
книги / Новые материалы и технологии.-1
.pdfсхема получения борных волокон. Вольфрамовая нить сматы вается с подающей катушки и с малой скоростью протягивается через реактор. Длина реактора составляет около 2 м, в нем идет химическая реакция
2ВС13 + ЗН2 «-> 2В + 6HCI. |
(4) |
Выделенный атомарный бор осаждается на разогретой вольфрамовой нити. Процесс осаждения низкопроизводитель ный: получают около 900 г волокон за неделю.
Рассмотрим технологию получения бороалюминиевого композита. Здесь важным является этап совмещения армирую щих волокон с матричным материалом. Это совмещение можно осуществить по-разному:
•в твердофазном состоянии;
•в жидкофазном состоянии матрицы;
•осаждением (напылением) матрицы. Для твердофазного ме
тода характерно использова ние матрицы в виде порошка, тонкого листа (фольги). Про цесс совмещения заключает
ся в выкладке пакета чере
дующимися |
слоями матрич |
Рис. 21. Выкладка пакета боро |
|
алюминиевого КМ: / - матрица |
|||
|
|
||
ной фольги |
и упрочняющих (алюминиевая фольга); 2 - блоки |
||
волокон (рис. 21). |
борных волокон |
||
|
Соединение в монолитный композит осуществляется пла
стическим прессованием со спеканием (диффузионной сваркой). Прессование проводится мягко, с небольшой скоростью при температуре 550 °С, давлении 50... 100 МПа, с последующей
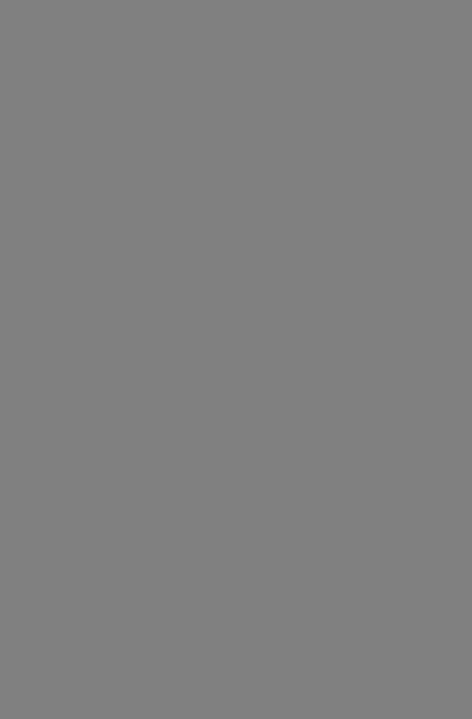
Рис. 23. Схема плазменного напыления ци линдрической заготовки: / - плазмотрон; 2 - оправка; 3 - борные волокна; 4 - напы ляемая матрица; 5 - радиальная подача;
б- продольная подача; ш - вращение оправки
Внастоящее время на базе металлургических производств организован выпуск полуфабрикатов в виде листов, труб, стержней и различных профилей (см. рис. 22).
Сложность технологии и высокая стоимость материала ограничивают применение этих композитов. В основном МКМ используют в авиационной, ракетной и космической технике. Из бороалюминиевого композита изготавливают горизонтальные и вертикальные стабилизаторы, рули, обшивки крыльев, ланжероны, стрингеры, подкосы шасси, лопасти вертолетов, силовые балки самолетов и вертолетов, стержневые конструкции. За счет применения МКМ удается снизить вес этих изделий на 15...40 %, что очень ценно для летательных аппаратов. Одни из перечисленных деталей уже применяются серийно, другие на ходятся на стадии внедрения. Подробнее технологии МКМ и их применение рассмотрены в работе [3], которую очень полезно использовать при изучении КМ.
Это новый КМ конца XX века. Углерод-углеродный ком позиционный материал (УУКМ) занимает особое место среди композитов, что объясняется особенностями его технологии и уникальными свойствами. Данный материал содержит два ком понента: волокна и матрицу, состоящие из одного и того же хи мического элемента - углерода, отличающегося своей тепло стойкостью. Это и предопределяет его основные свойства:
•уникальную термическую стойкость: рабочая темпера тура изделий из УУКМ до 1800...2500 °С, предельная кратко временная температура до 3500 °С;
•способность сохранять при высокой температуре исход ные значения прочности и модуля упругости;
•устойчивость к термоударам (допускает перепады до
1000 °С на 1 см толщины композита;
•высокую эрозионную стойкость;
•химическую инертность, биологическую совместимость;
•низкую плотность по сравнению с плотностью туго плавких металлов;
•высокую ударная вязкость;
•низкий коэффициент линейного температурного расши рения (всего (1... 3 • 1(Г6 ) 1/град).
Армирующий элемент - углеродные волокна - применяют
ввиде нитей, жгутов, стержней, лент, тканей, пряжи, трикотажа, плетеных или вязаных каркасов. Материалом для матрицы слу жат фенольные смолы, каменноугольные и нефтяные пеки, а также пироуглерод.
УУКМ получают тремя способами:
•жидкофазным - пропиткой углеродной заготовки смо лой или пеком с последующей карбонизацией и графитацией;
•газофазным осаждением углерода на каркас;
•комбинированным, сочетающим два предыдущих метода. Доходчиво и подробно эти методы изложены в работе [4],
там же рассмотрены структуры, свойства и механика углеродуглеродных композитов. Ознакомимся кратко с технологиями УУКМ.
7.1. Жидкофазный метод
Основными этапами этой Технологии являются:
•формование исходной углепластиковой заготовки или углеродного каркаса;
•пропитка углеродного каркаса смолой или пеком;
•карбонизация заготовки;
•повторение пропитки и карбонизации (при необходи
мости);
•графитация, с упорядочиванием молекулярной струк туры (по типу графита).
Углепластиковую заготовку получают намоткой или вы кладкой, а иногда и комбинируя эти способы. В качестве свя зующего берут смолу с повышенной способностью к коксова нию. Используют в основном фенолформальдегидные связую щие (коксовое число около 75 %). После отверждения заготовка поступает на карбонизацию в специальные термопечи. Процесс проходит при высокой температуре (примерно 800 °С), при этом горючие вещества выгорают из связующего и остается один кокс (углерод). В печи обеспечивают инертную среду (азот),
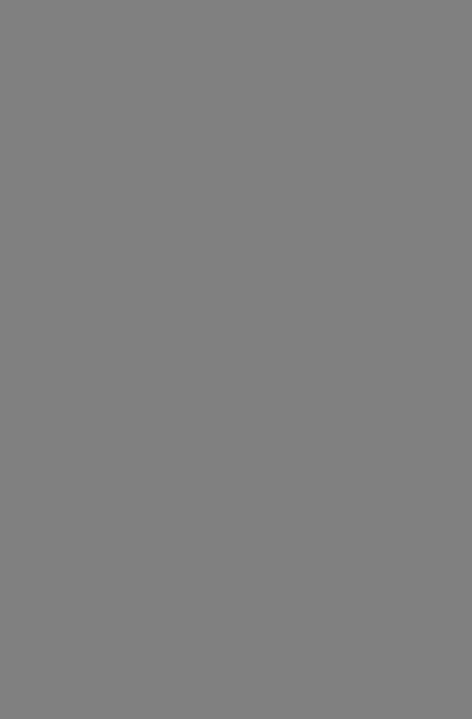
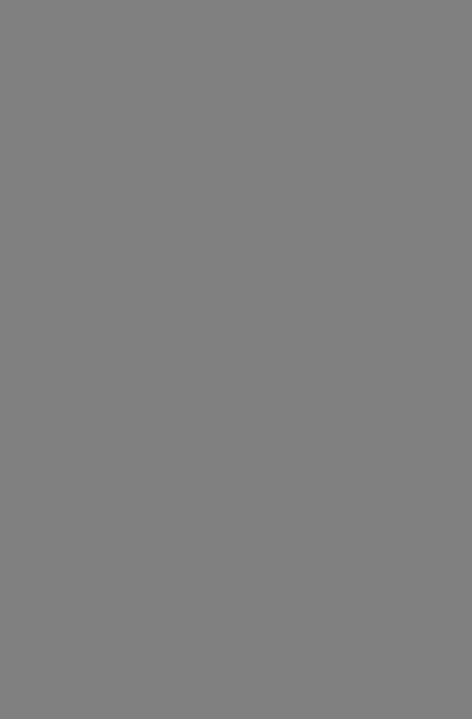
осуществляется в процессе осаждения углерода, получаемого пиролизом природного газа (метана). При нагреве метан разла гается с образованием атомарного углерода:
СН4-+С + 2Н2 |
(5) |
Процесс происходит в специальных печах. Каркас разме щают в печи на подставке и прогревают до температуры 1000 °С, одновременно создавая условия вакуума. Схема про цесса приведена на рис. 26.
Рис. 26. Схема печи для осаждения пироуглерода на каркас УУКМ: 1 - корпус камеры; 2 - индукци онный нагреватель; 3 - графитовый сердечник; 4 - выход Н2; 5 - углеродный каркас обтекателя; 6 - вход СН4 (метана)
Атомарный углерод заполняет объем печи и начинает осаждаться на поверхности углеродных волокон каркаса. Про цесс этот по времени длительный: пироуглерод слой за слоем ложится на волокна, пустоты за счет этого постепенно умень шаются и заполняются полностью. Различают два метода осаж дения пироуглерода:
•изотермический;
•термоградиентный.
При изотермическом методе весь объем заготовки равно мерно прогрет при одинаковой температуре, поэтому процесс осаждения углерода идет одновременно и равномерно по всему объему каркаса.
При термоградиентном методе каркас прогревается изнут ри, и здесь начинается осаждение углерода. Периферийные уча стки каркаса в это время не прогреты, там осаждения пока нет. С течением времени середина каркаса заполняется матрицей, а за тем фронт этого процесса перемещается постепенно на перифе рию, по мере прогрева каркаса до нужной температуры. Метод обеспечивает более равномерное заполнение матрицей всех уча стков каркаса, а также значительно сокращает длительность про цесса. Он эффективен для каркасов в виде тела вращения.
7.3. Комбинированный способ
Комбинированный способ заключается в последовательном применении двух вышерассмотренных методов к одной и той же заготовке. Эта технология более сложная и длительная. Необхо димость ее применения обусловлена с тем, что при производстве крупногабаритных высоконагруженных изделий насыщение их пироуглеродом затруднено из-за возникновения в локальных уча стках замкнутых пор. Комбинированный способ позволяет ис ключить этот недостаток и получить монолитный плотный ком позит. Способ предусматривает следующие этапы:
• осаждение на «сухой» • каркас пироуглерода с частич ным заполнением пустот;
•пропитку заготовки пеком под давлением 5... 10 МПа при температуре 200...250 °С;
•карбонизацию при температуре около 800 °С;
•графитацию при температуре 2500 °С;
•2...3 цикла повторения предыдущих этапов;
•повторное осаждение пироуглерода.
Врезультате удается получить качественный УУКМ с вы сокой плотностью, около 1,95...2 г/см3, что очень важно для высоконагруженных крупногабаритных изделий.
7.4. Свойства УУКМ и области его применения
Частично эти вопросы были затронуты в предыдущих раз делах. Здесь приведем дополнительные данные, относящиеся к указанной теме. В табл. 7 приведены основные физико-механи ческие характеристики УУКМ (усредненные), для сравнения взят промышленный графит марки ВПП (высокоплотный и прочный).
Таблица 7
Физико-механические характеристики УУКМ и графита
Тип |
Плот |
Прочность на |
Прочность |
Прочность |
|
ность, |
растяжение |
на сжатие |
на изгиб |
||
материала |
|||||
г/см3 |
|
МПа |
|
||
|
|
100...150 |
|||
УУКМ |
1,75...1,95 |
70...100 |
100...200 |
||
Графит ВПП |
1,9 |
10...15 |
40 |
60 |
Анализ данных в табл. 7 показывает, что новый компози ционный углеродный материал (УУКМ) по всем прочностным показателям намного превосходит ранее разработанный графит