
книги / Разработка подводных шельфов
..pdfподствующего направления ветра. Укладка пород в выработанное пространство может осуществляться с применением специальных защитных устройств. Для защиты карьера от заносимости породами отвалов могут быть применены:
–пневмо- и гидрозащита;
–выработки, пройденные между карьером и отвалом;
–подводная дамба, отсыпанная не на всю глубину воды.
Применение специальных защит не исключает частичного попадания отвальных пород в забой. Однако при комбинировании с другими технологическими схемами их применение может быть достаточно эффективным.
Частичное разубоживание полезного ископаемого сбрасываемыми в отвал породами может быть допущено при условии, что дополнительные затраты на разработку и обогащение, за счет снижения содержания полезных компонентов, не будут превышать затрат на транспортирование хвостов на внешние отвалы. Общие затраты на добычу единицы объема чернового концентрата при внутрикарьерном отвале не должны превышать общих затрат при транспортировании хвостов и вскрышных пород на внешние отвалы.
Размещение отвалов за пределами карьерного поля производится в тех случаях, когда не представляется возможным уложить отвальные породы в выработанное пространство. Необходимость внешних отвалов может быть продиктована как горно-геологической характеристикой месторождения, так и динамикой моря в месте проведения горных работ. Во внешние отвалы породы также укладываются в начальный период ведения горных работ, пока не создан объем выработанного пространства для размещения отвальных пород.
Внешние отвалы могут быть расположены на бортах подводного карьера за пределами карьерного поля, в определенных местах моря и на берегу. Располагать отвалы на бортах карьера можно при тех же условиях, что и при укладке пород в выработанное пространство. Существенное отличие будет иметь размещение отвалов по бортам карьера при разработке россыпей, вытянутых вдоль береговой линии на большие расстояния и малой их мощности и ширине. Отработка каждого участка такого месторождения производится в короткие сроки, и разубоживание полезного ископаемого за счет отвальных пород не произойдет или будет незначительным.
Подводная добыча полезных ископаемых на малых глубинах, где течение и волновые процессы охватывают всю толщу воды, имеет свои специфические особенности. В этой зоне отвалы подвержены интенсивному
31

разносу, а карьеры – заносимости. Отвалы при этом неустойчивы, иногда срок их существования небольшой и зависит от динамики моря в районе горных работ, поэтому при проектировании работ по отвалообразованию необходимо учитывать факторы разноса отвалов и заносимости карьеров. За счет заносимости увеличивается объем вскрышных и отвальных работ.
Для прогнозирования явления заносимости можно воспользоваться расчетными зависимостями, предложенными П.Б. Шаповаловым:
δ = (1−k ) H ,
H0
где δ – годовая толщина слоя наносов, м; Н – глубина на выемке, м; Н0 – естественная глубина моря, м;
k – поправочный коэффициент от 0 до 1.
В процессе разработки месторождений полезных ископаемых, при наличии наносонесущего потока, необходимо учитывать объем наносов, поступающих как во вскрышной, так и в добычной забой.
При вскрытии площадь полезного ископаемого, м,
S = HVдоб−kHв0 ,
где Vдоб – объем вскрытого полезного ископаемого, м3; kв – коэффициент вскрыши, м3/м3. Дополнительный объем за счет наносов, м3,
∆V = |
Vдобkв |
(1−k ) |
H |
|
t |
, |
|
|
|
||||
вск |
H − H0 |
|
H0 T |
|||
|
|
где t – время отработки вскрытой площади полезного ископаемого; Т – время ведения горных работ в году.
Тогда общий объем вскрыши за время t, м3,
|
|
|
(1+k ) |
H |
|
|
|
|
|
|
|
|
|
|
|
t |
|
||
|
|
|
H |
|
|
|
|||
V |
=V k 1 |
+ |
|
0 |
|
|
. |
||
H − H0 |
|
|
|
|
|||||
вск |
доб в |
|
|
|
|
T |
|||
|
|
|
|
|
|
|
|
|
|
|
|
|
|
|
|
|
|
|
|
При разработке вдольбереговых титано-циирконовых россыпей Восточной Балтики и титаномагнетитовых россыпей Охотского и Черного морей во время волнений дополнительный объем наносов, поступающих в выработку, был значительным, а в отдельных случаях выработки были полностью занесены.
32
К расчету объемов разносимых пород отвалов необходимо в каждом конкретном случае подходить индивидуально. Намытый в течение 9 дней отвал при разработке титано-циркониевой россыпи Балтийского моря объемом 40 000 м3 был полностью разнесен за 45 дней. Весь объем песков отвала поступил в наносонесущий вдоль береговой поток. Пути переноса песков отвала и их объемы были определены с помощью меченых песков, уложенных в тело отвала. Практикой дноуглубительных работ установлено, что в открытом море вынутую породу, во избежание попадания ее в выработки, целесообразно располагать не ближе 1,5–2 км от выработок по направлению господствующих движений водных масс. В закрытых бухтах, лагунах с малой глубиной эти расстояния могут быть сокращены вдвое. Технологические схемы с расположением отвалов на берегу при плавучем и добычном обогатительном комплексе наиболее трудоемки и могут быть применены в случае отсутствия необходимых площадей под отвалы в море, а также в ситуации сложной динамики моря в районе горных работ. Укладка хвостов обогащения при береговой обогатительной фабрике в гидроотвалы не отличается от технологии отвалообразования при ведении горных работ на суше.
При решении технологической схемы по выбору местоположения отвала и способа укладки пород в отвал при ведении горных работ в море необходимо учитывать затраты по возмещению ущерба, нанесенного биологическим ресурсам в прилегающих к карьеру районах моря.
33

МОДУЛЬ II
6. Технические средства добычи твердых полезных ископаемых со дна морей и океанов
Большинство технических средств добычи твердых полезных ископаемых со дна морей и океанов были разработаны во второй половине ХХ в. Представим общий обзор всех типов созданных в этот период технических средств, так как большинство из тех, что создавались в ХХ в., используются и сейчас.
По сравнению с объемом добычи морской нефти и газа объем добычи твердых морских полезных ископаемых менее значителен и в среднем составляет всего несколько процентов мировой добычи на суше. Однако для различных видов сырья эта величина колеблется в широких пределах, что объясняется, в частности, степенью доступности подводного сырья (подводных залежей) для разработки. Так, продукция морских россыпей уже сейчас составляет около 30 % добычи из «сухопутных» россыпей. Истощение «сухопутных» месторождений вызвало в последние годы повышенный интерес к добыче морских полезных ископаемых и привело к совершенствованию применяемых для этой цели технических средств.
Следует отметить, что помимо истощения сухопутных месторождений развитие морского горного дела стимулируется в некоторых странах общим недостатком сырьевых ресурсов. Примером тому может служить Япония, где ввиду острого дефицита железорудных ресурсов ведется интенсивная разведка и добыча титаномагиетитовых железистых песков на шельфовых месторождениях. Причем объем добычи начал стремительно расти еще во второй половине ХХ в.: с 30 тыс. т в 1970 г. до 20 млн т в 1982 г.
На несколько особом положении стоит добыча драгоценных металлов и алмазов, потребность в которых также постоянно растет. Например, в США основные запасы золота на суше (до 2,5 тыс. т) выработаны к 2008 г., поэтому в настоящее время ведутся интенсивные разведочные работы на континентальном шельфе, где уже открыты месторождения с общими запасами 1,5 тыс. т. Из морских россыпей в заливе Good News на побережье Беренгова моря США добывают 90 % всей производимой в стране платины. За время эксплуатации месторождения на нем было добыто 200 т сырой платины, а ежегодная добыча в настоящее время доведена до 500 кг в год.
Помимо перечисленных полезных ископаемых большое значение в мировом производстве имеет подводная добыча тяжелых минералов,
34
в первую очередь рутила и циркона. Их удельный вес в мировом производстве титана и циркония достиг соответственно 90 и 75 % (в основном за счет разработки прибрежных морских россыпей Австралии).
Главное место в прибрежных разработках в настоящее время все же принадлежит подводной добыче строительных материалов, составляющих примерно половину всего объема добычи твердых полезных ископаемых.
По мнению специалистов, в ближайшие годы подобное положение существенным образом изменится благодаря интенсивному росту потребления сырья и связанному с ним переходу на более богатые и рентабельные подводные месторождения, в которых среднее содержание полезных компонентов, как правило, в несколько раз превышает аналогичные показатели «сухопутных» месторождений. Создание эффективных технических средств подводной добычи позволило уменьшить расходы на получение готовой продукции. Так, средняя стоимость 1 т оловянного концентрата, извлекаемого из морских месторождений, примерно в полтора раза меньше стоимости 1 т «сухопутного» концентрата.
Выбор способов разработки морских месторождений полезных ископаемых определяется как типом месторождения, так и природноклиматическими условиями участка работ, в частности его удаленностью от берега и глубиной моря. Например, россыпные месторождения вблизи берегов на глубинах до 5 м успешно разрабатываются канатно-скре- перными установками, размещаемыми на берегу. Этот способ получил широкое распространение в Германии, США и Японии, где создано большое число установок этого типа. Основной проблемой здесь является монтаж и перебазирование задней опоры, располагающейся в море. Один из вариантов ее разрешения – монтаж опоры на специальной тележке, передвигающейся по рельсам, уложенным на дне вдоль береговой линии. При этом обеспечивается непрерывная разработка подводного карьера. Береговые опоры в этом случае монтируются на салазках и перемещаются тяговыми лебедками или имеют собственный привод. Другая характерная особенность береговых опор – их большая высота, необходимая для того, чтобы уменьшить длину соприкосновения тягового троса с дном и сократить длину пути волочения ковша по дну при чрезвычайно большой общей длине хода ковша.
Технологию скрепирования можно усовершенствовать, применив колесные ковши, приводимые в движение собственными двигателями или бесконечным тросом лебедки, которая устанавливается на берегу. Второй тип привода используется в канатно-скреперной установке (рис. 8), разработанной на базе самоходного экскаватора. Она включает в себя стрелу большой длины с подпорной стойкой и высокоскоростной лебедкой, трос
35
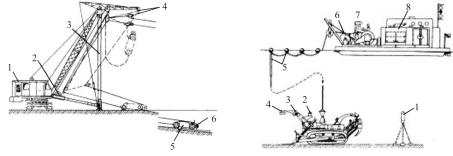
которой пропущен через систему блоков, и лебедку, смонтированную на колесном ковше (скрепере) и связанную с осью ведущих колес ковша при помощи редуктора. Протаскивание троса через барабан лебедки ковша против часовой стрелки заставляет ковш перемещаться в море, а при обратном движении – выходить на берег, где ковш при помощи вспомогательной системы роликов поднимается на стреле и опрокидывается.
Рис. 8. Канатно-скреперная |
Рис. 9. Дистанционно управляемый |
установка с колесным |
подводный бульдозер: |
самоходным скрепером: |
1 – приемник; 2 – ультразвуковой |
1 – экскаватор; 2 – лебедка; |
излучатель; 3 – видеокамера |
3 – подпорная стойка; 4 – система |
с прожектором; 4 – гидролокатор; |
блоков; 5 – скрепер; 6 – лебедка |
5 – поплавки; 6 – тросовая лебедка; |
скрепера |
7 – пульт управления; 8 – генератор |
Другой вариант разработки прибрежных россыпей, проводимой японскими компаниями, основан на использовании самоходных дистанционно управляемых бульдозеров. Одна из первых моделей, разработанная фирмой Kamatsu в 1968 г., прошла успешные испытания на глубинах до 20 м. Производительность бульдозера, перемещавшего грунт на расстояние 10 м, была порядка 40 м3/ч (рис. 9). Одна из последних моделей установки включает в себя обеспечивающее судно-катамаран водоизмещением 210 т. В качестве главного двигателя используется дизель мощностью 270 кВт. Бульдозер работает от генератора переменного тока мощностью 300 кВт при напряжении 3300 В.
Электроэнергия подается по кабель-тросу длиной 150 м, намотанному на барабан кормовой лебедки. Спуск рабочего механизма на дно осуществляется краном грузоподъемностью 40 т. Для точного позиционирования установки на дне применяется акустическая система. Подводные бульдозеры выпускаются также компанией Hitachi.
Современные подводные бульдозеры можно использовать на весьма значительных глубинах моря (до 60 м) в комплексе со специальными сис-
36
темами для подъема горной массы. Примером такой системы служит установка, разработанная и построенная в 1971 г. фирмой «Мицуи кайе кайхацу». Она представляет собой затапливаемый в месте работ понтон длиной 107,5 м, шириной 32 м и высотой 21 м. Комплекс установленного на нем оборудования включает в себя три крана с грейферными захватами, три погрузочных конвейера и два разгрузочных транспортера. Краны поднимают грунт на поверхность, конвейеры загружают его в трюмы, транспортеры перегружают добытую горную массу на грузовые суда. Производительность комплекса – 250 т/ч.
В подавляющем большинстве случаев разработка подводных месторождений твердых полезных ископаемых, расположенных в рыхлых грунтах, производится с помощью драг. Среди них принято выделять установки черпающего типа (грейферные, одночерпаковые и многочерпаковые)
ивсасывающие установки (с грунтовыми насосами, эжекторные и эрлифтные).
Выбор типа драги зависит как от глубины моря, так и от условий залегания и вида полезного ископаемого. Например, одноковшовые грейферы рационально использовать на месторождениях с мощной продуктивной толщей, так как одно из важнейших преимуществ снарядов этого типа – возможность проведения работ на больших глубинах моря и в условиях волнения. Их весьма эффективно использует, например, канадская компания «Грейт Кэнэйдьен ойл сэндз», добывающая с помощью трех грейферных установок нефтеносные пески, залегающие слоем в 60 м на глубине 610 м. Годовая производительность трех установок достигает 300 тыс. т, что при среднем содержании нефти 17 % обеспечивает высокую рентабельность работ.
Сдругой стороны, при добыче такого полезного ископаемого, как алмазы, залегающие в галечниковых отложениях, расщелинах и изломах донных пород, могут успешно применяться маневренные эрлифтные установки. Они позволяют одновременно обогащать поднимаемый материал
исбрасывать отработанную породу непосредственно в месте добычи. Так, производительность добывающего судна «Дайманкус» водоизмещением 3812 т на глубине моря до 120 м составила 300 т/ч твердого материала. Работали три эрлифтные установки с диаметром всасывающего отверстия 406 мм и диаметром пульпопровода 460 мм. Пульпа поступала в обогатительную установку, последовательно проходя обезвоживающий сепаратор диаметром 2,1 м, классификатор, аккумулирующий бункер, смесительный конус и сепаратор с тяжелой средой, в котором легкий материал поднимался вверх и удалялся, а тяжелая фракция, включая алмазы, разгружалась на сортировочный стол.
37
Подводные песчаные и гравийные карьеры разрабатываются с помощью земснарядов, способных поднимать большое количество материала, не нуждающегося в обогащении, тогда как для добычи залегающих на дне руд, содержащих олово, железо, золото и т.д., как правило, необходимы земснаряды с режущей головкой или многоковшовые драги, обеспечивающие разрыхление продуктивного слоя, полное его отчерпывание на всю глубину до подстилающего слоя и обогащение добываемой горноймассы.
Многочерпаковые установки широко применяются на глубине моря порядка 15–20 м, хотя известны установки, приспособленные для работы на глубинах до 50 м. В качестве примера можно привести индонезийскую государственную корпорацию «П.Н. Тимах», ведущую интенсивную добычу кассетерита в проливах между островами Суматрой и Банка с помощью 13 многочерпаковых драг. Крупнейшая из них «Банка-1», построенная в 1966 г. компанией «Саймоне – Лобнитц» (Шотландия), представляет собой прямоугольную несамоходную баржу длиной 91,5 м, шириной 24,4 м, высотой борта 4,9 м с осадкой 3 м. Она работает на глубине моря до 40 м, бесконечная цепь перемещает 142 черпака вместимостью по 0,5 м3 со скоростью 6,7 м/мин. Суммарная мощность двигателей равна 2800 кВт, четыре дизельных двигателя мощностью по 450 кВт используются для привода черпаковой цепи. Стоимость драги 6,7 млн долл. Годовая производительность составляет 2400 т оловянного концентрата, который содержит 50 % беспримесного олова.
Землесосные снаряды с рыхлителями различных типов работают в более глубоких водах. Например, канадская фирма «Сидбэк» использует их на разработке низкокачественной россыпи магнетитовых песков (месторождение Дьювэль) у северного побережья залива Святого Лаврентия. Годовая производительность снаряда длиной 91,44 м, шириной 29,26 м и высотой борта 5,48 м составляет 762 тыс. т первичного концентрата. Мощность фрезерного рыхлителя равняется 2240 кВт, а мощность привода 812-миллиметровых грунтозаборных насосов – 1500 кВт. Исходный материал по подъемному трубопроводу поступает на решетки для отделения крупных включений. Отсев идет в приемный бункер, а затем четыре центробежных насоса подают материал в ротационные распределители, каждый из которых питает 16 магнитных сепараторов. Полученный концентрат перекачивается на берег, где подвергается вторичному обогащению, а отходы сбрасываются в выработанный котлован.
Производительность землесосов можно повысить, расширив подводный забой с помощью специальных грунтозаборных установок, подающих
38
горную массу к трубопроводу. Кроме того, в этом случае удается уменьшить влияние морского волнения на работу грунтоприемного устройства
идраги. Так, японские инженеры разработали специальное устройство, снабженное механизмами для срезания и подгребания разрабатываемого грунта к всасывающему трубопроводу землесоса. Устройство представляет собой смонтированную на салазках раму с двумя балластными цистернами, на которой размещены герметичный машинный блок с электродвигателями и контрольно-аварийной аппаратурой, а также вращающийся шнековый нож диаметром 0,6 м и длиной 2,2 м. Спуск устройства на дно
иего всплытие, а также изменение угла наклона шнека к забою, т.е. регулировка его заглубления в грунт, осуществляется изменением плавучести цистерны. Исходным параметром для регулировки заглубления шнека
иизменения скорости буксировки служит консистенция пульпы, контролируемая с помощью конситомера. Принцип работы прибора основан на определении массы участка пульпопровода с пульпой. Показания прибора передаются на панель управления. Испытания показали, что одновремен-
ная эксплуатация трех таких устройств позволяет отрабатывать забой шириной до 10 м с суммарной производительностью до 300 м3/ч при максимальной концентрации твердого вещества в пульпе до 52 %.
Помимо разработки подводных россыпных месторождений в рыхлых отложениях морского дна, в настоящее время ведется интенсивная подводная добыча твердых полезных ископаемых из коренных месторождений, залегающих под морским дном. Среди них наибольшее значение имеют барит, железная и никелево-медная руда, сера, каменный уголь
иизвестняк, добываемые на более чем 100 подводных рудниках в прибрежных водах Австралии, Греции, Ирландии, США, Финляндии, Великобритании, Чили и Японии.
Примером разработки подводных рудных месторождений с помощью взрыва может служить американский рудник Kestel Island Mine на Аляске, где с 1969 г. ведется добыча барита из рудного тела (замещенный баритом известняк мощностью залегания 30 м), перекрытого толщей рыхлых отложений и слоем воды 30–40 м. В настоящее время продукция рудника составляет 15 % общей добычи барита в стране.
Ведется также интенсивная разработка природной серы в донной толще Мексиканского залива. Учитывая очень высокое качество получаемого продукта (до 99,9 % серы), можно считать рентабельной добычу на расстоянии до 175 км от берега из пластов, залегающих на глубинах до 350 м под дном. Добыча ведется расплавлением серы по методу Фраша: в продуктивных пластах бурят скважины и опускают в них колонну из че-
39
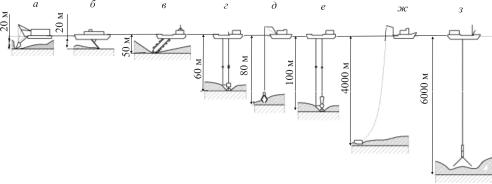
тырех концентрических труб, из которых наружная (обсадная) труба достигает кровли пласта, а вторая – его подошвы. В пространство между второй и третьей трубами в скважину под давлением 1,5 МПа подается перегретая вода при температуре не менее 160°, которая через специальную перфорацию проникает в трещины серосодержащей породы. При этом сера выплавляется, а подаваемый в скважину под давлением 7 МПа воздух вспенивает серонасыщепную жидкость, выводимую эрлифтом на поверхность.
Все рабочее оборудование рудника монтируется на свайных основаниях, соединенных с основной эксплуатационной платформой при помощи эстакад длиной до 2 км. Глубина моря в месте установки оснований не превышает 15 м.
Рис. 10. Технические средства добычи полезного ископаемого шельфовой зоны в зависимости от глубины разработки: а – плавучие платформы
с добычным оборудованием; б – штанговые земснаряды; в – многочерпаковые драги; г – земснаряды со свободным всасом; д – грейферные драги;
е – драглайн; ж – самоходные добычные устройства; з – глубоководные гидравлические драги
Шахтный способ разработки подводных месторождений получил широкое распространение, в частности при подводной добыче каменного угля, на долю которой в Японии, например, приходится более 25 % всей продукции угольных шахт страны. Добыча ведется с помощью выработок, проходимых с берега (месторождение «Убе» на острове Хонсю), а также посредством создания искусственных (месторождение «Такасима») или использования естественных (месторождение «Мики») островов. Кроме Японии интенсивная добыча угля из подводных месторождений ведется в Великобритании и Канаде.
Общий обзор технических средств добычи полезных ископаемых со дня шельфовой зоны представлен на рис. 10.
40