
новая папка 1 / 241569
.pdfопределяется соответствующим комплектом шестерен однопарной гитары a/b, можно использовать шесть ступеней частот вращения для каждой позиции револьверной головки (три левых и три правых). Предварительную установку требуемой частоты вращения для каждой позиции револьверной головки осуществляют соответствующими трехпозиционными переключателями на пульте управления, встроенном в основание станка.
Движения подач револьверного и поперечных суппортов осуществляются от дисковых кулачков 8 и 12, 13, 14, которые устанавливаются соответственно на поперечном и продольном распределительных валах. При вращении кулачков рычажно-реечные передачи сообщают суппортам движение подачи, пара-
метры которого определяются профилем рабочих участков кулачков и частотой вращения распределительного вала. Поэтому изготовление каждой конкретной детали на станке требует применения специального комплекта кулачков.
Поворот револьверной головки РГ осуществляется при воздействии на приводной рычаг переставных кулачков на барабане 16. При этом срабатывает правая часть однооборотной кулачковой муфты М2 вспомогательного вала и получает вращение шестерня Z57. От неё через шестерни Z76, Z38, пару конических зубчатых колёс Z23/Z46 с помощью элементов мальтийского механизма 5 и 6 осуществляется поворот револьверной головки. Перед её поворотом посредством кривошипно-шатунного механизма происходит быстрый отвод суп-
порта и расфиксация револьверной головки, а в конце поворота выполняется фиксация РГ и быстрый подвод револьверного суппорта.
Подача и зажим прутка осуществляются при воздействии на приводной рычаг переставного кулачка на левом торце барабана 15. При этом включается левая часть однооборотной муфты М2 и получает вращение от шестерен Z36 и
Z72 промежуточный вал VIII с установленными на нём цилиндрическими кулачками 2 и 3. Кулачки 2 и 3 через рычажные системы обеспечивают соответственно подачу прутка и работу механизма разжима-зажима прутка.
Указания по расчёту настройки станка
Расчёт настройки станка производят в соответствии с этапами: 1. Разработка технологического процесса
Выбирают заготовку. Распределяют процесс обработки детали по переходам. При этом определяют, какими инструментами будет обрабатываться де-
таль и какие стандартные и специальные державки нужно применить. Вычерчивают в таблице операционной технологической карты (см. при-
ложение 2) эскизы переходов в соответствии с принятой технологической последовательностью с указанием номера и наименования перехода.
2.Определение расстояния L от торца шпинделя до револьверной головки
вконце каждого перехода
Расстояние L складывается из расстояния от торца шпинделя до отрезного резца (принимается 5…7 мм); ширины отрезного резца; части длины детали от плоскости отрезки до режущей кромки инструмента; расстояния от режущей кромки инструмента до револьверной головки. Минимальное значение Lmin ре-
гулируемое и для станка 1Б136 может быть в пределах Lmin = 64…100 мм.
3.Выбор режимов резания
Сучетом технологических особенностей обработки детали по нормативам режимов резания (см. табл. 1) для каждого перехода принимают значения подачи S (мм/об) и скорости резания V′ (м/мин). При совмещенной работе ин-
струментов одного суппорта в качестве подачи принимается меньшая величина. 4.Определение частоты вращения шпинделя
Ориентировочное значение частоты вращения шпинделя ni′шп (мин-1) для каждого перехода рассчитывается по формуле
ni шп |
|
1000V |
, |
|
D |
||||
|
|
|
где D – наибольший диаметр обрабатываемой поверхности, мм.
При совмещении работы группы инструментов выявляют лимитирующий инструмент, работающий с наименьшей частотой, которую и принимают в качестве общей для всей группы.
По таблице частот вращения шпинделя (см. табл. 1.2) выбирают обеспечиваемые приводом значения ni шп ближайшие расчётным и определяют соответствующие сменные колеса a, b однопарной гитары скоростей.
|
С учетом принятых значений ni шп определяют действительные значения |
|||||||
скорости резания V для каждого перехода. |
||||||||
|
5. Определение длины рабочего хода инструмента Lрх , мм |
|||||||
|
Для каждого инструмента длина рабочего хода определяется по формуле |
|||||||
|
Lрх Lрез Lпод Lпер , |
|||||||
где |
Lрез – длина обрабатываемого участка, Lпод – длина подвода (0,5…2 мм), |
|||||||
Lпер – перебег инструмента (принимается для отрезных резцов Lпер =1,5 мм). |
||||||||
|
При сверлении необходимо учитывать высоту конуса сверла. При совме- |
|||||||
щении работы инструментов расчет Lрх ведут для инструмента с наибольшим |
||||||||
рабочим ходом. |
|
|
|
|
|
|
|
|
|
6. Определение количества оборотов шпинделя за время выполнения |
|||||||
каждого перехода и суммарного числа оборотов |
||||||||
|
Количество оборотов шпинделя на переход Пp (шт) при частоте вращения |
|||||||
nшп и подаче S определяется по формуле |
|
|
|
|
||||
|
|
П |
|
|
Lрх |
. |
|
|
|
|
р |
|
|||||
|
|
|
|
|
S |
|||
|
|
|
|
|
|
|||
|
Приведенное количество оборотов Ппр шпинделя за время выполнения |
|||||||
каждого перехода определяется по формуле |
||||||||
|
П |
|
|
Пp nосн |
, |
|||
|
пр |
|
||||||
|
|
|
|
|
nшп |
|||
|
|
|
|
|
|
|||
где |
nосн – максимальная или часто используемая частота вращения при выпол- |
|||||||
нении переходов, мин-1. |
|
|
|
|
|
|
|
Суммарное количество оборотов ΣПпр определяется как сумма чисел оборотов для несовмещённых переходов.
7. Определение ориентировочного времени цикла Тср, с Ориентировочное время цикла определяется по формуле
Tор To Txх ,

где To 60 Ппр – время для выполнения рабочих ходов, Тхх – расчетное вре-
nосн
мя для выполнения всех вспомогательных движений складывается из времени подачи прутка (1 с), поворотов револьверной головки (поворот 1 с), реверса шпинделя (0,5 с), переключения частоты вращения (0,25 с), пауз (1,5 с), отвод отрезного резца (3% от То).
8. Определение радиусов кулачка револьверного суппорта
Для перехода с Lmin конечный радиус кулачка Rк = Rmax =120 мм.
Если 64 мм ≤ Lmin≤ 100 мм, то конечный радиус кулачка для остальных переходов рассчитывается по формуле
RK Rmax (L Lmin ) ,
где L – расстояние от торца шпинделя до револьверной головки в конце соответствующего перехода.
При Lmin ≥ 100 мм
RK Rmax (L 100) .
Начальные радиусы рассчитываются по формуле
Rн Rк Lрх .
Для перехода «Подача прутка» RК = RН и равны RН следующего перехода. Для перехода «Нарезка резьбы» принимается RК = RН + 0,85Lрх.
Радиус участка холостого хода должен быть на 1…2 мм меньше RН. 9. Определение радиусов кулачков поперечных суппортов
Наибольший радиус кулачка Rmax = 75 мм соответствует положению лезвия режущего инструмента на оси заготовки. Конечный радиус кулачка определяется по формуле
RK Rmax r ,
где r – радиус обработанной поверхности на данном переходе, мм
10. Определение числа сотых кулачков для вспомогательных ходов Так как кулачок имеет всего 100 делений (сотых), то движениям продол-
жительностью 1с соответствует 100:Tор сотых кулачка. Следовательно, число

сотых Mi хх для выполнения вспомогательного хода определяется по формуле
Mi xx Ti xx 100 ,
Toр
где – время выполнения вспомогательного хода, с.
С учетом Tор и значений радиусов кулачка по табл. 1.3 и табл. 1.4 определяется и принимается наибольшее значение необходимого количества сотых Mi рг для каждого поворота револьверной головки.
Суммарное число сотых, приходящихся на несовмещённые холостые ходы, определяется по формуле
Mхх Mi хх Mi рг .
11. Определение числа сотых кулачков для осуществления рабочих ходов Суммарное число сотых, приходящихся на несовмещенные рабочие ходы
определяется по формуле
Mp 100 Mхх .
Число сотых на отдельный рабочий ход определяется по формуле
M Ппр |
Mр |
. |
|
П |
пр |
||
|
|
|
С учетом М определяют порядковые номера делений, соответствующие началу и концу каждого перехода.
Количество оборотов шпинделя за время обработки детали равно
Пдет Ппр 100 .
Mр
12. Определение продолжительности цикла Предварительное время цикла обработки рассчитывается по формуле
|
|
60Пдет |
. |
Tоп |
nосн |
||
|
|
|
По табл. 1.5 уточняется время цикла и окончательно принимаются значение Топ и соответствующий комплект сменных зубчатых колес – c, d, e, f.
13. Определение цикловой Qц (шт/мин) производительности автомата Цикловую производительность автомата рассчитывают по формуле

QЦ Tlоп 60 .
14. Вычерчивание кулачков Кулачки вычерчивают согласно данным операционной технологической
карты и таблицы размеров кулачков. Профили холостых ходов выполняются по шаблонам в зависимости от времени изготовления детали.
Последовательность выполнения наладки станка
1.Ознакомиться с операционной технологической картой и изучить технологический процесс.
2.Подобрать соответствующий пруток, необходимые режущие инструменты, инструментальные державки, кулачки, сменные шестерни, приспособ-
ления и другую оснастку.
3.Установить подающую и зажимную цанги и отрегулировать величину подачи и силу зажима прутка.
4.Согласно карте наладки установить сменные шестерни коробки скоростей a и b и привода вращения распределительных валов c, d, e, f.
5.Согласно технологической карте и таблице станка для каждой позиции револьверной головки установить тумблеры пульта управления частотой вращения шпинделя в соответствующие положения А, Б, В.
6.Установить и закрепить на поперечном распределительном валу кулачок револьверного суппорта, учитывая направление его вращения.
7.На продольном распределительном валу установить кулачки поперечных суппортов.
8.Согласно технологической карте устанавливают напротив соответствующих делений на барабанах 15 и 16 (см. рис.) командные кулачки подачи и зажима прутка, переключения револьверной головки и лотка для сбора готовых деталей.
9.Вращая вручную распределительный вал, добиться срабатывания механизма подачи и зажима прутка. Поворотом револьверной головки установить
врабочую позицию гнездо 1. Установить командоаппарат в позицию 1.
10.Включить вращения шпинделя и вспомогательного вала и проверить правильность срабатывания механизмов в цикле работы станка.
11.Установить в гнёзда револьверной головки соответствующие инструменты и отрегулировать их положения в соответствии с установочными разме-
рами, указанными на эскизах технологической карты. Установочные расстояния для каждого перехода указаны при крайнем левом положении револьверного суппорта.
12.Проверить правильность наладки инструментов при ручном вращении распределительного вала. Установить в нужные положения кулачки реверса шпинделя.
13.Вставить пруток, включить вращение шпинделя и, вращая вручную распределительный вал, произвести обработку пробной детали.
14.По результатам контроля детали выполнить подналадку станка.
15.Произвести обработку нескольких деталей в автоматическом режиме.
Указания по технике безопасности
1. К лабораторной работе допускаются студенты, прошедшие общий и инструктаж по технике безопасности и инструктаж на рабочем месте.
2. Выполнять наладку станка разрешается только после изучения его кон - струкции и методики проведения работ, получив предварительно разрешение у преподавателя.
3. Выполнять работу разрешается только на исправном оборудовании. При отказе станка продолжение работы и самостоятельное устранение неисправности запрещено.
4. Запрещается выполнение всех видов подналадочных работ при работа - ющем оборудовании.
5. Запрещается выполнение контрольных измерений при работе станка.
Указания по оформлению отчета
Отчет представляется в письменном виде и должен содержать:
-титульный лист;
-операционную технологическую карту по форме, приведенной в приложении 2;
-результаты контроля обработанных деталей;
-выводы.
Контрольные вопросы
1.В каких типах производств целесообразно применять станок 1Б136?
2.Дайте характеристику системе управления станка 1Б136.
3.С учетом какого условия настраивается частота вращения распределительного вала?
4.Какой способ регулирования скорости применяется в приводе главного движения станка 1Б136?
5. Назовите механизмы, обеспечивающие функционирование станка в автоматическом режиме.
Библиографический список
1. Камышный, Н.И. Конструкции и наладка токарных автоматов и полу-
автоматов [Текст] / Н.И. Камышный, В.С. Стародубов. М.: Высшая школа, 1988
–256 с.
2.Фомин, С.Ф. Наладка одношпиндельных токарных автоматов [Текст] / С.Ф. Фомин. – М.: Машиностроение, 1986. – 236 с.
3.Батов, В.П. Токарные автоматы и полуавтоматы [Текст] / В.П. Батов. –
М.: Машиностроение, 1982. – 192 с.
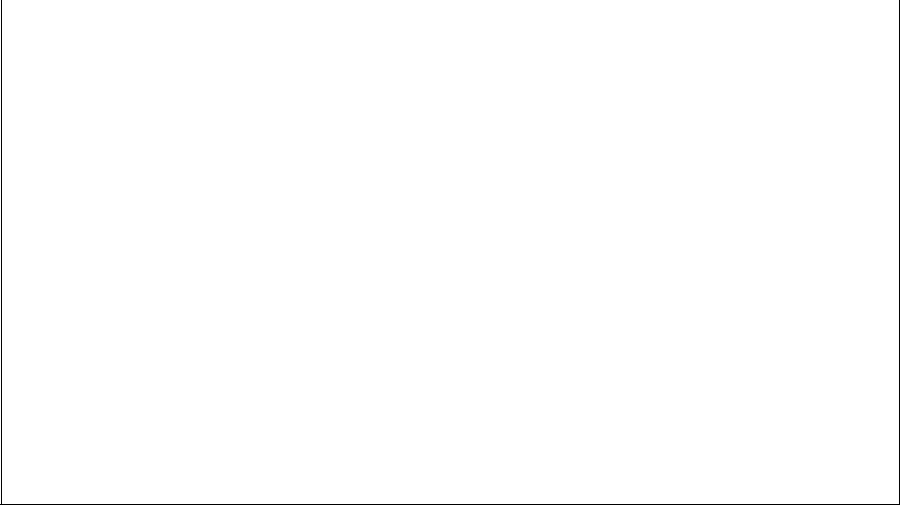
Приложение 1
|
|
|
|
|
Таблица 1.1 |
||
Подачи и скорости резания при применении инструмента из быстрорежущей стали |
|
||||||
|
|
|
|
|
|
|
|
|
|
Виды обработки |
|
|
|
||
|
|
|
|
|
|
|
|
Обрабатываемый материал |
|
|
|
Нарезание резьбы |
|||
Продольная |
Фасонная об- |
Сверление, |
метчиками при шаге |
||||
|
|||||||
|
обточка |
точка и отрезка |
центровка |
|
P (мм) |
|
|
|
|
|
|
|
|
|
|
|
|
|
|
1 |
1,5 |
1,75 |
|
|
|
|
|
|
|
|
|
Сталь 20 |
0,05…0,18 |
0,02…0,05 |
0,04…0,14 |
1 |
1,5 |
1,75 |
|
|
45…55 |
30…40 |
40…50 |
5,2 |
7,2 |
10.0 |
|
|
|
|
|
|
|
|
|
Сталь 45 |
0,05…0,15 |
0,015…0,04 |
0,03…0,1 |
1 |
1,5 |
1,75 |
|
|
35…50 |
30…40 |
25…35 |
3,9 |
4,9 |
7,0 |
|
|
|
|
|
|
|
|
|
Автоматная сталь 12 |
0,06…0,2 |
0,04…0,15 |
0,10…0,35 |
1 |
1,5 |
1,75 |
|
|
45…70 |
45…55 |
45…50 |
8,4 |
8,8 |
12,6 |
|
|
|
|
|
|
|
|
|
Латунь |
0,1…0,22 |
0,02…0,1 |
0,08…0,25 |
1 |
1,5 |
1,75 |
|
|
70…150 |
70…150 |
50…100 |
12,3 |
17,5 |
20,0 |
|
|
|
|
|
|
|
|
|
Алюминий |
0,1…0,22 |
0,02...0,08 |
0,03…0,18 |
1 |
1,5 |
1,75 |
|
|
200…250 |
200…250 |
150…200 |
14,5 |
19,5 |
22,5 |
|
|
|
|
|
|
|
|
Примечание: 1. В верхней строке указаны значения подач S (мм/об), в нижней – значения скоростей резания
V′ (м/мин).
2. При работе твердосплавным инструментом скорости резания увеличиваются в 2…3 раза
Таблица 1.2 Частоты вращения шпинделя, обеспечиваемые приводом
Гитара скоростей |
Частоты вращения шпинделя nшп, мин-1 |
|||||
a |
b |
при левом вращении |
при правом вращении |
|||
|
|
|
|
|||
50 |
45 |
2500, 630, 1250 |
1000, 250, 500 |
|||
|
|
|
|
|||
45 |
50 |
2000, 500, 1000 |
800, 200, 400 |
|||
|
|
|
|
|||
39 |
56 |
1600, 400, 800 |
630, 160, 315 |
|||
|
|
|
|
|||
34 |
61 |
1250, 315, 630 |
500, 125, 250 |
|||
|
|
|
|
|||
29 |
66 |
1000, 250, 500 |
400, 100, 200 |
|||
|
|
|
|
|
|
|
25 |
70 |
800, |
200, 400 |
315, |
80, |
160 |
|
|
|
|
|
|
|
21 |
74 |
630, |
160, 315 |
250, |
64, 125 |
|
|
|
|
|
|
|
|
Таблица 1.3 Число сотых для поворота револьверной головки с учётом цикла обработки
Ориентировочное время цикла Тор, с |
Число сотых |
11,6 |
6,0 |
|
|
13,0 |
5,5 |
|
|
14,6 |
5,0 |
|
|
16,6 |
4,5 |
|
|
18,2 |
4,0 |
|
|
20,3 |
3,5 |
|
|
22,9…25,7 |
3,0 |
|
|
27,5…32,8 |
2,5 |
|
|
34,3…40,6 |
2,0 |
|
|
43,2…61,0 |
1,5 |
|
|
Свыше 61 |
1,0 |
|
|
Таблица 1.4 Число сотых для поворота револьверной головки с учётом радиуса кулачка
Радиус кулачка,мм |
Число сотых |
Радиус кулачка, мм |
Число сотых |
|
|
|
|
40 |
6,5 |
80 |
4,0 |
|
|
|
|
45 |
6,0 |
85 |
3,5 |
|
|
|
|
50 |
5,5 |
90 |
3,5 |
|
|
|
|
55 |
5,0 |
95 |
3,5 |
|
|
|
|
60 |
4,5 |
100 |
3,0 |
|
|
|
|
65 |
4,5 |
105 |
3,0 |
|
|
|
|
70 |
4,5 |
110 |
3,0 |
|
|
|
|
75 |
4,0 |
115 |
2,5 |
|
|
|
|