
2774.Вакуумные технологии
..pdf2.2. Электрические вакуумные печи
Широкое распространение в связи с возникновением таких отраслей промышленности, как атомная, ракетная и др. получили различные типы вакуумных электропечей. Переплав в вакууме металлов и сплавов обеспечивает: значительное снижение содержания растворенных газов; повышение чистоты по неметаллическим включениям; получение слитков без дефектов ликвационного происхождения за счет направленной, последовательной и замедленной кристаллизации жидкого металла; значительное улучшение физико-механических свойств металла; высокую гомогенность и плотность выплавляемых слитков.
По устройству и назначению вакуумные электропечи подразделяются на следующие типы: сопротивления, индукционные, дуговые и электронно-лучевые печи.
Наиболее распространенные вакуумные электропечи сопротивления являются наиболее универсальными и, таким образом, имеют множество областей применения. Их используют для нагрева крупногабаритных и тяжелых садок, деталей в подвешенном состоянии для предохранения их от деформации, длинномерных изделий, для отжига трансформаторной стали
ит.п. Устройство печей подразумевает наличие герметичной, теплоизолированной рабочей камеры, внутри которой установлены нагреватели, выделяющие тепло за счет протекания по ним электрического тока. Печи откачиваются механическими
идиффузионными насосами до остаточного давления менее 10–1–10–7 Па. По производительности вакуумные электропечи сопротивления делятся на садочные и методические. В садочных электропечах садка остается неподвижной в течение всего времени нагрева, в них нельзя произвести очередную загрузку, предварительно не разгрузив печь. Эти печи отличаются низкой производительностью. Наибольшее распространение получили
51
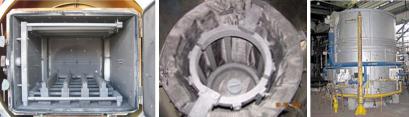
следующие типы садочных вакуумных электропечей: камерные (фронтальная загрузка), шахтные (загрузка сверху), колпаковые и элеваторные (загрузка снизу) (рис. 2.14, 2.15).
а |
б |
в |
Рис. 2.14. Вакуумные печи: а – камерная; б – шахтная; в – колпаковая
Высокопроизводительные вакуумные методические электропечи включают в себя загрузочную и разгрузочную шлюзовые камеры, одну или несколько камер нагрева и охлаждения, систему механизмов для перемещения садки в печи и вакуумную систему. По принципу перемещения садки нашли применение следующие виды вакуумных методических печей: печи с шагающим подом, многокамерные печи с перекатной тележкой, толкательные печи и печи для термической обработки ленты и проволоки.
По назначению вакуумные печи сопротивления подразделяются:
на печи для термообработки, закалки, отжига и пайки
(производители – SHMETZ, Technocentro, Timet, Cezus, Zircotube, TAV, МЗВЭ (Москва), ВНИИЭТО (г. Истра), ПО «Эмитрон»);
печи для спекания и дегазации (TAV, МЗВЭ (Москва), ВНИИЭТО (г. Истра), ПО «Эмитрон»);
печи для нагрева заготовок под обработку давлением;
печи для проведения специальных химико-технологичес- ких процессов.
52
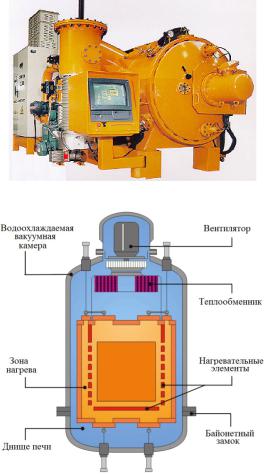
а
б
Рис. 2.15. Закалочные вакуумные печи: а – камерная; б – элеваторная
Вакуумный отжиг (при давлении 10–1–10–3 Па) – термический вакуумный процесс обработки металлов и сплавов, состоящий в их нагреве, выдержке определенное время и охлаждении для снятия наклепа, изменения структуры в нужном направле-
53
нии, повышения пластичности, для очистки от газовых и неметаллических включений, а также придания определенных электрических, магнитных и других свойств. Отжигу в вакууме подвергаются проволока, листы, детали из различных металлов
исплавов, заготовки для последующей обработки давлением.
Так, отжиг тантала и ниобия рекомендуется проводить в течение 1 ч при температуре 1300−1400 °С и давлении не более 10–3 Па. Ниобий первоначально обрабатывается вакуумной прокаткой при температуре 1100−1250 °С, а после разрушения литой структуры легко обрабатывается давлением при комнатной температуре.
После отжига при 1700−1730 °С в вакууме предел прочности ниобия возрастает до величины 300−400 Н/мм2, твердость по Бриннелю – до 800−900 Н/мм2, относительное удлинение– до 30 %.
Выделяют следующие виды отжига: высокотемпературный, рекристаллизационный, обезгаживающий, обезуглероживающий
ипрочие. Так, при производстве ртутных выпрямителей в вакуумных печах осуществляется обезгаживающий отжиг деталей, изготавливаемых из низкоуглеродистых сталей. Он обеспечивает обезгаживание и получение светлой поверхности, что при нагреве деталей во время эксплуатации исключает образование или отслаивание окисных пленок и уменьшает величину газовыделения, благодаря чему предотвращается замыкание и пробой. Высокотемпературный отжиг в печах также улучшает магнитные свойства и повышает процент выхода годного при производстве высших марок трансформаторной стали.
Вакуумная закалка − вакуумный процесс термообработки
стали и некоторых цветных сплавов (например, бронзы, латуни и др.) путем нагрева и затем быстрого охлаждения. Закалка вызывает заметное изменение свойств металла: в частности, у стали − повышение упругости, прочности, твердости при пониженной вязкости, уменьшение деформации и коробления, получение чистой светлой поверхности без науглероживания или обезуглероживания и т.д. У некоторых сталей и сплавов закалка приводит только к повышению вязкости. Например, широко применяется закалка рельсов из бессемеровской стали, обеспечивающая
54
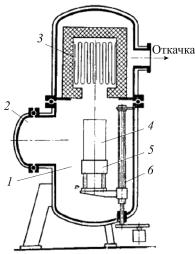
высокие пластические свойства и высокое значение ударной вязкости даже при температурах вплоть до –50 °С при малой чувствительности к старению.
Электропечи для вакуумной закалки подразделяют на печи для закалки в газе (в том числе и при повышенных давлениях (до 6–10 атм) – так называемые вакуумно-компрессионные печи)
и для закалки в жидких средах. Закалка в газе после нагрева
ввакууме проводится в камерных и шахтных печах (рис. 2.16, 2.17). Эти печи широко применяются для закалки крупногабаритных изделий, деталей приборов и машин, медицинского и точного инструмента и прочее. В России впервые была создана шахтная элеваторная вакуумная печь с камерой охлаждения СЭВ 5,5/20 с графитовой футеровкой и нагревателями для закалки в циркулирующем инертном газе пресс-форм, фильер, металлорежущего инструмента из легированных и быстрорежущих сталей и деталей шариковых подшипников (см. рис. 2.16).
Рис. 2.16. Элеваторная вакуумная печьсхолодильной камерой (СЭВ5,5/20): 1 – холодильная камера; 2 – загрузочный люк; 3 – нагревательная камера; 4 – садка; 5 – под; 6 – механизм подъема садки
55
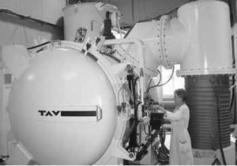
Рис. 2.17. Камерная печь TAV H8 для закалки в вакууме и среде азота и аргона при давлении охлаждающего газа до 0,6 МПа и различных типах циркуляции газа в закалочной камере (TAV, Италия)
Нагрев изделий под закалку осуществляется при величине остаточного давления в печи 0,1 Па. Печи, предназначенные для проведения закалки в масле, снабжаются специальным закалочным баком. Применяются различные схемы компоновки закалочных баков и нагревательных камер: закалочный бак не отсекается от нагревательной камеры затвором и располагается вертикально под ней, нагревательная камера находится под закалочным баком и отделена от него вакуумным затвором и др. Применение технологии закалки в вакууме позволяет повысить качество изделий и устранить последующую механическую обработку.
Индукционные вакуумные печи (VIM) (рис. 2.18) применя-
ются для плавки и разливки широкой номенклатуры металлов и сплавов. Наибольшее распространение получили плавильные печи с опрокидываемым тиглем, расположенным внутри стационарного корпуса (кожуха). Индукционные печи используются для производства заготовок из широкого спектра материалов, включая специальные и прецизионные сплавы на основе никеля или кобальта.
Вакуумная индукционная плавка (VIM) является одним из наиболее часто используемых процессов во вторичной металлур-
56
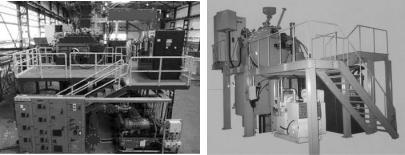
гии для очистки, обработки в жидком состоянии и регулировки химического состава и температуры. Для достижения все более высоких требований к качеству конечного материала и одновременно экономии сырья (в том числе дорогостоящих лигатур) и энергии использовать вакуум в процессе индукционной плавки необходимо для многих специальных материалов. Вакуумная индукционная плавка незаменима при производстве спецсплавов (ВИАМ, новые авиационные жаропрочные сплавы: ЖС36-ВИ, ВЖМ1-ВИ, ВЖМ4-ВИ, ВЖМ5-ВИ, ВКНА-25, ВКНА-4У-ВИ, ВКНА-1В-ВИ и др., серийные и усовершенствованные сплавы: ЖС26-ВИ–ЖС26У-ВИ, ЖС32-ВИ–ЖС32У-ВИ, ЖС6У-ВИ– ЖС6УМ-ВИ, ВЖЛ12У-ВИ–ВЖЛ20-ВИ и др.), которые должны плавиться в вакууме либо атмосфере инертного газа, так как легко вступают в реакцию с атмосферным кислородом. Технология VIM также подходит для получения высокочистых металлов в бескислородной атмосфере, так как ограничивает образование неметаллических включений.
а |
б |
Рис. 2.18. Вакуумная индукционная печьSECO/WARWICK, Польша(а) и печь «ТайваньМетизАльянс», Тайвань (б)
Вакуумная индукционная плавка делает возможной эффективную дегазацию расплава и высокоточное составление сплава, поскольку температура, вакуум, атмосфера газа, давление и перемещение материала посредством перемешивания расплава могут регулироваться независимо друг от друга. Кроме того, точная
57
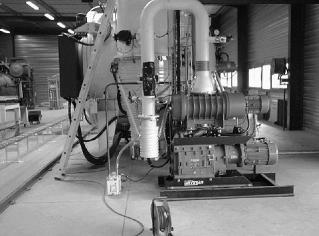
концентрация легирующих элементов, содержание микролегирующих элементов также важны для многих сплавов.
Печи VIM предназначены для отливки в условиях чистой вакуумной атмосферы, заготовки, производимые в этом оборудовании, имеют специальные свойства структуры, необходимые для эффективной и длительной работы. В зависимости от применения производимых заготовок, в печах VIM получают равноосевую (EQ), направленную (DS) или монокристальную (SC) структуру заготовки.
Принцип работы этих печей заключается в том, что в огнеупорном тигле, помещенном в вакуумную камеру, при помощи высокочастотного индуктора расплавляют твердую шихту (чистые металлы и ферросплавы, специальные заготовки, отходы) и рафинируют полученный расплав. Индукционные печи могут работать и на жидкой садке. Индукционные печи откачиваются паромасляными диффузионными и бустерными насосами, а также безмасляными (когтевыми и Рутса), обеспечивающими остаточные давления менее 10 Па (рис. 2.19).
Рис. 2.19. Установка для откачки вакуумной индукционной печи (бустерный насос, насосРутса икогтевойнасос), ВОСEDWARDS, Великобритания
58
В последние годы проводились интенсивные разработки по созданию промышленных вакуумных плазменно-индукционных печей и систем их откачки. Применение плазмотронов ускоряет процесс плавления шихтовых материалов и позволяет организовать его более рационально, так как появляется возможность поддержания постоянной мощности печи, не зависящей от ее габаритов и плотности укладки шихты.
Вакуумные дуговые печи (ВДП, VAR) используются для вы-
плавки высококачественных сталей – конструкционных, нержавеющих, электротехнических, шарикоподшипниковых (VAR-S); жаропрочных сплавов, тугоплавких и высокореакционных металлов – ниобия, тантала титана и циркония (VAR-T).
Промышленное освоение этих печей относится к периоду 1953–1954 гг. Если первые слитки, выплавленные в ВДП, имели диаметр 100–150 мм, то в настоящее время, например в Германии, выплавляют стальные слитки диаметром 1500 и 1800 мм и массой 50 и 200 т соответственно. Основные конструктивные особенности печи: расходуемый электрод крепится на электрододержателе, к которому присоединен отрицательный полюс источника постоянного тока. Шток электрода через уплотнение вводится в вакуумное пространство печи. Между концом электрода и прокладкой поддона кристаллизатора образуется мощная электрическая дуга. Материал электрода под влиянием тепла дуги расплавляется и стекает в охлаждаемый кристаллизатор, где затвердевает и из него постепенно формируется слиток (рис. 2.20). Электрод, служащий одним из полюсов дуги, может быть как расходуемым (эта схема чаще всего применяется в промышленности), так и нерасходуемым. Расходуемый металлический электрод состоит из материала, подлежащего переплаву, его химический состав соответствует составу получаемого конечного сплава. Между электродом и затравкой при подаче постоянного тока возникает электрическая дуга. Выделяющееся при горении дуги тепло расплавляет электрод, образующийся
59
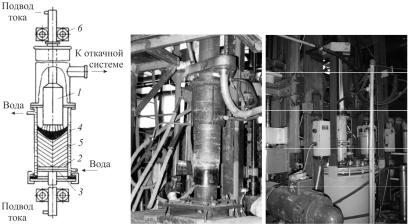
жидкий металл стекает либо в кристаллизатор, либо в тигель –
вслучае плавки в гарнисаже. В ВДП с нерасходуемым электродом, который обычно изготавливают из графита или вольфрама,
взону плавки подается твердая шихта. Нерасходуемый электрод участвует в процессе плавки исключительно как проводник тока. Мощность электрической дуги выбирают с расчетом обеспечения получения бездефектной плотной макроструктуры слитка. Величина давления в дуговом промежутке в процессе плавки определяется упругостью паров металла над расплавом и составляет для стали 0,1–1 Па, для титана 1–10 Па и для молибдена 0,01–0,1 Па. Заданное давление поддерживают системой вакуумной откачки.
а |
б |
в |
Рис. 2.20. Дуговая вакуумная печь для выплавки слитков в медных водоохлаждаемых кристаллизаторах: а – схема дуговой вакуумной электропечи с кристаллизатором: 1 – расходуемый электрод, 2 – затравка, 3 – поддон, 4 – охлаждаемый кристаллизатор, 5 – слиток, 6 – механизм перемещения электродов; б, в – внешний вид печи производства
ВНИИЭТО (б), производства «КОМТЕРМ» (в)
60