
книги / Процессы обработки заготовок. Методы механической обработки поверхностей деталей машин-1
.pdfОтверстия протягивают на горизонтальных и вертикальнопротяжных станках при скорости резания 3–15 м/мин. Подача на зуб – 0,02–0,1 мм.
В настоящее время на ряде передовых предприятий применяют скоростное протягивание со скоростью резания до 25 м/мин. Припуски под протягивание цилиндрических отверстий составляют 0,5–1,5 мм на диаметр. В качестве СОЖ применяют сульфофрезол, масло индустриальное И-20А или 20%-ный раствор эмульсола
вводе сдобавлением 4%-ного мыла.
3.2.ОБРАБОТКА ОТВЕРСТИЙ АБРАЗИВНЫМ
ИНСТРУМЕНТОМ
3.2.1. Шлифование отверстий
Внутреннее шлифование сквозных и глухих цилиндрических отверстий из чугунов, сталей, жаропрочных сплавов обеспечивает точность 5–6-го квалитета и шероховатость поверхности Ra = 0,15...1,25 мкм. Обработку отверстий производят на шлифовальных станках: при вращающейся детали, закрепленной в патроне станка; при неподвижной детали на станках с планетарным движением шпинделя; при вращающейся незакрепленной детали на бесцентрово-шлифовальных станках.
Диаметр шлифовального круга обычно принимают равным 0,8–0,9 диаметра отверстия.
3.2.1.1. Шлифование при вращающейся детали, закрепленной в патроне станка
Наиболее распространен первый способ обработки с продольной или поперечной подачей (рис. 3.13).
Взависимости от свойств обрабатываемого материала
ивида операции, скорость резания при шлифовании изменяется от 25 до 100 м/с.
61
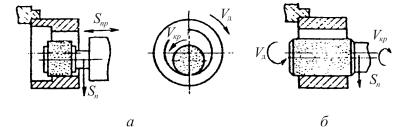
Продольная подача выражается в долях ширины шлифовального круга Вкр и принимается Sпр= (0,2...0,3) Вкр, мм/об при чистовом шлифовании, а при черновом шлифовании – Sпр= = (0,6...0,8) Вкр, мм/об.
Рис. 3.13. Схема шлифования отверстий:
а – с продольной подачей; б – с поперечной подачей
Поперечная подача Sпоп круга при чистовом шлифовании равна 0,003–0,015 мм/дв. ход стола, а при черновом– 0,05–0,075 мм/дв. ход стола. Глубина резания при чистовом шлифовании равна 0,005–0,015 мм, а при черновом – 0,015–0,04 мм. Длина продольного хода стола определяется по формуле: а) при шлифовании на проход (мм)
L = L0 – (0,2–0,4) Bкр;
б) при шлифовании в упор (мм)
L = L0 – (0,4–0,6) Bкр,
где L – длина продольного хода стола (мм); L0 – длина шлифуемой поверхности (мм); Bкр – ширина шлифовального круга (мм).
При черновом шлифовании вращающейся детали, закрепленной в патроне, получают точность 7–8-го квалитета и шероховатость Ra = 0,16...1,25 мкм; при чистовом шлифовании – 5–6-го квалитета и Ra = 0,08...0,32 мкм.
62
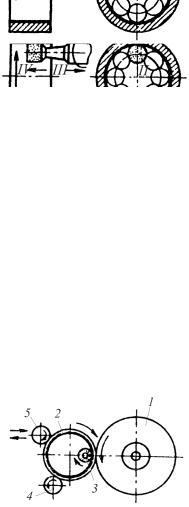
3.2.1.2. Планетарное шлифование отверстий
При этом способе шлифования (рис. 3.14) шпиндель шлифовального станка имеет четыре движения:
–вращение круга вокруг своей оси 1;
–планетарное движение по окружности внутренней поверхности детали, неподвижно закрепленнойнастолестанкаII;
–возвратно-поступатель- ное движение вдоль оси дета-
ли III; |
Рис. 3.14. Схемапланетарного |
– поперечноеперемещение |
шлифованияотверстий |
(поперечнаяподача) IV. |
|
Эта схема шлифования применяется для обработки корпусных деталей.
Точность обработки и шероховатость с планетарным движением шпинделя соответствует:
причерновомшлифовании7–8-муквалитетуиRa = 0,16...1,25 мкм; при чистовом шлифовании 5–6-му квалитету и Ra = 0,08...0,32 мкм.
3.2.1.3. Бесцентровое шлифование отверстий
При этом способе шлифования деталь поддерживается тремя роликами (рис. 3.15). Один ролик является ведущим 1 и создает
вращательное движение детали 2 |
|
относительно шлифовального |
|
круга 3, который вращается во- |
|
круг собственнойоси. |
|
Верхний зажимной ролик 5 |
|
прижимает деталь 2 к ведущему |
|
ролику 1 и третьему опорному |
Рис. 3.15. Схема бесцентрового |
ролику 4. Деталь, зажатая между |
|
тремя роликами, имеет скорость |
шлифования отверстий |
|
63
ведущего ролика. При смене деталей зажимной ролик 5 отводят влево, освобождая деталь 2.
Точность обработки при бесцентровом шлифовании по диаметру соответствует 5–6-му квалитету, Ra = 0,16...1,25 мкм, а концентричность и параллельность осей внутреннего и наружного диаметров достигает 0,003 мм.
3.2.2. Хонингование отверстий
Хонингование (перекрестное шлифование брусками) применяется для обработки предварительно развернутых, расточенных или шлифованных сквозных и глухих цилиндрических отверстий.
Обработка осуществляется хоном – инструментом, имеющим абразивные или алмазные бруски (рис. 3.16).
Хон совершает одновременно вращательное и возвратнопоступательное движения.
Бруски в процессе обработки раздвигаются (радиальная подача). Раздвижение в радиальном направлении брусков осуществляется механическим, гидравлическим или пневматическим устройствами. Давление брусков на поверхность детали
0,1–4,0 МПа.
Существуют также конструкции хонинговальных головок с механическим дозированным раздвижением брусков
(рис. 3.16, а).
Перебег головки на сторону lп составляет 12–15 мм
(рис. 3.16, б).
Для обработки отверстий с прерывистыми поверхностями, например, отверстие со шпоночной канавкой или шлицевое отверстие, используют хонинговальные головки (рис. 3.16, в) с размещением абразивных брусков не параллельно оси головки, а под углом α = 15–30°.
Головка состоит из корпуса 4, в котором шток 2 ввернут в шток 6, соединенный с четырьмя колодками 8, несущими абразивные бруски 9. На штоке имеются два усеченных конуса под углом 15°. Для предохранения от выпадения колодок 8 из корпуса 4 служат две пружины 7.
64
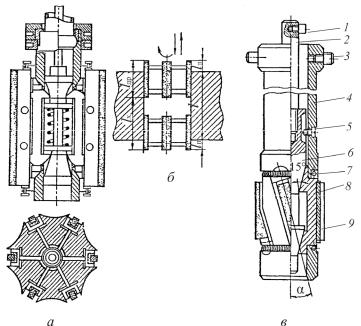
Рис. 3.16. Хонинговальная головка:
а – конструкция; б – схема для определения длины перемещения; в – головка для хонингования шлицевого отверстия
Хонинговальная головка закрепляется в шпинделе станка с помощью шпилек 1 и 3. Шуруп 5 препятствует штоку 6 провертываться. Расположение абразивных брусков под углом 15–30° обеспечивает постоянное перекрытие шпоночных пазов не менее чем двумя брусками одновременно. Режущие зерна хонинговальных брусков изготавливают из электрокорунда, карбида кремния, эльбора или алмаза.
Процесс хонингования осуществляется с СОЖ, выполняющей смазывающее, охлаждающее и вымывающее действие. При обработке чугуна в качестве СОЖ используют керосин с добавкой 10–15 % масла индустриального И-20А, а для стали – смесь из масла индустриального И-20А– 12–25% и керосина – 75–88 %.
65
Для отверстий диаметром 25–500 мм величина припуска составляет 0,02–0,20 мм для чугунных деталей и 0,01–0,08 мм для стальных деталей.
Хонингование производят на горизонтальных и вертикальных одно- и многошпиндельных станках.
Хонинговальная головка вращается со скоростью 60–75 м/мин для чугуна и бронзы и 45–60 м/мин для стали; скорость возвратнопоступательного движения головки – 12–30 м/мин.
Хонингование устраняет овальность, конусность, бочкообразность и обеспечивает точность 5–6-го квалитета и шероховатость поверхности Ra = 0,16...0,63 мкм.
Тонкое хонингование обеспечивает точность 3–4-го квалитета и шероховатость поверхности Ra = 0,04...0,16 мкм.
Хонингование является одним из самых распространенных способов финишной обработки глубоких отверстий, например труб артиллерийских стволов.
3.2.3. Притирка (доводка) отверстий
Притирка – отделочная абразивная обработка, обеспечивающая точность размеров 4–5-го квалитета и шероховатость поверх-
ности Ra = 0,01...0,16 мкм.
Инструментом служит притир, представляющий собой разрезную втулку, создающую давление на стенки отверстия при помощи пружин (рис. 3.17).
Для достижения высокой точности 3–4-го квалитета (овальность и конусность 1–2 мкм) используют притиры с дозированным изменением диаметра притира.
Корпус притира в этом случае изготавливается в виде разрезной втулки с внутренней поверхностью в виде конуса, надетой на ответный конус штока.
При перемещении штока вдоль оси притира разрезная втулка упруго деформируется, изменяя диаметр корпуса притира.
На наружной цилиндрической поверхности корпуса притира наносятся перекрещивающиеся пазы.
66
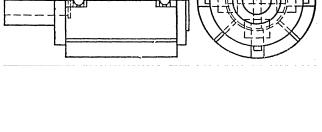
Притиры изготавливают из чугуна, мягкой стали, латуни, меди и других материалов более мягких, чем материал обрабатываемой детали.
Рис. 3.17. Чугунный притир
На поверхность притира наносится паста или суспензия на основе корунда, карбида кремния, карбида бора (зернистостью М2 – М3), алмаза (зернистостью 1–100 мкм).
В качестве связующих материалов в пастах применяют стеарин, парафин, вазелин, олеиновую кислоту и другие составляющие.
Состав связующих материалов паст, как правило, выбирают, основываясь на существующих рекомендациях и производственном опыте.
Притир совершает вращательное (vвр = 15...50 м/мин) и воз- вратно-поступательное (vп = 10...25 м/мин) движения с удельным давлением 0,2–0,5 МПа или работает с дозированной подачей разжимного конуса.
67
4. МЕТОДЫ ОБРАБОТКИ ПЛОСКИХ ПОВЕРХНОСТЕЙ
При обработке плоских поверхностей применяют: строгание, долбление, фрезерование, протягивание, шлифование, полирование, притирку (доводку) и шабрение.
4.1. СТРОГАНИЕ И ДОЛБЛЕНИЕ
Обработку производят на продольноили поперечно-стро- гальных станках (последние называются шепингами) одним резцом или несколькими резцами.
При строгании на продольно-строгальных станках стол с закрепленной на нем обрабатываемой заготовкой (или заготовками) совершает возвратно-поступательное движение; подача в поперечном направлении (поперечная подача) придается резцу путем перемещения резцового суппорта, которое осуществляется прерывисто после каждого рабочего хода. Стружка снимается во время хода стола в одном направлении, то есть во время рабочего хода. Обратный – холостой ход совершается со скоростью в 2–3 раза большей, чем скорость рабочего хода, тем не менее потеря времени при холостых ходах делает строгание менее производительным способом обработки, чем другие способы (например, фрезерование).
Схема строгания плоскости представлена на рис. 4.1.
На поперечно-строгальных станках возвратно-поступа- тельное движение имеет резец, который закреплен на суппорте ползуна. Обрабатываемая заготовка, закрепляемая на столе станка, получает поперечную подачу благодаря прерывистому перемещению стола в поперечном направлении после каждого рабочего хода.
68
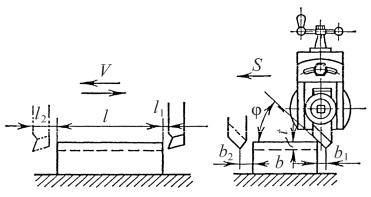
Рис. 4.1. Схема строгания плоскости
Продольно-строгальные станки изготавливают одностоечными и двухстоечными, с одним, двумя, четырьмя и более (до 12) суппортами.
Одностоечные строгальные станки применяют для заготовок, которые не помещаются полностью на столе станка и свешиваются с него.
Продольно-строгальные и поперечно-строгальные станки применяют в единичном, мелкосерийном и серийном производствах вследствие их универсальности, простоты управления, достаточной точности обработки и меньшей стоимости по сравнению с фрезерными станками.
Работы на строгальных станках не требуют сложных приспособлений и инструментов. Однако этот вид обработки малопроизводителен. Низкая производительность объясняется тем, что обработку ведут одним резцом с потерями времени на обратные холостые ходы. Повысить производительность на строгальных станках можно за счет:
–установки нескольких резцов на одной державке, что сокращает число рабочих и холостых ходов и позволяет снимать значительно больший припуск за один проход;
–одновременной работы нескольких суппортов и, следовательно, совмещения времени обработки нескольких поверхностей;
69
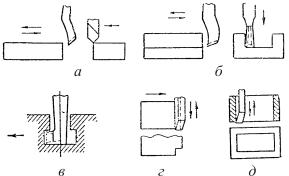
–применения широких резцов и больших подач, специальных установочно-зажимных приспособлений и шаблонов для установки резцов при профильном строгании;
–увеличения скорости холостого хода в 2–3 раза по сравнению со скоростью рабочего хода.
Производительность можно также повысить за счет последовательной или параллельно-последовательной обработки одного илиодновременно несколькихрядовобрабатываемых заготовок.
На долбежных станках, относящихся к классу строгальных, долбяк с закрепленным на нем резцом совершает возвратнопоступательные движения в вертикальной плоскости.
Стол станка, на котором закрепляется обрабатываемая заготовка, имеет движение подачи в горизонтальной плоскости в двух взаимно-перпендикулярных направлениях.
Долбежные станки применяют в единичном, мелкосерийном
исерийном производствах для получения шпоночных канавок в отверстиях, а также для обработки квадратных, прямоугольных
идругих форм отверстий. Для этих же работ в крупносерийном
имассовом производствах применяют протягивание.
Наиболее характерные виды работ, выполняемые на строгальных и долбежных станках, показаны на рис. 4.2, а–д.
Рис. 4.2. Виды обработки на строгальных и долбежных станках: а – строгание плоскости; б – строгание паза;
в– строгание Т-образного паза; г – долбление углового профиля; д – долбление прямоугольного отверстия
70