
1499
.pdfзаданных условий их сжатия. Отсутствуют проблемы при ЭЛС тонких деталей с толстостенными или деталей из материалов с сильно различающимися теплофизическими характеристиками. Как уже было указано выше, вакуум как защитная среда обеспечивает обезгаживание свариваемого металла и высокую чистоту металла сварного шва.
Из-за высокой чистоты процесса ЭЛС идеально подходит для сварки химически активных при высоких температурах металлов и металлов, полученных электронно-лучевой плавкой или другими методами специальной электрометаллургии (вакуумно-индукционной, вакуумно-дуговой или электрошлаковой плавкой). В ряде случаев применения ЭЛС возможно проведение процесса сварки на дне узкого зазора или отверстия. Это является дополнительным преимуществом ЭЛС перед электродуговой и плазменной сваркой.
Высокая скорость сварки, глубокие и узкие сварные швы и минимальная величина зоны термического влияния – это основные преимущества ЭЛС, которые обусловливают широкое применение процесса. Этим способом сварки возможно сваривать металлы значительной толщины. При этом отношение ширины сварного шва к его глубине может достигать 1:30, при этом размеры зоны термического влияния минимальны. Такая форма зоны проплавления (рис. 2.4, б) носит название кинжального проплавления. Критическая плотность мощности, выше которой полученный при ЭЛС шов имеет кинжальную форму, имеет порядок 106 Вт/см2, а при сварке с плотностью мощности, значительно меньшей критической, сварной шов имеет форму полусферы (рис. 2.4, а).
Узкий и глубокий сварной шов получается как при нахождении корня шва в глубине свариваемой детали, так и при выходе электронного пучка с обратной стороны свариваемой пластины. На рис. 2.5 показаны макрошлифы поперечных сечений сварных швов в пластине из высокопрочной малоуглеродистой стали толщиной 22 мм, скорость сварки – 2,2 см/с, ускоряющее
171
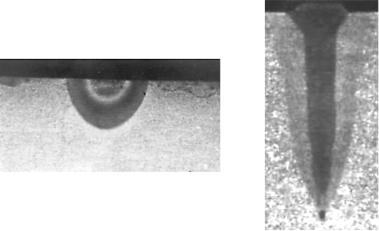
а |
б |
Рис. 2.4. Макрошлифы поперечных сечений сварных швов:
а– « полусферический» шовприплотности мощности электронного пучка ниже 5·105 Вт/см2; б– кинжальный шов при плотности мощности пучка 108 Вт/см2 в пластине с толщиной78 мм.
Нашлифах видны зонытермического влияния
напряжение – 42 кВ, ток пучка – 50 мА для шва, приведенного на рис. 2.5, а, и 55 мА для шва, показанного на рис. 2.5, б.
Режим кинжального проплавления для сварного шва, приведенного на рис. 2.5, а, выбирался таким образом, чтобы корень шва находился в непосредственной близости от нижней поверхности металла. При этом увеличение тока пучка на 10 % без изменения остальных параметров сварки приводило к переходу формы поперечного сечения шва из кинжальной в параллельную со сквозным проплавлением металла, после чего ток электронного пучка можно уменьшить на 30 %, что обеспечивает сохранение режима сквозного проплавления с некоторым уменьшением ширины шва.
Большая глубина проплавления и малая ширина сварных швов, приведенных на рис. 2.4, б и 2.5, обусловлена формирова-
172
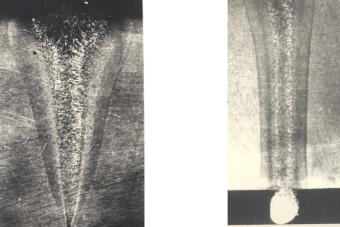
а |
б |
Рис. 2.5. Изменение формы поперечного сечения сварного шва и ширины зоны термического влияния при различных режимах
проплавления металла: а – без прохождения электронного пучка сквозь свариваемое изделие (шов с кинжальным несквозным проплавлением); б – при выходе канала проплавления с нижней поверхности свариваемого изделия (сварной шов со сквозным проплавлением)
нием в металле канала проплавления, образующегося при плотности мощности в электронном пучке выше критической и достаточной величине общей мощности пучка.
Изменение формы проплавления при открытии этого канала и возможность сквозного проплавления металла при меньших значениях мощности электронного пучка демонстрируют существенное влияние процессов взаимодействия электронного пучка с материалом свариваемого изделия и показывают важность процессов, протекающих в системе электронный пучок – канал проплавления.
При достаточной мощности электронного пучка и соответствующей его фокусировке возможно прохождение пучка через несколько пластин, что позволяет получить уникальное
173
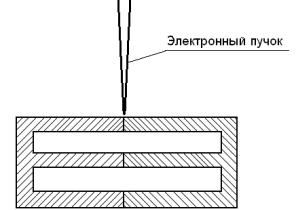
для сварочных процессов одновременное проплавление двухтрех сварочных стыков, размещенных друг над другом на пути вертикально падающего электронного пучка (рис. 2.6).
ЭЛС с плотностью мощности ниже критической (5·105– 106 Вт/см2), при которой в результате изотропного распространения тепла от поверхностного источника тепла наблюдается полусферическая форма проплавления (см. рис. 2.4, а), применяется для сварки тонкостенных деталей. В зависимости от взаимного расположения свариваемых кромок здесь, как и в традиционных способах сварки, применяется сварка встык (часто с отбортовкой свариваемых кромок с целью снижения требований к зазору в стыке) и сварка нахлесточных и тавровых соединений. Обычно толщина свариваемого металла в этом случае находится в пределах 0,4–4,0 мм, причем размеры сварочной ванны в значительной степени определяют условия получения качественного сварного шва. Для достижения этого зазор между свариваемыми кромками надо минимизировать путем применения соответствующего сварочного приспособления, обеспечивающего плотное прижатие этих кромок друг к другу, а также путем предварительной механической подготовки кромок.
Рис. 2.6. ЭЛСодновременнотрехсварочных стыков, расположенныхдругнаддругом
174
Существенное преимущество сварного шва с кинжальным проплавлением по сравнению со швом, имеющим полусферическую форму проплавления, более характерную для дуговых методов сварки, заключается в том, что при кинжальном проплавлении для получения швов аналогичной глубины необходима меньшая энергия. Швы с примерно одинаковой формой зоны проплавления получаются при ЭЛС в разных пространственных положениях (как электронного пучка, так и свариваемого изделия). В большинстве случаев ЭЛС производят вертикальным электронным пучком (сварка в нижнем положении), однако применяются и технологии ЭЛС с использованием горизонтального электронного пучка, а в редких случаях сварка электронным пучком ведется и в потолочном положении. Зона термического влияния при ЭЛС с кинжальным проплавлением мала, что дает возможность сваривать изделия с расположенными в непосредственной близости от сварного шва деталями, для которых недопустим нагрев до высоких температур. Структура металла сварного шва и зоны термического влияния изменяется по сравнению со структурой исходного металла лишь в небольших объемах, как это показано на рис. 2.7.
Из рисунка видно, что кристаллическая структура основного металла свариваемых деталей изменяется только в узкой области вблизи шва.
Другой существенной характеристикой сварных швов являются показатели твердости металла. Быстропротекающий термический цикл (в частности, скорость охлаждения металла) приводит к тому, что в области сварного шва твердость металла выше, чем твердость основного металла. Очень высокие значения твердости являются нежелательными (шов становится хрупким). Результаты измерения твердости металла сварного соединения приведены на рис. 2.8. В результате закалки металла при сварке твердость металла шва, измеренная по Виккерсу, увеличилась по сравнению с твердостью основного металла почти в 4 раза. Если такое увеличение твердости нежелательно, следу-
175
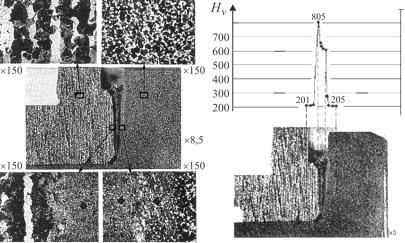
ет поменять режим сварки. В некоторых случаях целесообразно применение предварительного подогрева деталей (при относительно небольших значениях толщины металла необходимые значения температуры удается достигнуть, используя подогрев поверхности деталей расфокусированным электронным пучком).
Рис. 2.7. Форма сварного шва |
Рис. 2.8. Твердость шва |
и микроструктура зоны |
по Виккерсу Нv, измеренная |
термического влияния (внизу) |
на участке шва и зоны |
и основного металла (вверху) |
термического влияния |
В последние несколько десятилетий ЭЛС применяется не только для соединения гетерогенных и разнородных металлов, но и для сварки химически активных при высоких температурах и тугоплавких металлов и их сплавов (Zr, Ta, Ti, Hf, Nb, Mo, W,
Be, V, Li и др.).
Электронный пучок является удобным инструментом для соблюдения различных требований к выполнению сварных соединений благодаря легкому и безинерционному управлению вводом энергии в металл и регулированию конфигурации зоны
176
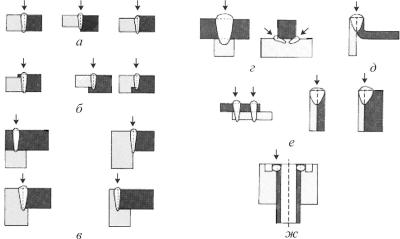
нагрева свариваемого изделия с использованием микропроцессорных систем. Кроме непрерывно действующего электронного пучка, для более точного регулирования вводимой в металл тепловой энергии и для сварки сплавов с легко испаряющимися компонентами, а также в случаях микроразмерной электроннолучевой обработки возможно использование импульсных электронных пучков. При этом длительность импульсов воздействия пучка находится в пределах 0,01–0,000 05 с, а частота следования импульсов – до 300 импульсов в секунду.
Конструкция сварных соединений для ЭЛС может быть очень различной. На рис. 2.9 показаны различные варианты конструкции сварных соединений при использовании кинжальной формы шва.
В практических случаях применения ЭЛС можно встретить очень большое количество конкретных решений выполнения сварных соединений. Несколько примеров сварных узлов, полученных с применением ЭЛС, приведено на рис. 2.10 и 2.11.
Рис. 2.9. Типичные соединения при ЭЛС: а – встык; б – « в замок»;
в– угловые; г – Т-образное; д – с отбортовкой; е – внахлест;
ж– приварка фланца к трубе
177
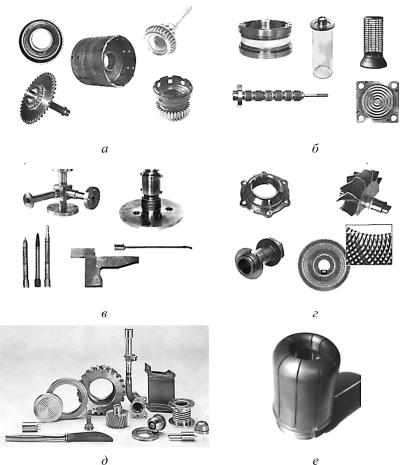
Рис. 2.10. Некоторые примеры применения ЭЛС: а – элементы коробок передач автомобилей; б – вверху – узлы вакуумных электронных приборов, внизу – соединение деталей разной толщины (сильфоны, мембраны); в – узлы измерительных приборов; г – детали самолетных турбин и электродвигателей; д – детали бытовых приборов и промышленных машин; е – разъемный соединитель из вольфрама и меди для мощных электрических цепей
178
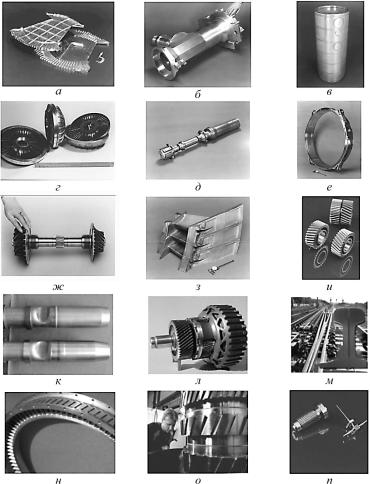
Рис. 2.11. ДругиепримерыпримененияЭЛС: а– радарныеволновые
иантенныеузлы; б, в, г– корпусныеэлементыразличныхизделий;
д– измерительныйэлементизтитановогосплава; е, ж– деталиавиационногодвигателя; з– элементтурбиныэлектрогенератора; и– зубчатыеколеса авиационногоредуктора; к– распределительныевалы; л– блокшестерен
автоматическойкоробкипередачавтомобиля; м– железнодорожныестрелки, сваренныеизстандартныхрельс; н– элементавиационнойтурбины; о– турбинныйвалбольшогоэлектрогенератора; п– датчикдавления
179
Можно отметить, что максимальная глубина при однопроходной ЭЛС с мощностью электронного пучка 60 и 120 кВт (по данным Института электросварки им. Е.О. Патона, Киев, Украина) составляет соответственно: для углеродистых сталей 100 и 200 мм, для аустенитных сталей – 120 и 250 мм; для титана – 150 и 300 мм; для алюминиевых сплавов – 200 и 400 мм.
Таким образом, основные преимущества ЭЛС заключаются в следующем:
–широкийдиапазонзначенийтолщинысвариваемыхдеталей;
–формирование узких и глубоких сварных швов;
–прецизионное управление вводом тепла в свариваемый
металл;
–мелкодисперсная структура металла сварного шва (существенно отличающаяся от близкой к литой структуры широких сварных швов, полученных дуговыми способами сварки);
–узкая зона термического влияния;
–высокие декоративные свойства сварного шва и сохранение чистоты свариваемого изделия после сварки;
–минимальные деформации сварной конструкции;
–возможность сварки с высокими скоростями, что обеспечивает высокую производительность процесса и эффективное использование энергии;
–возможность автоматизации процесса, включая комплексную автоматизацию;
–высокая универсальность оборудования для различных применений;
–отсуствие необходимости использования дополнительных сварочных материалов (сварочных электродов, проволки, флюсов, защитных газов и т.п.).
В то же время процессу ЭЛС присущ и ряд недостатков:
–высокая цена электронно-лучевого оборудования;
–высокие требования к механической подготовке свариваемых кромок в связи с необходимостью отсуствия зазора между ними (зазор в стыке свариваемых деталей не должен превышать 0,1 мм);
180