
3147
.pdf20
изготовления изделий (ритм потока) только по заданной производитель-
ности ( Rтр1 ) и по нормам проектирования ( Rтр3 ).
В этом случае определение количества формовочных постов (техно-
логических линий) можно производить по формуле
N фп = |
R |
3 |
|
|
|
|
тр |
, |
(7) |
||
R1 |
|||||
|
|
|
|||
|
|
тр |
|
|
Производительность (Р) технологической линии, м3/год, расположенной в пролете (по варианту 1 или 2) определяется по формуле [25]
|
|
Р = |
60 |
× t × T ×Vиср.вз. |
|
|
|
|
|
(7) |
|
|
|
|
|
||
|
|
|
|
Rпоток |
|
где t |
- |
количество рабочих часов в сутки. При двухсменном режи- |
|||
ме работы в соответствии с [26] t=16 часов; |
|||||
Т |
- |
расчетное |
|
количество рабочих дней в году по |
|
ОНТП 07-85 [26]; |
|
|
|
||
V ср.вз. |
- средневзвешенный объем бетона в одной формовке, м3; |
||||
и |
|
|
|
|
|
Rпоток - ритм потока технологической линии, мин.
5.6. Определение количества постов по изготовлению изделия на конвейерной линии
Число элементных циклов (постов конвейерной линии) принимается в соответствии с числом технологических операций по изготовлению изделия, средней продолжительности каждой технологической операции [40] с учетом времени на перемещение формы с поста на пост. Все расчеты производятся в табличной форме. Пример таблицы для расчета числа элементных циклов приведен на странице 22.
При выполнении курсовой работы допускается определять число
постов конвейерной линии по количеству технологических операций, необ-
21
ходимых для изготовления изделия. Окончательное число постов конвей-
ерной линии (в том числе число постов-дублеров) в обязательном порядке согласуется с руководителем проекта.
5.7. Расчет длины конвейерной линии
Длина конвейерной линии без учета постов снижения изделий в камеру и их подъема из камеры определится следующим образом:
|
Lконв = n × lф−в + l1 × ( n + 1 ), м , |
(9) |
где n - |
число технологических постов (без учета постов снижения и |
|
|
подъема) на конвейерной линии; |
|
lф-в |
- длина формы-вагонетки, м. Принимается из технических |
|
характеристик формы-вагонетки или по справочным данным; |
|
|
l1 |
- величина зазора между формами-вагонетками, м. |
Обычно |
принимается l1 =0,6...1,2 м. |
|
Следует отметить, что предварительная выдержка при изготовлении изделий по конвейерной технологии, как правило, осуществляется на верхнем ярусе конвейерной линии. Таким образом, длина конвейера должна определяться с учетом постов предварительной выдержки.
Полная длина конвейерной линии (включая посты снижения и подъема) составит:
Lпконв = Lкон + 2 × lпод−сн , м |
(10) |
где lпод−сн - длина подъемника-снижателя, м. Принимается по заводским данным, из справочников или из технических характеристик подъемника-снижателя.
Таблица 1 - Расчет количества постов двухветвевой конвейерной линии и назначение технологического оборудования
|
|
Длительность |
|
|
|
|
Требуемое |
Номер |
Наименование |
операции |
Назначение |
Ритм |
Требуемое |
Номера |
обору- |
операции |
операции |
ti = tопер×kв + tпер |
поста |
работы, |
количест- |
постов |
дование |
|
|
мин. |
|
R, мин. |
во постов |
|
|
|
|
|
|
|
|
|
|
1. |
Подъем из камеры |
10 |
Подготовка |
12 |
1 |
1 |
Подъемник |
|
|
|
|
|
|
|
|
.... |
....................................... |
...... |
................. |
......... |
......... |
......... |
.................... |
|
|
|
|
|
|
|
|
8. |
Передача формы с одной ветви |
10,0 |
Подготовка |
12 |
1 |
11 |
Передаточный |
|
на другую |
|
|
|
|
|
мост |
|
|
|
|
|
|
|
|
... |
............................................ |
........ |
................ |
........ |
.......... |
....... |
....................... |
|
|
|
|
|
|
|
|
16. |
Снижение в камеру |
10,0 |
Доводка |
24 |
1 |
17, 17а |
Снижатель |
|
|
|
|
|
|
|
|
23 5.8. Расчет числа и габаритных размеров щелевой камеры
При расчете числа и габаритных размеров щелевой камеры следует помнить, что длина щелевой камеры при ее расположении под конвейерной линией должна равняться длине конвейера, т.е.
|
|
Lщ.к. = Lконв , м . |
|
(11) |
||
Внутренняя ширина камеры определится по формуле |
|
|||||
|
|
Bкамвн |
= bф−в + 2 × l3 , |
м, |
(12) |
|
где |
bф−в - |
ширина формы-вагонетки, м; |
|
|||
|
l3 - |
зазор между формой-вагонеткой и стенкой камеры. При- |
||||
нимается |
l3 =0,2...0,3 м. |
|
|
|
|
|
Внутренняя высота щелевой камеры может быть определена по фор- |
||||||
муле |
|
|
|
|
|
|
|
|
H вн |
= h |
+ h + h , |
м, |
(13) |
|
|
кам |
ф−в |
1 2 |
|
|
где |
hф−в - |
высота формы-вагонетки, м. Принимается из технических |
||||
характеристик, по заводским данным, либо по иным источникам; |
|
|||||
h1 |
- зазор между потолков камеры и верхом формы-вагонетки, м. |
|||||
Обычно принимается h1 =0,15...0,2 м; |
|
|
||||
h2 |
- зазор между полом камеры и низом формы-вагонетки (высота |
рельса, по которому движется вагонетка), м. h2 =0,15 м.
В камере вагонетки располагаются одна за другой, без зазоров (кроме двух - по краям камеры), т.е. одна вагонетка толкает другую.
Таким образом в щелевой камере по длине располагается всегда целое число форм-вагонеток. Число форм-вагонеток, располагающихся в камере,
определяется по формуле |
|
|
|
|
n |
= |
Lконв − 2l2 |
, форм-вагонеток , |
(14) |
|
||||
ф−в |
|
lф−в |
|
|
|
|
|
где l 2 - зазор между первой (или последней) в составе формывагонетки и краем камеры, м. Обычно принимается l2 =0,3...0,7 м.
24
Если число форм-вагонеток, определенное по формуле (14), оказывается не целым, то подбирая зазоры l1 в формуле (9) и l 2 в формуле (14), добиваются целого числа форм-вагонеток в камере.
Число камер, необходимых для обеспечения принятого режима тепловой обработки и заданной производительности, определяется по формуле
|
N кам = |
60 × τто |
, |
(15) |
|
Rпоток × nф−в |
|||
где |
Rпоток - ритм потока технологической линии, мин. |
|
Число камер, определенное по формуле (15), всегда округляется в сторону увеличения до ближайшего целого.
Как уже отмечалось выше, предварительная выдержка, как правило, осуществляется на верхнем ярусе конвейерной линии, поэтому щелевая камера делится обычно на три зоны:
-зона подъема температуры в камере; -зона изотермической выдержки;
-зона снижения температуры (зона охлаждения изделий). Длина зоны подъема температуры определится по формуле
Lпод = |
60 × τпод |
× lф−в + l2 , м . |
(16) |
||
R |
× N |
кам |
|||
|
поток |
|
|
|
Длина зоны изотермической выдержки определится из формулы
Lизот = |
60 × τизот |
× lф−в , м . |
(17) |
||
R |
× N |
кам |
|||
|
поток |
|
|
|
|
Длина зоны охлаждения, м., определится по формуле |
|
||||
Lохл = Lщ.к. − Lпод − Lизот , м. |
(18) |
Следует помнить, что округление числа камер в большую сторону до ближайшего целого фактически означает увеличение длины камеры по сравнению с расчетной и, в свою очередь, удлиннение режима тепловой обработки. Уточнение фактического режима тепловой обработки производится через определение фактической продолжительности всех стадий тепловой обработки.
25
Фактическая продолжительность стадии подъема температуры определится по формуле
τфакт = |
( Lпод − l2 ) × Rпоток × N кам |
, ч. |
|
(19) |
||||||||
|
|
|
|
|
||||||||
под |
|
|
|
|
60 × lф−в |
|
|
|
|
|
|
|
|
|
|
|
|
|
|
|
|
|
|
||
Фактическая |
продолжительность |
стадии |
изотермической выдерж- |
|||||||||
ки определится по формуле |
|
|
|
|
|
|
|
|
||||
τфакт = |
Lизот × Rпоток × N кам |
, |
ч. |
|
(20) |
|||||||
|
|
|
||||||||||
изот |
60 × lф−в |
|
|
|
|
|
|
|
||||
|
|
|
|
|
|
|
|
|
|
|
|
|
Фактическая |
продолжительность |
стадии |
охлаждения определится |
|||||||||
по формуле |
|
|
|
|
|
|
|
|
|
|
|
|
τфакт = |
( Lохл − l2 ) × Rпоток × N кам |
, |
час |
(21) |
||||||||
|
||||||||||||
охл |
60 × lф−в |
|
|
|
|
|
|
|||||
|
|
|
|
|
|
|
|
|
|
|
||
Фактическая продолжительность режима тепловой обработки соста- |
||||||||||||
вит |
|
|
|
|
|
|
|
|
|
|
|
|
|
τф |
= (τфакт + τ |
факт + |
τ |
факт ) |
ч. |
(22) |
|||||
|
|
т.о. |
под |
изот |
|
охл |
|
|
5.9. Определение толщины ограждения (теплоизоляции) щелевой камеры
Определение толщины ограждения (определение толщины теплоизоляции многослойной стенки) производится по методике, изложенной в [35]. Конструктивно ограждение щелевой камеры может быть выполнено однослойным или многослойным с внутренним или внешним слоем утеплителя. Однослойные ограждения в целях снижения затрат тепла на их нагрев следует изготовлять из легкого железобетона, имеющего среднюю плотность 1200...1800 кг/м3. Конструктивные решения многослойных ограждений, позволяющих практически полностью исключить затраты тепла на нагрев железобетонных несущих стен разработаны и приведены в [17]. Одним из вариантов многослойного ограждения могут быть стены с внутренней теплоизоляцией. Внутренняя теплоизоляция выполняется из минераловатных изделий или вспененных пластмасс с защитой их от увлажнения слоем гид-

26
роизоляционного материала (например, металлическим листом толщиной δги=2...3 мм). Свойства материалов для выполнения несущего и теплоизоляционного слоев ограждения приведены в приложениях к настоящим “ Методическим указаниям”.
Для определения толщины однослойного ограждения (толщины слоя теплоизоляции многослойного ограждения) определяют последовательно коэффициенты теплоотдачи конвекцией ( αк ) и лучеиспусканием ( αл ), коэффициент теплопередачи (К) и затем, задаваясь материалом (его коэффициентом теплопроводности λогр ) ограждения (или материалом , из которого
выполняется теплоизоляция λи), определяется толщина ограждения ( δогр).
Расчет можно выполнять либо вручную, либо с применением ЭВМ по программе IZOL.XLS, составленной доц. В.В.Крюковым с использованием электронных таблиц EXEL. Коэффициент теплоотдачи конвекцией αк ,
Вт/(м2*°С), можно рассчитать по следующей формуле
α |
к |
= 1,66 × 3 t |
// |
− t |
ос |
, |
(23) |
|
|
ст |
|
|
|
где tст// - температура наружной поверхности ограждения тепловой установки. Принимается не выше 30...45 ОС из условий техники безопасности, экономических и гигиенических соображений. Для уменьшения теплопотерь в окружающую среду целесообразно принимать меньшие значения температуры;
tос - температура воздуха в цехе. Принимается равной 15...20 ОС.
Коэффициент теплоотдачи лучеиспусканием αл , Вт/(м2*°С), определяется по формуле
|
|
|
|
|
273 + t |
// |
|
4 |
|
|
273 + t |
|
4 |
|
|
|
|
|
|
|
|
|
|
ос |
|
|
|||||||
|
|
|
|
|
|
ст |
|
|
|
|
|
|
|
|||
|
|
|
С × |
|
|
|
|
|
− |
|
|
|
|
|
||
|
|
|
|
|
|
|
|
|||||||||
|
|
|
|
|
100 |
|
|
|
|
|
100 |
|
|
|
||
|
|
|
|
|
|
|
|
|
|
|
|
|||||
|
|
|
|
|
|
|
|
|
|
|
|
|
|
|
||
α |
л |
= |
|
|
|
|
|
|
|
|
|
|
|
|
, |
(24) |
|
|
|
t // |
− t |
|
|
|
|
|
|||||||
|
|
|
|
|
|
|
|
|
|
|
|
|||||
|
|
|
|
|
|
ос |
|
|
|
|
|
|
||||
|
|
|
|
|
|
ст |
|
|
|
|
|
|
|
|
где С - коэффициент излучения наружной поверхности огражде-
ния щелевой камеры, Вт/( м2 × °С4 ). Для наиболее распространенных строительных материалов коэффици-
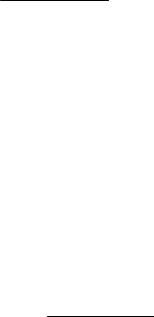
|
|
|
|
|
|
|
|
|
|
|
|
|
|
|
|
|
|
27 |
|
|
|
|
|
|
|
|
|
ент излучения |
приведен |
в |
|
приложениях к настоящим |
|||||||||||||||||||
|
|
“ Методическим указаниям”, а также в [35]. |
|
||||||||||||||||||||||
Коэффициент теплопередачи К, |
Вт/(м2×°С ), можно определить по |
||||||||||||||||||||||||
формуле |
|
|
|
|
|
|
|
|
|
|
|
|
|
|
|
|
|
|
|
|
|
|
|
|
|
|
|
|
|
К = (αк + αл )× (t"ст − t |
ос ), |
|
|
(25) |
|||||||||||||||||
|
|
|
|
|
|
|
|
|
|
|
|
(tс − tос ) |
|
|
|
|
|
|
|
||||||
где |
tс - |
температура среды в щелевой камере в период изотермиче- |
|||||||||||||||||||||||
ской выдержки, °С. |
|
|
|
|
|
|
|
|
|
|
|
|
|
|
|
|
|
|
|
|
|
|
|||
Толщину однослойного ограждения |
δогр, м, можно вычислить из со- |
||||||||||||||||||||||||
отношения: |
|
|
|
|
|
|
|
|
|
|
|
|
|
|
|
|
|
|
|
|
|
|
|
|
|
|
|
|
|
|
δогр |
= |
αк + αл |
|
− К |
|
|
|
|
|
(26) |
||||||||||
|
|
|
|
|
|
|
|
(α |
|
+ α |
|
|
)× К |
, |
|
|
|
||||||||
|
|
|
|
|
λ |
к |
л |
|
|
|
|||||||||||||||
|
|
|
|
|
огр |
|
|
|
|
|
|
|
|
|
|
|
|
|
|
|
|||||
где |
λогр - |
|
коэффициент |
|
|
теплопроводности материала одно- |
|||||||||||||||||||
|
|
|
|
|
|
слойного ограждения, |
Вт /( м× °С ). |
Принима- |
|||||||||||||||||
|
|
|
|
|
|
ется по справочным данным для известного мате- |
|||||||||||||||||||
|
|
|
|
|
риала ограждения. |
Если ограждение камеры проек- |
|||||||||||||||||||
|
|
|
|
|
|
тируется многослойным (например, трехслойным, |
|||||||||||||||||||
|
|
|
|
|
|
состоящего из несущего слоя, слоя теплоизоляции |
|||||||||||||||||||
|
|
|
|
|
|
и защитного гидроизоляционного слоя) формула |
|||||||||||||||||||
|
|
|
|
(25) |
|
принимает вид: |
|
|
|
||||||||||||||||
|
|
|
δн |
+ |
δи |
+ |
δги |
= |
αк + αл |
− К |
(27) |
||||||||||||||
|
|
|
|
|
|
|
|
|
|
(α |
|
|
+ |
|
|
|
)× К |
, |
|||||||
|
|
|
λн |
λ |
|
λ |
ги |
к |
α |
л |
|||||||||||||||
|
|
|
|
|
|
и |
|
|
|
|
|
|
|
|
|
|
|
|
|||||||
|
где |
δн |
|
- толщина несущего слоя ограждения, м. Принимается |
из условия прочности ограждения, а при отсутствии прочностного расчета принимается ориентировочно в пределах 0,15...0,25 м;
δи - |
толщина слоя тепловой изоляции, м; |
δги - |
толщина защитного гидроизоляционного слоя, м. Ес- |
ли в качестве гидроизоляции принимается металлический лист, то его толщина принимается 0,002...0,003 м;
28
λн , λи , λги - коэффициенты теплопроводности, Вт / м× °С , со-
ответственно, защитного слоя, слоя тепло- и гидроизоляции. Определяются по справочным данным для известного материала каждого из слоев.
Температура на границе несущего слоя и слоя теплоизоляции можно определить по формуле
t гран = tc − |
δ |
× λ |
× (t |
c |
− t |
// |
) |
|
|
н |
и |
|
|
ст |
|
. |
(28) |
||
|
δиз × λн |
|
|
||||||
|
|
|
|
|
|
Примеры расчета ограждения камеры приведены в [35].
Следует отметить, что при проектировании камер непрерывного действия, расположенных ниже уровня пола, ограждение целесообразно принимать однослойным из керамзитобетона со средней плотностью 1200...1400 кг/м3. Это обуславливается тем, что тепло на нагрев ограждений тратится только один раз во время пуска камеры в эксплуатацию.
5.10. Описание устройства и работы щелевой камеры
Описание устройства и работы щелевой камеры необходимо проводить одновременно с выполнением графической части. В этом разделе рассматриваются конструктивные решения ограждений камеры, способы подачи теплоносителя и удаления конденсата, а также наличие, назначение и работа рециркуляционной системы. На примере описания продвижения формы вагонетки по вертикально (или горизонтально) замкнутой конвейерной линии рассматриваются механизмы продвижения форм как на верхнем, так и на нижнем (в щелевой камере) ярусе, способы перемещения формвагонеток с одного яруса на другой, а также вопросы ремонта и обслуживания линии. Для удобства ремонта и обслуживания щелевой камеры, предусматриваются ходовые тоннели, с монтажными проемами в стенках. Такие тоннели располагаются параллельно щелевой камере. Приводятся необходимые сведения и мероприятия по контролю за соблюдением заданного режима тепловой обработки. При написании этого раздела необходимые сведения заимствуются из учебной и технической литературы [7, 9, 11...16, 27...31], а также из прослушанного курса лекций по дисциплине “ Теплотехническое оборудование”.
29
5.11.Охрана труда и техника безопасности
Вэтом разделе необходимо указать источники производственного травматизма и предусмотреть мероприятия и устройства, обеспечивающие удобные и безопасные условия труда при обслуживании тепловой установки. Здесь же необходимо рассмотреть санитарные и противопожарные мероприятия. При написании этого раздела необходимо использовать нормативную и техническую литературу [36...38].
5.12.Теплотехнический расчет щелевой камеры
5.12.1. Общие принципы теплотехнического расчета
При выполнении теплотехнического расчета щелевой камеры предполагается, что изделия и формы прогреваются за стадию подъема температуры до максимальной температуры изотермической выдержки. Кроме того, следует помнить, что в камерах сухого прогрева изделия не только проходят тепловлажностную обработку, но и подвергаются сушке, т.к. к ряду изделий (например, панели наружных стен) предъявляются строгие требования по теплопроводности. В связи с этим в суммарных расходах тепла на стадии подъема температуры и изотермической выдержки должны учитываться расходы тепла на испарение воды. Конечную влажность изделий после тепловой обработки принимают по данным соответствующих ГОСТов, а количество испаряемой воды на каждой стадии рассчитывается с учетом конкретного состава бетона и конечной влажности изделия.
В основе теплотехнического расчета тепловых установок лежит закон сохранения энергии, в соответствии с которым сумма статей расхода тепла равняется сумме статей прихода.
Основной задачей теплотехнического расчета является определение удельного расхода тепла и теплоносителя на единицу продукции (на 1 м3 бетона), а также расчет среднечасовых расходов теплоносителя, необходимых для определения диаметра подводящих паропроводов и расчета мощности котельных.