
2112
.pdf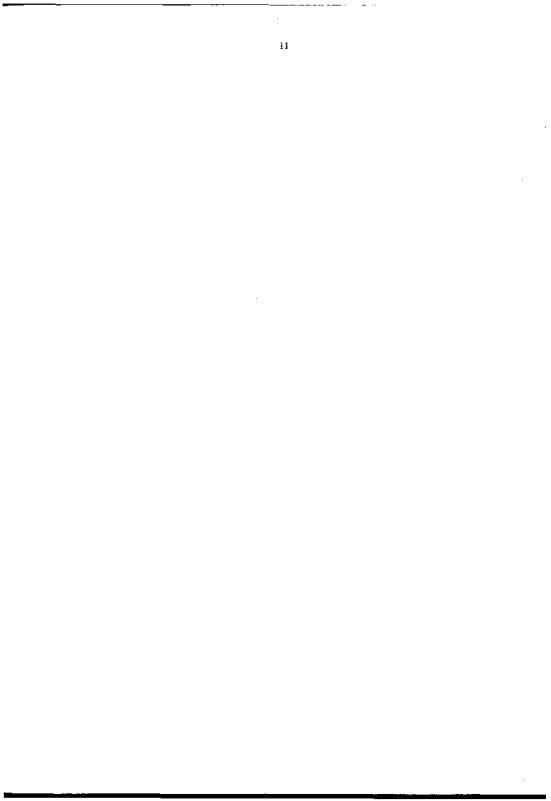
управления, структура и элементное наполнение на основе ограничений в соответствии с требованиями внешней среды. Математически данная модель описывается следующим образом. Верхний уровень - множество А (аj), средний уровеньмножество В (BJ ) и нижний уровеньмножество С (сj ). Любой объект программно-целевого управления описывается как локальный- {С(сi) е B(вi ) e A(ai )},
Обозначенная модель анализируется с целью определения направлений и логики развития процесса организации программноцелевого управления по уровням. В дальнейшем это используется при определении логических взаимосвязей и последовательности решений проектных задач в процессе проектирования системы программноцелевого управления.
На основе анализа вариантов решения задач предприятий в локальном аспекте в пределах каждого уровня структурной модели программно-целевого управления, в диссертации сделан вывод, что выявленные с точки зрения теории организации закономерности могут быть отражены в совокупности общих принципов, согласно которым устанавливается логическая взаимосвязь и последовательность решения задач как в случае полной организации программно-целевого управления, так и в случае локальной организации (организации отдельных подсистем или элементов любого уровня).
На рис. 2. отражена последовательность решения организационных задач в модели развития процесса организации интегрированной системы
программно-целевого управления. Модель отражает логику
взаимодействия и последовательность решения укрупненных задач
организации в соответствии со структурой модели программно-целевого
управления.
Основная цель программно-целевого управления — эффективное использования ресурсов на предприятии. В диссертационном исследовании в этом направлении выделяются три основные задачи.
Инжиниринг системы, включающий разработку требований к выпускаемому продукту (услуге) и планирование рентабельного производства. В эту часть входят организация труда, материальнотехническое снабжение, планирование и оптимизация технологии, организация эффективного капиталовложения.
Управление системой, состоящее в разработке процедур анализа, планирования, координации, составления оперативно календарных графиков, а также в обеспечении системы необходимыми ресурсами.
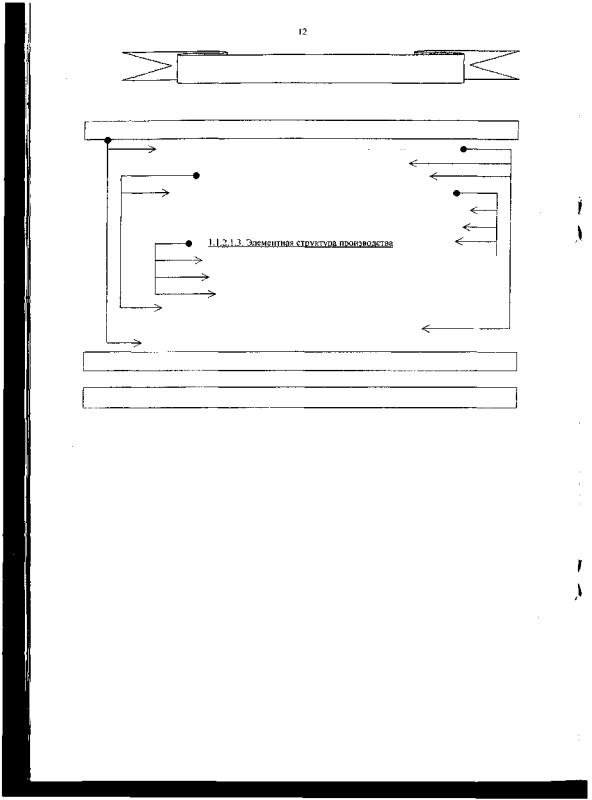
Создание системы программно-целевого управления промышленным предприятием
Задание исходных требований к организации
1.Организация объекта управления
1.1.Структурная организация объекта управления 1 . 1 . 1 . Организация сбыта
1.1.2.Организация производства
1.1.2.3.Организация основного производств а
1.1.2.1.1. Организационная структура производства 1.1.2,1.2.Функциональнаяструктурапроизводства
1.1.2.1.3.1. Структура предметовтруда
1.1.2.1.3.2.Структура средств труда
1.1.2.1.3.3.Структура живого труда
1.1.2.2.Организация обслуживания производства
1.1.3.Организация снабжения
1.2.Организация функционирования объекта управления
2.Организация системы управления
3.Согласование на системном уровне
Рис. 2. Модель организации системы программно-целевого управления
Администрирование системы, включающей принятие решений по всем аспектам эксплуатации и финансирования этой системы.
Вдиссертации разработан алгоритм организации системы программно-целевого управления.
4.Установлены особенности функционирования интегрированной системы программно-целевого управления промышленными предприятиями и определены этапы ее разработки.
Вдиссертации констатируется, что система программно-целевого
управления должна состоять из четырех функционально обособленных подсистем: организационных расчетов; их методической поддержки; моделирования; ведения банка данных. Разрабатываемые в данных подсистемах методы и модели должны строиться как по объектноориентированному, так и по инвариантному принципу. На основе обобщения результатов проведенного анализа методической базы и задач организационного проектирования в диссертации сделаны выводы о том, что в процессе организации трудно формализовать задачи выбора, поэтому
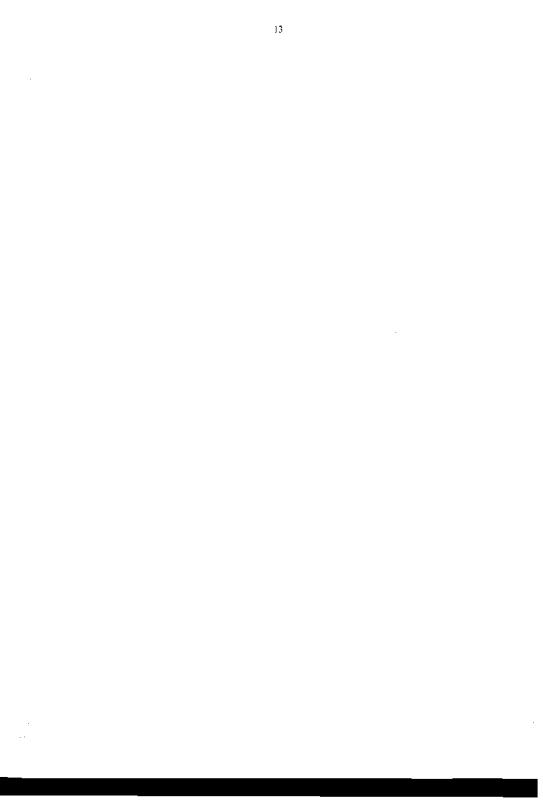
их решение достигается за счет использования экспертных процедур различного уровня.
Важным моментом являться определение способа сведения производственных задач к однокритериальным с помощью: свертывания в один критерий по принципам выбора главного (частного) критерия; построения аддитивного критерия; построения мультипликативного критерия. Кроме выбора способа сведения к однокритериальным задачам необходимо задать объективную оценку для рассматриваемых критериев. После выполнения выделенных этапов, данные задачи могут быть формализованы как оптимизационные, и решаться методами математического программирования.
В качестве главной цели работы ставится разработка рациональных схем соединения в пространстве и во времени всех составляющих производственного процесса - живого труда, предметов труда и средств труда - в заданных производственных условиях с наилучшими техникоэкономическими показателями решения задач, поставленных перед проектируемой системой. Проектирование интегрированной системы программно-целевого управления выполняется при техническом перевооружении, реконструкции и расширении производства, разработке новых производственных процессов или их частей, а также при реализации долгосрочных и текущих программ реорганизации и совершенствования действующего производства.
В диссертации выделяются девять основных принципов построения программно-целевого управления как системы проектных решений: целевая направленность; поступательность; наращиваемость; непрерывность; интегрированность; параллельность; модульность; много вариантность и оптимальность.
По составу задач и характеру принимаемых организационных решений в рамках интегрированной системы программно-целевого управления выделяются две стадии:
-стадия структурной организации производственной системы.
-стадия организации функционирования производственной
системы.
Одной из главных задач организации интегрированной системы программно-целевого управления на ранних стадиях является построение структуры производственной системы и определение основных параметров ее функционирования.
Выбор формы организации интегрированной системы программноцелевого управления производства включает решение следующих задач: а) обоснование типа производства; б) обоснование состава подразделений и их специализации; в) обоснование форм организации подразделений;
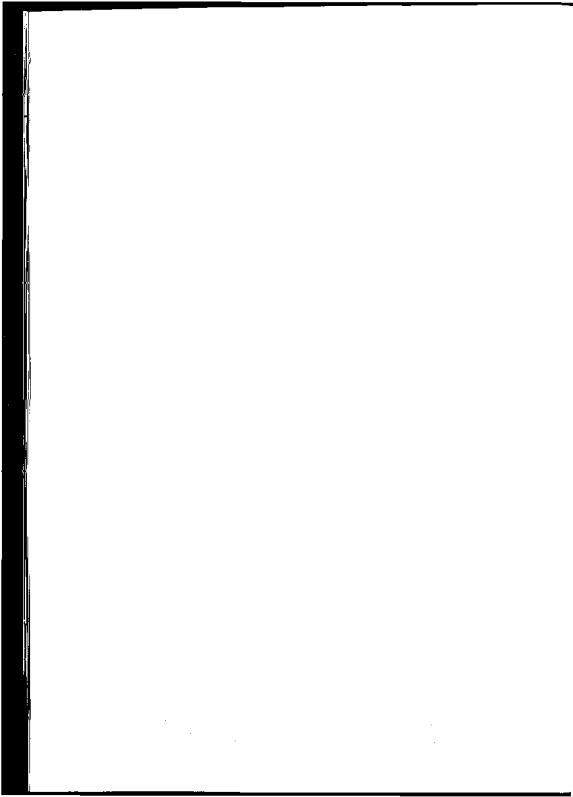
14
г) построение организационной структуры производства.
При организации структуры производственной системы особое значение имеет сопряжение внешних и внутренних связей системы. Сопряжение должно быть обеспечено по: общему объему ингредиентов производства за плановый период; качественному состоянию ингредиентов; способам ориентации и расположения в пространстве; размерам транспортных партий и ритмичности их движения; режимам сменности функционирования потоков. Функции сопряжения во времени и по объемным параметрам выполняют пункты приема/отправки на входевыходе производственной системы.
Результатом процедуры синтеза функциональной структуры производственной системы является ее структурно-функциональная схема изображенная на рис. 3.
Схема дает возможность, подробно описать работу производственной системы, изучить ее поведение в различных режимах работы и производственных ситуациях. Она может служить основой для построения графоаналитических моделей с целью выбора оптимального состава, количества и компоновки оборудования производственной системы в рамках макропроцедуры системотехнического синтеза и предполагает последовательное структурирование предметов труда, средств труда и живого труда, конкретное содержание которых определено на этапе структурно-функциональной организации производственной системы.
5. Определена логика функционирования интегрированной системы программно-целевого управления предприятиями.
Цель интегрированной системы программно-целевого управления на стадии рабочего проекта заключается и том, чтобы дать детальное определение схем функционирования всех элементов (подсистем) производственной системы и их взаимодействия между собой и с внешней средой.
В диссертации определяется порядок выполнения функций в зависимости от сложившейся производственной ситуации, т.е. представлены алгоритмы функционирования по направлениям: организация работы транспортно-накопительной системы; организация функционирования комплекса средств технологического оснащения; организация работы персонала; построение алгоритмической модели функционирования комплекса технических средств.
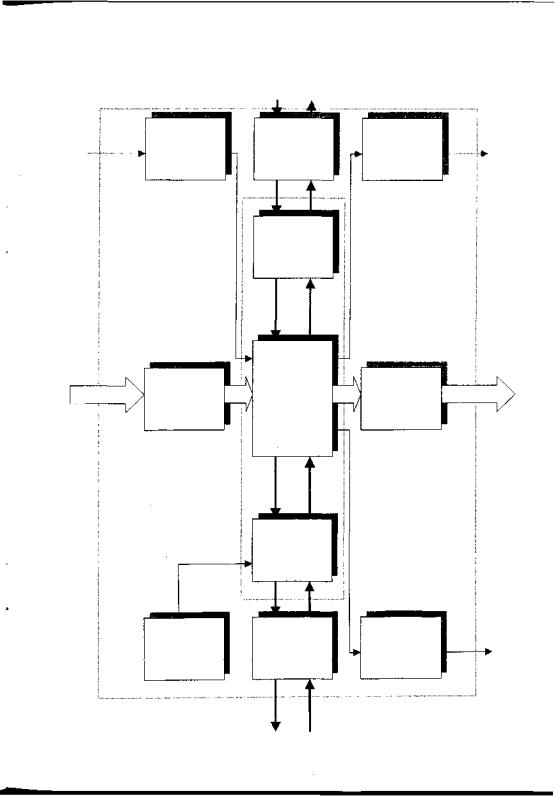
Техническая документация
Входной
поток
проб
15
Рис. 3. Структурно-функциональная схема производственной системы.
Предметы МТО
Инженерно- |
Склад |
Управ- |
техническое |
МТИ |
ляющий |
бюро |
||
|
|
комплекс |
Результаты испытаний
Ремонтное
отделение
|
Гибкий |
|
|
Приемный |
производ- |
Пункт от- |
|
ственный |
|||
пункт |
правки |
||
комплекс |
|||
|
|
Выход
потоков
образцов
Инструментальное отделение
Хозяйст- |
Инстру- |
Пункт уда- |
венная |
менталь- |
ления от- |
часть |
ный склад |
ходов |
От ходы
Техоснастка
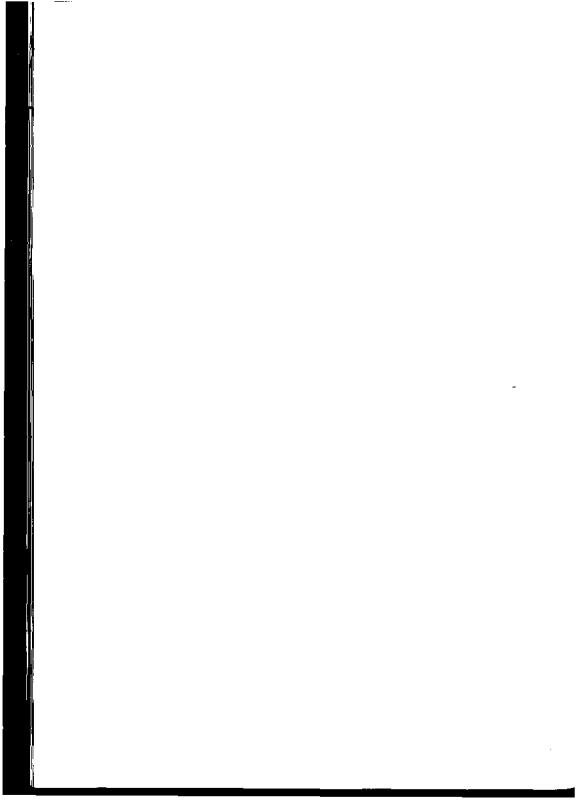
16
На основе использованных в диссертации методов и средств, могут быть разработаны частные методики управления промышленными предприятиями в рамках системы программно-целевого управления, учитывающие отраслевую и/или функциональную специфику объекта, а также целевую направленность организации процесса в каждом конкретном случае. Методику предложено строить по модульному принципу и реализовать в виде пакетов специальных программ для использования автономно при решении локальных задач по выбору пользователя или в составе комплекса средств, обеспечивающих системную интеграцию поставленных задач.
6. Разработана технология применения и практическое обеспечение элементов программно-целевого управления.
Практическая реализация методических положений интегрированной системы программно-целевого управления в диссертации рассмотрена на примере промышленных предприятий Нижегородской области. Результаты проведенного исследования позволили сделать вывод о том, что в среднем длительность производственного цикла выпуска продукции достигает 9-14 суток. Из них 6-10 суток приходится на долю цикла изготовления и испытания продукции, из которых лишь несколько часов непосредственно на процесс изготовления. В связи с этим была поставлена задача осуществить реконструкцию и техническое перевооружение производства на базе гибкой интегрированной системы. Внедрение средств гибкой автоматизации производства сопровождалось внедрением мероприятий по совершенствованию организации производства, труда и управления.
Опыт проектирования подтвердил правильность выдвинутого ранее теоретического положения о том, что концептуальные проектные решения по определению качественного состава структурообразующих элементов производственной системы, формированию их взаимосвязей и связей с внешней средой принимаются на ранних стадиях организации производственной системы.
Исследование связности элементов структуры производственной системы по материальным взаимосвязям показало, что в составе гибкого автоматизированного производства могут быть выделены слабо связанные между собой гибкие производственны комплексы, реализующие главную функцию, а также контур подразделений (подсистем) его обеспечения, выполняющий вспомогательные функции обслуживания основного производства и обеспечивающий функционирование гибких производственных комплексов в автоматизированном режиме в течение заданного временного интервала.
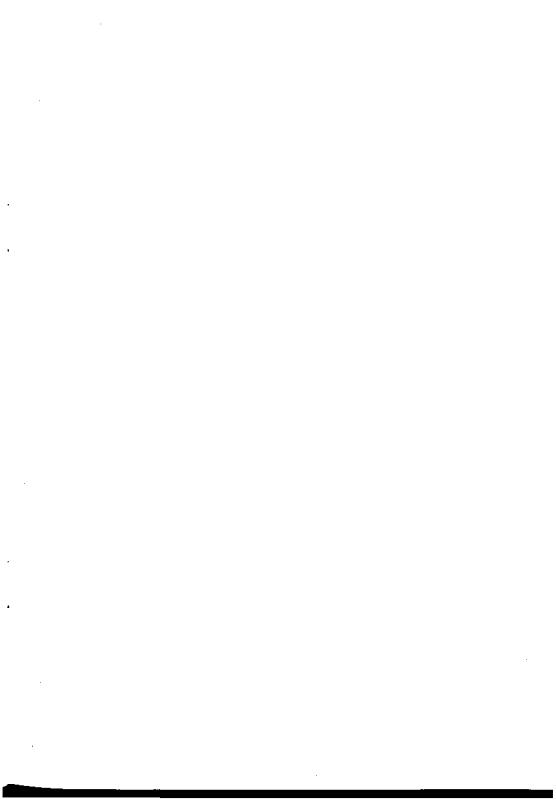
17
На этом основании сделан вывод, подтвержденный результатами имитационного моделирования, об инвариантности реализующих схем структурной организации центра и контура обеспечения интегрированной производственной системы относительно друг друга.
Учитывая факт инвариантности и наличия внешних ограничений при структурной организации ядра и контура обеспечения гибкой интегрированной производственной системы, в диссертации проведено исследование вариантов технологической структуры производственной системы при заданной схеме организации контура ее обеспечения. Для фиксирования принципиальных организационных различий между вариантами предложен подход, основанный на учете технологической, номенклатурной и объемной полноты структурообразующих элементов производственной системы.
7. Предложены концептуальные проектные решения интегрированной системы программно-целевого управления предприятиями и дана оценка эффективности применения данного подхода.
Расчет характеристик функционирования интегрированной производственной системы при изменении объема заказов позволил получить графические зависимости по вариантам, которые использованы для выбора наиболее экономичного варианта на основе анализа критической точки. Как показали расчеты, экономически целесообразным в данных производственных условиях оказалось построение гибкой итерированной производственной системы на базе типовых производственных линий. Это дает возможность осуществлять объемное регулирование выхода производственного ядра относительно изменения характеристик входного потока заказов, обусловленного колебаниями спроса.
Автоматизация на базе интегрированной производственной системы создает предпосылки для широкого использования оптимизационных процедур оперативно-календарного планирования (ОКП).
В диссертации предлагается метод оптимизации порядка запуска в обработку на гибких автоматизированных линиях без промежуточных накопителей с целью повышения пропускной способности производственной системы, заключающийся в построении модели работы линии и оптимизации ее по критерию минимума совокупной длительности цикла обработки всех изделий из текущего портфеля заказов.
Проведенное исследование на основе эксперимента и техникоэкономического анализа вариантов организации функционирования гибкой автоматизированной линии в составе гибкой интегрированной производственной системы позволило сделать вывод об экономической
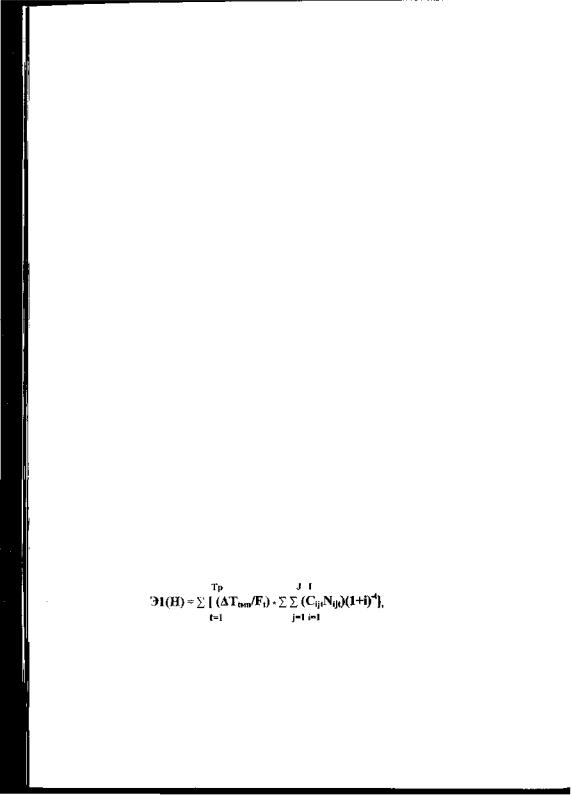
18
целесообразности применения оптимизационных процедур ОКП в процессе эксплуатации гибкой автоматизированной линии. Реализация системы управления гибкой автоматизированной линии в режиме реального времени процедур оптимизации порядка запуска заказов в обработку, основанных на любом из рассматриваемых методов, позволяет сократить длительность совокупного цикла их обработки в среднем на 25%.
Для окончательного выбора вариантов организации структуры и процесса функционирования производственного ядра, а также в целом для экономического обоснования целесообразности его создания или реконструкции, необходим наиболее полный учет затрат и результатов его внедрения, в т.ч. в его системном окружении. В результате исследования на объекте механизма взаимного влияния и взаимосвязей смежных звеньев технологической цепочки в рамках предприятия выявлена и проанализирована система факторов формирования и составляющих экономического эффекта внедрения интегрированной системы программно-целевого управления как синергетического эффекта логистической цени.
При расчетах экономической эффективности гибкой производственной системы изготовления продукции необходимо учитывать как прямой эффект в сфере производства, так и синергетический эффект в сфере производства и потребления продукции.
Синергетический эффект в сфере производства продукции Эобщ возникает как результат снижения издержек производства и складывается из двух составляющих:
Эобщ = Э1(Н)+Э2(S) (1),где
Э1(Н) - эффект сокращения связывания средств в незавершенном производстве рассчитываемой по формуле:
(2), где
-ТtMП - сокращение длительности цикла продукции в t-ом году расчетного периода;
-Ft - годовой фонд рабочего времени в производстве предприятия;
-Cijt - издержки производства 1 т продукции j-ro типа из 1-го
материала в t-ом году;
- Nijt — объем производства продукции j-ro типа из i-го материала в t- ом году, т;
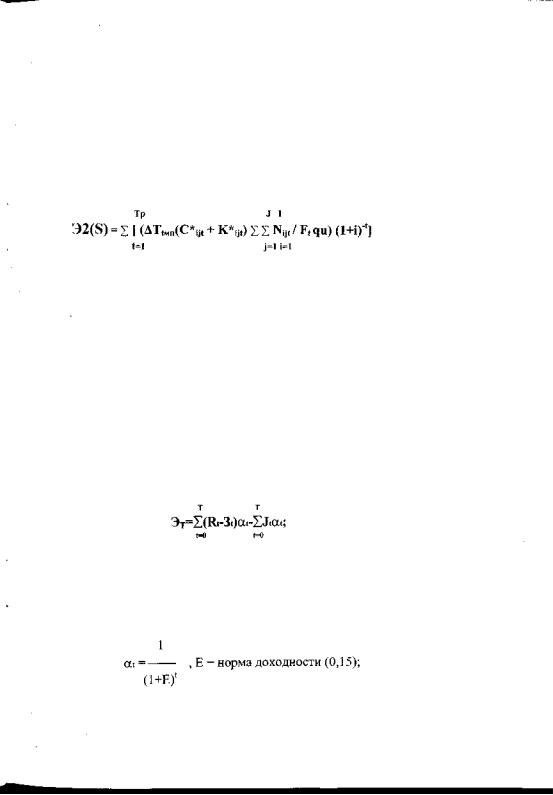
19
-Тр - расчетный период, равный длительности жизненного цикла логистической цепи, лет;
-i - коэффициент дисконтирования.
иЭ2(S) - эффект высвобождения производственных площадей изпод пролеживавшей продукции, рассчитываемый по формуле:
(3), где
-С* ijt K* ijt - соответственно годовые издержки содержания и цена единицы производственной площади, занимаемой под хранение продукции j-ro типа из i-ro материала в t-ом году;
-q - нормативная нагрузка на единицу площади при хранении продукции;
-и - коэффициент использования площади мест складирования продукции.
Результаты расчета синергетического эффекта сокращения циклов контроля качества изделий при внедрении интегрированной системы программно-целевого управления приведены в таблице 1.
При оценке эффективности диссертационных разработок суммарный экономический эффект (Эт) рассчитывался по формуле:
(4) ,где
3t - текущие затраты без учета инвестиций; Rt - полезные экономические результаты; Jt - инвестиции,
t - количество лет или оборотов капитала.
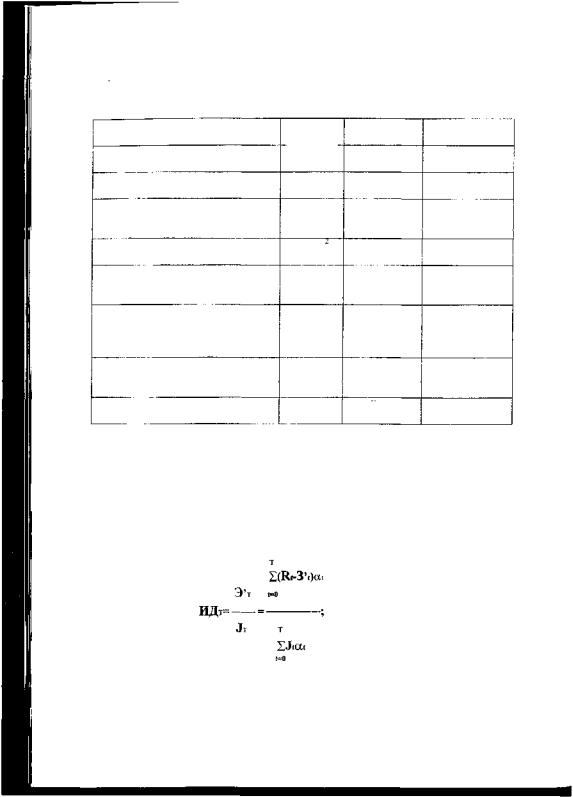
20
Таблица 1
Результаты расчета синергетического эффекта сокращения циклов контроля качества изделий при внедрении интегрированной системы программно-целевого управлении
|
Показатели |
|
|
Единица |
Обозначение |
Значение |
|
|
|
|
|
|
измерения |
|
|
1. |
Сокращение |
годового |
объема |
тыс. т. |
|
2,104 |
|
незавершенного производства |
|
|
|
||||
2. |
Сокращение связывания средств |
тыс. руб. |
|
1955 |
|||
в незавершенном производстве |
|
|
|
||||
3. Эффект, возникающий за счет |
тыс. |
Э1(Н) |
29З,2 |
||||
сокращения связывания |
средств в |
руб./год |
|
|
|||
незавершенном производстве |
|
|
|
||||
4. |
Сокращение |
производственных |
тыс.м2 |
|
2,338 |
||
площадей под складирование |
|
|
|
|
|||
5. Сокращение капитальных вложе- |
тыс. руб. |
|
275,5 |
||||
ний в производственные |
площади |
|
|
|
|||
под складирование |
|
|
|
|
|
||
6. |
Сокращение |
годовых |
издержек |
тыс. |
|
27,8 |
|
хранения (в части содержания про- |
руб./год |
|
|
||||
изводственных площадей иод скла- |
|
|
|
||||
дирование) |
|
|
|
|
|
|
|
7. Эффект высвобождения произ- |
тыс. |
Э2(S) |
84,2 |
||||
водственных площадей под склади- |
руб./год |
|
|
||||
рование |
|
|
|
|
|
|
|
8. Эффект сокращения цикла кон- |
тыс. |
Эобщ |
377,4 |
||||
троля качества смеси (п.З+п.7) |
руб./год |
|
|
||||
|
Приведенный конкретный экономический эффект, с учетом фактора |
||||||
времени, составил 27663,72 тыс. руб. |
|
|
|||||
|
Индекс доходности |
(рентабельности) |
(ИДТ) проекта, |
рассчитанный |
на 3 года, представляющий собой отношение суммы приведенных эффектов к суммарным инвестициям, определяемым с учетом фактора времени, рассчитывался по формуле:
(5),
Результаты расчета синергетического эффекта с использованием предложенной методики показали, что на долю эффекта интеграции системы программно-целевого управления вследствие сокращения длительности цикла продукции (внешний эффект) приходится около 78%