
книги / Плазменные технологии в сварочном производстве. Ч
.1.pdf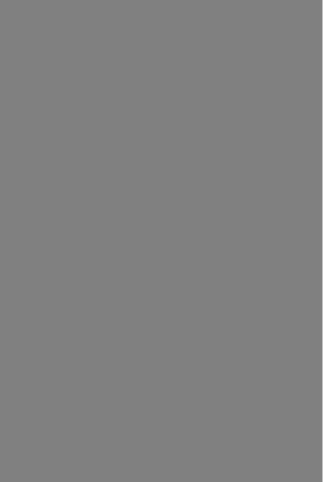
В первую очередь все плазмотроны разделяются на две группы по виду дуги: плазмотроны с дугой прямого и косвенного действия (см. рис. 12). По системе охлаждения электрода и сопла плазмотроны могут быть с газовым и водяным охлаждением (см. рис. 12). Теплоемкость воды намного выше теплоемкости воздуха и других газов, поэтому наиболее эффективной и распространенной является водяная система охлаждения. При'водяном охлаждении допускаются высокие тепловые нагрузки на элеюрод и сопло, т.е. обеспечивается надежная работа при больших токах и высокой степени обжатия столба дуги. Известная формула отводимой тепловой мощности при водяном охлаждении
NB = cSAT, |
(37) |
где NB - отводимая мощность, Вт; с - теплоемкость воды, Дж/(кгград) (4190); S -расход воды, кг/с; АТ - разность температур на выходе и входе в соответствующий элемент плазмотрона, АГ= ^вых ~ Тш позволяет оценить предельную мощность плазмотрона в зависимости от
расхода воды. Учитывая, что в плазмотрон отводится порядка 25-40 % мощности сжатой дуги, для обеспечения работоспособности плазмотрона на токах 500-600 А, теоретически достаточно небольшого расхода воды (1,5-2 л/мин) при АТ= 40 °С. Известные конструкции плазмотронов такой мощности требуют расхода воды от 10 л/мин и более и отличаются слож ностью системы охлаждения, значительными габаритами и массой. Чисто та воды существенно влияет на эффективность охлаждения. Для установок большой мощности целесообразно использовать автономную замкнутую систему охлаждения с дистиллированной водой во избежание образования накипи.
Системы газового охлаждения ввиду низкой эффективности приме няются реже, главным образом, для охлаждения маломощных плазменных горелок и ручных плазменных резаков для воздушной резки.
Плазмотроны можно классифицировать по способу стабилизации дуги. Система стабилизации обеспечивает сжатие столба дуги и строгую ориентацию его по оси электрода и сопла плазмотрона и является одним из важнейших элементов плазмотрона. Существует три вида стабилизации дуги: газовая, водяная и магнитная. Наиболее простой и распространенной является газовая стабилизация, при которой наружный, холодный слой ра бочего плазмообразующего газа, омывая стенки столба дуги, охлаждает и сжимает его. При этом, в зависимости от способа подачи газа газовая ста билизация может быть аксиальной или вихревой (см. рис. 12). Наибольшее обжатие дуги достигается при вихревой стабилизации, поэтому этот спо соб чаще используется в плазмотронах для резки и напыления. При акси альной стабилизации поток газа, обдувающий столб дуги, имеет более спокойный, ламинарный характер, что обеспечивает лучшие условия за-
3 2
щиты нагреваемого изделия от воздействия окружающей среды. Такую стабилизацию предпочтительней использовать для сварки и наплавки. В ряде случаев используют двойную стабилизацию дуги (см. рис. 12), при которой сочетается аксиальная подача через первичное сопло и вихревая подача газа через вторичное сопло и наоборот.
При водяной стабилизации можно достичь наиболее высокой степе ни сжатия и температуры столба дуги (до 50 000-70 000 К). Однако при сутствие паров воды вблизи катодной области приводит к интенсивному сгоранию электродов из любых материалов. Поэтому в плазмотронах с во дяной стабилизацией (например, для резки) чаще используют графитовый электрод, автоматически перемещаемый по мере его сгорания (см. рис. 12).
Магнитная стабилизация (см. рис. 12), при которой создаваемое про дольное магнитное поле сжимает столб дуги, менее эффективна, чем водя ная и газовая. Кроме того, наличие соленоида усложняет конструкцию плазмотрона и увеличивает его габариты. Преимущество магнитной стаби лизации состоит в возможности регулирования степени сжатия столба дуги независимо от расхода рабочего газа. На практике наложение продольного магнитного поля применяется не столько для стабилизации дуги, сколько для вращения ее анодного пятна по внутренним стенкам сопла, при работе в режиме косвенной дуги, с целью повышения стойкости последнего, на пример, в плазмотронах, применяемых для напыления.
По виду электрода-катода плазмотроны постоянного тока можно разделить на плазмотроны со стержневым и распределенным катодом (см. рис. 12). В плазмотронах со стержневым катодом катодное пятно фиксиру ется на торце электрода, а в плазмотронах с расщепленным катодом - ин тенсивно перемещается с помощью газовихревого или магнитного враще ния по развитой поверхности электрода.
Стержневые катоды могут быть трех видов: расходуемые, газоза щитные и пленкозащитные (см. рис. 12). Расходуемый (чаще всего графи товый) электрод, несмотря на высокую температуру плавления, имеет по вышенный расход из-за возгонки вблизи температуры плавления. Газоза щитный вольфрамовый электрод - самый распространенный из всех видов электродов. Вольфрам имеет высокую прочность и достаточно высокую электро- и теплопроводность. При работе в инертной (аргон, гелий) среде при нагрузке j = 15...20 АУмм2 вольфрам практически не расходуется. Пленкозащитные катоды обладают высокой стойкостью в активных газах (воздух, углекислый газ, технический азот). Он представляет собой стер жень из циркония или гафния, запрессованный в медной обойме. Высокая термостойкость таких электродов обусловлена образованием стойкой ту гоплавкой пленки из оксидов и нитридов, защищающей чистый металл от испарения. Активная вставка расходуется главным образом при включении дуги, вследствие разрушения пленки от термоудара. При использовании
3 3
циркониевого электрода допускается большая плотность тока, достигаю щая 80-100 А/мм2, чем при использовании вольфрамового электрода.
При работе плазмотрона с окислительной плазмообразующей средой на больших токах (1000 А и более) применяются разнообразные виды рас пределенных катодов, наиболее распространенными из которых являются полый, дисковый и кольцевой (см. рис. 12). Недостатками распределенных катодов являются сложность их конструкции, трудность равномерного пе ремещения катодного пятна по всей поверхности электрода, низкая ста бильность горения дуги, рост напряжения прикатодной области дуги и связаиное с этим увеличение потерь мощности в электроде.
Плазмотроны различаются по используемой плазмообразующей сре де. Состав плазмообразующей среды диктуется технологическим процес сом и, в свою очередь, является определяющим фактором при выборе схе мы плазмотрона. По химическому воздействию на обрабатываемое изде лие и электроды плазмотрона все плазмообразующие среды можно разде лить на три большие группы: инертные, восстановительные и окислитель ные.
По роду тока плазмотроны отличаются большим разнообразием. По давляющее большинство плазмотронов выполняются для работы на постоянном токе прямой полярности. Это объясняется тем, что на аноде дуги выделяется большее количество тепла, чем на катоде. Тепловая мощность, выделяемая в электроде плазмотрона, в отличие от плавящегося электрода сварочной дуги является не только бесполезной, но и вредной. Наименьшую тепловую нагрузку несет электрод, являющийся катодом.
Предельно допустимая нагрузка на лантанированный вольфрамовый электрод на переменном токе примерно в два раза ниже, а на обратной по лярности при использовании постоянного тока в десять раз ниже, чем на прямой полярности. Поэтому плазмотроны постоянного тока прямой по лярности имеют наиболее высокий коэффициент полезного использования мощности.
При работе плазмотрона на переменном токе прохождение тока че рез ноль может вызвать гашение дуги, поэтому напряжение холостого хода источника питания переменным током должно не менее чем в два раза превышать рабочее напряжение дуги. Плазмотроны, работающие на пере менном токе, рекомендуется применять для сварки алюминиевых сплавов, т. к. в периоды обратной полярности происходит разрушение тугоплавкой оксидной пленки, препятствующей качественному формированию сварно го шва. Существует несколько схем плазмотронов переменного тока. На рис. 12 (VI) представлены плазмотроны, питание которых происходит от однофазного трансформатора. При вентильной коммутации тока (схема 21) электрод функционирует только как катод (в полупериод прямой полярно сти), а сопло - как анод (в полупериод обратной полярности). При такой
3 4
схеме питания обеспечивается большая стойкость вольфрамового электро да. Однако с увеличением тока ухудшаются условия работы сопла, а при работе на токах ниже определенного предела (порядка 150 А) нарушается стабильность горения дуги. Стабильность горения дуги обеспечивается при трехфазной схеме питания плазмотрона, но электроды и сопло нахо дятся в сравнительно тяжелых условиях работы, и значительно усложняет ся конструкция плазмотрона. В ряде случаев плазмотроны выполняют комбинированными для повышения стабильности горения дуги перемен ного тока.
Наряду с дуговыми плазмотронами, работающими на токе промыш ленной частоты, были разработаны высокочастотные и сверхвысокочас тотные (ВЧ и СВЧ) плазмотроны (см. рис. 12, VI). Принцип работы высо кочастотного индуктивного или безэлектродного плазмотрона заключается в нагреве газа до состояния плазмы в электромагнитном поле индуктора. Для этого в полость индуктора, питаемого от высокочастотного генератора (частотой 1-40 МГц, напряжением до 10 кВ и мощностью до 50 кВт), по мещается трубка из термостойкого изоляционного материала, например кварца. В трубку подается плазмообразующий газ и кратковременно вво дится графитовый или металлический пруток. Последний раскаляется под действием поля индуктора и вызывает нагрев и первоначальную иониза цию окружающего газа. Когда электропроводность газа возрастает до оп ределенной величины, начинается интенсивный его нагрев и ионизация вихревыми токами, создаваемыми полем индуктора. После развития само стоятельного кольцевого разряда пруток удаляется из полости трубки. Продуваемый через трубку газ, проходя через кольцевой разряд, нагрева ется и истекает в виде плазменной струи, температура которой достигает 15 000-20 000 К, а скорость истечения в десятки раз меньше скорости ис течения плазменной струи дуговых плазмотронов. Оборудование для вы сокочастотной плазмы дорого и имеет ограниченную мощность, поэтому ВЧ-плазма находит применение в специальных технологиях.
В сверхвысокочастотных плазмотронах (СВЧ) газ также нагревается электромагнитным полем, создаваемым электродом-излучателем (см. рис. 12, VI). СВЧ-плазма возникает у электрода при остроконечной его форме и высокой напряженности поля вблизи него. В высоковольтном и сверхвысокочастотном электрическом поле свободные электроны ускоря ются и приобретают такую кинетическую энергию, что при столкновении с частицами газа вызывают их диссоциацию и ионизацию. Электрод плазмо трона подключен к магнетронному генератору частотой с 2000-3000 МГц и мощностью 2-5 кВт. Плазменный факел СВЧ-плазмотрона интересен тем, что в нем нет термического равновесия. Температура электронов на порядок выше температуры ионов и свободных атомов. Например, при температуре факела, .равной 3500 К, электронная температура достигает
3 5
35 ООО К. Такая высокая температура электронов позволяет производить химические реакции синтеза некоторых специальных материалов.
2.1. Конструкции узлов плазмотрона
Основными узлами плазмотронов являются электродный, сопловой, изолятор, система подачи плазмообразующего газа.
Катоды. Основной характеристикой материала катода являются эмиссионные свойства, которые определяются работой выхода электронов. Чем выше эмиссионные свойства материала катода (чем меньше работа выхода), тем лучше решаются задачи стабилизации дуги и охлаждения ка тода. Для инертных плазмообразующих газов наилучшим материалом ка тодов является вольфрам, легированный окислами лантана и иттрия (марки ВЛиСВИ).
Конструктивно катоды из вольфрама выполняются двумя способами: в виде прутка, который фиксируется цанговым зажимом, закрепленным в электродном узле плазмотрона (рис. 13, /), и в виде медной державки с за-
Рис. 13. Конструкции катодов плазмотронов
деланным в нее стержнем вольфрама, закрепленным в электродном узле. Последняя конструкция менее удобна, но обеспечивает более высокие плотности тока на катоде (рис. 13, 2). Катодная вставка может закреплять ся в цельном корпусе (см. рис. 13,2) и сменных медных наконечниках, со единяемых с корпусом электрододержателя конусной посадкой или резь бой (рис. 13, 3). Конструкции 3, 4, 5 характерны для катодов с активной вставкой (цирконий, гафний), предназначенных для работы в кислородсо держащих средах. Вставка соединяется с наконечником различными спо собами: пайкой, диффузионной сваркой, запрессовкой, совместной холод ной штамповкой активной вставки с медной державкой и др.
Аноды. Выше отмечалось, что при работе плазмотрона на обратной полярности тепловая нагрузка на электрод резко возрастает. Опыт показы вает, что для обеспечения адекватной стойкости сечение вольфрамового электрода, при работе на обратной полярности, должно быть в девять раз больше, чем на прямой полярности. В связи с этим стараются рассредото
3 6
чить разряд по поверхности анода для снижения плотности теплового по тока в анод. Эксперименты, проводимые с вольфрамовыми электродами различной конструкции (рис. 14), показали, что при токе 150 А и токе воз буждения 50 А они разрушались за время, меньшее 23 мин, а при токе 200 А - за 2-3 мин. Это объясняется недостаточной теплопроводностью вольфрама.
Рис. 14. Конструкции электродов-анодов из вольфрама
Эксперименты, проведенные с медными анодами (теплопроводность в 3 раза выше, чем у вольфрама) различной конструкции (рис. 15), показа ли, что конструкции а и б при токе 200 А и токе возбуждения 50 А быстро разрушались. На электроде в активное пятно располагалось на кромке электрода, что приводило к аварийной работе плазмотрона (двойной дуге). Электрод конструкции г при токе 200 А имел ресурс 300 мин при 60 воз буждениях дуги.
Считается, что рост ресурса анодов связан с увеличением размеров электродов и улучшением их охлаждения. Предложен анодный узел, со стоящий из медной водоохлаждаемой державки и активной вольфрамовой вставки (рис. 16).
Высокая стойкость анода обеспечивается качественным соединением меди с вольфрамом и системой водяного охлаждения. Наилучшие резуль таты достигались при осадке расплавленной меди на вольфрамовую встав ку. Стойкость таких анодов достигает 100-300 ч при рабочем токе до 400 А при 100-500 включениях.
3 7
Ппазмообразуюшие сопла восприни мают большие тепловые нагрузки и поэтому требуют тщательного конструктивного оформления. Опыт эксплуатации показал, что наилучшим материалом для изготовле ния сопел является медь высокой чистоты (марки МО, M l), обладающая высокой теп лопроводностью и сравнительно невысокой стоимостью. Армирование стенок сопла те плостойкими материалами приводит к уменьшению срока его службы из-за сниже ния теплопроводности. Сопла малоампер ных и ручных плазменных горелок могут выполняться с естественным или газовым охлаждением (рис. 17,1,2).
В большинстве случаев применяется водяное охлаждение сопел, при этом уча сток сопла, контактирующий с плазменным столбом, может выполняться сменным
(рис. 17,3,4).
Рис. IS. Конструкции медных электродов-анодов
|
!1 |
\ |
|
: . Ч |
р |
- |
:с |
|
|||
V - |
1 |
/ |
я |
|
i |
|
|
(Ц_1 |
|
|
|
, |
0 |
J , |
|
Рис. 16. Конструкция комбинированного анода
3 8

- герметичность, поскольку через изолятор могут проходить комму никации плазмообразующего газа и водяной системы охлаждения.
Материалы, наиболее применимые для изготовления изоляторов плазмотронов, можно условно разделить на две группы: обрабатываемые на универсальном оборудовании из заготовок (прутки, листы) и получае мые с использованием специальной технологической оснастки (прессформы, заливочные формы).
К первой группе относятся фторопласт Ф-4, иногда капролон, эбо нит; ко второй - эпоксидная смола холодного отверждения ЭД-5 с кремнийорганическим наполнителем, стеклонаполненные пресс-материалы ти пов АГ-4В, ДСВ, КМК-218, КПС и др., а также высокоглиноземистые ке рамические типа кристаллокорунд и 22ХС.
Из материалов первой труппы изоляторы изготовляются на универ сальном оборудовании (токарные, фрезерные, сверлильные станки) и мо гут быть достаточно сложными. К недостаткам их можно отнести низкую технологичность процесса изготовления и невысокую термостойкость.
Из материалов второй группы детали можно изготовлять достаточно простым способом с минимальной трудоемкостью и потерями материала. Недостатком является трудность обеспечения точности размеров и формы изолятора. Это объясняется наличием литейных конусов и уклонов, а так же изменением коэффициента усадки у одного и того же материала. В свя зи с этим в пресс-формах изготовляют простые детали, не требующие вы сокой точности.
Применение перспективных керамических материалов сдерживается двумя причинами. Первая - большой разброс коэффициента усадки шликерной массы при спекании, что не позволяет получать детали выше пято го класса точности. Вторая причина - для изготовления керамических де талей требуется набор специального технологического оборудования (ша ровые мельницы, машины шликерного литья, водородные печи для спека ния), это снижает рентабельность при мелкосерийном производстве.
2.2.Условия безаварийной работы плазмотронов
Стабильная работа плазмотронов обеспечивается при соблюдении определенных размерных соотношений между геометрическими парамет рами катода и плазмообразующего сопла. В плазмотронах дугу можно сжимать до определенного предела. При определенном значении тока и диаметра сопла образуется «двойная» или каскадная дуга, горящая между электродом и соплом и соплом и изделием. Это явление связано с тем, что при увеличении тока и уменьшении диаметра сопла увеличивается падение напряжения в столбе дуги и одновременно уменьшается пограничный хо лодный слой газа у стенки сопла, благодаря чему повышается его электро
4 0