
книги / Сварка трубопроводов
..pdfСварку корневого слоя шва выполняют электродами диамет рами 3 или 3,25 мм; при этом зазор выставляется ближе к верхнему пределу обычно рекомендуемого диапазона (2,5 —3 мм).
Сварку осуществляют легким опиранием на свариваемые кром ки и ведением электрода сверху вниз без поперечных колебаний. Усилие на электрод в отличие от варианта сварки электродами с цел люлозным видом покрытия минимально. Сварочный ток соответ ствует коэффициенту А = 25 —30 А/мм. Скорость сварки должна быть не менее 10, но не более 15м/ч. Толщина корневого слоя шва изза повышенного коэффициента наплавки и меньшей скорости свар ки (в сравнении с электродами с целлюлозным покрытием) не мень ше, чем суммарная толщина корневого слоя шва (после шлифовки) плюс "горячего" прохода при сварке электродами с целлюлозным ви дом покрытия. Благодаря особенностям формирования корневого слоя шва сварка электродами этого вида осуществляется без образо вания зашлакованных карманов, формы этого шва более плавные, чем в случае электродов с целлюлозным видом покрытия, шлифовка абразивным кругом после сварки не требуется, шлак отделяется хо рошо, ввиду формирования низководородистого металла и благо приятной формы наружной поверхности корневого слоя проведе ние "горячего" прохода необязательно.
Факторы, позволяющие регулировать проплавление, пред ставлены в табл. 3.1.
Таблица 3.1
Регулировка проплавления при сварке на спуск электродами с основным видом покрытия
Регулируемые |
При отсутствии сквозного |
При наличии прожогов |
|
параметры |
проплавления |
||
|
|||
Наклон электрода |
Ближе к перпендикуляр |
Поддерживать положе |
|
относительно |
ному положению (около |
ние электрода подуглом |
|
поверхности |
90 °) |
65-70° |
|
свариваемой |
|
|
|
пластины |
|
|
|
Скорость переме |
Медленнее |
Быстрее |
|
щения электрода |
|
|
|
Усилие на электрод |
Сильнее |
Не давить |
|
Сила тока |
Повыситьпримерно на 20А |
Уменьшить примерно на |
|
|
|
20—30 А |
Сварка заполняющих и облицовочного слоев шва обычно осу ществляется электродами диаметром 4 мм без поперечных колеба ний (многоваликовые слои) с высокой линейной скоростью до 26 м/ч. Низкое разбрызгивание и повышенный коэффициент наплавки делают эти электроды при сварке заполняющих слоев конкурентоспособными электродам с целлюлозным видом покры тия диаметром 5 и даже 5,5 мм. Достижение сквозного проплавле ния фиксируется по характерному шуму проходящей "навылет" дуги.
Качество электродов. При правильной технике сварки (соот ветствующей квалификации сварщика) и соблюдении технологии сборки и сварки (следование регламентации нормативной доку ментации) качество сварных соединений при ручной дуговой сварке во многом определяется качеством сварочных электродов. При этом под качеством понимают в первую очередь качество из готовления и упаковки электродов, а также технологичность элек трода как таковую, определяемую рецептурой его покрытия.
С учетом специфики трубопроводного строительства из мно гообразия оперативных показателей качества электродов следует выделить два первостепенных показателя: чувствительность к об разованию козырька в процессе сварки и недопустимый уровень влажности электродного покрытия.
Во избежание образования козырька завод-изготовитель дол жен обеспечить поставку электродов с минимальной разнотолщинностью нанесения покрытия на электродный стержень. Этот критерий во многом связан с толщиной электродного покрытия. Так, для электродов, применяемых в трубопроводном строитель стве, этот критерий зависит от диаметра электродов и типа покры тия (табл. 3.2). Однако минимальная разнотолщинность нанесе ния покрытия — требование необходимое, но недостаточное. В практике нередко встречаются случаи, когда электрод с почти идеальной равномерностью нанесения покрытия (разнотолщин ность 0 —0,03 мм) образует козырьки, особенно при сварке корне вого слоя шва в нижней полуокружности трубы. Образование ко зырька в этом случае обусловлено неоднородностью покрытия, его неудовлетворительными физическими свойствами (тугоплав кость, интервал размягчения шлака, вязкость расплава покрытия ит. д.).
При недостаточной прочности покрытия, особенно в процессе
Таблица 3.2
Максимально допустимая разнотолщинность электродных покрытий, мм
Вид покрытия |
|
Диаметр электрода, мм |
|
|||
3-3,25 |
4 |
4,5 |
5 |
5,5 |
||
электрода |
||||||
Целлюлозный |
0,08 |
0,12 |
0,12 |
0,135 |
0,135 |
|
Основной для сварки |
0,135 |
0,15 |
0,175 |
— |
— |
|
сверху вниз |
|
|
|
|
|
|
Основной для сварки |
0,135 |
0,18 |
|
0,25 |
|
|
снизу вверх |
|
|
|
|
|
сварки опиранием, втулочка разрушается, что не только мешает правильному формированию шва, но может явиться причиной об разования пор и шлаковых включений. На рис. 3.9 показаны по следствия образования козырька в случае электродов с основным
ис целлюлозным видом покрытия [1, 24].
Впроцессе сварки толстопокрытыми электродами с основным видом покрытия, чувствительными к образованию козырька, крупная капля на торце электрода отклоняется в сторону, дуга
Рис. 3.9. Образование козырька при сварке электродами:
а — с основным видом покрытия; б — с целлюлозным видом покрытия: 1,3 —равномерное сплавление покрытия; 2и4 —неравномерное оплав ление покрытия с образованием "козырька"
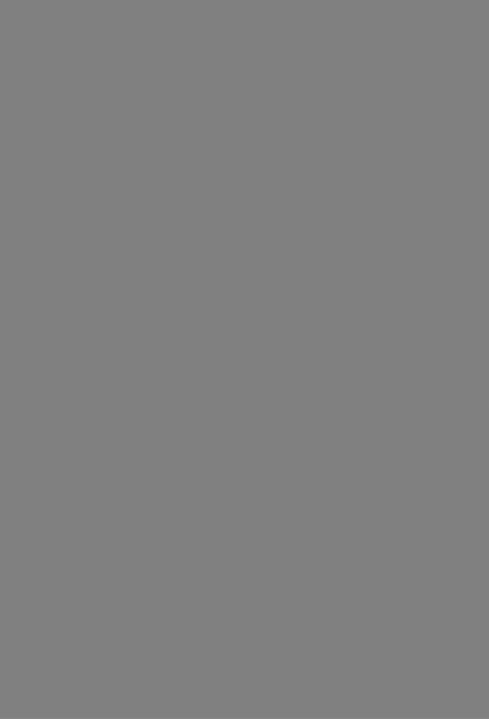
пытки сварщика избавиться от козырька, повернув электрод или энергично "воздействуя" на него, приводят к образованию зашла кованных "карманов" и пор под "карманами". Другим важным по казателем качества электродов являются требования к обеспече нию минимальной влажности при сварке электродами с основным видом покрытия и поддержание ее в определенных пределах при сварке электродами с целлюлозным видом покрытия.
В случае использования электродов с основным видом покры тия повышенная влажность приводит к образованию холодных трещин в металле шва и зоне термического влияния, способствует порообразованию, вызывает дефекты формы шва в связи с ухуд шением технологичности электродов (нестабильное горение дуги, разбрызгивание, ухудшение отделимости шлака).
Наиболее действенным средством обеспечения перед началом работ допустимого уровня влаги основного электродного покры тия является прокалка электродов непосредственно перед свар кой. Однако требования к режимам термообработки весьма про тиворечивы и колеблются в довольно широких пределах как по температуре (от 250 до 450 °С), так и по времени выдержки (от 0,5 до 2,5 ч).
Естественно, что на эффективность того или иного из выбран ных режимов прокалки могут влиять самые различные факторы, начиная с условий производства (рецептура покрытия, характери стики связующего, режимы заводской термообработки, вид упа ковки) и кончая условиями транспортировки и хранения. Однако в настоящее время при сварке стыков газонефтепроводов призна но целесообразным использовать сушильно-прокалочные устрой ства с единым, заранее установленным режимом термообработки электродов.
При монтаже используется весьма широкая номенклатура электродов с основным видом покрытия, различающихся как по технологии производства, так и по типу упаковки.
За критический уровень влаги основного покрытия перед употреблением электродов чаще всего принимают величину 0,3 %. Что же касается влажности электродов с целлюлозным видом по крытия, то требования к ней неоднозначны. Если электроды пере сушены (на заводе, при повторной сушке или в процессе сварки — отсутствие огарков), то в металле шва возникают поры. Если элек троды переувлажнены, то их технологичность резко ухудшается
(нестабильное горение дуги, потеря втулкой прочности, сильное разбрызгивание). Поэтому влажность целлюлозного покрытия должна поддерживаться в определенных пределах. Если упаковка электродов герметична, например жестяные банки запаяны, то их можно использовать без предварительной термообработки. Если эти условия нарушаются, то перед сваркой необходимо их слегка просушить по режиму, указанному в табл. 3.3.
В зависимости от типа электродов и прочностного класса сва риваемых сталей регламентируется допустимое время выдержки электродов перед сваркой и возможное число повторных термо обработок (табл. 3.4).
Существуют различные методы организации сварочно-мон тажных работ при строительстве магистральных и промысловых трубопроводов. Эти методы предусматривают сварку трубопрово да в нитку из трехтрубных секций, заранее сваренных на трубо сварочной базе, или присоединением отдельных труб. Перечис лим основные:
Метод последовательного наращивания. Бригада сварщиков состоит из одного звена. Каждый сварщик обычно сваривает один слой шва (корневой, "горячего" прохода, заполняющий, облицо вочный). При малых диаметрах трубопровода и небольшой толщине труб каждый сварщик может сваривать весь стык от начала до конца.
Поточно-групповой метод. Бригада сварщиков состоит из двух или трех звеньев. Первое звено выполняет корневой слой шва и "горячего" прохода. Остальные звенья выполняют заполня ющий и облицовочный слои шва.
Поточно-групповой метод сварки с расчленением операций сварки корневого слоя шва и "горячего" прохода, т. е. при работе по этому варианту головная группа состоит из двух звеньев свар щиков: одно звено, выполнив сварку только корневого слоя шва, переходит к следующему стыку, а на его место приходит другое
звено, которое |
выполняет "горячий" проход. |
|
|
|||
|
|
|
|
|
Таблица 3.3 |
|
Режимы сушки и прокалки электродов (время сушки 1 ч) |
|
|||||
Видпокрытия |
Э42Ц |
Э50Ц |
Э60Ц |
Э42-Б Э50А-Б |
760-Б |
770-Б |
электрода |
|
|
|
|
|
|
Температура, °С |
60-100 |
60-100 |
60-100 |
200-250 250-300 |
300-350 |
300-350 |
|
Условия термообработки и хранения электродов |
|
|
|||||
|
|
|
|
Максимально допус |
|
|||
Вид |
|
Темпе |
|
тимое время выдерж Допус |
||||
|
ратура Время |
ки до сварки при |
тимое |
|||||
покрытия |
Свариваемые стали |
сушки сушки температуре 15—25°С число |
||||||
электрода |
(ств, МПа) |
(про |
(про- |
и относительной |
повтор |
|||
|
|
калки), калки), |
влажности (%) окру |
ных |
||||
|
|
°С |
мин |
жающего воздуха, ч |
термо- |
|||
|
|
|
|
|
60- |
80- |
|
обра |
|
|
|
|
<60 |
>95 |
боток |
||
|
|
|
|
|
80 |
95 |
|
|
Целлю |
Нелегированные |
60-90 |
60 |
12 |
10 |
8 |
6 |
6 |
лозное |
или низколеги |
|
|
|
|
|
|
|
|
рованные (540) |
|
|
|
|
|
|
|
|
Низколегирован |
60-90 |
60 |
10 |
8 |
6 |
4 |
4 |
Основное |
ные (540—590) |
300 |
|
|
|
|
|
|
Нелегированные |
60 |
6 |
4 |
2 |
1 |
3 |
||
|
или низколеги |
|
|
|
|
|
|
|
|
рованные (540) |
350 |
|
|
|
|
|
|
|
Низколегирован |
60 |
6 |
4 |
2 |
1 |
3 |
|
|
ные (540—590) |
350 |
|
6 |
|
|
|
|
|
Низколегирован |
90 |
4 |
2 |
1 |
2 |
||
|
ные (590—670) |
400 |
90 |
4 |
2 |
2 |
0,5 |
2 |
|
Низколегирован |
|||||||
|
ные (670—780) |
|
|
|
|
|
|
|
Поточно-расчлененный метод сварки с расчленением опера ций не только в головной группе, но и при выполнении заполняю щих и облицовочного слоев шва. При работе по этому методу каж дый сварщик при выполнении сварки заполняющих и облицовоч ного слоев шва сваривает на каждом стыке только "свой" опреде ленный сектор данного слоя и, закончив эту работу, сразу же переходит на следующий стык. Для этого метода характерна мак симальная специализация сварщиков. Данный метод целесооб разно применять только при условии расчленения операций в го ловном звене.
На практике наибольшее распространение получил поточнорасчлененный метод. Сборка и сварка секций труб на трассе по точно-расчлененным методом охватывает комплекс работ, в кото рый входят следующие трудовые процессы:
подготовка стыков секций труб к сборке и сварке; сборка и сварка корневого слоя шва; сварка второго слоя шва — "горячего" прохода;
сварка заполняющего и облицовочного слоев шва.
Сварку секций труб на трассе поточно-расчлененным мето дом осуществляют в три технологических этапа:
I этап — подготовка стыков секций труб к сборке и сварке.
В состав работ входят: правка или обрезка дефектных кромок стыков; очистка внутренней полости секций; зачистка кро мок стыков; выкладка труб или секций труб вдоль трассы для цент ровки.
II этап — сварка первого (корневого) и второго ("горячего" прохода) слоев шва.
В состав работ входят: центровка стыка и установка зазора; предварительный подогрев кромок стыков секций; сварка корне вого слоя шва и "горячего" прохода.
III этап — сварка заполняющего и облицовочного слоев шва. Технологические этапы подразделяют на пять характерных
зон выполнения операций:
подготовка стыков секций труб к сборке и сварке; предварительный подогрев кромок стыка секций, подготов
ленных к сборке; центровка стыков секций с ниткой трубопровода и сварка
корневого слоя шва; сварка "горячего" прохода;
сварка заполняющего и облицовочного шва.
При строительстве нефтепровода Каспийского трубопровод ного консорциума (КТК) сварку неповоротных стыков труб в ли нейном потоке осуществляли по двум технологическим вариантам ручной дуговой сварки:
Вариант № 1 (комбинированная технология). Корневой слой шва и "горячий" проход выполняли электродами с целлюлозным видом покрытия, последующие слои — электродами с основным видом покрытия.
Вариант № 2. Корневой слой и все последующие слои шва — электродами с основным видом покрытия.
Первый вариант сварки был наиболее предпочтительным, так как позволял значительно увеличить темп сварки и производи тельность работы бригады при высоком качестве выполнения корне
вого слоя шва. Использовали как для сварки неповоротных стыков труб на линейной части нефтепровода, так и для сварки захлестов.
Второй вариант сварки применяли для сварки неповоротных стыков на линейной части нефтепровода в случае невозможности применения электродов с целлюлозным видом покрытия по объективным причинам. Его также использовали для сварки захлесточных соединений.
Комбинации сварочных электродов, использованных для руч ной дуговой сварки неповоротных стыков труб из стали класса Х65 и Х70, приведены в табл. 4.7 и 4.8.
Ручная дуговая сварка осуществлялась от источников тока, обеспечивающих специальные характеристики дуги. Сварку элек тродами с целлюлозным видом покрытия производили только от современных источников тока: выпрямителей с тиристорным уп равлением, например моделей Idealarc DC-400, RCR-500, LHF или их аналогов; инверторных источников тока, например Invertec V300-1; автономных дизельных источников Commander 400 или их аналогов.
3.1.2. Оборудование для ручной дуговой сварки
3.1.2.1. Источники питания для ручной дуговой сварки
Качество и производительность сварки стыков магистральных и промысловых трубопроводов в значительной степени зависят от технологических характеристик и конструкции источников сварочного тока. В качестве сварочных источников тока в монтаж ных условиях применяют коллекторные генераторы, вентильные бесколлекторные генераторы и выпрямители. Для удобства эксп луатации сварочные источники тока компонуют в однопостовые или многопостовые сварочные агрегаты (см. рис. 3.11), которые выпускаются промышленностью в передвижном (на прицепе) и самоходном (на тракторе) исполнении. Многопостовые агрега ты, помимо сварочного источника тока, имеют источник электри ческой энергии для питания электрического инструмента и осве щения, электропечи для термообработки электродов. Имеются также устройство для намотки кабелей, емкости для хранения ин струмента.
