
1757
.pdf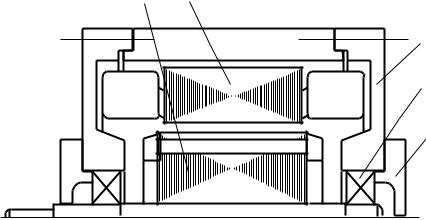
Пример ССС для простейшей конструкции асинхронного электродвигателя с к.з. ротором (рис. 1) приведен на (рис. 2). Здесь горизонтальной линей 1 условно показана спецификация общего вида, а линиями 2,3 и 4 – спецификации сборочных единиц, получаемых в процессе изготовления статора в сборе. Такие же линии спецификаций сборочных единиц показаны в потоках ротора и щита подшипникового.
1 2
3
4
5
Рис. 1. Конструктивная схема асинхронного электродвигателя с к.з. ротором: 1
– ротор; 2 – статор; 3 – щит подшипниковый; 4 – подшипник; 5 – крышка
Из рисунка можно легко сделать вывод, что изготовление составных частей двигателя можно производить одновременно и независимо друг от друга отдельными потоками: статор, ротор, щит, крышки, шайбы, крепеж. Таким же образом параллельными потоками (или подпотоками) можно организовать изготовление частей каждой сборочной единицы.
Сохраняя все потоки и подпотоки, можно для каждой детали и сборочной единицы, указанных на (рис.2), назначить необходимые для изготовления операции, расположив их в надлежащей последовательности, образуя технологический маршрут. В итоге получим так называемую технологическую схему производства (ТСП) электрической машины, которая позволит не только логически связать конструкцию машины с технологией ее изготовления, но и способствовать более эффективному контролю и управлению процессом выпуска изделия.
21
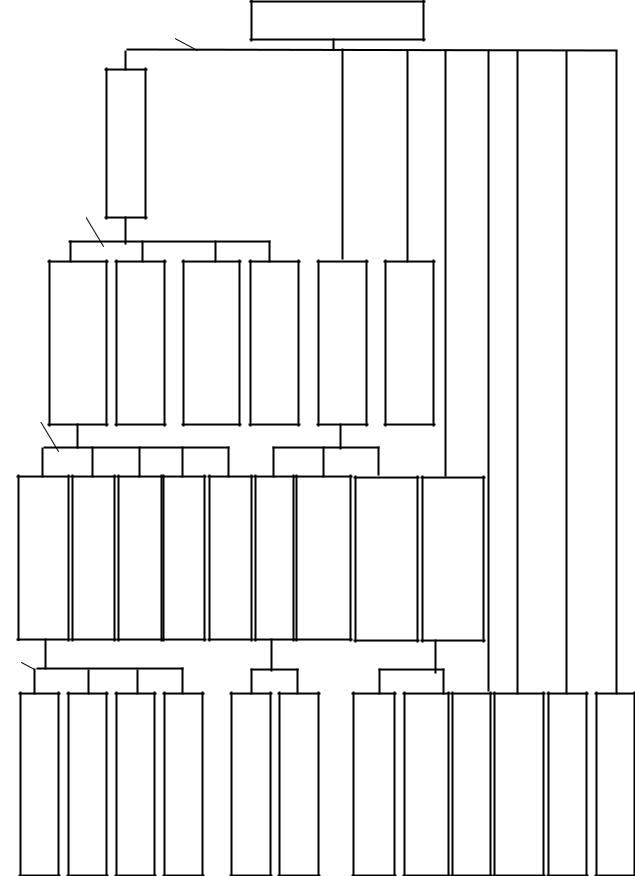
2
Электродвигатель
1
Статор в сборе
3
Статор обмотанный |
Колодка клеммная |
Крышка коробки выводов |
Крепеж |
Ротор залитый |
Подшипник |
необмотанный |
Катушка |
Выводы |
Изоляция |
Ниткибандажные |
Роторнезалитый |
алюминиевое |
балансировочный |
|
подшипниковый |
|
|
|
таторС |
|
|
|
|
|
итьеЛ |
Груз |
Щит |
|
|
|
|
4 |
статорныйЛист |
|
|
|
|
роторныйЛист |
|
алюминиевоеЛитье |
передняяКрышка |
регулировочная |
Крышказадняя |
|
Станина |
Скоба |
Крепеж |
|
Вал |
Втулка |
Крепеж |
||||||
|
|
|
|
|
|
|
|
|
|
Шайба |
|
|
Рис.2.Схема сборочного состава асинхронного электродвигателя с к.з. ротором
22
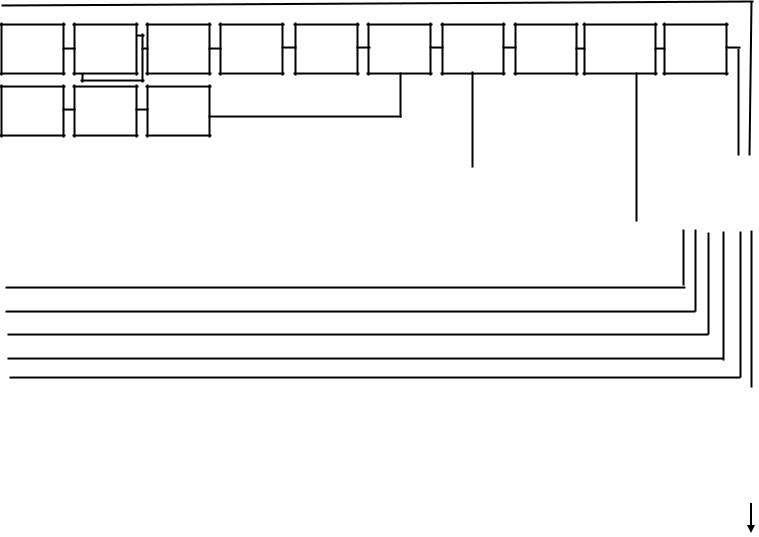
23
Вал сталь 45
Лист роторный сталь 2112
Литье алюминий А-6
Груз
балансировочный
свинец
|
|
|
|
Ротор |
|
|
|
|
|
Заготови- |
Токарная |
Фрезер- |
Терми- |
Шлифо- |
Сбороч- |
Литейная |
Шлифо- |
Балансиро- |
Контроль- |
тельная |
|
ная |
ческая |
вочная |
ная |
|
вочная |
вочная |
ная |
Заготови- |
Штампо- |
Терми- |
|
|
|
|
|
|
|
тельная |
вочная |
ческая |
|
|
|
|
|
|
|
Заготови- |
|
|
|
|
|
|
тельная |
|
|
|
|
|
Оконча- |
|
|
|
|
|
||
|
|
|
|
|
|
тельная |
|
|
|
|
|
|
|
Заготови- |
|
Штампо- |
|
|
|
сборка |
тельная |
|
вочная |
|
|
|
|
|
|
|
|
|
|
|
Щит подшипниковый Крышка передняя Крышка задняя Шайба регулировочная Крепеж
|
|
Контроль- |
|
|
|
|
ная |
|
|
|
|
|
|
|
|
|
|
|
|
|
|
Отделоч- |
|
|
Рис.3. Технологическая схема производства |
|
ная |
|
|
|
|
|
|
|
асинхронного двигателя с к..з. ротором |
Склад готовой |
|||
|
||||
|
|
продукции |
На рис. 3. в сокращенном виде показана ТСП принятой выше конструкции асинхронного электродвигателя. На этой схеме более подробно показан техпроцесс потока ротора. Согласно рис. 2. детали и другие составные части ротора изготавливаются по четырем подпотокам, где маршруты вала и листа роторного соединяются в сборочную единицу «ротор незалитый», а последний, соединяясь с маршрутами алюминиевого литья и балансировочного груза, образует сборочную единицу «ротор залитый», поступающий на окончательную сборку двигателя. Потоки остальных составных частей двигателя показаны на рис. 3. условно пунктиром, объединясь в прямоугольник «окончательная сборка». Построение ТСП может выполняться в несколько этапов, заложив в начале типовые технологические процессы, а затем, анализируя каждый маршрут с позиций имеющихся производственных возможностей и накопленного опыта, постепенно совершенствовать схему, приближая техпроцесс к оптимуму.
Отработанная ТСП может быть использована для оформления маршрутных технологических карт. Если же эту схему дополнить указаниями, в каких цехах, на каких участках и на каком оборудовании выполняется каждая операция, то такая ТСП может быть использована в диспетчерском управлении производственным процессом.
ТСП может быть полезна при проектировании новых цехов и заводов.
2.6. Производственные цехи электромашиностроительного завода
Большинство электромашиностроительных заводов работают с замкнутым циклом производства. Это значит, что на заводе изготовляются все детали и узлы, из которых комплектуются машины. Исключение обычно составляют подшипники, щетки, постоянные магниты и др. комплектующие изделия, приобретаемые заводом на специализированных предприятиях. Такие комплектующие изделия принято называть «покупными».
Замкнутый цикл усложняет организацию выпуска изделий, что особенно ощущается в многономенклатурном серийном производстве. Это приводит к увеличению количества цехов, специализированых участков, расширяет парк оборудования.
Для удобства организации и контроля управления цехи принято классифицировать по общности производственных признаков. Так, например, все цехи электромашиностроительного завода можно объединить по их отношению к основной продукции предприятия:
основные цехи, в которых обеспечиваются все технологические процессы по изготовлению изделий;
вспомогательные цехи, чаще всего обеспечивающие бесперебойную работу основных цехов.
24
Основные цехи предприятия по общим признакам используемых в производстве технологических режимов или приемов, могут, объединятся в так называемые группы цехов:
заготовительные, обеспечивающие раскрой материалов, получение заготовок и др.;
горячие, где технологические процессы предусматривают применение высоких температур;
механические, обеспечивающие чаще всего окончательное формообразование механических деталей электрических машин;
изоляционные, где изготавливаются изоляционные детали, пластмассовые изделия и т.п.;
коллекторные, где изготовляются коллекторы и токосъемные кольца; обмоточные, где производится изготовление катушек и катушечных
групп, укладка обмоток в пазы, гибка и изолировка стержней обмоток статора и ротора, изолировка катушек или их частей;
пропиточные, где производят пропитку, сушку или компаундирование обмоток, обмотанных якорей, статоров и др.;
промежуточной сборки, где производят сборку отдельных узлов электрических машин;
выпускающие, где производятся окончательная сборка, регулировка и промышленные испытания изделий;
отделочные, где производят грунтовку, шпаклевку и окраску готовых машин.
Приведенный перечень дан ориентировочно, чтобы можно было понять принцип объединения основных цехов в группы.
К вспомогательным цехам относятся различного рода ремонтные цехи, цех обслуживания территории, транспортный цех и т.п. По принятой классификации к вспомогательным следует отнести и инструментальный цех. В то же время по уровню технологической оснащенности, квалификации персонала и другим показателям этот цех не только не уступает, но зачастую и превосходит многие основные цехи.
Для удобства размещения оборудования, по общности техпроцессов или габаритов изделий, для обеспечения поточности производства в цехах выделяют более мелкие подразделения - участки.
Глава III
ОСНОВЫ ТЕХНОЛОГИИ ПРОИЗВОДСТВА МЕХАНИЧЕСКИХ ДЕТАЛЕЙ
3.1. Сортаменты материалов и получение заготовок
Механические детали электрических машин изготовляют чаще всего из различного рода металлических сплавов. Большое применение, в особенности - при изготовлении электрических машин средней и большой мощности,
25

получили черные сплавы (различные стали и чугуны). С уменьшением мощности электрических машин все чаще для изготовления корпусных деталей применяют цветные сплавы, в частности - на основе алюминия.
Важно исходному материалу детали изначально придать такую форму и размеры, чтобы трудоемкость изготовления детали и количество отходов материалов были наименьшими. Предприятия-изготовители придают выпускаемым материалам различную форму и размеры, что называется сортаментом материала. Большинство сортаментов материалов стандартизировано. Для получения конкретной детали выбирается оптимальный сортамент материала.
При изготовлении детали из выбранного сортамента, как правило, образуются отходы, например, стружка. Поэтому для изготовления детали необходимо затратить материала больше, чем весит сама деталь. Отношение чистого веса детали к весу затраченного на ее изготовление материала называют коэффициентом использования материала:
Ки |
Gдет |
, |
(1) |
|
Gнорм |
||||
|
|
|
где: Gдет - чистый вес детали;
Gнорм -норма расхода материала на одну деталь.
Коэффициент использования материала является важным показателем технологичности конструкции детали.
Некоторые стандартные виды сортамента перечислим на примере черных конструкционных металлов и сплавов:
лист-характеризуется длинной, шириной и толщиной; рулон-характеризуется шириной и толщиной ленты, а также - весом
рулона:
проволока и катанка - характеризуются диаметром сечения и весом бухты;
пруток и кругляк-характеризуется диаметром сечения и длиной; профильный прокат-характеризуется формой и размерами сечения и
длиной; чушка характеризуется формой отливки и весом и т.д.
Кроме стандартного сортамента материал можно приобрести по специальному заказу. В качестве примера можно назвать поковки, применяемые для изготовления валов крупных электрических машин. По своей геометрии поковка напоминает форму детали с припусками на обработку. Поковки для валов электрических машин изготовляют на металлургическом заводе на ковочных или радиально-обжимных машинах. В таких поковках на завершающем этапе изготовление высверливается сквозное осевое отверстие для удаления возможных пороков материала (трещин, пористости, раковин и т.п.).
26
Вкачестве примера специального сортамента можно назвать также коллекторную медь, выпускаемую кабельными заводами в виде шин трапециевидного сечения. Известно, что достаточно изменить число коллекторных пластин на одну и потребуется новый профиль меди. Этим и объясняется отсутствие стандарта на этот сортамент.
Прежде, чем приступить к изготовлению детали из выбранного сортамента материала, нужно получить заготовку /9/. Заготовка - это часть (порция) сортамента, предназначенная для изготовления одной детали. Уже при конструировании детали конструктор совместно с технологом решают, из какой заготовки и какого сортамента она может быть изготовлена. Решение этой задачи также влияет на технологичность конструкции, так как вид заготовки определяет трудоемкость дальнейшей ее обработки и коэффициент использования материала. В то же самое время способ получения самой заготовки также влияет на эти показатели.
Выбрать заготовку - это, значит, установить сортамент материала, способ
ееполучения, определить припуск на обработку, размеры и допуски. Повышение точности размеров заготовки позволяет приблизить ее к конфигурации и размерам детали, уменьшить трудоемкость обработки, снизить потери материала. С другой стороны - повышение точности размеров заготовки может усложнить ее изготовление, что также сопряжено с затратами средств.
Вэлектромашиностроении чаще всего возникает необходимость получения заготовок из прутка для изготовления валов, из листа или рулона для изготовления шихтованных магнитопроводов, тонкостенных или изоляционных деталей, а также в виде литья.
Получение заготовок из прутка достигается в две - три операции: правка, резка и в ряде случаев - обработка торцов. Последняя операция предусматривается при так называемой черновой резке, когда торцы заготовки приобретают неправильную форму или длина заготовки выполняется с недопустимой погрешностью. К таким способам следует отнести газопламенную резку, рубку на ножницах или штампах, распиловка ножовками, ленточными или дисковыми пилами и т.п.
Чистовая резка прутка предусматривает получение заготовок, осевой размер которых соответствует осевому размеру детали. Этот способ реализуется на токарных, револьверных или фрезерных станках. Изготовление заготовки для вала завершается образованием на торцовых поверхностях центровых отверстий, для чего удобнее использовать специальные фрезерноцентровальные двухпозиционные автоматы. Следует отметить, что при использовании цилиндрической заготовки для изготовления валов до 40 % материала может уходить в стружку при образовании ступеней вала. Поэтому такая форма заготовки может быть оправдана для гладких валов или - для валов с небольшим перепадом диаметров ступеней.
Более прогрессивными способами получения заготовок для валов следует считать способ пластического деформирования. Наибольшее распространение получили:
27
поперечно - клиновой прокат; радиальная ковка.
Поперечно - клиновой прокат позволяет получить заготовку ступенчатого вала с небольшим припуском на обработку ступеней, так как получаемая заготовка по форме и размерам становится очень близкой к форме и размерам детали. Это достигается деформированием нагретой до ковочной температуры (11000 - 12000 С) заготовки двумя вращающимися валками с выступающими клиновидными элементами на их внешней поверхности. Нагретая заготовка размещается между валками, которые, вращаясь, своими клиновидными выступами внедряются в тело заготовки, вращая и обжимая ее до требуемого размера. Этот способ используется для изготовления валов электродвигателей серии 4А с высотой оси до 132 мм /11, 23/.
Поперечно - клиновой прокат может быть реализован также с использованием двух плоских плашек с клиновидными выступами.
Радиальная ковка используется для получения ступеней в заготовках валов электрических машин больших габаритов, с высотой оси до 280 мм (11). Здесь хорошо зарекомендовали себя ковочные машины австрийской фирмы «Stcir», позволяющие обрабатывать заготовки диаметром до 110 мм. Нагретую до ковочной температуры заготовку размещают между четырьмя радиально расположенными бойками, совершающими колебательные движения с частотой 550 колебаний в минуту. При обработке заготовку поворачивают и перемещают вдоль оси, образуя ступень вала. Машина работает по заранее разработанной программе.
Корпусные детали электрических машин до 100 кВт (станины, подшипниковые щиты) изготовляют чаще из заготовок, получаемых литьем в специальные формы /11/. При этом применяются различные способы литья в зависимости от материала, требуемой точности размеров, габаритов, применяемой литьевой формы:
литье в землю; литье в металлическую форму (статическое и вибрационное);
литье под давлением; центробежное литье.
Литье в землю отличается малыми затратами на оснастку, но получаемые отливки имеют шероховатую поверхность, большие припуски на обработку. Этот способ отличается малой производительностью и может быть оправдан в индивидуальном или мелкосерийном производстве для получения деталей из черных сплавов.
Литье в металлические формы обеспечивает хорошее качество простых по конфигурации отливок. Этот способ предусматривает два варианта его реализации: статическое и вибрационное литье. Они отличаются тем, что в первом случае форма при заливке остается неподвижной, а во втором - в течение периода заливки и затвердевания сплава форма подвергается вибрационному воздействию, что позволяет повысить качество отливки. Способ отличается большой стойкостью форм при использовании легкоплавких
28
сплавов (цинк, алюминий и т.п.) - сотни тысяч отливок. Для черных сплавов (чугун, сталь) стойкость форм существенно уменьшается: от 600 - 700 мелких до 20 - 25 крупных отливок.
Литье под давлением - высокопроизводительный способ получения точных заготовок из цветных сплавов. Тщательностью обработки стенок литьевой формы можно достичь точности размеров до 7 - 8 квалитета, что часто позволяет отказаться от последующей обработки. Стойкость форм для алюминиевых сплавов - до 40000 отливок. Из-за высокой стоимости форм и специального оборудования этот способ рационально применять в крупносерийном и массовом производстве.
Центробежное литье заключается в том, что жидкий металл заливают во вращающуюся форму. Под действием центробежных сил металл уплотняется к внешним стенкам формы. Способ приемлем для получения цилиндрических полых заготовок с небольшой толщиной стенок, что ограничивает его применение.
В электромашиностроении для получения заготовок и деталей широко используются различные виды холодной штамповки /4, 5, 11/. Наиболее распространенные из них:
вырубная листовая штамповка; резка прутка в закрытых штампах; вытяжка; гибка.
Вырубная листовая штамповка обеспечивает отделение заготовки или детали от листового или рулонного сортамента одновременно по всему контуру разделения за один ход рабочего органа инструмента. Этот способ отличается высокой производительностью, малыми затратами. Получаемые изделия мало разнятся между собой по форме и размерам. Чаще всего вырубная штамповка используется для изготовления листов шихтованных магнитопроводов, плоских заготовок, в том числе и из изоляционных материалов. Более подробно эти процессы будут рассмотрены ниже.
Резка прутка в закрытых рубочных штампах обеспечивает более высокую точность концов цилиндрических заготовок, также высокопроизводительна, имеет низкие затраты. В закрытых штампах режущие кромки ножей спрофилированы по контуру сечения разрезаемого прутка, а пруток и получаемая заготовка в процессе рубки зажаты. Распространение получили рубочные штампы, в которых ножи выполнены в виде двух втулок с внутренним диаметром, близким к максимальному диаметру разрезаемого прутка. Пруток подается в рубочные штампы вручную или с помощью автоматических загрузочных устройств.
Формообразование деталей в виде оболочек сферической, конической, цилиндрической или другой подобной формы осуществляется способом вытяжки. Суть этого процесса в том, что заготовка в виде листа вдавливается, например, в цилиндрический зазор между подвижной (пуансон) и неподвижной (матрица) частями вытяжного штампа, в результате чего плоская заготовка
29
путем пластического деформирования приобретает вид стакана. Подобные приемы используются в электромашиностроении для получения заготовок корпусов, щитов, полых роторов электрических машин малой мощности.
Гибка используется для придания плоским заготовкам той или иной объемной формы. В качестве примера рассмотрим получение заготовки станины машины постоянного тока. Для электрических машин малой мощности такую заготовку легко получить порезкой трубчатого сортамента стали. Однако с повышением мощности машин для решения этой задачи приходится использовать листовой сортамент с толщиной, превышающей радиальный размер станины на величину припуска. Порезкой металла вначале получают плоскую заготовку, которую затем сгибают в цилиндр и сваривают в месте стыка. Гибку заготовки осуществляют в специальных гибочных штампах или в гибочных валках. Для крупных машин заготовку станины собирают и сваривают из двух или более согнутых по радиусу сегментов.
Получение сложных заготовок деталей крупных электрических машин сваркой отдельных простых элементов используется в производстве электрических машин большой мощности.
3.2. Изготовление валов
Вал электрической машины является важной механической деталью, несущей основную статическую и динамическую нагрузку. Встречаются различные конструкции валов: гладкие, ступенчатые, составные и др. Гладкие валы отличаются высокой технологичностью, они просты в изготовлении, отличаются малой трудоемкостью. Технологический процесс их изготовления может быть ограничен двумя - тремя основными операциями: заготовительная, термическая, шлифовальная. На всей протяженности такой вал имеет один размер диаметра и один допуск на этот размер. Поэтому для его окончательной обработки можно применить бесцентровую шлифовку /4/ - высокопроизводительный и недорогой процесс. Однако это главное достоинство вала снижает технологичность конструкции ротора, особенно, если с валом сопрягается при сборке несколько разных деталей. Поскольку характер сопряжения этих деталей (магнитопровода, подшипников, вентилятора, коллектора и др.) с валом, как правило, оказывается различным, их сопрягаемые поверхности приходится выполнять в системе вала. Это, как известно, сильно удорожает изделие /2/. Мы столкнулись с конкретным примером, когда повышение технологичности конструкции детали может привести к снижению технологичности изделия, куда эта деталь входит. Кроме того, гладкие валы обладают повышенной металлоемкостью.
Набольшее распространение в электрической машине имеют ступенчатые валы. Это значит, что для сопряжения с каждой деталью, располагаемой на валу, выполняется отдельная ступень, имеющая свой размер и допуск. Такое
30