
книги / Сущность и техника различных способов сварки плавлением
..pdfПри сварке труб или закрытых сосудов газ пропускают внутрь сосуда. Инертные газы, увеличивая поверхностное натя жение расплавленного металла, улучшают формирование корня шва. Поэтому их поддув используют при сварке сталей на весу. При сварке на весу, особенно без присадочного металла, следует тщательно поддерживать требуемую величину зазора между кромками.
Рис. 45. Подкладки для защиты от воздуха обратной стороны шва при сварке:
а - односторонней; б - двусторонней; 1 - медная подкладка; 2 —защитный газ; 3 - свариваемый металл;
4 - зажимное приспособление
При соединении встык металла толщиной до 10 мм ручную сварку ведут справа налево (рис. 46). При сварке металла мень шей толщины угол между горелкой и изделием устанавливают равным 60°. При сварке изделий больших толщин применяют правый способ; угол между горелкой и изделием, так же, как и при сварке угловых соединений, устанавливают равным 90°
Рис. 46. Расположение горелки и присадочного прутка при ручной аргонодуговой сварке:
1 - электрод; 2 —присадочный пруток; 3 - защитный газ; 4 - сопло
Присадочный пруток при ручной сварке тонколистового ма териала вводят не в столб дуги, а несколько сбоку возвратно
поступательными движениями; при сварке металла большей толщины - поступательно-поперечными перемещениями. При сварке многослойных швов отдельные валики рекомендуется вы полнять не на всю ширину разделки (многопроходными).
При автоматической и полуавтоматической сварке электрод располагают перпендикулярно к поверхности изделия. Угол меж ду ним и присадочной проволокой (обычно диаметром 2-4 мм) должен приближаться к 90°. В большинстве случаев направление сварки выбирают таким, чтобы присадочный пруток находился впереди дуги (подавался в головную часть сварочной ванны).
Однако при сварке по криволинейному контуру такая схема подачи присадочной проволоки неудобна из-за сложности обра зования шва на разворотах. В этом случае применяется верти кальная подача присадочной проволоки в сварочную ванну. При этом криволинейные участки шва сваривают без разворота сва рочной горелки. Однако при этом уменьшается глубина проплав ления и шов несимметричен, так как присадочная проволока на различных участках криволинейного контура вводится в различ ные части сварочной ванны (головную, боковую, хвостовую).
При автоматической и полуавтоматической сварке верти кальных швов на спуск, если сварочная ванна имеет значитель ные размеры, возможно затекание расплавленного металла под вольфрамовый электрод, что резко уменьшает глубину проплав ления и может привести к короткому замыканию. Вылет конца электрода из сопла не должен превышать 3-5 мм, а при сварке уг ловых швов и стыковых с глубокой разделкой - 5-7 мм. Длина дуги должна поддерживаться в пределах 1,5-3 мм. Для предупре ждения непровара в начале и конце шва рекомендуется приме нять выводные планки. В настоящее время при сварке толсто листового металла находит применение щелевая разделка кро мок. За счет сокращения количества наплавляемого металла зна чительно повышается производительность процесса сварки. Од нако при этом сложно проваривать кромки шва, где могут обра зовываться несплавления. В этом случае может использоваться вольфрамовый электрод с отогнутым концом и поворотом его в зазоре. Другая схема (рис. 47) предусматривает использование 2- х электродов. Обрывать дугу следует постепенным ее удлинени ем, а при автоматической сварке - уменьшением силы сварочного
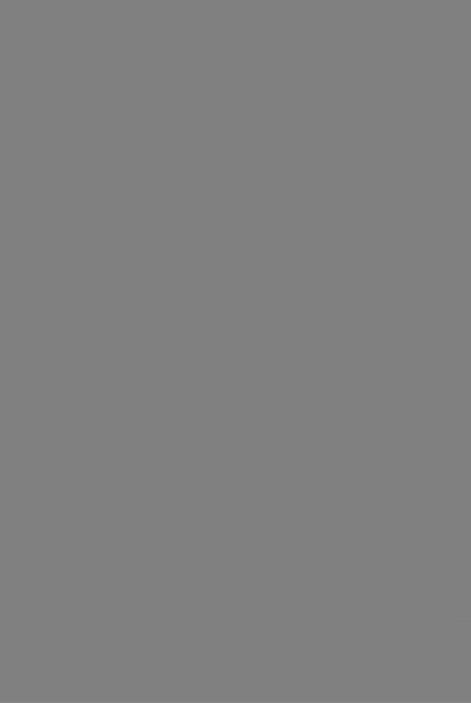
При сварке плавящимся электродом шов образуется за счет проплавления основного металла и расплавления дополнительно го металла - электродной проволоки. Поэтому форма и размеры шва, помимо прочего (скорости сварки, пространственного по ложения электрода и изделия и др.), зависят также от характера расплавления и переноса электродного металла в сварочную ван ну. Характер переноса электродного металла определяется ос новным материалом электрода, составом защитного газа, плотно стью сварочного тока и рядом других факторов.
При традиционном способе сварки можно выделить три ос новные формы расплавления электрода и переноса электродного металла в сварочную ванну. Процесс сварки с периодическими короткими замыканиями характерен для сварки электродными проволоками диаметром 0,5-1,6 мм при короткой дуге с напряже нием 15-22 В. После очередного короткого замыкания (/ и 2 на рис. 48, а) силой поверхностного натяжения расплавленный ме талл на торце электрода стягивается в каплю. В результате длина и напряжение дуги становятся максимальными.
Во все стадии процесса скорость подачи электродной про волоки постоянна, а скорость ее плавления изменяется и в перио ды 3 и 4 меньше скорости подачи. Поэтому торец электрода с ка плей приближается к сварочной ванне (длина дуги и ее напряже ние уменьшаются) до короткого замыкания (5). При коротком за мыкании резко возрастает величина сварочного тока и, как ре зультат этого, сжимающее действие электромагнитных сил, со вместное действие которых разрывает перемычку жидкого ме талла между электродом и изделием. Во время короткого замы кания капля расплавленного электродного металла переходит в сварочную ванну. Далее процесс повторяется.
Частота периодических замыканий дугового промежутка может изменяться в пределах 90-450 в секунду. Для каждого диаметра электродной проволоки в зависимости от его материа ла, защитного газа и т.д., существует диапазон сварочных токов, в котором возможен процесс сварки с короткими замыканиями. При оптимальных параметрах процесса сварка возможна в раз личных пространственных положениях, а потери электродного металла на разбрызгивание не превышают 7%.
Увеличение плотности сварочного тока и длины (напряже ния) дуги ведет к изменению характера расплавления и переноса электродного металла, перехода от сварки короткой дугой с ко роткими замыканиями к процессу с редкими короткими замыка ниями или без них. В сварочную ванну электродный металл пе реносится нерегулярно, отдельными крупными каплями различ ного размера (рис. 48, б), хорошо заметными невооруженным глазом. При этом ухудшаются технологические свойства дуги, затрудняется сварка в потолочном положении, а потери элек тродного металла на угар и разбрызгивание возрастают до 15%.
Для улучшения технологических свойств дуги применяют периодическое изменение ее мгновенной мощности - импульсно дуговая сварка (рис. 49). Теплота, выделяемая основной дугой, недостаточна для плавления электродной проволоки со скоро стью, равной скорости ее подачи. Вследствие этого длина дугово го промежутка уменьшается. Под действием импульса тока про исходит ускоренное расплавление электрода, обеспечивающее формирование капли на его конце. Резкое увеличение электроди намических сил сужает шейку капли и сбрасывает ее в направле нии сварочной ванны в любом пространственном положении.
t
Рис. 49. Изменение тока и напряжения дуги при импульсно-дуговой сварке; In, Un - ток и напряжение основной дуги; lu, Uu - ток и напряжение дуги во время импульса; Тп, Ти —длительность паузы и импульса
Можно использовать одиночные импульсы (рис. 49) или группу импульсов с одинаковыми и различными параметрами. В Последнем случае первый или первые импульсы ускоряют рас плавление электрода, а Последующие сбрасывают каплю элек тродного металла в сварочную ванну. Устойчивость процесса за
висит от соотношения основных параметров (величины и дли тельности импульсов и пауз). Соответствующим подбором тока основной дуги и импульса можно повысить скорость расплавле ния электродной проволоки, изменить форму и размеры шва, а также уменьшить нижний предел сварочного тока, обеспечиваю щий устойчивое горение дуги.
При достаточно высоких плотностях постоянного по вели чине (без импульсов или с импульсами) сварочного тока обрат ной полярности и при горении дуги в инертных газах может на блюдаться очень мелкокапельный перенос электродного металла. Название «струйный» он получил потому, что при его наблюде нии невооруженным глазом создается впечатление, что расплав ленный металл стекает в сварочную ванну с торца электрода не прерывной струей (рис. 48, в). Изменение характера переноса электродного металла с капельного на струйный происходит при увеличении силы сварочного тока до «критического» для данного диаметра электрода.
Величина критического тока уменьшается при активирова нии электрода (нанесении на его поверхность тем или иным спо собом некоторых легкоионизирующих веществ), увеличении вы лета электрода. Изменение состава защитного газа также влияет на величину критического тока. Например, добавка в аргон до 5% кислорода снижает значение критического тока. При сварке в уг лекислом газе без применения специальных мер получить струй ный перенос электродного металла невозможно, также как и при использовании тока прямой полярности.
При переходе к струйному переносу поток газов и металла от электрода в сторону сварочной ванны резко интенсифицирует ся благодаря сжимающему действию электромагнитных сил. В результате под дугой уменьшается прослойка жидкого металла, в сварочной ванне появляется местное углубление. Повышается теплопередача к основному металлу, и шов приобретает специ фическую форму с повышенной глубиной проплавления по его оси. При струйном переносе дуга очень стабильна - колебаний сварочного тока и напряжений не наблюдается. Сварка возможна во всех пространственных положениях.
С целью управления характером переноса электродного ме талла предпринимаются попытки воздействовать на него им
пульсной подачей электродной проволоки. Это нестационарный процесс. Он сопровождается соответствующим изменением сва рочного тока и напряжения дуги. Импульсная подача позволяет расширить диапазон значений рабочих токов, в том числе при сварке с короткими замыканиями. Частота коротких замыканий может быть увеличена в 3-5 раз по сравнению с непрерывной по дачей проволоки. Однако промышленное применение этого спо соба затрудняется из-за отсутствия надежных механизмов им пульсной подачи проволоки.
Более перспективным является способ управляемого пере носа расплавленного металла с использованием быстродейст вующего инверторного сварочного источника. При традицион ном способе сварки перенос электродного металла осуществляет ся сериями коротких замыканий, имеющих хаотичный характер. Процесс отделения образующейся капли происходит при высо ком уровне сварочного тока. Это обуславливает нестабильность процесса и повышенное разбрызгивание. При управляемом про цессе переноса по изменению напряжение дуги электронный микропроцессорный модуль воздействует на быстродействую щий инверторный источник сварочного тока. В течение всего цикла переноса капли величина сварочного тока жестко зависит от фазы ее формирования и перехода в сварочную ванну. В мо мент контакта капли расплавленного металла находящейся на торце электрода с поверхностью сварочной ванны (напряжение дуги близко к нулю) величина сварочного тока уменьшается до минимума (до 10 А). Поэтому в перемычке капли не возникает больших электромагнитных сжимающих сил (меньше разбрызги вание) и она просто переливается в сварочную ванну. Процесс сварки проходит спокойно. Однако его использование сдержива ется высокой стоимостью оборудования.
При сварке плавящимся электродом, так же как и при сварке неплавящимся электродом, внешние магнитные поля отклоняют дугу. Однако эффект от использования внешнего магнитного по ля наблюдается при сварке длинной дугой и наиболее заметен при струйном переносе электродного металла. В этом случае рас плавленный торец электрода колеблется синхронно с частотой внешнего магнитного поля. При поперечных колебаниях увели чивается ширина шва й уменьшается глубина проплавления. В
результате образующийся шов не имеет повышенной глубины проплавления по его оси.
Изменять технологические характеристики дуги можно, ис пользуя центральную подачу защитного газа с высокой скоро стью. Высокие скорости истечения газа при обычных расходах достигаются применением сопл с уменьшенным выходным от верстием. Обдувание дуги газом способствует уменьшению ее поверхности, т.е. сжатию. В результате ввод теплоты дуги в изде лие становится более концентрированным. Кинетическим давле нием потока газа расплавленный металл оттесняется из-под дуги,
идуга углубляется в изделие. В результате глубина проплавления увеличивается в 1,5-2 раза. Однако при этом повышается и воз можность образования в швах дефектов.
Вотечественной и зарубежной практике находит примене ние способ сварки по узкому или щелевому зазору. При этом способе изделия толщиной до 200 мм без скоса кромок собирают
сзазором между ними 6-12 мм. Сварку осуществляют на автома тах (рис 50). Однако, как и при сварке вольфрамовым электро дом, в этом случае дело осложняется возможными несплавлениями швов кромки разделки. Для улучшения провара предпри нимаются попытки использования отогнутого электрода. При сварке сталей плавящимся электродом для защиты лучше исполь зовать смесь из 75-80% аргона и 25-20% углекислого газа. Для сварки алюминия и его сплавов применяют смесь аргона и гелия. Разделку заполняют путем наложения одинаковых по сечению валиков. Метод характеризуется уменьшенной протяженностью зоны термического влияния и равномерной мелкокристалличе ской структурой швов. Возможна сварка не только в нижнем, но
ив других пространственных положениях.
Экономичность способа определяется уменьшением числа проходов в шве за счет отсутствия разделки кромок. Повышение производительности достигается также повышением скорости расплавления электродной проволоки с увеличенным вылетом. Нагрев электрода в вылете протекающим по нему сварочным то ком обеспечивает повышение коэффициента расплавления. Од нако при этом уменьшается глубина проплавления, поэтому спо соб целесообразно применять для сварки швов, требующих большого количества наплавленного металла.
Рис. 50. Схема импульсно-дуговой сварки плавящимся электродом
взащитном газе при узкощелевой разделке кромок:
1- токопроводящий мундштук; 2 —электродная проволока; 3 - сопло; 4, 5 - свариваемые детали; 6 - остающаяся подкладка
из основного материала
При сварке плавящимся электродом в защитных газах зави симости формы и размеров шва от основных параметров режима такие же, как и при сварке под флюсом (рис. 29). Для сварки ис пользуют электродные проволоки малого диаметра (до 3 мм). По этому швы имеют узкую форму провара и в них может наблю даться повышенная зональная ликвация. Применяя поперечные колебания электрода, изменяют форму шва и условия кристалли зации металла сварочной ванны и уменьшают вероятность зо нальной ликвации. Имеется опыт применения для сварки в угле кислом газе электродных проволок диаметром 3-5 мм. Сила сва рочного тока в этом случае достигает 2000 А, что значительно повышает производительность сварки. Однако при подобных форсированных режимах наблюдается ухудшенное формирова ние стыковых швов и образование в них подрезов. Формирование и качество угловых швов вполне удовлетворительны.
Ввиду высокой проплавляющей способности дуги повыша ются требования к качеству сборки кромок под сварку. Качест венный провар и формирование корня шва обеспечивают теми же приемами, что и при ручной сварке или сварке под флюсом (под кладки, флюсовые и газовые подушки и т.д.). С уменьшением плотности тока стабильность дуги понижается (табл. 4). Величи на вылета электрода также влияет на стабильность процесса и
размеры шва. Ниже приведен оптимальный вылет плавящегося электрода при сварке в защитных газах:
Диаметр электродной проволоки, мм |
0,5 |
0,8 |
1,0 |
1,6 |
2,0 |
Вылет электрода, мм |
5-7 |
6-8 |
8-10 |
10-12 |
12-14 |
Расстояние от сопла горелки до изделия обычно выдержи вают в пределах 8-15 мм. Токоподводящий наконечник должен находиться на уровне краев сопла или утапливаться до 3 мм. При сварке угловых и стыковых швов с глубокой разделкой допуска ется выступание токоподводящего наконечника из сопла на 5- 10 мм. Полуавтоматическую сварку в нижнем положении можно выполнять правым или левым методом, узким валиком или с по перечными колебаниями.
Таблица 4
Величина минимального тока (А), при котором обеспечивается стабильное горение дуги (электрод,
плавящийся из низколегированной стали)
Диаметр электродной |
Аргон |
Углекислый газ |
|
проволоки, мм |
|||
30 |
35 |
||
0,6 |
|||
1,0 |
50 |
60 |
|
1,6 |
90 |
90 |
|
2,0 |
120 |
120 |
При сварке тонколистового металла электрод отклоняют от вертикали на 20-30° в сторону направления сварки. При сварке угловых швов в соединениях с вертикальной стенкой держатель дополнительно отклоняют от вертикальной стенки на угол 3045°. Вертикальные швы на тонколистовом металле обычно вы полняют на спуск (электрод под углом назад для лучшего удер жания расплавленного металла от стекания). Сварку на подъем применяют при необходимости обеспечить глубокий провар кро мок. При сварке горизонтальных швов электрод располагают на нижней части кромок и перемещают с поперечными колебания ми. Потолочные швы выполняют вертикальным электродом или с наклоном углом назад с поперечными колебаниями.
Сущность и техника сварки электрозаклепками. Сварная точка образуется за счет теплоты неподвижной дуги, обеспечи