
книги / Основы физики и механики разрушения
..pdf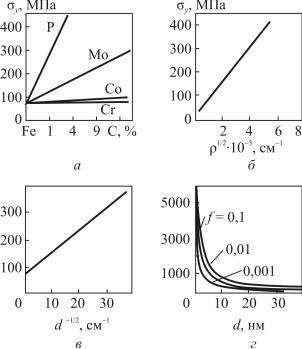
стичности и повышения склонности металлического сплава к хрупкому разрушению. В связи с этим интерес представляет определение тех границ, в которых эффективно действует каждый из механизмов упрочнения применительно к сплавам на основе α-железа.
Твердорастворное упрочнение − это упрочнение, возникающее
врезультате искажений кристаллической решетки матрицы из-за присутствия в ней примесных атомов. Растворение легирующих элементов
вжелезе может происходить по типу замещения и внедрения. Атомы замещения практически не влияют на прочность сплава, так как они изоморфны решетке матрицы и имеют близкий атомный радиус с ато-
мами матрицы (данном случае − железа).
Рис. 1.1. Упрочнение α-железа посредством различных механизмов: а – образование твердого раствора замещения; б – увеличение плотности дислокаций (деформационное упрочнение); в – упрочнение границами зерен; г – максимальное упрочнение частицами (расчетные значения)
Примесью внедрения, оказывающей наибольший упрочняющий эффект в сплавах на основе α-железа, несомненно, является углерод. В литературе имеется достаточно большое количество данных [1, 5], свидетельствующих о том, что с увеличением содержания углерода
11
взакаленной стали до 0,2 % сопротивление пластической деформации быстро возрастает. При увеличении содержания углерода от 0,2 до 0,4 % темп нарастания сопротивления пластической деформации снижается, а при дальнейшем увеличении содержания углерода в закаленной стали упрочнения практически не происходит. В работе Э. Хорнбогена [1] имеется прямое указание на то, что при содержании углерода
вFe–C мартенсите более 0,1 % твердорастворное упрочнение преобладает над упрочнением за счет дефектов решетки.
Ю.Я. Мешков в работе [6] получил следующее соотношение между
пределом текучести и сопротивлением пластической |
деформации |
в пределах одного зерна для сплавов на основе α-железа: |
σ0 = 0,7 σт. |
Данное соотношение говорит о том, что вклад внутризеренных механизмов упрочнения в общий уровень прочности не должен быть слишком большим, чтобы не привести к потере вязкости. При содержании углерода более 0,1 % твердорастворное упрочнение является доминирующим механизмом упрочнения железоуглеродистого мартенсита. Очевидно, что содержание углерода, равное 0,1−0,2 %, и является той разумной границей, до которой данный механизм действует эффективно, т.е. при значительном повышении уровня прочности (предел прочности и предел текучести возрастают примерно на 500−750 МПа) пластичность и сопротивление хрупкому разрушению остаются на достаточно высоком уровне.
Зернограничное упрочнение − это упрочнение границ зерен и элементов субструктуры, которые являются препятствиями на пути движения дислокаций.
Известно, что при уменьшении размеров элементов микроструктуры сопротивление пластической деформации увеличивается в соответствии с зависимостью Холла – Петча:
σт = σ0 + Ky d −1/2 ,
где σ0 – напряжение, необходимое для поддержания скольжения внутри зерна (напряжение трения); Ky − постоянная, зависящая от типа
и состояния границ; d − средний размер элемента структуры, в пределах которого происходит скольжение, Ky d − напряжение, необхо-
димое для эстафетной передачи скольжения от одного элемента структуры другому.
12
С другой стороны, в литературе имеются данные [7], что напряжение хрупкого разрушения σкр также увеличивается при уменьшении размеров зерна:
σкр |
= |
l |
βγGd −1/2 , |
|
|||
|
|
k |
где β − коэффициент, связанный с типом напряженного состояния; γ − эффективная энергия образования поверхности разрушения; G − модуль сдвига; d − средний размер зерна; k = σd0 l−1/2 (σd − напряжение, необходимое для отрыва дислокаций от атмосфер, l − расстояние между источниками дислокаций).
В своих работах [6, 8] Ю.Я. Мешков приводит зависимости сопротивления микросколу от размеров элементов структуры:
Rмc = Kpd −1/2 ,
где Kр − константа, зависящая от типа субмикротрещины; d − размер элемента структуры, в котором возникает субмикротрещина.
В тех случаях когда субмикротрещина возникает у границы ферритного зерна, перлитной колонии, мартенситного или бейнитного па-
кета, Kр = 18 кГ·мм−3/2, или Kр 6 МПа·м−1/2.
Таким образом, измельчение элементов микроструктуры одновременно с повышением уровня прочности приводит к снижению склонности металлов к хрупкому разрушению. Однако изменение балла зерна от 2 до 8, легко достигаемое при обычных скоростях нагрева, приводит к сравнительно небольшому росту значений предела прочности и предела текучести [9, 10]. Для получения более существенного повышения прочности стали требуется измельчение аустенитного зерна до 14−15 баллов (диаметр зерна 1−3 мкм), для чего необходимо получение однородной и дисперсной исходной структуры, например с помощью закалки: нагрев со скоростью 100−1000 оС/с при ограничении температуры и времени аустенитизации. Очень малые размеры зерна аустенита, и следовательно, кристаллов мартенсита, в некоторых случаях получают многократным повторением этой обработки (термоциклическая обработка) [10]. Если при обычной термической обработке конструкционных сталей при достижении 8 баллов зерна аустенита размер мартенситных пакетов составляет 7−15 мкм, то при специальной термоциклической обработке получается зерно 15 баллов, а размер мартенситных пакетов уменьшается до 0,5−2,0 мкм [9–11].
13
Таким образом, в случае зернограничного упрочнения сложность заключается не в отыскании границы, до которой данный механизм действует эффективно, а в реализации термообработки, приводящей к формированию сверхмелкого зерна.
Деформационное упрочнение. Деформационным, или дислокационным, называют упрочнение в результате повышения плотности дислокаций, например при закалке, холодной пластической деформации ит.д.
Одним из способов получения высокой плотности дислокаций в материале является холодная пластическая деформация (ХПД). При увеличении степени холодной пластической деформации до 25−30 % прочность низкоуглеродистых сплавов на основе α-железа существенно возрастает, а затем стабилизируется, приближаясь к насыщению [12]. Параллельно с повышением прочности снижается уровень характеристик пластичности, ударной вязкости, вязкости разрушения; критическая температура хрупкости при этом возрастает.
В то же время в литературе имеются данные, что увеличение степени холодной пластической деформации до 20−25 % благоприятно сказывается на уровне предела выносливости низкоуглеродистой фер- ритно-перлитной стали [12]. Кроме того, ХПД повышает пороговый коэффициент интенсивности напряжений, ∆Kth, а также увеличивает сопротивление росту усталостной трещины на парисовском участке диаграммы циклической трещиностойкости [12, 13]. Необходимо также отметить, что сопротивление микросколу Rмс армко-железа и низкоуглеродистых сталей с феррито-перлитной структурой экстремально зависит от степени ХПД, причем максимальный уровень Rмс зафиксирован при степени ХПД е = 30…50 % [6, 8].
Таким образом, деформационное упрочнение при ХПД также может оказаться полезным для повышения прочности низкоуглеродистых сплавов на основе железа, особенно в тех случаях, когда речь идет о повышении сопротивления усталости и циклической трещиностойкости. Судя по литературным данным, степень ХПД, благотворно влияющая на свойства низкоуглеродистых сталей, находится на уров-
не 20−25 %.
Дисперсионное упрочнение. Дисперсионное упрочнение – повышение прочности сплава вследствие образования в нем дисперсных упрочняющих фаз при распаде пересыщенного твердого раствора [1]. Различают упрочнение когерентными и некогерентными частицами.
14
Механизмы дисперсионного упрочнения можно подразделить на основные и косвенные. Все основные механизмы базируются на том, что дисперсные частицы являются препятствиями на пути движения дислокаций, вследствие чего повышается предел текучести материала. Косвенные механизмы упрочнения связаны с влиянием дисперсных частиц и собственно распада пересыщенного твердого раствора на характер субструктуры [1]. К основным упрочняющим фазам относятся карбиды, нитриды, карбонитриды, интерметаллиды.
Дисперсионное упрочнение когерентными выделениями описывается моделью Мотта – Набарро [9]. Когерентные выделения создают вокруг себя поле упругих напряжений. Дислокации при своем скольжении перерезают когерентные выделения. Получаемый при этом прирост прочности
∆τ = 2Gмεf ,
где Gм − модуль сдвига матрицы; f – объемная доля когерентных частиц; ε – параметр несоответствия кристаллических решеток матрицы и выделений.
Дисперсионное упрочнение некогерентными выделениями описывается механизмом Орована [5]. Механизм предложен для случая, когда расстояние между частицами значительно превышает их радиус. Модель применима в случаях, когда в матрице находятся более жесткие
частицы (Gч > Gм).
Согласно модели Орована дислокация удерживается некогерентными выделениями до тех пор, пока прилагаемое напряжение не станет достаточным для того, чтобы линия дислокации изогнулась и прошла между частицами, оставив вокруг них дислокационную петлю. Получаемый прирост прочности
|
1 |
|
|
|
|
λ |
, |
|
∆τ = |
|
Gb |
Φ ln |
|||||
|
|
|
|
|||||
|
2π λ |
2b |
где λ − расстояние между частицами; Ф − коэффициент, учитывающий тип дислокации [5, 9].
Оптимальные размеры частиц упрочняющей фазы, при которых упрочнение максимально, очевидно, определяются их химсоставом и характером выделения (когерентные, некогерентные). Так, в сплавах железа, легированных медью, наибольшее упрочнение дают обогащен-
15

ные медью кластеры размером около 12,5 нм [1]. Частицы большего размера могут сами служить источниками дислокаций, и тогда они определяют поведение сплава при упрочнении, а также слабую зависимость предела текучести от размера зерна.
Микролегированные конструкционные стали содержат немного больше эквивалентного количества Ti, V, Hf или Nb с суммарным содержанием легирующех элементов около 1 %. В этих сталях выделения TiC весьма мелкодисперсны. Их упрочняющее действие выше, чем влияние обогащенных медью кластеров, достаточно уже очень малой объемной доли (f ≈ 0,001), чтобы вызвать заметное упрочнение [1].
Электронно-микроскопические исследования мартенситностареющих сталей показывают, что после термической обработки на максимальную прочность в структуре сталей наблюдаются два типа выделений: игольчатые и чечевицеобразные. Игольчатые выделения имеют d ≈ 5 нм (50 Å), l ≈ 20 нм (200 Å), среднее расстояние между ними 10−20 нм (100−200 Å). Эти выделения, вероятнее всего, имеют структуру Ni3Ti [14]. Чечевицеобразные выделения (Fe2Mo, Ni3Mo) – диаметром около 15−20 нм (150−200 Å) и толщиной около 5−10 нм (50−100 Å), среднее расстояние между ними 30−50 нм (300−500 Å) [14].
В соответствии с представлениями современной дислокационной теории [13, 15] радиус частиц, до которого сохраняется когерентность выделившейся фазы с матрицей,
r< 4γs ,
ε2G
где γs – поверхностная энергия на границе раздела фаз; ε − параметр несоответствия периодов решеток матрицы и фаз выделения.
Из формулы видно, что для увеличения размеров частиц, в которых не наблюдается перестаривания, необходимо легировать их элементами, уменьшающими различия в параметрах решеток матрицы
ивыделяющейся фазы.
1.2.Упрочнение в результате формирования мартенситной структуры
Врезультате мартенситного превращения в сталях реализуются сразу несколько (2−3) из четырех перечисленных механизмов, вот почему закалка на мартенсит является одним из наиболее распространенных технологических приемов упрочнения сталей.
16
PNRPU
Важно отметить, что вклад того или иного механизма упрочнения решающим образом зависит от химического состава стали, в том числе от содержания углерода. Так, в низкоуглеродистых сталях и безуглеродистых сплавах (содержание углерода менее 0,1 %) доля твердорастворного упрочнения сравнительно невелика, а доминирующим является дислокационное и субструктурное упрочнение. С увеличением содержания углерода вклад твердорастворного упрочнения увеличивается.
1.2.1. Мартенситное превращение и морфологические типы мартенсита в сплавах на основе железа
Мартенситное превращение является сдвиговым фазовым превращением и состоит в закономерной перестройке решетки, при которой атомы железа не обмениваются местами, а лишь смещаются один относительно другого на расстояния, не превышающие межатомные. В результате превращения твердый раствор внедрения углерода в α-железе упорядочивается и имеет тетрагональную решетку, степень тетрагональности которой зависит от содержания углерода. Состав исходной и конечной фаз одинаков [10].
Известно, что система всегда стремится к минимуму затрат энергии при превращении. Это условие определяет следующие характерные признаки мартенситной структуры [10, 16]:
1.Между решетками исходной и конечной фазы имеется определенное ориентационное соотношение.
2.Наиболее типичной структурной формой новой фазы является пластина, толщина которой много меньше других линейных размеров.
3.Габитусная плоскость пластины имеет определенную ориентировку относительно кристаллографических осей исходной и конечной фаз.
4.Изменение формы превращенной области создает характерный рельеф на поверхности образца.
5.Кристаллы мартенсита обладают закономерной субструктурой.
6.Имеется тенденция к упорядоченному взаимному расположению мартенситных кристаллов.
Для углеродистых сталей существует определенное ориентацион-
ное соотношение: (111)А || (110)М и [110]А || [111]М, которое называют соотношением Курдюмова – Закса. Из одного кристалла аустенита могут образоваться 24 различно ориентированных кристалла мартенсита, которые удовлетворяют этому условию [16, 17].
17
В сплавах на основе железа существуют два основных морфологических типа мартенсита: пластинчатый и реечный [17].
Пластинчатый мартенсит образуется в две стадии: первая соответствует двойникованию и образованию зоны мидриба; на второй стадии происходит скольжение и образование периферийной части кристалла с неплоскими поверхностями. Эти периферийные области мартенситного кристалла заполнены дислокациями с относительно невысокой плотностью (109–1010 см–2) [17].
Пакетный (реечный) мартенсит образуется по механизму скольжения. Элементарный объем превращения имеет форму рейки, каждая из которых является результатом гомогенного сдвига. Последовательные сдвиги образуют пакет параллельных реек. Рейки в пакете разделяются как малоугловыми, так и высокоугловыми границами или находятся в двойниковой ориентации [18–20]. По данным работы [20] отношение числа высокоугловых границ к малоугловым составляет 1:5. Внутри реек наблюдаются клубки и сплетения дислокаций с плотностью 1010–1011 см–2 [16]. В пределах исходного аустенитного зерна образуется несколько пакетов мартенсита, имеющих различную ориентировку. В каждом пакете рейки имеют примерно один и тот же размер, который практически не зависит от размера исходного аустенитного зерна [20]. Поперечный размер реек составляет от 0,1 до нескольких микрон, наиболее часто встречаются рейки с поперечным размером 0,2 мкм [18, 19].
Морфология мартенсита определяется температурной зависимостью механизмов пластической деформации превращения. Из рис. 1.2 [16], следует, что при t > T0 формируется реечный мартенсит (превращение идет по механизму скольжения), а при t < T0 формируется пластинчатый мартенсит (по механизму двойникования).
Мартенситное превращение протекает в интервале температур Мн−Мк, и очевидно, что тип мартенсита определяется соотношением между Т0 и Мн−Мк. Если на известную схему А.П. Гуляева [21] нанести Т0 (рис. 1.3), то становится ясно, что в углеродистых сталях, для которых Мк > Т0 (стали с содержанием углерода % С < С1), формируется только реечный мартенсит; в сталях, для которых Мн < Т0 (содержание углерода % С > С2), − только пластинчатый мартенсит; и наконец, в сталях, для которых Мк < Т0 < Мн (С1 < % С < С2), присутствуют оба типа мартенсита.
18
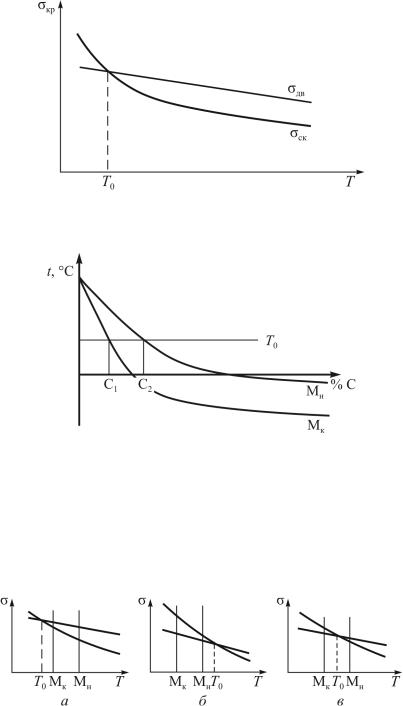
Рис. 1.2. Температурная зависимость напряжений скольжения и двойникования
Рис. 1.3. Схема А.П. Гуляева с нанесенной на нее Т0
Данную схему можно представить в виде трех случаев (рис. 1.4). В первом случае (рис. 1.4, а) Мк > Т0 − формируется реечный мартенсит, во втором случае (рис. 1.4, б) Мн < Т0 − формируется пластинчатый мартенсит, а в третьем случае (рис. 1.4, в) в стали присутствуют оба типа мартенсита.
Рис. 1.4. Варианты соотношения мартенситного интервала Мн−Мк и температуры Т0: а – Мк > Т0; б – Мн < Т0; в – Мк < Т0 < Мн
19
В углеродистых сталях переход от пакетного мартенсита к пластинчатому наблюдается в интервале 0,6−1,0 % С, при этом сосуществуют оба типа мартенсита [22]. Ниже этого интервала мартенсит в углеродистых сталях в основном пакетный, выше − пластинчатый. По данным [13] смена механизма превращения обусловлена сильным упрочнением аустенита по мере увеличения содержания углерода в стали. Таким образом, морфология мартенсита определяется составом сплава и, как следствие, температурой мартенситного превращения.
1.2.2. Влияние морфологического типа мартенсита на механические свойства сталей
Морфологический тип мартенсита в Fe−C сплавах оказывает влияние не только на их прочность, но и на весь комплекс механических свойств. Сочетание высокого уровня прочности и трещиностойкости малоуглеродистых сталей с реечным мартенситом [22, 23] является следствием целого ряда его структурных особенностей по сравнению с пластинчатым мартенситом. Малые размеры элементов субструктуры (толщина реек составляет примерно 0,2 мкм) и высокая плотность дислокаций в их внутренних объемах (1010−1011 см–2) обеспечивают уровень прочности 1000−1100 МПа, а низкое содержание углерода в твердом растворе минимизирует искажения решетки и, следовательно, силу Пайерлса – Набарро, что обеспечивает высокую пластичность при высоких напряжениях, когда наступает общая текучесть.
Кроме преимущественного дислокационно-субструктурного упрочнения реечного мартенсита существует еще целый ряд его структурных особенностей, препятствующих локализации пластической деформации и инициации хрупкого разрушения. Во-первых, в реечном мартенсите практически полностью отсутствуют двойниковые прослойки, границы которых являются эффективными барьерами на пути движущихся дислокаций [20] и, как следствие, − местами зарождения хрупких трещин. Во-вторых, соотношение высокоугловых и малоугловых границ в пакете мартенсита составляет 1:5 [20]. При этом малоугловая граница может работать как полупроницаемая: при определенных критических напряжениях в голове дислокационного скопления происходит прорыв дислокационной границы, часть дислокаций уходит в соседний объем, и напряжения в голове скопления уменьшаются [24]. В-третьих, установлено [25], что практически полное закрепление дис-
20