
Конструкционные материалы. Свариваемость и сварка
.pdfЭлектрошлаковая сварка
Применяется для сталей толщиной свыше 30 мм. При электрошлаковой сварке детали, как правило, устанавливают с зазором, расширяющимся к концу шва. Фиксацию взаимного положения деталей производят скобами, установленными на расстоянии 500–1000 мм друг от друга, удаляемыми по мере наложения шва. При автоматических способах электрошлаковой сварки в начале и конце шва устанавливают выводные планки.
По общепринятой технологии электрошлаковая сварка осуществляется, как правило, с последующей или сопутствующей нормализацией с целью повышения ударной вязкости металла шва и зоны термического влияния до регламентируемого уровня. При сварке сталей 16ГС, 09Г2С, 14Г2 применяют флюс АН-8 и сварочные проволоки Св-08ГС, Св-10Г2. Для повышения ударной вязкости сварные соединения подвергают нормализации и высокому отпуску.
Возможно проведение электрошлаковой сварки с регулированием термического цикла в сочетании с последующим отпуском. В результате регулирования термического цикла увеличивается скорость охлаждения, это приводит к предотвращению образования структурно-свободного феррита при γ→α-превращении. Такая структура повышает коррозионную стойкость сварного соединения. Применение данной технологии сварки позволяет достичь не только требуемого уровня равнопрочности сварного соединения, но и высокого сопротивления соединения хрупкому разрушению без применения последующей термической обработки. Электрошлаковая сварка с регулированием термического цикла применяется, например, для кольцевых швов аппаратов нефтяного, газового и химического производства с толщиной стенки до 100 мм при температуре эксплуатации до –40 °С (сталь 16Г1С) или до –55 °С (сталь 09Г2С).
31
1.4. ТЕРМИЧЕСКАЯ ОБРАБОТКА СВАРНЫХ СОЕДИНЕНИЙ
Последующая термическая обработка низколегированных сталей проводится в основном для ответственных конструкций. Целью термической обработки является получение необходимых механических свойств сварных соединений (высокой прочности или пластичности или их необходимого сочетания) и снятие остаточных сварочных напряжений. В качестве термической отработки сварных соединений могут применять высокий отпуск или нормализацию.
В процессе изготовления конструкций из низколегированных сталей на заготовительных операциях и при сварке в зонах, удаленных от высокотемпературной области, возникает холодная пластическая деформация. Попадая при наложении последующих швов под сварочный нагрев до температур около 300 °С, эти зоны становятся участками деформационного старения, приводящего к снижению пластических и повышению прочностных свойств металла и возможному возникновению холодных трещин, особенно при низких температурах или в местах концентрации напряжений. Высокий отпуск при 600–650 °С в этих случаях является эффективным средством восстановления свойств металла. Высокий отпуск применяют и для снятия сварочных напряжений.
Нормализации подвергают сварные конструкции для улучшения структуры отдельных участков сварного соединения и выравнивания их свойств. Термическая обработка снижает прочностные и повышает пластические свойства металла. Нормализацию применяют в тех случаях, когда при сварке в сварных соединениях в результате повышенных скоростей охлаждения возможно образование неравновесных структур закалочного характера (угловые однослойные швы, последние проходы, выполненные на полностью остывших предыдущих). При сварке короткими участками по горячим, предварительно наложенным швам замедленная скорость охлаждения металла шва и зоны термического влияния способствует получению равновесных структур. Влияние термической обработки в этом случае оказывается незначительным.
32
2. МИКРОЛЕГИРОВАННЫЕ СТАЛИ (ВЫСОКОПРОЧНЫЕ СТРОИТЕЛЬНЫЕ СТАЛИ)
Микролегированные стали применяются для изготовления конструкций ответственного назначения, таких как железнодорожные и автомобильные мосты, магистральные трубопроводы
ирезервуары нефтехранилищ, сосуды высокого давления, танкеры, суда, ледоколы, береговые и морские нефтегазовые сооружения
идр. Данные стали обладают высокой прочность σв = 450…750 МПа в сочетании с малой склонность к хрупкому разрушению, поэтому могут эксплуатироваться в районах с температурой ниже –40 °С. Одновременное повышение прочности и снижение хладноломкости осуществляется несколькими путями: карбонитридным упрочнением сталей, созданием малоперлитных и бейнитных сталей, термической обработкой (нормализация, улучшение), контролируемой прокаткой.
2.1. СОСТАВ И МЕХАНИЧЕСКИЕ СВОЙСТВА МИКРОЛЕГИРОВАННЫХ СТАЛЕЙ
Микролегированные стали представляют собой низколегированные стали с добавлением, кроме обычных легирующих элементов Mn, Si, Ni, микродобавок в следующих пределах (%): Al ≤ 0,06; Cr ≤ 0,25; Zr ≤ 0,15; V ≤ 0,15; Ti = 0,1…0,2; Nb ≤ 0,06; Mo ≤ 0,20; B ≤ 0,05. Суммарное содержание Zr и Ti не должно превышать 0,2 %, а Nb, Ti и W – 0,16 %. В качестве микролегирующих добавок также могут использоваться редкоземельные элементы (Ce, La, Y) и N. Содержание углерода, как правило, не превышает 0,20 %.
Микролегирующие элементы вводят в состав стали как в процессе ее выплавки, так и в ходе внепечной обработки. Они могут присутствовать в металле в составе включений вторых фаз или не-
33
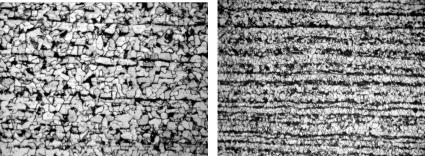
посредственно в матрице. Для повышения ударной вязкости и снижения анизотропии свойств в данных сталях отграничивают содержание S в составе стали до 0,005–0,012 %.
Стали с карбонитридным упрочнением
В сталях, микролегированных V и Nb (иногда дополнительно Al и Ti) в сочетании с повышенным содержанием N до 0,03 %, образуются упрочняющие дисперсные карбонитридные фазы типа V (C, N), Nb (C, N), AlN и др. Главными факторами карбонитридного упрочнения являются: собственно дисперсионное упрочнение, измельчения аустенитного и действительного зерна стали, а при определенной технологии – образование субзеренной структуры (рис. 2.1). Вследствие этого стали с карбонитридным упрочнением обладают повышенной прочностью и наименьшей температурой перехода в хрупкое состояние. К данным сталям относятся следующие марки: 14Г2АФ, 16Г2АФ, 18Г2АФ, 10Г2ФБ, 10Г2СФР, 10Г2СМФ.
а |
б |
Рис. 2.1. Микроструктура сталей после проката:
а – 09Г2С; б – 16Г2АФ (×200)
Малоперлитные стали имеют пониженное содержание C до 0,10 %, что приводит к уменьшению количества перлита в стали, а следовательно, к повышению ударной вязкости и пластичности, снижению порога хладноломкости и улучшению свариваемости.
34

При этом снижение прочностных характеристик компенсируется введением в сталь Mn до 1,7 % и карбонитридообразующих элементов – V, Nb, Ti, N, Al. К отечественным малоперлитным сталям относятся стали марок 07Г2ФБ, 08Г2СФБ, 09Г2ФБ.
Низкоуглеродистые бейнитные стали благодаря легирова-
нию обладают повышенной устойчивостью переохлажденного аустенита, которая обеспечивает после контролируемой прокатки превращение аустенита с образованием продуктов промежуточного превращения – игольчатого феррита и малоуглеродистого бейнита. Типичными представителями таких сталей являются 08Г2МФБ, 12Г2СМФ, 12Г2СМФ, 12ГН2МФАЮ.
Химический состав ряда марок микролегированных сталей приведен в табл. 2.1. Аналогами этих марок сталей в зарубежной практике являются стали типов Х55–Х80 (число указывает предел прочности, МПа 10–1).
Оптимальная структура и высокие механические свойства достигаются либо после термической обработки, либо после контролируемой прокатки.
Таблица 2 . 1 Химический состав микролегированных сталей
Маркастали |
|
Содержаниехимическихэлементов, % |
|||||
C |
Si |
Mn |
|
V |
N |
Другие |
|
|
|
||||||
|
|
|
|
|
|
|
|
14Г2АФ |
0,12–0,18 |
0,3–0,6 |
1,2–1,6 |
|
0,07–0,12 |
0,015–0,025 |
− |
16Г2АФ |
0,14–0,20 |
0,3–0,6 |
1,3–1,7 |
|
0,08–0,14 |
0,015–0,025 |
− |
18Г2АФ |
0,18–0,22 |
0,4–0,7 |
1,3–1,7 |
|
0,08–0,15 |
0,015–0,030 |
− |
|
|||||||
09Г2ФБ |
≤0,10 |
≤0,7 |
≤1,7 |
|
0,04–0,08 |
0,015 |
0,05 В |
|
|
|
|
|
|
|
|
10Г2ФР |
≤0,12 |
0,4–0,7 |
1,3–1,7 |
|
0,07–0,12 |
− |
0,004 Nb |
12Г2СМФ |
0,09–0,15 |
0,4–0,7 |
1,3–1,7 |
|
0,07–0,15 |
Ост. |
0,15–0,25 Мо |
12ГН2МФАЮ |
|
|
|
|
|
|
0,05–0,1 Аl |
0,09–0,16 |
0,4–0,6 |
0,9–1,6 |
|
0,05–0,10 |
0,02–0,03 |
0,15–0,25 Мо |
|
|
|
|
|
|
|
|
1,4–1,7 Ni |
35
Термическая обработка (нормализация или улучшение, заключающиеся в закалке с высоким отпуском) обеспечивает получение мелкого зерна, вследствие чего стали имеют по сравнению с низколегированными сталями наивысшую прочность и наименьшую температуру перехода из вязкого в хрупкое состояние.
Контролируемая прокатка является разновидностью термомеханической обработки, представляет собой обработку металлов давлением, при которой регламентируется температура окончания прокатки ≈ 800–850 °С и степень обжатия 15–20 % в последних проходах. Режимы контролируемой прокатки выбирают так, чтобы получить в стали высокодисперсные рекристаллизованные зерна аустенита. При дальнейшем охлаждении металла из аустенита образуются многочисленные зародыши феррита и дисперсные карбиды. Ферритные зерна полигонизуются и упрочняются в результате выделения сверхмелких карбонитридов. Карбонитриды тормозят процессы возврата и рекристаллизации после прокатки, что обеспечивает получение мелкого зерна стали, хорошо развитой субзеренной структуры и дисперсионного упрочнения. Контролируемая прокатка исключает последующую термическую обработку. Механические свойства для некоторых марок микролегированных сталей приведен в табл. 2.2.
|
|
|
|
Таблица 2 . 2 |
Механические свойства микролегированных сталей |
||||
|
|
|
|
|
Маркастали |
|
Механическиесвойства(неменее) |
||
σ0,2, МПа |
σв, МПа |
KCU–40, МДж/м2 |
Состояниепоставки* |
|
14Г2АФ |
400 |
550 |
0,4 |
Н |
16Г2АФ |
450 |
600 |
0,4 |
Н |
18Г2АФ |
500 |
650 |
0,4 |
НилиТУ |
09Г2ФБ |
460 |
560 |
0,6 |
КП |
10Г2ФР |
420 |
600 |
0,4 |
КП |
12Г2СМФ |
600 |
700 |
0,35 |
ТУ |
12ГН2МФАЮ |
600 |
700 |
0,35 |
ТУ |
* Н – нормализация; ТУ – термическое упрочнение; КП – контролируемая прокатка.
36
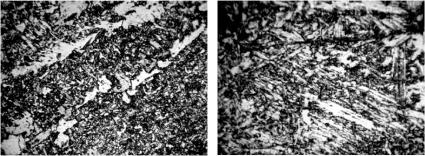
2.2. СВАРИВАЕМОСТЬ МИКРОЛЕГИРОВАННЫХ СТАЛЕЙ
Стали с содержанием углерода до 0,1 % обладают благоприятной свариваемостью, при большем содержании углерода свариваемость микролегированных сталей ухудшается, что связано с образованием неравновесных закалочных структур как в шве, так и в зоне термического влияния (рис. 2.2).
а |
б |
Рис. 2.2. Микроструктура металла шва (а) и зоны перегрева (б) стали 16Г2АФ (×600)
При сварке на небольших погонных энергиях (до 50 кДж/см), как правило, свойства сварных соединений удовлетворяют предъявляемым требованиям. С увеличением погонной энергии сварки (более 100 кДж/см) ударная вязкость металла в зоне термического влияния снижается из-за роста зерна аустенита, образования смеси структур верхнего бейнита, игольчатого феррита и высокоуглеродистого мартенсита (рис. 2.3).
Например, в сварных соединениях стали 09Г2ФБ, выполненных дуговой сваркой под флюсом при погонной энергии 30 кДж/см, значение ударной вязкости при температуре –60 °С составляет не менее 0,8 МДж/м2, а при погонной энергии 45 кДж/см – не менее
0,45 МДж/м2.
37
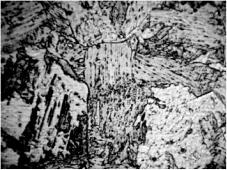
Рис. 2.3. Микроструктура зоны перегрева стали 10Г2ФБ (×600)
На повышение ударной вязкости металла шва и зоны термическоговлиянияблагоприятноевлияниеоказываютследующиефакторы:
–сниженноесодержанияСиN, чтоповышаетвязкостьматрицы;
–легирование V, Nb, Ti и Al, образующими трудно растворимые при нагреве фазы V (C, N), Nb (C, N), AlN, TiN, препятствую-
щие росту зерна аустенита;
– микролегирование В с целью повышения дисперсности ферритной составляющей структуры.
Свариваемость микролегированных сталей в значительной степени зависит от содержания вредных примесей, особенно S. Сера повышает склонность соединений к образованию горячих и слоистых трещин. Это является следствием не только «раскатывания» сульфидных включений при прокатке, но и изменения их состава и физических свойств при сварке.
2.3. ОСОБЕННОСТИ ТЕХНОЛОГИИ СВАРКИ МИКРОЛЕГИРОВАННЫХ СТАЛЕЙ
Технология сварки микролегированных сталей мало чем отличается от технологии сварки низколегированных сталей, однако изза специфики легирования имеет ряд особенностей, которые представлены ниже.
38
Для ручной дуговой сварки микролегированных сталей с уровнем прочности 600 МПа применяют электроды с повышенной прочностью типа Э-50 и выше с целлюлозным и основным покрытием. Так, электроды типа Э-50 с целлюлозным покрытием (ВСЦ-4, ВСЦ-4А) используют для выполнениякорневого слоя шва, электроды типа Э-60 и Э-70 с основным покрытием (ВСФ-65, ВСФ-75) – для выполнениязаполняющих иоблицовочныхслоев шва.
Микролегированные стали с пониженным содержанием С и углеродного эквивалента Сэкв допускается сваривать без подогрева для толщин изделия больших, чем для низколегированных сталей соответствующей категории прочности. Однако при сварке корневых швов в ряде случаев подогрев обязателен с целью предотвращения возможности образования холодных трещин.
Температуру подогрева выбирают с учетом степени легированности стали, оцениваемой по величине Сэкв, толщины стенки свариваемой конструкции, температуры окружающего воздуха и типа покрытия электрода. Эквивалент углерода для микролегированных сталей рассчитывается по формуле
Сэкв = С+ |
Mn |
+ |
Сr + Mo + V + Ti |
+ |
Ni + Cu |
, |
(2.1) |
|
6 |
5 |
15 |
||||||
|
|
|
|
|
где символы обозначают содержание соответствующих химических элементов в процентах.
Для электродов с основным покрытием при сварке из стали
спределом прочности σв = 550…600 МПа условия выполнения подогрева приведены в табл. 2.3.
Дуговую сварку под флюсом из микролегированных сталей
спрочностью σв = 550…600 МПа осуществляют с применением сварочных проволок Св-08ХМ, Св-08МХ в сочетании с флюсами АН-348А, АН-348АМ, АН-47.
Для сталей типа 16Г2Ф и 12ГН2МФАЮ применяют сварочную проволоку Св-10НМА и флюс АН-17М, сварку проводят на ограниченной погонной энергии во избежание образования зака-
39
лочных структур, особенно в зоне термического влияния, и для получения необходимого уровня механических свойств сварных соединений. При дуговой сварке под флюсом стали 09Г2ФБ применяют проволоку Св-08ГНМ и флюс АН-60.
Таблица 2 . 3
Определение температуры подогрева для электродов с основным покрытием
Значениеэквивалента |
Толщина |
Температура |
Температура |
|
окружающего |
подогрева, |
|||
углеродаСэкв, % |
изделия, мм |
|||
воздуха, °С |
°С |
|||
|
|
|||
0,37–0,41 |
15–20 |
от0 до–35 |
100 |
|
более20 мм |
любая |
|||
|
|
|||
0,42–0,46 |
12–16 |
от+10 до–35 |
100 |
|
более16 |
любая |
|||
|
|
|||
|
10–12 |
от0 до–20 |
100 |
|
0,47–0,51 |
12–18 |
любая |
||
|
||||
|
более18 |
любая |
150 |
Исходя из условия обеспечения необходимых вязкопластических свойств и равнопрочности сварных соединений термоупрочненных сталей сварку эффективно осуществлять с регулированием термических циклов.
Электрошлаковая сварка микролегированных сталей осуществляется премущественно регулированием термического цикла.
При сварке термоупрочненной стали 12ГН2МФАЮ толщиной 40 мм используют сварочную проволоку Св-10Г2СМА и флюс АН-8. Применяли следующие режимы сварки:
–сварочный ток Iсв = 800…850 А;
–напряжение U = 50…51 В;
–скорость подачи электрода vэ = 340…360 м/ч;
–скорость сварки vсв = 3,0 м/ч.
При регулируемом термическом цикле посредством принудительного сопутствующего охлаждения достигается интенсивность охлаждения металла шва и зоны термического влияния до
40