
1514
.pdf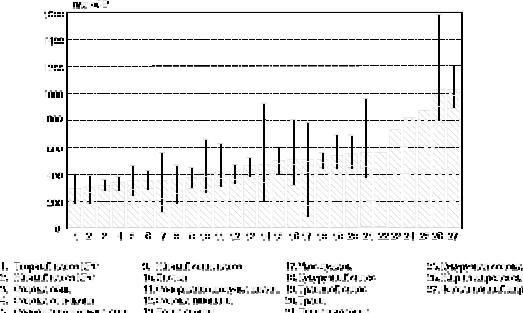
Рис. 1.14. Выход биогаза для различных субстратов [20]
частиц, в особенности бактерий, и пузырьков газа. Верхняя граница концентрации твердых частиц, при которой еще возможно свободное перемещение фаз, для субстрата с мелкодисперсной взвесью твердых веществ соответствует 10…12 %. При больших значениях выход газа значительно уменьшается. Путем интенсивного перемешивания и соответствующего подвода энергии нежелательный эффект можно существенно ограничить. Условия метаногенеза приведены в табл. 1.9.
6. Размеры твердых частиц [11, 13, 20,]
Активного обмена веществ и высокой скорости биохимических обменных процессов можно достигнуть, если поддерживать и непрерывно обновлять максимально возможную величину граничных поверхностей между твердой и жидкой фазами. Поэтому твердые материалы должны быть предварительно подготовлены с помощью дробилок и шредеров, чтобы в результате эффективного механического воздействия получить частицы возможно меньшего размера. Доля взвешенных в жидкости твердых частиц в значительной мере зависит от технических средств, которые используются для получения тщательного перемешивания, гидравлического транспортирования субстрата и отделения газа.
31
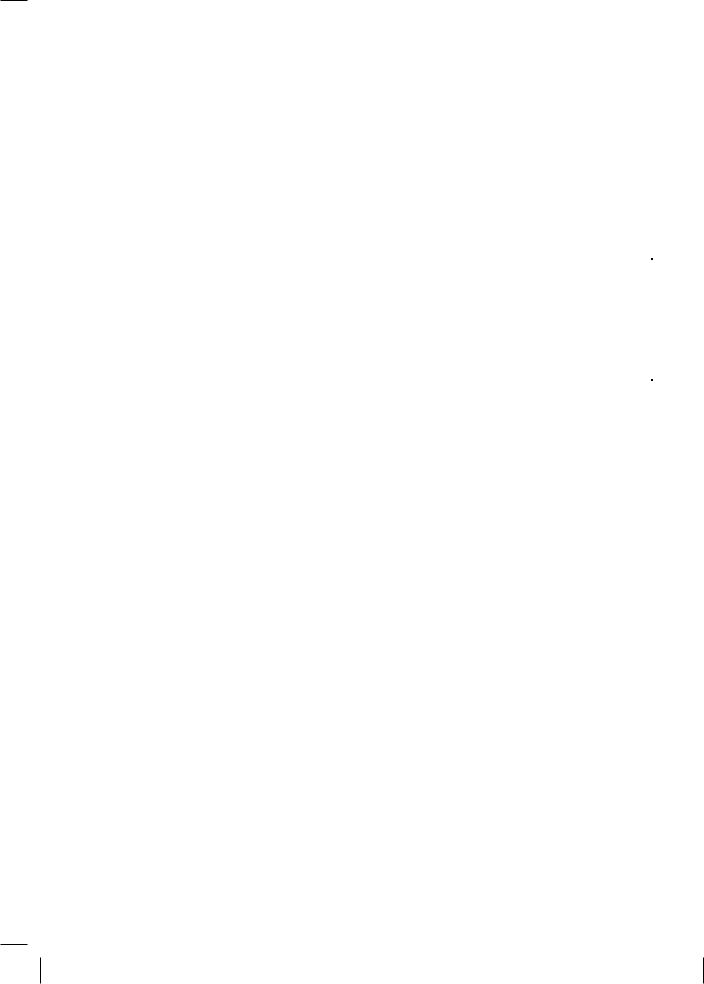
|
Таблица 1 . 9 |
Минимальные физико-химические требования к метаногенезу [20] |
|
|
|
Фактор среды |
Значение |
Уровень рН |
6,5–8,0 |
Электропроводность (содержание солей) |
2,5–25 мСм/см |
Температура |
8–55 град |
Элемент |
Концентрация, % |
Кислород |
Менее 0,0001 |
Водород |
6 Па |
Общий углерод |
ХПК 0,2–50 г/л |
Натрий |
0,0045–0,02 |
Калий |
0,075–0,025 |
Магний |
0,001–0,004 |
Сера |
0,005–0,01 |
Железо |
0,001–0,02 |
Никель |
0,00005–0,003 |
Кобальт |
0,00005–0,002 |
Молибден, вольфрам, селен |
0,00001–0,000035 |
Цинк |
0–0,0003 |
Фосфаты |
0,005–0,015 |
Соотношение C : N : P : S (в целом процесс) |
2000 : 15 : 5 : 3 |
Твердые вещества, плотность которых существенно выше, чем жидкости, обусловливают образование осадка (седиментацию) или плавающей корки, чему способствует флотация. Возникающие в связи с этим механико-гидравлические проблемы и ухудшение процесса газообразования могут привести к тому, что для устранения подобных нарушений потребуются более высокие затраты технических средств и энергии.
Эти трудности можно исключить, если упомянутые вещества перед подачей в реактор отделить от субстрата с помощью механического сепаратора [13]. Однако это приводит к соответствующему уменьшению выхода газа. Степень измельчения сырья имеет влияние на количество произведенного газа через длительность периода брожения. Чем короче период брожения, тем лучше должен быть измельчен материал.
1.4.3. Технологические факторы, влияющие на процесс анаэробной переработки отходов
Практически достижимый в промышленной установке выход газа зависит от многочисленных факторов, влияние которых, обусловленное конструкцией установки и производственными условиями, может быть самым различным. В дополнениекуже названным вразделе 1.4.2 факторам существенное значение имеют:
– загрузка рабочего пространства (количество загружаемой органической массы, приходящееся на единицу времени и единицу чистого объема реактора);
32
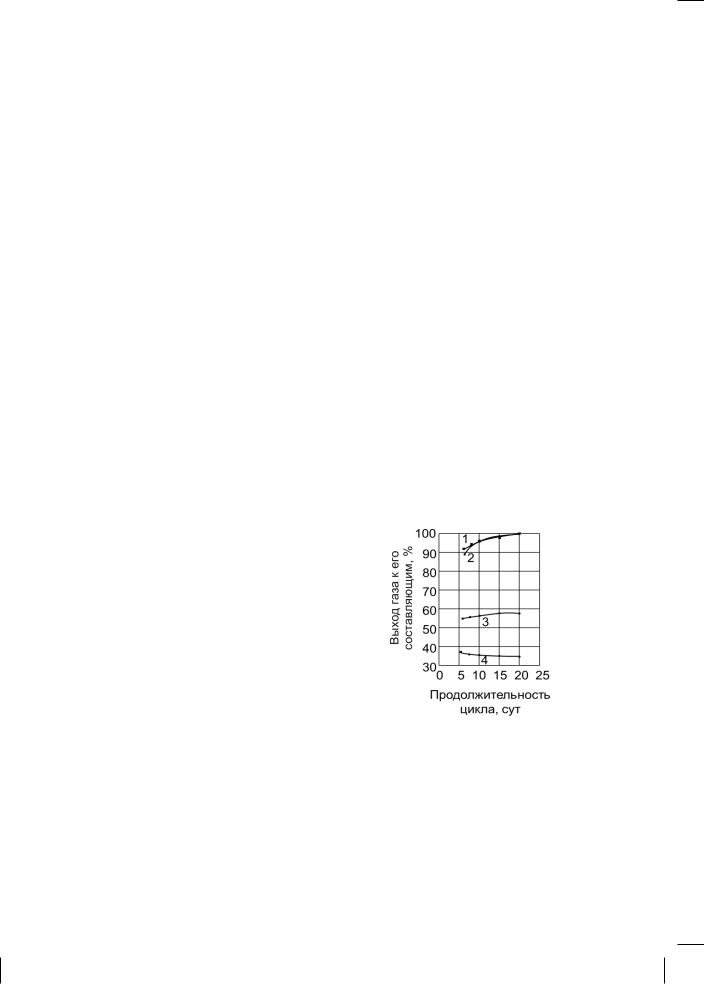
–технологическое время цикла брожения (время пребывания в реакторе закладываемой в него органической массы);
–интенсивность перемешивания.
1. Загрузка рабочего пространства
При непрерывном или квазинепрерывном технологическом процессе сбраживания наибольшая интенсивность разложения получается в том случае, если количество органического вещества, которое добавляется в единицу времени к находящемуся в реакторе субстрату, соответствует уже разложившемуся к данному моменту количеству органического вещества. Добавление больших партий массы ведет к получению менее разложившегося субстрата и, следовательно, к меньшему выходу газа [13], добавление меньших партий – к худшему использованию рабочего объема реактора.
Если реактор, работающий в дискретном режиме, заполнять слишком быстро, то нарушается соотношение между имеющимся количеством активных бактерий и массой питательных веществ, вследствие чего обмен веществ также не может протекать оптимальным образом, и, соответственно, выделяется меньше газа
вединицу времени и на единицу массы органического вещества. Загрузка реактора должна быть тем ниже, чем выше доля способных к разложению веществ
взакладываемой в него органической массе.
2.Технологическое время брожения (время пребывания массы в ре-
акторе) [11, 13, 20]
Потребность во времени, необходимом для полного сбраживания массы, как правило, очень большая, что соответственно должно было бы привести к применению реакторов больших размеров. Поэтому, исходя из экономических соображений, несколько укорачивают время пребывания массы в реакторе, сознательно идя на некоторое недополучение газа.
Выбор продолжительности пребывания массы в реакторе зависит, с одной стороны, от скорости реакции, присущей каждому кон-
кретному виду сбраживаемого материала, |
|
сдругой стороны, от заданной степени разло- |
|
жения, которая определяет выход газа и ослаб- |
|
ление интенсивности запаха перебродившей |
Рис. 1.15. Количествои состав выде- |
массы (шлама). Кроме того, следует учитывать, |
|
что с увеличением времени брожения увели- |
лившегосягаза[13]: 1 и2 – количество |
чивается содержание СН4 в общем объеме вы- |
всего выделившегося газаиметана |
соответственнов% от выходак момен- |
|
деляющегося газа и одновременно уменьшает- |
туокончания цикла; 3 и 4 – содержание |
ся содержание СО2, что означает улучшение |
СН4 и CO2 соответственно в% отвсего |
качестваполучаемогогаза(рис. 1.15). Продол- |
выделившегося газа |
|
|
|
33 |

жительность брожения в условиях прерывистого производства газа по современным данным примерно на 20… 25 % дольше.
3. Интенсивность перемешивания
Интенсивным перемешиванием содержимого реактора достигается контакт бактерий с субстратом вследствие постоянной перемены ориентации и обновления граничных поверхностей отдельных фаз, а также затрудняется накапливание промежуточных и конечных продуктов процесса разложения. Будучи основной предпосылкой высокой скорости реакции, перемешивание способствует также равномерному распределению питательных веществ в объеме реактора. В то же время оно препятствует образованию осадка и плавающей корки
иобеспечивает перемещение массы в реакторе.
1.4.4.Технологические схемы биогазовых установок
1.4.4.1. Системы, применяемые в производстве (рис. 1.16)
Система с попеременным использованием реакторов [11, 13, 20] характеризуется прерывистым процессом, протекающим не менее чем в двух одинаковых по размерам и форме реакторах (рис. 1.16 и 1.17).
Рис. 1.16. Системы получения биогаза
34
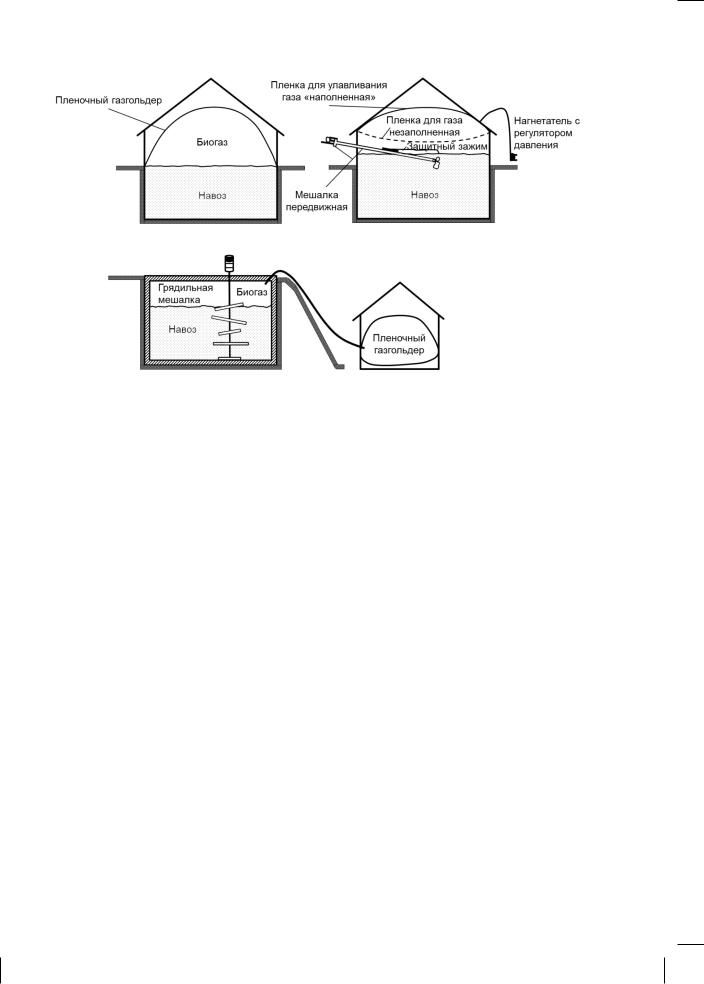
Рис. 1.17. Накопительная система
Поскольку при постоянном количестве подаваемого в реактор материала загрузка рабочего пространства во время процесса заполнения будет постоянно снижаться по сравнению с оптимальным значением, соответствующим исходному количеству шлама, потенциальная производительность этой системы будет использоваться не полностью. Кроме того, если учитывать наличие порожнего объема реактора во время процесса заполнения, то эта система требует большего рабочего объема, чем проточная; согласно американским исследованиям он должен быть вдвое больше [15]. Еще одна особенность рассматриваемой системы заключается в том, что ее нельзя использовать без газового аккумулятора (газгольдера) с постоянным запасом газа, достаточным для заполнения освобождающегося при выгрузке шлама объема реактора. Это требуется для предотвращения попадания воздуха в рабочее пространство реактора.
В проточной системе (при непрерывном или квазинепрерывном процессе) субстрат загружают в реактор непрерывно или через короткие отрезки времени (например, ежесуточно), удаляя соответствующий объем шлама (см. рис. 1.16).
Если обеспечивается постоянство условий производства, то этот вид производства позволяет получить максимальный выход газа при непрерывном процессе газообразования.
Система с накоплением газа и шлама [23] выполняется только с одним жидкостным реактором (см. рис. 1.16, 1.17). Последний играет роль бродильной камеры и накапливает шлам до момента вывозки в поле. Поэтому реактор никогда не опорожняют полностью; остаток шлама служит затравкой для новой
35
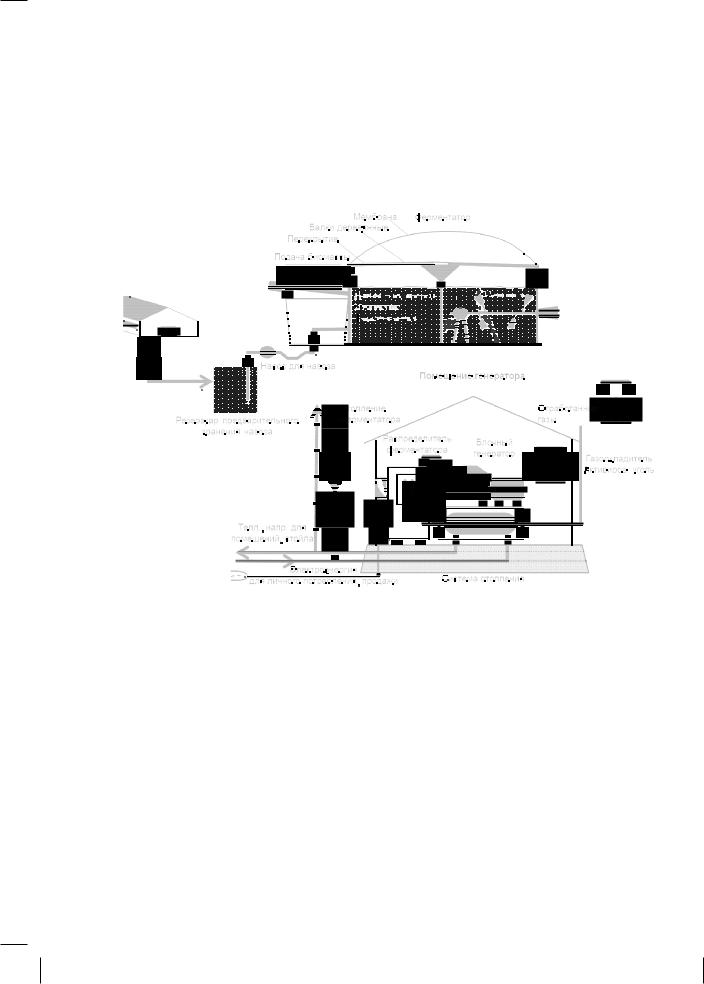
порции субстрата. При непрерывной подаче свежего субстрата постоянно снижается время, отводимое для брожения. В результате этого газовый потенциал накопившейся в реакторе массы используется не полностью.
В промышленных масштабах для получения биогаза из ТБО чаще используют проточно-накопительные системы (рис. 1.18), отличающиеся тем, что реактор (метантенк) находится постоянно в загруженном состоянии.
Рис. 1.18. Схема проточно-накопительной установки [20]
Пульпа из отходов подается в реакционную среду постоянно. Данный тип реакторов отличается стабильностью работы и однородностью условий, что обеспечивает высокий выход биогаза и компактность установок.
1.4.4.2. Компоненты установки
Реактор. Конструкция реактора для получения биогаза зависит от ряда технологических требований, наиболее часто упоминаются в литературе следующие виды:
–вертикальные цилиндрические,
–горизонтальные цилиндрические,
–траншейного типа,
36
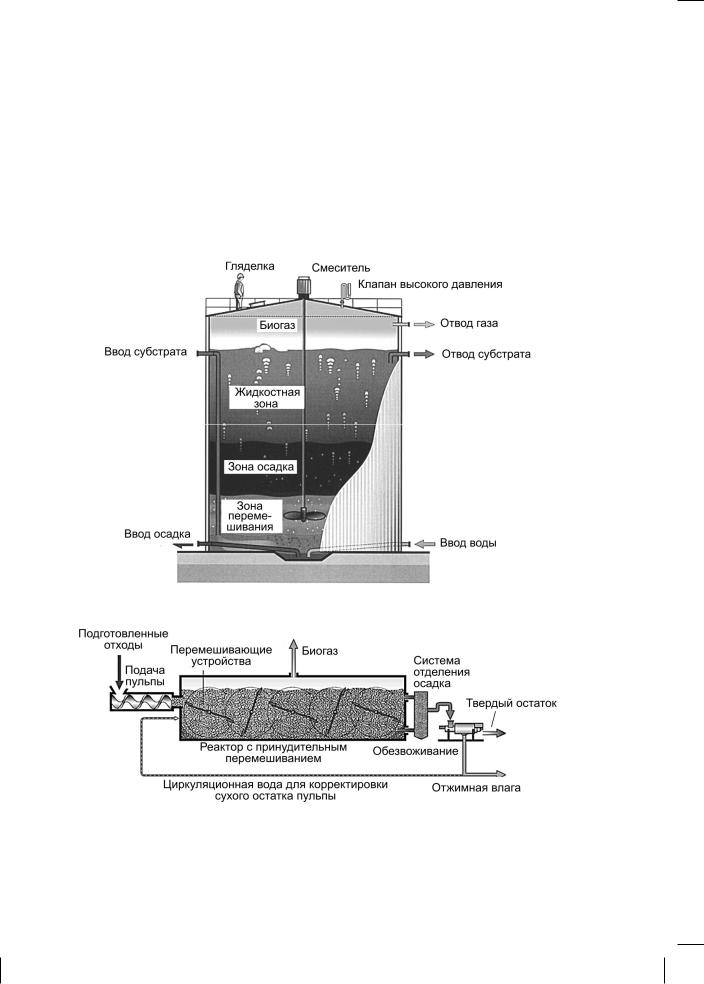
–кубические,
–из эластичных материалов (форма пузыря).
Наиболее часто для сбраживания высокообводненных отходов применяются вертикальные реакторы с принудительной механической мешалкой (рис. 1.19). Отвод газа осуществляется в верхней части реактора, отвод субстрата – в средней части. Реактор работает в проточном режиме. Для обеспечения безопасности реактор оборудован предохранительным клапаном.
Для сбраживания отходов с низким содержанием влаги (сухое сбраживание) чаще применяются горизонтальные реакторы (рис. 1.20).
Рис. 1.19. Общий вид метантенка для сбраживания отходов
Рис. 1.20. Горизонтальный реактор с принудительным перемешиванием для «сухого» сбраживания отходов
37
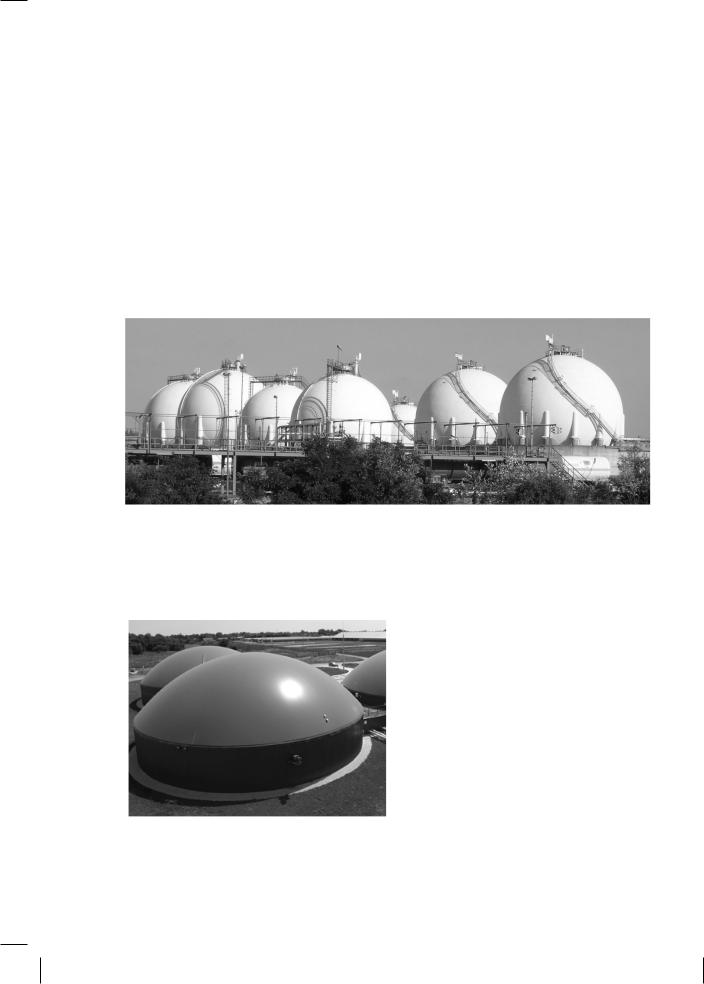
Накопление биогаза. В литературе приводятся следующие основные технические варианты накопления газа:
–подземное газохранилище пористого типа – хранение газа под давлением
вподземном пласте пористой породы, который сверху и с боков ограничен газонепроницаемыми слоями;
–подземное газохранилище кавернозного типа – хранение газа под давлением в специально оборудованных под землей газонепроницаемых полостях;
–газгольдер высокого давления (для сжиженного природного газа);
–газгольдер низкого давления.
Наиболее часто применяемый вариант накопления биогаза для заводов МБПО – это газгольдеры низкого и высокого давления. Для газгольдеров высокого давления традиционно выбирают сферические резервуары (рис. 1.21).
Рис. 1.21. Газгольдер сферического типа
Они работают обычно при рабочем давлении 0,8… 1 МПа. К их преимуществам относятся сравнительно небольшие габариты и отсутствие каких-либо движущихся частей. Недостатком считается необходимость в компрессорной установке. Биогаз приходится засасывать из бродильной камеры реактора.
Для использования газа в качестве топлива требуется дополнительно понизить давление до 1…5 кПа.
Уже традиционной стала конструкция цилиндрических реакторов, оборудованных эластичным колпаком, выполняющим также роль газгольдера низкого давления. Аналогичную конструкцию могут иметь отдельно стоя-
Рис. 1.22. Газгольдер с эластичным колпаком щие газгольдеры(рис. 1.22).
38
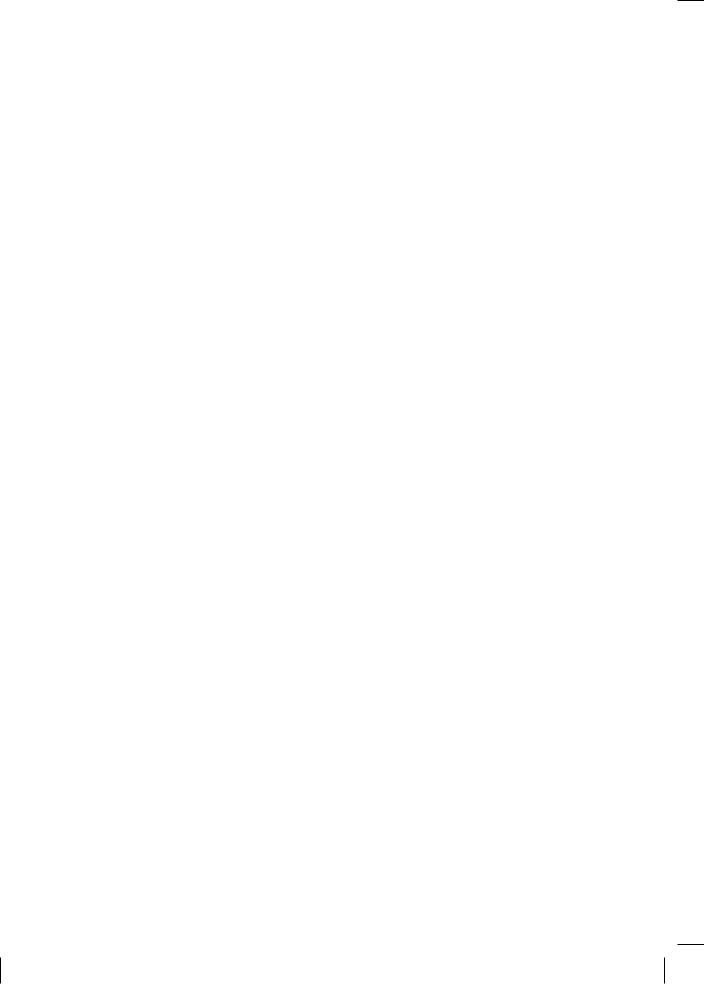
Чаще всего тенты газгольдеров изготавливают из EPDM (этилен-пропилен- диен-метиленового) каучука толщиной 1,2–1,5 мм. Этот материал среди прочего отличается большой устойчивостью к ультрафиолету и озону, а также слабой пропускной способностью.
Возможно использование в качестве крыши газгольдера конического, укрепленного тканью тента из ПВХ, фиксирующегося центральным контрфорсом, в качестве внешней защиты от неблагоприятных погодных условий. При этом внутри прокладывается еще один слой пленки ПВХ, повторяющий контуры внешнего слоя.
Подготовка биогаза. Биогаз, поступающий только что из ферментатора, почти на 100 % насыщен водяным паром и преимущественно имеет высокое содержание сероводорода, что вызывает коррозию трубопроводов, арматуры, газовых счетчиков и газопотребляющего оборудования. При интенсивном перемешивании могут образовываться также аэрозоли – мелкие капли жидкости из субстрата, переносящиеся вместе с газом, которые осаждаются и образовывают отложения.
Первым важным этапом подготовки биогаза перед использованием является удаление влаги, которое осуществляется в конденсаторах за счет охлаждения. Удаляемая влага используется далее в технологическом процессе.
Для очистки биогаза от серы применяются следующие методы: 1. Химико-физический метод:
а) добавление в бродильный субстрат солей железа; б) адсорбирование железосодержащими субстратами (сухой фильтр); в) фильтр из активированного угля.
2.Биологический метод.
3.Комбинированный метод.
Добавление в бродильный субстрат солей железа не обеспечивает достаточно низкого уровня сероводорода на выходе, но отличается низкой себестоимостью. Адсорбция сероводорода на гранулах, содержащих соли железа, отличается значительными затратами на регенерацию загрузки, в связи с чем данный метод практически не используется в настоящий момент. Адсорбция с использованием активированного угля, импрегнированного йодом, обеспечивает высокую степень очистки (в том числе от ряда других примесей), имеет сравнительно низкую себестоимость.
На сегодняшний день очистка от серы биологическим методом путем направленного нагнетания небольшого количества воздуха в газовую камеру метантенка получила очень широкое распространение. Благодаря деятельности серных бактерий (Sylfobakteroxydans) при подаче воздуха сероводород превращается в элементарную серу, а также серные кислоты и воду. При этом сера выпадает в виде желтоватого осадка на поверхности субстрата и при вносе
39
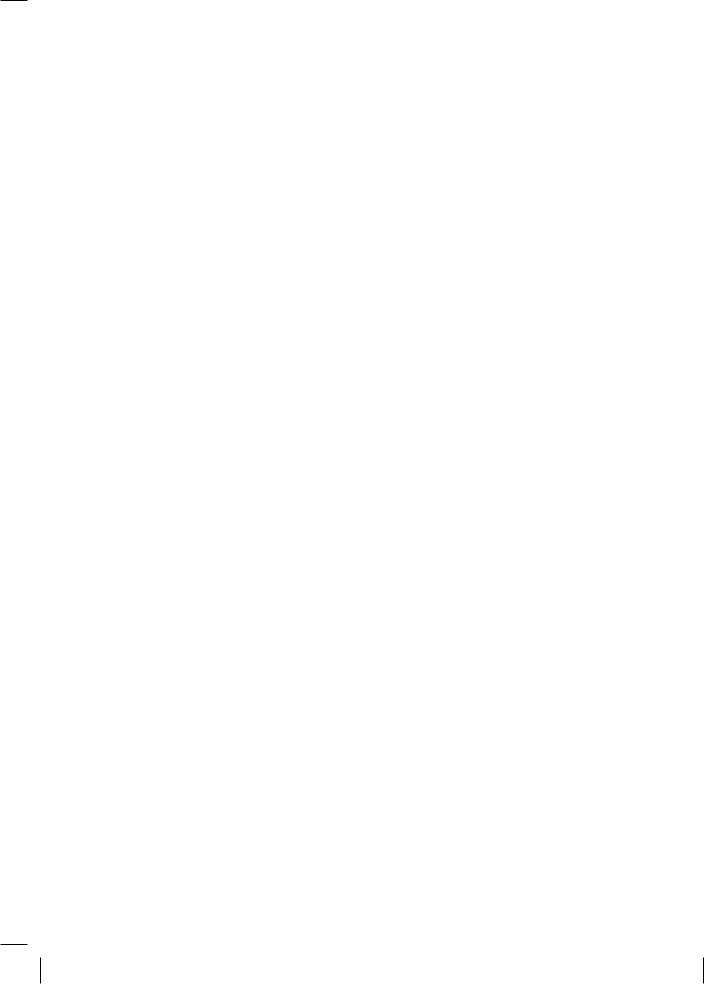
в грунт используется в качестве питательного вещества для растений. Описанный выше метод применяется приблизительно на 90 % в биогазовых установок. Причиной для этого в первую очередь является простое устройство, которое при правильном применении дает достаточную очистку до 0,001 % H2S биогаза, а также небольшие затраты на приобретение и обслуживание [20].
Комбинация из химико-физического и биологического метода очистки применяется в первую очередь там, где требуется почти чистый газ с примесями не более 0,0005 %, как, например, это требуется в случае подачи в газоцентрали или при использовании биогаза в топливных элементах, или в качестве топлива [20].
1.5. Экологические аспекты МБПО
Возможное воздействие процессов МБПО на окружающую среду может быть реализовано в виде воздействия на атмосферный воздух, объекты гидросферы, почву и здоровье человека.
1.5.1. Загрязнение атмосферного воздуха
Аэробные процессы биологической переработки отходов (компостирование, биосушка, дозревание компоста) являются источником выброса следующих загрязняющих компонентов: углекислого газа, биоаэрозоля (бактериальные клетки, вирусы, споры и пр.), летучих органических соединений, неорганической пыли, аммиака.
При анаэробном процессе загрязняющие примеси входят в состав биогаза и поступают в атмосферу при его сжигании. К подобным примесям следует отнести: монооксид углерода, оксиды азота, оксиды серы, сероводород. При аварийных ситуациях и при сбросе через предохранительные клапаны возможно поступление метана и прочих летучих органических соединений [1].
На стадии механической переработки в атмосферный воздух поступают пыль, биоаэрозоль и одоранты. Более подробно источники указанных поллютантов рассмотрены в табл. 1.10.
Способы очистки газовых выбросов от предприятий МБПО
Система очистки газовых выбросов от предприятий МБПО, включающих механическую обработку отходов и аэробную стадию, как правило, предусматривает наличие биофильтров и термического окислителя.
Биофильтры достаточно часто используются на предприятиях МБПО для контроля за содержанием одорантов и биоэрозолей. Связано это с их достаточной дешевизной. Более подробно устройство биофильтра рассмотрено в главе 2 в разделе, посвященном очистке газовых выбросов от компостирования.
40