
книги / Управление техногенными отходами
..pdfбатареек, люминесцентных ламп, красок, ядовитых веществ, металлов (на практике эта проблема в подавляющем большинстве случаев решается посредством организации раздельного сбора ТКО).
Но даже компост, полученный в результате переработки раздельно собранных фракций ТКО с высоким содержанием биоразлагаемых веществ, не содержащих экологически опасных компонентов, не может конкурировать с другими удобрениями по содержанию питательных веществ. Он способен лишь улучшить почвенную структуру, что позволяет повысить устойчивость почвы к эрозии, улучшить ее водно-воздушный режим и т.д. Однако поскольку при любом способе компостирования ТКО не удается полностью избежать потенциальной опасности попадания в компост нежелательных для здоровья человека веществ, компост, полученный из ТКО или из его обогащенных фракций, рекомендуется использовать не в сельском хозяйстве, а в лесных питомниках, при озеленении, рекультивации земель (в том числе после добычи полезных ископаемых), в технологии полигонного захоронения ТКО (в качестве покрывающего материала), в качестве заполнителя для покрытия заболоченных земель и т.п.
В настоящее время в промышленности наиболее распространены три метода компостирования:
компостирование в биобарабанах;
туннельное компостирование;
компостирование в бассейне выдержки.
Биобарабан представляет собой сварной стальной цилиндр, установленный на двух или трех роликах-опорах с уклоном в сторону разгрузочного устройства. От продольного смещения биобарабан удерживают упорные ролики, установленные на ближайшей к разгрузочному устройству роликоопоре. Для сокращения теплопотерь поверхность биобарабана покрывают теплоизоляцией (пенопласт, минераловатные маты). Загрузка материала в биобарабан (и, соответственно, разгрузка) осуществляется в течение 1,0–1,5 смен (8–12 часов). Время нахождения материала в биобарабанах – около двух суток. За это время процесс компостирования, по существу,
151
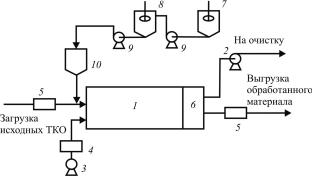
только начинается. Для дозревания компост размещается в штабелях на открытых площадках; продолжительность процесса дозревания – несколько месяцев. Схема компостирования ТКО в биобарабане представлена на рис. 3.24.
Рис. 3.24. Схема компостирования ТКО в биобарабане: 1 – биобарабан; 2 – всасывающий вентилятор; 3 – напорный вентилятор; 4 – электрокалорифер; 5 – конвеерные весы; 6 – термодатчик; 7 – накопитель субстрата; 8 – микробиологический ферментер; 9 – насос; 10 – накопитель-дозатор биомассы [34]
Основные недостатки компостирования в биобарабанах:
бесконтрольность процесса;
плохой товарный вид конечной продукции (сложность очистки материала, выходящего из биобарабана из-за его большой влажности);
эксплуатационные сложности (образование в барабанах пробок из текстиля, в весенне-осенний период биобарабаны «текут»);
потребность в большой площади для дозревания компоста (по существу, за двое суток процесс компостирования, как отмечено, только начинается, и потеря массы биоразлагаемого вещества на выходе из биобарабана не превышает 5 %);
невозможность, в соответствии с отечественной практикой, эксплуатации завода более 260 дней в году (замедленное дозревание компоста на открытом воздухе в зимний период, сложность сбыта продукции и пр.).
152
Поэтому в зарубежной практике основная тенденция развития технологий компостирования заключалась в переходе от компостирования в биобарабанах к компостированию в бассейне выдержки и в туннеле.
Отличие этих двух технологий друг от друга состоит в том, что
вбассейне выдержки материал находится 4–6 недель, а в туннеле – 7–10 дней. Соответственно, в бассейне выдержки процесс компостирования полностью заканчивается с получением сухого стабилизированного продукта (потеря массы вещества – 50 %), а в туннеле получается полупродукт (потеря массы исходного вещества – 20–30 %, влажность – 30 %). Вместе с тем во всех случаях, когда не предполагается получение конечного продукта в виде компоста для сельскохозяйственного использования, предпочтительнее применять компостирование обогащенной органической фракции в туннеле, рассматривая эту технологию как ферментативную сушку, обеспечивающую одновременно обезвреживание, измельчение и гомогенизацию материала. Материал после туннельного компостирования в большей степени обогащен углеродом, чем после компостирования в бассейне выдержки, что предпочтительно для последующих процессов термической переработки. При сопоставимой производительности капитальные затраты на строительство цеха компостирования в бассейне выдержки в 2–3 раза выше, чем при туннельном компостировании. Выбор той или иной технологии определяется в каждом конкретном случае и зависит от производительности завода, целей и задач переработки ТКО и ряда других факторов.
Бассейн выдержки представляет собой закрытую площадку для компостирования с линейными размерами в несколько десятков метров и глубиной слоя отходов, закладываемых на компостирование,
внесколько метров. Бассейн выдержки обслуживается мостовым краном с четырьмя шнеками, расположенными под yглoм к горизон- тали. Назначение шнеков – равномерное распределение материала
вбассейне с одновременным его перемешиванием. В процессе перемешивания и перемещения материал хорошо измельчается и гомоге- низируется. Температура в бассейне выдержки поддерживается по-
153
стоянной (50–60 °С). Компостируемый материал снизу продувается воздухом, который подается по трубам с отверстиями. После созревания компост с помощью шнека подается на систему ленточных конвейеров и транспортируется на линию сортировки для очистки от примесей. Визуально готовый компост представляет собой однород- ную зернистую массу коричневатого оттенка разных тонов (светлых и более темных), без посторонних примесей.
Туннель для компостирования можно рассматривать как большой контейнер. Средние габариты одного туннеля: длина – 30 м, ширина – 5 м, высота – 3–4 м. Загрузка-разгрузка материала осуществляется периодически (один раз в 10 суток). Производительность одного туннеля – 15–18 т/сут. Технологический процесс компостирования в туннеле, как и в бассейне выдержки, поддается полной автоматизации и непрерывно контролируется (температура, расход аэрируемого воздуха, влажность). Количество подаваемого вентилятором воздуха на входе в туннель корректируется в соответствии с содержанием кислорода (или СО2) на выходе.
Другой биологический метод переработки ТКО – сбраживание, или анаэробная ферментация, т.е. разложение органических компонентов в анаэробных условиях. Продукт сбраживания – метан – генерируется с помощью анаэробных бактерий. В Германии, Бельгии, Франции и ряде других стран разработана и реализована в условиях заводской практики технология получения биогаза из органической фракции, выделенной из ТКО при их обогащении.
Сбраживание наиболее эффективно при переработке влажных отходов с высоким содержанием органических веществ. Выход биогаза (содержит около 60 % метана) при сбраживании пищевых и растительных отходов составляет 80–100 м3/т влажных органических отходов.
Основные факторы, влияющие на процесс сбраживания, – температура и содержание сухого вещества. Наиболее эффективно процесс сбраживания органических веществ протекает при температуре от 35 °С (мезофильный режим) до 55 °С (термофильный режим). Распад органического вещества происходит быстрее при бо-
154
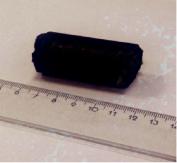
лее высокой температуре. Продолжительность пребывания влажных органических отходов в реакторе сбраживания – три недели. Хвосты сбраживания подвергаются обезвоживанию, дозреванию и очистке от примесей (стекло, текстиль, пластмасса и др.) с применением методов сортировки. В итоге получается новый вид удобре-
ния, который |
существенно отличается от компоста (более схож |
с перегноем), |
продается в гранулированном виде (размер гранул |
около 10 мм) и используется как дополнение к минеральным удобрениям.
Заводы, на которых реализована технология сбраживания, являются самыми дорогими среди альтернативных технологий, что связано с необходимостью применения большого числа реакторов большой емкости [11].
3.6.3. Получение и использование вторичного топлива из ТКО
Как было показано в п. 3.2.1, ТКО имеют определенный энергетический потенциал, который можно использовать. Существуют технологии механической, биологической и механобиологической обработки ТКО, позволяющие получить из ТКО продукт, обогащенный высококалорийными фракциями (к числу таких фракций относятся пластики, дерево, макулатура, текстиль, некоторые комбинированные материалы типа тетрапака и др.). Топливо из ТКО (иногда используют термин «вторичное топливо», или «замещающее топливо»,
англ. RDF – refuse derived fuel) мо-
жет использоваться в качестве заменителя традиционных видов ископаемого топлива (рис. 3.25).
Топливо из ТКО намного более изменчиво по составу по сравнению с традиционными видами
ископаемого топлива. Поэтому особенно важным становится со-
155
блюдение технологической дисциплины при его производстве. При правильно организованном производстве низшая теплота сгорания топлива из ТКО может достигать 9 МДж/кг, а по содержанию золы, влаги, серы и азота его характеристики будут практически соответствовать аналогичным характеристикам бурых углей. Следует учитывать и то, что в зависимости от типа установок, на которых планируется сжигать топливо из ТКО, требования к составу топлива будут различными. В частности, следует учитывать концентрации загрязняющих веществ в топливе из ТКО и особенности систем газоочистки используемых установок термической утилизации.
Топливо из ТКО может использоваться:
дляпроизводственныхцелей (напримервцементныхпечах);
в существующих энергетических установках (ТЭС и т.п.);
на специализированных энергетических установках. Одной из предпосылок для использования топлива из ТКО
впромышленности является то, что существенную долю себестоимости продукции производства составляют затраты на топливо. Помимо асфальтовых и кирпичных заводов, доменного производства, одними из самых важных потребителей топлива из ТКО в промышленном секторе являются цементные заводы.
Существенного повышения эффективности применения топлива из ТКО можно достичь за счет частичного замещения им угля на ТЭС (технология совместного сжигания). В этом случае при сжигании на ТЭС бурого угля целесообразно использовать предтопок для сжигания топлива из ТКО с направлением дымовых газов, получаемых в предтопке, в топочное пространство существующего котельного агрегата. При сжигании на ТЭС природного газа целесообразно использовать установку для газификации топлива из ТКО с последующей очисткой полученного газа и сжиганием его
втопках котлов ТЭС. В обоих случаях нет необходимости изменять существующую на ТЭС паросиловую установку. В этом случае снижаются капитальные затраты на обращение с ТКО – благодаря использованию существующей на ТЭС инфраструктуры и сокраще-
156
ния расходов на газоочистное оборудование. Доля топлива из ТКО по количеству тепла может составлять примерно 10 % от тепловой мощности котла. Анализ технико-экономических показателей, полученных при частичном (10%-ном) замещении энергетического топлива на одном из стандартных блоков ТЭС, работающих на природном газе, показал, что в этом случае стоимость природного газа, используемого на ТЭС, может быть полностью покрыта доходами от приема топлива из ТКО.
Возможно также использование специализированных энергоустановок. В этом случае используются технологии слоевого сжигания и сжигания в кипящем (псевдосжиженном) слое.
Некоторые требования, предъявляемые к топливу из ТКО в Германии для утилизации его на различных производствах, приведены в табл. 3.12.
Содержание хлора в топливе из ТКО – один из самых важных параметров, хлор может активизировать высокотемпературную коррозию оборудования для сжигания. Так, на угольных ТЭС, использующих пароводяной цикл, процессы коррозии могут развиться при содержании хлора в топливе из ТКО порядка 0,5 %. Наиболее высокое содержание хлора в топливе из ТКО допускается при его сжигании на специализированных энергоустановках.
Таблица 3.12 Требования к качеству вторичного топлива из отходов (ФРГ)
Параметр |
Цементная |
ТЭС |
Специализированная |
|
печь |
на угле |
энергоустановка |
||
|
||||
Низшая теплота сгорания, |
> 20,0 |
> 18,0 |
12,0–16,0 |
|
МДж/кг сухого вещества |
||||
|
|
|
||
Влажность, % |
< 15 |
< 15–25 |
< 30–40 |
|
Зольность, % от сухого |
< 15 |
< 15–20 |
< 25–30 |
|
вещества |
||||
|
|
|
||
Содержание хлора, % |
< 1,0 |
< 0,5–1,5 |
< 1,0–1,5 |
|
от сухого вещества |
||||
|
|
|
Использование специализированных энергоустановок также допускает более широкий предел размеров частиц топлива из ТКО
157
по сравнению с объектами совместного сжигания. Так, на специализированных энергоустановках можно использовать топливо из ТКО с размером составляющих до 50 см, в то время как для процессов совместного сжигания на угольных ТЭС требуется, чтобы частицы топлива имели небольшие размеры.
Технологии, используемые для производства топлива из ТКО, зависят от выбранного направления применения топлива и могут изменяться в зависимости от глубины процесса обработки и финансовых возможностей производителя. Задача переработки ТКО в топливо в общем виде сводится к отделению горючей фракции отходов от негорючей. Для этого из массива (потока) ТКО удаляют крупные, опасные и мешающие компоненты, а также негорючие компоненты и компоненты с высокой влажностью. Ведущую роль здесь играют процессы сепарации отходов (обычно это многоступенчатые процессы сортировки в сочетании с такими вспомогательными операциями, как, например, дробление). Нежелательное влияние на свойства топлива из ТКО компонентов с высокой влажностью (например пищевых отходов) может быть нейтрализовано с помощью процессов стабилизации отходов (в основном используются процессы биостабилизации).
Можно выделить следующие основные технологии утилизации ТКО с получением топлива:
1)механическая переработка;
2)механобиологическая переработка;
3)механобиологическая стабилизация;
4)физико-механическая стабилизация. 1. Механическая переработка.
Эта технология обычно применяется для отходов специфиче-
ских производств, характеризующихся низким содержанием органики, что делает биологическую обработку необязательной. Сначала из потока ТКО на магнитном и вихретоковом сепараторах отделяются черные и цветные металлы. После этого отходы рассеиваются по крупности на тонкую и грубую фракции (например по крупности 20 см). Обе фракции подвергаются сортировке с целью отбора ме-
158
шающих (нецелевых) компонентов: тонкая фракция сортируется автоматически, а грубая – вручную. После сортировки оба полученных потока целевых компонентов смешиваются (перед этим целевые компоненты с крупностью свыше 20 см могут подвергаться дроблению – например, в случае последующего брикетирования отходов) с получением итогового топлива.
2. Механобиологическая переработка.
Эта технология, как и предыдущая, основана на процессах дробления и сортировки отходов: она предполагает дробление крупных включений, сепарацию ценных и балластных компонентов (посредством сортировки, грохочения или других операций) и биологическую переработку остатка для снижения объема отходов. Биологическая переработка может заключаться в компостировании отходов либо в их сбраживании. Таким образом, помимо топлива в качестве полезных продуктов на конечной стадии переработки получают компост и/или биогаз, который может быть использован для производства электроэнергии, тепла либо в локальной системе газоснабжения.
3. Механобиологическая стабилизация.
В данном варианте ТКО после предварительного дробления подвергаются аэробной стабилизации (аэробному компостированию в бункерах или туннелях, при котором в отходах снижается содержание органики). Далее отходы сепарируются на легкую и тяжелую фракции, из которых средствами магнитной и вихретоковой сепарации извлекаются металлы. Легкая фракция после этого используется как топливо, а из тяжелой фракции после дополнительной сортировки извлекаются опасные и инертные компоненты, после чего остатки сортировки направляются на захоронение. Получаемый RDF содержит повышенное количество органического материала и поэтому отличается более низким качеством, однако выход топлива в данном случае выше, чем в предыдущих двух.
4. Физико-механическая стабилизация.
ТКО подвергаются грубому измельчению и просеиванию. Мелкая фракция отправляется на захоронение. Из крупной фракции отбираются металлы. Выходящий поток отходов высушивается
159
(обычно в барабанной сушилке). Далее высушенные отходы просеиваются и разделяются по плотности. Легкая фракция используется в качестве топлива. В некоторых случаях из тяжелой фракции отделяется стекло, после чего фракция захоранивается. Ввиду затрат внешней энергии на сушку, стоимость переработки ТКО по этой схеме возрастает.
Независимо от технологии производства конечный продукт может поставляться потребителю в двух видах: в виде сыпучей смеси либо в виде спрессованных гранул (пеллетов).
3.7. Захоронение ТКО
Согласно федеральному закону «Об отходах производства и потребления», захоронение отходов – это «изоляция отходов,
не подлежащих дальнейшей утилизации, в специальных хранилищах
вцелях предотвращения попадания вредных веществ в окружаю-
щую среду». От захоронения отходов следует отличать хранение отходов – «складирование отходов в специализированных объектах сроком более чем одиннадцать месяцев в целях утилизации, обез-
вреживания, захоронения». Захоронение и хранение отходов входят
всостав более широкого понятия – размещение отходов. Основное отличие захоронения отходов от их хранения связано с конечной целью размещения: в случае захоронения – это максимально надежная изоляция отходов от окружающей среды, в случае хранения – это последующие утилизация, обезвреживание или захоронение отходов (т.е. хранение не является конечным этапом в цепочке действий по обращению с отходами). Захоронение ТКО осуществляется на специализированных сооружениях – полигонах.
Для обеспечения безопасного захоронения ТКО в окружающей среде необходимо предусматривать проведение специальных мероприятий и применение защитных средств, называемых барьерами. Многобарьерная защита предполагает использование комплекса организационно-технических мероприятий, направленных на снижение эмиссии загрязняющих веществ от полигона в окружающую среду.
160