
книги / Технология органического и нефтехимического синтеза
..pdf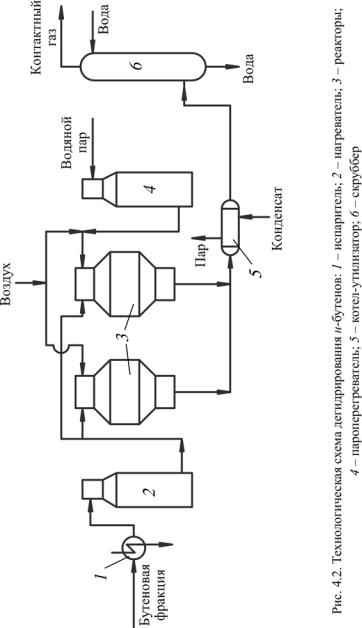
101
Согласно схеме бутадиеновая фракция в смеси с рециркулирующими бутенами в испарителе 1 испаряется и нагревается до 80 °С, проходит через нагреватель 2, где подогревается до 550 °С и поступает
вверхнюю часть реактора 3. Туда же подается водяной пар, перегретый
втрубчатом пароперегревателе 4 до 700–760 °С. В итоге температура
на входе в реактор 3 поддерживается на уровне 650 °С. Пары бутенов и водяной пар смешиваются в верхней части реактора в специальных смесителях инжекционного или диафрагменно-дискового типа.
Реактор представляет собой пустотелый аппарат, в нижней части которого имеется решетка, на которой находится катализатор.
Вторая стадия дегидрирования является весьма энергоемкой: расход топлива в 5 раз выше, чем на первой стадии, из-за необходимости перегрева больших количеств водяного пара.
4.1.1.2. Одностадийное дегидрирование н-бутана
При одностадийном дегидрировании н-бутана упрощается схема производства (исключается первая стадия дегидрирования и разделение продуктов данной стадии). Выход бутадиена при одностадийном дегидрировании составляет 50 % на н-бутан.
Процесс одностадийного дегидрирования основан на том, что при повышенных температурах и давлении равновесие реакции дегидрирования н-бутана сдвинуто в сторону образования бутадиена-1,3:
С4Н14 С4Н8 + Н2 С4Н6 + 2Н2 |
(4.4) |
Процесс одностадийного дегидрирования идет на алюмохромовом катализаторе. При этом наряду с бутадиеном-1,3 образуется значительное количество бутенов, которые вновь возвращаются в процесс.
Поскольку на дегидрирование поступает смесь н-бутана с н-буте- нами, для процесса существенно, чтобы количество н-бутенов в контактном газе после реактора было не меньше их содержания в исходном газе, иначе будут дегидрироваться только н-бутены, а не будет обеспечена одностадийность процесса.
102
Процесс одностадийного дегидрирования идет при температуре
610–630 °С и давлении 0,015–0,02 МПа.
Процесс проводят в реакторах регенеративного типа. В связи с тем, что применяется алюмохромовый катализатор, разбавление сырья водяным паром исключается и разряжение создается вакуум-компрес- сорами.
Регенеративный тип реакторов обусловливает то, что циклы дегидрирования и регенерации катализатора чередуются в одном и том же реакторе. Выделяющееся при регенерации тепло аккумулируется катализатором и используется при дегидрировании. Однако этого тепла не хватает, и для его компенсации в реактор подводится тепло за счет сжигания топлива и подачи на регенерацию горячего кислородсодержащего газа.
Для улучшения теплообмена между газом и катализатором последний смешивается с инертным теплоносителем, представляющим собой плавленый Al2О3, при массовом соотношении 1 : 3.
Катализатор для одностадийного дегидрирования должен обладать высокой активностью и повышенной прочностью, стабильностью и высокой регенерационной характеристикой. Это связано с тем, что во время чередующихся циклов дегидрирования и регенерации катализатора значительно меняются условия, а циклы регенерации очень короткие.
Рассмотрим принципиальную технологическую схему одностадийного дегидрирования н-бутана (рис. 4.3).
Процесс дегидрирования идет в нескольких группах реакторов (3–8 реакторов в каждой группе). Согласно схеме сырье – бутанбутеновая фракция, содержащая 25–35 % н-бутенов – перегревается в печи 1 до 600–620 °С и поступает в часть реакторов 2, где контактирует с катализатором. Температура процесса колеблется в пределах 590–630 °С в конце и начале цикла дегидрирования. Разряжение создается при помощи двух вакуум-компрессоров.
Контактный газ из реактора 2 поступает на охлаждение и далее идет на разделение. После окончания цикла дегидрирования поток сырья переключается на следующую группу реакторов, а реакторы,
103
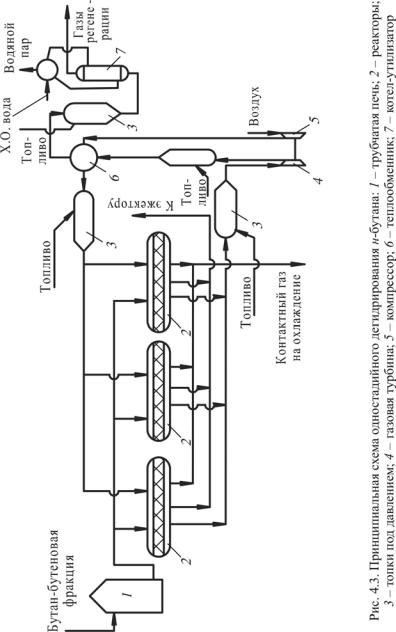
104
бывшие в работе, продуваются для удаления углеводородных паров. После продувки реакторы переключаются на регенерацию топочными газами, содержащими небольшое количество кислорода. Затем идет эвакуация продуктов сгорания пароструйным эжектором, после чего в реакторы вновь начинает поступать поток сырья.
Воздух для регенерации поступает на прием компрессора 5 (давление 0,6 МПа), нагревается в теплообменнике 6 до температуры 520–540 °С, в топке 3 до температуры 630 °С и далее направляется в реактор 2.
Газы регенерации, выходящие из реактора 2, дополнительно нагреваются в топке до температуры, отвечающей рациональному режиму работы газовой турбины 4, из которой охлажденные газы за счет совершения работы с температурой 450 °С поступают в топку 3, нагреваются и далее отдают часть тепла воздуху в теплообменнике 6. После дополнительного подогрева газов регенерации
вследующей топке 3, они используются для генерации водяного пара в котле-утилизаторе 7.
Такая схема позволяет работать без потребления водяного пара и электроэнергии со стороны, но требует повышенного давления
вреакторе в процессе регенерации.
Имеются схемы с пятью, шестью, семью и восьмью реакторами в группе. Переключение реакторов с режима на режим происходит автоматически.
Реакторы представляют собой горизонтальные пустотелые аппараты из стали, футерованные изнутри керамической плиткой. Смесь катализатора и теплоносителя (алунда) насыпается на решетку невысоким слоем. Решетка также выполнена из керамики во избежание коррозии, вызванной восстановительно-окислительной средой при высоких температурах.
Основные достоинства одностадийного процесса:
–более простая схема;
–снижение расходных коэффициентов по сырью;
–уменьшение энергетических затрат.
105
Недостатки одностадийного процесса:
–короткие периоды контактирования, что требует сложной автоматики;
–низкий выход бутадиена-1,3 за проход.
4.1.1.3. Разделение контактного газа дегидрирования
Контактный газ дегидрирования н-бутана и н-бутенов содержит наряду с углеводородами С4 водород, продукты распада (С1–С3) и углеводороды с числом углеродных атомов больше 4. Из этого газа необходимо, прежде всего, выделить фракцию С4 (бутан-бутеновую или бутен-бутадиеновую), направляемую на дальнейшее разделение. В случае одностадийного дегидрирования выделяется фракция, состоящая из бутана, бутенов и бутадиена.
Рассмотрим принципиальную технологическую схему выделения фракции С4 из газа дегидрирования (рис. 4.4).
Согласно схеме газ, сжатый компрессором 1 до 1,3 МПа, охлаждается рассолом до 10 °С в холодильнике-конденсаторе 2. Несконденсировавшийся газ из холодильника-конденсатора 2 направляется в абсорбер 3, где из него извлекаются компоненты С2 и выше. В качестве абсорбента используется остаток колонны 12 (тяжелая фракция контактного газа дегидрирования). Смесь метана и водорода (СН4 + Н2) направляется в топливную сеть, а насыщенный абсорбент поступает через теплообменник 6 в десорбер 5, где отпариваются поглощенные углеводороды. Абсорбент из десорбера 5 после его регенерации возвращается в абсорбер 3. Отпаренные углеводороды из десорбера 5 после конденсации подаются в колонну 11 для выделения фракции С3. Сюда же подается конденсат из холодильникаконденсатора 2.
Из верхней части колонны 11 отбирается фракция С3, которая далее направляется в топливную сеть. Остаток колонны 11 идет в колонну 12 для отделения фракции С5, которая уходит из нижней части, а из верхней части колонны 12 уходит фракция С4.
106
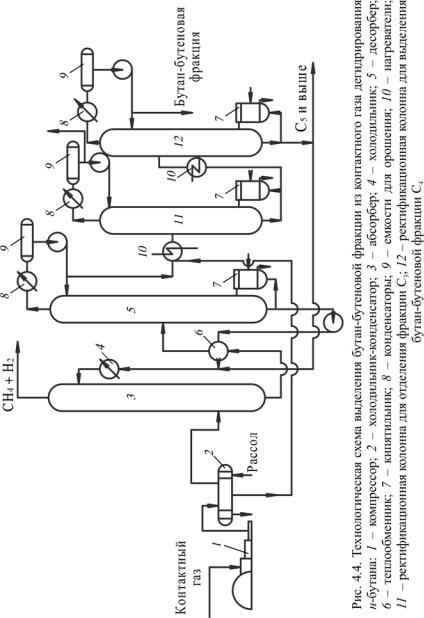
107
Получаемый абгаз (СН4 + Н2) содержит в своем составе значительные количества СО2, N2, но не более 1,5 % углеводородов С4.
Потери целевой фракции С4 с тяжелыми углеводородами не пре-
вышают 0,4–0,5 %.
Процесс разделения контактного газа дегидрирования на второй стадии аналогичен данному процессу разделения контактного газа на первой стадии дегидрирования.
4.1.1.4. Разделение бутан-бутеновой фракции
Для разделения бутан-бутеновой фракции используется метод экстрактивной дистилляции ввиду близости температур кипения углеводородов, подлежащих разделению.
В качестве экстрагентов при этом нашли применение ацетон, ацетонитрил, фурфурол, диметилформалид, N-метилпирролидон.
Процесс экстрактивной дистилляции проходит в тарельчатой колонне, куда наряду с сырьем подается экстрагент. В ректификате колонны концентрируются более насыщенные компоненты, а остаток состоит из экстрагента и ненасыщенных компонентов.
Установка включает отпарную колонну для выделения бутенов из экстрагента, а также аппаратуру для выделения и регенерации растворителя из конечных углеводородных фракций.
Наибольшее применение как наиболее низкокипящий и более эффективный экстрагент получил ацетонитрил (заменив ацетон). Он более селективен, при его использовании в большей степени расширяется интервал летучести бутана и бутенов, он обладает большей растворяющей способностью по сравнению с ацетоном.
Рассмотрим принципиальную технологическую схему процесса экстрактивной дистилляции бутан-бутеновой фракции (рис. 4.5).
Согласно схеме бутан-бутеновая фракция поступает в испаритель 5, где частично испаряется и направляется в нижнюю часть колонны экстрактивной дистилляции 2, которая, в свою очередь, разбита на две колонны по 65 тарелок в каждой. Колонна 2а снабжена кипятильником 1, а колонна 2б – конденсатором 3 и сборникоморошения4.
108
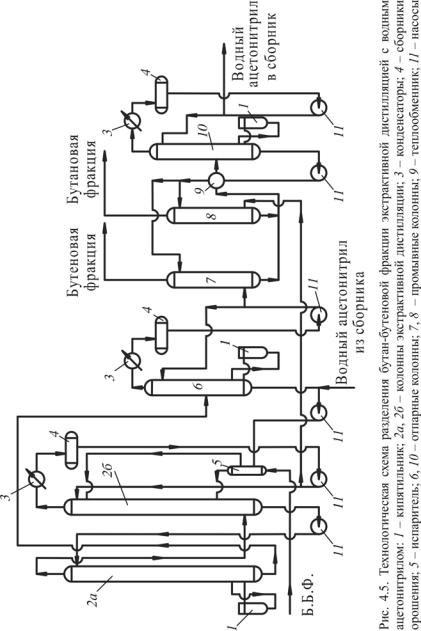
109
В верхнюю часть колонны 2б подается предварительно охлажденный водный ацетонитрил, который стекает по тарелкам вниз навстречу парам углеводородов. Остаток из колонны 2б подается на верхнюю тарелку колонны 2а, а пары из верхней части колонны 2а – под нижнюю тарелку колонны 2б. Из верхней части колонны 2б выходит непоглощенная бутановая фракция, а остаток из колонны 2а представляет собой раствор бутенов в экстракте. Бутеновая фракция направляется в промывную колонну 8, а раствор бутенов в экстракте –
вколонну 6 на десорбцию бутенов. Пары бутенов из колонны 6 конденсируются, часть конденсата возвращается на орошение в колонну 6, а балансовое количество идет на промывку водой в колонну 7. Отмытые фракции выводятся с установки.
Промывные воды из колонн 7 и 8 поступают в отпарную колонну 10 для отгона ацетонитрила от избыточной воды. Вода после отгона ацетонитрила из нижней части колонны 10 используется для орошения колонн 7 и 8.
Ацетонитрил из верхней части колонны 10 конденсируется, часть его идет на орошение, а остальное количество направляется
вкачестве экстрагента в колонну экстрактивной дистилляции 2б. Для предотвращения накопления в экстрагенте тяжелых углеводородов часть его (до 3 %) подвергается очистке ректификацией.
4.1.1.5. Выделение бутадиена-1,3 из бутен-бутадиеновой фракции
Бутадиен высокой чистоты (именно такой нужен для полимеризации) не может быть выделен обычной ректификацией из бутенбутадиеновой фракции вследствие незначительной разности температур кипения разделяемых углеводородов. Для этого применяются методы азеотропной и экстрактивной дистилляции и хемосорбции.
Выделение бутадиена методом хемосорбции основано на раз-
личной способности олефинов и диенов образовывать комплексные соединения с солями одновалентной меди и серебра. На практике в качестве хемосорбента получил применение водно-аммиачный рас-
110