
новая папка 1 / 773639
.pdf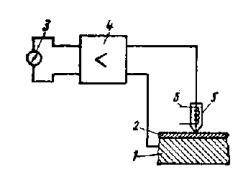
1.5. Термоэлектрический метод
Заключается в следующем: при нагреве места соединения покрытия с оснóвным металлом возникает термоэлектродвижущая сила (ТЭДС), зависящая от сочетания металла и температуры нагрева, чем толще слой покрытия, тем ниже окажется температура места соединения (спая), а следовательно, и возникающая при этом ТЭДС. Таким образом, возникающая ТЭДС будет определять функциональную зависимость между толщиной покрытия и различными сочетаниями металлов. Измеряя с помощью специального электроизмерительного прибора ТЭДС можно определить толщину покрытия.
Метод применяют для металлических покрытий на металлах при толщине покрытия до 50 мкм и разности удельных термо-ЭДС не менее 20 мкВ/град. Относительная погрешность метода ±15 %
Метод применим для всех комбинаций материалов, которые обеспечивают термонапряжение, достаточно большое для надежных измерений (несколько сот мкВ).
Термоэлектрический метод обладает высокой погрешностью, не позволяющей использовать его для определения толщины покрытий элементов на поверхности ответственных технических объектов.
Рис. 3. Принципиальная схема измерения толщины покрытия термоэлектрическим методом: 1 – основа;
2 – металлическое покрытие; 3 – электроизмерительный прибор; 4 – усилитель постоянного тока; 5 – щуп;
6 – нагревательный элемент щупа
Для реализации метода необходимо соблюдение следующих условий:
11
а) для каждого сочетания материалов покрытия и основы необходимы индивидуальная тщательная градуировка прибора по соответствующим эталонам,
б) факторы, влияющие на точность измерения толщины покрытий (температура щупа, давление щупа на деталь, площадь контакта его с деталью и др.), должны быть по возможности постоянными;
в) щуп должен быть изготовлен из того же материала, что и покрытие; в противном случае в месте соединения покрытия со щупом образуется новый спай с дополнительным источником возникновения термо-ЭДС.
2. МЕТОДЫ ОПРЕДЕЛЕНИЯ ПОРИСТОСТИ МЕТАЛЛИЧЕСКИХ ПОКРЫТИЙ
Пористость гальванических покрытий – один из самых серьезных недостатков, ухудшающих защитные антикоррозионные свойства покрытий.
Различают два вида пор макропоры и микропоры. Причиной возникновения макропор чаще всего является неудовлетворительная очистка поверхности от различных загрязнений, приводящая к нарушению сплошности покрытия. На участках с загрязнениями преимущественно выделяется водород, пузырьки которого препятствуют осаждению металла.
Микропоры образуются главным образом вследствие прилипания водородных пузырьков к покрываемой поверхности; пузырьки экранируют участки поверхности, затрудняя кристаллизацию металлического покрытия. В результате появляются водородные поры, имеющие обычно форму кратера и часто пронизывающие покрытие по всей толщине. Повышение внутренних напряжений в покрытии нередко приводит к появлению точечной и канальчатой пористости. Загрязнения электролита анодным шламом, неметаллические включения и взвешенные частицы также способствуют образованию пористости.
Пористость зависит в основном от толщины слоя покрытия: с увеличением толщины слоя пористость уменьшается. Пористость можно снизить повышением температуры и введением окислителей, если поры образуются пузырьками водорода. Отделению пузырьков
12
газа от покрываемой поверхности способствуют также вибрация катодных штанг и перемещение покрываемых деталей.
Применяемые в настоящее время методы выявления пор заключается в использовании реагентов, дающих окрашенные соединения с ионами основного металла или металла подслоя.
Следует различать методы без наложения и с наложением тока. Рекомендуются методы выявления пор до основного металла или металла подслоя. При исследовании пористости покрытия необходимо в большинстве случаев вызвать разрушение основного металла на дне пор и вывести наружу продукты коррозии. Это возможно без наложения внешнего тока, когда покрытие является катодом по отношению к основному металлу в растворе, применяемом для исследования пористости. Основным критерием для классификации способов испытания пористости является наличие гальванической пары: покрытие основной металл.
Если анодом является основной металл, поры выявляют по образованию продуктов его коррозии. Если анодом является покрытие, то при наличии пор происходит ускоренная коррозия покрытия по краям пор.
Перед испытанием поверхность детали обезжиривают, протирая пастой из окиси магния или соответствующим растворителем. Затем тщательно промывают струёй воды и высушивают фильтровальной бумагой или сжатым воздухом. Перед контролем детали выдерживают в помещении, где будут проводить испытание, для выравнивания температур среды и детали. Воздух помещения должен быть чистым, без пыли, содержащей железо или его соединения.
Для исследования пористости покрытий используют методы погружения, наложения паст и фильтровальной бумаги. Эти методы основаны на взаимодействии основного металла или металла подслоя с реагентом в местах пор и образовании окрашенных соединений.
2.1. Метод погружения
Основан на погружении детали в специальный раствор, содержащий: 2 г железосинеродистого калия, 200 мл этилового спирта, 15 25 г пищевого желатина, 10 мл 0,5 н. раствора Н2SО4 и 790 мл воды; температура раствора при испытании детали 25 35 °С. Раствор
13
должен быть жидким, хорошо смачивать деталь и при застывании покрывать равномерным слоем всю поверхность. Для приготовления этого раствора помещают в мерную колбу вместимостью 1 л 2 г железосинеродистого калия и добавляют 200 мл воды, перемешивают до полного растворения, затем добавляют 200 мл этилового спирта и 10 мл 0,5 н. Н2SО4. Отдельно в два стакана вместимостью 500 мл помещают по 10 12 г желатина, добавляют по 250 мл воды и выдерживают для набухания желатина. Стаканы с набухшим желатином нагревают при температуре 50°С до образования коллоидного раствора, помещают его в ту же мерную колбу, охлаждают, доводят водой до метки и перемешивают. Раствором можно пользоваться многократно; его считают непригодным, если он изменил цвет или выпал осадок. Хранить раствор необходимо в темном месте в банках из оранжевого стекла.
При испытании подготовленную деталь равномерно смачивают указанным раствором либо погружением в раствор, либо кистью с наконечником из пластмассы. Детали, смоченные раствором, выдержи-
вают 5 мин при температуре 18 30°С, после чего на исследуемой поверхности при дневном или электрическом освещении подсчитывают число синих точек, соответствующих числу пор в покрытии на данном участке.
По результатам подсчета пор рассчитывают среднее число пор:
NСР NОБЩ / A |
(1) |
где NОБЩ – общее число пор на контролируемой поверхности; A – площадь контролируемой поверхности.
Образование синих точек объясняется взаимодействием раствора, проходящего через поры, с металлом основы. При этом металл основы растворяется с образованием ионов Fе(II), которые реагируют с железосинеродистым калием, образуя соединение синего цвета (турнбулева синь):
3Fe2- + 2K3[Fe(CN)6] Fe3[Fe(CN)6]2 + 6K.
Метод применим для определения пористости никелевых, хромовых, оловянных и серебряных покрытий на стали для деталей малогабаритных и сложной конфигурации.
14
Результаты контроля считают удовлетворительными, если среднее число пор не превышает установленного ГОСТ 9.302–79.
2.2. Метод паст
Основан на химическом взаимодействии основного металла или металла подслоя с реагентом, входящим в состав паст, в местах пор и других несплошностей покрытия. При этом образуются окрашенные соединения, наблюдаемые визуально. Метод применим для определения пористости металлических покрытий на стали, меди, алюминии, цинке и их сплавах, на деталях любой конфигурации и любых размеров. Метод отличается высокой чувствительностью. Рекомендации по выбору индикаторных паст приведены в табл. 1.
Таблица 1 Пасты, применяемые для определения пористости
Вид покрытия |
Основной |
Номер |
Время |
Признак |
|||||
выдержки, |
|||||||||
|
|
|
металл |
пасты |
пористости |
||||
|
|
|
|
|
|
мин |
|
|
|
Все виды |
покрытий |
|
|
|
|
красное |
ок- |
||
(кроме |
цинкового и |
сталь |
1 |
3 |
рашивание |
||||
кадмиевого) |
|
|
|
|
|
|
|
||
То же |
|
|
медь и ее |
3 |
1 |
красное |
ок- |
||
|
|
сплавы |
рашивание |
||||||
|
|
|
|
|
|||||
Все виды |
покрытий |
|
|
|
|
|
|
||
(кроме |
цинкового, |
|
|
|
|
|
|
||
кадмиевого, |
оловян- |
|
|
|
|
|
|
||
ного, никелевого, по- |
медь и ее |
|
|
красно- |
|
||||
лученного |
химиче- |
2 |
5 |
коричневое |
|||||
сплавы |
|||||||||
ским способом, и по- |
|
|
окрашивание |
||||||
|
|
|
|
||||||
крытий |
|
сплавами |
|
|
|
|
|
|
|
олово свинец (оло- |
|
|
|
|
|
|
|||
во висмут) |
|
|
|
|
|
|
|
||
|
|
|
цинк |
и |
|
|
розово- |
|
|
Все виды покрытий |
его |
спла- |
4 |
5 |
лиловое |
ок- |
|||
|
|
|
вы |
|
|
|
рашивание |
||
То же |
|
|
алюминии |
5 |
5 |
розовое |
ок- |
||
|
|
и сплавы |
рашивание |
||||||
|
|
|
|
|
|||||
|
|
|
|
15 |
|
|
|
Золотое, палладиевое |
|
|
|
|
(и их сплавы), хромо- |
никель и |
6 |
|
|
вое |
|
|
красное ок- |
|
его спла- |
|
10 |
||
|
|
рашивание |
||
Серебряное, золотое, |
|
|||
вы |
|
|
||
палладиевое (и их |
7 |
|
|
|
|
|
|
||
сплавы), хромовое |
|
|
|
|
Перед испытанием детали обезжиривают спиртом или пастой из окиси магния. После обезжиривания пастой детали промывают дистиллированной водой и высушивают фильтровальной бумагой или сжатым воздухом. Затем на поверхность покрытия наносят слой инди-
каторной пасты из расчета 50 120г/см2. Пасту наносят волосяной кистью, пульверизатором, погружением или другим способом, обеспечивающим нанесение равномерного слоя пасты. После выдержки в течение времени, указанного в табл. 1, рассчитывают среднее число пор по формуле (1).
Таблица 2 – Составы паст для проверки пористости гальванических покрытий
Металл |
Покрытия |
Компоненты пасты |
Цвет со- |
|
основы |
единения |
|||
|
|
|||
|
|
а, а-дипиридил или о- |
|
|
Сталь |
Любое |
фенантролин, соляная ки- |
Красный |
|
|
|
слота, двуокись титана |
|
|
|
Любое, |
Дифенилкарбазид, кислота |
|
|
Медь и ее |
уксусная, аммоний надсер- |
Красно- |
||
кроме Zn |
||||
сплавы |
нокислый, глицерин, дву- |
коричневый |
||
и Cd |
||||
|
окись титана |
|
||
|
|
|
||
|
|
Дифенилтиокарбазид, ще- |
Розово- |
|
Цинк и его |
|
лочь, пропиловый или эти- |
||
Любое |
лиловый |
|||
сплавы |
ловый спирт, двуокись ти- |
|||
|
|
|||
|
|
тана |
|
|
Медь и ее |
Оловянное |
Кадион II, аммоний, аммиак, |
|
|
сплавы |
двуокись титана |
Красный |
||
|
||||
Алюминий и |
Любое |
Алюминон |
||
|
||||
его сплавы |
|
|
||
|
|
|
||
|
|
16 |
|
Приготовление индикаторных паст
Паста 1. ,-дипиридил растворяют в 0,1 н. растворе HCl из расчета 1 г на 100 мл HCl. Полученный раствор смешивают с пропиловым спиртом (отношение объемов раствора и пропилового спирта 4:1). Двуокись титана TiO2 перемешивают с полученной смесью из расчета 12 20 г TiO2 на 10 мл смеси до получения кашицеобразной массы. Полученная паста пригодна к употреблению в течение двухтрех недель.
Паста 2. Готовят смесь этилового и пропилового спирта (соотношение 1:1). В 100 мл полученной смеси растворяют 1 г дифенилкарбазида. Отдельно растворяют в 100 мл воды 5 г уксуснокислого аммония и 5 г азотнокислого натрия. Полученные водный и спиртовой растворы смешивают в соотношении 1:1. К полученной водноспирто-
вой смеси добавляют двуокись титана (из расчета 10 15 г TiO2 на 10 мл смеси растворов) и перемешивают до получения однородной массы. Паста пригодна к употреблению в течение двух суток.
Паста 3. В 100 мл воды растворяют 2 г кадиона II (динатриевая соль паранитродиазоаминоазобензолдисульфокислоты). Отдельно растворяют 10 г надсернокислого аммония в 70 мл воды, добавляют 10 мл раствора аммиака (ρ=910 кг/м3), разбавляют водой до 100 мл и перемешивают. Аммиачный раствор и раствор кадиона II смешивают в соотношении 1:1. К четырем объемам полученной смеси добавляют один объем пропилового спирта и перемешивают. К полученной сме-
си добавляют TiO2 из расчета 12 15 г на 10 мл смеси. Паста пригодна к употреблению в течение двух суток.
Паста 4. В 100 мл смеси этилового и пропилового спиртов (в соотношении 1:1) растворяют 0,5 г дифенилкарбазида и добавляют TiO2 (из расчета 20 30г на 10 мл раствора дифенилкарбазида) и хорошо перемешивают. К полученной смеси добавляют 0,5 н. NaОН (двукратное количество по отношению к взятому количеству раствора дифенилкарбазида в смеси спиртов). Смесь тщательно перемешивают и используют в течение двух-трех суток.
Паста 5. 2 г алюминона (аммониевая соль ауринтрикарболовой кислоты) растворяют в 100 мл воды и добавляют пропиловый спирт в соотношении 3:1. На каждые 10 мл полученного водноспиртового рас-
твора алюминона добавляют 25 35 г TiO2 и перемешивают. К полученной смеси добавляют 20 25%-ный раствор перекиси водорода
17
(в количестве, составляющем половину взятого количества водноспиртового раствора алюминона, т. е. на каждые 10 мл водноспирто-
вого раствора алюминона 5 мл раствора перекиси водорода). Смесь тщательно перемешивают. Паста пригодна к употреблению в течение
2 3 ч.
Паста 6. Диметилглиоксим и кристаллический йод растворяют в смеси этилового и пропилового спирта (взятых в соотношении 3:11) из расчета 1 г диметилглиоксима и 1 г йода на 100 мл раствора (раствор 1). Азотнокислый натрий растворяют в воде из расчета 10 г на 100 мл раствора (раствор 2). Растворы 1 и 2 смешивают в соотношении 1:1. Двуокись титана замешивают на смеси растворов 1 и 2 из рас-
чета 10 15 г TiO2 на 10 мл смеси растворов. Паста пригодна к употреблению в течение двух, суток.
Паста 7. Диметилглиоксим растворяют в смеси этилового и пропилового спирта (взятых в соотношении 3:1), из расчета 1 г диметилглиоксима на 100 мл раствора (раствор 1). Азотнокислый натрий и углекислый аммоний растворяют в воде из расчета 5 г каждого из компонентов на 100 мл раствора (раствор 2). Растворы 1 и 2 смешивают в соотношении 1:1.
Двуокись титана замешивают на смеси растворов 1 и 2 из расчета 10 15 г TiO2 на 100 мл смеси растворов. Паста пригодна к употреблению в течение двух суток.
2.3. Электрохимический метод
Применим для контроля пористости хромовых и никелевых покрытий. Определение пористости хромовых покрытий основано на электрохимическом осаждении меди на основе или подслое в местах пор и трещин покрытия. В состав электролита для осаждения меди входят медь сернокислая (200 г/л) и серная кислота 20 г/л. Катодная
плотность тока при испытании 0,3 А/дм2, температура 18 20С. Продолжительность обработки более 1 мин, загрузку проводят под током. Если пористость определяют через некоторое время после покрытия, то перед испытанием деталь обрабатывают в растворе HNO3 (10 20г/л) при температуре 95С в течение 4 мин. Наличие пор и трещин в покрытии определяют при отраженном свете под микроскопом.
18
Метод определения пористости никелевого покрытия, в том числе полученного химическим способом, на алюминии и его сплавах основан на анодной обработке в электролите, содержащем 0,4 г/л алюминона, 0,2 г/л натрия углекислого (безводного). Водородный показатель раствора рН=8...8,5. Анодная плотность тока 0,6 А/дм2, темпера-
тура 18 30°С; время выдержки 1,5 мин. Катоды свинцовые. В местах пор появляется красное окрашивание. Среднее число пор рассчитывают по формуле (1).
Лабораторная работа 1 Определение толщины никелевого покрытия капельным методом
Цель работы: ознакомиться с методиками определения толщин слоя покрытия и освоить капельный метод для определения толщины покрытия образцов. Экспериментально капельным методом определить толщину никелевого покрытия.
Порядок выполнения: участок поверхности изделия, на котором определяют толщину покрытия, предварительно тщательно обезжиривают венской известью, окисью магния или органическим растворителем, промывают водой и сушат фильтровальной бумаги.
Детали с верхним никелевым слоем для снятия пассивной пленки после обезжиривания протирают ватой, смоченной раствором соляной кислоты (1:1), промывают водой, сушат.
Для снятия пассивной или фосфатной пленки пассированные (хромированные), оцинкованные и кадмированные или фосфатированные оцинкованные детали перед испытанием быстро протирают ватным тампоном, обернутым марлей и смоченной раствором соляной кислоты (1:8), промывают водой и просушивают.
Определение толщины лучше проводить до пассивации и фосфатирования. Далее на поверхность наносят одну каплю соответствующего раствора (таблица) и выдерживают ее в течение определенного времени, по истечению которого каплю удаляют фильтровальной бумагой или ватой, насухо вытирают и на тоже место наносят следующую каплю. Нанесение капель продолжается до обнажения основного
19
покрытия, что устанавливается по изменению окраски в месте нанесения капель.
Местную толщину покрытия (мкм) определяют по формуле
НМ = НК ( n – 0,5),
где НК – толщина покрытия, снимаемая одной каплей раствора в течении заданного времени; n – число капель, израсходованных на растворение покрытия до основы или подслоя.
Оформление работы:
1.Экспериментальная часть.
2.Обсуждение результатов. Проанализировать и описать каждый образец с металлическим покрытием.
3.Выводы. Практические рекомендации.
Лабораторная работа 2 Определение пористости никелевого покрытия методом
наложения
Цель работы: ознакомиться с методиками определения пористости слоя покрытия и освоить метод наложения фильтровальной бумаги для определения пористости покрытия образцов. Определить пористость никелевого покрытия.
Порядок выполнения: Деталь предварительно обезжиривают спиртом или пастой из окиси магния, затем промывают дистиллированной водой и сушат фильтровальной бумагой или сжатым воздухом. На подготовленную деталь накладывают фильтровальную бумагу, пропитанную соответствующим раствором таким образом, чтобы между поверхностью детали и бумагой не оставалось пузырьков воздуха. После выдержки в течение времени указанного в табл. 2, бумагу с отпечатками пор в виде точек или пятен снимают с детали, промывают струей дистиллированной воды и просушивают на чистом стекле. При наличии пор, доходящих до основы металла на фильтровальной бума-
20