
книги / Машины и оборудование для разработки мерзлых грунтов
..pdf
Среднее значение горизонтальной составляющей сопротивления пород рыхлению Рк (Р1) можно определить также решением системы уравнений [10]
P h2 |
|
p |
; |
P 0,5К |
вд |
b(h h ) , |
(7) |
к 1 |
|
|
к |
р 1 |
|
где h1 – глубина зоны развала, см; h1 = (0,65…0,85) hp; σ – предел прочности пород на растяжение, кгс/см2;
Kвд – удельное сопротивление вдавливанию наконечника в мерзлую породу, кгс/см2;
hр – глубина рыхления, см.
С учетом распределения температуры пород по глубине рыхления
Kвд 21σр ttсм , (8) раз
где tсм – средняя температура пород в слое (hр – h1), С; tраз – средняя температура пород в слое h1, С.
Вертикальная составляющая усилия рыхления Рв (Р2), кгс/см2, находится из выражения
Pв Рк ctg(α0 1 ) , |
(9) |
где α0 – угол рыхления, С; φ – угол трения мерзлых пород по материалу наконечника рыхли-
теля, град.
Тяговое усилие базового трактора по сцеплению Тсц должно быть больше суммы сопротивления пород рыхлению, определяемого по формуле (7), и сопротивления перемещению трактора или равно ей:
Рпер (Gт Gp Gб Pв )( f1 i) , |
(10) |
где Gт – масса трактора, кг;
Gp + Gб – масса навесного оборудования (рыхлителя и бульдозера), кг; f1 – коэффициент сопротивления перемещению трактора;
i – уклон местности.
41
Общая величина сопротивления перемещению рыхлителя при его работе
P Pк Рпер Тсц . |
(11) |
При определении значения Тсц необходимо учитывать величину и направление нормальной составляющей Рв (Р2) усилия рыхления. Эта составляющая при образовании достаточной площадки износа наконечника и в начале его заглубления направлена вверх, а при установившемся процессе рыхления и остром наконечнике рыхлителя направлена в массив пород, т.е. рабочий орган заглубляется в породу. В этом случае увеличивается сцепная масса трактора, а следовательно, возрастает и тяговое его усилие:
Tсц (Gт Gр Gб Pв ) 2 , |
(12) |
где φ2 – коэффициент сцепления трактора с поверхностью мерзлых пород.
При работе с использованием трактора-толкача суммарное тяговое усилие
Т сц Тсц1 (1 К0 ) , |
(13) |
где Tсц1 – тяговое усилие толкача на породе, кгс/см2;
К0 – коэффициент использования толкача, или коэффициент одновременности работы, К0 = 0,6...0,7.
Усилие заглубления зуба рыхлителя в породу P2 = Рзаг определяют из расчета опрокидывания тягача вперед. Исходя из условий вывешивания базового трактора относительно ребра А и зуба рыхлителя
в статическом положении равновесия ΣМА = 0. усилие заглубления
(рис. 15, б):
при работе без толкача
P P |
|
Gтl1 Gp (L l2 ) Gбl |
, |
(14) |
|
||||
2 заг |
|
L l3 |
|
|
|
|
|
42
при работе с толкачом
P P |
|
Gтl1 Gp (L l2 ) Pт (L l4 ) Gбl |
, |
(15) |
|
||||
2 заг |
|
L l3 |
|
|
|
|
|
где Рт – усилие толкача, кгс.
Усилие подъема зубьев рыхлителя (вертикальная составляющая сопротивления пород рыхлению) Рв определяют из расчета опрокидывания тягача назад относительно ребра Б при максимальной глубине
рыхления (см. рис. 15, б). Исходя из условия равновесия ΣМБ = 0 это усилие
P |
Gб l L Gтl4 Gрl2 |
. |
(16) |
|
|||
в |
l3 |
|
|
|
|
При расчете гидропривода выбирают гидроцилиндры в соответствии с расчетными положениями по определению усилий подъема
изаглубления зубьев (см. рис. 15, б), определяют скорости подъема
иопускания зубьев рыхлителя, рассчитывают гидроцилиндры на прочность.
Усилие, развиваемое гидроцилиндром с установленным штоком
вверх, Sц.о (кгс) при заглублении зубьев рыхлителя определяется по формуле
S |
ц.о |
0,785(D2 |
d 2 )P , |
(17) |
|
|
|
|
где D – внутренний диаметр цилиндра, см; d – диаметр штока, см;
Р– рабочее давление в цилиндре, кгс/см2.
Усилие, развиваемое гидроцилиндром при подъеме рабочего ор-
гана (кгс)
|
S |
ц.п |
0,785D2 P . |
(18) |
|
|
|
|
|
Соотношение скорости подъема Vп и опускания Vo при обычном |
||||
конструктивном исполнении: |
|
|
||
если Р = 100 кгс/см2 |
Vп / Vo = 1,25...1,35; |
|
||
если Р = 160 кгс/см2 |
Vп / Vо = 1,33...1,65. |
|
43
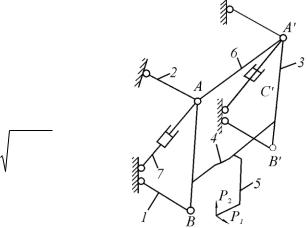
2.1.3. Расчет рамы рыхлителя на прочность
Определение наибольших нагрузок на раму
Схема навесного оборудования со схемой четырехшарнирной подвески приведена на рис. 16. Она состоит из нижних тяг 1 и верхних тяг 2, соединенных с вертикальными стойками 3. Нижние и верхние тяги шарнирно крепят к тягачу. Вертикальные стойки соединены между собой поперечной балкой 4, на которой закреплен зуб рыхлителя 5, и ригелем 6. Заглубление и выглубление рыхлителя производят при помощи гидроцилиндров 7.
Наибольшие нагрузки в элементах рамы и рыхлителя возникают при встрече зуба с непреодолимым препятствием. При этом на зуб действуют силы Р1 и Р2. Силу Р1 определяют по формуле
P G |
|
|
|
V |
Gсц |
C |
|
, (19) |
сц |
max |
|
o |
|||||
1 |
|
|
|
|
|
q |
|
|
где Gсц – сцепной вес рыхлителя, кН; |
|
|
φmax – максимальный коэффициент |
|
|
сцепления, φmax = 0,90...0,95; |
Рис. 16. Схема навесного обору- |
|
V – скорость трактора на первой |
||
дования со схемой четырехшар- |
||
|
передаче, м/с; |
нирной подвески |
|
|
q – ускорение свободного паде- |
|
ния, м/с2; |
|
Со – жесткость навесного оборудования и препятствия, кН/м. Суммарная жесткость препятствия и навесного оборудования
Co |
C1C2 |
, |
(20) |
||
C1 |
C2 |
||||
|
|
|
где С1 – жесткость металлоконструкции навесного оборудования; C2 – жесткость препятствия.
44
Эти жесткости определяют по приближенным формулам
C1 αGсц ; |
C2 βB , |
где – коэффициент жесткости навесного оборудования на единицу веса трактора, α = 90...100 кН м –1·кН –1;
В – ширина стойки зуба рыхлителя, м;
β– коэффициент жесткости препятствия на единицу ширины стойки зуба.
Сила P2 направлена вверх при заглублении и вниз при выглублении. Ее можно определить по приближенной формуле
P2 = (0,3...0,5)Р1, |
P2 = 0,5P1. |
Далее дан расчет наиболее нагруженных элементов конструкции рамы рыхлителя.
Расчет стоек
Расчетная схема стойки АВ представлена на рис. 17. Реакции определяют из уравнений равновесия:
ΣX : ХА – ХВ + P1 = 0, |
|
ΣY : – YА + P2 = 0, |
(21) |
|
МА : ХВL – P α + Р2b = 0, |
||||||||||
|
|
|
|
|
1 |
|
|
|
|
|
|
где P = 0,5Р1; P = 0,5P2, с учетом того, что нагрузку воспринимают |
|||||||||||
1 |
2 |
|
|
|
|
|
|
|
|
|
|
две стойки. |
|
|
|
|
|
|
|
|
|
|
|
Значения реакций в опорах: |
|
|
|
|
|
||||||
|
X |
|
P |
a L |
P |
b |
, |
||||
|
|
|
|
|
|||||||
|
|
A |
|
1 |
|
L |
|
|
2 |
L |
|
|
|
X |
|
P |
a |
P |
b |
, |
|
||
|
|
|
|
|
|
||||||
|
|
|
B |
|
1 L |
2 |
L |
|
|
YA P2 .
Строят эпюры продольных сил N, поперечных сил Q и изгибающих моментов М для балки АВ (рис. 18). На нее действуют в точке С усилия, равные Р1 и P2, и изгибающий момент MC = P1 (a – L + l) – P2b.
45
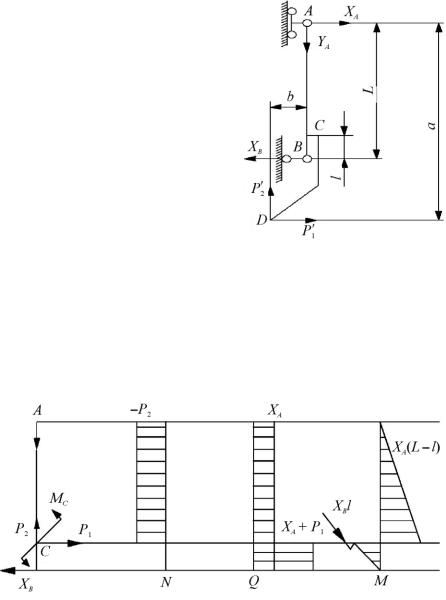
Наиболее опасными являются сечения, близкие к точке С. Приближенный расчет на прочность осуществляют по максимальным нормальным напряжениям σ, возникающим от действия изгибающего момента:
σ |
|
M max |
h ; |
σ [ ]/ n , |
|
|
|
|
|||
|
|
I |
|
|
|
где Мmax – максимальный изгиба- |
|
||||
|
|
ющий момент; |
|
||
|
|
I – момент сопротивления |
|
||
|
|
сечения стойки; |
Рис. 17. Расчетная схема cтойки АВ |
||
|
|
|
|||
|
h – максимальное расстояние от точек сечения до нейтральной |
||||
|
|
линии; |
|
|
|
|
п – коэффициент запаса, п = 1,5...2,5; |
||||
[σ] |
– допускаемые напряжения для материала стойки, [σ] = |
||||
|
|
= 3 105 кН/м2. |
|
Рис. 18. Эпюры продольных сил N, поперечных сил Q и изгибающих моментов М для балки АВ
46
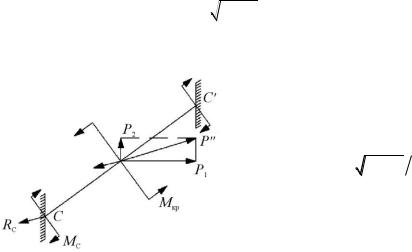
Расчет балки
Расчетная схема балки СС представлена на рис. 19. Балка нагружена крутящим моментом
M |
0 |
P (a L) P b |
|||
|
1 |
|
2 |
||
и поперечной силой |
|
|
|
|
|
|
|
|
|
. |
|
|
|
P |
P P |
||
|
|
0 |
1 |
2 |
|
Реакции в заделках определяют из уравнений равновесия и условий симметрии.
В рассматриваемом случае
M |
|
M |
|
M |
|
P |
a L |
P |
b |
, |
|||
|
|
|
|
|
|||||||||
|
C |
|
C ' |
|
|
0 / 2 |
1 |
2 |
2 2 |
|
|||
|
R R |
|
R |
|
|
|
|
|
|
||||
|
|
P P 2 . |
|
||||||||||
|
|
C |
C ' |
|
0 / 2 |
|
1 |
2 |
|
|
|
Строят эпюры крутящего Мкр и изгибающего М моментов, а также поперечной силы Q для балки СС' (рис. 20).
Рис. 19. Расчетная схема балки СС' Приближенный расчет осу-
ществляют по допускаемым нормальным напряжениям от изгиба и касательным напряжениям от кручения:
σ |
M max |
h ; |
σ [ ]/ n , |
|
|
||||
|
I |
|
||
τ |
Mкр max |
; |
τ [ ]/ n , |
|
|
||||
|
Wт |
|
где Мкр mах – максимальный крутящий момент в балке;
Wт – момент сопротивления кручению сечения балки;
[τ]– допускаемые касательные напряжения материала балки,
[τ]= 1,9 · 105 кН/м2.
47
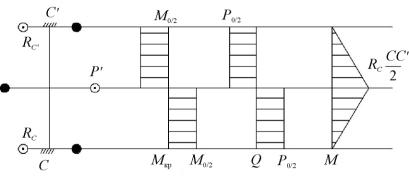
Рис. 20. Эпюры крутящего Мкр и изгибающего M моментов, поперечной силы Q для балки СС
Отметим, что форму и размеры поперечных сечений менее нагруженных элементов навесного оборудования выбирают из конструктивных соображений с учетом опыта работы существующих образцов.
2.1.4. Определение производительности бульдозерно-рыхлительных агрегатов
Разработку площадей мерзлых пород тяжелыми навесными рыхлителями ведут послойно параллельными или взаимно перпендикулярными проходами на максимально возможную глубину. При глубине промерзания до 50–70 см возможна работа одним-тремя зубьями
срыхлением на всю глубину за один проезд. При большей глубине промерзания разработка пород осуществляется одним зубом за дватри хода с глубиной рыхления 30–35 см за каждый ход. После того как первый слой мерзлых пород разрыхлен, он убирается отвалом, расположенным на том же тягаче. Перед началом работы на площадке, подлежащей рыхлению, проводят подготовительные работы, связанные
срасчисткой участка от снега, так как при работе по снегу (даже толщиной всего несколько сантиметров) коэффициент сцепления базового тягача с породой снижается до 40–50 %. В результате не полностью используется мощность тягача и снижается производительность рыхления. Снеговой покров желательно снимать на площади, которая может быть разрыхлена не более чем за 4–5 ч. При рыхлении пород очень важен правильный выбор направления движения рыхлителя.
48
Поэтому необходимо осуществлять рыхление при движении тягача под уклон, что увеличивает тяговое усилие и позволяет разрыхлять породу на более значительную глубину. Рыхление выполняют обычно на первой передаче со средней скоростью 0,8–2,4 км/ч.
В зависимости от прочности и необходимой степени дробления мерзлых пород средняя глубина их рыхления за один проход для базовых тягачей мощностью 200–300 л.с. колеблется от 40 до 70 см.
Расстояние между продольными бороздами в среднем равно 120 см, угол развала борозды составляет 42–49°.
Перед рыхлением крепких пород навесными рыхлителями целесообразно производить сотрясательное взрывание массива или применять толкачи. Тандемный способ рыхления с использованием дополнительного трактора-тягача наиболее эффективен. Он обеспечивает большую возможность механического рыхления пород, чем при обычном способе, так как суммарное горизонтальное усилие на зубе рыхлителя достигает 784 кН и более, а вертикальное – 294 кН и более. Это и позволяет эффективно разрабатывать особо тяжелые скальные и вечномерзлые породы. Однако работа с толкачом увеличивает машинное время на разработку 1 м3 породы и общие затраты примерно
в2 раза, но при этом в 3–4 раза возрастает производительность и значительно снижается износ трактора и рыхлителя. С увеличением длины борозды скорость рабочего и холостого ходов возрастает. Так, при длине борозд 30 м средняя скорость рабочего хода составляет 0,7 м/с, холостого –0,95 м/с. С увеличением длины борозд до 60 м рабочая скорость возрастает до 0,75 м/с, а холостая – до 1,02 м/с при неизменной глубине рыхления. Длина борозд в пределах 60–100 м признана наиболее целесообразной. Установлено, что износ сменного наконечника зуба рыхлителя (коронки) по высоте (при длине рыхления более 1000 м) при работе в илисто-глинистых отложениях составляет 5–8 мм,
вгалечно-щебеночных – 14–17 мм.
Часовая производительность рыхлителя Прых (м3/ч) в общем виде выражается уравнением [9]
П |
V |
. |
(22) |
рых T
При определенных размерах разрыхляемого участка, возможности разворота на его концах и работе без поперечных проходов экс-
49

плуатационная производительность рыхлителя (м3/ч) определяется выражением
П BhLр.х kт kв |
|
Lр.х |
|
tp |
|
|
|
|
|
|
|
|
, |
(23) |
|||
1000v |
3600 |
|||||||
|
|
|
|
|
|
|||
|
|
р.х |
|
|
|
|
|
где В – ширина захвата при рыхлении, м;
h– средняя глубина рыхления, h = (0,6–0,8)hуст (hуст – возможная
вданных условиях глубина рыхления);
Lр.х – средняя длина рабочего хода в одну сторону;
kт – коэффициент, учитывающий, с одной стороны, потери времени на подход толкача, с другой – увеличение рабочей скорости рыхления, kт = 0,8...1,2;
kв – коэффициент использования времени (для средних условий
kв = 0,85);
vр.х – средняя скорость рабочего хода, км/ч; vр.х = (0,6…0,7) vн – номинальная скорость базового трактора с механической трансмиссией на передаче соответствующей скорости движения порядка 2,5…3,0 км/ч);
tp – время одного разворота в конце участка с учетом выглубления зубьев, tp = 15...20 с.
Ширина захвата при рыхлении
B kп[bn 2h tg μ t(n 1)] , |
(24) |
где kп – коэффициент перекрытия, kп = 0,75; п – количество зубьев;
b – толщина зуба;
μ– угол скола от вертикали, μ = 15...45° – меньшие значения при рыхлении мерзлых грунтов и скальных пород, а большие –
обычных грунтов; t – шаг зубьев.
Сменная эксплуатационная производительность Пэ(см), м3, определяется выражением
П |
|
|
3600Тсм Вр hp Lp.x Kв |
, |
(25) |
||
э(см) |
|
||||||
|
|
|
1 |
|
|
|
|
|
|
|
|
t |
|
|
v пер
где Тсм – продолжительность смены.
50