
3149
.pdf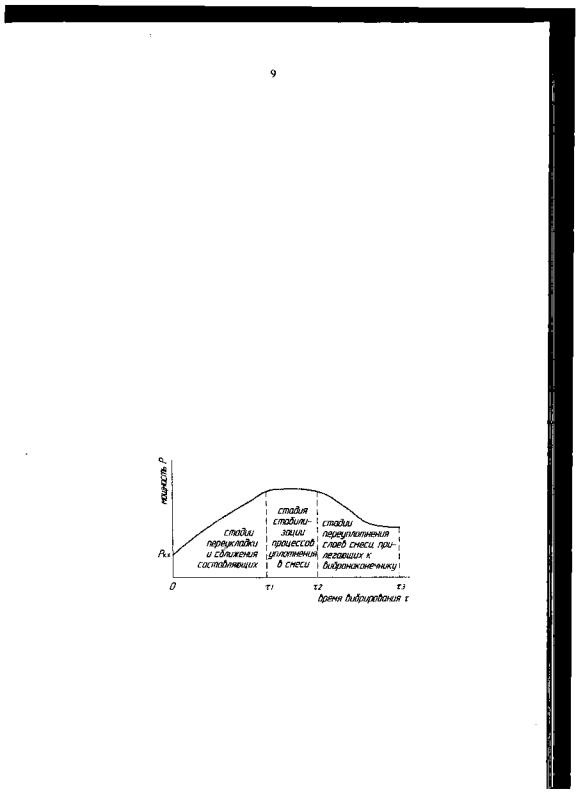
Вторая глава посвящена теоретическим исследованиям методов и средств технологического контроля качества уплотнения бетонной смеси и прочностных параметров монолитного бетона в различном возрасте.
С учетом особенности технологического процесса уплотнения сформулированы требования к методам и средствам контроля степени уплотнения бетонной смеси. На основе изучения изменения реологических свойств бетонной смеси в процессе виброуплотнения сделана теоретическая предпосылка о существовании изменяющейся во времени зависимости между степенью уплотнения смеси и мощностью, потребляемой электродвигателем глубинного вибратора. Сущность метода основывается на зависимости между степенью уплотнения (мгновенной плотностью) бетонной смеси, нагрузкой на вибронаконечник вибратора, моментом, развиваемым электродвигателем, и потребляемой при этом мощностью. Первоначальный рост мощности, потребляемой электродвигателем, характеризует начальные процессы уплотнения бетонной смеси, стабилизация значений говорит об окончании этих процессов, а последующее уменьшение - о начале процесса расслоения (рис. 3).
Рис. 3. График теоретической зависимости мощности, потребляемой электродвигателем глубинного вибратора, от времени уплотнения бетонной смеси:
Рх.х. - мощность холостого хода
Для определения прочностных параметров монолитного бетона был предложен комплексный контроль, состоящий из ультразвукового импульсного метода, метода расчетного определения прочности бетона по температурно-

10
временному фактору, а также метода испытания контрольных образцов-кубов, извлекаемых из тела монолитной конструкции посредством специальных закладных форм.
Основным неразрушающим методом контроля прочности монолитного бетона, выделенным в качестве приоритетного (ГОСТ 18105-86), является ультразвуковой импульсный метод. Главным недостатком традиционного ультразвукового метода контроля является трудоемкость и материалоемкость операций, необходимых для построения корреляционной зависимости «скорость прохождения ультразвукового импульса - прочность бетона», обязательных для каждого конкретного состава бетона, условий его твердения и испытания.
Для устранения данного недостатка автором предложена новая, более универсальная методика. Предпосылкой для ее создания послужило изучение ряда аналогов, используемых за рубежом (Румыния, Польша и другие). Сущность предлагаемой автором методики заключается в назначении исходного (эталонного) бетона, к которому «привязываются» все другие бетоны посредством введения коэффициентов, учитывающих все основные факторы, влияющие на корреляционную зависимость «скорость ультразвука — прочность бетона».. К ним относятся: марка и расход цемента, вид, крупность и расход крупного заполнителя, расход мелкого заполнителя, условия твердения и его продолжительность, температура и влажность бетона в момент измерения, степень армирования железобетонной конструкции, вид и расход добавки. Значение прочности бетона определяется по выражению
где V- скорость ультразвука в бетоне, м/с; Собщ - общий коэффициент влияния.
Для эталонного бетона общий коэффициент влияния Собщ=1,0. Если состав бетона монолитной конструкции и производственные условия отличаются от
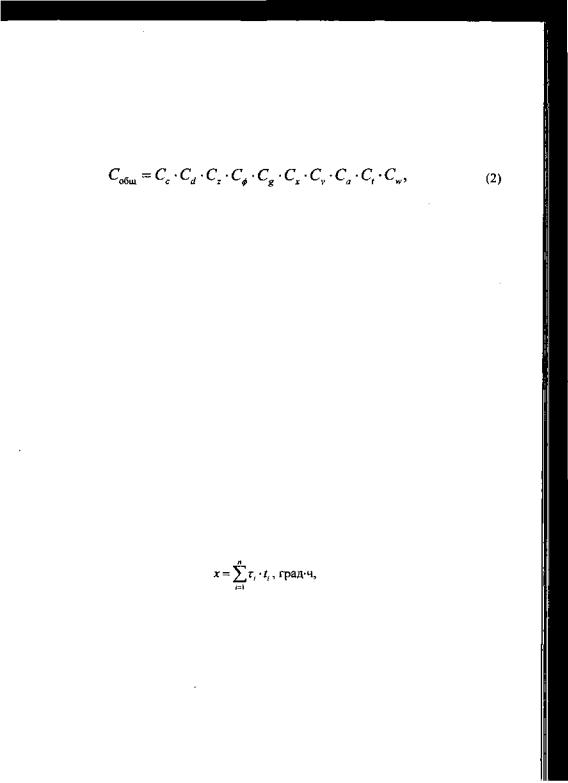
11
стандартного варианта, необходимо вычислять общий коэффициент влияния Собщ отражающий совокупность всех изменяющихся параметров, влияющих на прочность бетона и скорость прохождения ультразвукового импульса:
где С с - коэффициент влияния марки цемента (Сс = 0,62... 1,07);
Сd - коэффициент влияния дозировки цемента (Cd = 0,46... 1,38);
Сz - коэффициент влияния вида крупного заполнителя (для основных видов
заполнителей, |
применяемых |
в |
Нижегородской |
области |
Сz |
= |
= 0,82...6,00); |
|
|
|
|
|
|
С0 - |
коэффициент влияния |
крупности заполнителя |
(С0 |
— |
-0,944... 1,269);
Cg - коэффициент влияния мелкого заполнителя (Cg = 0,96... 1,28);
Cv - коэффициент влияния вида и содержания добавок (для Лигнопан-Б2 Cv
= 0,65...6,06); |
|
|
||
Са |
- |
коэффициент влияния степени армирования конструкции |
(Са |
— |
-0,14...1,00); |
|
|
||
Сt - коэффициент влияния температуры бетона (Сt = 0,951... 1,057); |
|
|
||
Cw - коэффициент влияния влажности бетона (Сw = 0,811... 1,00); |
|
|
||
Сх |
- |
коэффициент влияния фактора созревания бетона |
(Сх |
- |
- 0,588.. .1,031), который определяется по формуле |
|
|
||
|
|
|
|
(3) |
где ti- |
температура бетона в определенном интервале i, °С; |
|
|
|
τi - продолжительность твердения бетона при температуре ti, ч. |
|
|
Значения коэффициентов влияния получены путем обработки и анализа данных других ученых, а также исследованиями автора, включающими ряд простых и многофакторных экспериментов.
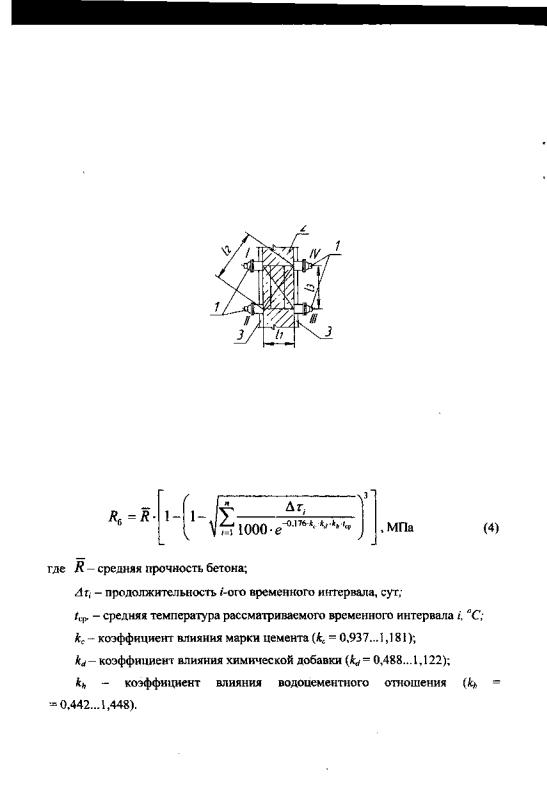
12
При использовании данной методики для контроля прочности бетона в раннем возрасте (распалубочная, критическая) ультразвуковые преобразователи устанавливаются в палубу щита - по два с каждой стороны конструкции (рис. 4). Такое расположение датчиков позволяет выполнять четыре измерения на каждом участке контроля: два сквозных соосных измерения (I-IV и //-/// на базе l1 ), два сквозных диагональных измерения (/-/// и //-/Vна базе l2.
о
Рис. 4. Схема расположения ультразвуковых преобразователей на щитах опалубки: 1 - ультразвуковые преобразователи; 2 - монолитная конструкция; 3 - опалубка
Дублирующим методом контроля прочности бетона монолитных конструкций принято расчетное определение прочности по температурновременному фактору. Значение текущей прочности определяется по аналитическому выражению
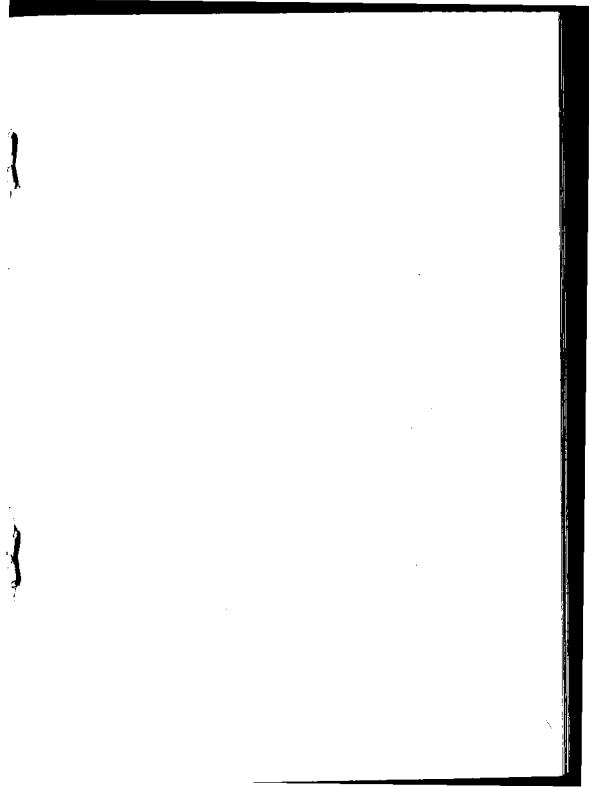
13
Третья глава посвящена экспериментальным исследованиям методов и средств контроля степени уплотнения бетонной смеси при бетонировании монолитных конструкций.
Основной задачей исследования была экспериментальная проверка теоретической предпосылки о наличии устойчивой связи между мощностью, потребляемой электродвигателем глубинного вибратора, и степенью уплотнения бетонной смеси в конструкции. В качестве параметра, характеризующего изменения потребляемой мощности, принята сила тока. Эксперимент проведен на основных видах бетона: тяжелый, с заполнителем из гранита (месторождение "Питкяранта" (Карелия)), легкий, на керамзитовом гравии (г. Чебоксары), мелкозернистый (песчаный). Лабораторные исследования проводились на моделях монолитной стены с варьированием толщины конструкции от 200 до 400 мм.
Уплотнение бетонных смесей осуществлялось послойно глубинным вибратором с гибким валом ИВ-116А и вибратором со встроенным электродвигателем ИВ-102А. Степень уплотнения бетонной смеси регистрировалась визуально (согласно ранее действовавшим СНиП III-15-76), по появлению основных признаков достаточного уплотнения (появление цементного молока на поверхности уплотняемой смеси, прекращение выхода пузырьков воздуха и оседания смеси), предлагаемым методом по стабилизации значения силы тока, потребляемого электродвигателем вибратора. Вибрирование производилось до появления всех визуальных признаков достаточного уплотнения, после чего процесс продолжался еще в среднем 10-15 с для изучения дальнейшего изменения указанного параметра.
Одновременно проводился контроль однородности бетонной смеси посредством изъятия проб из верхней и нижней частей бетонируемой конструкции и разделения их на составляющие. Пробы отбирались в момент появления визуальныхпризнаковуплотненияипоокончаниивибрирования.
В результате экспериментов на всех видах бетона подтверждена теоретическая предпосылка о возможности использования метода контроля степени
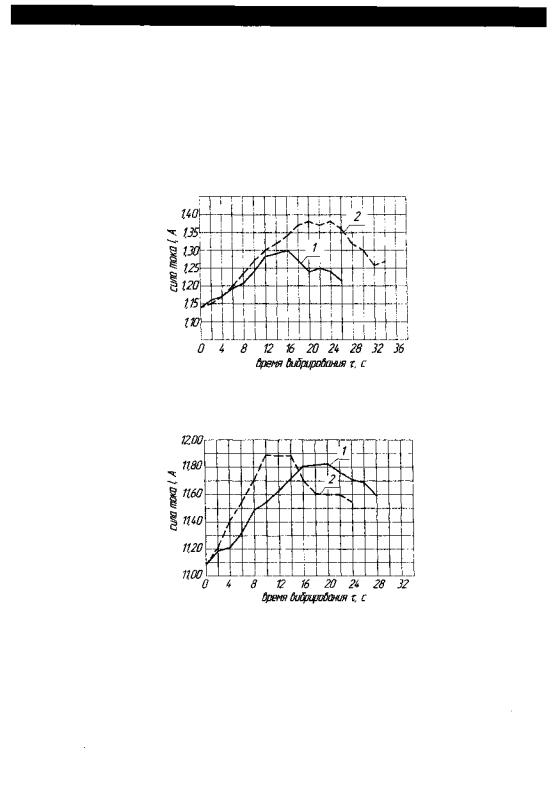
14
уплотнения по стабилизации силы тока, потребляемого электродвигателем глубинного вибратора, вне зависимости от его типа (с гибким валом, со встроенным электродвигателем). Толщина конструкции также не вносит существенных изменений в характер получаемой кривой графика (рис. 4 и 5).
Рис. 4. График зависимости силы тока, потребляемого двигателем глубинного вибратора ИВ116А, от времени уплотнения бетонных смесей в конструкции толщиной 200 мм:
1 - тяжелый бетон состава 1:2,8:6,1; 2 - тяжелый бетон состава 1:1,6:4,2
Рис. 5. График зависимости силы тока, потребляемого электродвигателем вибратора ИВ102А, от времени уплотнения бетонных смесей в конструкции толщиной 400 мм:
1 - легкий бетон состава 1:2,3:6,1; 2 - песчаный бетон состава 1:5,1
Момент стабилизации силы тока соответствует появлению визуальных признаков достаточного уплотнения смеси, отсутствие расслоения при этом подтверждено методом изъятия и исследования проб.
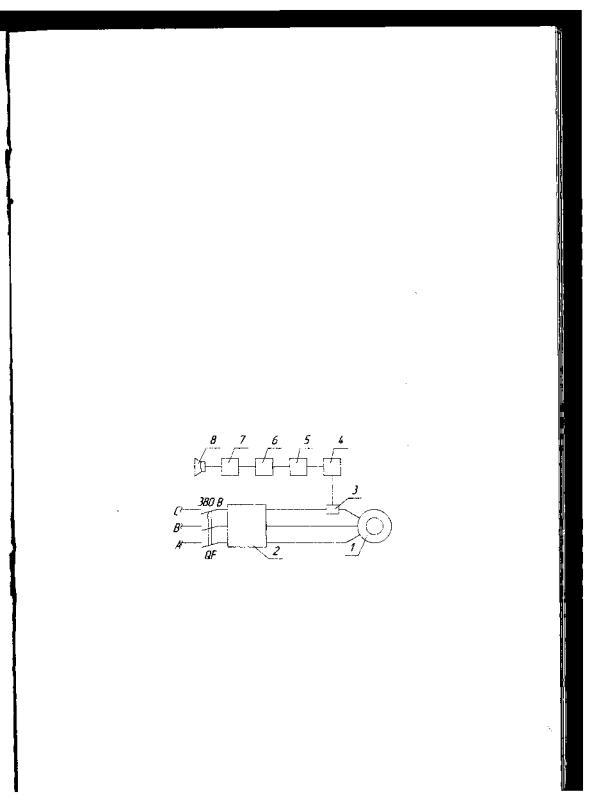
15
Дополнительно контролировалось влияние качества уплотнения (времени вибрирования) на прочностные характеристики бетона на плотных и пористых заполнителях. Контроль осуществлялся путем испытания образцов-кернов, вырезаемых из монолитной конструкции с помощью установки RC-5A, и методом упругого отскока с применением молотка Шмидта типа N. Анализ результатов однозначно подтверждает, что прочность бетона, виброуплотнение которого было завершено в момент стабилизации силы тока, отличается максимальным значением параметра и минимальным коэффициентом вариации.
Разработанный метод контроля степени уплотнения реализован в виде автоматизированной установки, схема которой представлена на рис. 6. Основным звеном ее является микропроцессор MU300-71548DA3, который обеспечивает работу установки, согласно разработанному автором алгоритму (рис. 7). Звуковой сигнал о прекращении процесса уплотнения бетонной смеси в данной точке вибрирования наиболее рационально выводить на динамики наушников, используемых рабочим, производящим уплотнение.
Рис. 6. Схема установки для автоматизированного контроля степени уплотнения: 1 - электродвигатель глубинного вибратора; 2 - преобразователь частоты тока;
3 - датчик тока SR-215Z437; 4 - аналогово-цифровой преобразователь; 5 - микропроцессор
MU3GO-71548DA3; 6 - ключ; 7 - усилитель; 8 - звуковой сигнал
Применение автоматизированного варианта метода контроля степени уплотнения позволяет обеспечить требуемое быстродействие и повысить точность определения момента прекращения уплотнения за счет исключения субъективного влияния «человеческого фактора».
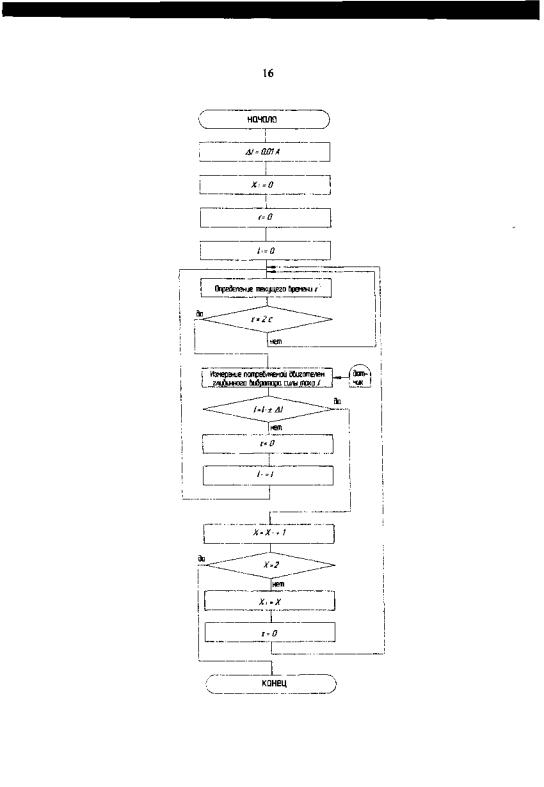
Рис. 7. Алгоритм автоматизированного контроля степени уплотнения бетона
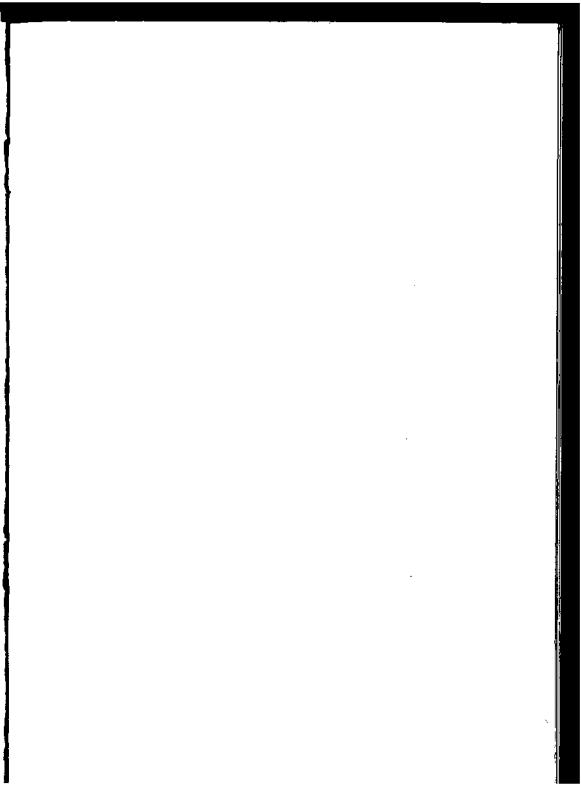
17
Эффективность использования данного метода в автоматизированном варианте подтверждена полупроизводственными испытаниями на объектах монолитного домостроения г. Н.Новгорода.
Четвертая глава посвящена экспериментальным исследованиям методов и средств контроля прочности монолитного бетона в раннем и зрелом возрасте. Основной задачей исследований являлась оценка объективности предлагаемой комплексной системы контроля прочности монолитного бетона. Исследования проводились на экспериментальной модели монолитной стены толщиной 200 и 400 мм. При этом исследования охватывали все основные виды бетона (тяжелый, легкий на пористом заполнителе, мелкозернистый) и область классов прочности, наиболее характерных для современного строительства г. Н.Новгорода (В5 ... В20). В качестве условий твердения применялись обогрев в термоактивной опалубке и естественное твердение. Варьировалось также армирование конструкций.
Контроль прочности производился комплексом методов, включающим ультразвуковой импульсный метод, метод расчетного определения прочности бетона по температурно-временному фактору и метод испытания контрольных об- разцов-кубов, изымаемых из тела монолитной конструкции. Дополнительно применены метод испытания образцов-кубов, твердеющих около бетонируемой конструкции (при твердении бетона в естественных условиях), и механический неразрушающий метод упругого отскока (молоток Шмидта типа N).
Для реализации первых двух методов созданы измерительные блоки, включающие в себя аппаратуру для контроля влажности и температуры бетона (ВИСМ-1.0УЗ и ТЕМП-3.01 с комплектами датчиков), ультразвуковой прибор УК-14П с комплектом преобразователей. Схема измерительных блоков представлена на рис. 8.
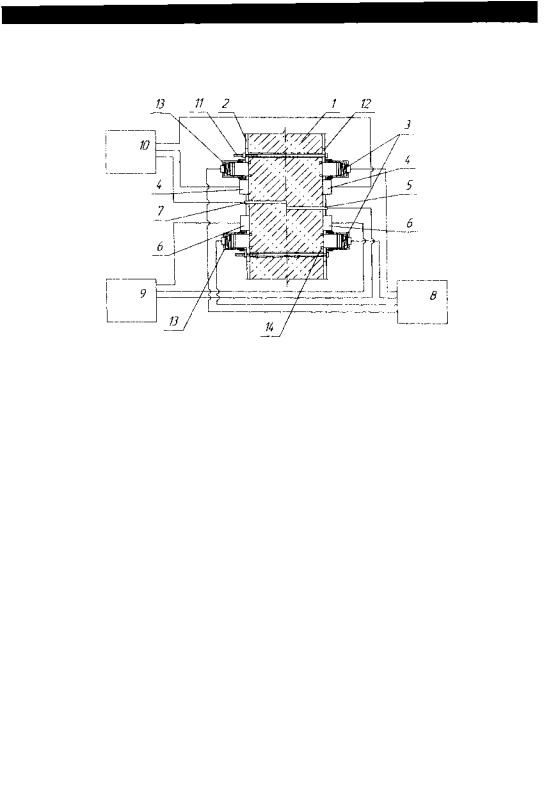
18
Рис. 8. Принципиальная схема измерительного блока:
1 - монолитная конструкция; 2 - палуба щита; 3 - ультразвуковые преобразователи; 4 - поверхностный датчик температуры; 5 - глубинный датчик температуры;
6 поверхностный датчик влажности; 7 - глубинный датчик влажности; 8 - УК-14П;
9- ВИСМ-1.0УЗ; 10 - ТЕМП-3.01; 11 - градуированный крепежно-измерительный стержень;
12 - основание измерительного блока; 13 - устройство для прижима преобразователей к поверхности бетона после уплотнения смеси; 14 — фиксатор перемещения преобразователей
Для контроля прочностных параметров монолитного бетона методом испытания образцов—кубов, изымаемых из тела монолитной конструкции, автором разработаны конструкция специальной закладной формы (рис. 9) и технология извлечения с ее помощью бетонного образца-куба. Разработанная форма устанавливается в конструкцию до ее бетонирования и извлекается вместе с образцом в любой момент времени после снятия опалубки. Конструкция формы позволяет получать контрольный образец-куб, имеющий идентичные характеристики с бетоном монолитной конструкции, не требующий дополнительных затрат на подготовку к испытанию.
Анализ результатов экспериментальных исследований показал надежность и объективность контроля прочности бетона предлагаемой комплексной системой контроля. Расхождение результатов контроля прочности предлагаемыми