
645
.pdfПри проектных расчетах по известной величине усилия, которое должно быть создано тягой электромоторного устройства, определяется мощность электромотора по приведенной выше формуле. По величине мощности и принятому числу оборотов подбирают электромотор по каталогу электродвигателей переменного тока.
4.9. Расчет приспособления на точность
Для получения требуемой точности обрабатываемой детали необходимо выбрать такую схему приспособления, при которой действительные погрешностибазирования б заготовки вприспособлении были бы меньше или равны допустимым значениям доп погрешности базирования.
Расчетнаясуммарнаяпогрешность приспособленияопределяется по формуле
пр – (K1 б + у + K2 ),
где — допуск на полученный размер детали; б — погрешность базирования этой детали. Формулы для определения действительного значения погрешностейбазирования для встречающихсясхембазированияприведенывлитературе[4, 5]; —точность обработки на размер детали при выполнении данной операции. При расчетах в курсовой работе можно принимать среднюю экономическую точность обработки, указанную в таблицах справочника [5] для соответствующего способа обработки.
у — погрешность установки заготовки. Определяется по справочнику [5].
4.10. Прочностной расчет приспособлений
Прочность — одно из основных требований, предъявляемых к деталям и приспособлениям в целом. Прочность деталей может рассматриваться по коэффициентам запаса или по номинальным допускаемым напряжениям. Расчеты по номинальным допускаемымнапряжениямменееточныи прогрессивны,нозначительно проще.
С помощью расчета деталей (элементов) приспособлений на прочность можно решать две задачи:
1. Проверка на прочность уже существующих деталей с определенными размерами сечений путем сравнения фактичес-
2 1

ких напряжений (моментов, сил) с допускаемыми — проверочный расчет.
2. Определение размеров сечений деталей — предварительный проектный расчет.
Расчет на прочность детали в виде стержня круглого сечения, нагруженного осевой силой, по допускаемым напряжениям растяжения (сжатия) осуществляется по формуле
4P ,d2
где — фактическое напряжение растяжения (сжатия), МПа; Р — расчетная осевая сила, Н; d — диаметр опасного сечения (для резьбового стержня — внутренний диаметр резьбы), мм; [ ] — допускаемое напряжение растяжения (сжатия), МПа.
Определение необходимого размера опасного сечения для подобного случая можно производить по формуле
4P d .
Полученное значение округляется в сторону увеличения до целого или ближайшего стандартного значения. При наличии шпоночного паза в опасном сечении детали полученное расчетом значение d следует увеличить на 5…10 %.
Расчеты на прочность валов и осей с целью определения их размеров можно производить по формулам:
на изгиб (детали круглого сечения)
d 3 Mиз ,
0,1 из
на изгиб (детали кольцевого сечения)
d 3 |
Mиз |
|
, |
0,11 k04 |
из |
на кручение
d 3 Mкр ,
0,2 кр
на изгиб с кручением (детали круглого сечения)
d 3 Mэкв ,
0,1 из
2 2
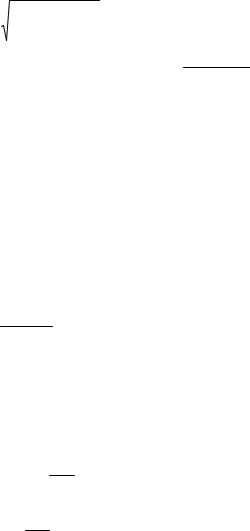
на изгиб с кручением (детали кольцевого сечения)
d 3 |
Mэкв |
|
|
, |
|
0,11 k04 из |
где Миз — изгибающий момент, Н∙мм; Мкр — крутящий момент,
Н∙мм; Мэкв — эквивалентный момент, Н∙мм, Мэкв Миз2 Мкр2 ; [ из] — допускаемое напряжение при изгибе, МПа; [ кр] — допускаемое напряжение при кручении, МПа; k0 = d0/d — отношение внутреннего диаметра вала (оси) d0 к наружному d.
Необходимо помнить, что оси рассчитываются только на изгиб, так как они не передают крутящего момента.
Валы и оси можно рассчитывать на жесткость, но диаметр деталей в этом случае получается большим, чем при расчете на прочность.Расчетнаизгибнуюжесткостьсостоитизопределения углов наклона и прогибов упругой линии осей и валов и сравнения их с допускаемыми значениями. Следует отметить и сложность расчетов деталей на жесткость. Например, расчет валов на жесткость при кручении производится по формуле
180Mкрl ,
GIр
где — действительный угол закручивания вала, град; [ ] — допускаемый угол закручивания; Мкр — крутящий момент, Н∙мм; l — длина скручиваемой части вала, мм; G — модуль упругости при сдвиге, МПа; Iр — полярный момент инерции сечения вала, мм4.
Для круглого сечения
d4
Iр 32 ;
для кольцевого сечения
Iр d4 (1 k04). 32
Уточненный расчет валов на прочность, в случае возникновения такой необходимости, заключается в определении коэффициентов запаса для опасных сечений.
При нагружении соединения силами в плоскости (по поверхности) стыка деталей и в случаях установки штифта (цилиндри-
2 3

ческого гладкого стержня винта) без зазора и работы на срез проверочный расчет штифта (винта) может осуществляться по формуле
ср 4dР2i ср ,
где Р — срезающая сила, Н; d — диаметр штифта (стержня винта), мм; i — число стыков (количество штифтов или винтов) в соединении; [ ср] — допускаемое напряжение среза, МПа.
Расчет на прочность шпоночных и шлицевых соединений заключается в сравнении фактически передаваемого крутящего момента с допускаемым моментом из условий прочности шпонок (шлиц).
Расчет на прочность шпоночных соединений производится по формулам:
на смятие для призматических шпонок
Mкр 0,25Dhl см ;
для сегментных шпонок
Mкр 0,5DKшl см ;
на срез для призматических и сегментных шпонок
Mкр 0,5Dbl ср ,
где Мкр — крутящий момент, Н∙мм; D — наружный диаметр вала, мм; h — высота призматической шпонки, мм; Kш — размер выступающей из паза части сегментной шпонки, мм; l — рабочая длина шпонки, мм; [ см] — допустимые напряжения смятия, МПа.
Проверочный расчет на прочность шлицевых соединений может осуществляться по формулам:
на смятие прямобочный профиль
Mкр 0,5zhl ' см ;
эвольвентный профиль
Mкр 0,5mz2hl ' см ;
на срез прямобочный и эвольвентный профили
Mкр 0,5zbl '(D d)[ ср],
где Мкр — крутящий момент, Н∙мм; z — число шлицев; h — высота поверхности контакта; D— наружный диаметр вала, мм;
2 4
d —внутренний диаметр отверстия, мм; b — ширинашлица, мм; m — модуль эвольвентного соединения, мм; — коэффициент, учитывающий неравномерность распределения нагрузки по шлицам.
При необходимости расчеты на прочность сварных соединений, пружин, подшипников, клиноременных, зубчатых передач
идругих специфических сборочных единиц и деталей специальных приспособлений следует выполнять с помощью справочных
идругих литературных источников.
5. ГРАФИЧЕСКАЯ ЧАСТЬ КУРСОВОЙ РАБОТЫ
Графическая часть курсовой работы показывает результат проектирования и конструирования и содержит сборочный чертеж станочного приспособления.
На сборочном чертеже приспособления указывают необходимые размеры, которые обеспечивают точность расположения элементов приспособления, справочные размеры (монтажные, установочные и др.). На свободном поле чертежа над штампом основной надписи размещают технические требования на изготовление станочного приспособления.
На сборочном чертеже приспособления все составные части (сборочные единицы и детали) нумеруют. Номера позиций располагают параллельно основной надписи чертежа вне контураизображения игруппируют вколонку или строчку по возможности на одной линии. На листе сборочного чертежа приспособления допускается помещать в правом верхнем углу операционный эскиз.
В процессе проектирования станочного приспособления необходимо выполнятьтребованияЕдинойсистемыконструкторской документации (ЕСКД) и государственных стандартов на все элементы проектируемого приспособления.
Рекомендуемая литература
1.Аксенов В.А., Полиновский Л.А. Технология машиностроения и производство машин: Метод. указ. к лабораторно-практическим работам (часть 1). Новосибирск: Изд-во СГУПСа, 1998. 46 с.
2.Аксенов В.А., Полиновский Л.А. Технология машиностроения и производство машин: Метод. указ. к курсовой работе. Новосибирск: Изд-во СГУПСа, 1999. 28 с.
2 5
3.Альбом по проектированию приспособлений: Учеб. пособие для студентов машиностроительных специальностей вузов / Б.М. Базров, А.И. Сорокин, В.А. Губарь и др. М.: Машиностроение, 1991. 121 с.
4.Андреев Г.Н., Новиков В.Ю., Схиртладзе А.Г. Проектирование техно-
логической оснастки: Учеб. пособие для высш. учеб. заведений. М.: Станкин, 1997. 416 с.
5.Справочниктехнолога-машиностроителя:В 2т./ Подред. А.Г.Косиловой, Р.К. Мещерякова. 4-е изд., перераб. и доп. М.: Машиностроение, 1986. 496 с.
6.Технология машиностроения и производство машин (Резание металлов): Метод. указ. к выполнению лабораторных и практических работ / Сост. Л.А. Полиновский, В.А. Шаламов, О.А. Шаламова. Новосибирск: Изд-во СГУПСа, 2003. 68 с.
2 6
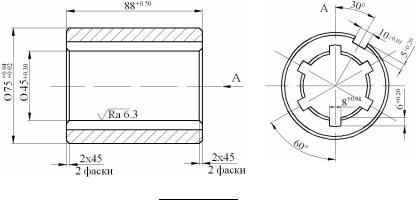
ПРИЛОЖЕНИЯ
Приложение А
Федеральное агентство железнодорожного транспорта Сибирский государственный университет путей сообщения
Кафедра «Технология транспортного машиностроения и эксплуатация машин»
Задание
для курсовой работы по дисциплине «Технологическая оснастка»
Тема: «Проектирование станочных приспособлений»
студенту |
|
Иванову П.С. |
|
группы |
|
МТМ – 411 |
|
Вариант № 12 |
|
|
|
|
|
|
|
|
|
|
|
|
|
|
Исходные данные: |
|
|
||||
Деталь: |
|
|
|
|
Втулка |
|
|
||
Тип производства: |
|
|
|
|
Единичное |
||||
Операция: |
|
|
|
|
Фрезерование |
||||
Поверхность: |
|
|
|
|
Шпоночный паз |
||||
Вид заготовки: |
|
|
|
|
Отливка |
|
|
||
Материал отливки: |
|
|
|
Бронза |
|
|
|||
Количество одновременно обрабатываемых заготовок: |
1 |
|
|
|
Чертеж детали
Срок сдачи на проверку: до 10.12.2006 г. Сроки защиты: 25.12.2006 г.
1.Задание вшить в расчетно-пояснительную записку после титульного листа. Без задания работа на проверку не принимается.
2.Работу оформить в соответствии со стандартом организации СТП СГУПСа 01.01– 2000 «Курсовой и дипломный проекты. Требования к оформлению».
Задание выдано: 16.10.2006 г. Руководитель: ______________ А.С. Ильиных
2 7
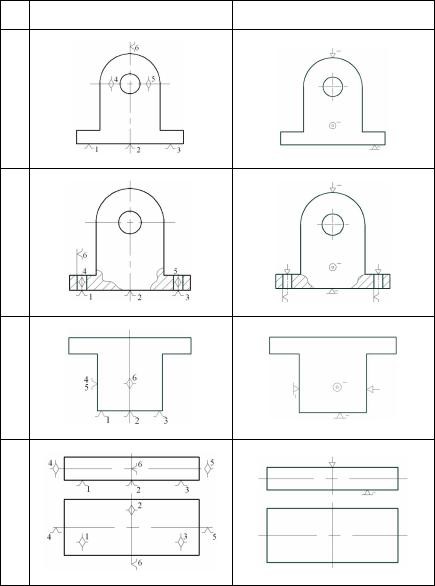
Приложение Б
Схемы базирования и закрепления заготовок
№
Схема базирования Схема закрепления
п/п
1
2
3
4
2 8
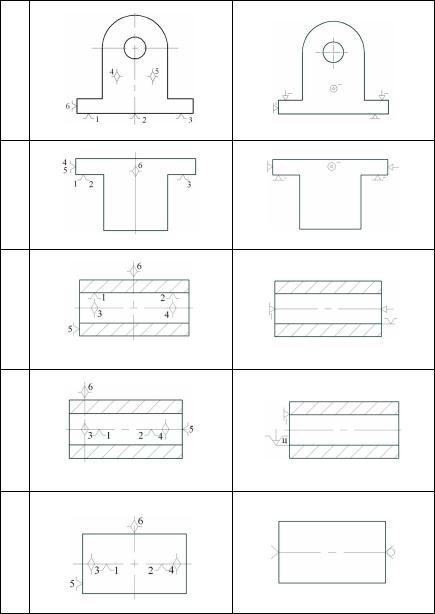
Продолжение прил. Б
5
6
7
8
9
2 9
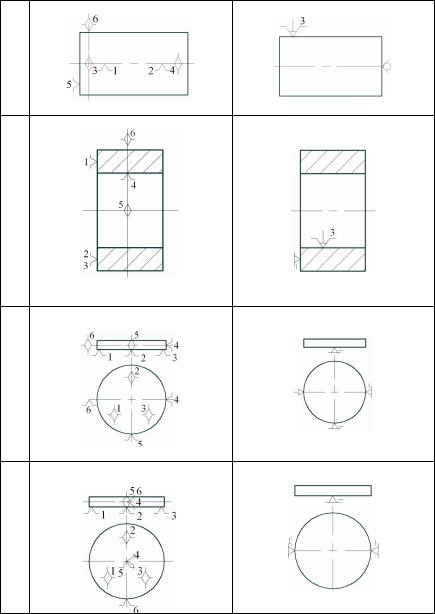
Продолжение прил. Б
10
11
12
13
3 0