
2858.Оборудование литейных цехов учебное пособие
..pdf
11.4. Выбор конструктивно-технологических параметров газоимпульсных формовочных машин
1.Объем газоимпульсной камеры сгорания Vк = (3,5…5,5) Vсм, где Vсм – начальный объем уплотняемой смеси.
Конструктивно камера сгорания чаще всего представляет собой цилиндр со штампованными сферическими днищами. Расчет на прочность камеры сгорания проводится по обычным формулам сопромата.
2.Скорость потока газов, создаваемых вентилятором в камере сгорания, v2 = 0–12 м/с.
3.Площадь поперечного сечения дефлектора
Fд = 12 F2 ,
где F2 – площадь поперечного сечения камеры сгорания; диаметр дефлектора Dд = 2F2 / π.
Толщина стенки дефлектора δ = 0,004…0,005 м.
4.Площадь поперечного сечения переходной камеры Fпер выбирается из соотношения Fпер/Fо = 1/(3–5), где Fо – площадь опоки в свете.
5.Площадь клапана выброса Fкл отработанных газов выбирается из соотношения Fо/Fкл = 10:1.
Скоростное (ударное) прессование. Наиболее простой ва-
риант этого процесса – единичный удар прессовой колодки по смеси, находящейся в опоке. Слоям смеси и отдельным частицам, так же как и при газовой и воздушно-импульсной формовке,
сообщается достаточно высокая скорость движения (6–8 м/с). В результате удара слои смеси и колодка под действием сил инерции движутся с большой скоростью в направлении модельной плиты, что и приводит к более равномерному уплотнению, чем при статическом прессовании. Кроме того, при ударе повышается давление воздуха, находящегося в порах смеси, образуются фильтрационные потоки в направлении вент в оснастке,
221
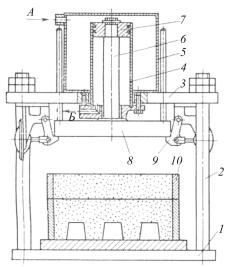
что также способствует снижению внешнего и внутреннего трения и повышению равномерности плотности смеси.
Рис. 11.5. Схема рабочего органа процесса скоростного прессования
Схема рабочего органа скоростного (ударного) прессования представлена на рис. 11.5. Нижняя траверса 1 и верхняя 3 соединены четырьмя колоннами 2. На нижней траверсе устанавливается модельно-опочная оснастка 10 со смесью, а на верхней – пневмоударник, состоящий из рабочего цилиндра 4 с поршнем 7. На нижнем конце штока 6 закреплена прессовая плита 8, удерживаемая от падения пневмозахватами 9. Рабочий цилиндр 4 встроен в ресивер 5, питаемый от сети сжатым воздухом р = 0,5…0,6 МПа. Впуск воздуха в ресивер производят через отверстие А до начала удара, одновременно открывается отверстие Б для свободного выхода воздуха из штоковой полости цилиндра в атмосферу. Затем захваты 9 отводятся в сторону. Под действием давления воздуха в ресивере колодка ударяет по смеси и уплотняет ее. Процесс скоростного прессования обладает рядом преимуществ.
222
Равномерность плотности смеси по высоте опоки намного выше, чем при статическом прессовании. Время уплотнения исчисляется сотыми долями секунды. Расход воздуха на уплотнение одной формы незначительный. Режим рабочего органа легко регулируется давлением воздуха в ресивере и ходом прессовой колодки. Колебания фундамента в 3–4 раза ниже, чем при встряхивании.
К недостаткам процесса следует отнести высокую чувствительность к режимам уплотнения, необходимость устройства вент как на модельной плите, так и в карманах моделей.
Пневматический ударный привод хотя и прост конструктивно, но скорость его ограничена (v = 10…12 м/с), он имеет значительные габариты. Эти недостатки исключены в пневмогидравлическом и магнитоимпульсном приводах, но их мало применяют.
Вопросы для повторения
1.Поясните устройство газоимпульсной формовочной установки.
2.Факторы, влияющие на рабочий процесс газоимпульсных машин.
3.В чем преимущества и недостатки газоимпульсного процесса уплотнения?
12. ПЕСКОМЕТЫ
Пескомет – формовочная машина, механизирующая процесс уплотнения смеси в опоке. Отличительной особенностью пескомета является совмещение двух технологических операций: заполнение форм смесью и ее уплотнение. Второй основной особенностью пескомета является равномерность степени уплотнения смеси по высоте полуформы независимо от ее высоты, площади и местоположения опоки в зоне его досягаемости.
223
В связи с такими преимуществами в сочетании с транспортным, поворотным и вытяжными устройствами пескомет эффективно используется при изготовлении форм и стержней в единичном, мелкосерийном и массовом производстве средних и крупных отливок. Распространение метода на мелкие и частично средние отливки сдерживается недостаточной производительностью серийно выпускаемых пескометов.
Однако и этот недостаток в последние годы находит свое разрешение благодаря разработке надежно работающих ширококовшовых пескометов. Так удалось создать конструкцию пескометов, которые позволяют использовать на одном и том же пескомете (например, с шириной ленты В = 1600 мм) полуформы различной ширины, но существенно не отличающиеся по высоте. Уплотнение же опок разной длины не представляет на пескомете проблемы, так как это легко регулируется ходом тележки, на которой установлена опока. Пескомет может уплотнять как низкопрочные, так и высокопрочные смеси. Заданная плотность смеси достигается определенной скоростью перемещения головки (или оснастки), обеспечивающей равномерное распределение поступающих в форму пакетов.
Важнейшим фактором, оказывающим влияние на надежность и долговечность пескомета, является степень защиты формовочной смеси от попадания в нее металлических и особенно немагнитных включений. Таким образом, следует ожидать развития ширококовшовых пескометов и не только в мелкосерийном, но и в серийном и крупносерийном производстве. Возможно также появление ширококовшовых пескометов с допрессовкой вместо срезки верхних слоев смесив настоящее время.
Метательная головка центробежного пескомета
(рис. 12.1) – основной рабочий орган пескомета. Быстро вращающийся на горизонтальном валу ротор приводится непосредственно от электродвигателя. На роторе крепится одна (как показано на данной схеме) сменная лопатка или ковш. Формовочная или стержневая смесь непрерывно поступает с ленточного
224
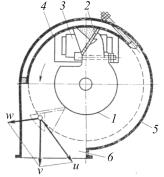
конвейера в кожух головки в осевом направлении через окно в задней стенке кожуха. Поток смеси отсекается быстровращающейся лопаткой, формируется под действием центробежных сил в пакет и продвигается лопаткой по окружности (на схеме против часовой стрелки). При этом продвижении пакет смеси ограничивается с периферии стальной направляющей дугой, которую закрепляют в головке якорным болтом и устанавливают строго по дуге окружности с минимальным зазором по отношению к кромке лопатки. При передвижении лопаткой вдоль направляющей дуги пакет смеси под действием центробежных сил приобретает некоторое уплотнение.
После того как пакет смеси и лопатка ротора пройдут горизонтальный радиус головки, где кончается направляющая дуга, начинается соскальзывание пакета с лопатки, так как теперь с периферии пакет уже не имеет ограничивающей поверхности дуги. В некотором положении лопатки, показанном на рисунке штриховой линией, центр тяжести пакета достигает окружности выходной кромки лопатки, и пакет смеси сходит с лопатки. В этот момент пакет приобретает под действием центробежных сил
некоторую выходную скорость w относительно лопатки. Абсолютная скорость схода v пакета с ротора получается как геометрическая сумма этого вектора w и вектора u переносной, окружной скорости пакета на выходной окружности ротора.
225
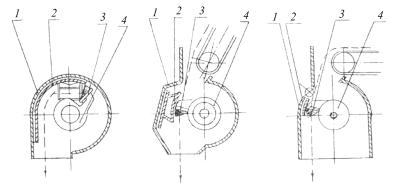
Подача формовочной смеси в головку пескомета осуществляется не только в осевом направлении, как показано на рис. 12.2, а, но и в тангенциальном, причем тангенциальный подвод может быть с принудительной загрузкой (рис. 12.2, б)
исо свободной загрузкой (рис. 12.2, в). В рукавных пескометах загрузка смеси осуществляется в осевом направлении, а в ширококовшовых – в тангенциальном. С точки зрения затрат энергии
инадежности загрузка в тангенциальном направлении более предпочтительна.
а |
б |
в |
Рис. 12.2. Подачаформовочнойсмесивголовкупескомета: а– основная; б– тангенциальная; в– свободная; 1 – кожух головки; 2 – направляющая дуга; 3 – метательный ковш; 4 – ротор
Современные центробежные пескометы выпускают производительностью до 60 м3/ч (по уплотненному объему смеси). Они имеют диаметр окружности ротора (окружности вращения выходной кромки лопатки) 400–800 мм. Частота вращения ротора n = 1000…1500 об/мин; число лопаток на роторе от 1 до 3. Выходная абсолютная скорость у пакетов смеси должна быть достаточной для получения надлежащего уплотнения литейных форм – не менее 30 м/с и до 45–60 м/с.
226
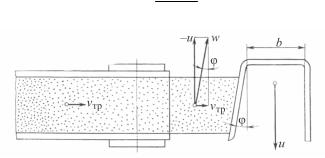
12.1. Рабочий процесс пескомета
Вход формовочной смеси на ротор. Формовочная смесь подается в головку центробежного пескомета ленточным конвейером. При этом непрерывный поток смеси на ленте конвейера превращается в дискретный поток отдельных порций или пакетов смеси на роторе.
Подача смеси лентой обычно производится в аксиальном направлении, т.е. в направлении, параллельном оси ротора головки. В этом случае из простых геометрических соотношений вытекает, что скорость транспортирующей ленты vтр м/с должна быть увязана с числом ковшей i на роторе, шириной ковша b, мм, и частотой вращенияротора n, об/мин, следующим образом (рис. 12.3):
60n vтр 103 = bi,
откуда скорость ленты
vтр = |
bin |
|
60 103 . |
(12.1) |
Рис. 12.3. Схема подачи формовочной смеси на ротор центробежного пескомета
При этих условиях поток смеси, сбрасываемый лентой, будет без потерь отсекаться последовательно подводимыми на роторе лопатками или ковшами, и ковши будут заполняться смесью полностью на всю их ширину.
227
Боковая стенка ковша со стороны подающей ленты, отрезающая поток смеси, должна быть отклонена от направления вращения ротора на некоторый угол φ, соответствующий отклонению вектора относительной скорости движения потока смеси w. Из построенного на рис. 12.3 параллелограмма скоростей легко видеть, что этот искомый угол
φ= arctg |
vтр |
, |
(12.2) |
|
u |
||||
|
|
|
где u – окружная скорость ротора на радиусе встречи ковша с потоком смеси, м/с.
Формирование пакета смеси и его уплотнение на рото-
ре. В первоначальных приближенных расчетах [1, 4] для упрощения принимали, что сечение пакета формовочной смеси на лопатке вращающегося ротора пескомета представляет собой треугольник с отношением высоты к основанию 1:1. Более подробный анализ [10] показывает, что пакет формовочной смеси, находящейся на роторе пескомета в поле центробежных сил, получает более сложное очертание свободной поверхности.
ρ= Re− f (φ−φ0 ) , |
(12.3) |
т.е. уравнение логарифмической спирали.
Здесь R – радиус ротора (радиус направляющей дуги); φ0 – угловая координата крайней передней точки пакета.
Под действием центробежных сил смесь прижимается к направляющей дуге, образуя пакет с различной по длине плотностью.
Больше уплотняется слой смеси, примыкающий непосредственно к направляющей дуге, так как на него действует также прижимающая сила всех остальных слоев пакета.
Центробежная сила, удельное давление прессования и степень уплотнения смеси зависят от радиуса, на котором лежит данный слой пакета. Для обеспечения более благоприятных ус-
228
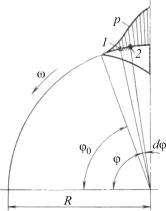
ловий движения и направления выхода смеси лопатка колеса на роторе повернута на угол γ = 15…25° к радиусу ротора.
Трение пакета смеси о направляющую дугу и расчет потребляемой ротором мощности. Центробежные силы пакета смеси оказывают на направляющую дугу давление р, эпюра которого приведена на рис. 12.4.
Рис. 12.4. Эпюра давлений пакета смеси на направляющую дугу
Силы этого давления возбуждают трение пакета о направляющую дугу. Выделив на поверхности дуги элемент 1–2 с угловым протяжением dφ и площадью bRdφ, получим момент сил трения на этом элементе
dM = R2bf1 pdφ,
где f1 – коэффициент трения смеси о дугу, который для пакета (в пределах р = 2…4 кгс/см2) принимаем постоянной величиной, не зависящей от плотности смеси.
Суммарный момент трения
|
π |
|
|
4 |
|
|
|
M = R2bf1 |
pdφ. |
(12.4) |
|
0 |
|
|
|
|
|
|
229 |
После вычисления по формуле (12.4) момента трения пакета о дугу нетрудно найти мгновенную мощность, кВт, затрачиваемую на это трение. Очевидно, при i ковшах на ротореонасоставит
Nтр.мгн = |
|
Mi πn |
1 |
= |
Mni |
, |
(12.5) |
||||
|
|
|
|
|
|
|
|||||
100 30 |
102 |
97500 |
|||||||||
|
|
|
|
а средний расход мощности (кВт) на трение пакетов смеси
Nтр.мгн = εNтр.мгн = |
εMni |
, |
(12.5а) |
|
97500 |
||||
|
|
|
где коэффициент ε учитывает, что трение пакета имеет место не на всей окружности вращения ротора, а лишь на той ее части, где имеется направляющая дуга. Очевидно, ε = ψ/360, где ψ – центральный угол направляющей дуги. Для обычной конструкции метательной головки ψ = 90° и ε = 0,25.
Кроме преодоления трения пакетов смеси о направляющую дугу, приводная мощность ротора метательной головки пескомета расходуется на преодоление других вредных сопротивлений, а именно потерь на трение в подшипниках Nподш и вентиляционных потерь Nвент, а также на полезную работу выбрасывания пакетов смеси Nпол. Полная мощность привода головки, таким образом, составляет
N = Nпол + Nтр + Nподш + Nвент. |
(12.6) |
Мощность, кВт, расходуемая на трение в подшипниках, определяется по обычной формуле
Nподш = |
Gf2rn |
, |
(12.7) |
|
97500 |
||||
|
|
|
где G – вес ротора, кгс; f2 – коэффициент трения в подшипниках; r – радиус подшипника, см; n – частота вращения вала ротора, об/мин.
Мощность вентиляционных потерь можно определить исходя из предположения, что массе (кгс·с2/м) воздуха в кожухе метательной головки,
230