
Промышленное применение лазеров
..pdfДругая область успешного применения лазерной резки связана с распиловкой керамических подложек сложной формы. Простое разделение пластины глиноземной керамики на прямоугольные под ложки с прямолинейными краями отреза можно, по-видимому, осу ществить значительно проще путем скрайбирования, которое будет рассмотрено ниже.
При изготовлении многих интегральньгх схем возникает необхо димость в нарезке керамических подложек сложной формы. Процесс изготовления таких подложек обычными методами оказывается слиш ком дорогостоящим и медленным. В то же время применение ССЬ-ла- зеров позволяет нарезать подложки неправильной формы из стандарт ных прямоугольных заготовок и существенно сокращает расходы на их изготовление. В одной из таких систем применен непрерывный ССЬ-лазер мощностью 250 Вт. Она позволяет нарезать из глиноземной пластины толщиной 0,6 мм подложки со сложным контуром при ли нейной скорости резки 1,2 см/с. Перемещение лазерного пучка по за данному контуру осуществляется с помощью пантографа. Время, не обходимое для вырезания типичной подложки из исходной заготовки при условии хорошего воспроизведения деталей контура и высокого качества края отреза, не превышает 30 с. Стоимость изготовления подложки указанным способом оказывается ниже, чем при использо вании обычных методов резки. Кроме того, лазерный метод позволяет значительно сократить разнообразие форм исходных заготовок, по скольку достаточно иметь .лишь прямоугольные заготовки.
Большие возможности технология лазерной резки открывает в про изводстве гибридных интегральных схем. Одной из основных операций этого производства является подгонка номиналов тонко- и толстопленоч ных резисторов интегральных схем, которая традиционно выполняется струей сжатого воздуха с абразивным материалом. Применение лазерной технологии позволяет повысить производительность изготовления рези сторов с 1-М-тыс. резисторов в час до 2(К30 тыс.
Лазерная резка импульсным излучением применяется для полу чения пазов в кристаллах естественных алмазов перед их распилов кой дисками, шаржированными алмазным порошком. В этом случае
по сравнению с традиционной обрабогкой при лазерной резке паза шириной 0,1 мм и глубиной 0,5 мм вместо 15 мин требуется 5 с.
Технология лазерной резки незаменима при изготовлении дета лей из слюдыслюда не расслаивается, практически отсутствует дефектный слой.
Применение СС>2-лазеров для резки материалов на основе ба зальтовых волокон связано с тенденцией увеличения использования материалов на основе базальтового волокна. Ранее изделия из ба зальтовых волокон были практически недоступны, но по мере разви тия науки и техники применение этих материалов охватывает все большие области. В связи с этим возникает необходимость обработ ки данных материалов.
Применяемые в настоящее время методы механического рас кроя материалов на основе базальтового волокна отличаются суще ственными недостатками, такими как: невысокая точность реза, низ кая скорость резки, быстрое изнашивание режущего инструмента, расслоение материала в направлении, перпендикулярном резу, рас пад листа на отдельные волокна и т.д. В связи с этим встает вопрос о получении качественного материала.
На предприятии «Исток-Лазер» (дочернем предприятии корпо рации «Исток», г. Фрязино) были отработаны технологические режи мы резки материалов на основе базальтового волокна. Результаты этой работы позволили следующие преимущества лазерной резки по срав нению с традиционными методами раскроя материалов (рис. 4.4):
-отсутствие расслоения волокон с одновременным оплавлени ем поверхности реза, что позволяет существенно увеличить износо стойкость материала;
-высокая скорость лазерной резки значительно увеличивает производительность;
- исключаются затраты средств и времени на изготовление
изамену режущего инструмента;
-технологические режимы лазерной резки позволяют обраба тывать материалы различной толщины (ткань от 1 до 8 и более слоев, картон от 5 до 50 мм, вату 1 и 2 слоев) и химического состава, что
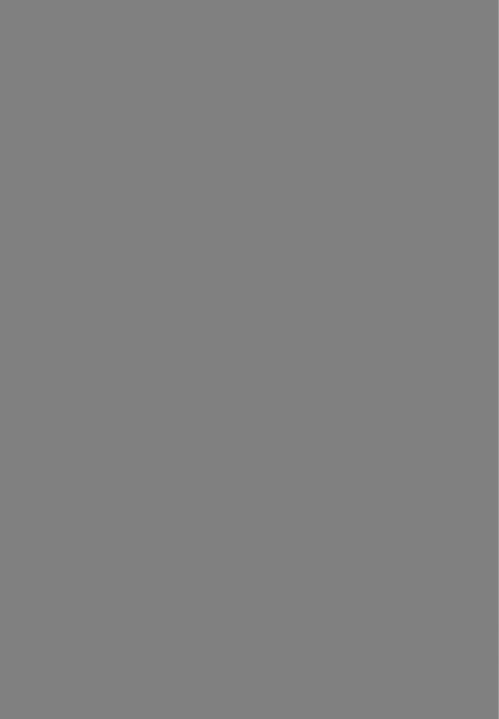
Резка металлов
На начальном этапе развития лазерной техники технология резки металлов развивалась очень медленно. Чтобы обеспечить резку метал лов. обладающих высокой теплопроводностью и высоким коэффици ентом отражения от поверхности, с достаточно высокой скоростью, необходимы большие значения средней мощности излучения. Указан ную проблему удалось разрешить в результате создания мощных лазе ров. Так как средняя мощность излучения должна быть большой, для резки металлов чаще всего используются С02-лазеры. Требуемая мощность лазерного излучения была снижена за счет применения ме тода лазерной резки с одновременной продувкой кислорода.
В этом случае большая часть энергии, затрачиваемой на резку, получается за счет экзотермических реакций между металлом и ки слородом. Лазерное излучение нагревает материал до точки возгора ния, а сам процесс резки протекает в результате реакции металла с кислородом. Указанный процесс позволяет разрезать с высокой ско ростью металлические пластины большой толщины при мощности источника лазерного излучения всего лишь в несколько сотен ватт. В присутствии кислородной струи скорость резки возрастает пример но на 40 % по сравнению с резкой в присутствии струи инертного газа.
В наиболее типичной конструкции кислородная форсунка рас полагается коаксиально с лазерным пучком. Пучок С02-лазера фоку сируется через форсунку на поверхность обрабатываемого образца с помощью линз, изготовленных из прозрачного в ИК-области мате риала (например, германия или галоидов щелочных металлов). Обычно для подачи кислорода используются конусные форсунки диаметром 1,3-К>,5 мм, работающие при давлении Н2 атм.
В табл. 4.3 приведены значения скорости резки, достижимые при использовании лазерно-кислородного метода на С02-лазерах с мощностью порядка нескольких сотен ватт. Данные таблицы при ведены лишь для того, чтобы проиллюстрировать уровень достигну тых в экспериментальных условиях скоростей резки, и поэтому от нюдь не обязательно являются оптимальными. Более того, получен
ные различными авторами значения скорости резки могут различать ся даже при одинаковых условиях проведения эксперимента. Причи ной указанных различий могут быть неконтролируемые параметры и возможные различия методик измерения мощности.
|
|
|
Таблица 4.3 |
|
Резка металлов излучением СОг-лазера |
|
|||
Материал |
Толщина, мм |
Мощность |
Скорость рез |
|
лазера, кВт |
ки, м/мин |
|||
|
|
|||
|
1,0 |
3,0 |
6,35 |
|
Алюминий |
3,2 |
4,0 |
2,54 |
|
6,4 |
3,8 |
1,02 |
||
|
12,7 |
5,7 |
0,76 |
|
|
12,7 |
10 |
1,02 |
|
Инконель |
12,7 |
11 |
1,27 |
|
|
0,3 |
200 |
2,3 |
|
Нержавеющая сталь |
0,3 |
350 |
4,3 |
|
1,6 |
250 |
1,3 |
||
|
2,8 |
250 |
0,25 |
|
|
3,2 |
3,0 |
2,54 |
|
Малоуглеродистая сталь |
3,2 |
3,0 |
2,54 |
|
16,8 |
3,0 |
1,14 |
||
Углеродистая сталь |
||||
3,2 |
190 |
0,56 |
||
|
0,5 |
135 |
15,0 |
|
Титан |
6,4 |
3,0 |
3,56 |
|
17,0 |
240 |
6,1 |
||
|
31,8 |
3,0 |
1,27 |
|
|
50,8 |
3,0 |
0,51 |
|
|
1,3 |
210 |
7,6 |
|
Титановый сплав (сплав 6A14V) |
2,2 |
210 |
3,8 |
|
5,0 |
850 |
3,3 |
||
|
6,4 |
250 |
2,8 |
|
|
7,4 |
260 |
2,5 |
|
Сплав Rene |
0,5 |
250 |
2,0 |
|
1,3 |
250 |
0,5 |
||
|
||||
Сплав циркалой |
0,5 |
230 |
15,0 |
Без продувки кислорода резка осуществляется на существенно меньших скоростях. Значения скорости резки довольно большие и представляют интерес для промышленности. Для того чтобы пре дотвратить сгорание материала, можно воспользоваться защитным инертным газом (например, гелием).
Лазерно-кислородный метод наиболее удобен для резки хими чески активных металлов типа титана. Все исследования, результаты которых опубликованы, выполнены с помощью непрерывных СО2-лазеров. В ходе процесса получается узкий разрез с небольшой шириной зоны, подвергающейся тепловому воздействию.
Применение лазерно-кислородного метода резки обеспечивает значительную экономию при резке некоторых металлов за счет сни жения расхода материала и уменьшения требований к последующей чистовой обработке. В табл. 4.4 приведены стоимостные оценки рез ки листового титана различными методами. Полностью автоматизи рованная лазерная система резки характеризуется высокими началь ными капитальными затратами. В полную стоимость резки в расчете на единицу длины сделанного разреза входят расходы на сам процесс резки и на операции по вторичной обработке. Применение лазерных методов резки обеспечивает значительное снижение стоимости резки в расчете на единицу длины (в особенности для достаточно большой толщины материала).
|
|
|
|
Таблица 4.4 |
Стоихмостные оценки различных методов резки титана |
||||
|
Капиталь |
Полная стоимость резки при заданной |
||
Метод |
ные затра- |
толщине материала, долл./м |
||
|
ты, долл. |
3.2 мм |
6,4 мм |
12,7 мм |
|
|
|||
Ленточная пила |
2000 |
5,0 |
7,15 |
13,62 |
Лазерная система (250 Вт) |
96000 |
2,33 |
3,90 |
42,0 |
Методы лазерной резки достигли уровня промышленного при менения в таких областях, как производство самолетов и космиче
ских летательных аппаратов, где они применяются для резки метал лов типа титана. Производительность одной из лазерных установок для резки материала на основе С02-лазера мощностью 250 Вт со ставляет - 30 000 м/год. Для разрезки поверхностей со сложным кон туром используются сложные системы с перемещением по несколь ким степеням свободы. Процесс резки алюминия в авиационной промышленности пока еще не достиг стадии промышленного приме нения и в настоящее время подвергается тщательной проверке.
В случае, когда заготовки из листового материала имеют уни фицированные окна, отверстия и другие стандартные элементы, це лесообразно сочетание на одном оборудовании выполнений двух операций: лазерного раскроя и получения с помощью вырубного штампа стандартных (унифицированных) элементов. Такая обработ ка ведется на оборудовании типа лазер-пресс.
Способом лазерной резки изготовляются дисковые пилы с раз личным профилем режущих зубьев, ножи грануляторов химического машиностроения, пуансоны и матрицы наборных вырубных штампов, специальные матрицы для резки или тиснения картонной упаковки.
Микрогеометрия поверхности реза специфична. На ряде режи мов проявляется характерная «бороздчатая» структура микрорелье фа. Неоднородна структура рельефа и по глубине реза. Обычно на выходе луча из материала шероховатость несколько выше, чем в средней части реза и на входе его в материал. Наибольшее влияние на шероховатость поверхности реза оказывает скорость обработки. Для каждого вида и толщины материала можно найти оптимальную скорость, при которой шероховатость будет минимальной. Следует, однако, учесть, что такая скорость в то же время не соответствует самому производительному режиму обработки.
Тем не менее по сравнению с другими методами раскроя мате риала лазерная резка обеспечивает четкие кромки реза, практическое отсутствие грата при обработке (рис. 4.5).
Положительные качества лазерной резки: высокая скорость рез ки, невысокая стоимость расходных материалов (газ).
Рис. 4.5. Поперечное сечение реза в углеродистой стали
Отрицательные качества лазерной резки: термическая закалка кромок, дополнительная механическая обработка, оплавление кромок.
Интенсификация механической обработки лазерным излучени ем заключается в его использовании для предварительного нагрева слоя материала на заготовке перед последующим удалением его ре жущим инструментом (рис. 4.6). При нагреве улучшается обрабаты ваемость стали вследствие изменения механических характеристик материала в зоне стружкообразования, увеличения его пластичности, снижения прочности и твердости.
Рис. 4.6. Схема лазерного воздействия при механической обработке
4.2.2. П робивка отверстий
Режим лазерного воздействия, приводящий к эрозии материала, используется не только при резке и раскрое металлических и неме таллических материалов, но и для прошивания отверстий малых раз меров, получения прецизионных щелей и пазов.
Это связано с тем,.что луч лазера при встрече с твердым телом может в месте встречи развивать температуру до 40 000° С и дать испарение любого материала. Лазерный луч служит обрабатываю щим инструментом высокой точности, он может делать отверстия, диаметр которых меньше диаметра человеческого волоса; может проникать в места, не доступные для обычных сварочных горелок.
Обработка отверстий, как правило, выполняется импульсным излучением, хотя есть ряд операций, на которых для этих целей це лесообразно использовать непрерывное излучение. Как правило, ис пользуются импульсы излучения с длительностью порядка несколь ких сотен микросекунд (или же более короткие).
Управляемыми параметрами процесса лазерной обработки от верстий являются энергия излучения Е, длительность импульса т (определяющие мощность Рср излучения), фокусное расстояние фо кусирующей системы F, смещение поверхности детали относительно фокальной плоскости фокусирующей системы AF (определяющие площадь S пятна фокусирования), число импульсов п. Эти параметры на современном технологическом оборудовании могут изменяться
в довольно |
широких |
пределах. С увеличением энергии излучения |
растут как |
диаметр, |
так и глубина отверстия, причем и диаметр, |
и глубина зависят от |
энергии излучения нелинейно. Увеличение F |
(при заданных Е й т) приводит к уменьшению плотности мощности q лазерного излучения, что вызывает уменьшение глубины и входного
диаметра отверстия. К изменению плотности мощности |
приводит |
и изменение длительности импульса т. При воздействии |
коротких |
импульсов вследствие возрастания плотности мощности излучения увеличивается доля испаренного материала в продуктах эрозии. К области обычной размерной обработки следует отнести диапазон
длительностей от 0,1-19~3 до 21 (Г3 с. Рост числа импульсов п приво дит к увеличению глубины, диаметра отверстия, изменению его формы в продольном сечении.
Производительность П обработки отверстий может быть оце нена числом прошиваемых отверстий в единицу времени. Она зави сит как от частоты v подачи импульсов и их числа п, необходимого для прошивания одного отверстия, так и от времени tn, связанного с относительным перемещением луча и заготовки после прошивания очередного отверстия:
где /?кан - число лучевых каналов установки, обычно пкш = 1.
В зависимости от частоты следования импульсов и степени ав томатизации оборудования производительность обработки может достигать от одного до нескольких десятков и даже сотен отверстий в секунду.
Пробивка отверстий в металлах при помощи лазера может ока заться выгодной во многих областях (например, для изготовления небольших отверстий в соплах и устройствах для контролируемого напуска газов, апертур для электронно-лучевой аппаратуры и точеч ных диафрагм для оптических устройств). При помощи лазера можно без особого труда пробить в тонких металлических листах аккурат ные отверстия размером не более 25 мкм. Метод позволяет формиро вать близкие к заданной конфигурации отверстия без нагрева и за грязнения прилегающих областей. При необходимости можно про бивать очень небольшие отверстия специальной формы в таких изделиях, где обычные методы не приводят к хорошим результатам.
С помощью одиночного лазерного импульса с высокой энерги ей или последовательности импульсов меньшей энергии, направляе мых на одно и то же место, в металлических листах можно пробить отверстия глубиной порядка нескольких миллиметров. Максималь ная глубина отверстия, которое может быть получено на практике