
705
.pdfФормовка холодных КФ сухим ОН производят перед их прокалкой. На дно опоки насыпают слой ОН, чтобы уровень торца литниковой воронки совпадал с уровнем верхнего торца опоки, закрываютворонку крышкой и засыпают ОН до верхнего уровня опоки.
Для уплотнения ОН опоки формуют на вибростолах с амплитудой колебаний0,5–0,6 мм ичастотой 1400 колебанийв минуту.
ВкачествеОНприменяютматериалы,неимеющиеполиморфных превращений в интервале температур прокалки: шамотный порошок, плавленый кварц (НКС), электрокорунд.
ФормовкуКФжидкоподвижнымОНпроизводятприизготов-
лениикрупногабаритных отливоксповышеннымитребованиями к точности размеров и формы.
Состав жидкоподвижного наполнителя, % (массовая доля):
—цемент марки 300–500 — 9–12;
—бой электрокорундовых оболочек, шамотного порошка —
60–63;
—вода остальное.
Опоку устанавливаютнавибростол,помещаютвнутрь нееКФ и заливаютпод воздействием вибрации с амплитудой 0,3–0,4 мм, частотой 1400–1500 кол./мин и продолжительностью 10–15 мин.
После естественного твердения цемента КФ прокаливают по режиму: нагрев до 300 °С — 3 ч; 450 °С — 1 ч; 580 °С — 2 ч; 680 °С — 2 ч; 950 °С — 2…4 ч. Итого 10–12 ч.
Формовка прокаленных горячих КФ в кипящий слой ОН.
ОН — электрокорунд зернистостью 40, 50 в устройстве для заливки горячим воздухом приводят в «кипящее» состояние и погружают КФ, после погружения КФ в «кипящий» слой электрокорунда,прекращают подачу сжатоговоздуха. КФплотно окружена электрокорундом. После заливки и охлаждения в дно установки подают сжатый воздух, электрокорунд переходит в «кипящее» состояние и блок отливок вынимают из установки для формовки.
Прокалку КФ производят в электрических печах сопротивления или в газовых печах.
Преимущество газовых печей заключается в увеличении скорости нагрева КФ до температуры прокалки.
11
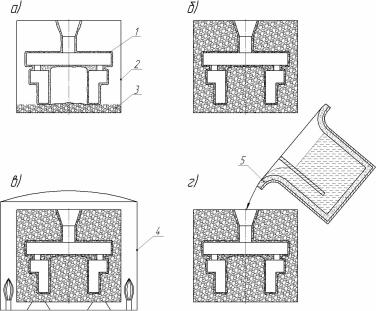
Продолжительность прокалкиКФ зависиттакжеотматериала основы и способа прокалки с опорным наполнителем или без него.
Продолжительность прокалки КФ без опорного наполнителя составляет в зависимости от материала основы: НКС — 0,10– 0,24 ч; электрокорунд — 2,5–3,0 ч; шамот — 3,0–3,5 ч.
Продолжительность прокалки КФ на основе кристаллического кварца, заформованных в сыпучий ОН, составляет 5–6 ч.
Подготовка форм к заливке в ЛВМ представляет совокупность операций прокалки и формовки КФ перед заливкой.
Типоваясхемапроцессаподготовки КФкзаливке показанана рис. 1.5.
Керамические формы заливают, как правило, сразу после извлечения из прокалочной печи. Температура КФ перед заливкой составляет соответственно для литья стали — 700–900 °С, чугуна и медных сплавов — 400–600 °С, алюминиевых и магниевых сплавов — 100–300 °С.
Рис. 1.5. Типовая схема подготовки и заливки керамических форм:
а — засыпка на дно опоки 2 слоя опорного наполнителя 3 и установка КФ на уровне с верхним торцом опоки; б — заформованная в опоку КФ; в — прокалка опок в газовой или электрической печи 4; г — извлечение опок из прокалочной печи и заливка их из чайникового ковша 5
12
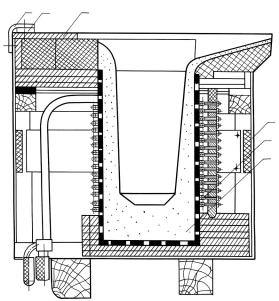
Плавка или приготовление литейных сплавов для заливки КФ включает следующие этапы:
—футеровку и подготовку плавильной печи к плавке;
—расчет, приготовление и навеску шихты;
—подготовку шлакообразующей смеси;
—загрузку и расплавление шихты;
—обработку расплаваи доводку его дотемпературы заливки. В ЛВМ наибольшее распространение, как наиболее удобные,
получили среднечастотные индукционные установки с частотой колебаний электрического тока 1000–2400 Гц, мощностью 60– 320 кВт и емкостью тигля печи от 30 до 250 кг.
Устройство индукционной сталеплавильной печи емкостью 160 кг показано на рис. 1.6.
6 |
5 |
4 |
1
2
3
Рис. 1.6. Устройство индукционной сталеплавильной печи емкостью 160 кг: 1 — каркас печи; 2 — индуктор; 3 — футеровка; 4 — верхняя плита; 5 — электроизоляционная прокладка; 6 — прижим
Футеровку тигля индукционной печи выполняют из смеси порошков огнеупорных оксидов: для плавки углеродистой стали и чугуна применяют кварцит или НКС; для плавки легирован-
13
ных сталей — магнезитовые, хромомагнезитовые или шпинельные порошки (Al2O3∙MgO), для плавки медных и алюминиевых сплавов применяют готовые графитовые тигли, для плавки магниевых сплавов — стальные тигли.
К особенностям плавки в индукционных печах относится то, что расплавляют не всю навеску шихты, а только ее часть, и остальную часть постепенно вводят в жидкий расплав до наплавления всего объема тигля. Поэтому для плавки применяют хорошо очищенные от загрязнений отходы и прокаленные ферросплавы,никельикатоднуюмедь.Крометого,шихтуразрезают на размеры по габаритам в зависимости от емкости тигля печи.
Вторая особенность индукционной плавки состоит в том, что шлак выполняет только функцию защиты расплава от взаимодействия с атмосферой, так как в верхней части тигля его температура недостаточна для проведения реакций восстановления тугоплавких окислов. В индукционных печах не применяют диффузионный метод раскисления сплава из-за низкой активности шлаков. В индукционных печах раскисление стали производятвдваэтапапередвыпускомв тиглепечи алюминиеми вковше силикокальцием или РЗМ.
После заливки формы охлаждают на полу цеха или в холодильных камерах с принудительным охлаждением обдувкой холодным воздухом.
Выбивка отливок—это операцияизвлечения залитых КФ — металлических блоков,окруженных керамикой,и освобождение и очистка опок от ОН в установках, оборудованных кантователем и вибраторами. После кантовки опоки в установке выбивки ОНчерез решеткувысыпаетсяподдействиемвибрацииизопоки, а после кантовки в опоке остаются только металлические блоки, которые извлекают из опок после их выхода из установки выбивки.
Отделение керамики отметаллическихблоковпроизводятна виброударных установках. В результате от металлического блока отделяется керамика с внешних поверхностей отливок. В пазах, глухих полостях и отверстиях малого диаметра остаются частицы керамики.
14
Отделениеотливокотлитниковойсистемыпроизводятпутем отрезки или отбивки. Наибольшее распространение получил метод отделения ЛС от отливок настанках с абразивным кругом.
Очистка отливок — после отделения литниковой системы отливки очищают методами пескоструйной или дробеметной очистки.
В результате этого полностью удаляется керамика, пригар и следы окислов с поверхности отливки.
После очистки производят предварительный контроль отливок внешним осмотром для выявления дефектов. Отливки с неисправимыми дефектами бракуют, а допустимые к исправлению зачищают и заваривают.
После внешнего контроля годных отливок их подвергают контролю внутренних и наружных дефектов различными неразрушающими методами.
Годные отливки термообрабатывают, очищают поверхность и производят окончательный контроль и сдачу отливок в механический цех.
Таким образом, производство литых деталей методом ЛВМ включает следующие этапы: подготовку производства, заключающуюся в разработке технологического процесса, приобретении материалов, проектировании и изготовлении формообразующей оснастки; изготовление керамических форм; плавку и приготовление литейного сплава; заливку керамических форм, охлаждение и выбивку отливок с отделением керамики; обрубку и доработку отливок до требований технических условий; контроль и сдачу годных отливок.
Производство отливок ЛВМ поясняется примерами применяемойформообразующейоснастки,промежуточнымипродуктами и некоторыми операциями технологического процесса, которые приведены ниже на фотографиях.
15
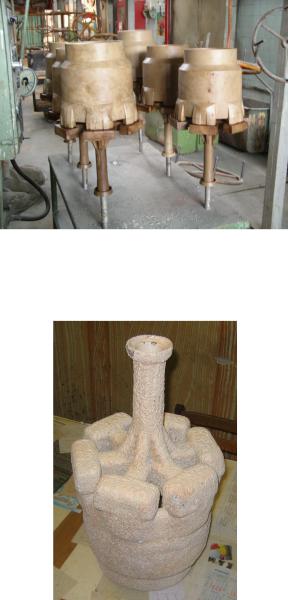
Пример 1.1. Выплавляемые модели отливки «корпус», состоящей из двух частей (рис. 1.7).
Рис. 1.7. Выплавляемая модель отливки «корпус»
Пример 1.2. Готовая КФ отливки «корпус» (рис. 1.8).
Рис. 1.8. Готовая КФ отливки «корпус»
16
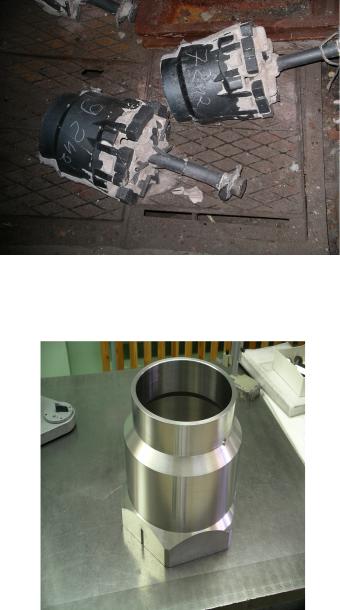
Пример1.3.Отливка«корпус»послевыбивкиизКФ(рис.1.9).
Рис. 1.9. Отливки «корпус» после выбивки из КФ
Пример 1.4. Готовая деталь «корпус» (рис. 1.10).
Рис. 1.10. Готовая деталь «корпус»
17
Контрольные вопросы
1.Дать определение КФ.
2.Что такое ВМ?
3.Как называют формообразующую оснастку для изготовления ВМ?
4.Как называют операцию приготовления сплава для заливки КФ?
5.Рассчитайте размер полости пресс-формы для отливки Ж200 мм из стали 45, если усадка стали равна 1,5 %, материал ВМ — модельный
состав МВС-3А, материал КФ — кристаллический кварц SiO2, температура КФ при заливке 800 °С.
6.Как называют материал для формовки КФ в опоках?
7.Какой огнеупорный материал для изготовления КФ обладает наименьшим коэффициентом линейного расширения?
8.Какие огнеупорные материалы применяются для футеровки индукционных печей при плавке высоколегированных сталей?
9.Как производят очистку отливок?
2. ЛИТЬЕ В КОКИЛЬ
Литьевкокиль—этоспециальный видизготовленияотливок методомсвободной,гравитационнойзаливкижидкогометаллаиз ковша в металлические формы.
Кокиль (фр. coquille — раковина, скорлупа) — металлическая многоразовая форма, служащая для образования наружной поверхности отливки, а для получения внутренней ее полости применяют песчаные или металлические стержни.
Устройство кокиля с песчаными стержнями показано на рис. 2.1 по разъему кокиля.
Устройство кокиля для алюминиевого литья с металлическим стержнем показано на рис. 2.2. Разрез выполнен по разъему.
Для изготовленияполовиноккокиляприменяют серыйчугун, а для плит (нижней части кокиля) и стержней — углеродистые стали.
В настоящее время литьем в кокиль получают отливки из всех промышленных черных и цветных металлов и их сплавов развесом до 200 кг и более.
Экономическая эффективность литья в кокиль определяется его стойкостью.
Стойкость кокиля — это количество годных отливок, получаемых в кокиле до его разрушения или поломки.
18
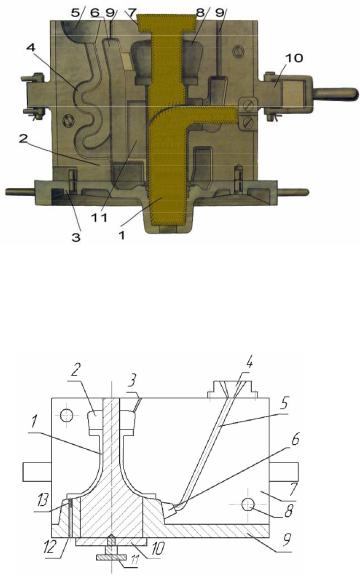
Рис. 2.1. Устройство кокиля с вертикальным разъемом и песчаными стержнями для алюминиевого литья:
1 — нижний стержень из песчано-смоляной смеси; 2 — половины кокиля с вертикальным разъемом; 3 — нижняя часть кокиля; 4 — змеевидный стояк; 5 — литниковая чаша; 6 — обратный стояк (колодец); 7 — верхний песчаный стержень; 8 — прибыли; 9 — выпора; 10 — крепление половины кокиля; 11 — щелевые питатели
Рис. 2.2. Устройство кокиля для алюминиевого литья с металлическим стержнем:
1 — полость отливки; 2 — прибыль; 3 — выпор; 4 — заливочная воронка; 5 — стояк; 6 — коллектор; 7 — половина кокиля; 8 — центрирующие штыри; 9 — плита; 10 — стержень; 11 — хвостовик; 12 — отверстие для установки вентиляционных пробок; 13 — вентиляционная пробка (вента)
19
Металлические формы в результате многократного нагрева и охлаждения при заливке и выбивке отливок испытывают тепловые и механические нагрузки, от которых в стенках кокиля и металлических стержней возникают знакопеременные внутренние напряжения и эрозионное разрушение каналов литниковой системы и мест подвода металла около питателей.
Стойкость кокиля зависит от температуры плавления заливаемого сплава, конфигурации отливки конструкции кокиля и литниковой системы.
Стойкость кокилей для отливокиз черных металлов составляет сотни штук, а из алюминиевых сплавов — тысячи.
Поэтому наибольшее применение литье в кокиль получило для изготовления отливок из алюминиевых сплавов. Сорок процентов всего объема алюминиевого литья, выпускаемого в мире, производится литьем в кокиль.
Особенностью алюминиевых сплавов является их склонность к пленообразованию (окислению наружной поверхности струи жидкого металла) и пенообразованию (захвату воздуха). Для предупреждения попадания плен и воздушных пузырей в полость отливки применяют щелевые (см. рис. 2.1) или коллекторные литниковые системы с поводом металла в нижнюю полость отливки (рис. 2.3).
Для снижения скорости движения потока жидкого металла стояк выполняют змеевидной формы (см. рис. 2.1) или под наклоном 30–45° (см. рис. 2.2). В вертикально-щелевой литниковойсистемедляудержанияпленкислужитобратныйстоякили колодец, а в нижней литниковой системе — коллектор.
Устройство коллекторной литниковой системы показано на рис. 2.3. Показан вид по разъему кокиля после заливки и вид сверху без половинок кокиля.
Сечениестоякапринимаютпрямоугольнойформы,апитатели имеют форму щели. Коллекторв сечении имеетформу трапеции.
При литье в кокиль черных сплавов и сплавов на основе меди литниковую систему выполняют в песчаных стержнях.
Пример устройства неразъемного (вытряхного) кокиля для литья чугуна и медных сплавов с дождевой литниковой системой приведен на рис. 2.4.
20