
599
.pdf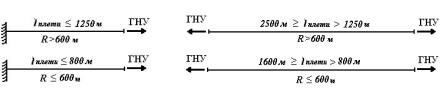
При этом, как уже отмечалось ранее, от начала плети до середины раскрепленной части плети
|
L − l |
|
|
x = |
анк |
|
создаваемые продольные силы будут превышать расчетные, а от середины и до |
|
|||
|
2 |
|
|
конца раскрепленной части плети создаваемые продольные силы будут меньше расчетных. На рис. 5.24 выше графиков перемещений приведены отклонения созданных продольных сил от расчетных. Для оценки отклонений перемещений сечений от расчетных представляется возможным приведенную выше зависимость.
В соответствии с законом Гука:
∂u = |
Nx |
, откуда |
∂u = |
Nx∂x |
. |
(5.32) |
|
|
|||||
∂x |
EF |
|
EF |
|
Проинтегрировав выражение (5.32) от х до (L − lанк ) , получим формулу для определения отклонений перемещений сечений плети от расчетных:
|
|
= |
r x2 |
− |
r (L − l |
)x |
|
||
U |
|
0 |
0 |
анк |
|
. |
(5.33) |
||
x |
2EF |
|
2EF |
|
|||||
|
|
|
|
|
|
|
|||
|
|
|
|
|
|
|
|
Анализ выражения (5.33) показывает, что максимальное отклонение перемещений от расчетных будет в средней части раскрепленного участка плети (L − lанк ) :
|
|
= |
r (L − l |
)2 |
|
|
U |
|
0 |
анк |
|
(5.34) |
|
max |
|
8EF |
|
|||
|
|
|
|
|
||
|
|
|
|
|
|
В табл. 5.5 приведен пример расчета фактических отклонений перемещений сечений от
расчетных при растяжении плети усилием |
N |
|
= N |
|
+ |
r0 (L − lанк ) |
для рельсовой плети длиной 800 |
ГНУ |
p |
|
|||||
|
|
|
2 |
|
|||
|
|
|
|
|
|
м, длиной анкерного участка 50 м (рельсы типа Р65). Рассматривается погонное сопротивление перемещению свободно лежащей плети (r0 = 0,5 кН/м) и погонное сопротивление перемещению плети, вывешенной на ролики или антифрикционные прокладки (r0 = 0,15 кН/м).
Из |
данных |
табл. 5.5 |
|
|
|
|
|
|
|
Таблица 5.5 |
||||
следует, |
что |
без вывески |
|
|
|
|
|
|
|
|
|
|
|
|
|
|
|
|
Расстояние от начала плети до сечения x, м |
|
|
||||||||
рельсовой плети на роликовые |
|
|
|
|
|
|
||||||||
|
|
|
|
|
|
|
|
|
|
|
||||
|
|
|
0 |
100 |
200 |
375 |
500 |
600 |
750 |
|
||||
|
|
|
|
|
|
|
|
|||||||
опоры или антифрикционные |
|
r0 |
= 0,5 кН/м |
0 |
–9 |
–16 |
–20 |
–18 |
–13 |
0 |
|
|||
прокладки |
|
отклонения |
|
|
||||||||||
|
Ux, мм |
|
|
|
|
|
|
|
|
|
|
|||
|
r0 |
= 0,15 кН/м |
0 |
–3 |
–5 |
–6 |
–5 |
–4 |
0 |
|
||||
|
|
|
|
|
|
|||||||||
перемещений |
от |
расчетных |
|
|
|
|
|
|
|
|
|
|
|
весьма существенны. Максимальное отклонение — для х = 375 м (середина раскрепленной части плети).
На основании подобных расчетов в ТУ–2001 приведены требования к порядку нагружения рельсовых плетей продольной нагрузкой в зависимости от их длины. При этом учтено влияние кривизны пути на возрастание погонного сопротивления продольному перемещению рельсовых плетей.
При работе с натяжными устройствами при длинах плетей до 1250 м и радиусе более 600 м производится растяжение сразу всей плети в одну сторону (рис. 5.25). При радиусе менее 600 м подобная схема нагружения может быть реализована при длине плети до 800 м.
При больших длинах плетей принудительный ввод их в расчетный режим эксплуатации производится полуплетями (см. рис. 5.26).
Рис. 5.25. Растяжение |
Рис. 5.26. Растяжение полуплетей в две стороны |
|
плетей в одну сторону |
||
|
Пример определения расчетных параметров ввода рельсовых плетей в расчетный режим с
применением ГНУ. |
|
|
|
Рельсовая плеть длиной L = 800 м (рельсы Р65) |
укладывается |
при |
температуре tз = 0 °С. |
Расчетная (оптимальная) температура закрепления |
tp = tопт = +30 |
°С. |
Величина погонного |
сопротивления продольному перемещению плети, закрепленной на шпалах, r принята равной 12 кН/м (для незамерзшего и уплотненного балласта). Величину стыкового сопротивления принимаем равной — 400 кН. Величину погонного сопротивления продольному перемещению плети, вывешенной на ролики, принимаем равной r0 = 0,15 кН/м .
Величину расчетной растягивающей продольной силы, соответствующей температурному
эквиваленту, равному t = 30 °С можно определить по формуле Np = αEF ti = αEF(tp − ti ) , а
также можно использовать полученную ранее зависимость — эквивалент одного градуса равен 20,5 кН. Тогда: Np = = 30× 20,5 = 615 кН.
Длина анкерного участка со стороны подвижного конца плети: lанк′ = Np / r = 615/12 = 51м ,
а со стороны неподвижного конца плети:
lанк = (Np − R)/ r = (615− 400)/12 ≈15 м .
Для упрощения нанесения контрольных сечений на плети и проведения расчетов примем длину анкерного участка lанк = 50 м.
Величину растягивающей продольной силы, обеспечивающей создание в плети продольных сил, в среднем равных расчетным (с учетом погонного сопротивления), определяем по
зависимости (5.22): |
|
|
|
|||||
N |
|
= N |
|
+ |
r0 (L − lанк ) |
= 615+ |
0,15(800 − 50) |
≈ 671 кН . |
ГНУ |
p |
|
|
|||||
|
|
2 |
2 |
|
||||
|
|
|
|
|
Величину необходимых перемещений контрольных сечений без учета погонного сопротивления можно определить по формуле
ux = αai (tp − ti ) ,
где ai — расстояние от неподвижного конца плети до контролируемого сечения, или использовать ранее полученную зависимость — участок плети длиной 50 м при изменении температуры на один градус изменяет свою длину на 0,6 мм. Соответственно, при изменении температуры на 30 °С — на 18 мм.
Отклонение перемещений сечений плети от расчетных определяем по зависимости (5.33):
|
|
= |
r x2 |
− |
r (L − l |
)x |
|
|||
U |
|
0 |
0 |
анк |
. |
|
||||
x |
|
|
|
|
|
|||||
|
|
2EF |
|
|
2EF |
|
|
|
|
|
|
|
|
|
|
|
|
|
|
||
Расчетные перемещения сечений плети определяются выражением |
||||||||||
|
|
|
ux = up + ux . |
|
|
|
(5.35) |
|||
Величину относительных перемещений соседних сечений определяем по зависимости |
||||||||||
uр, i−(i+1) = up, i − up, i+1 . |
|
|||||||||
Разность перемещений |
соседних |
|
сечений |
uр, i−(i+1) в соответствии с известной |
||||||
зависимостью: |
|
|
|
|
|
|
|
|
|
|
N = EFξ = EF |
p,i−(i+1) |
, |
(5.36) |
|||||||
|
||||||||||
|
|
|
|
|
|
l |
|
|
|
|
определяет величину созданных продольных сил. Здесь EF — продольная жесткость рельса; ξ — относительная деформация участка l = 50 м. Разности перемещений соседних сечений uр, i−(i+1) соответствует также температурный эквивалент продольных сил, определяемый из зависимости uα = αl t , где t = tp − ti .
При α =11,8×10-6 1 |
/ °C и учете размерности Δλα |
в мм и l в м, получим приведенную в |
|||||
ТУ–2001 формулу: |
|
|
|
|
|
||
|
|
|
|
|
up,i−(i+1) |
|
|
|
|
|
t ≈ 85 |
|
. |
. |
|
|
|
|
|
|
|
||
|
|
|
|
|
l |
|
|
Расчет сводим в табл. 5.6. |
|
|
|
||||
Среднее |
значение |
созданной в плети продольной растягивающей силы равно |
|||||
Np, ср. = 624 |
кН , |
а среднее значение соответствующего температурного эквивалента — |
|||||
tр, ср. = 31°С. |
Несовпадение |
среднего значения |
созданной продольной силы от |
расчетного его значения (615 кН) и среднего температурного эквивалента от расчетной температуры закрепления (30 °С) объясняется погрешностью при вычислениях.
В табл. 5.6 приведен расчет необходимых перемещений сечений плети и определение расчетного напряженного состояния. Для контроля создания расчетного напряженного состояния при производстве работ необходимо подобный расчет производить для фактических перемещений сечений плети в форме табл. 5.7, аналогичной табл. 5.6.
|
|
|
|
|
|
|
|
|
|
|
|
|
|
|
|
|
|
|
|
|
|
|
|
|
|
|
|
|
|
Таблица 5.6 |
|||
|
|
|
|
|
|
|
|
|
|
|
|
|
|
|
|
|
|
|
|
|
|
|
|
|
|
|
|
|
|
|
|
|
|
№ |
a |
, |
u , |
|
u |
, |
|
u |
, |
u |
|
|
|
|
N |
, |
|
|
t |
, |
|
t |
|
, |
|
|
|
|
|
|
|
|
|
|
|
|
|
, |
|
|
|
|
|
р |
|
|
|
|
|
|
|
|
|
||||||||||||||
|
|
х |
|
|
рi |
р |
i−(i |
|
|
|
|
|
р |
|
|
|
|
|
|
|
|
|
|
|
|
||||||||
сече- |
i |
|
x |
|
|
|
|
|
+1) |
|
|
p |
|
|
|
|
|
|
|
|
|
|
|
|
|
|
|
|
|
|
|||
м |
мм |
|
мм |
|
|
|
|
|
|
|
|
кН |
|
|
°C |
|
°С |
|
|
|
|
|
|
|
|
|
|
||||||
ния |
|
|
мм |
мм |
|
|
|
|
|
|
|
|
|
|
|
|
|
|
|
|
|||||||||||||
|
|
|
|
|
|
|
|
|
|
|
|
|
|
|
|
|
|
|
|
|
|
|
|||||||||||
|
|
|
|
|
|
|
|
|
|
|
|
|
|
|
|
|
|
|
|
|
|
|
|
|
|
|
|
|
|
|
|
||
1 |
0 |
270 |
|
0 |
|
|
270,0 |
19,5 |
|
|
670 |
|
|
33 |
|
3 |
|
|
|
|
|
|
|
|
|
|
|
||||||
|
|
|
|
|
|
|
|
|
|
|
|
|
|
|
|
|
|
|
|
|
|
|
|
|
|
||||||||
2 |
50 |
252 |
|
–1,5 |
|
250,5 |
|
|
|
|
|
|
|
|
|
|
|
|
|
|
|
|
|||||||||||
|
|
19,0 |
|
|
660 |
|
|
32 |
|
2 |
|
|
|
|
|
|
|
|
|
|
|
||||||||||||
|
|
|
|
|
|
|
|
|
|
|
|
|
|
|
|
|
|
|
|
|
|
|
|
|
|
||||||||
3 |
100 |
234 |
|
–2,5 |
|
231,5 |
19,5 |
|
|
670 |
|
|
33 |
|
3 |
|
|
|
|
|
|
|
|
|
|
|
|||||||
|
|
|
|
|
|
|
|
|
|
|
|
|
|
|
|
|
|
|
|
|
|
|
|
|
|
||||||||
4 |
150 |
216 |
|
–4,0 |
|
212,0 |
19,0 |
|
|
660 |
|
|
32 |
|
2 |
|
|
|
|
|
|
|
|
|
|
|
|||||||
|
|
|
|
|
|
|
|
|
|
|
|
|
|
|
|
|
|
|
|
|
|
|
|
|
|
||||||||
5 |
200 |
198 |
|
–5,0 |
|
193,0 |
18,5 |
|
|
643 |
|
|
31 |
|
1 |
|
|
|
|
|
|
|
|
|
|
|
|||||||
6 |
250 |
180 |
|
–5,5 |
|
174,5 |
18,5 |
|
|
643 |
|
|
31 |
|
1 |
|
|
|
|
|
|
|
|
|
|
|
|||||||
7 |
300 |
162 |
|
–6,0 |
|
156,0 |
18,0 |
|
|
625 |
|
|
31 |
|
1 |
|
|
|
|
|
|
|
|
|
|
|
|||||||
8 |
350 |
144 |
|
–6,0 |
|
138,0 |
18,0 |
|
|
625 |
|
|
31 |
|
1 |
|
|
|
|
|
|
|
|
|
|
|
|||||||
|
|
|
|
|
|
|
18,0 |
|
|
625 |
|
|
31 |
|
1 |
|
|
|
|
|
|
|
|
|
|
|
|||||||
9 |
400 |
126 |
|
–6,0 |
|
120,0 |
|
|
|
|
|
|
|
|
|
|
|
|
|
|
|
|
|||||||||||
|
|
|
|
|
|
|
|
|
|
17,5 |
|
|
608 |
|
|
30 |
|
0 |
|
|
|
|
|
|
|
|
|
|
|
||||
10 |
450 |
108 |
|
–6,0 |
|
102,0 |
|
|
|
|
|
|
|
|
|
|
|
|
|
|
|
|
|||||||||||
|
|
|
|
|
|
|
|
|
|
|
|
|
|
|
|
|
|
|
|
|
|
|
|
|
|
||||||||
|
|
|
|
|
|
|
|
|
|
17,5 |
|
|
608 |
|
|
30 |
|
0 |
|
|
|
|
|
|
|
|
|
|
|
||||
11 |
500 |
90 |
|
–5,5 |
|
84,5 |
|
|
|
|
|
|
|
|
|
|
|
|
|
|
|
|
|||||||||||
|
|
|
|
|
|
|
591 |
|
|
|
|
|
|
|
|
|
|
|
|
|
|
|
|
|
|||||||||
|
|
|
|
|
|
|
|
|
|
17,0 |
|
|
|
|
29 |
|
–1 |
|
|
|
|
|
|
|
|
|
|
|
|||||
12 |
550 |
72 |
|
–5,0 |
|
67,0 |
|
|
|
|
|
|
|
|
|
|
|
|
|
|
|
|
|||||||||||
|
|
17,0 |
|
|
591 |
|
|
29 |
|
–1 |
|
|
|
|
|
|
|
|
|
|
|
||||||||||||
|
|
|
|
|
|
|
|
|
|
|
|
|
|
|
|
|
|
|
|
|
|
|
|
|
|
||||||||
13 |
600 |
54 |
|
–4,0 |
|
50,0 |
|
|
|
|
|
|
|
|
|
|
|
|
|
|
|
|
|||||||||||
|
|
16,5 |
|
|
573 |
|
|
28 |
|
–2 |
|
|
|
|
|
|
|
|
|
|
|
||||||||||||
|
|
|
|
|
|
|
|
|
|
|
|
|
|
|
|
|
|
|
|
|
|
|
|
|
|
||||||||
14 |
650 |
36 |
|
–3,0 |
|
33,0 |
|
|
|
|
|
|
|
|
|
|
|
|
|
|
|
|
|||||||||||
|
|
16,5 |
|
|
573 |
|
|
28 |
|
–2 |
|
|
|
|
|
|
|
|
|
|
|
||||||||||||
15 |
700 |
18 |
|
–1,5 |
|
16,5 |
|
|
|
|
|
|
|
|
|
|
|
|
|
|
|
|
|||||||||||
|
|
|
|
|
|
|
|
|
|
|
|
|
|
|
|
|
|
|
|
|
|
|
|
|
|
||||||||
16 |
750 |
0 |
|
0 |
|
0 |
|
|
|
|
|
|
|
|
|
|
|
|
|
|
|
|
|
|
|
|
|
|
|
|
|||
|
|
|
|
|
|
|
|
|
|
|
|
|
|
|
|
|
|
|
|
|
|
u |
|
|
|
||||||||
П р и м е ч а н и я. |
1. Значения |
ux |
определены |
|
с |
погрешностью — |
1 |
|
мм; значения |
u |
, |
u |
, |
|
— |
с |
|||||||||||||||||
|
|
|
|
|
|
|
|
|
|
|
|
|
|
|
|
|
|
|
|
|
|
|
|
|
|
|
х |
|
рi |
рi−(i+1), |
|
|
|
погрешностью 0,5 мм; Np — с погрешностью 1 кН; |
t |
, |
t |
р |
— с погрешностью 1 °С. |
|
|
|
|
|
|
|
|
||||||||||||||||||||
|
|
|
|
|
|
|
|
|
|
|
|
|
р |
|
|
|
|
|
|
|
|
|
|
|
|
|
|
|
|
|
|
||
2. Np — значение |
созданной |
продольной |
растягивающей |
силы, |
определяемой по |
формуле |
5.36; |
t |
р |
— |
|||||||||||||||||||||||
|
|
|
|
|
|
|
|
|
|
|
|
|
|
|
|
|
|
|
|
|
|
|
|
|
|
|
|
|
|
|
|
|
|
температурный эквивалент созданной продольной силы; |
|
t |
|
— отклонение температурного эквивалента созданной |
|||||||||||||||||||||||||||||
|
|
|
|
|
|
|
|
|
|
|
|
|
|
|
|
|
|
р |
|
|
|
|
|
|
|
|
|
|
|
|
|
|
|
продольной силы от расчетной температуры, равной 30 °C. |
|
|
|
|
|
|
|
|
|
|
|
|
|
|
|
|
|
|
|||||||||||||||
|
|
|
|
|
|
|
|
|
|
|
|
|
|
|
|
|
|
|
|
|
|
|
|
|
|
|
|
|
|
Таблица 5.7 |
|||
|
|
|
|
|
|
|
|
|
|
|
|
|
|
|
|
|
|
|
|
|
|
|
|
|
|
|
|
|
|
|
|
|
|
№ |
a |
, |
u , |
|
u |
, |
|
u |
, |
u |
|
|
|
|
N , |
|
|
t |
, |
|
t |
|
, |
|
|
|
|
|
|
|
|
|
|
|
|
|
|
|
|
|
|
|
|
|
|
|
|
|
|
|
|
|
|
||||||||||||||
сече- |
i |
|
x |
|
|
ф |
|
|
фi |
фi−(i+1), |
|
|
ф |
|
|
|
ф |
|
ф |
|
|
|
|
|
|
|
|
|
|
||||
м |
мм |
|
мм |
|
|
|
|
|
|
|
|
кН |
|
|
°C |
|
°С |
|
|
|
|
|
|
|
|
|
|
||||||
ния |
|
|
мм |
мм |
|
|
|
|
|
|
|
|
|
|
|
|
|
|
|
||||||||||||||
|
|
|
|
|
|
|
|
|
|
|
|
|
|
|
|
|
|
|
|
|
|
||||||||||||
|
|
|
|
|
|
|
|
|
|
|
|
|
|
|
|
|
|
|
|
|
|
|
|
|
|
|
|
|
|
|
|
|
|
Как уже указывалось, создание продольных растягивающих сил, соответствующей расчетной температуре закрепления плети, осуществляется за счет перемещений сечений плети относительно начала анкерного участка (сечения x = L − lанк ). Но это сечение в
процессе нагружения плети также перемещается. Поэтому фактические перемещения расчетных сечений uфi необходимо уменьшить на величину смещения сечения x = L − lанк .
Для определения отклонений перемещений сечений плети от расчетных (по формуле 5.33) необходимо знать фактическое значение погонного сопротивления продольному перемещению плети. Для получения его значения целесообразно нагрузить полностью раскрепленную и вывешенную на антифрикционные элементы рельсовую плеть продольной силой до начала перемещения всей плети. Тогда величина погонного сопротивления определится из очевидного выражения:
r0 = Nr0 / L ,
где Nr0 — продольная сила, необходимая для смещения рельсовой плети.
Раздел 6. ВОССТАНОВЛЕНИЕ РАСЧЕТНОГО НАПРЯЖЕННОГО СОСТОЯНИЯ РЕЛЬСОВЫХ ПЛЕТЕЙ
6.1. Восстановление целостности рельсовых плетей
Восстановление целостности рельсовых плетей
Технология восстановления рельсовых плетей должна обеспечить:
—восстановление целостности рельсовых плетей;
—восстановление расчетных напряжений в зоне сварки и на прилегающих участках.
Иначе говоря, после выполнения работ рельсовые плети должны иметь состояние, близкое к
состоянию, имевшемуся до излома или появления опасного дефекта.
Начальный этап восстановления
При обнаружении в рельсовой плети излома или опасного дефекта первоочередной задачей является обеспечение безопасного пропуска поездов и определение этапности восстановления.
Восстановление целостности плетей производится в два или три этапа:
—краткосрочное;
—временное;
—окончательное.
Для определения условий пропуска подвижного состава и этапности восстановления при обнаружении опасного дефекта необходимо с помощью съемного ультразвукового дефектоскопа определить границы распространения внутренней трещины относительно рабочей грани головки рельса, а также уточнить место расположения дефекта по длине рельса. Для работы дефектоскопа очищают поверхность катания и смачивают ее в зоне поиска дефекта водой, а при отрицательной температуре — водным раствором спирта. Искатель многократно перемещают по поверхности катания вдоль рельса на длине около 20 см с каждой стороны дефекта, направляя пучок ультразвуковых колебаний вдоль продольной оси рельса. Первый проход искателя начинают от внутренней грани головки, последующие — с шагом сканирования 2–3 мм до установления границы распространения трещины в поперечном направлении головки.
Краткосрочное восстановление
Краткосрочное восстановление заключается в установки в месте повреждения накладок, сжатыми струбцинами (рис. 6.1). Разрешается пропуск поездов в течение 3-х часов со скоростью 25 км/ч. Этот стык должен находиться под наблюдением.
Краткосрочное восстановление применяется:
—при внутренней поперечной трещине (дефекты 21.2 и 69), если ее границы выходят за середину головки рельса (за вертикальную ось симметрии) или она вышла на поверхность рельса;
—при сквозном поперечном изломе и образовавшемся зазоре менее 40 мм.
По дефектному месту в течение трех часов представляется возможным пропускать поезда со скоростью до 25 км/ч. При этом за стыком должно обеспечиваться непрерывное наблюдение. В течение трех часов должно быть организовано временное или окончательное восстановление рельсовой плети.
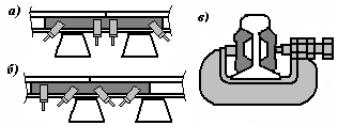
Рис. 6.1. Схемы расположения струбцин при изломе рельса: a — между шпалами; б — над шпалой;
в — струбцина для стягивания накладок
Если внутренняя трещина, вызванная дефектом 21.2, не выходит на поверхность, а ее границы за середину головки, допускается установка на поврежденное место шестидырных накладок с четырьмя болтами. Накладки устанавливаются так, чтобы их середина совмещалась с дефектом. Во избежание развития дефекта отверстия для двух средних болтов не сверлятся. После постановки накладок поезда пропускаются с установленной скоростью. Для повышения усилия затяжки стыковых болтов стыка рекомендуется использовать высокопрочные болты.
Для предотвращения растяжения зазора и среза болтов в случае сквозного излома рельса под накладками необходимо произвести усиленное закрепление клеммных и закладных болтов на протяжении 50 м в каждую сторону от дефектного места. Место с дефектом, взятым в накладки, необходимо осматривать при всех проверках пути. В случае выхода трещины на поверхность рельса или распространении трещины за середину головки рельсовая плеть должна быть временно или окончательно восстановлена.
Временное восстановление
Временное восстановление производится после краткосрочного, а также в случае развития дефекта, взятого в накладки.
Если трещина или излом произошли по дефектам 24, 25, 26.3, ЗОВ.2, 50.2, 52.2, 55, 56.3, 60.2, а также если были обнаружены два и более дефекта 21.1 между двумя сварными стыками, запрещается осуществлять краткосрочное восстановление. Запрещается также производить краткосрочное восстановление, если при сквозном изломе образовался зазор более 40 мм. В этих случаях необходимо сразу производить временное или окончательное восстановление рельсовой плети.
При временном восстановлении из рельсовой плети вырезается часть рельса с дефектом и укладывается рельс длиной 8–11 м, соединяемый с образовавшимися концами рельсовой плети шестидырными накладками. Расстояние от края дефекта или от конца трещины до ближайшего пропила, а также до ближайшего сварного стыка должно быть не менее 3 м. Сведения о местах временного восстановления заносятся в журнал или паспорт-карту и хранятся до окончательного восстановления плети.
При выполнении работ по временному восстановлению рельсовых плетей в перерывах между поездами необходимо руководствоваться следующими технологическими указаниями.
—Для пропуска поезда снимают рельсорезный станок, на место пропила ставят накладки, прикрепляемые со стороны вырезаемого рельса струбцинами, а со стороны плети — болтом, для которого заранее просверливают отверстие в шейке рельса.
—Расстояние между двумя пропилами должно равняться длине вставляемого рельса плюс два зазора. Положение второго пропила на плети намечается только после полного температурного перемещения ее концов в месте первого пропила.
—При температуре рельсовой плети, превышающей температуру ее закрепления, временное восстановление производят на закрытом для движения перегоне. В этом случае сначала вырезается газовым резаком кусок рельса длиной 10–20 см в месте дефекта, а затем рельсорезным станком обрезаются концы плетей в расчетных сечениях. Чтобы исключить заклинивание вырезаемого куска рельса при удлинении концов плетей, а также для обеспечения безопасности работающих, его необходимо вырезать постепенно (рис. 6.2).
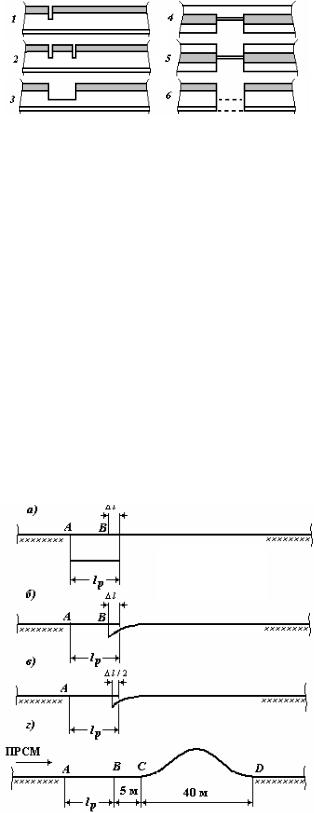
Вначале прорезают всю головку и шейку до половины высоты по концам вырезаемого куска. Далее горизонтальным резом удаляют часть рельса, находящегося между двумя вертикальными прорезями. Затем на той же длине вырезают две части подошвы по обе стороны шейки. В завершение постепенно выжигают оставшуюся часть шейки.
Рис. 6.2. Последовательность вырезки автогеном куска рельса: 1–3 — расположение резов при виде сбоку;
4–5 — расположение резов в плане; 6 — выжигаемая оставшаяся часть шейки рельса
(обозначена пунктирной линией)
Постановка накладок на дефектное место и временное восстановление плети выполняется под руководством дорожного мастера, а окончательное восстановление сваркой — под руководством старшего дорожного мастера при работе на перегоне или дорожного мастера — при работе на станциях.
Окончательное восстановление рельсовых плетей
Окончательное восстановление рельсовых плетей заключается в вырезке части плети с дефектом, взятым в накладки, или в удалении рельса, уложенного при временном восстановлении с обрезкой прилегающих концов плетей, и последующим вваркой рельсовой рубку длиной не менее 8 м, одинаковой по износу и качеству металла с рельсовой плетью. Вваривают рельсовую рубку электроконтактным способом при помощи передвижной сварочной машины. При окончательном восстановлении рельсовой плети с дефектом, взятым в накладки, дефектную часть плети вырезают до «окна» так же, как при временном восстановлении.
При окончательном восстановлении плети после ее временного восстановления, обрезку одного конца плети (сечение А на рис. 6.3, а) целесообразно выполнить в период подготовительных работ до «окна».
Рис. 6.3. Окончательное восстановление рельсовой плети
Обрезку второго конца плети (сечение В на рис. 6.3, а) выполняют в «окно» на расстоянии от первого пропила, равным lр – l, где l — запас на усадку и оплавление металла при сварке двух стыков.
Данный запас устанавливают при сварке контрольных образцов во время подготовки машины ПРСМ к работе на перегоне (запас на усадку и оплавление металла на один стык ≈ 40–50 мм).
После удаления вырезанной части плети вместе с временным рельсом в плеть вваривают рельсовую рубку. Первый стык рельса с плетью сваривают с подтягиванием рельса (рис. 6.3, б). Второй стык В сваривается с предварительным изгибом концевого участка привариваемой плети (рис. 6.3, г).
Окончательное восстановление целостности плети сваркой необходимо выполнять при температуре ее закрепления с возможным отклонением ± 5 °С. Возможность восстановления целостности плети при температурах, отличающихся от температуры рельса при ее закреплении, рассматривается в подразд. 6.3.
При восстановлении пути после выброса или сдвига участки рельсовых плетей в месте наибольшего остаточного искривления на длине 25 м должны быть вырезаны и заменены рельсами с соответствующим износом, соединенными с плетями накладками или сваренными с ними.
Изменение напряженно-деформированного состояния в зоне сварки и на прилегающих участках при восстановлении целостности плети
Наряду с восстановлением целостности рельсовых плетей необходимым условием их последующей эксплуатацией безопасной является восстановление в зоне сварки и на прилегающих участках напряженного состояния, близкого к расчетному.
При восстановлении целостности плетей при температурах рельсов отличающихся от температуры закрепления плетей в зоне сварки и на прилегающих участках могут возникнуть продольные силы существенно отличающиеся от расчетных. Указанное следует из рассмотрения эпюр продольных сил, формирующихся в зоне восстановления целостности плети (рис. 6.4).
При изломе рельсовой плети при некоторой температуре рельса меньше температуры закрепления плети (t1 < tзакр ) в месте излома и на прилегающих участках длиной lд произойдет
реализация продольных сил площадью W1 в продольные деформации (рис. 6.4, а). После окончательного восстановления целостности рельсовой плети при температуре t2 < tзакр (рис. 6.4,
б) и последующего повышения температуры до t3 эпюра продольных сил примет вид, изображенный на рис. 6.4, в. Как следует из эпюры продольных сил на рис. 6.4, в, в зоне сварки возникает дополнительная сжимающая сила Nt3 , численно равная величине продольной силы в
плети, соответствующей температуре рельса при окончательном восстановлении t2.
При окончательном восстановлении целостности рельсовой плети при температуре выше температуры закрепления (t4 > tзакр ) эпюра продольных сил в зоне сварки и на прилегающих
участках имеет вид, изображенный на рис. 12.4, г. При понижении температуры до t5 < tзакр в зоне
сварки возникает дополнительная растягивающая сила |
Nt |
, численно равная величине |
|
|
5 |
продольной силе в плети при восстановлении ее целостности t4.
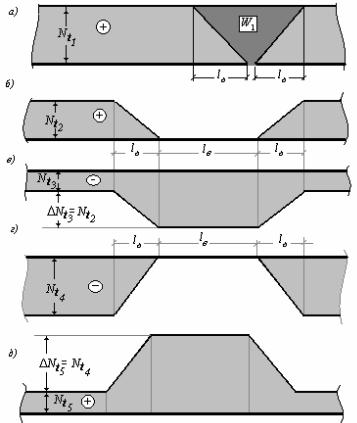
Рис. 6.4. Изменение продольных сил в зоне восстановления целостности плети при циклическом изменении температуры рельсов:
lд — концевые участки продольной деформации ; lв — рабочая зона восстановления плети
Величины возникающих дополнительных как сжимающих, так и растягивающих продольных сил могут достигать существенных значений.
Пример
Расчетная температура закрепления плети tзакр = +30 °C.
Температура рельса при окончательном восстановлении плети t2 = +5 °C.
Тогда при повышении температуры выше расчетной температуры закрепления плети в зоне сварки и на прилегающих участках возникает дополнительная сжимающая сила, равная:
Nt = αEF(t2 − tзакр ) .
Учитывая, что для рельсов типа Р65 — αEF ≈ 20,5 кН / °С, получим:
Nt = αEF(t2 − tзакр ) = 20,5(5 − 30 ) = −512,5 кН.
Полученная величина дополнительной продольной сжимающей силы вызывает опасность потери устойчивости при температурах, близких к максимальным.
Таким образом, выполнение окончательного восстановления целостности плети сваркой при температурах, отличающихся от температуры ее закрепления более чем на ± 5 °С, вызывает появление в зоне сварки и на прилегающих участках дополнительных продольных сил, вызывающих осложнения при эксплуатации бесстыкового пути. Поэтому при восстановлении целостности плетей необходимы технологические решения, исключающие появление указанных дополнительных продольных сил.

Восстановление расчетного напряженного состояния рельсовой плети в зоне сварки и на прилегающих участках с использованием гидравлических натяжных устройств
Для снятия ограничений температурных условий производства работ по окончательному восстановлению целостности рельсовых плетей существует технология, обеспечивающая создание в зоне сварки и на прилегающих участках напряженного состояния, близкого к расчетному. При окончательном восстановлении целостности плети при некоторой температуре рельса t, которая меньше температуры закрепления плети, в зоне сварки и на прилегающих участках необходимо создать продольные растягивающие силы Nt на участке ( 2lд + lp + lсв ). Общая площадь необходимых продольных сил равна W
(см. рис. 6.5, а). Восстановление расчетных продольных сил на участке ( 2lд + lp + lсв )
осуществляется посредством создания до сварки в плети избыточных продольных сил на одном из прилегающих концов плетей площадью W и перераспределением этих сил после сварки.
Работы производятся с помощью гидравлического натяжного устройства в следующей технологической последовательности.
•Разболчивается стык и раскрепляется концевой участок одной из прилегающих к зоне сварки плетей (l0 на рис. 6.5, б). Длину участка раскрепления в соответствии с ТУ–2001 рекомендуется принимать равной 150 м. Для уменьшения погонного сопротивления раскрепленный участок необходимо вывесить на роликовые опоры или антифрикционные прокладки.
•Укладывается рельсовая рубка длиной, обеспечивающей создание расчетного зазора. Устанавливается гидравлическое натяжное устройство (ГНУ на рис. 6.5, б). На протяжении временного рельса lp и участка lсв для создания предварительного изгиба при сварке гайки клеммных и закладных болтов затягивают крутящим моментом
соответственно 200 и 150 Н м.
•Производится растяжение раскрепленного участка на расчетную величину. Эпюра созданных продольных сил имеет вид, представленный на рис. 6.5, в (без учета погонного сопротивления на протяжении участка раскрепления).
•Закрепляется раскрепленный участок протяженностью l0. Снимается гидравлическое натяжное устройство. В зоне стыка и на прилегающих участках происходит частичная разрядка продольных сил. Подготавливается участок (lp +lсв ) для сварки плети. Эпюра
остаточных продольных сил имеет вид, изображенный на рис. 6.5, г. При этом площадь избыточных растягивающих продольных сил WГНУ численно должна быть равна площади продольных сил W, необходимых для восстановления в зоне сварки продольных сил, близких к расчетным.
• После восстановления целостности плети посредством сварки рельсовой рубки с концами плетей производится раскрепление участка (lд-ГНУ + l0 + lвост ) . В результате
перераспределения продольных сил в зоне сварки и на прилегающих участках будет создано напряженное состояние, близкое к расчетному (рис. 6.5, д).
Для определения необходимой величины растягивающей продольной силы, создаваемой ГНУ используем ранее рассмотренный графо-аналитический метод. Величина продольных деформаций растяжения, эквивалентная восстанавливаемому напряженному состоянию, определяется выражением:
W
λW = , (6.1)
EF
где W — площадь эпюры создаваемых продольных сил; EF — продольная жесткость рельса.
В соответствии с рис. 6.5, а:
W = (lд + lр + lсв )× Nt = (lд + lвосст )× Nt . |
(6.2) |
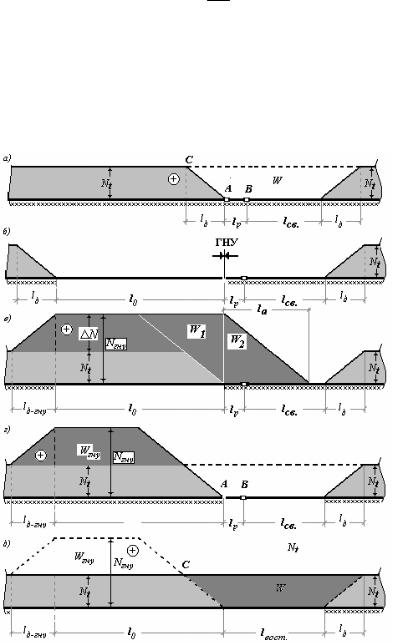
В соответствии с технологией восстановления целостности рельсовой плети после сварки заключительного стыка В (рис. 6.5) остается изогнутый участок плети с остаточной стрелой fост = 0,15–0,30 м. Последующее выпрямление изогнутого участка приводит к появлению сжимающих продольных сил, которые соответственно уменьшают расчетные растягивающие силы. Поэтому необходимо создать дополнительные растягивающие силы, равные величине данных сжимающих сил. Деформационный эквивалент указанных сжимающих продольных сил можно оценить по известной зависимости:
f 2
λизг = 2,75 ост , (6.3) l
где l — хорда стрелы изгиба (можно принять l = 40 м). С учетом (6.3) деформационный эквивалент составит:
λэкв = λW + λизг |
(6.4) |
Следовательно, необходимая площадь эпюры создаваемых дополнительных продольных сил WГНУ (рис. 6.5) определяется выражением:
WГНУ = λэкв × EF . |
(6.5) |
Рис. 6.5. Создание в зоне сварки и на прилегающих участках расчетного напряженного состояния:
lд — длина участка продольной деформации, соответствующая продольной силе Nt; lр — рельсовая вставка; lсв — участок для предварительного изгиба плети при сварки; l0 — участок раскрепления; lд-ГНУ — длина участка продольных деформаций, соответствующая дополнительным продольным
силам; lвост — рабочая зона восстановления целостности плети