
книги / Основы сварочных работ при сооружении магистральных трубопроводов
..pdfзапорную и регулирующую арматуру и сварочные материалы, которые будут применены для сооружения объекта, а также соответствие маркировки обозначениям, указанным в сертификатах (паспортах).
При отсутствии клейм, маркировки, сертификатов (или других документов, удостоверяющих их качество) трубы, соединительные детали трубопроводов, запорная арматура и сварочные материалы к сборке и сварке не допускаются.
Трубы должны иметь сварное соединение, равнопрочное основному металлу трубы. Сварные швы труб должны быть плотными, непровары и трещины любой протяженности и глубины не допускаются.
Отклонения от номинальных размеров наружных диаметров торцов труб на длине не менее 200 мм не должны превышать ±2 мм величин, приведенных в соответствующих государственных стандартах, по которым допускается применение труб для магистральных трубопроводов.
Овальность концов труб (отношение разности между наибольшим и наименьшим диаметром в одном сечении к номинальному диаметру) не должна превышать 1 %.
Кривизна труб не должна превышать 1,5 мм на 1 м длины, общая кривизна – не более 0,2 % длины трубы.
Косина торцов труб должна быть не более 2 мм.
В металле труб не допускается наличие трещин, закатов, а также расслоений длиной свыше 80 мм в любом направлении. Расслоения любого размера на торцах труб и в зоне шириной 25 мм от торца труб не допускаются.
Трубы по результатам входного контроля должны быть промаркированы на предмет пригодности.
Для дуговой сварки кольцевых стыков магистральных трубопроводов и для автоматической сварки в среде защитных газов для соединения секций труб в нитку могут применяться следующие сварочные материалы:
– электроды покрытые, с покрытиями целлюлозного вида;
81
–проволока сварочная сплошного сечения;
–защитный газ активный и инертный, а также смесь защитных
газов.
Все сварочные материалы перед их использованием должны пройти входной контроль, включающий:
–проверку соответствия марки сварочного материала;
–проверку наличия сертификатов качества завода-изготовителя;
–проверку сохранности упаковки электродов;
–проверку соответствия электродов требованиям по качеству изготовления, разности толщины и механической прочности электродного покрытия;
–проверку сварочно-технологических свойств электродов.
Сварочные материалы следует хранить в соответствии с требованиями изготовителя в условиях, предупреждающих их увлажнение и гарантирующих сохранность и герметичность упаковки.
Электроды непосредственно перед сваркой должны быть просушены или прокалены в соответствии с рекомендациями изготовителя или технологической инструкции.
8. ПОДГОТОВКА ТРУБ К СБОРКЕ И СВАРКЕ
Трубы, соединительные детали трубопроводов, запорная и регулирующая арматура и сварочные материалы должны пройти входной контроль в установленном порядке. Результаты контроля регистрируются в журнале входного контроля.
Применяемые трубы, СДТ, ЗРА и сварочные материалы должны иметь сертификаты (паспорта) качества. До начала производства работ следует проверить соответствие клейм, маркировки труб, СДТ, ЗРА, сварочных материалов обозначениям, указанным в сертификатах (паспортах).
При отсутствии клейм, маркировки, сертификатов (или других документов, удостоверяющих их качество) трубы, СДТ, ЗРА и сварочные материалы к сборке и сварке не допускаются.
82
Следует проверить соответствие формы, размеров, перпендикулярности свариваемых кромок требованиям технических условий на трубы, СДТ, ЗРА.
Следует проверить соответствие минимальных фактических толщин стенок в зоне свариваемых торцов допускам, установленным в технических условиях.
Трубы, СДТ и ЗРА с недопустимыми дефектами на свариваемых кромках, а также на внутренней и наружной поверхностях к сборке не допускаются.
Обработку (переточку) кромок под сварку в случае несоответствия заводской разделки кромок требованиям технологии сварки следует производить механическим способом с использованием специализированных станков.
Допускается осуществлять расточку изнутри трубы («нутрение») шлифмашинками с применением абразивных шлифовальных кругов. После «нутрения» следует проверить соответствие минимальной фактической толщины стенки в зоне свариваемых торцов допускам, установленным в технических условиях на трубы, а также соответствие угла внутреннего скоса кромок более толстой трубы. Качество выполнения «нутрения» фиксируется соответствующим протоколом визуально-измерительного контроля.
Допускается производить резку труб для выполнения специальных сварочных работ (например, захлестов) с применением оборудования для механизированной орбитальной газокислородной или воздушно-плазменной резки с последующей обработкой резаных торцов труб специализированным станком для подготовки требуемой разделки кромок.
При этом металл кромок должен быть удален станком на глубину не менее 1,0 мм.
При использовании труб с обработанными специализированными станками торцами необходимо, чтобы форма и геометрические параметры кромок, а также качество подготовки свариваемых кромок соответствовали требованиям технических условий и операционной технологической карты.
83
Контроль точности обработки кромок под сварку и параметров разделки выполняется инструментально.
Перед сборкой необходимо очистить внутреннюю полость труб, СДТ и ЗРА от попавшего грунта, снега и прочих загрязнений, а также механически очистить (шлифмашинкой с дисковой проволочной щеткой или абразивным кругом) до металлического блеска кромки и прилегающие к ним внутреннюю и наружную поверхности соединяемых элементов на ширину не менее 15 мм.
Усиление заводских швов снаружи трубы следует удалить до величины от 0,5 до 1,0 мм на участке шириной от 10 до 15 мм от торца трубы.
Перед сборкой следует осмотреть поверхности кромок свариваемых элементов. Устранить шлифованием на наружной поверхности неизолированных торцов труб царапины, риски, задиры глубиной до 5 % от нормативной толщины стенки, но не более минусовых допусков на толщину стенки, оговоренных техническими условиями на трубы.
Не разрешается производить ремонт любых повреждений поверхности трубы, включая вмятины на концах труб, забоины и задиры фасок кромок свариваемых элементов. Поврежденный участок трубы должен быть обрезан, а требуемая разделка кромок выполнена специализированным станком. При этом металл резаных кромок должен быть удален станком на глубину не менее 1,0 мм.
После обрезки (вырезки) участка с недопустимыми дефектами с целью выявления возможных расслоений следует выполнить ультразвуковой контроль сплошным сканированием всего периметра участка трубы, прилегающего к торцу, на ширине не менее 40 мм.
Если в процессе ультразвукового контроля выявлено наличие расслоений, труба должна быть обрезана на расстоянии не менее 300 мм от торца и произведен ультразвуковой контроль.
Смещение кромок труб с одинаковой нормативной толщиной стенки не должно превышать 2,0 мм. Допускаются локальные смещения кромок до 3,0 мм при общей протяженности участков с указанными смещениями не более 1/6 периметра свариваемого соединения.
84
Измерение величины смещения кромок при сборке следует выполнять универсальными шаблонами по наружным поверхностям или специализированными шаблонами по внутренним поверхностям свариваемых элементов.
Сборку труб следует выполнять с применением внутренних центраторов гидравлического или пневматического типов. Центратор не должен оставлять царапин, задиров, масляных пятен на внутренней поверхности труб. В случае применения труб с внутренним гладкостным покрытием перед началом работ должна быть проведена подготовка центратора, позволяющая обеспечить целостность покрытия.
При сборке захлестных соединений труб, прямых вставок (катушек), соединений труб с СДТ и ЗРА, а также в других случаях (например, выполнение работ на уклонах), когда применение внутренних центраторов технически невозможно, сборку соединений следует выполнять на наружных центраторах преимущественно с гидравлическим приводом.
При сборке запрещается любая ударная правка (подгонка) кромок свариваемых элементов.
При сборке заводские швы следует смещать относительно друг друга на расстоянии не менее чем 100 мм (рекомендуется 250 мм и более). При этом они должны располагаться в верхней половине периметра свариваемых элементов.
Величина зазора стыковых соединений свариваемых элементов устанавливается в зависимости от применяемого способа сварки, диаметра сварочного материала и приведена в табл. 7.
Сборку на внутреннем центраторе неповоротных кольцевых сварных соединений труб с заводской разделкой кромок или кромками, подготовленными механическим способом специализированными станками, следует осуществлять без прихваток. Если в процессе установки технологического зазора возникла объективная необходимость в установке прихваток, то они должны быть полностью удалены механическим способом (абразивным кругом) в процессе сварки корневого слоя шва.
85
Таблица 7
Величина зазоров в сварных соединениях, выполняемых различными способами сварки
|
|
Диаметр |
|
|
|
|
|
Способ сварки |
|
электрода |
Величина зазора, мм |
||||
|
или сварочной |
||||||
|
|
проволоки, мм |
|
|
|
|
|
Автоматическая сварка в среде |
0,9 / 1,0 |
Без |
зазора. |
Допускается |
|||
защитных газов на оборудова- |
|
наличие зазора не |
более |
||||
нии CRC-Evans AW |
|
|
0,5 мм на участках стыка |
||||
|
|
|
длиной до 100 мм |
|
|||
Автоматическая сварка в среде |
1,0 |
Без |
зазора. |
Допускаются |
|||
защитных газов на оборудова- |
|
локальные |
зазоры |
до |
|||
нии Saturnax фирмы |
Serimer |
|
0,5 мм на длине до 100 мм |
||||
Dasa |
|
|
|
|
|
|
|
Ручная дуговая сварка элек- |
2,5 / 2,6 |
От 2,0 до 3,0 включительно |
|||||
тродами с основным |
видом |
|
|
|
|
|
|
3,0 / 3,2 |
От 2,5 до 3,5 включительно |
||||||
покрытия |
|
||||||
Ручная дуговая сварка элек- |
|
От 1,0 до 2,5 включительно |
|||||
тродами с целлюлозным видом |
3,2 4,0 |
|
|
|
|
||
От 1,5 до 2,5 включительно |
|||||||
покрытия (на спуск) |
|
|
|||||
Ручная дуговая сварка элек- |
3,2 |
От 1,5 до 3,5 включительно |
|||||
тродами с целлюлозным видом |
|
|
|
|
|
||
покрытия (на подъем) |
|
|
|
|
|
|
|
Механизированная сварка ме- |
1,14 |
От 2,5 до 4,0 включительно |
|||||
тодом STT |
|
|
|
|
|
|
|
Двусторонняя автоматическая |
3,0 / 3,2 / 4,0 |
Без |
зазора. |
Допускается |
|||
сварка под флюсом |
|
|
наличие зазора не |
более |
|||
|
|
|
0,5 мм на участках стыка |
||||
|
|
|
длиной до 100 мм |
|
|||
Автоматическая сварка в среде |
1,0 |
Без |
зазора, |
допускаются |
|||
защитных газов на оборудова- |
|
локальные зазорыдо 0,5 мм |
|||||
нии СWS.02 фирмы Pipe |
|
на длине до 100 мм |
|
||||
Welding Technology |
|
|
|
|
|
|
|
Механизированная сварка са- |
1,6 (1,7) |
От 2,5 до 3,5 |
|
|
|||
мозащитной порошковой про- |
|
|
|
|
|
||
волокой типа «Иннершилд» |
|
|
|
|
|
86
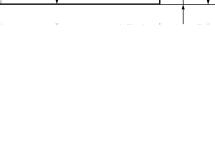
9. РАСКЛАДКА ТРУБ
Трубы или трубные секции укладывают на бровке траншеи на инвентарных лежках под углом к оси траншеи таким образом, чтобы к их торцам был свободный доступ. Расстояние от грунта до нижней образующей трубы для труб диаметром 1420 мм должно быть не менее 300 мм.
Впроцессе раскладки необходимо провести визуальный осмотр труб, соединительных деталей и арматуры. На поверхности труб или деталей не допускаются:
– трещины, плены, рванины, закаты любых размеров;
– царапины, риски и задиры глубиной более 0,4 мм;
– местные перегибы, гофры и вмятины;
– расслоения на концах труб.
Вслучае трудности идентификации расслоения рекомендуется цветная дефектоскопия.
Если обнаружены расслоения, то по результатам дополнительного ультразвукового контроля концы труб с расслоением подлежат вырезке.
Допускается ремонт сваркой дефектов кромок труб (забоин, задиров) глубиной не более 5 мм с последующей механической зачисткой мест исправления дефектов до восстановления необходимого скоса кромок.
Концы с дефектами глубиной более 5 мм должны быть отрезаны.
Концы труб и соединительных деталей должны иметь форму и размеры скоса кромок,
соответствующие |
применяе- |
Рис. 26. Геометрические параметры: |
мым процессам сварки (рис. 26). |
В = 9 ± 0,5 для толщины стенки |
При их несоответствии до- |
15 < S ≤ 19 мм |
|
пускается механическая обра- |
||
|
87
ботка кромок непосредственно в трассовых условиях машиной подготовки кромок типа МПК. Машины подготовки кромок предназначены для обработки и зачистки торца и фасок под сварку на трубах для магистральных трубопроводов, выпускаются с электрическим
игидравлическим приводом.
10.СБОРКА СТЫКОВ ТРУБ
Сборка стыков труб должна гарантировать:
–перпендикулярность стыка оси трубопровода;
–отклонение от перпендикулярности не должно превышать 2 мм;
–равномерность технологического зазора;
–минимально возможную величину смещения кромок. Предварительный подогрев стыков – одна из наиболее ответст-
венных технологических операций, требующая жесткого контроля при выполнении сварки неповоротных стыков в линейном потоке.
Предварительный подогрев при сварке трубопровода 1420×17 из стали не требуется, так как Сэ < 0,45 %.
Непосредственно перед прихваткой или сваркой корневого слоя шва производится просушка торцов труб и прилегающих к ним участков.
Просушка торцов труб путем нагрева до 50 °С обязательна:
–при наличии влаги на трубах независимо от температуры окружающего воздуха;
–при температуре окружающего воздуха ниже 5 °С. Предварительный и, при необходимости, сопутствующий по-
догрев следует осуществлять нагревательными устройствами (газовыми или электрическими), обеспечивающими равномерный нагрев металла по всему периметру свариваемого стыка. Ширина зоны равномерного нагрева металла в каждую сторону от оси шва должна быть не менее 75 мм.
Предварительный и сопутствующий подогрев, как и послесварочная термообработка, не должны нарушать целостность наружной изоляции трубы.
88
Контроль температуры предварительного и/или сопутствующего подогрева следует выполнять перед началом сварки на расстоянии до 15 мм от торца трубы и в пределах 60–75 мм не менее чем в трех точках по периметру трубы. Замерять температуру следует контактными термопарами или термокарандашами.
При использовании внутреннего центратора, сборка труб может осуществляться преимущественно выполнением непосредственно корневого слоя без прихваток.
При сборке стыков на наружных центраторах количество прихваток – не менее четырех, равномерно распределенных по периметру стыка, длиной не менее 200 мм.
Прихватки следует выполнять не ближе 100 мм от продольных швов трубы (детали, арматуры).
Приварка временных технологических креплений (планок, скоб
ит.п.) к телу трубы (детали, арматуры) запрещается.
Впроцессе сборки должно быть исключено попадание масла, влаги и других загрязнений в разделку и зазоры соединений, а также на прилегающие к разделке поверхности труб и деталей.
Изготовление секций из труб на трубосварочных базах типа БТС. Механизированные трубосварочные базы (БТС) позволяют полностью механизировать сварочно-монтажные работы за счет применения метода двухсторонней автоматической сварки под слоем флюса стыков труб с увеличенным притуплением кромок.
Перед сваркой необходимо осуществить подготовительные операции и обработку кромок (рис. 27).
Взависимости от типа применяемого оборудования последовательность наложения слоев шва может быть следующей:
– сварка наружных слоев шва и последующая сварка внутреннего слоя;
– сварка первого наружного слоя и последующая одновременная сварка второго наружного и внутреннего слоев шва.
Для предотвращения непроваров и шлаковых включений автоматическую сварку прихваток и начального участка шва не следует
89
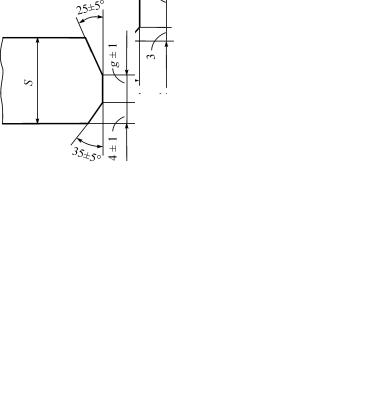
выполнять при значениях тока ниже нижнего предела диапазона режимов сварки.
а |
б |
Для труб диаметром до 1020 мм |
Для труб диаметром 720–1420 мм |
S = 6,0–10,9 мм |
S = 11,0–18,0 мм |
в г
Рис. 27. Типы разделки кромок труб для двусторонней автоматической сварки под флюсом
Начало и окончание сварки стыка должны располагаться на расстоянии не менее 100 мм от продольных швов свариваемых труб.
90