
книги / Микроэлектроника. Гибридные интегральные микросхемы
.pdfвеществ (газов, влаги, масла насосов), являющихся основной причиной плохой адгезии. Температура подложки также влияет на структуру напыляемой пленки и, следовательно, на ее электрофизические параметры.
Структура напыленной пленки зависит от материала, состояния поверхности, температуры подложек и скорости напыления: она может быть аморфной, поликристаллической и монокристалличесКой. Размер зерна металлических пленок зависит от температуры плавления металла. Металлы с высокой температурой плавления (вольфрам, молибден, тантал и др.) образуют пленки с малыми размерами зерен. Металлы с низкой температурой плавления образуют круп нозернистые пленки. Такие пленки имеют большую стабиль ность их электрофизических свойств, чем мелкозернистые.
Для получения стабильных пленок при вакуумном на пылении необходимо повышать скорость напыления, а раз меры зерен пленки увеличивать за счет повышения темпера туры подложки при напылении и отжиге.
Отжиг пленок производится в вакуумных установках непосредственно после напыления при температуре подло жек, несколько превышающей температуру подложек при напылении. Это делается для упорядочения структуры и уменьшения внутренних механических напряжений пленок
сцелью повышения их стабильности и улучшения адгезии
кподложкам. При этом сопротивление резистивных и про водящих пленок снижается.
Метод ионного распыления. Источником ионов служит самостоятельный тлеющий разряд либо плазма несамостоя тельного разряда (дугового или высокочастотного) инерт ных газов (обычно высокой чистоты аргона). Существует большое разнообразие процессов ионного распыления, от личающихся характером напряжения питания (постоянное, переменное, высокочастотное), способом возбуждения и под
держания разряда, числом и конструкцией электродов и т. д.
Реальные условия под колпаком при катодном распыле нии (рис. 2.12) можно описать следующим образом. При бомбардировке положительными ионами инертного газа по верхность катода одновременно подвергается воздействию молекул остаточных активных газов. Это приводит к образо ванию оксидных пленок на катоде, которые резко снижают скорость распыления. Часть оксида переносится на подлож ку. На поверхности подложки вместе с распыленными атома ми присутствуют и отрицательно заряженные активные ио ны остаточных газов, которые также способствуют формиро-
Рис 2.12. Реальные условия под колпаком при катодном распыле нии в тлеющем разряде:
/ — вакуумная откачка; 2 — электроны,
бомбардирующие поверхность подложкй; |
||
3 — |
напуск инертного |
газа; 4 — подлож |
ка; |
5 — бомбардировка |
поверхностей мо |
лекулами кислороде; 6 — |
катод; |
7 — эк |
||||
ран; 8 —- высоковольтный |
ввод; |
9 — ионы |
||||
инертного газа; |
10 — |
траектория распы |
||||
ленных |
атомов; |
11 — |
граница |
темного ка |
||
тодного |
пространства; |
12 |
— |
полимерные |
загрязнения
ванию оксидных пленок. Это указывает на то, что при катод ном распылении необходимо вводить жесткий контроль чис тоты рабочего инертного газа и обеспечивать стерильность технологического процесса.
В простейшей двухэлектродной схеме катодного рас пыления источником ионов является плазма тлеющего раз ряда (рис. 2.13, а), возникающая в среде инертного газа.
Рис. 2.13. Схемы камер для катодного распыления:
а |
— диодная система; |
6 — диодная система со |
смещением; в — диодная систе |
|
ма |
с асимметричным полем; г — катодно-плазменное распыление; д. — |
катодно- |
||
плазменное распыление |
С разделением камеры |
формирования разряда |
и -каме |
ры распыления мишени и осяиудения пленки; е — система, с пушкой, для ион ного распыления; К — катод; А анод; М •— мишень; П — подложка; Э — управляющие электроды; МК — магнитная катушкаг О — crriepcrtfe
Чтобы осуществить относительно чистый процесс рас пыления, необходимо на подложку подать небольшой от рицательный потенциал относительно анода (100—300 В)— процесс катодного распыления со смещением (рис. 2.13,6). С одной стороны, это приведет к отталкиванию отрицатель но заряженных ионов, а с Другой — слабая бомбардировка положительными ионами инертного газа способствует обезгаживанию поверхности подложки, а затем и пленки.
Разновидностью катодного распыления со смещением яв ляется распыление при переменном асимметричном напря жении (рис. 2.13, в). В отрицательный полупериод прово дится распыление, а в положительный полупериод с меньг шёй амплитудой — слабая бомбардировка подложки для обезгаживания и очистки.
Применение триодной системы распыления (рис. 2.13, г) позволило существенно улучшить ваккумные условия фор мирования тонких пленок и несколько повысить скорости распыления по сравнению с диодной системой (рис. 2.13, а).
Для достижения больших скоростей осаждения необхо димо снизить давление в рабочей камере, с тем чтобы свобод ный пробег атомарных частиц был больше расстояния ми шень — подложка, а также повысить плотность ионного тока на мишень. Технически в триодной системе это решено следующим образом: разряд поддерживается дополнитель ным источником электронов (рис, 2.13, г). С этой целью в разрядную камеру вводится накальный катод, что обеспечи вает возникновение разряда при напряжении 100 В.. Дав ление в камере понижается до 10-1 — 10-2 Па, что резко увеличивает длину свободного пробега частиц. Накальный катод эмиттирует поток электронов, которые ионизируют ос таточный рабочий газ, поддерживая разряд. При подаче на мишень большого отрицательного смещения относительно катода на нее вытягиваются положительные ионы плазмы, в результате чего происходит распыление мишени. В такой системе электрические цепи разряда и распыления развяза ны, это обеспечивает гибкость управления процессом распы ления. При катодном распылении давление рабочего газа, необходимое для поддержания разряда, относительно ве лико (1—10 Па) и вероятность загрязнения пленки повыша ется. При ионно-плазменном распылении давление ниже (10-1 — 10~3 Па), но для поддержания газового разряда нужны специальные устройства. В некоторых установках (рис. 2,13, д, ё) области разряда и осаждения конструктивно разделены, что позволяет с помощью калиброванных от верстий О и экранов Э создавать необходимые условия для
эффективного управления разрядом и стерильности процес са осаждения пленок.
Магнетронные распылительные системы относятся к си стемам распыления диодного типа. Высокая скорость распы ления достигается увеличением плотности ионного тока за счет локализации плазмы у распыляемой поверхности мише ни с помощью сильного поперечного магнитного поля.
Основными элементами устройства являются катод — мишень, анод и магнитная система (рис. 2.14). Характерной особенностью является наличие замкнутого магнитного по ля у распыляемой поверхности мишени, позволяющего лока лизовать плазму аномального тлеющего разряда непосред ственно у мишени. Силовые линии в виде дуг замыкаются между полюсами магнитной системы. Поверхность мишени, расположенная между местами входа и выхода силовых ли ний, интенсивно распыляется и имеет вид замкнутой дорож ки, геометрия которой определяется формой полюсов маг нитной системы.
При подаче постоянного напряжения между мишенью (отрицательный потенциал) и анодом (положительный или нулевой потенциал) возникает неоднородное электрическое аоле и возбуждается аномальный тлеющий разряд. Эмиттированные с катода под действием ионной бомбардировки
Рис. 2.14. Схемы базовых конструкций магнетронов:
(I — с плоским катодом; б — с кольцевым катодом; в — с полусферическим катодом; г — с цилиндрическим катодом и полым наружным анодом; д —
с полым цилиндрическим катодом и внутренним анодом (схема «обращен
ного |
магнетрона»); |
е — с |
сетчатым |
анодом; / — |
анод; |
2 — магнитная |
систе |
ма; |
3 — экран; 4 — катод-мишень; |
5 — подложкодержатель; 6 — зона |
распы |
||||
ления. Стрелками |
указано |
направление силовых |
линий |
магнитного поля |
электроны захватываются магнитным полем, им сообщается сложное циклоидальное движение по замкнутым траекто риям у поверхности мишени. Электроны оказываются как бы в ловушке, созданной, с одной стороны, магнитным полем, возвращающим электроны на катод, а с другой — поверхностью мишени, отталкивающей электроны. Элект роны совершают циклические движения в ловушке до тех пор, пока не произойдет несколько ионизирующих столкно вений с атомами рабочего газа, в результате которых элект роны потеряют свою энергию. Эти столкновения приводят к возрастанию концентрации положительных ионов у по верхности мишени, что увеличивает интенсивность ионной бомбардировки мишени и вызывает рост скорости распыле ния. Следует отметить, что плазма разряда локализована в области магнитной ловушки в непосредственной близости от мишени.
По сравнению с диодными системами распыления маг нетронные системы обладают следующими достоинствами: высокая скорость распыления (до 35—40 нм/с) при сравни тельно низком рабочем напряжении (~500 В) и небольшом давлении рабочего газа (0,3—0,7 Па); низкий уровень ради ационных дефектов и отсутствие перегрева подложек; ма лая степень загрязненности пленок посторонними газовыми включениями; разнообразие форм распыляемых мишеней; простота конструкций. К недостаткам следует отнести слож ность распыления магнитных материалов и материалов с низкой теплопроводностью, а также низкий коэффициент полезного использования материала мишени.
По мере увеличения масштабов производства ГИС рас тет потребность в оборудовании, которое обеспечивало бы высокую надежность и высокий выход годных ИМС в соче тании с высокой производительностью. Конструкция высо копроизводительной установки катодного распыления пред ставлена на рис. 2.15.
Установка имеет две высоковакуумные секции, шлюзо вую 3 и рабочую 7 камеры, отделенные друг от друга шлю зом. Шлюзовая камера снабжена инфракрасным нагревате лем 14 и высоковакуумным насосом 2. В нее загружается магазин /, в который входит несколько носителей подложек. В каждом носителе помещается до 28 подложек. Рабочая ка мера содержит систему для транспортировки подложек, сос тоящую из конвейера 10 с двумя цепями. Шлюз между обеи ми камерами во время загрузки магазина закрыт, в резуль тате чего в рабочей камере все время поддерживается необ ходимый вакуум.
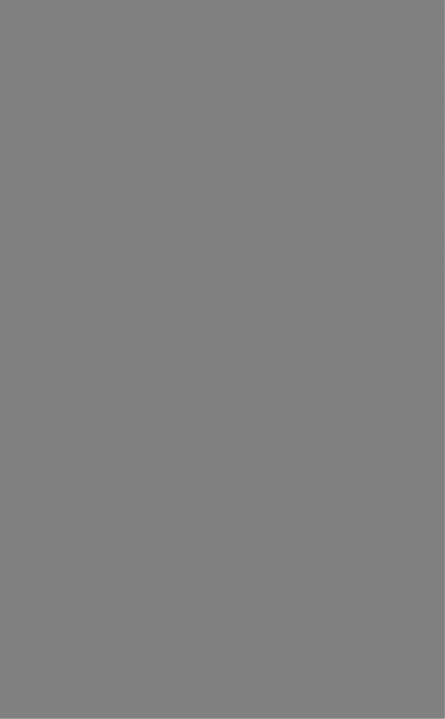
В рабочей камере может размещаться до шести катодов; число катодов зависит от количества материала, необходи мого для создания слоев, а также от того, на одну или на обе стороны подложек должна напыляться пленка и сколь ко раз нужно производить напыление. Такая необходимость может возникать в том случае, когда из-за каких-либо па раметров процесса требуется поддерживать температуру подложек ниже определенного значения, а необходимая толщина пленки не может быть достигнута при этой темпе ратуре за одно распыление. В подобных случаях цикл рас пыления может быть повторен один или несколько раз.
Если необходимо, с каждой стороны системы транспорти ровки подложек может быть установлено до трех катодов, изготовленных из различных материалов. Благодаря этому облегчается создание многослойных структур.
Выход годных изделий увеличивается по сравнению с другими методами благодаря сочетанию ряда факторов: вертикальной ориентации системы, препятствующей осаж дению загрязняющих частиц на поверхности подложки или катода, использованию турбомолекулярных вакуумных на сосов, обеспечивающих создание вакуума без паров масел.
Высокопроизводительные катоды, которые могут рабо тать при постоянном или высокочастотном напряжении» монтируются на откидных дверках 4} 3, закрывающих рабо чую камеру во время работы установки. Когда дверки за крыты, катоды располагаются вблизи обеих сторон системы транспортировки подложек; среднее расстояние между като дом и подложкой составляет.около 60 мм. Если подложки на пыляются только с одной стороны, то одна группа катодов может быть удалена или закрыта.
Установка позволяет наносить пленки на прямоуголь ные или круглые подложки с максимальным размером до 150 мм; она обладает производительностью (ориентировочно) до 250 подложек/ч.
Схема конструкции установки магнетронного распыле ния сМагна* показана на рис. 2.16. Подложки из кассеты 1 загружаются в шлюзовую камеру 2 и с помощью транспор тера 5 перемещаются в вакуумную рабочую камеру б, где попадают сначала в зону предварительного нагрева и очи стки подложек 3, а затем в зону магнетронного распыления 4. Далее подложки поступают в шлюзовую камеру выгруз ки 7 и кассету выгрузки 8. Диффузионный зысоковакуумный насос 9 и последовательно ‘ включенный форвакуумный насос 10 создают необходимое давление в рабочей камере,
Рис. 2.16. Схема установки магнетронного распы ления непрерывного действия «Магна»:
1 , 8 — кассеты с подложками; 2 — загрузочная шлюзовая камера; 3 — зона ионной очистки; 4 — зона магнетронного распыления; 5 — транспортер; 6 — рабочая камера; 7 — шлю зовая камера выгрузки; 9 — диффузионный насос; 10, 11—
форвакуумные насосы
форвакуумные насосы 10, 11 — в шлюзовых камерах. Про изводительность установки при толщине напыляемых пле нок 1 мкм составляет до 100 подложек/ч.
§ 2.4. Нанесение толстых пленок
Толстопленочные ГИС выполняют методом трафарет ной печати последовательным нанесением на керамическую подложку различных по составу паст с их последующим вжиганием, в результате чего образуется прочная монолит ная структура с толщиной пленки 10—70 мкм.
Толстопленочные ГИС нашли широкое распространение благодаря простоте технологии при сравнительно низких затратах на оборудование и материалы, высокой надежно сти, возможности изготовления мощных схем и другим до стоинствам.
Пасты, используемые в толстопленочной технологии, представляют собой тиксотропные (уменьшающие свою вяз кость при увеличении давления) суспензии мелкодисперс ных порошков функциональных материалов (металлов, ок сидов металлов, солей) и стекла в органическом связующем.
Функциональные материалы придают пленкам необхо димые физические свойства. В процессе вжигания эти части цы должны оставаться в твердой фазе и равномерно распре деляться в стекле по объему формируемого элемента.
В зависимости от состава функциональной составляющей
различают проводниковые, резистивные и диэлектрические пасты.
Стекло в мелкодисперсном состоянии (размер, частичек 1—3 мкм) в процессе вжигания расплавляется, а при после дующем затвердевании формирует монолитную конструк цию толстопленочного элемента с равномерно распределен ными в ней частицами функционального материала и одно временно создает прочное соединение элемента с подложкой.
На границе раздела пленка—подложка образуется пере ходный слой толщиной 6—8 мкм, обеспечивающий прочную связь пленки с подложкой. Этот слой компенсирует некото рое несоответствие ТКЛР материалов пленки и подложки.
Используют обычно легкоплавкие стекла, содержащие окислы бора, кремния, свинца, висмута, кадмия и олова. Эти стекла размельчают на шаровых мельницах до размеров частиц, не препятствующих прохождению пасты через тра фарет.
Масса органической связки составляет от 1/4 до 1/3 мас сы пасты; ее назначение состоит в сохранении пасты в виде суспензии, пригодной для трафаретной печати. В качестве связки применяют канифольно-скипидарные смеси, ланолин с циклогексанолом, раствор этилцеллюлозы в терпинеоле.
Проводниковые пасты содержат порошок благодродных металлов (серебро, смесь серебро — палладий, золото), ко торый составляет 70 — 80 % от общей массы твердой фазы пасты. Палладий вводят для снижения коррозии и мигра ции, а также уменьшения стоимости пасты. При изготовле нии многослойных керамических плат применяют марганце во-молибденовые проводниковые пасты, что обусловлено вы сокой температурой обжига спрессованного пакета керами ческих слоев (до 1700° С). Проводниковые пасты должны обе спечить низкое электрическое сопротивление проводников, способность их к пайке и сопротивляемость к выщелачива нию при облуживании.
В резистивных пастах количество функционального ма териала определяется удельным сопротивлением и поэтому варьируется в широких пределах — от единиц до десятков процентов от общего количества твердой фазы. Наиболь шее применение нашли резистивные пасты на основе пал ладия и соединений рутения. В первой из них свойства ре зистора определяются оксидом палладия, образующимся во время вжигания. Для оптимизации температурного коэф фициента сопротивления (ТК/?), дрейфа сопротивления и шумовых характеристик к палладию добавляют серебро, которое при вжигании образует сплав палладий — серебро. Характеристики серебро-палладиевых паст чувствительны к составу атмосферы и профилю распределения температуры
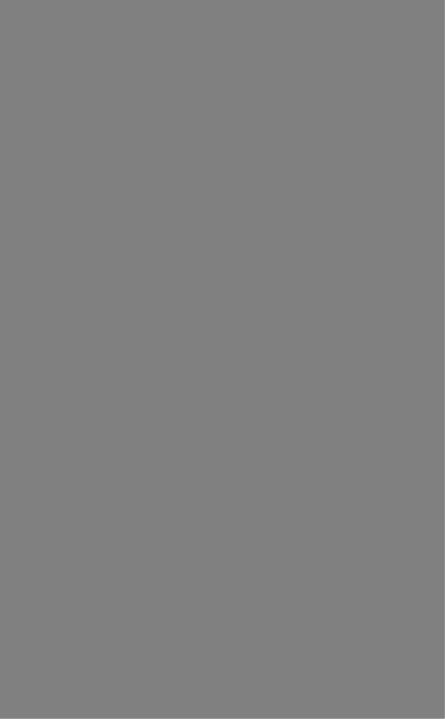