
книги / Наукоемкие химические технологии
..pdfного сероводородсодержащего газа блока вакуумной перегонки мазута. Установка по производству серной кислоты является экологически направленным производством. Расчетная производительность установки по серной кислоте составляет 65 тыс. т/год, по сырью (H2S) – 24 тыс. т/год.
Сырьем установки по производству серной кислоты является сероводородсодержащий газ установок гидроочистки и ГФУ и влажный сероводородсодержащий газ с блока вакуумной перегонки мазута установки ЛВТ-5.
Усредненный состав сероводородсодержащего газа гидроочистки и ГФУ, об. %:
H2S – 95,00; Н2 – 3,78; СН4 – 0,84;
С2Н6 – 0,21; С3Н8 – 0,16; С4Н10 – 0,01.
Молекулярная масса – 32,6.
Состав влажного сероводородсодержашего газа, мас. %:
H2S – 22;
NH3 – 62;
Н2О – 16.
Плотность – 1,52 кг/м3.
Молекулярная масса – 19,3.
Основным продуктом установки является товарная серная кислота с концентрацией 98 мас. % (ГОСТ 2184–77). Концентрированная серная кислота (H2SO4) – маслянистая, прозрачная, бесцветная, токсичная невзрывоопасная жидкость.
Состав, мас. %:
H2SО4 – 98; Н2О – 2.
Молекулярная масса – 98. Плотность – 1834 кг/м3.
21
Температура кипения – 330 °С. Температура плавления – 10,35 °С.
Побочным продуктом установки является отработанный чистый технологический газ состава, об. %: О2 – 12,66; Н2О –
2,21; N2 + Ar – 84,98; СО2 – 0,11; SO2 – 0,04; SО3 10 ppm.
В качестве катализатора реакции окисления сернистого ангидрида в серный ангидрид на установке применяется ванадиевый катализатор VK-WSA фирмы «Хальдор Топсе» (нанесенная пятиокись ванадия – V2O5). Внешний вид – кольца до 10 мм. Температура реакции окисления – более 360 °С; максимальная температура – 630 °С. Российский аналог ИК-1-6 (ТУ-113-08-615–87). Материал катализатора содержит растворимые соли, которые при контакте с водой могут перейти в раствор, поэтому катализатор нельзя подвергать воздействию влаги. Катализаторы на основе пятиокиси ванадия не горючи.
Производство серной кислоты из сероводорода методом «мокрого» катализа состоит из 3 основных стадий:
– сжигание сероводорода в воздухе с получением диоксида серы по реакции
H2S + 1,5О2 = SО2 + H2O;
– окисление диоксида серы в триоксид серы по реакции
SО2 + 0,5О2 = SО3;
– получение серной кислоты в результате взаимодействия по реакции
SО3+ Н2О = H2SО4.
Технологическая схема производства серной кислоты из сероводородсодержащего газа (рис. 5)
Сероводород и влажный сероводород, поступая на установку, объединяются в сепараторе сероводорода В-207, в котором отделяется конденсат воды. Объединенный газовый поток направляется на сжигание в котлы-утилизаторы КУ-А,
22
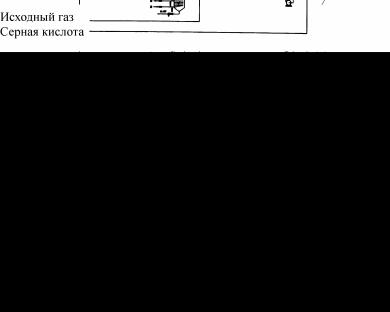
В, С (2 работающих и 1 резервный). При пуске установки для разогрева котлов-утилизаторов используется топливный газ из заводской линии.
Рис. 5. Технологическая схема производства серной кислоты из сероводородсодержащего газа: 1 – газосмесители; 2 – контактный аппарат; 3 – газоохладитель; 4 – конденсатор; 5 – воздуходувки; 6 – холодильник; 7 – печь сжигания с котлом-утилизатором; 8 – сепараторы
Котлы-утилизаторы состоят из циклонной топки для сжигания сероводородного сырья и котловой части для утилизации тепла технологического газа. Котловая часть, в свою очередь, состоит из следующих основных частей: конвективной поверхности разогрева котловой воды, барабанасепаратора пара и паропеpeгревающей части котла. Воздух, поступая по кожуху котла, омывает всю котельную часть, за-
23
тем проходит под кожухом циклонной гонки и вводится непосредственно в саму топку в трех точках.
Часть воздуха тангенциально вводится в топку перед пережимом, сохраняя его от преждевременного теплового раз-
рушения. Основной поток |
смешивается с сероводородом |
и тангенциально вводится |
в объем циклонной топки, где |
и поджигается. Тем самым в топке поддерживается циклонный вихрь, способствующий наиболее полному сгоранию газа. Температура технологических газов на выходе из каждого работающего котла поддерживается количеством подводимого на сжигание сероводорода и соотношением сероводород : воздух на эти же агрегаты.
Технологический газ из печного отделения с температурой 575–600°С и содержанием SO2 – 8–11 % направляется в конвертер SO2. С целью предотвращения образования кислотных паров необходимо регулировать содержание водяного пара в очищенном газе, выходящем из конденсатора WSA. Это осуществляется вводом перегретого пара в поток технологического газа до конвертера. Количество добавляемого пара зависит от климатических условий: максимальное количество добавляется в сухих зимних условиях. После ввода пара технологический газ разбавляется воздухом с целью охлаждения технологического газа до температуры реакции 410 °С и одновременно для обеспечения кислотной точки росы на входе конденсатора WSA не более 255 °С. Технологический газ, водяной пар и воздух смешиваются в газосмесителе, установленном непосредственно в трубопроводе, и однородным потоком поступают в конвертер SO2 2. В схеме предусмотрена конверсия газов на двух горизонтальных каталитических слоях в конвертере SO2 с промежуточным охлаждением газов насыщенным паром в межслойном охладителе 3. Два каталитических слоя загружены сернокислотным катализатором типа VK-WSA фирмы «Хальдор-Топсе». В первом слое катализатора температура
24
повышается с 410 °С до 520 °С. Затем газ охлаждается до 400 °С в межслойном охладителе 3, перемешивается во втором газосмесителе и поступает на второй каталитический слой. Температура газа на выходе из конвертера составляет приблизительно 407 °С.
После конвертера SО3-содержащий газ охлаждается до 290 °С насыщенным паром в газоохладителе 3. При охлаждении SO3 частично гидратируется в парообразную кислоту:
SО3 + Н2О = H2SО4(г) + 101 кдж/гмоль.
Окончательное поглощение SO3 происходит в конденсаторе WSA 4, в котором технологический газ проходит вверх в стеклянных трубах длиной 7 м (конденсатор состоит из 5 модулей по 720 труб каждый). Снаружи трубы охлаждаются потоком воздуха в режиме противотока. Каждая труба заканчивается встроенным в нее патронным фильтром для очистки от тумана кислоты. На внутренней поверхности трубы конденсируется кислота и пленкой стекает в нижнюю часть аппарата, откуда выводится в охлажденный циркуляционный поток кислоты. Конденсат кислоты в верхней части труб имеет концентрацию 70–75 % и температуру 110 °С. По мере стекания кислоты по трубе ее концентрация повышается и на выходе конденсатора составляет не менее 96 % с температурой около 250 °С. Подача воздуха в межтрубное пространство для охлаждения труб осуществляется воздуходувкой 5. Горячий воздух на выходе из WSA делится на несколько потоков. Один поток воздуходувкой 5 дожимается и подается в печи для сжигания сероводорода, другой поток воздуходувкой дожимается и смешивается с потоком технологического газа перед контактным аппаратом. Остальное количество воздуха сбрасывается в атмосферу. Отработанные чистые технологические газы после аппарата WSA через выхлопную трубу сбрасываются в атмосферу.
25
Кислотный цикл выполнен в виде кольцевой линии перекачки кислоты. Кислота с температурой 60 °С насосом подается из сборника в пластинчатый холодильник 6, где она охлаждается до 40 °С, и далее смешивается с потоком горячей кислоты (250 °С), при этом температура кислоты вновь повышается до 60 °С. С этой температурой кислота возвращается в сборник кислоты, балансовое количество серной кислоты из цикла выводится на склад.
С целью предотвращения замерзания кислоты зимой ее разбавляют питьевой водой от водяного бака до нужной концентрации. Концентрация кислоты в холодное время года обычно составляет 93–94 %.
3. Технология серы из сероводородсодержащих газов
Современные нефтеперерабатывающие заводы являются крупными производителями серы. Это связано с вовлечением
впереработку тяжелых нефтей и в большей степени с ужесточением экологических требований по ограничению содержания серы в нефтепродуктах и газовых выбросах НПЗ
ватмосферу. Производство серы процессом Клауса на базе утилизации серосодержащих газовых выбросов значительно увеличивает рентабельность нефтеперерабатывающего предприятия.
Процесс Клауса основан на окислении сероводорода в серу. Первые промышленные установки, использующие сероводородсодержащие газы, были созданы в 50-х годах XX столетия. Большое количество исследований тех лет посвящено разработке конструкционного оформления и анализу технологических параметров работы каталитических ступеней установок Клауса. В 70–80-е годы были разработаны процессы переработки низкоконцентрированных сероводородсодержащих газов и обессеривания «хвостовых» газов установок по переработке нефти.
26
В последующие годы наряду с разработками стабильных катализаторов были созданы новые каталитические процессы проведения реакции Клауса: процесс селективного окисления и разложения сероводорода с получением серы и водорода.
Однако следует заметить, что ни один из новых методов получения серы не доведен до такой степени совершенства, как классический процесс Клауса, на который ориентируется большинство нефтепереработчиков, о чем свидетельствуют вновь строящиеся установки.
Кконцу 80-х годов мировое производство серы из газа,
восновном нефтеперерабатывающими заводами, оценивалось почти в 60 млн т/год. Выработка серы на современном этапе развития нефтеперерабатывающей промышленности за
счет более глубокой степени обессеривания нефтепродуктов составляет 5,1 кг/м3 нефти.
Утилизация серы из перерабатываемой нефти имеет огромное природоохранное значение.
В отечественной промышленности до 85 % получаемой серы идет на производство серной кислоты. Наиболее высокие технико-экономические показатели имеют установки получения серной кислоты на основе «газовой» серы, получаемой из сероводорода методом Клауса. Важным потребителем серной кислоты, полученной на основе серы процесса Клауса, является производство минеральных удобрений, особенно азотных и фосфорных. Сера используется, так же как фунгицид, в борьбе с вредителями сельского хозяйства (при выращивании картофеля, винограда, хлопчатника), а также в производстве некоторых гербицидов. Большое применение сера и ее соединения находят в целлюлозно-бумажной промышленности для получения целлюлозы, в химической – для получения волокон, сероуглерода, хлорида серы, в производ-
стве красителей, в резинотехнической промышленности в качестве вулканизирующего агента, а также в радиоэлектронике.
27
3.1. Теоретические основы процесса
Основные реакции. Процесс получения серы из сероводородсодержащих (кислых) газов был разработан лондонским химиком Карлом Фридрихом Клаусом в 1883 году. До современного аппаратурного оформления процесс был доведен в концерне «И.Г. Фарбен-индустри», Германия. Процесс включает несколько стадий: термическую и две-три каталитические.
Поступающий на установку Клауса кислый газ подвергается высокотемпературному (900–1300 °С) сжиганию в свободном пламени в присутствии стехиометрического количества воздуха с получением элементарной серы (выход до 70 %) и диоксида серы в соответствии с уравнениями:
3H2S + 1,5О2 3Н2О + 3Sх; Н = –622,8 кДж/моль; H2S + 1,5О2 Н2О + SO2; Н = –518,3 кДж/моль.
Диоксид серы взаимодействует с непрореагировавшим сероводородом с образованием серы:
2H2S + SO2 2Н2О + 3/х Sх; Н = –104,5 кДж/моль.
Реакция идет частично на термической стадии при охлаждении газового потока, но в большем объеме — на стадии каталитического окисления.
Подача воздуха в камеру сгорания ведется с таким расчетом, чтобы на выходе из печи соотношение H2S:SO2 составляло 2:1 (в соответствии с последующей реакцией каталитического окисления сероводорода диоксидом серы). Содержание кислорода в отходящих газах должно быть сведено к минимуму, так как его наличие способствует сульфатации катализатора на основе оксида алюминия.
На всех стадиях процесса степень превращения сероводорода стремятся довести до состояния термодинамического равновесия. На рис. 6 приведена зависимость равновесной
28
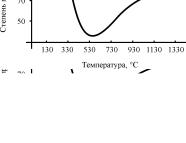
степени |
превращения серо- |
|
|
||||
водорода |
в |
элементарную |
|
|
|||
серу |
от |
температуры |
при |
|
|
||
окислении его воздухом, взя- |
|
|
|||||
тым |
в |
стехиометрическом |
|
|
|||
соотношении. |
|
|
|
|
|||
В процессе Клауса ре- |
|
|
|||||
акции |
протекают в |
трех |
|
|
|||
Рис. 6. Температурная зависи- |
|||||||
зонах: |
1 |
– высокотемпера- |
|||||
турная (выше |
800 °С), |
где |
мость равновесной степени пре- |
||||
превращение H2S в серу дос- |
вращения H2S в парообразную |
||||||
тигает 70–80 % и возрастает |
|
элементарную серу |
|||||
|
|
с повышением температуры, так как сероводород начинает разлагаться на элементы; 2 – переходная зона, в которой снижение выхода серы при температуре 530–730 °С обусловливается ассоциацией серы вида S2 в более высокомолекулярные виды S4, S6, S8; 3 – низкотемпературная каталитическая зона, в которой снижение температуры повышает степень конверсии.
Реакции в пламени ведут к превращению сероводорода
вэлементарную серу, образованию диоксида серы и разрушению примесей, которые могли бы дезактивировать катализатор. В высокотемпературной зоне пламени образуется сера
ввиде S1–2, в низкотемпературной – S3–8.
Побочные реакции. Присутствие углеводородов, диоксида углерода и других примесей в сырьевом газе резко увеличивает число потенциально возможных реакций в печи и в каталитических конверторах.
Углеводороды сгорают с образованием СО2, СО, Н2О, Н2. При высоких температурах в пламени в результате взаимодействия углеводорода с парами серы образуется сероуглерод:
СН4 + S2 CS2 + 2H2;
СН4 + 2S2 CS2 + 2H2S.
29
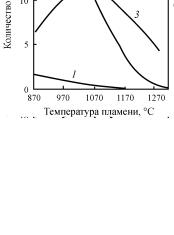
|
|
|
Свободный водород, об- |
||
|
|
|
|||
|
|
|
разовавшийся |
при |
термиче- |
|
|
|
ской диссоциации |
сероводо- |
|
|
|
|
рода, восстанавливает диоксид |
||
|
|
|
углерода до оксида, который, |
||
|
|
|
взаимодействуя с серой, обра- |
||
|
|
|
зует серооксид углерода: |
||
|
|
|
|||
|
|
|
СО + 0,5S2 COS. |
||
|
|
|
Изучение |
механизма об- |
|
|
|
|
разования сероуглерода и се- |
||
|
|
|
рооксида углерода |
показало, |
|
|
|
|
что они образуются автоном- |
||
Рис. 7. Зависимость количества |
но. Образованию сероуглеро- |
||||
образовавшихся CS2 и COS от |
да способствуют, в основном, |
||||
температуры пламени и содер- |
ароматические |
углеводороды |
|||
жания H2S в кислом газе: 1 – |
(рис. 7). Максимальное его |
||||
CS9 из метана; 2 – CS9 из аро- |
образование наблюдается при |
||||
матических углеводородов; 3 – |
температуре 1000 °С (из мета- |
||||
|
COS |
на CS2 образуется при 800 °С), |
а серооксида углерода – при 1100 °С. Повышение температуры пламени в реакционной печи до 1300 °С (при постоянном составе кислого газа) приводит к прекращению образования CS2 и снижению образования COS.
Вследствие высокого содержания водяных паров в газе, полученном на термической стадии и поступающем в каталитический конвертор, CS2 и COS в присутствии катализаторов процесса частично гидролизуются. Скорость гидролиза возрастает с повышением температуры в конверторе (так, скорость гидролиза CS2 возрастает примерно вдвое на каждые 20 °С). Температуру на выходе из первого конвертора поддерживают в пределах 320–360 °С, при этом степень превращения COS достигает 90 %, CS2 – 70–75 % (несмотря на это, потери серы в виде CS2 и COS очень ощутимы).
30