглые (рис. 1.37, г) и многоугольные (рис. 1.37, д). Последние носят название полигональных. Полигональные сита имеют большую производительность, чем сита круглого сечения тех же размеров, так как материал при вращении полигонального сита переваливается с грани на грань и благодаря ударам быстрее просеивается. Размеры ячеек сетки барабанных сит для оборотной смеси 6–12 мм. Рационально применение сетки с прямоугольными ячейками размером 6 × 12 — 6 × 20 мм.
Основное достоинство барабанных сит — медленное и равномерное, без толчков и сотрясений, вращение. Недостатки — неполное (12–20 %) использование поверхности сита и невысокая эффективность просеивания, обусловленная тем, что материал движется параллельно полотну сита, а не перпендикуляр-
но, как |
у вибросит. КПД просеивания барабанных сит |
ε = 0,6… |
0,75 . На рис. 1.38 представлено барабанное коническое |
полигональное сито.
Рассмотрим движение просеиваемого материала в барабане цилиндрического сита. Предельное положение равновесия частицы материала на внутренней поверхности неподвижного барабана сита будет в точке A, лежащей на радиусе с углом ϕ тре-
ния материала о сито (рис. 1.39). При вращении к действующим силам добавляется центробежная сила инерции. Новая точка B
73
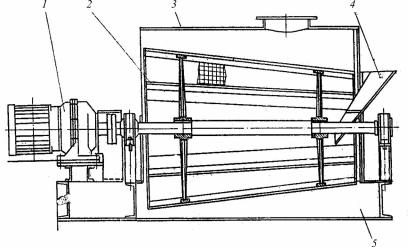
предельного положения равновесия будет характеризоваться углом поднятия β > ϕ , который определится из условия
G sinβ = Pf ,
где Pf — сила трения, возбуждаемая как радиальной составляющей G cosβ веса G частицы, так и центробежной си-
лой
Р0 = |
G |
πn 2 |
||
|
|
|
R . |
|
|
||||
|
g |
30 |
|
Рис. 1.38. Барабанное полигональное сито: 1 — привод; 2 — полигональный барабан; 3 — кожух; 4 — загрузочная воронка; 5 — рама сита
Таким образом, имеем
|
|
G |
π 2n2 R |
||
G sinβ = |
f G cosβ + |
|
|
|
, |
|
|
|
|||
|
|
9,81 |
900 |
74
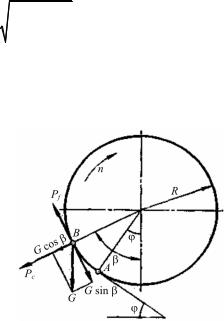
где f = tg ϕ — коэффициент трения. Отсюда частота вращения сита, об/мин,
n = 30 |
sin (β − ϕ ) |
, |
|
R sin ϕ |
|||
|
|
где R — радиус барабана сита, м.
Угол поднятия β рекомендуется брать в пределах β = ϕ + (5… 10° ) , но не боль-
ше β = 48° .
Для выяснения характе- |
|
||||
ра движения частицы мате- |
|
||||
риала |
вдоль |
барабана |
сита |
|
|
рассмотрим |
схему |
на |
|
||
рис. 1.40. Частица, вращаясь |
|
||||
вместе с барабаном, подни- |
|
||||
мается от точки 1 до точки |
|
||||
2, лежащей на радиусе с уг- |
|
||||
лом поднятия β . При даль- |
|
||||
нейшем поднятии |
равнове- |
|
|||
сие |
частицы |
нарушается, |
Рис. 1.39. Угол поднятия частицы на |
||
и она |
начинает |
скользить |
барабанном сите |
вниз по внутренней поверхности барабана по линии наибольшего ската. Направление этой
линии составляет с направлением касательной к окружности в точке 2 угол, величина которого ψ ≈ 2α . Израсходовав свою
живую силу, частица остановится в некоторой точке 3 и отсюда снова будет подниматься, вращаясь вместе с барабаном, до новой точки 4, в которой она снова потеряет равновесие на барабане и опять начнет соскальзывать.
При достаточно правильной, ровной внутренней поверхности барабана и постоянном коэффициенте трения величина отрезков соскальзывания частицы 2–3, 4–5 и т. д. будет весьма малой и в пределе равной нулю. В своем абсолютном движении
75
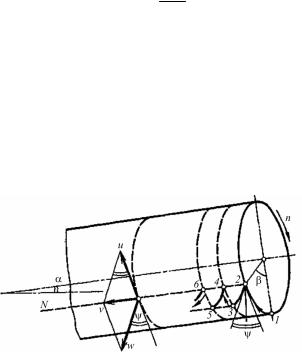
частица будет перемещаться вдоль оси сита по образующей 2N с некоторой скоростью υ . Относительно же сита частица будет двигаться по винтовой линии с углом подъема ψ .
Как видно из параллелограмма скоростей, эта абсолютная скорость υ частицы является геометрической суммой окружной
переносной скорости u = πRn и относительной скорости ω , на30
правленной под углом 180 − ψ = 180 − 2α к скорости u. Отсюда осевая скорость движения материала вдоль сита
υ = u tg 2α = π Rn tgα2 . 30
Материал в барабане сита, перемещаясь вдоль его оси, постепенно просеивается таким образом, что площадь сечения материала, которая имеет вид сегмента, будет по длине сита переменной.
В начале барабана, в месте загрузки сита, центральный угол сегмента загрузки, по практическим данным, не должен превышать 90°. По другим данным рекомендуется иметь величину стрелки сегмента h = 0,1 до 0,125R.
Рис. 1.40. Движение частицы вдоль барабанного сита
Имея площадь сечения F материала в сите (площадь сегмента) в месте загрузки и рассматривая движущийся вдоль оси
76
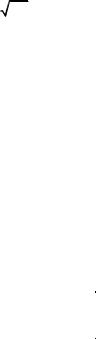
сита сегмент как одно целое, получим производительность барабанного сита, т/ч,
Q = 3600µγυ F ,
где — коэффициент относительного разрыхления материала при просеивании, равный 0,8–0,95;
γ— плотность материала, т/м3;
υ— осевая скорость движения материала вдоль барабана
сита, м/с;
F — площадь сечения материала в сите (площадь сегмента) в месте загрузки сита, определяемая приближенно по формуле
F = 1,9h Rh м2,
где h — стрелка сегмента, м;
R — радиус барабана сита, м.
Длину барабана сита, м, чаще всего принимают в пределах 4–5R. Можно приближенно также считать, что на 1 т/ч просеиваемой отработанной формовочной смеси требуется 20–30 дм2 поверхности барабанного сита. Мощность, потребляемая барабанными ситами, берут по практическим данным.
Наша промышленность выпускает следующие типы сит
(табл. 1.1).
Таблица 1 . 1
Сита для просеивания формовочных материалов и смесей
|
Наименование |
Модель |
Произво- |
Наибольший |
Установленная мощ- |
|
дитель- |
размер ячейки |
ность электродвигате- |
||
|
оборудования |
||||
|
|
ность, м3/ч |
сита, мм |
ля, кВт |
|
|
|
13321 |
25 |
20 |
– |
Сито |
вибрационное |
|
|
|
|
13322 |
40 |
20 |
– |
||
грубой очистки |
|
|
|
|
|
13324 |
100 |
20 |
– |
||
|
|
13326 |
240 |
20 |
30 |
Сито |
вибрационное |
13331 |
25 |
12 |
– |
тонкой очистки |
13332 |
40 |
12 |
– |
77
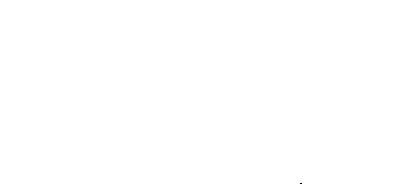
Окончание табл. 1 . 1
Наименование |
Модель |
Произво- |
Наибольший |
Установленная мощ- |
||
дитель- |
размер ячейки |
ность электродвигате- |
||||
оборудования |
||||||
|
ность, м3/ч |
сита, мм |
ля, кВт |
|||
|
13334 |
100 |
|
12 |
– |
|
|
|
|
|
|
|
|
|
13336 |
240 |
|
12 |
18,5 |
|
|
173М1 |
5 |
|
16 |
1,1 |
|
|
174М1 |
10 |
|
16 |
1,5 |
|
Сито барабанное поли- |
175М |
20 |
|
16 |
3,0 |
|
гональное |
176М |
40 |
|
16 |
5,5 |
|
|
178М |
80 |
|
16 |
7,5 |
|
|
179 |
125 |
|
16 |
10,0 |
1.2.3.Оборудование для гомогенизации и охлаждения отработанной смеси
Отработанная формовочная смесь после выбивной решетки в литейных цехах поточно-массового производства с применением сырых литейных форм неравномерна по своей температуре и влажности. В зависимости от того, из какой части формы ее выбили, ближе или дальше расположенной от отливки, температура ее может достигать 80–120 °С и выше, а влажность — колебаться в пределах от нуля до 3 %. Поэтому при подготовке отработанной смеси, кроме магнитной сепарации и просеивания, необходимо также усреднение ее по влажности (гомогенизация) и охлаждение до температуры, близкой к комнатной.
Гомогенизация отработанной смеси частично осуществляется при ее просеивании. Однако в современных смесеприготовительных системах, имеющих в своем составе установки для испарительного охлаждения, эффективная гомогенизация отработанной смеси осуществляется в агрегате предварительного увлажнения на входе в эти установки.
На рис. 1.41 приведена принципиальная схема установки для испарительного охлаждения отработанной формовочной смеси, апробированной многолетней практикой. В установке смесь перед испарителем (охладительным конвейером) проходит через лопаточный смеситель, где она подвергается предва-
78
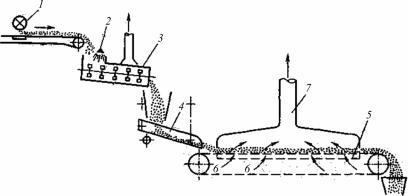
рительному увлажнению. В настоящее время эта операция в такого рода установках производится в особых смешивающих барабанах, или гомогенизаторах (рис. 1.42).
Рис. 1.41. Схема установки для испарительного охлаждения отработанной формовочной смеси: 1 — весы; 2 — увлажнение; 3 — лопаточный смеситель; 4 — виброжелоб; 5 — перфорированный пластинчатый конвейер; 6 — воздух от вентилятора; 7 — отсос
Гомогенизирующий цилиндроконический барабан вращается около оси, наклоненной под углом 18° к горизонту. Отработанная смесь непрерывно поступает внутрь барабана через его открытый торец с ленточного конвейера, имеющего скорость 1,3 м/с, в направлении под углом 30° к оси барабана в плане и непрерывно выходит из барабана, переваливаясь через его кромку. Вода для увлажнения подается внутрь барабана через восемь форсунок, включаемых автоматически в зависимости от влажности поступающей смеси. Чтобы смесь не налипала на поверхность барабана, он подогревается лампами инфракрасного излучения на 3–5° выше температуры смеси. Для предотвращения коррозии барабан изготовляют из коррозионно-стойкой стали.
79
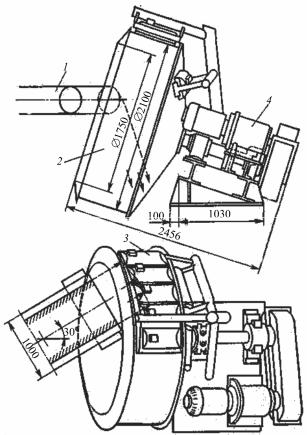
Рис. 1.42. Гомогенизатор: 1 — ленточный конвейер для подачи отработанной смеси в барабан; 2 — гомогенизационный барабан; 3 — нагреватели; 4 — привод. Объем смеси в барабане 1,35 м3; частота вращения 25,6 об/мин; число нагревателей 7; мощность нагревателей 21 кВт; мощность электродвигателя 18 кВт
На рисунке показан гомогенизационный барабан пропускной способностью 200 т/ч. Такие гомогенизаторы и соответствующие им охладители системы Бюрера строятся швейцарской фирмой «Фишер», их пропускная способность 100–400 т/ч. Установки испарительного охлаждения с гомогенизационными
80