
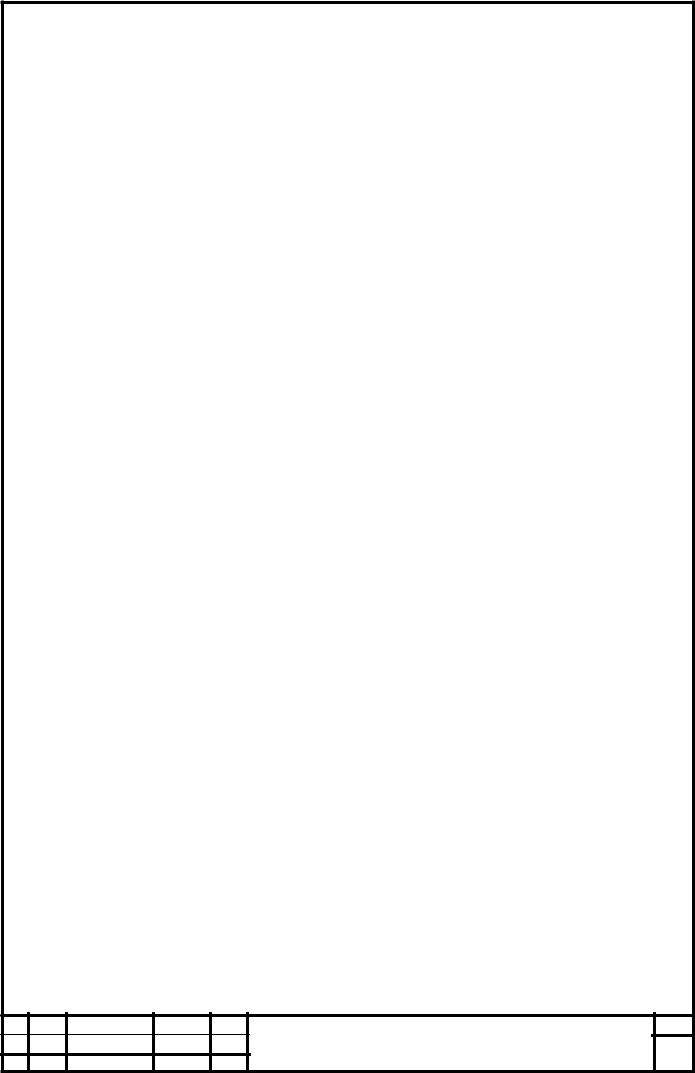
5 ФОРМИРОВАНИЕ ТЕХНОЛОГИЧЕСКОГО ПРОЦЕССА И ЕГО МАРШРУТНОЕ ОПИСАНИЕ
На первой формообразующей операции (010) крепление заготовки (рисунок 3.3,а) при базировании на поверхности специального припуска величиной 7…8 мм. По данной операции (рисунок 3.3,б) обрабатываются верхняя и боковые поверхности, а также другие конструктивны элементы со стороны верхней плоскости. Описание операции – в пункте 5.1.1.
5.1 Описание формообразующих операций.
5.1.1 Операция 010 (первая формообразующая).
Деталь устанавливается в тисках при базировании на поверхности специального припуска (рисунок 3.3,а). Припуск на обработку верхней плоскости по предварительным расчетам лежит в пределах 2…3 мм. Для надежного крепления детали в тисках достаточно обжатия материала порядка 5…6 мм. С учетом необходимости обеспечения свободного прохода фрезы над тисками при выполнении боковых поверхностей на операции 010 назначаем величину специального припуска порядка 7…8 мм.
Таким образом, размер заготовки между торцами детали назначается 36 мм – на 10 мм больше размера готовой детали.
По операции 010 (рисунок 3.3,б) обрабатываются боковые поверхности и верхняя плоскость детали, также выполняются различные конструктивные элементы со стороны верхней плоскости.
Отметим, что сквозные отверстия детали на операции 010 выполняются глухими. Запрограммировано, что они будут «открываться» на последующей операции 015 в момент обработки противоположной плоскости детали в окончательный размер 26. Такой подход несколько увеличивает долговечность сверл.
При формировании верхней плоскости задействовано количество этапов обработки, соответствующее количеству этапов, необходимому для выполнения окончательного размера. Такой подход обеспечивает соответствие качества выполняемой верхней плоскости заданному квалитету окончательного размера. Поскольку окончательный размер 26 h9 по существующим рекомендациям требует трех этапов обработки (черновая, получистовая, чистовая), то и верхняя плоскости выполняется также в три указанных этапа.
Глубину обработки боковой грани детали задаем 27+0.5, при этом превышение размера по высоте детали (26h9) составляет примерно на 1 мм. Это превышение было предусмотрено для гарантированного формирования полного профиля боковой грани по высоте детали.
Лист
10
Изм. Лист |
№ докум |
Подпись Дата |
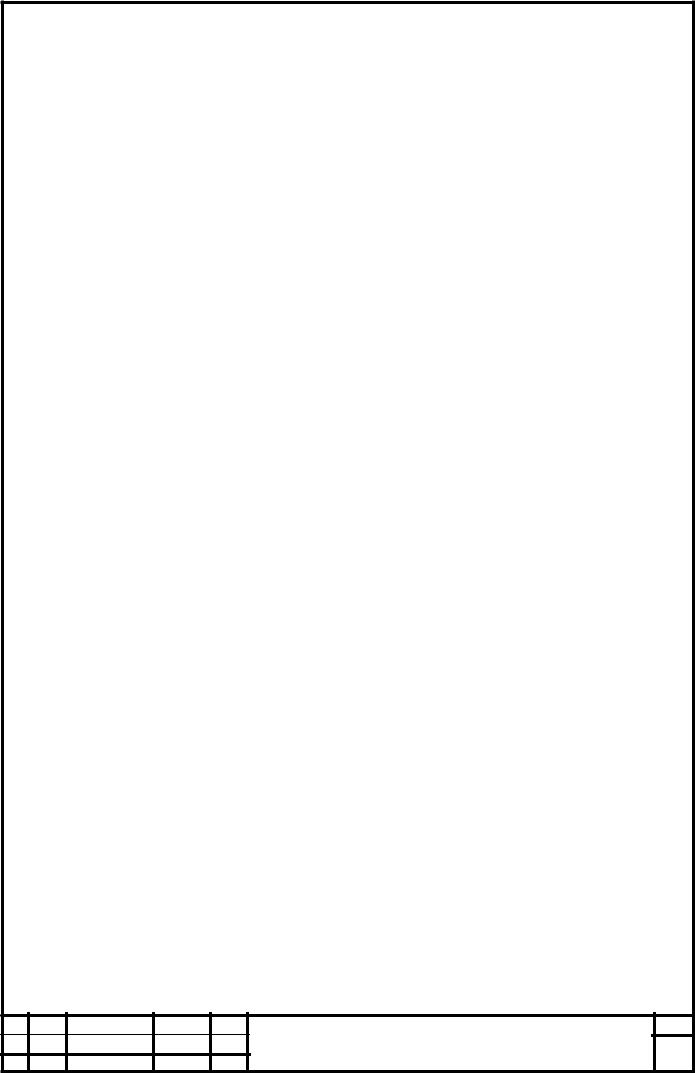
Положение детали относительно тисков на операции 010 задается высотой параллельных планок 5 (рисунок 3.3,б), которая выбирается из соображений обеспечения свободного прохода фрезы над губками тисков при выполнении боковой грани детали.
5.1.2 Операция 015 (вторая формообразующая).
Деталь устанавливается в тисках (рисунок 3.3,в) в перевернутом положении по отношению к прежней позиции на операции 010. Базирование производится на обработанные ранее торцевую и боковую поверхности. При необходимости для обеспечения нужной высоты установки детали могут быть применены параллельные планки 6.
Производится многопроходная обработка плоскости с целью снятия дополнительного специального припуска величиной 7…8 мм, который был задействован для крепления детали на операции 010. В процессе обработки плоскости формируется окончательный размер детали 26 h9 (размер «Д» на рисунке 3.3,в), при этом «открываются» сквозные отверстия. Кроме того, выполняется уступ, расположенный со стороны этой плоскости, а также углубления Ø16 в готовые отверстия Ø10.5.
5.1.3 Операция 020 (третья формообразующая).
Деталь устанавливается в тисках (рисунок 3.3,г) и базируется по длинной боковой грани. В детали фрезеруется паз, а также выполняются отверстия.
5.1.4 Операция 025 (четвертая формообразующая).
Деталь базируется в специальном приспособлении. Фрезеруется паз и выполняются отверстия.
Маршрутное описание изготовления детали представлено в рамках комплекта технологической документации и содержит комплект маршрутных карт и маршрутных эскизов.
5.2 Определение исполнительных размеров
При разработке маршрутного описания технологического процесса требуется проведение специального расчета для одного из исполнительных размеров обработки. Это размер, формируемый на операции 010, обозначенный на маршрутном эскизе «поз. 14» – расстояния от плоскости базирования до верхней обрабатываемой плоскости (фрагмент маршрутного эскиза операции 010 приведена на рисунке 5.1).
Лист
11
Изм. Лист |
№ докум |
Подпись Дата |
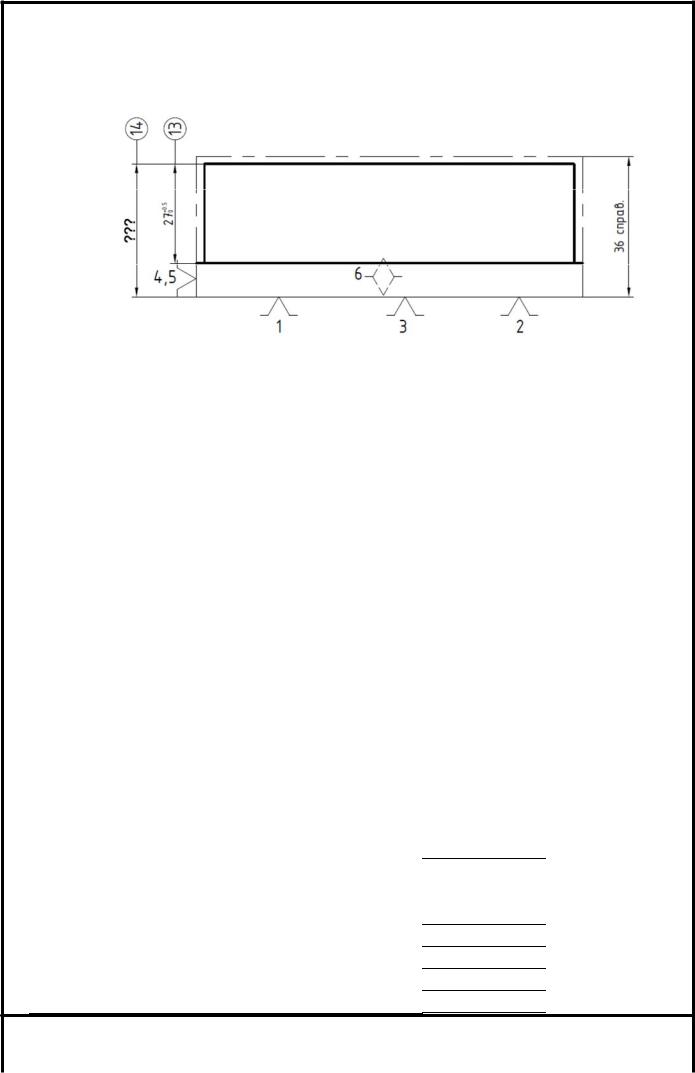
Рисунок 5.1 – Фрагмент маршрутного эскиза операции 010 с указанием на размер, определение величины которого требует проведения расчета
Необходимость расчета обусловлена следующим. Реальный размер заготовки был назначен ранее 36 мм с учетом припуска для крепления детали в тисках. При этом величина припуска на обработку верхней плоскости заранее неизвестна, а именно она определяет величину указанного размера.
Как было показано выше, верхняя плоскость должна быть обработана по технологии, необходимой доля получения размера по квалитету h9, требующей три этапа обработки: чернового, получистового, чистового.
Расчет будем проводить в два этапа.
5.2.1. Предварительный этап расчета размера «поз. 14» на рисунке 3.4.
На данном этапе расчета назначим в качестве исполнительного размера обработки некоторый условный размер, который должен получиться при выполнении верхней плоскости; установим этот размер, допустим, 34h9 (минус 2 мм от габаритного размера заготовки).
Проведем расчет условного размера заготовки с учетом назначенного нами условного исполнительного размера обработки «34h9», обозначенного
|
«поз.14». |
|
|
|
|
|
|
|
|
|
|
|
|
|
|
|
|
|
|
|
|
|
Припуски на |
|
|
|
|
|
|
|
|
Вид |
|
|
Допуски, |
Метод |
|
||||
|
|
|
|
|
Квалитет |
обработку |
|
||||||
|
|
|
обработки |
|
|
мм |
( |
) |
обработки |
|
|||
|
|
|
|
|
|
|
|
|
|
|
|
||
|
Условный |
Заготовка |
|
14 |
0,62 |
|
- |
- |
|
|
|||
|
размер |
|
Черновой |
|
12 |
0,25 |
|
0,9 |
Фрезерование |
|
|||
|
|
34 h9 |
Получист. |
|
11 |
0,16 |
|
0,25 |
Фрезерование |
|
|||
|
|
. |
|
|
|
|
|
|
0,13 |
|
|
||
|
|
|
Чистовой |
|
9 |
0,062 |
|
Фрезерование |
|
||||
|
|
|
|
|
|
|
|
|
|
|
Лист |
||
|
|
|
|
|
|
|
|
|
|
|
|
12 |
|
Изм. |
Лист |
№ докум |
|
Подпись |
Дата |
|
|
|
|
||||
|
|
|
|
|
|
|
|
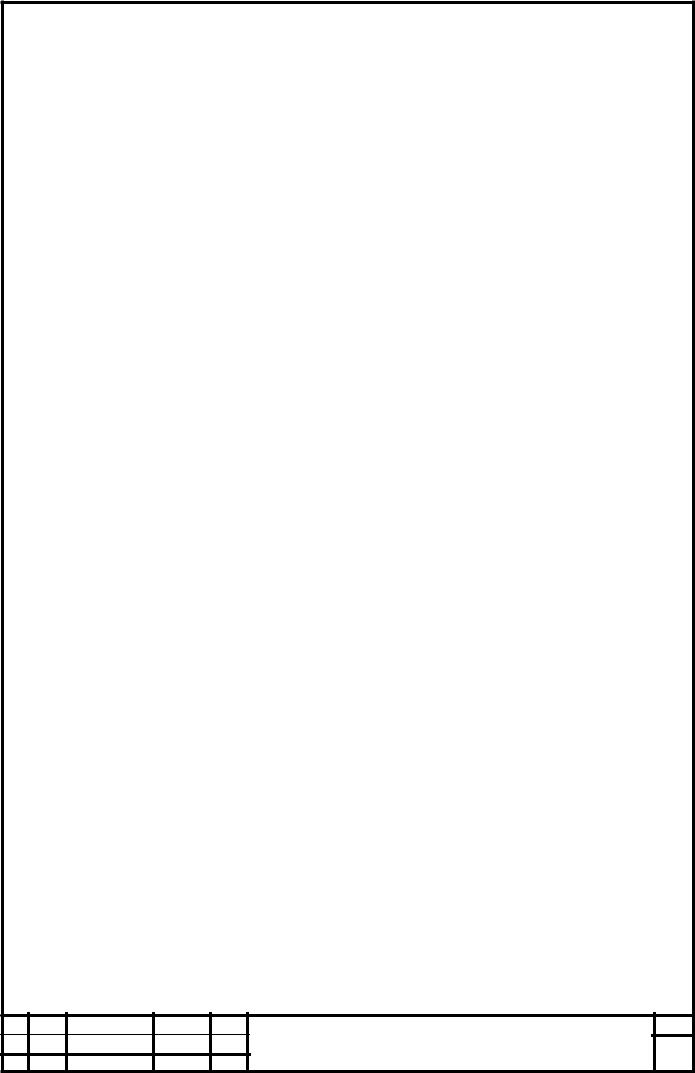
Выполняем расчет по системе формул для односторонней наружной обработки:
Аmax i-1= Аmax i + Zmin i + Ti-1 ,
Аmin i-1= Аmax i + Zmin i.
4. Исполнительные размеры чистовой обработки (окончательные):
34;
33,938.
3. Исполнительные размеры получистовой чистовой обработки (подготовка к чистовой обработке):
34 0,13 0,16 34,29;
34 0,13 34,13.
2. Исполнительные размеры черновой обработки (подготовка к получистовой обработке):
34,29 0,25 0,25 34,79;
34,29 0,25 34,54.
1. Припуски на черновую обработку (от плоскости заготовки):
34,79 0,9 0,62 36,31;
34,79 0,9 35,69.
5.2.2. Корректировка расчета размера «поз. 14» на рисунке 3.4.
Размер заготовки был определен ранее – 36 мм.
Условный размер заготовки « 36,31h14(-0,062) » был рассчитан в пункте 5.2.1. Соответственно, при окончательном определении исполнительных размеров выполнения торцевой поверхности детали все первоначально полученные размеры должны быть сдвинуты по отношению к расчетным величинам на 0,31 мм в сторону уменьшения, так как реальный размер заготовки установлен « 36h14(-0,062) ».
Лист
13
Изм. Лист |
№ докум |
Подпись Дата |
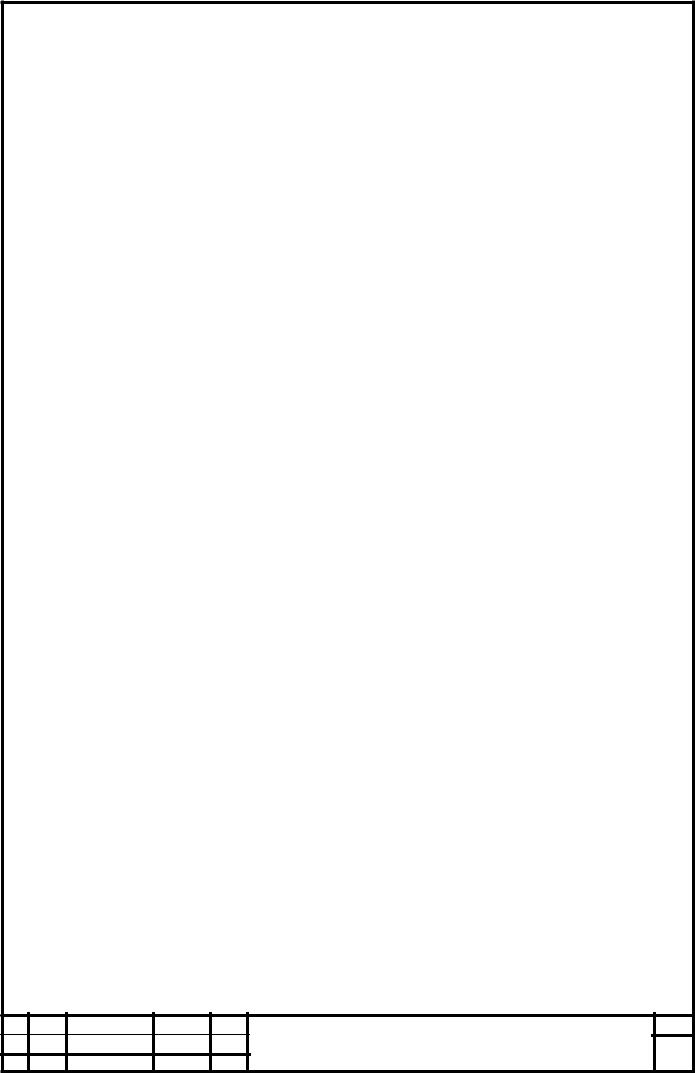
1. Припуски на черновую обработку (от плоскости заготовки).
Расчетные значения: |
36; |
35,38. |
|
Окончательные значения: |
|||
36,31; |
35,69. |
||
2. Исполнительные размеры черновой обработки (подготовка к |
|||
получистовой обработке). |
|
|
|
Расчетные значения: |
34,48; |
34,23. |
|
3. Исполнительные |
|||
Окончательные значения: |
34,79; |
34,54. |
|
|
размеры получистовой чистовой обработки |
||
(подготовка к чистовой обработке). |
|
||
Расчетные значения: |
34,29; |
34,13. |
|
Окончательные значения: |
|||
|
чистовой обработки (окончательные). |
||
4. Исполнительные размеры 33,98; |
33,72. |
||
Расчетные значения: |
33,69; |
33,628. |
|
Окончательные значения: |
|||
34; |
33,938. |
Таким образом, по результатам расчета на маршрутном эскизе операции 010 устанавливаем величину размера «поз. 14» (рисунок 3.4):
« 33, 69h14(-0,062) ».
Еще раз отметим, что расчет других исполнительных размеров для подготовки маршрутного описания не требуется.
Лист
14
Изм. Лист |
№ докум |
Подпись Дата |
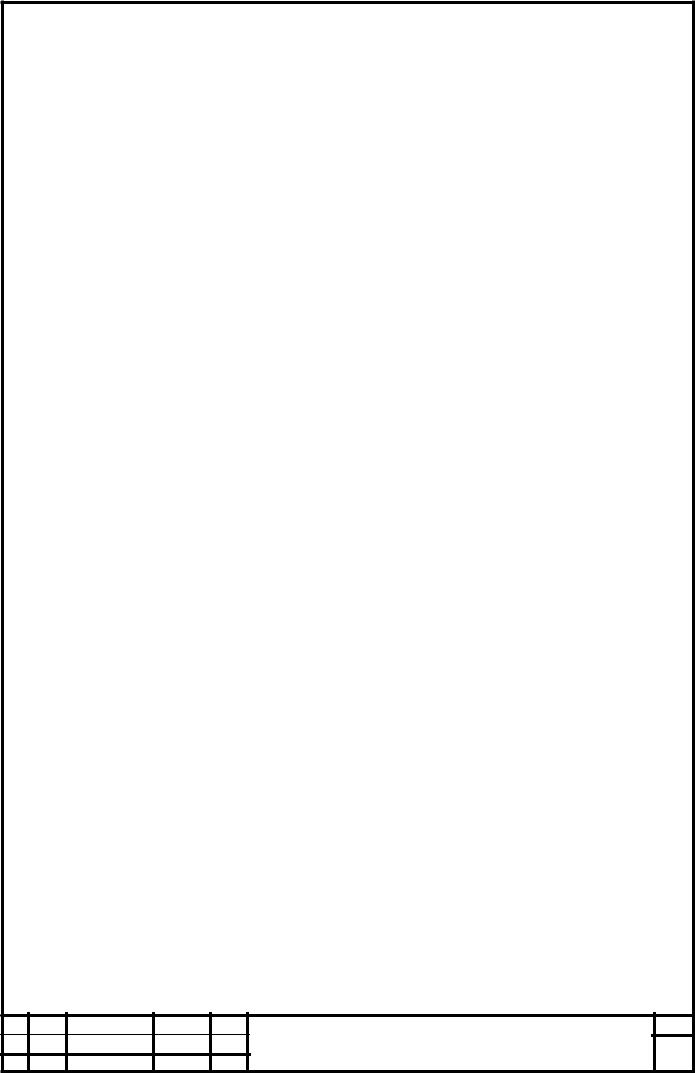
Теоретическая часть. РАЗРАБОТКА ТЕХНОЛОГИЧЕСКОГО ПРОЦЕССА
В процессе разработки технологического процесса формообразующей операции производится:
-Определение общей последовательности выполнения операции;
-Определение исполнительных размеров по этапам обработки;
-Выбор инструментов для обработки детали на различных этапах;
-Определение режимов обработки на каждом выполняемом этапе.
Часть размеров, задействованных в технологическом процессе, определяются заранее, при определении размеров заготовки.
Последовательность обработки поверхностей и определение исполнительных размеров по этапам обработки
Как было показано выше, обработка поверхностей детали производится за несколько этапов. Каждая из поверхностей подвергается черновой обработке. Далее в зависимости от точности выполняемого размера назначается получистовая и чистовая обработка, обработке повышенной точности и т.д.
В практике часто встречаются случаи, при которых контур образован поверхностями, формирующими размеры с разной степенью точности. Число этапов обработки поверхностей, формирующих менее точные размеры, назначается таким же, что и число этапов обработки поверхностей, формирующих наиболее точный размер. При этом расчет промежуточных размеров следует выполнять только для поверхностей, формирующих наиболее точный размер.
Общее правило обработки поверхностей связано с соблюдением последовательности этапов обработки: сначала производится обработка всех поверхностей по черновому этапу, затем по получистовому этапу, затем по чистовому этапу и т.д.
Расчеты исполнительных размеров по этапам обработки выполняется аналогично расчетам, которые применялись ранее при определении размеров заготовки.
Лист
15
Изм. Лист |
№ докум |
Подпись Дата |
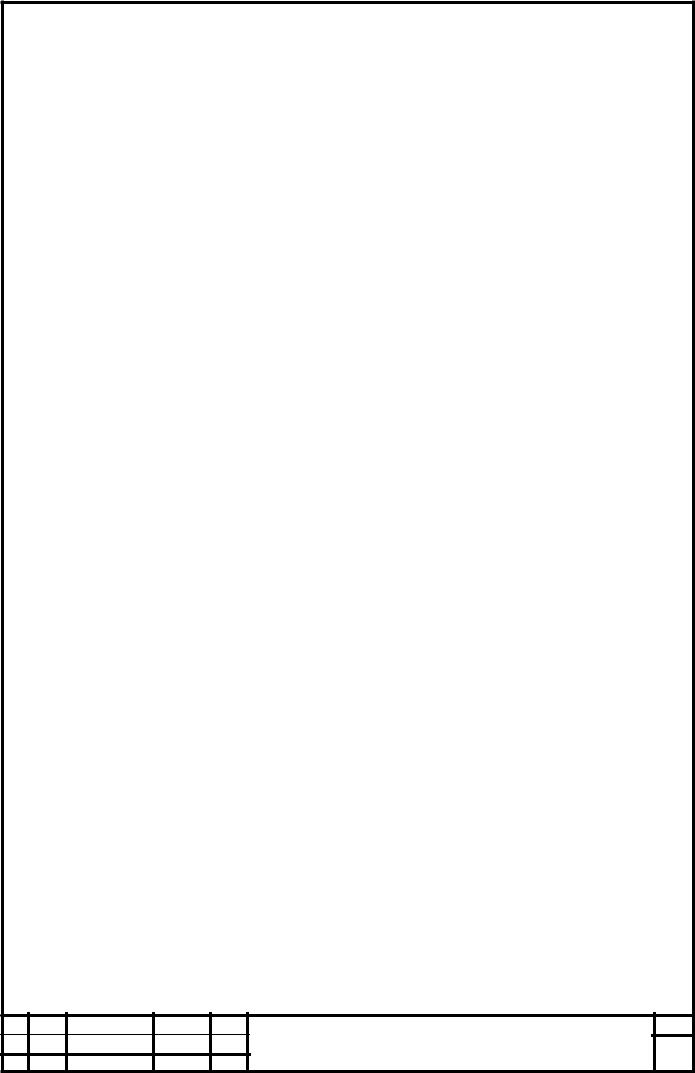
Выбор инструментов для обработки делали на различных этапах
Фрезерная обработка детали на черновом этапе выполняется специальными инструментами, обеспечивающими повышенный съем материала; при котором вопрос обеспечения качества выполняемой поверхности решающего значения не имеет. Последующие этапы, в рамках которых основной задачей является получение требуемого качества поверхностей, выполняются инструментами с другой геометрической конфигурацией.
Во многих случаях получистовая и чистовая обработка может выполняться общим инструментом при его последовательном прохождении по заданной поверхности. В других случаях допускается выполнение
чистового этапа сразу после чернового этапа, минуя получистовой этап.
Определение режимов обработки на каждом выполняемом этапе
Режимы обработки назначаются на базе рекомендаций, представленной в специальной литературе.
Лист
16
Изм. Лист |
№ докум |
Подпись Дата |
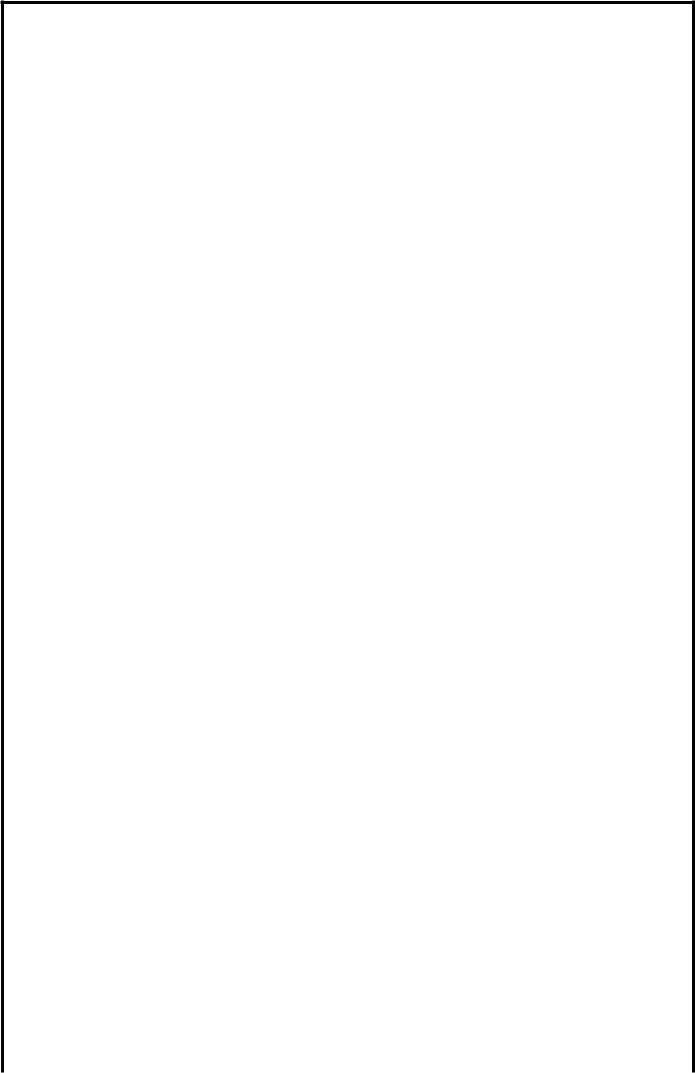
6 ОПЕРАЦИОННОЕ ОПИСАНИЕ ОПЕРАЦИИ 010.
6.1 Определение общей последовательности выполнения операции
На операции 010 выполняются верхняя плоскость в окончательный размер 33, 69-0,062 (расчет исполнительных размеров по этапам обработки был
выполнен ранее), а так круглый карман в окончательные размеры Ø60 H9(+0.074) и 7Js9(+/-0.018); всего три поверхности. Также выполняется группа
мелких отверстий.
Обработка детали на операции 010 выполняется в несколько этапов.
1.Черновая обработка поверхностей.
2.Получистовая обработка поверхностей.
3.Чистовая обработка поверхностей
4.Черновая обработка различных элементов отверстий.
5.Чистовая обработка отверстия Ø12Н7(+0.018) зенкером.
6.Обработка отверстия Ø12Н7(+0.018) повышенной точности разверткой.
6.2Расчет исполнительных размеров по этапам обработки
Размер «100h11».
Определение допусков и припусков на обработку был проведен в процессе расчета размеров заготовки.
Размер «196h12».
Поверхности, формирующие этот размер, входят в общий контур обработки с поверхностями, формирующими более точный размер «100h11». Поэтому число этапов обработки этих поверхностей назначается таким же, как и поверхностей с размером «100h11». Определение допусков на промежуточные размеры и припусков на обработку проводить нецелесообразно.
Размер «8h12».
Поверхности, формирующие этот размер, входят в общий контур обработки с поверхностями, формирующими более точный размер «100h11». Поэтому число этапов обработки этих поверхностей назначается таким же, как и поверхностей с размером «100h11». Определение допусков на промежуточные размеры и припусков на обработку проводить нецелесообразно.
Размер «Ø60 H9».
Определение допусков и припусков на обработку.
|
|
|
|
|
Вид |
|
|
Допуски, |
Припуски на |
Метод |
|
|||
|
|
|
|
|
Квалитет |
обработку |
|
|||||||
|
|
|
|
обработки |
|
|
мм |
( |
) |
обработки |
|
|||
|
|
|
|
|
|
|
|
|
|
|
|
|
||
|
Размер |
|
Черновой |
12 |
0,3 |
|
1.1 |
Фрезерование |
|
|||||
|
Ø60 H9 |
|
Получист. |
11 |
0,19 |
|
0,25 |
Фрезерование |
|
|||||
|
. |
|
|
|
|
|
|
|
|
|||||
|
|
Чистовой |
9 |
0,074 |
|
0,13 |
Фрезерование |
|
||||||
|
|
|
|
|
|
|
|
|
|
|
|
|
|
|
|
|
|
|
|
|
|
|
|
|
|
|
|
Лист |
|
|
|
|
|
|
|
|
|
|
|
|
|
|
17 |
|
Изм. |
Лист |
№ докум |
|
Подпись |
Дата |
|
|
|
|
|||||
|
|
|
|
|
|
|
|
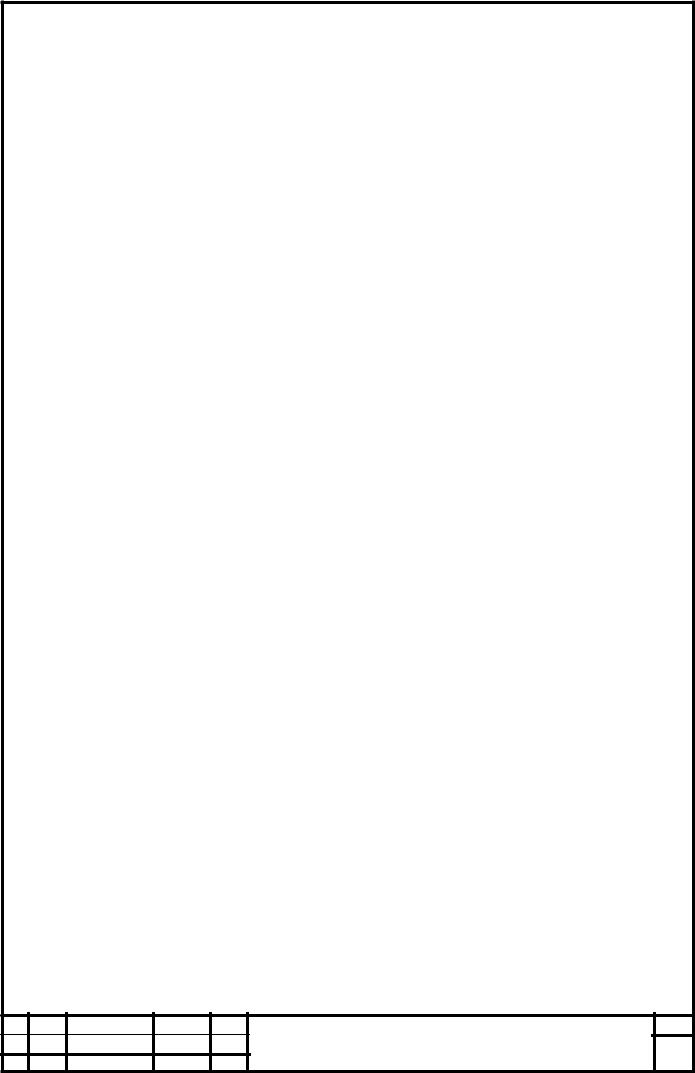
Выполняем расчет по системе формул для двухсторонней внутренней обработки:
Аmax i-1= Аmin i - 2Z min i; Аmin i-1= Аmin i - (2Z min i + Ti-1).
3. Исполнительные размеры чистовой обработки (окончательные):
60,074;
60.
2. Исполнительные размеры получистовой чистовой обработки (подготовка к чистовой обработке):
60 2·0,13 59,74;
60 2·0,13 0,19 59,55.
1. Исполнительные размеры черновой обработки (подготовка к получистовой обработке):
59,55 2·0,25 59,05;
59,55 2·0,25 0,3 58,75.
Размер «7 Js9».
Определение допусков и припуском на обработку.
|
Вид |
|
Допуски, |
Припуски на |
Метод |
|
|
Квалитет |
обработку |
||||
|
обработки |
|
мм |
( |
) |
обработки |
|
|
|
|
|
||
Размер 7 |
Черновой |
12 |
0,15 |
|
0,9 |
Фрезерование |
Js9 |
Получист. |
11 |
0,09 |
|
0,25 |
Фрезерование |
. |
|
|
|
|
|
|
Чистовой |
9 |
0,036 |
|
0,13 |
Фрезерование |
|
. |
|
|
|
|
|
|
Выполняем расчет по системе формул для односторонней внутренней обработки:
,
.
Лист
18
Изм. Лист |
№ докум |
Подпись Дата |
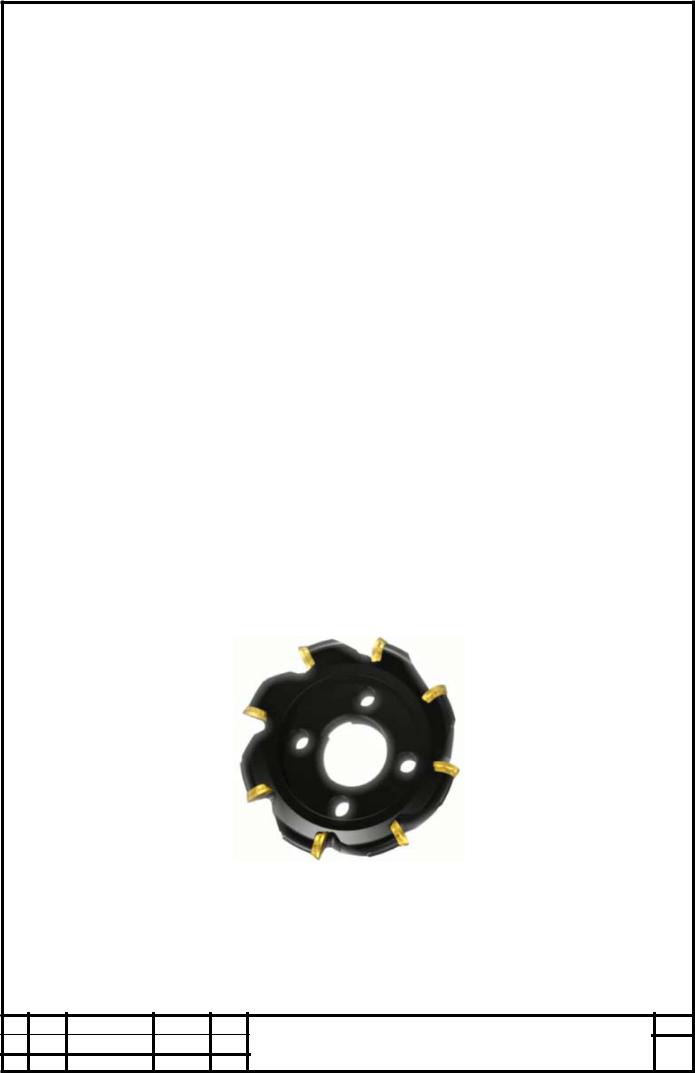
3. Исполнительные размеры чистовой обработки (окончательные):
7,018;
6,982.
2. Исполнительные размеры получистовой чистовой обработки (подготовка к чистовой обработке):
6,982 0,13 6,852;
6,982 0,13 0,09 6,762.
1. Исполнительные размеры черновой обработки (подготовка к получистовой обработке):
6,762 0,25 6,512;
6,762 0,25 0,15 6,362.
6.3 Выбор инструментов для фрезерной обработки
Верхняя плоскость детали выполняется торцевыми фрезерными головками диаметром 100 мм. Диаметр головки должен по возможности превышать ширину обрабатываемой плоскости для обеспечения ее обработки за один проход. Применяются фрезерные головки различного конструктивного исполнения:
- Для всех этапов обработки выбираем фрезерные головки с числом режущих пластин 8 (рисунок 7.1).
Рисунок 7.1 – Торцевая фрезерная головка
Прочие поверхности детали выполняются монолитными концевыми твердосплавными фрезами, диаметр которых выбирается, исходя из соображений обеспечения эффективной работы и геометрической возможности выполнения контура:
Лист
19
Изм. Лист |
№ докум |
Подпись Дата |