
книги / Снижение экологической нагрузки при обращении со шлаками черной металлургии
..pdf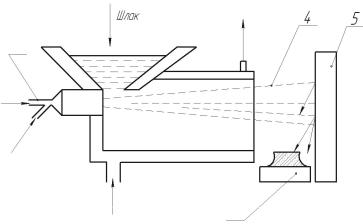
(рис. 6.8) струя энергоносителя 2 (сжатый воздух или пар) эжектирует воду 3, а образующаяся эмульсия с высокой кинетической энергией воздействует на струю стекающего с приемной камеры 1 шлака, разбивая его, вспучивая и охлаждая. Вспученный шлак 4 с высокой кинетической энергией вылетает из аппарата в виде снопа раскаленных гранул, ударяется о водоохлаждаемый экран 5, конгломерируется и опадает с него в виде плоских кусков на пластинчатый транспортер 6. Во время движения на транспортере полученный продукт слипается и окончательно охлаждается, образуя застывшую массу. Эта масса поступает на дробление и сортировку, а полученный песок и шлакопемзовый щебень транспортируются в соответствующие штабеля. Струйные аппараты обладают следующими преимуществами: относительная долговечность из-за отсутствия движущихся частей, контактирующих с расплавленным шлаком; простота конструкции, обусловливающая дешевизну изготовления и обслуживания.
1 |
|
|
|
|
|
|
Шлак |
|
|
4 |
|
|
|
3 |
|
|
5 |
|||
|
|
|
|
|
||
|
|
|
|
|
|
|
|
|
|
|
|
|
2
3
3 |
6 |
|
Рис. 6.8. Схема струйного аппарата для получения шлаковой пемзы [3]
При использовании бассейнового способа шлаковый расплав выливается в стационарный или опрокидной металлический бассейн, в который через перфорированное днище под давлением 0,4–0,6 МПа подается вода. Под воздействием образуемого пара и выделяемых газов происходит вспучивание расплава. Образуе-
241
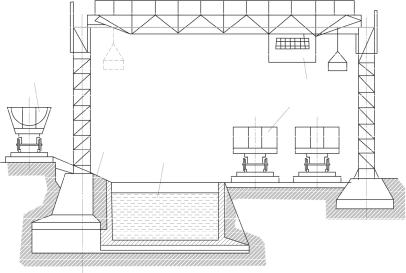
мые глыбы пористого материала дробятся и рассеиваются на фракции. Стационарные и опрокидные установки различны по способу выгрузки: в первых она выполняется с помощью экскаваторов или скреперов, а во вторых – опрокидыванием бассейна.
Грануляция шлака в бассейнах (рис. 6.9) – самый старый и простой способ. При бассейновом способе расплав из ковша сливают в бассейн с водой. Шлаковый расплав выгружается грейферным краном на площадку для вылеживания и обезвоживания или подается непосредственно в вагоны. Однако гранулированный шлак, полученный мокрым способом, при сливе из ковша в заполненный водой бассейн содержит 25–30 % влаги, которая не только является балластом, но и при хранении и транспортировке в зимнее время затрудняет погрузку и выгрузку и увеличивает их стоимость, является причиной смерзания масс. Расход воды при такой грануляции составляет около 3 м3/т, и для сушки продукта перед помолом требуется дополнительная затрата тепла (топлива).
1 |
3 |
4
2
5
Рис. 6.9. Схема бассейновой установки для грануляции шлака: 1 – шлаковозный ковш; 2 – откос; 3 – грейферный кран;
4 – железнодорожный вагон; 5 – бассейн [3]
242
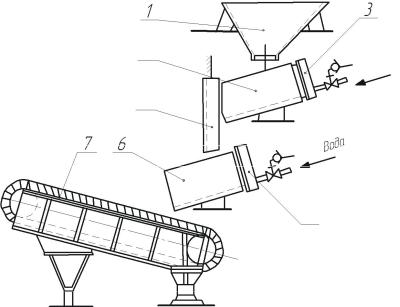
Наиболее эффективным в настоящее время является гидроэкранный способ (рис. 6.10), основанный на резком охлаждении шлакового расплава в системе последовательно установленных гидрожелобов, состоящих из желобов и гидромониторных насадок 3, 5 через которые подается вода. Между гидрожелобами установлен экран.
1 |
|
3 |
|
2
Вода
4
7 |
|
6 |
|
Вода |
|
|
|
5
Рис. 6.10. Схема гидроэкранного устройства: 1 – воронка; 2 – первый желоб; 3 – первая гидромониторная насадка; 4 – экран; 5 – вторая гидромониторная насадка; 6 – второй желоб; 7 – перегружатель [4]
Вспучивающийся шлаковый расплав с желоба 2 струями воды выбрасывается на экран 4, отразившись от которого, попадает на желоб 6, откуда водой выносится на конвейерный перегружатель 7 для последующего охлаждения и дробления.
Шлаковую пемзу выпускают в виде щебня трех фракций: 5–10, 10–20 и 20–40 мм – и песка (рядового – с зернами крупностью менее 5 мм, мелкого – менее 1,25 и крупного – 1,25–5,00 мм).
243
Для каждой фракции щебня, а также мелкого и крупного песка нормируется зерновой состав.
В зависимости от насыпной плотности (кг/м3) шлаковую пемзу делят на марки: для щебня – 400, 450, 500, 550, 600, 650, 700, 750, 800, 850, 900; для песка – 600, 700, 800, 900, 1000. Ме-
жду прочностью щебня и его маркой по насыпной плотности существует определенная зависимость [2]:
Марка щебня по |
400 |
450 |
500 |
550 |
600 |
650 |
700 |
750 |
800 |
850 |
900 |
насыпной плотности |
|||||||||||
Прочность при сдав- |
|
|
|
|
|
|
|
|
|
|
|
ливании в цилиндре, |
0,30 |
0,35 |
0,40 |
0,45 |
0,55 |
0,65 |
0,70 |
0,90 |
1,10 |
1,30 |
1,50 |
МПа, не менее |
|
|
|
|
|
|
|
|
|
|
|
Марку щебня из шлаковой пемзы по морозостойкости определяют по числу циклов попеременного замораживания и оттаивания, при котором потеря массы исследуемой пробы не должна превышать 8 %. Морозостойкость щебня из шлаковой пемзы должна составлять не менее 15 циклов. Размер пор шлаковой пемзы зависит от способа получения и равен 0,04–4,50 мм, пористость составляет 52–78 %, водопоглощение – 10–55 %.
Перспективной является гравиеподобная шлаковая пемза, имеющая плотную остеклованную оболочку зерен. Ее применение позволяет уменьшить расход цемента и снизить среднюю плотность легких бетонов. При получении гравиеподобной шлаковой пемзы частицы расплава с воздушного гранулятора направляют на экран, где они объединяются в более крупные куски. Во вращающемся барабане с продольными лопастями происходит дополнительное вспучивание и окатывание зерен
сприданием им гравиеподобной формы. Показатели качества такой шлаковой пемзы в 2–3 раза выше показателей пористого шлакового щебня.
Шлаковая пемза применяется как заполнитель легких бетонов
сшироким диапазоном по средней плотности и прочностным показателям. Ее используют как пористый заполнитель для конст- рукционно-теплоизоляционных легких бетонов с плотностью
244
1300–1600 кг/м3 и прочностью 5,0–7,5 МПа и конструкционных бетонов с плотностью 1500–1800 кг/м3 и прочностью 10–20 МПа. При использовании шлаковой пемзы для армированных и в особенности преднапряженных конструкций должна быть проверена стойкость арматуры, коррозия которой возможна за счет содержащейся в шлаке серы.
Затраты на изготовление 1 м3 этого материала в 5 раз меньше, производительность труда в 4–5 раз выше, чем при производстве других пористых заполнителей. На выпуск шлаковой пемзы практически не расходуется технологическое топливо. Расход электроэнергии на производство 1 м3 щебня и песка из шлаковой пемзы составляет 6,2 кВт·ч, а на производство 1 м3 керамзитового гравия и аглопорита – соответственно 24 и 47,4 кВт·ч.
В НИИСМ им. С.А. Дадашева разработана технология получения искусственных пористых заполнителей – азеритов – из стекловатных шлаков металлургического и химического производств и других неорганических отходов промышленности. Она позволяет получать заполнители с насыпной плотностью 430–765 кг/м3 и пределом прочности при сжатии в цилиндре 3,7–13,8 МПа. При этом снижается температура вспучивания сырьевых гранул с 1150–1180 до 850–1000 °С. На базе изготавливаемых легких заполнителей можно получить высокопрочные легкие бетоны марок М100–М500 (классов В7,5–В40) для несущих конструкций зданий и сооружений.
6.3. Шлаковая вата
Шлаковая вата – это разновидность минеральной ваты, занимающая ведущее место среди теплоизоляционных материалов как по объему выпуска, так и по строительно-техническим свойствам.
Примерно 80 % минеральной ваты производится из доменных шлаков. Производительность печей для получения минерального расплава из металлургических шлаков на 24 % выше, чем из природного сырья, а себестоимость значительно ниже.
245
Для получения минеральной ваты наряду с доменными шлаками применяются также ваграночные, мартеновские шлаки и шлаки цветной металлургии.
Химический состав шихты подбирается в соответствии с условиями достижения оптимальной величины вязкости расплава. Рекомендуется такой состав шихты, при котором вязкость расплава не превышала бы 0,5 Па·с при 1500 °С и 1,5 Па·с при 1400 °С. При такой вязкости обеспечиваются достаточная текучесть и необходимые условия получения кондиционного минерального волокна. Вместе с тем при чрезмерно низкой вязкости затрудняется вытягивание длинных волокон.
Условия раздува расплава, диаметр и длина волокон зависят также от скорости нарастания вязкости при снижении температуры и от отношения вязкости к силам свободной энергии поверхности расплава, т.е. от поверхностного натяжения.
Основным критерием качества шлаков как сырья для производства минеральной ваты является значение модуля кислотности Мк – величины, обратной модулю основности. Минеральная вата марки 100 по средней плотности имеет Мк > 1,4, а мар-
ки 75 – Мк > 1,5.
Требуемое соотношение кислотных и основных оксидов в шихте обеспечивается применением кислых шлаков. Кислые шлаки более устойчивы к распаду, недопустимому в минеральной вате. Повышение содержания кремнезема расширяет температурный интервал вязкости, т.е. разность температур, в пределах которых возможно волокнообразование.
Модуль кислотности шлаков корректируется введением в шихту кислых или основных добавок. В качестве кислых добавок обычно применяют бой глиняного или силикатного кирпича, золу теплоэлектростанций, различные кремнеземистые горные породы, а основными являются доломиты и известняки.
246
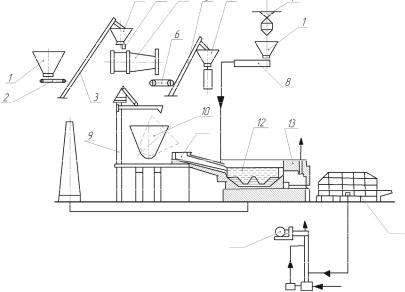
|
|
|
|
1 |
4 |
5 |
|
|
|
1 |
|
|
|
7 |
|
|
|||||||
|
|
|
|
3 |
|
|
|
|
|
|
|||||||||||||
|
|
|
|
|
|
|
|
|
|
|
|
|
|
|
|
|
|
|
|
|
|
|
|
|
|
|
|
|
|
|
|
|
|
|
|
|
|
|
|
|
|
|
1 |
||||
|
|
|
|
|
|
|
|
|
6 |
|
|
|
|
|
|
|
|
|
|
|
|
|
|
|
|
|
|
|
|
|
|
|
|
|
|
|
|
|
|
|
|
|
|
|
|
|
|
|
1 |
|
|
|
|
|
|
|
|
|
|
|
|
|
|
|
|
|
|
|
|
||
|
|
|
|
|
|
|
|
|
|
|
|
|
|
|
|
|
8 |
|
|
|
|||
|
|
|
|
|
|
|
|
|
|
|
|
|
|
|
|
|
|
||||||
|
|
|
|
|
|
|
|
|
|
|
|
|
|
|
|
|
|
|
|
|
|
|
|
|
2 |
|
|
3 |
|
|
|
|
|
|
|
|
|
|
|
|
|
|
|
|
|
||
|
|
|
|
|
|
|
|
|
|
|
|
|
|
|
|
|
|
|
|
|
|
|
|
|
|
|
|
|
|
|
|
|
|
|
10 |
|
|
|
|
|
|
|
|
|
|||
|
|
|
|
|
|
|
|
|
|
|
|
|
|
|
|
|
12 |
|
|
|
|
|
|
|
|
|
|
|
|
|
|
|
|
|
11 |
|
|
|
|
13 |
|
||||||
|
|
|
|
9 |
|
|
|
|
|
|
|
|
|
||||||||||
|
|
|
|
|
|
|
|
|
|
|
|||||||||||||
|
|
|
|
|
|
|
|
|
|
|
|
|
|
|
|
|
|
|
|
|
|
Пар
14
15
Вода
Рис. 6.11. Схема производства минеральной ваты из огненно-жидких шлаков: 1 – бункер для песка; 2 – питатель; 3 – наклонный шнек; 4 – тарельчатый питатель; 5 – сушильный барабан; 6 – конвейер; 7 – тельфер; 8 – шнек-питатель; 9 – копер для пробивки шлаковой корки; 10 – шлаковый ковш; 11 – желоб для слива шлака в печьшлакоприемник; 12 – печь-шлакоприемник; 13 – печь-питатель; 14 – камера волокноосаждения; 15 – дымосос с системой очистки воздуха от пыли [4]
Для шлаков, содержащих повышенное количество оксидов железа и марганца, дополнительной качественной характеристикой является коэффициент насыщения, представляющий собой отношение суммы процентного содержания SiО2 + A12О3 к суммарному процентному содержанию прочих оксидов. Этот коэффициент при плавке шихты в вагранках составляет 1,5–2,0.
Технологический процесс производства шлаковой ваты (рис. 6.11), как и других разновидностей минеральной ваты, со-
247
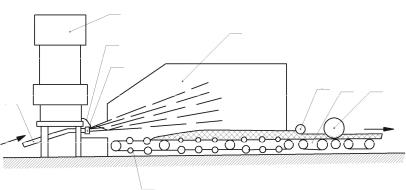
стоит из двух основных стадий: получения расплава и переработки его в волокно.
Из шлаковой ваты с помощью органических и неорганических вяжущих или без них изготавливают разнообразные теплоизоляционные изделия и материалы.
Для получения шлаковых расплавов применяют печи шахтного типа (вагранки) и ванные печи. При использовании вагранок в верхнюю их часть периодически загружается газопроницаемая шихта (рис. 6.12). Оптимальная величина кусков шлака и кокса составляет 50–70 мм. Шихта, опускаясь вниз, расплавляется. Продукты горения топлива поднимаются вверх и передают тепло расплавляемому материалу.
Наиболее выгодным шлаковым сырьем является литой шлаковый щебень. Использование его вместо несортированных шлаков повышает производительность вагранок на 30 %.
1
5
2
4
8 7 9
3
6
Рис. 6.12. Схема ваграночного производства минераловатных изделий: 1 – вагранка; 2 – струя расплава; 3 – паропровод; 4 – сопло; 5 – камера волокноосаждения; 6 – сетчатый транспортер;
7 – транспортер; 8 – уплотняющий валок; 9 – диск для продольной резки минераловатного полотна [3]
В последние годы для плавления шлаков применяют ванные печи, тепловой КПД которых составляет 35–45 %, в то время как у вагранок он 16–25 %.
248
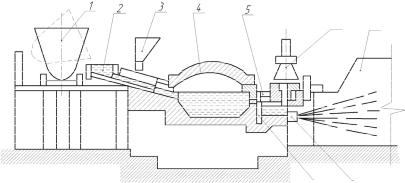
Наиболее эффективным способом производства ваты является ее получение непосредственно из первичных шлаковых расплавов доменных печей. Расплавленный шлак подогревается в ванных печах до требуемой температуры; здесь же корректируется его состав (рис. 6.13).
Производство минеральной ваты из огненно-жидких шлаков на 30–50 % экономичнее, чем из холодных при плавке в вагранках. Затраты условного топлива на получение 1 т продукции из жидких шлаков в 4–7 раз ниже, чем при плавлении шихты из горных пород.
1 |
|
2 |
|
3 |
|
4 |
|
|
|
|
|
|
5 |
||||
|
|
|
|
|
||||
|
|
|||||||
|
|
|
|
|
|
|
|
|
6 7
8 9
Рис. 6.13. Схема получения минеральной ваты с использованием огненно-жидкого шлака: 1 – шлаковозный ковш; 2 – шлакоприемная ванна; 3 – бункер для подачи подкисляющих добавок; 4 – ванная печьмиксер; 5 – печь-питатель; 6 – вытяжной зонт; 7 – камера осаждения; 8 – скиммерная доска; 9 – узел раздува [3]
Шлаковый расплав превращают в минеральное волокно, воздействуя на него потоком пара, воздуха или газа (дутьевой способ) или центробежной силой (центробежный способ). Дутьевой способ получения шлаковой ваты заменяется на центробежный и комбинированный способы, позволяющие получить длинноволокнистую вату с плотностью до 100 кг/м3 и минимальным содержанием неволокнистых включений.
249
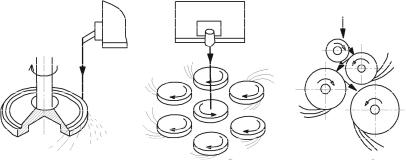
Наиболее известный дутьевой способ подразделяется на гори- зонтально-дутьевой и вертикально-дутьевой. В первом случае энергоноситель направляют на струю расплава диаметром 7–10 мм под углом 15–20° к горизонтали, во втором – на струю диаметром до 3 мм сверху вниз под углом 10–11° к вертикали.
При центробежных способах получение волокон из расплава осуществляется механическими средствами – одно-, двух- и многоступенчатыми центрифугами (рис. 6.14).
а |
б |
в |
Рис. 6.14. Схемы центробежных устройств для получения шлаковаты:
а– однодисковая центрифуга; б – многовалковая центрифуга
сцентральной распределительной чашей; в – вертикальная многовалковая центрифуга [3]
И, наконец, комбинированные способы включают переработку расплава совмещенными приемами – обычно центробежным и дутьевым (рис. 6.15, 6.16).
Наряду с приведенными способами существует много их разновидностей, не имеющих принципиальных отличий от описанных. Наиболее простой и прежде широко распространенный дутьевой способ уступает место центробежным и комбинированным способам, позволяющим получить качественную минеральную вату.
250