
книги / Материаловедение. Теория легирования
.pdfобразующих пакеты. Толщина рейки низкоуглеродистого мартенсита всегда меньше ширины в несколько раз.
В пакетном мартенсите между рейками реализуются границы трех типов: малоугловые (когерентные); близкие к регулярным (полукогерентные); большеугловые (некогерентные). Отношение числа большеугловых границ к малоугловым составляет от 1:5 до 1:3. Разориентировка между кристаллами в пределах одного пакета, судя по размытости рефлексов на электронограммах, не более 1–3°. В каждом пакете мартенсита рейки имеют примерно один и тот же размер, который может не зависеть от размера исходного аустенитного зерна. Внутри реек имеются дислокации нескольких систем скольжения с высокой плотностью (1010–1012 см–2), при этом двойники превращения полностью отсутствуют. Поскольку экспериментально доказано, что вклад реек в упрочнение пакетного мартенсита на 1–2 порядка превосходит вклад других структурных составляющих, то за характерный элемент структуры принята рейка мартенсита.
Преимущественное влияние на характеристики механических свойств стали оказывает реечная структура, в том числе когерентные и полукогерентные границы между рейками (влияние полукогерентных и когерентных границ рассматривается как суммарный эффект). Известно, что только 1/3 межреечных границ с малой разориентировкой являются проницаемыми для дислокаций. Проницаемые границы обеспечивают релаксацию напряжений, а непроницаемые повышают сопротивление движению дислокаций. В результате наноструктурированный низкоуглеродистый реечный мартенсит обеспечивает повышение прочности при равномерном распределении напряжений в объеме.
Таким образом, именно рейка как структурная составляющая определяет комплексхарактеристикмеханических свойств НМ.
При сдвиговом превращении из низкоуглеродистого аустенита образуется мартенсит, причем меньшему зерну аустенита соответствуют меньшие размер рейки и количество пакетов.
21
Однако свойства определяет тонкая структура, а размер зерна аустенита – это элемент, только косвенно ее характеризующий. Основной характеристикой является характерный элемент структуры, определяющий свойства, – рейка. Поэтому цель обработки состоит в получении требуемой реечной структуры с соответствующим уровнем свойств, а способ заключается в измельчении зерен аустенита, что далеко не всегда приводит к диспергированию реек. Низкоуглеродистые мартенситные стали с установленным ранее типом структурной наследственности – это одно из исключений, характерное для достаточно узкого интервала варьирования размеров зерна аустенита и реек мартенсита.
Сотрудниками кафедры был проведен эксперимент по диспергированию НМС.
Методика проведения эксперимента
Влияние температуры аустенитизации и способа охлаждения на размер зерна исследовали при нагреве от 850 до 1200 С с шагом 50 С. Выдержка при температуре аустенитизации составляла 15 мин, охлаждение проводили по режимам, представленным на рис. 8 (скорость охлаждения V1 = 600 оС/с (вода), V2 = 30 оС/с (воздух) и V3 = 0,2 оС/с (печь)).
Варьирование размеров зерен и тонкой структуры НМС осуществляли за счет применения термоциклирования с ассиметричными циклами нагрев-охлаждение. Каждый цикл термической обработки включал в себя нагрев до 950 оС, выдержку 15 мин и охлаждение до комнатной температуры, затем нагрев до 850 оС, выдержку 15 мин и охлаждение. Образцы загружали в разогретую до температуры аустенитизации лабораторную печь (ПЛ-10/12,5). На каждый режим изготавливали по 3–5 образцов каждой из двух сталей.
Структуру выявляли методом оптической микроскопии.
22
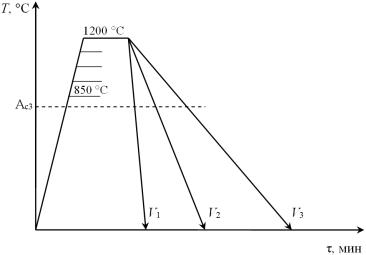
Границы зерен НМС выявляли методом окисления, изготавливая косые срезы на шлифах, обеспечивающие плавный переход структуры от окисленной поверхности до глубины 1 мм. Затем в случае необходимости шлифы протравливали насыщенным спиртовым раствором пикриновой кислоты. Для выявления микроструктуры НМС поверхность шлифа подвергали травлению 4%-ным раствором азотной кислоты в этиловом спирте.
Рис. 8. Режимы аустенитизации
Зеренную структуру порошкового магнитотвердого материала выявляли с помощью реактива Васильева, микроструктуру –
спомощью нагретого до 50–60 оС насыщенного спиртового раствора пикриновой кислоты.
Исследование микроструктуры проводили на микроскопе «Neophot-32» при увеличении до 1500 крат.
Средний размер зерна аустенита определяли в соответствии
сГОСТ5639–82 методомсекущих, используяпрограмму«Grain-size».
Врезультате эксперимента были получены следующие зависимости (табл. 3).
23
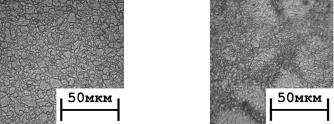
Таблица 3
Влияние термоциклирования на размер зерна аустенита
Режим термической обработки |
Размер зерна, мкм |
|||
Цикл |
Температура аустенитизации, оС |
15Х2Г2НМФБ |
07Х3ГНМ |
|
1 |
950 |
9 |
10 |
|
850 |
5 |
3 |
||
|
||||
2 |
950 |
6 |
7 |
|
850 |
4 |
3 |
||
|
||||
3 |
950 |
6 |
10 |
|
850 |
6 |
7 |
||
|
||||
4 |
950 |
6 |
10 |
Минимальные размеры зерен аустенита (примерно 3–4 мкм) были достигнуты уже после одного-двух циклов такой обработки (рис. 9). Судя по литературным данным, предельное для ТЦО измельчение размера зерна аустенита до 141/2 баллов по шкале ASTM (3–5 мкм) у мартенситных сталей ранее достигали лишь многократным циклированием с быстрымнагревом иохлаждением.
а |
б |
Рис. 9. Зерна аустенита НМС после двух циклов термообработки: а – 15Х2Г2НМФБ, б – 07Х3ГНМ
Размер зерна аустенита закономерно связан с размером реек и пакетов. При охлаждении из аустенита в низкоуглеродистых сталях образуется мартенсит с числом реек в каждом пакете от 4–6 до 12–16 и числом пакетов в зерне не менее 2–4, причем меньшему зерну аустенита соответствуют меньшие размер рейки и коли-
24
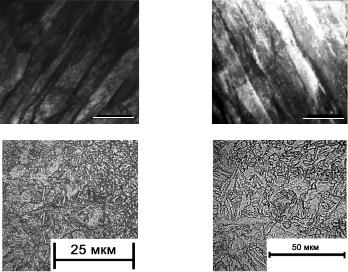
чество пакетов. Предельным случаем является (для сверхмелких зерен с диаметром порядка 1 мкм) формирование в каждом зерне по 1 пакету мартенсита. Образование в зерне аустенита реек одной ориентации возможно после закалки из расплава.
Дисперсность структуры низкоуглеродистого мартенсита не всегда является функцией размера зерна аустенита. Следует разделить интервалы содержания углерода на более чем 0,1–0,2 %, когда такая связь чаще всего существует, и менее 0,1 %, когда такую зависимость обычно не выявляют. Исследования исходного размера зерен и пакетов показали, что зерну аустенита, равному 9 мкм, соответствует размер пакета 2,5 мкм для сталей марок 15Х2Г2НМФБ и 07Х3ГНМ.
Важно отметить близкие значения средних размеров реек при равном содержании углерода (0,13 %) и одинаковой температуре аустенитизации (950 оС), полученные в результате эксперимента и приведенные в литературных источниках.
300 нм |
200 нм |
а |
б |
в |
г |
Рис. 10. Реечная (а, б) и пакетная (в, г) структуры НМС:
а, в – 15Х2Г2НМФБ; б, г – 07Х3ГНМ
25
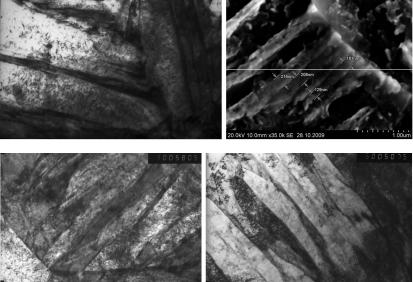
При содержании углерода 0,14–0,20 % понижение температуры аустенитизации до 850 оС приводит к уменьшению средней ширины кристаллов до 0,1 мкм. Наименьшему размеру зерна аустенита соответствует нанометрическая и субмикронная толщина реек со средним размером на уровне 0,15 мкм (рис. 10).
Однократная (1 цикл) обработка практически не повлияла на механические свойства стали.
Наиболее высокого уровня механические свойства достигли после проведения двух ассиметричных циклов перекристаллизации и отпуска на 250 оС (табл. 4). Температура отпуска выбрана
сучетом ранее проведенных исследований.
Врезультате такой обработки образуется структура с нанометрическим размером основного элемента – рейки (90 нм) (рис. 11). Следует также отметить, что фрагментация и измельчение реек и блоков происходили согласованно.
а |
б |
в |
г |
Рис. 11. Фрагментирование структуры стали 15Х2Г2НМФБ после двух циклов ТЦО: а – закалка на воздухе. 30000; б – закалка на воздухе.
35000; в – закалка в воде. 30000; г – закалка в масле. 50000
26

Таблица 4
Влияние размера характерного элемента структуры НМС 15Х2Г2НМФБ на ее механические свойства [10]
|
Режим ТО, |
Диаметр |
dср(dн.в), |
Предел прочности |
Отн. сужение |
Ударная вязкость, |
||||
|
зерна d, |
(пределтекучести) |
(отн. удлин.) |
|
МДж/м2 |
|
||||
|
среда охлаждения |
мкм (балл) |
нм |
σв (σ0,2), МПа |
ψ(δ), % |
|
|
|
|
|
|
KCU |
KCV |
|
KCT |
||||||
|
|
|
|
|
||||||
950 оС, воздух |
8 (11) |
200 |
(175) |
1440 (1110) |
55 (16) |
1,00 |
0,85 |
|
0,35 |
|
1 |
цикл, воздух |
8 (11) |
190 |
(125) |
1470 (1140) |
56 (16) |
1,20 |
1,00 |
|
0,40 |
2 |
цикла, воздух |
8 (11) |
160 |
(125) |
1470 (1250) |
55 (16) |
1,30 |
1,20 |
|
0,50 |
2 |
цикла, воздух + отпуск |
8 (11) |
|
– |
1480 (1250) |
56 (17) |
1,35 |
1,20 |
|
0,50 |
2 |
цикла, масло |
7 (11–12) |
90 |
(75) |
1530 (1250) |
56 (15) |
1,20 |
1,00 |
|
0,35 |
2 |
цикла, масло + отпуск |
7 (11–12) |
|
– |
1530 (1260) |
57 (16) |
1,20 |
1,00 |
|
0,40 |
Примечания: dср – средний размер характерного элемента; dн.в – наиболее вероятный размер характерного элемента. Цикл: нагрев на 950 оС, охлаждение; нагрев на 850 оС, охлаждение. Отпуск: выдержка 2 ч при 250 оС. Исходный размер зерна аустенита 9–10 мкм.
27
27
Фрагментированной реечной структуре образцов, закаленных в масле, соответствовали наиболее высокие значения механических свойств. Причина наибольшей степени фрагментации после закалки в масле состоит в том, что при аустенитизации и охлаждении действуют два механизма: рекристаллизация с последующим ростом зерна и измельчение при охлаждении, которое ранее наблюдали только у пакетного мартенсита (другие виды мартенсита имеют более низкую температуру образования). Фрагментирование пакетного мартенсита связано с его самоотпуском.
Блоки (глобулы) низкоуглеродистого мартенсита также фрагментируются при термоциклировании, что было установлено впервые. Необходимость протекания процессов отпуска требует для фрагментирования относительно невысоких скоростей охлаждения, поэтому наилучшиесвойстваимеласталь, охлажденнаявмасле(см. табл. 4).
Выводы. В ходе проведенного эксперимента установлено, что методами ТЦО возможно повысить характеристики механических свойств НМС за счет измельчения зерна при термической обработке, что позволяет получить однородные свойства по всему сечению заготовки безприменениявысокоэнергетического воздействия.
В качестве недостатков данного метода можно отметить следующее: 1) необходимо строгое соблюдение температурно-времен- ных параметров процесса ТЦО; 2) использование данной технологии возможно только наструктуренизкоуглеродистого мартенсита.
Практическая часть
Выполнить работу в следующем порядке:
1.Изучить теоретический материал.
2.В отчет внести основные методы повышения конструкционной прочности стали.
3.Оценить преимущества и недостатки каждого из методов, данные представить в виде таблицы.
4.Основываясь на теоретическом материале, предложить свои методы повышения конструкционной прочности сталей. Предложения обосновать.
28
Практическая работа № 10
ИЗУЧЕНИЕ ВИДОВ ТЕРМИЧЕСКОЙ ОБРАБОТКИ, ПРИМЕНЯЕМЫХ ДЛЯ КОНСТРУКЦИОННЫХ СТАЛЕЙ
Цель работы: научиться назначать режим термической обработки для конструкционных сталей в зависимости от необходимых характеристик механических свойств.
Выполнить работу в следующем порядке:
I. Получить задание, вариант выбрать согласно порядковому номеру студента в журнале группы (полный пофамильный список группы).
Варианты заданий:
1.Назначьте и обоснуйте режим термической обработки шестерни из стали 20ХГР для твердости зуба 58–60 HRC. Покажите графически режим упрочняющей обработки, опишите сущность происходящих превращений, микроструктуру и свойства поверхности зуба исердцевинышестернипослетермической обработки.
2.В результате термической обработки детали машин должны получить повышенную прочность по всему сечению (твердость 30–35 HRC). Для изготовления их выбрана сталь 40ХН. Укажите химический состав и определите группу стали по назначению. Назначьте и обоснуйте режим термической обработки, объяснив влияние легирования на превращения, происходящие при термической обработке данной стали. Опишите структуру
исвойства изделий после окончательной термической обработки. Укажите распределение легирующих элементов по фазам, начиная с исходного состояния стали (до термической обработки).
3.Назначьте нержавеющую сталь для изделий, работающих в слабоагрессивной среде (атмосферные осадки). Приведите химический состав стали, необходимую термическую обработку и получаемую структуру. Объясните физическую природу коррозионной устойчивости сталиироль каждого легирующего элемента.
4.Обоснуйте выбор режима высокотемпературного нагрева деталей машин из стали 30ХН3А при условии, что одни закалены от
29
температуры 800 С, а другие – от температуры 850 С (охлаждение в масле). После закалки в обоих случаях проведен высокий отпуск при температуре 600 С. Укажите химический состав и определите группу стали по назначению, объяснив влияние легирования на температуры фазовых превращений, необходимые для выбора высокотемпературных режимов термической обработки данной стали. Покажите графически данные режимы обработки (с указанием фазового состава и распределения легирующих элементов в них) и объясните, какие из этих деталей будут обладать наиболее благоприятнымиэксплуатационнымисвойствами ипочему.
5.Назначьте сталь для изготовления хирургических скальпелей, принимая во внимание условия ее эксплуатации. Изобразите график режима термической обработки с указанием фазового состава стали на каждом из этапов термической обработки. Опишите сущность происходящих превращений и свойства стали после окончательной термической обработки. Характеристики механических свойств стали приведите в виде таблицы.
6.Подберите режим термической обработки, в результате которого пружины должны получить высокую упругость. Для изготовления их выбрана сталь 65Г. Укажите химический состав
стали, изобразите графически режим термической обработки с указанием фазового состава стали на всех этапах термической обработки, объяснив влияние легирования на превращения, происходящие при термической обработке данной стали. Приведите свойства пружин после окончательной термической обработки (данные приведите в виде таблицы).
7.Опираясь на требования, предъявляемые к эксплуатационным свойствам материалов, подберите марку жаропрочной стали для изготовления трубопроводов установок сверхвысокого давления. Укажите состав, назначьте и обоснуйте режим термической обработки стали. Опишите микроструктуру и основные свойства после термической обработки.
8.Подберите режим термической и химико-термической обработки шестерни из стали 12ХН3А для твердости зуба 58–62 HRC.
30