
634
.pdf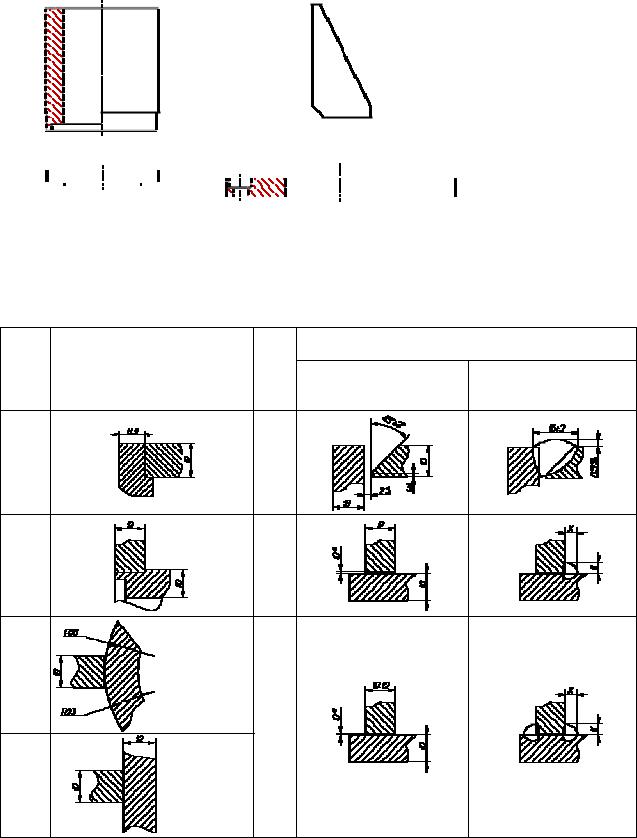
|
Крышка |
|
Фланец |
|
|
|
|
|
|
|
|
|
|
|
|
|
|
|
|
|
|
|
|
|
|
|
|
|
|
Рис. 11. Детали, входящие в сварную сборочную единицу
2. Выбор тип сварного шва для соединения полученных деталей ручной дуговой сваркой (ГОСТ 5264-80).
В разработанной сварной сборочной единице будет использовано 3 типа сварных швов (табл.
7).
Таблица 7
Используемые сварные швы
|
Соединяемые |
детали |
Корпус |
и крышка |
|
|
Корпус |
и фланец |
|
Ребро и корпусом |
|
|
Ребро и фланцем |
Место соединения
Тип шва
У6
Т1
Т3
Конструктивные элементы
Подготовленных
сварного шва
кромок свариваемых деталей
3. Составление спецификации сварной сборочной единицы (рис. 12).
15
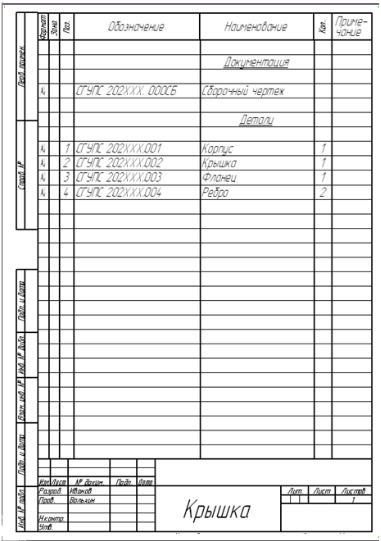
Рис. 12. Спецификация
4. Оформление сборочного чертежа сварной единицы и чертежей всех входящих в неё деталей. На рис. 13 приведен пример сборочного чертежа сварного соединения.
16
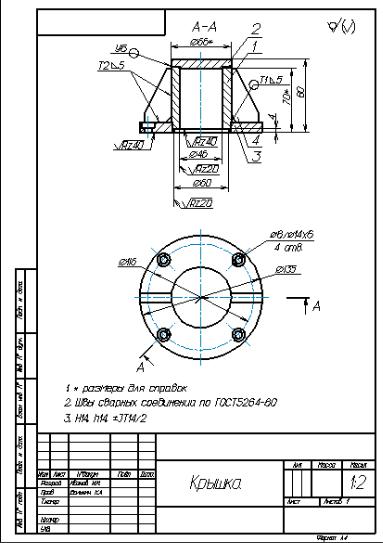
Рис. 13. Сборочный чертеж
На рис. 14, 15, 16 и 17 приведены чертежи всех входящих в сборочную единицу деталей.
17
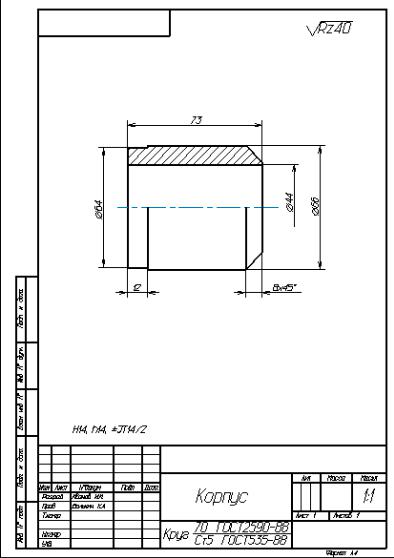
Рис. 14. Рабочий чертеж корпуса
18
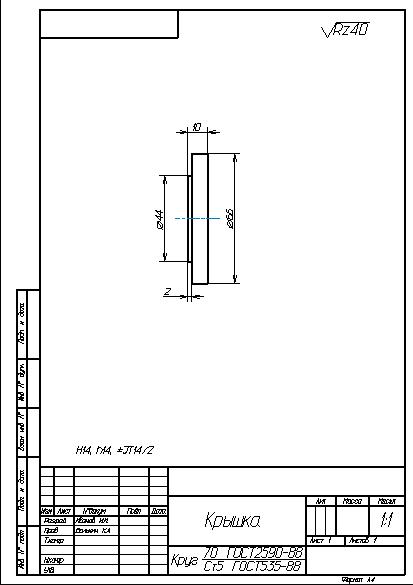
Рис. 15. Рабочий чертеж крышки
4.РАБОЧИЙ ЧЕРТЕЖ ЗУБЧАТОГО КОЛЕСА
Впроцессе работы над заданием необходимо:
–ознакомиться с правилами оформления чертежей зубчатых колес;
–на основании исходных данных (таблица 8), разработать конструкцию зубчатого колеса
–построить 3D модель и выполнить рабочий чертеж зубчатого колеса.
Справочная информация для выполнения задания
На рис. 18 дано наглядное изображение цилиндрического прямозубого колеса.
19
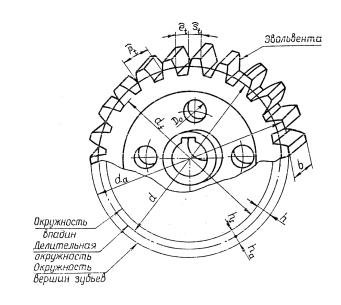
Рис. 18. Наглядное изображение цилиндрического прямозубого колеса
Основными параметрами зубчатого колеса согласно ГОСТ 16531–70 являются: d – диаметр делительной окружности;
dа – диаметр окружности выступов; df – диаметр окружности впадин;
Pt – окружной делительный шаг зубьев, представляющий собой расстояние между одноименными профилями соседних зубьев по дуге делительной окружности;
Таблица 8
Варианты для выполнения зубчатых колес
варианта |
|
|
Тип |
Шири- |
Общая |
Диа- |
Диа- |
Кол-во |
Диаметр |
|
|
|
|||||||
|
Мо- |
Кол-во |
на зуб- |
шири- |
метр |
||||
|
дуль |
зубьев |
сту- |
чатого |
на ко- |
ступи- |
метр |
отвер- |
отвер- |
№ |
|
|
пицы |
венца |
леса |
цы |
вала |
стий |
стий dо |
|
|
|
|
|
|
|
|
|
|
|
|
|
|
|
|
|
|
|
|
1 |
2 |
3 |
4 |
5 |
6 |
7 |
8 |
9 |
10 |
|
|
|
|
|
|
|
|
|
|
1 |
4 |
90 |
С |
80 |
100 |
60 |
50 |
3 |
70 |
2 |
3 |
78 |
С |
50 |
80 |
80 |
40 |
5 |
35 |
3 |
5,5 |
94 |
В |
80 |
120 |
120 |
60 |
5 |
100 |
4 |
5 |
88 |
В |
100 |
120 |
120 |
65 |
6 |
60 |
5 |
2,25 |
86 |
В |
80 |
110 |
80 |
50 |
7 |
18 |
6 |
2 |
80 |
В |
60 |
90 |
70 |
40 |
7 |
20 |
7 |
1,25 |
66 |
В |
30 |
45 |
40 |
20 |
8 |
10 |
8 |
1,5 |
58 |
С |
30 |
50 |
35 |
18 |
5 |
13 |
9 |
1,75 |
72 |
С |
30 |
50 |
50 |
30 |
5 |
20 |
10 |
2 |
76 |
С |
30 |
50 |
50 |
30 |
5 |
25 |
11 |
2,75 |
88 |
С |
30 |
50 |
60 |
35 |
4 |
50 |
12 |
1,5 |
54 |
В |
50 |
60 |
30 |
20 |
7 |
25 |
13 |
3 |
86 |
С |
80 |
110 |
80 |
50 |
4 |
55 |
14 |
7 |
90 |
С |
80 |
150 |
100 |
70 |
4 |
120 |
16 |
4,5 |
62 |
В |
60 |
80 |
80 |
45 |
5 |
55 |
17 |
3 |
68 |
В |
80 |
100 |
75 |
42 |
7 |
30 |
18 |
2 |
60 |
С |
50 |
60 |
45 |
26 |
5 |
20 |
19 |
3,5 |
30 |
С |
32 |
50 |
40 |
18 |
5 |
15 |
20 |
2,75 |
34 |
С |
40 |
60 |
40 |
20 |
6 |
13 |
21 |
2,25 |
42 |
С |
40 |
55 |
35 |
20 |
7 |
15 |
22 |
1,75 |
46 |
С |
20 |
35 |
30 |
16 |
6 |
14 |
23 |
2 |
52 |
С |
30 |
50 |
35 |
20 |
5 |
18 |
24 |
2,75 |
58 |
С |
45 |
70 |
50 |
26 |
6 |
30 |
25 |
3,5 |
66 |
С |
50 |
75 |
75 |
35 |
5 |
40 |
26 |
4 |
74 |
С |
75 |
100 |
90 |
50 |
6 |
50 |
20 |
|
|
|
|
|
|
|
|
|
27 |
2,75 |
68 |
С |
60 |
90 |
65 |
30 |
7 |
30 |
28 |
3,5 |
76 |
В |
80 |
110 |
90 |
55 |
6 |
45 |
29 |
3 |
72 |
В |
100 |
140 |
70 |
35 |
5 |
45 |
30 |
4 |
80 |
В |
80 |
110 |
90 |
45 |
6 |
60 |
21
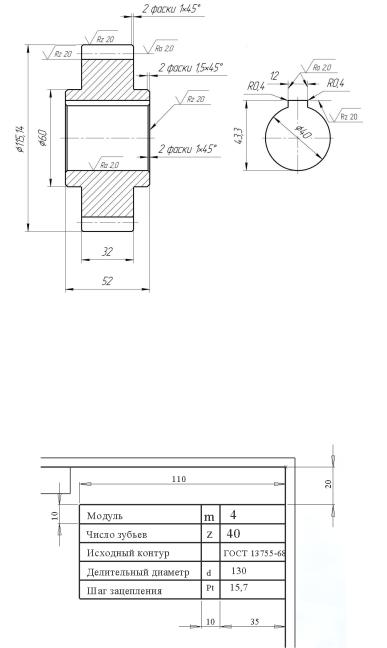
St – окружная толщина зуба;
et – окружная ширина впадины зуба; ha – высота головки зуба;
hf – высота ножки зуба; z – число зубьев.
Основным расчетным параметром зубчатого зацепления является модуль зацепления. Так как длина делительной окружности d = Pt Z, то d = m Z.
Из этих уравнений следует два определения модуля:
–это линейная величина, в dπ раз меньшая окружного шага;
–это число мм делительного диаметра, приходящихся на один зуб.
Модуль является основным расчетным параметром зубчатой передачи. Его значения являются стандартными (0,05…100 мм), их при проектировании выбирают из ГОСТ 9563–60.
Рабочие чертежи зубчатых колес должны быть выполнены в соответствии с требованиями ГОСТ 2.403–75. На рис. 19 представлен образец рабочего чертежа зубчатого колеса.
Рис. 19. Чертеж зубчатого колеса
Пояснения по типу ступицы:
А – без ступицы; В – с односторонней ступицей; С – с двусторонней ступицей.
Вверхнем правом углу приводится таблица параметров зубчатого колеса. В учебных целях таблица дается в сокращенном варианте.
Вней указывается модуль, число зубьев, исходный контур (для прямозубых цилиндрических колес ГОСТ 13755–81..), делительный диаметр и шаг зацепления зубчатого колеса.
Пример оформления таблицы параметров приведен на рис. 20.
Рис. 20. Таблица параметров зубчатого колеса
22
5.РАБОЧИЙ ЧЕРТЕЖ ПРУЖИНЫ
Впроцессе работы над заданием необходимо:
–ознакомиться с правилами оформления чертежей пружин;
–на основании исходных данных (табл. 9), разработать конструкцию пружины;
–выполнить 3D модель пружины, ее рабочий чертеж, а также необходимые расчеты ее основных параметров.
Справочная информация для выполнения задания
Детали машин и механизмов, служащие для накопления энергии за счет упругой деформации, называются пружинами. После соответствующей термообработки пружины приобретают устойчивые во времени свойства упругости, позволяющие сопротивляться ударным нагрузкам.
Рабочие чертежи пружин должны быть выполнены в соответствии с требованиями ГОСТ 2.401–68.
Пружины всех типов изображают в свободном состоянии, когда на пружину не действуют внешние силы. Винтовые пружины на рабочих чертежах изображают горизонтально и только с правой навивкой. Действительное направление навивки указывают в технических требованиях.
Опорные витки цилиндрических винтовых пружин сжатия поджаты на 3/4 длины витка. На опорных витках шлифовкой создают плоскую опорную поверхность, перпендикулярную оси пружины. Это предупреждает перекосы пружины при воздействии на нее осевых сил.
Приняты обозначения:
–n – число рабочих витков, имеющих полное сечение, определяется расчетом и округляется до 0,5 витка;
–n1 – полное число витков, n1 = n + 1,5.
Винтовые пружины растяжения отличаются от пружин сжатия тем, что в свободном состоянии их витки плотно, без зазоров прилегают друг к другу так, что их шаг t равен диаметру проволоки d. Все витки пружины растяжения, за исключением кольцевых зацепов, являются рабочими.
Таблица 9
Варианты заданий для выполнения пружины растяжения
|
Пружи- |
Пружи- |
Пру- |
Сред- |
|
|
|
|
|
№ |
жина в |
|
Диа- |
|
Кол-во |
|
|||
вари |
на в сво- |
на в на- |
конеч- |
ний |
Шаг |
метр |
Марка |
рабо- |
|
ри- |
бодном |
чальном |
ном ра- |
диаметр |
пру- |
прово- |
стали |
чих |
|
анта |
состоя- |
рабочем |
бочем |
пружи- |
жины |
локи |
|
витков |
|
|
нии |
сжатии |
сжатии |
ны |
|
|
|
|
|
|
|
|
|
|
|
|
|
|
|
1 |
40 |
30 |
15 |
20 |
10 |
2,5 |
60С2А |
4 |
|
2 |
50 |
30 |
15 |
20 |
10 |
3 |
51ХФА |
5 |
|
3 |
45 |
30 |
20 |
30 |
7 |
3 |
70С3А |
6,5 |
|
4 |
55 |
35 |
20 |
30 |
10 |
3 |
65СВА |
5,5 |
|
5 |
70 |
50 |
30 |
40 |
10 |
4 |
60С2А |
7 |
|
6 |
100 |
70 |
45 |
40 |
10 |
4 |
51ХФА |
10 |
|
|
|
|
|
|
|
|
|
|
Окончание табл. 9 |
|
|
|
|
|
|
|
|
|
|
|
Пружи- |
Пружи- |
Пру- |
Сред- |
|
|
|
|
|
№ |
на в сво- |
на в на- |
жина в |
ний |
Шаг |
Диа- |
|
Кол-во |
|
вари |
бодном |
чальном |
конеч- |
диаметр |
пру- |
метр |
Марка |
рабо- |
|
ри- |
состоя- |
рабочем |
ном ра- |
пружи- |
жины |
прово- |
стали |
чих |
|
анта |
нии |
сжатии |
бочем |
ны |
|
локи |
|
витков |
|
|
сжатии |
|
|
|
|
|
|||
|
|
|
|
|
|
|
|
|
|
7 |
95 |
80 |
60 |
30 |
30 |
4,2 |
70С3А |
13,5 |
|
8 |
120 |
80 |
60 |
50 |
15 |
6 |
65СВА |
8 |
|
9 |
110 |
90 |
75 |
45 |
12 |
7 |
60С2А |
9 |
|
10 |
100 |
75 |
55 |
40 |
7 |
3,5 |
51ХФА |
14,5 |
|
11 |
155 |
120 |
80 |
60 |
15 |
7 |
70С3А |
10,5 |
|
12 |
85 |
65 |
60 |
40 |
8 |
5,6 |
65СВА |
10,5 |
|
13 |
70 |
50 |
40 |
25 |
6 |
3,2 |
60С2А |
12 |
|
14 |
45 |
40 |
30 |
30 |
5 |
3,2 |
51ХФА |
9 |
|
15 |
50 |
45 |
30 |
25 |
5 |
2,8 |
70С3А |
10 |
|
16 |
60 |
50 |
40 |
35 |
5 |
3 |
65СВА |
12 |
|
23
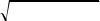
17 |
80 |
70 |
45 |
35 |
8 |
4 |
60С2А |
10 |
18 |
70 |
60 |
40 |
30 |
7 |
3,8 |
51ХФА |
10 |
19 |
60 |
50 |
35 |
30 |
6 |
3,2 |
70С3А |
10 |
20 |
50 |
45 |
30 |
25 |
5 |
2,5 |
65СВА |
10 |
21 |
40 |
35 |
20 |
30 |
5 |
2,2 |
60С2А |
8 |
22 |
30 |
25 |
20 |
35 |
5 |
2,5 |
51ХФА |
6 |
23 |
110 |
70 |
30 |
35 |
20 |
5 |
70С3А |
5,5 |
24 |
75 |
60 |
35 |
30 |
10 |
4 |
65СВА |
7,5 |
25 |
60 |
45 |
30 |
25 |
8 |
3,5 |
60С2А |
7,5 |
26 |
55 |
45 |
40 |
30 |
6 |
4,2 |
51ХФА |
9 |
27 |
55 |
45 |
35 |
20 |
5 |
3 |
70С3А |
11 |
28 |
90 |
70 |
50 |
30 |
9 |
4,5 |
65СВА |
10 |
29 |
85 |
75 |
60 |
40 |
6 |
4,2 |
60С2А |
14 |
30 |
75 |
70 |
65 |
40 |
5 |
3,8 |
51ХФА |
15 |
Длина развернутой пружины растяжения рассчитывается по формуле
L = (D – d)(n + 2).
Длина развернутой пружины сжатия считается по формуле:
L = l n1,
где l – длина одного витка пружины; n1 – полное число витков
l = π2 (D − d)2 + t2 ,
где D – наружный диаметр пружины; t – шаг пружины; d – диаметр проволоки. В технических требованиях указываются:
–направление навивки пружины;
–L – длина развернутой пружины;
–n – число рабочих витков;
–n1 – полное число витков;
–DC – диаметр контрольного стержня, указанный для контроля кривизны оси пружины;
–Dг – диаметр контрольной гильзы, указанный для контроля кривизны самой пружины;
–* размеры для справок.
DC = 0,96 D1, где D1 – внутренний диаметр пружины D1 = D – 2d; Dг = 1,06D
В основной надписи чертежа (гр. 3) указывается материал, из которого выполнена пружина, например:
Проволока II – 4.0 ГОСТ 9389–75,
где II – класс изготовления проволоки (норм.), а 4.0 – диаметр проволоки.
Материал для пружины выбирают с учетом степени и продолжительности нагрузки. Наиболее часто используют стали марок 65Г, 70, 65, 50 х А и др.
Выбор материала зависит от параметров пружины по ГОСТ 13.766–68. На рис. 21 приведен пример оформления рабочего чертежа пружины.
24