
книги / Моделирование химико-технологических систем с использованием программного обеспечения Design-II for Windows
..pdfи расход топливного газа на огневом подогревателе для обеих технологических схем и обосновать оптимальный вариант схемы
сучетом того, что при сбросе давления турбина будет вырабатывать электроэнергию с указанным КПД).
Отчетность: отчет на Word с графиками и таблицами, подтверждающими расчеты и выводы.
Примечания:
–понятие эффективности связано с затратами на проведение процесса, т.е. чем меньше будет текущих затрат, которые связаны
спотребной мощностью компрессора и расходом топливного газа в огневом подогревателе, отнесенных к единице продукции (расход ПГС), тем работа схемы будет более эффективной;
–все графики должны строиться по 4 и большему количеству точек, а сами зависимости должны иметь гладкий вид;
–при составлении отчета необходимо объяснить полученные зависимости с точки зрения теории технологических про-
цессов, а не просто ограничиться констатацией полученных зависимостей.
ЗАДАНИЕ № 2
Цели работы
1.Получение навыков построения химико-технологической системы в среде Design-II for Windows на основании технологической схемы производства;
2.Получение навыков работы с модулями Design-II for Windows, связаннымис теплопередачей ихимическим превращением;
3.Получение навыков анализа и оптимизации ХТС с операторами, связанными с теплопередачей и химическим превращением.
Примечание: данная работа базируется на лабораторной работе № 1 и является ее расширением
11

Технологическая схема
Описание технологической схемы
На ГРС из магистрального трубопровода природного газа высокого давления происходит отбор газа на технологию, давление которого затем адиабатически сбрасывается до безопасных 15 кг/см2 (абс), после чего он подается на производство по трубопроводу с заданными диаметром и длиной. Поскольку температура природного газа низка, поэтому во избежание обледенения оборудования он смешивается с потоком горячего рециркулирующего газа после компрессора. Температура на всасе компрессора поддерживается в пределах 25–30 °С регулировкой расхода рециркулирующего потока природного газа. Далее из этого потока отбирается газ на горелки, а остальная часть потока газа подается на компрессор, где его давление увеличивается до рабочих 40–45 кг/см2 (абс). Далее природный газ после компрессора смешивается с потоком азотоводородной смеси (АВС) и по трубопроводу с заданными длиной и диаметром подается в смеситель, где смешивается с потоком перегрето-
12

го пара, также подаваемого в смеситель по трубопроводу с заданными длиной и диаметром от котла-утилизатора, обогреваемого потоком дымовых газов после подогревателя конверсии. Количество перегретого пара регулируется по расходу природного газа. Парогазовая смесь подается в подогреватель, обогреваемый потоком дымовых газов после горелок, и далее на паровую конверсию. После паровой конверсии конвертированный газ вместе с заданным количеством сжатого воздуха и дополнительного пара подается на паровоздушную конверсию. Дымовые газы после подогревателя ПГС подаются в котел-утилизатор, где котловая вода превращается в перегретый пар (371 °С), подаваемый на смешение с потоком газа по трубопроводу.
Примечание: Необходимо отметить, что в реальном производстве процесс подогрева парогазовой смеси продуктами горения природного газа и процесс паровой конверсии происходят одновременно, однако для моделирования данной ХТС в данной конкретной лабораторной работе производят декомпозицию данного узла:
– топливный газ смешивается с воздухом (условно: N2 – 79 об.% и O2 – 21 об.%) и происходит полное сгорание веществ топлива в реакторе (горелке) с остаточным содержанием кислорода
3,0±0,1 об. %;
–дымовые газы после горелки подогревают парогазовую смесь в прямоточном теплообменнике с заданной площадью теплопередачи и коэффициентом теплопередачи. При проведении расче-
тов обратить внимание на недопустимость пересечения линий нагрева и охлаждения;
–подогретая парогазовая смесь подается в адиабатный реактор паровой конверсии (Steam Reformer).
Исходные данные
–Основные исходные данные берутся из лабораторной рабо-
ты № 1.
–Параметры котловой воды: температура 50 °С, давление 40,5 кг/см2изб.
–Соотношение пар/метан после смесителя ПГС: 3,70±0,01.
13
–В потоке конгаза соотношение (H2+CO)/N2 = 3,00±0,01.
–Реактор горелок: адиабатный Stoichiometric Reaction. Полное горение веществ топлива с остаточным содержанием кислорода на выходе 3–5 об.%.
–Реактор паровой конверсии: модуль Reactor (режим: адиа-
батный Steam Reformer).
–Реактор паровоздушной конверсии: модуль Reactor (режим:
адиабатный Secondary Reformer).
–Теплообменник-подогреватель ПГС продуктами горения: прямоточный, КТП = 150 Вт/м2К (при расчете использовать kJ/s/m2/K),
FТП = 920 м2.
–Теплообменник котла-утилизатора: противоточный, КТП =
=110 Вт/м2К (при расчете использовать kJ/s/m2/K).
– Компрессор воздуха: политропный, трехступенчатый, с межступенчатым охлаждением до 50 °С и давлением после ступе-
ней: 14; 28; 40,5 кг/см2изб.
– Расход дополнительного пара – 40 (371 °С): от 3 до 16 т/ч.
Этапы выполнения работы
1.Разобраться с технологической схемой, ее описанием, заданными ограничениями, допущениями и исходными данными.
2.Освежить знания по теории технологических процессов производства аммиака.
3.Освежить знания по особенностям функционирования используемых в работе модулей из программного обеспечения Design-II for Windows.
4. Самостоятельно формализовать технологическую схему
вХТС с использованием операторов среды Design-II for Windows.
5.В среде Design-II for Windows создать указанное задание, добиться корректных расчетов (SOLUTION HAS BEEN RICHED) и показать их преподавателю.
6.Выполнить соответствующее индивидуальное задание. ВНИМАНИЕ: при проведении расчетов следует учитывать,
что давления потоков пара и технологического воздуха должны быть выше давления технологического потока в местах смешения.
14
Варианты индивидуальных заданий
1.Определить влияние соотношения пар/газ в ПГС на остаточ-
ное содержание СН4 после вторичного риформинга и эффективность работы схемы (т.е. определить, как будут изменяться полнота использования сырья, требуемая мощность компрессоров, потери тепла с дымовыми газами, расходы потоков сырья и необходимая поверхность теплообмена при изменении в ПГС соотношения пар/газ, при условии поддержания заданных соотношений);
2.Определить влияние давления после компрессора газа на
остаточное содержание СН4 после вторичного риформинга и эффек-
тивность работы схемы (т.е. определить, как будут изменяться полнота использования сырья, требуемая мощность компрессоров, потери тепла с дымовыми газами, расходы потоков сырья и необходимая поверхность теплообмена при изменении давления газа после компрессора природного газа, при условии поддержания заданных соотношений и отношения давлений в местах смешения пара
ивоздуха с технологическим потоком);
3.Определить влияние расхода топлива на горелки на оста-
точное содержание СН4 после вторичного риформинга и эффектив-
ность работы схемы (т.е. определить, как будут изменяться полнота использования сырья, требуемая мощность компрессоров, потери тепла с дымовыми газами, расходы потоков сырья и необходимая поверхность теплообмена при изменении расхода топлива на горелки, при условии поддержания заданных соотношений и отношения давлений в местах смешения пара и воздуха с технологическим потоком);
4.Определить влияние количества воздуха, подаваемого на сжигание (т.е. концентрации кислорода в дымовых газах) на оста-
точное содержание СН4 и эффективность работы схемы при посто-
янном соотношении пар/газ (т.е. определить, как будут изменяться полнота использования сырья, требуемая мощность компрессоров, потери тепла с дымовыми газами, расходы потоков сырья и необходимая поверхность теплообмена при изменении расхода воздуха на горелки, при условии поддержания заданных соотношений и от-
15
ношения давлений в местах смешения пара и воздуха с технологическим потоком);
5.Определить влияние давления газа после ГРС на остаточное
содержание СН4 и эффективность работы схемы при постоянном соотношении пар/газ (при анализе расчетов также необходимо рассмотреть, как будут изменяться полнота использования сырья, требуемая мощность компрессоров, потери тепла с дымовыми газами, расходы потоков сырья и необходимая поверхность теплообмена);
6.Определить влияние величины расхода АВС на остаточное
содержание СН4 и эффективность работы схемы при постоянном соотношении пар/газ (при анализе расчетов также необходимо рассмотреть, как будут изменяться полнота использования сырья, требуемая мощность компрессоров, потери тепла с дымовыми газами, расходы потоков сырья и необходимая поверхность теплообмена);
7.Определить влияние давления газа после компрессора при-
родного газа на остаточное содержание СН4 и эффективность работы схемы при постоянном соотношении пар/газ (при анализе расче-
тов также необходимо рассмотреть, как будут изменяться полнота использования сырья, требуемая мощность компрессоров, потери тепла с дымовыми газами, расходы потоков сырья и необходимая поверхность теплообмена);
8.Определить влияние состава природного газа на эффективность работы узла: метан в природном газе заменяется на эквивалентное количество этана и пропана с соотношением концентраций этан/пропан = 4. Для данного варианта в ПГС мольное соотношение
пар/углерод должно быть Н2О/С = 3,50±0,01 (при анализе расчетов также необходимо рассмотреть, как будут изменяться полнота использования сырья, требуемая мощность компрессоров, потери тепла с дымовыми газами, расходы потоков сырья и необходимая поверхность теплообмена);
9.Определить целесообразность обогащения технического воздуха (подаваемого в реактор вторичного риформинга) кислоро-
16
PNRPU
дом (при анализе расчетов также необходимо рассмотреть, как будут изменяться полнота использования сырья, требуемая мощность компрессоров, потери тепла с дымовыми газами, расходы потоков сырья
инеобходимая поверхность теплообмена);
10.Определить наиболее целесообразный вариант подачи АВС синтеза: в поток газа на конверсию или в поток газа на сжигание. Содержание кислорода после сжигания 1–10 об.% (при анализе расчетов также необходимо рассмотреть, как будут изменяться полнота использования сырья, требуемая мощность компрессоров, потери тепла с дымовыми газами, расходы потоков сырья и необходимая поверхность теплообмена).
Примечания:
– понятие эффективности связано с затратами на проведение процесса, т.е. чем меньше будет текущих затрат, которые связаны с потребной мощностью компрессоров, потерями тепла с дымовыми газами и расходом потоков сырья, отнесенных к единице продукции (расход ПГС), тем работа схемы будет более эффективной;
– при создании задания использовать метрическую систему измерений – Metric (NTP);
– графики должны строиться по 4 и большему количеству точек, а сами зависимости должны иметь гладкий вид;
– при составлении отчета необходимо объяснить полученные зависимости с точки зрения теории технологических процессов,
а не просто ограничиться констатацией полученных зависимостей.
ЗАДАНИЕ № 3
Цели работы
1.Получение навыков моделирования химических реакторов
сучетом кинетики в среде Design-II for Windows;
2.Получение навыков анализа и оптимизации ХТС с химическим реактором идеального вытеснения.
17
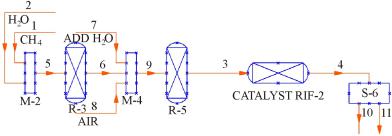
Для достижения указанных целей используется реактор идеального вытеснения, моделирующий процесс каталитической паровой конверсии метана во вторичном риформинге. Вариант построения ХТС в среде Design-II for Windows, позволяющий производить оптимизацию ее работы, представлен ниже:
Описание ХТС
Для обеспечения возможности оптимизации, составляется ХТС для расчета материального баланса, т.е. со всеми входящими потоками, и с помощью реакторов Design-II, работающих при заданных температурах и давлениях, производится расчет материального и теплового балансов. Так, для расчета равновесного состава газа после первичного риформинга при заданной температуре и давлении используется реактор R-3 (режим Steam Reformer), куда из смесителя М-2 подается парогазовая смесь. После первичного риформинга конгаз смешивается со сжатым воздухом и защитным паром (защита смесителя реактора от плавления) и подается на конверсию в аппарат вторичного риформинга. Исходя из конструкции, аппарат вторичного риформинга можно условно разделить на два реактора:
– реактор идеального смешения, где после смешения газов с помощью смесителя реактора, в гомогенной области происходит адиабатическое взаимодействие всего кислорода с водородом без расходования метана с образованием водяных паров (реактор R-5
врежиме Stoichiometric Reaction);
–реактор идеального вытеснения, где на поверхности катализатора происходит реакция адиабатической паровой конверсии метана.
18
Исходные данные
–Природный газ:
расход: 35 770 нм3/ч, давление: 28 кг/см2абс, температура: 500 °С,
состав: СН4 – 98 об.%, N2 – 1 об.%, СО2 – 1 об.%.
–Параметры воздуха:
температура: 320 °С, давление: 41,5 кг/см2абс,
состав: О2 – 21 об.%, N2 – 79 об.%,
расход воздуха подбирается, исходя из достижения соотношения в конвертированном газе после вторичного риформинга: (H2+CO)/N2 = 3,0 0,01.
–Параметры пара:
температура: 371 °С, давление 42 кг/см2абс.
–Мольное соотношение ПАР/ГАЗ на первичном риформин-
ге = 3,4.
–Расход дополнительного пара: 6 т/ч.
–Параметры на выходе парового риформинга (R-3): температура: 790 °С, давление: 28 кг/см2абс.
–Размер слоя катализатора:
диаметр: 3,7 м, высота: 4,15 м.
С целью обеспечения возможности анализа параметров сухого (а не влажного) газа используется модуль Component Splitter (S-6) – порядок пользования модулем см. в литературе.
В качестве контроля, параметры выходного потока будут близки к следующим:
19
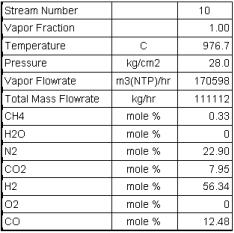
Зависимости констант равновесия от температуры и уравнения кинетики
Уравнения химических реакций:
1)CH4 + H2O = CO + 3H2;
2)CO + H2O = CO2 + H2.
Уравнения констант равновесия:
lg Kp1 9840T 8,343 lg T 2,059 10 3 T
0,178 10 6 T 2 11,96;
lg Kp2 2203,24T 5,1588 10 5 T 2,5426 10 7 T 2
7,461 10 11 T 3 2,3.
Константы скоростей химических реакций:
Kc1 1,03 105 exp 90850 ;8,31 T
Kc2 30,9.
20