
книги / Эксплуатация мостов. Особенности эксплуатации железобетонных конструкций мостов
.pdfВ состав грунтовок-преобразователей входит основа и ортофосфорная кислота, которые смешивают непосредственно перед применением в пропорциях, указанных в табл. 6.3.
6.7.Восстановление бетона конструкции, поврежденной на глубину свыше 30 мм с оголением арматуры
Подготовительные работы:
–очистка поверхностей бетонных конструкций отпыли, грязи;
–удаление старого разрушившегося бетона, продуктов коррозии арматуры металлическими щетками, пескоструйными (дробеструйными) аппаратами;
–удаление жировых пятен ветошью, смоченной ацетоном, бензином или другим растворителем;
–обработка открытой арматуры антикоррозионными составами и пассивирующими пастами;
–установка дополнительной арматурной сетки (при необходимости) для удержания и армирования ремонтного слоя, с тщательным креплением ее к имеющейся арматуре.
Для восстановления данных повреждений применяют бетон следующих составов.
6.7.1. Полимербетон на основе синтетического латекса СКС-65ГП
Состав в весовых частях:
50%-ная латексная эмульсия СКС-65ГП …………..25–30
цемент М400…………………………………………100 песок………………………………………………….100–150
щебень ……………………………………………….200–250
вода …………………………………………………..20–25
Перед нанесением состава поверхность бетона смочить 10%-ной латексной эмульсией, арматуру обработать антикоррозионными составами и пассивирующими пастами.
Опалубку снимать через 5–7 сут. Уход за бетоном не нужен. Предпочтительная область применения – средние балки.
81
6.7.2. Полимербетон на основе поливинилацетатной эмульсии
Состав в весовых частях:
–50%- ная латексная эмульсия ПВА…………………… 25–30
–цемент М400 …………………………………………... 100
–песок …………………………………………………… 100–150
–щебень………………………………………………….. 200–250
–вода……………………………………………………... 35–40.
Перед нанесением состава бетонную поверхность смочить из краскопульта 10%-ной эмульсией ПВА.
6.7.3. Обычный бетон по грунтовке КЦК
Состав и приготовление КЦК см. в п. 6.5.2. Состав бетона в весовых частях:
–цемент М400 ………………………………………….100
–песок …………………………………………………..135
–щебень ………………………………………………...270
–вода ……………………………………………………40–50
Приготовленный КЦК кистью наносят на очищенную бетонную поверхность. Затем по обычной технологии укладывают бетон.
6.8. Технология торкретирования
Для торкретирования используют сухую минеральную смесь с соответствующим соотношением цемента, песка и щебня 1:3(3,5):2. Максимальная крупность зерен щебня – 15 мм. Влажность заполнителей 2–6 %. Марка цемента не ниже М400. Для ускорения схватывания торкретбетона в его состав можно вводить добавку NaCl в количестве 1–2 % от массы цемента. Просеянные и отдозированные цемент, песок и щебень загружают в бетономешалку. Необходимое количество воды (В/Ц = 0,35…0,45) под давлением, превышающим давление на минеральную смесь на 2–1,5 атм, подают при нанесении торкретбетона непосредственно к соплу и регулируют вентилем на сопле.
Количество воды контролируют визуально и подбирают пробным нанесением торкретной смеси на специальный щит. Правильно
82
уложенная торкретная масса имеет факел из смеси одинакового цвета, а поверхность торкрета – жирный блеск. При недостатке воды на поверхности появляются сухие пятна и полосы, образуется значительное количество пыли. Избыток воды приводит к оплыванию смеси, образование мешков на поверхности. Перед нанесением торкретбетона ремонтируемую поверхность следует обработать воздушно-водяной струей из сопла бетон-шприц-машины. При торкретировании сопло должно находиться на расстоянии 80–100 см от обрабатываемой поверхности. Ствол сопла следует перемещать по спирали и держать его перпендикулярно к ремонтируемой поверхности. Средняя толщина слоя, наносимого за один раз не должна превышать 3–5 см, причем каждый последующий слой наносить примерно через 2–4 ч.
При нанесении торкретбетона необходимо следить, чтобы за арматурными стержнями не оставалось пустот.
Поверхность торкретбетона в процессе твердения следует укрывать песком, мешковиной и поливать водой в течение 7 сут. Допускается вместо смачивания водой на свежеуложенную поверхность наносить паронепроницаемые пленочные покрытия для предотвращения преждевременного высыхания поверхности. Для этой цели могут быть использованы кремнийорганическая жидкость ГКЖ-94, пленкообразующие жидкости типа «Помароль», ПМ-86,
ПМ-100А.
При ремонте поверхностей эксплуатируемых мостов целесообразно использовать передвижную торкретную установку, включающую в себя автомобильный прицеп, на котором смонтировано следующее оборудование (рис. 6.1):
–дизельная электростанция ДЭСМ-30;
–бетон-шприц-машина СБ-67;
–система водоснабжения (емкость для воды, водяной насос и необходимая трубная обвязка);
–скиповой подъемник;
–инвентарные передвижные подмости для осмотра и ремонта фасадов;
–ящик для шлангов – воздушного, водяного, материального.
83
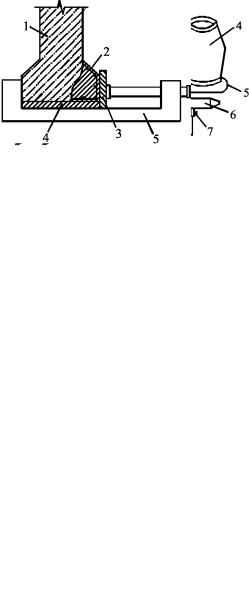
Рис. 6.1. Схема установки для торкретирования РД-802:
1 – компрессор; 2 – воздушный шланг; 3 – влагоотделитель; 4 – бетон- шприц-машина; 5 – материальный шланг; 6 – сопло; 7 – регулировочный вентиль; 8 – водяной шланг; 9 – водяной насос; 10 – емкость для воды; 11 – двигатель
Этот комплект оборудования входит в РД-802. На месте производства работ комплект дополняют передвижной компрессорной станцией производительностью не менее 5 м3/мин (ЗИФ-55, ЗИФ-55 В, ДК-9М, ПР-10). Комплект оборудования обслуживает бригада из четырех человек: моторист компрессора и электростанции, электрик, сопловщик, помощник сопловщика.
6.9. Ремонт локальных повреждений, раковин, сколов
Рассмотрим два различных вида локальных повреждений конструкции мостовой балки железобетонного пролетного строения
(рис. 6.2, 6.3).
Рис. 6.2. Ремонт откола нижнего пояса балки:
1 – железобетонная балка; 2 – ремонтируемый участок; 3 – вертикальная опалубка; 4 – горизонтальная опалубка; 5 – струбцина
84
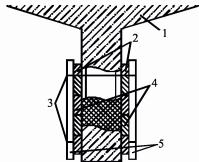
Рис. 6.3. Ремонт сквозного отверстия в ребре балки:
1 – железобетонная балка; 2 – подкладки; 3 – стяжные болты (скрутки); 4 – закладная опалубка; 5 – бруски
6.9.1. Обычные цементные растворы и бетоны
Состав обычных цементных растворов и бетонов приведен в табл. 6.4.
Таблица 6.4 Состав растворов и бетонов в весовых и объемных частях
Материал |
|
Раствор |
|
Бетон |
||
вес. ч. |
|
об. ч. |
вес. ч. |
|
об. ч. |
|
|
|
|
||||
Цемент |
100 |
|
100 |
100 |
|
100 |
Песок |
100–150 |
|
100–170 |
100–150 |
|
120–170 |
Щебень |
– |
|
– |
200–250 |
|
180–210 |
Вода |
45–50 |
|
75–85 |
40–45 |
|
68–75 |
Пластифици- |
|
|
|
|
|
|
рующие воз- |
|
|
|
|
|
|
духововле- |
|
|
|
|
|
|
кающие |
|
|
|
|
|
|
добавки: |
|
|
|
|
|
|
ГКЖ-94 |
0,05–0,2 |
|
|
|
|
|
СНВ |
0,005–0,02 |
|
|
|
|
|
ССБ |
0,15–0,2 |
|
|
|
|
|
6.9.2. Полимерцементный раствор (бетон) на основе ПВАЭ
Состав раствора в весовых частях:
– цемент……………………………… 100
85

– |
песок……………………………….. |
85–125 |
– |
щебень…………………………….. |
– |
– |
вода………………………………… 30–35 |
– 50% ПВАЭ…………………………. 25–30
Состав бетона в весовых частях:
– цемент……………………………… 100
–песок……………………………….. 100–150
–щебень……………………………... 200–250
– вода………………………………… 35–40
– 50% ПВАЭ…………………………. 25–30
Раствор (бетон) укладывают мастерком (при больших объемах раствора (бетона) насосом) на очищенную и увлажненную 10–15 % ПВАЭ поверхность. При ремонте сквозного отверстия по рис. 6.3 бетон подается через отверстие внизу щита (поз.4).
Предпочтительная область применения – средние балки.
6.9.3. Полимерраствор (бетон) на основе эпоксидных смол
Полимеррастворы (бетоны) приготовляют на основе смол ЭД-20, ЭД-22, ЭИС-1, ЭД-5, ЭД-6 (табл. 6.5).
|
|
|
|
Таблица 6.5 |
|
Состав полимерраствора (бетона) в весовых частях |
|||||
|
|
|
|
|
|
Материал |
|
Состав на основе смол |
|
||
ЭД-20, ЭД-22, ЭИС-1 |
ЭД-5 |
ЭД-6 |
|||
|
раствор |
бетон |
раствор |
||
Смола |
100 |
100 |
100 |
100 |
|
Деготь |
70 |
50–70 |
|
|
|
Растворитель |
– |
– |
20–22 |
20–22 |
|
Отвердитель |
8–12 |
8–12 |
11–13 |
9–12 |
|
(ПЭПА) |
|||||
|
|
|
|
||
Пластификатор |
– |
– |
– |
20–25 |
|
(дибутилфталат) |
|||||
|
|
|
|
||
Песок |
400 |
350 |
580–650 |
550–650 |
|
Щебень |
– |
500 |
– |
– |
|
Тонкомолотый напол- |
|
|
|
|
|
нитель (андезит, квар- |
– |
– |
250–300 |
250–300 |
|
цевый песок, цемент) |
|
|
|
|
86
Составы приготавливают в следующем порядке: в эпоксидную смолу вводят деготь и перемешивают, вводят отвердитель ПЭПА и снова перемешивают в течение 4–5 мин. Затем небольшими порциями добавляют песок и снова перемешивают. В последнюю очередь вводят щебень. Если дефект находится в сжатой зоне, деготь вводят в количестве 30 вес. ч. Составы укладывают по эпоксидной грунтовке. Опалубка может быть снята через 10–15 ч после затворения смеси отвердителем. Выбор применения бетона или раствора зависит от глубины дефекта. Максимальная крупность заполнителя должна быть не более 1/4 глубины дефекта и не более 15 мм. Предпочтительная область применения – крайние балки, поверхности опор.
6.9.4. Бетон на комплексном вяжущем КЦК
Состав в весовых частях:
–коллоидно-цементный клей ………………100
–песок ………………………………………..135
–щебень………………………………………270
–вода …………………………………………40
Бетон на вяжущем КЦК приготавливают и укладывают по обычной технологии бетонирования с той лишь разницей, что он должен быть подвергнут в течение 10 мин виброактивации при помощи вибробулавы вибратора с частотой 10–14 тыс. колебаний в 1 мин. Предпочтительная область применения – средние балки.
87
7. УСТРАНЕНИЕ ТРЕЩИН В ЖЕЛЕЗОБЕТОННЫХ КОНСТРУКЦИЯХ
Влага, попадающая в трещины бетонных конструкций, разрушает его периодическими циклами замораживания-оттаивания. Арматура от присутствия влаги, проникающей через трещины в защитном слое корродирует. Все трещины в бетоне, как и мелкие раковины, должны быть заделаны.
Способ заделки трещин выбирают в зависимости от причины их образования, степени влияния на грузоподъемность и долговечность сооружения, а также от величины раскрытия трещины и ее способности раскрываться под временной нагрузкой и от изменения температуры.
Трещины, расположенные вдоль арматуры и вызванные распиранием бетона изнутри продуктами коррозии арматуры, устраняют путем удаления защитного слоя бетона, очистки арматуры, ее обработки и восстановления защитного слоя по технологии заделки крупных дефектов.
Стабилизировавшиеся трещины рекомендуется заделывать жесткими цементными и полимерцементными составами, а трещины, изменяющиеся под воздействием временной нагрузки и температуры, – материалами, обладающими высокими эластичными свойствами. Эти составы не восстанавливают сниженную трещинами жесткость конструкции, а только защищают арматуру и внутренние части бетона от просачивания влаги.
При изменении трещин на 0,1 мм их покрывают полимерцементными составами на основе эпоксидных смол или латекса СКС-65ГП, а при изменении трещин на 0,15 мм и более их покрывают более эластичными материалами, например, тиоколовыми герметиками.
Все работы по заделке трещин ведут в теплое и сухое время года при температуре не ниже 10 ºС. В жаркую погоду работы вести не следует, из-за сокращения жизнеспособности составов. На рабо-
88
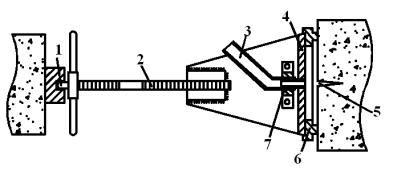
ты по инъецированию трещин с применением механизмов высокого давления 5 атм и более составляют проект с расчетом элементов на прочность.
7.1. Герметизация трещин без восстановления целостности элемента
Поверхностная герметизация – покрытие сетки трещин рас-
крытием до 0,15 мм защитными пленкообразующими материалами аналогично устранению шелушения бетона (см. подразд. 6.3).
Глубинная герметизация – нагнетание в трещины на глубину 2–3 см атмосферостойких и эластичных материалов (герметиков, эпоксидных компаундов, составов на основе синтетического латекса, тиокола и др.). Глубинную герметизацию выполняют ручным шприцем при давлении до 0,4 МПа.
Резиновый уплотнитель шприца (наконечник) охватывает участок трещины длиной 5 см. После нагнетания материала шприц без отрыва от бетона передвигают вдоль трещин на 4–5 см и продолжают нагнетание (рис. 7.1).
Рис. 7.1. Ремонт трещин методом инъецирования: 1 – шарнир-упор; 2 – винтовой домкрат; 3 – резиновый шланг; 4 – стальная плита; 5 – трещины; 6 – резиновый уплотнитель; 7 – стальная трубка
Для герметизации трещин рекомендуются тиоколовые герметики (табл. 7.1).
89
Состав герметиков в весовых частях |
Таблица 7.1 |
||||
|
|
||||
|
|
|
|
|
|
Материал |
|
Марки герметиков |
|
|
|
У-30М |
АМ-0,5 |
У-30, |
|
51-УТ-38 |
|
|
МЭС-10 |
|
|||
|
|
|
|
|
|
Герметизирующая |
|
|
|
|
|
паста: |
|
|
|
|
|
У-30 |
100 |
100 |
|
|
100 |
А-0,5 |
|
|
|
|
|
У-30, МЭС-10 |
|
|
100 |
|
|
Вулканизирующая |
|
|
|
|
|
паста: |
|
|
|
|
|
№9 |
5–9 |
|
8–15 |
|
|
№30 |
|
17–28 |
|
|
|
67%-ный водный раствор |
|
|
|
|
8–10 |
двухромовокислого натра |
|
|
|
|
|
(Na2Cr2O7) |
|
|
|
|
|
Наполнитель, пластифи- |
– |
– |
– |
|
|
катор – каменноугольная |
|
|
|
|
38,5 |
смола |
|
|
|
|
|
Ускоритель вулканиза- |
– |
– |
0,4–11 |
|
– |
ции – дифенилгуанидин |
|
|
|
|
|
Может также применяться однокомпонентный силиконовый герметик «Эластосил 11-01в».
Типовые герметики готовят в следующей последовательности: в герметизирующие пасты вводят вулканизирующие пасты, смесь тщательно перемешивают в течение 5 мин, затем добавляют ускоритель вулканизации и перемешивают еще 3–5 мин. Частоты вращения мешалок не должны превышать 80 об/мин во избежание нагрева материалов, снижающего жизнеспособность герметика.
Вязкость применяемого состава зависит от величины раскрытия трещин: при а = 0,2…1 мм вязкость должна быть30–60 с, при а = = 1…2 мм – 45–70 с, при а = 2…3 мм – 60–90 с.
Растворителями для тиоколовых герметиков являются: ацетон, этилацетат, циклогексан, растворитель Р-5. Наиболее эффективным
90