
1461
.pdfбудет поступать в лоток до тех пор, пока его уровень в стакане 10 не окажется ниже среза трубки 9.
Дозировка расхода масла осуществляется дросселем 14. При полностью закрытом дросселе разность давлений в стакане 10 и в полости К будет наибольшей и, следовательно, расход масла будет также наибольшим.
Шарик 2 препятствует понижению уровня масла в трубках 5 и 11 при отсутствии расхода воздуха через маслораспылитель, поэтому каплепадение начинается сразу после возобновления расхода воздуха через маслораспылитель. Наличие прозрачного колпачка 12 позволяет вести визуальное наблюдение за каплепадением.
Стакан 12 заполняется маслом через специальные пробки до начала резьбы под пробки в гильзе 6. Рекомендуется применять отфильтрованное индустриальное масло И-20А. Наличие в масле механических примесей может нарушить работу маслораспылителя– засоритьдроссельимаслопроводныетрубки.
Вновь установленный маслораспылитель подлежит ревизии с разборкой для осмотра деталей и удаления смазки консервации с промывкой деталей в бензине, керосине или соляровом масле.
На подъемных машинах, находящихся в эксплуатации, маслораспылитель можно не разбирать, если он работает нормально. При работе маслораспылителя проверить отсутствие утечек. При наличии утечек следует подтянуть винты, соединяющие корпус со стаканом 3. Если это не устранит утечек, осмотреть уплотнения и заменить их в случае необходимости. При просачивании воздуха через дроссель 2 осмотреть его уплотнения, в случае необходимости уплотнения заменить. Заливку масла в маслораспылитель производить по мере надобности при закрытом доступе сжатого воздуха в панель управления. Стакан 3 заполняется маслом через специальные пробки до уровня, отмеченного на стакане линией. Заливать необходимо чистое отфильтрованное индустриальное масло И-20А. Наличие в масле механических примесей может нарушить работу маслораспылителя – засорить маслопроводные трубки. Отрегулировать дросселем 2 подачу одной-двух капель масла за время впуска воздуха в тормозные цилиндры. Визуально наблюдать за каплепадением через прозрачный колпачок.
Ревизию и наладку воздушно-компрессорной станции производить
всоответствии и инструкцией завода изготовителя.
7.9.Грузопневматический привод тормоза
7.9.1. Устройство и принцип действия
Грузопневматический привод тормоза состоит из привода тормоза (цилиндры рабочего и предохранительного торможения, установленные на раме тормоза, дифференциальный рычаг, тормозные грузы), панели управления тормозом (электропневматический регулятор давления, воздухорас-
141
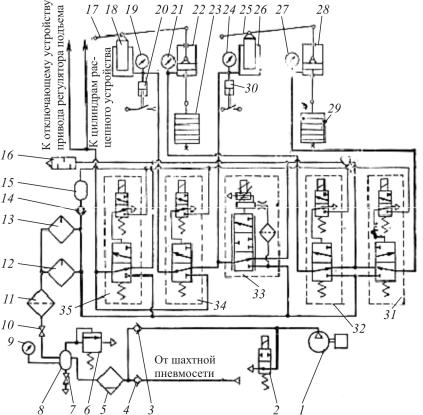
пределительные клапаны с электропневматическими вентилями, бачок, реле давления) и станции воздушно-компрессорной с воздухосборником (ком-
прессор, электровентиль, обратные клапаны, регулятор давления, воздухосборник, предохранительный клапан, воздушный фильтр, маслораспылители, сеть трубопроводов).
Нарис. 7.25 изображенасхематормозас грузопневматическимприводом.
Рис. 7.25. Схема тормоза с грузопневматическим приводом: 1 – компрессор; 2 – электропневматический вентиль; 3, 4, 14 – обратные клапаны; 5 – водомаслоотделитель; 6 – предохранительный клапан; 7, 10 – вентили; 8 – воздухосборник; 9, 19, 21, 24, 27 – манометры; 11 – воздушный фильтр; 12, 13 – маслораспылители; 15 – бачок; 16 – глушитель; 17, 25 – дифференциальные рычаги; 18, 26 – цилиндры рабочего торможения; 20, 30 – реле давления; 22, 28 – цилиндры предохранительного торможения; 23, 29 – тормозные грузы; 31, 32, 34, 35 – воздухораспределительные клапаны с электропневматическими вентилями; 33 – регулятор давления
Источником усилия для рабочего торможения является давление сжатого воздуха, подаваемого в цилиндры рабочего торможения ЦРТ 18 и 26.
142
Предохранительное торможение двухступенчатое. Первая ступень осуществляется подачей сжатого воздуха в ЦРТ под давлением определенной фиксированной величины. Источником усилия второй ступени являются тормозные грузы 23 и 29, опускающиеся при выпуске сжатого воздуха из цилиндров предохранительного торможения ЦПТ 22 и 28. На схеме тормозная система показана в положении «Заторможено».
Дифференциальные рычаги 17 и 25 приводов тормоза соединяются вертикальнымитягами сисполнительнымиорганамитормоза(насхеме непоказаны).
Цилиндры предохранительного торможения ЦПТ 22 и 28 управляются с помощью воздухораспределительных клапанов 31 и 32 (далее – клапанами). Управление клапанами осуществляется электропневматическими вентилями типа ВВ-32Ш. Клапан 32 управляет ЦПТ переставного (переставной части) барабана, а клапан 31 – ЦПТ заклиненного (заклиненной части) барабана.
Управление рабочим торможением осуществляется с помощью электропневматического регулятора давления. Воздух от регулятора давления 33 в ЦРТ 26 привода заклиненного барабана, подается непосредственно, а в ЦРТ 18 привода переставного (переставной части) барабана – через клапан 34. При работе машины по спуску-подъему груза с соединенными барабанами клапан 34 отключен, благодарячемуцилиндр18 соединен срегуляторомдавления.
Расцепное устройство механизма перестановки барабанов управляется клапаном 35. При расцеплении барабанов включаются клапаны 34 и 35, отключается клапан 32. При этом в пневматической схеме управления происходят следующие переключения. Сжатый воздух из воздухосборника через клапан 35 подается в цилиндры механизма перестановки и расцепное устройство регулятора подъема. Одновременно через клапаны 35 и 34 воздух подается в ЦРТ 18, который клапаном 34 отключается от регулятора давления. Из ЦПТ 22 воздух выпускается в атмосферу клапаном 32. В результате этих переключений переставной барабан оказывается заторможенным предохранительным тормозом, а привод тормоза заклиненного барабана управляется так же, как и при работе машины с соединенными барабанами. Реле давления 20 и 30 предназначены для контроля давлениявоздухавцилиндрахрабочеготорможения.
Привод тормоза (рис. 7.26) состоит из цилиндра рабочего торможения (ЦРТ) 1, цилиндра предохранительного торможения (ЦПТ) 2 с подвешенными к его поршнютормознымигрузами 3, дифференциального рычага4, сварной рамы 5, на которой смонтированы все элементы привода, буферного устройства с пружиной 6, стойки с блокировочными выключателями 7, распорной стойки 8, выключатель контроля давления воздуха 9. Технические характеристики грузопневматическихприводовтормозаприведены вприложении5.
При нормально работающей подъемной машине ЦПТ находится под давлением сжатого воздуха, благодаря чему тормозные грузы удерживаются в верхнем положении. В ЦРТ от электропневматического регулятора давле-
143
ния подается дозированное давление сжатого воздуха, в результате чего поршень ЦРТ через вертикальную тягу, соединенную с левым шарниром дифференциального рычага, передает соответствующее усилие исполнительному органу тормоза. Дифференциальный рычаг при этом будет поворачиваться вокруг его правого шарнира.
Таблица 7 . 8
Технические характеристики тормозных приводов
Наименование |
|
Норма |
|
|
Диаметр ЦРТ, мм |
400 |
450 |
500 |
600 |
Диаметр ЦПТ, мм |
200 |
220 |
250 |
300 |
Наибольшее тормозное усилие при |
45,5 |
56,0 |
77,0 |
10,5 |
наибольшем количестве грузов, кН |
|
|
|
|
Подъемное усилие ЦРТ, кН |
75,3 |
95,3 |
117,7 |
169,5 |
Подъемное усилие ЦПТ, кН |
18,1 |
22,0 |
28,2 |
34,3 |
Максимальный рабочий ход поршня ЦПТ, мм |
540 |
540 |
540 |
540 |
ЦРТ (от дна цилиндра) |
120 |
120 |
120 |
120 |
Максимальное количество грузов, шт. |
13 |
16 |
22 |
30 |
Максимально возможное перемещение |
680 |
680 |
680 |
700 |
поршня ЦПТ, мм |
|
|
|
|
Наибольшее давление воздуха, МПа |
0,6 |
0,6 |
0,6 |
0,6 |
Размеры дифференциального рычага, мм |
|
|
|
|
(рис. 7.26) |
|
|
|
|
А |
400 |
400 |
400 |
500 |
Б |
1400 |
1400 |
1400 |
1750 |
При включении предохранительного торможенияпроисходит следующее. От электропневматического регулятора давления в ЦРТ поступает сжатый воздух давлением 0,2–0,25 МПа, за счет чего создается первая ступень тормозного усилия. Одновременно электропневматическим клапаном осуществляется выпуск воздуха из ЦПТ, вследствие чего тормозные грузы опускаются, дифференциальный рычаг поворачивается вокруг левого шарнира, осаживая поршень ЦРТ на дно цилиндра. Тормозное усилие в это время оста-
ется равным усилию первой ступени.
После посадки поршня ЦРТ на дно цилиндра дифференциальный рычаг под действием тормозных грузов стремится повернуться вокруг среднего шарнира и через левый шарнир передает исполнительному органу тормоза вторую ступень тормозного усилия.
Наличие в ЦРТ сжатого воздуха первой ступени создает для поршня амортизационную подушку, благодаря которой достигается безударное приложение тормозного усилия.
Подготовка тормозного привода к нормальной работе после предохранительного торможения называется «зарядкой». При этом происходит подъем
144
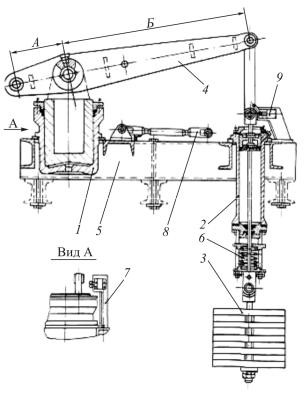
тормозного груза усилием поршня ЦРТ, что исключает внезапное растормаживание подъемной машины, после чего осуществляется впуск воздуха в ЦПТ. Для предотвращения ударов поршня в верхнюю крышку при зарядке тормоза в нижней части ЦПТ установлено буферное устройство с пружиной 6.
Рис. 7.26. Грузопневматический привод тормоза
Для удобства и безопасной замены уплотнений тормозных цилиндров привод снабжен распорной стойкой 8, позволяющей зафиксировать дифференциальный рычаг в определенном положении.
7.9.2. Ревизия и наладка привода тормоза
При ревизии и наладке привода необходимо выполнить внешний осмотр, регулировку концевых выключателей, ревизию цилиндра предохранительного торможения с разборкой и при необходимости заменить уплотнения на цилиндре рабочего торможения.
При внешнем осмотре привода тормоза необходимо проверить сле-
дующее:
1. Состояние рамы 5 привода (см. рис. 7.26), ее крепление к фундаменту. Обнаруженные в раме трещины заварить. Рама должна быть надежно за-
145
креплена на балках, концы балок должны быть забетонированы. В фундаменте под рамой привода не должно быть трещин. Обнаруженные дефекты фундамента устранить.
2.Правильность установки рамы по горизонтали и относительно исполнительного органа тормоза. Основными признаками неправильной установки привода являются:
–поперечные перемещения дифференциального рычага 4 при затормаживании ирастормаживании машинырабочимилипредохранительным тормозом;
–клиновидность зазоров в вертикальной плоскости в шарнирном соединении дифференциального рычага 4 с вертикальной тягой исполнительного органа тормоза, которая может быть обнаружена при проверке зазоров щупами по окружности шарнира. При извлечении шарнирного валика может быть обнаружена несоосность отверстий под валик в дифференциальном рычаге 4 и вертикальной тяге.
При обнаружении признаков неправильной установки привода необходимо переместить его соответствующим образом по балкам и установить по уровню с помощью прокладок между рамой 5 и балками. Прокладки приварить к балкам.
3.Состояние цилиндра рабочего торможения. Без особой необходимости разборку цилиндра производить не следует. Достаточно ограничиться его внешним осмотром, для чего увеличить зазор между тормозными колодками
иободом так, чтобы выход поршня над верхним прижимным кольцом уплотнения цилиндра 1 при рабочем торможении был около 120 мм. Выключатель износа колодок временно демонтировать. Осмотреть рабочую поверхность поршня, на которой не должно быть царапин, раковин, ржавчины и других дефектов. Мелкие дефекты устранить зачисткой напильником или мелкозернистой шлифовальной шкуркой. Проверить отсутствие трещин в корпусе, поршне и прижимном кольце уплотнения. Дефектные детали отремонтировать или заменить. При наличии утечек воздуха заменить или подтянуть уплотнение. Подтягивать уплотнение следует не чрезмерно туго, чтобы поршень мог свободно опускаться под собственным весом при растормаживании. Проверить состояние пресс-масленок и закачать смазку в цилиндр. Произвести продувку цилиндра через пробку в днище корпуса. По окончании
осмотра вновь установить рабочий зазор между тормозными колодками
иободом и установить выключатель износа колодок.
4.Состояние шарниров. При зазорах в шарнирах, превышающих допустимые значения, произвести их ремонт с заменой валиков и расточкой отверстий, если обнаружится овальность отверстий. Проверить подачу смазки в шарнирные соединения. Неисправные масленки заменить. Если смазка не продавливается, прочистить смазочные каналы и промыть их жидкой
146
смазкой. Проверить наличие всех стопорящих деталей (шайбы, шплинты, винты) и установить недостающие детали.
5.Состояние тормозных грузов и их подвески. Гайка под тормозными грузами должна быть зафиксирована от самоотвинчивания контргайкой, которая в свою очередь должна быть зашплинтована. Тормозные грузы должны состоять из стандартных плит. Масса стандартной плиты 100 кг. Укладка плит должна быть выполнена так, чтобы исключалась возможность выпадания отдельных плит. Для исключения подпрыгивания тормозного груза при его поднятии рекомендуется установить распорки между верхней плитой и шарнирной головкой подвески груза, распорки скрепить между собой. Шарнирная головка должна быть зафиксирована относительно тяги штифтом или стопорным болтом, а на головке и тяге необходимо нанести масляной краской совмещенную метку для контроля возможного вывинчивания тяги из головки.
6.Состояние приямка под тормозными грузами. Расстояние между тормозными грузами и дном приямка при крайнем конструктивно возможном положении грузов должно быть не менее 300 мм. В приямке не должно быть масла, воды, посторонних предметов. Тормозной груз при опускании не должен задевать стены фундамента и приямка, а расстояние от груза до стенок должно быть не менее 25 мм. При обшивке стен металлическим листом или облицовочной плиткой это расстояние может быть уменьшено до 10 мм;
7.Величины хода поршней цилиндров рабочего и предохранительно торможения при предельно допустимом суммарном зазоре между тормозными колодками и ободом. Величины хода поршней и запас хода поршня цилиндра предохранительного торможения до упора в нижнюю крышку должны быть в пределах величин, приведенных в подразд. 7.5.4 и приложении 5.
8.Состояние блокировочных выключателей. Отрегулировать выключатель износа колодок и воздействующий на него нажим (см. подразд. 7.5.4). Если имеется выключатель, подающий предупредительный сигнал об износе колодок, то он должен срабатывать при величине хода поршня цилиндра рабочего торможения на 5–10 мм меньше, чем при срабатывании, основного выключателя. Выключатель 9 и воздействующий на него нажим должны быть отрегулированы так, чтобы контакты выключателя замыкались при крайнем верхнем положении грузов 3. В то же время эти контакты не должны размыкаться при небольшом опускании грузов, которое происходит при минимальном рабочем давлении воздуха, установленном в воздухосборнике, и растормаживании машины рабочим тормозом.
9.Состояние буферного устройства. Размеры и жесткость пружины 6 должны соответствовать заводским данным. Нестандартные или поврежденные пружины заменить. Поднятие тормозных грузов не должно сопровождаться ударом поршня в верхнюю крышку цилиндра предохранительного
147
торможения. Для устранения ударов следует опустить демпферное устройство, установив для этой цели удлиненные направляющие стойки.
Ревизия цилиндра предохранительного торможения. Цилиндр пре-
дохранительного торможения 2 подлежит детальной ревизии с разборкой. Разборку цилиндра произвести в следующей последовательности:
–разгрузить подъемные сосуды и установить их в положение, при котором снимается окружное усилие с органа навивки, зафиксировать орган навивки стопором;
–зафиксировать тормозные грузы подкладками или специальными подвесками в положении на 100–150 мм ниже их нормального верхнего положения;
–полностью выпустить воздух из тормозной системы;
–распорнуюстойку 8 соединитьваликом сдифференциальнымрычагом;
–демонтировать выключатель 9;
–снять гайки, крепящие верхнюю крышку цилиндра, приподнять крышку и надежно прикрепить ее к рычагу 4;
–ослабить гайки, крепящие фланец уплотнения нижней крышки ци-
линдра;
–пользуясь распорной стойкой 8, снять нагрузку с шарнирных соединений штока цилиндра 2, после чего демонтировать валик нижнего шарнира;
–распорной стойкой поднять шток цилиндра на высоту, достаточную для свинчиваниянижней серьги, послечегорасстопоритьиотвинтитьэту серьгу;
–демонтировать валик шарнира верхней серьги штока цилиндра 2;
–рассоединитьраспорную стойку 8 срычагом, поднятьконецрычага4;
–извлечь шток с поршнем из цилиндра; снять поршень со штока (при необходимости).
При внутреннем осмотре цилиндра предохранительного торможения необходимо проверить следующее:
1.Состояние рабочих поверхностей цилиндра и поршня, очистить их от грязи и ржавчины и промыть в керосине. Рабочая поверхность цилиндра должна быть гладкой, ровной и не иметь царапин, борозд, раковин и других дефектов. При необходимости следует произвести шлифовку внутренней поверхности цилиндра.
2.Состояние уплотнений поршня и нижней крышки цилиндра (сальниковой набивки или манжет), при необходимости заменить их.
3.Состояние штока. Рабочая поверхность штока должна быть гладкой, без царапин, ржавчины и других дефектов. Распространенным дефектом является утонение штока в месте соприкосновения его с уплотнением нижней крышки цилиндра вследствие износа. При износе 0,4–0,5 мм по диаметру шток должен быть немедленно заменен. Кривизна штока недопустима, так
148
как может привести к заклиниванию поршня. Искривленный шток должен быть подвергнут правке в центрах токарного станка. Резьба на концах штока должна быть исправной. Шаткость серьг на резьбе не допускается. Серьги должны быть застопорены штифтами или стопорными болтами, а на серьгах и штоке необходимо нанести масляной краской совмещенную метку для контроля возможного свинчивании серьг.
4. Состояние масленок и каналов для подачи густой смазки. Неисправные масленки заменить, каналы прочистить.
Перед сборкой цилиндра смазать солидолом внутреннюю поверхность корпусаиштока. Сборку цилиндрапроизвести вобратнойпоследовательности.
После сборки цилиндра и подачи в него сжатого воздуха необходимо проверить следующее:
1.Отсутствиеутечек воздуха. Принеобходимостиподтянутьуплотнения.
2.Режим опускания тормозных грузов. Для проверки осуществить предохранительное торможение, исключив первую степень. Груз должен быстро опуститься, без зависаний. При неудовлетворительном режиме опускания груза ослабить затяжку уплотнений, но так, чтобы не вызвать появления утечек воздуха, устранить перекос (если он имеется) фланца уплотнения нижней крышки цилиндра. Если это не даст положительного результата, произвести повторную ревизию цилиндра с разборкой.
3.Крепление верхней крышки цилиндра и отсутствие задевания верхней серьгой краев окна в крышке.
7.9.3. Панель управления тормозом
Панель управления предназначена для распределения через электропневматический регулятор давления и через воздухораспределительные клапаны сжатого воздуха, поступившего из воздухосборника через маслораспылители между цилиндрами рабочего и предохранительного торможения и расцепного устройства.
Принципиальная схема панели управления (в рабочем состоянии) представлена на рис. 7.27.
Панель управления состоит из электропневматического регулятора давления РДУ, воздухораспределительных клапанов К1–К4 с электропневматическими вентилями, маслораспылителей МР, бачка Б, реле давления РДЦ, рамы, кожуха защитного.
Сжатый воздух, проходя через маслораспылители, обогащается тонкораспыленным маслом и подается на регулятор давления и клапаны К3 и К4, соединенные трубопроводами с ЦПТ заклиненного и переставного барабанов. От регулятора давления воздух подается к ЦРТ заклиненного барабана и через клапан К1 к ЦРТ переставного барабана. Непосредственно от воздухос-
149
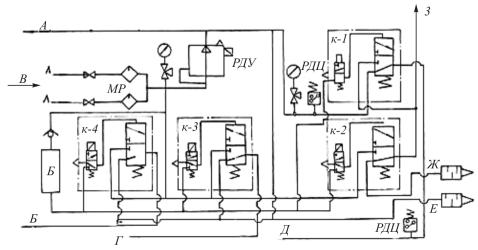
борника (после маслораспылителей) сжатый воздух подается и на клапан К2 расцепного устройства.
Электропневматический регулятор давления и воздухораспределительные клапаны с электропневматическими вентилями соединены между собой трубопроводами и включены в электрическую цепь управления. Таким образом, на панели управления сконцентрированы все аппараты управления тормозами и расцепным устройством шахтных подъемных машин. Для контроля давления воздуха в рабочих цилиндрах тормозных приводов в их цепях установлены реле давления РДЦ. Для визуального контроля давления воздуха в магистрали перед регулятором давления и после него установлены показывающие манометры.
Рис. 7.27. Принципиальная схема панели управления: А – к ЦРТ заклиненного барабана; В – от воздухосборника; Б – к ЦПТ заклиненного барабана; Г – к ЦПТ переставного барабана; Д – к ЦРТ переставного барабана; Е, Ж – к глушителям; З – к цилиндрам расцепного устройства и отключающего устройства ограничителя скорости
Ревизию и наладку панели управления тормозом произвести в соответствии с подразд. 7.8.3.
7.9.4. Станция воздушно-компрессорная с воздухосборником
Устройство, принцип действия, ревизию и наладку компрессора, воздухосборника, предохранительного и обратного клапанов регулятора давления АК11А3, воздушного фильтра, маслораспылителя произвести в соответствии с подразд. 7.8.4.
150