
6684
.pdf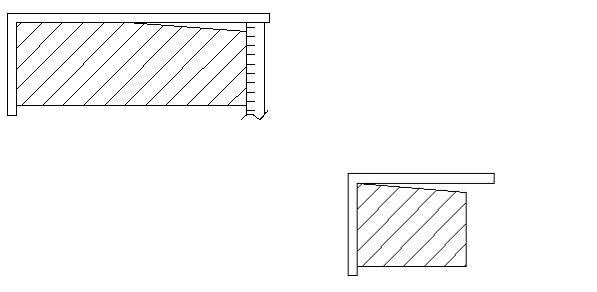
60
Рис. 18. Методика измерений силикатного кирпича
кирпичи вынимают из сосуда, обтирают мокрой тряпкой и взвешивают с точностью до 1%. Затем взвешенные, насыщенные водой образцы помещают в сушильный шкаф с температурой плюс 105-1100С и высушивают их до постоянной массы. Водопоглощение каждого кирпича в процентах (по массе) вычисляют по формуле (7). Водопоглощение кирпича определяют как среднее арифметическое результатов испытаний трех образцов.
Определение морозостойкости кирпича. Для испытания на морозостойкость отбирают десять кирпичей, пять из которых подвергают замораживанию и оттаиванию, остальные образцы являются контрольными и испытывают на сжатие для сравнения с прочностью кирпичей, испытанных на морозостойкость.
При определении морозостойкости кирпича его предварительно насыщают водой в течение 48 часов, а затем попеременно замораживают при температуре не выше минус 150С и не ниже минус 200С, после чего оттаивают погружением в воду с температурой плюс (20±5)° С. Продолжительность одного замораживания должна быть не менее 4-х часов. При оценке морозостойкости по степени повреждений после требуемого числа циклов замораживанияоттаивания производят визуальный осмотр образцов и фиксируют появившиеся дефекты.
Кирпич считается выдержавшим испытание на морозостойкость, если после испытания образцы не разрушатся или на их поверхности не будет обнаружено каких-либо признаков разрушения (расслоение, шелушение, растрескивание), а предел прочности при сжатии при этом понижается в пределах указанных ГОСТом.
Определение предела прочности кирпича при сжатий
Для установления предела прочности при сжатии приготовляют образцы
61
близкие по форме к кубу. Для испытания на сжатие отбирают 5 кирпичей, распиливают их поперек на две половинки и накладывают (постелями) одна на другую поверхностями разреза в противоположные стороны. Нижнюю и верхнюю плоскости обеих половинок устанавливают строго параллельно. Подготовленные таким образом кирпичи испытывают на сжатие на гидравлическом прессе по схеме, приведённой на рис. 1б. За величину площади поперечного сечения при испытании принимают площадь шва, соединяющего половинки кирпича.
Предел прочности при сжатии отдельного кирпича определяют по формуле (9), а предел прочности при сжатии партии вычисляют с точностью до 0,1 МПа как среднее арифметическое значение результатов испытаний пяти образцов. При вычислении среднего предела прочности не учитывают образцы, предел прочности которых превышает более чем на 40 % среднее значение предела прочности для 5 образцов.
При вычислении предела прочности при сжатии образцов из двух целых кирпичей толщиной 88 мм или из двух их половинок результаты испытаний умножают на коэффициент 1,2.
Определение предела прочности при изгибе. Для определения предела прочности пря изгибе кирпич укладывают плашмя по схеме, приведённой на рис. 1а. Расстояние между осями опор равно 20см. Опоры представляют собой металлические цилиндрические катки диаметром 20-30 мм.
Предел прочности при изгибе отдельного образца определяется по формуле (10). Предел прочности при изгибе партии кирпичей вычисляют с точностью до 0,05МПа как среднее арифметическое значение результатов испытаний пяти образцов. При вычислении предела прочности при изгибе образцов в партии не учитывают образцы, пределы прочности которых имеют отклонение от среднего значения предела прочности всех образцов более чем на 50 %.
Технические требования к силикатному кирпичу. Силикатный кирпич должен иметь форму прямоугольного параллелепипеда с равными и гладкими гранями однотонного цвета, с острыми ребрами и прямыми углами. Требования по показателям внешнего вида для рядового утолщённого кирпича представлены в табл.3.
Водопоглощение силикатного кирпича должно быть не менее 6 %. Масса утолщённого кирпича в высушенном состоянии должна быть не
более 4,3кг.
В образцах силикатного кирпича, испытанных на морозостойкость, допускается снижение средней прочности при сжатии без каких-либо признаков разрушения (расслоения, шелушения, растрескивания, выкрашивания и т.п.) не более чем:
62
-на 20 % - для лицевого кирпича, -на 25 % - для рядового кирпича.
Силикатный кирпич в зависимости от предела прочности при сжатии и изгибе подразделяется на марки, указанные в табл. 4.
|
|
|
|
Т а б л и ц а 4 |
|
|
Марки силикатного кирпича |
|
|
|
|
|
|
|
|
|
Предел прочности, МПа |
|
|
|
|
|
|
|
Марка |
при сжатии |
при изгибе |
||
кирпича |
средний для |
наименьший |
средний для |
наименьший |
|
для отдель- |
для отдель- |
||
|
пяти образцов |
пяти образцов |
||
|
ного образца |
ного образца |
||
1 |
2 |
3 |
4 |
5 |
300 |
30,0 |
25,0 |
4,0 |
2,7 |
250 |
25,0 |
20,0 |
3,5 |
2,3 |
200 |
20,0 |
15,0 |
3,2 |
2,1 |
175 |
17,5 |
13,5 |
3,0 |
2,0 |
150 |
15,0 |
12,5 |
2,7 |
1,8 |
125 |
12,5 |
10,0 |
2,4 |
1,6 |
100 |
10,0 |
7,5 |
2,0 |
1,3 |
75 |
7,5 |
5,0 |
1,6 |
1,1 |
3. МЕТОДИКА СТАНДАРТНЫХ ИСПЫТАНИЙ ТЯЖЕЛОГО БЕТОНА
Основной задачей при проектировании состава бетона является подбор такого расхода материалов на 1 м3 бетонной смеси, при котором наиболее экономично обеспечивается получение заданной подвижности или жесткости смеси, расчетной прочности и долговечности, а в ряде случаев – необходимой морозостойкости, водонепроницаемости и других специальных свойств бетона.
Наиболее распространённым является расчетно-экспериментальный метод подбора состава бетона, который включает в себя следующие основные этапы: теоретический расчёт состава бетона, опытный замес, определение подвижности (жёсткости) и прочности бетона, корректировка состава бетона (при необходимости), производственный расчёт состава бетона (с учётом влажности заполнителей).
Исходными данными для расчета состава бетона являются: класс (марка) бетона; характеристика бетонной смеси по степени подвижности или жесткости; характеристики исходных материалов (активность цемента, его плотность, плотности песка, щебня или гравия, наибольшая крупность щебня (гравия) и его пустотность).
Расчет состава тяжелого бетона производят в следующем порядке.
63
Определяют требуемую подвижность (жёсткость) бетонной смеси в зависимости от вида конструкции и способа уплотнения в соответствии с табл. 5.
Определяют водоцементное отношение (В/Ц), обеспечивающее получение бетона заданной прочности и долговечности по формуле
Rб = А × Rц ( |
Ц |
- 0,5) , |
(13) |
|
В |
||||
|
|
|
где Rб - требуемая прочность бетона;
А - коэффициент качества заполнителей (для рядовых заполнителей
А=0,6);
Rц - активность цемента, МПа.
Т а б л и ц а 5
Диапазон удобоукладываемости бетонной смеси при формовании на виброустановке с частотой 50Гц
Наименование изделий |
|
ОК, см |
Ж, с |
|
|
|
|
Плиты перекрытий внутренних стен |
|
1-4 |
-- |
|
|
|
|
Аэродромные, дорожные плиты |
|
-- |
5-10 |
|
|
|
|
Панели наружных стен однослойные |
|
-- |
5-10 |
|
|
|
|
Плиты ребристые |
|
1-4 |
-- |
|
|
|
|
Плиты пустотелые |
|
-- |
11-20 |
|
|
|
|
Конструкции со значительным насыщением |
5-9 |
-- |
|
арматурой |
|
||
|
|
|
|
|
|
|
|
Блоки фундаментные и другие |
подобные |
-- |
5-10 |
изделия простой конструкции |
|
||
|
|
|
|
|
|
|
|
Затем определяются расходы материалов на 1м3 бетона: |
|
||
- воды - по табл. 6. |
|
|
|
64
Таблица 6
Расход воды для приготовления бетонной смеси
|
|
Расход воды при крупности заполнителя, мм |
|||||||
Удобоукладываемость |
|
|
|
|
|
|
|
|
|
|
гравия |
|
|
щебня |
|
||||
|
|
|
|
|
|
||||
|
|
|
|
|
|
|
|
|
|
подвижность |
жесткость |
|
|
|
|
|
|
|
|
ОК, см |
Ж, с |
10 |
20 |
40 |
70 |
10 |
20 |
40 |
70 |
|
31 и более |
150 |
135 |
125 |
120 |
160 |
150 |
135 |
130 |
|
|
|
|
|
|
|
|
|
|
|
21—30 |
160 |
145 |
130 |
125 |
170 |
160 |
145 |
140 |
|
11—20 |
165 |
150 |
135 |
130 |
175 |
165 |
150 |
145 |
|
5—10 |
175 |
160 |
145 |
140 |
185 |
175 |
160 |
155 |
4 и менее |
|
190 |
175 |
160 |
155 |
200 |
190 |
175 |
170 |
5—9 |
|
205 |
190 |
175 |
170 |
215 |
205 |
.190 |
185 |
10—15 |
|
220 |
210 |
197 |
185 |
230 |
220 |
207 |
195 |
16 и более |
|
227 |
218 |
203 |
192 |
237 |
228 |
213 |
202 |
|
|
|
|
|
|
|
|
|
|
-цемента, исходя из значения В/Ц и расхода воды;
-крупного заполнителя - по формуле
Щ = |
|
1000 |
|
|
|
|
|
; |
|
|
(14) |
|||
|
|
|
|
|
|
|
|
|
|
|
||||
|
V щ |
× |
|
α |
+ |
1 |
|
|
|
|
||||
|
|
|
|
|
|
|
|
|
|
|||||
|
пуст |
|
ρн.щ. |
|
|
|
ρщ |
|
|
|
||||
- песка - по формуле |
|
|
|
|
|
|
|
|
|
|
|
|
|
|
П = [1000 - ( |
Ц |
+ |
|
В |
+ |
Щ |
)] × ρп , |
(15) |
||||||
|
|
|
|
|||||||||||
|
|
|
|
ρц |
|
ρв |
ρЩ |
|
где Ц, В, П, Щ - содержание, соответственно цемента, воды, песка, и щебня;
ρц, ρв, ρп, - соответственно, средние плотности этих материалов, кг/л; ρщ - насыпная плотность щебня;
Vпустщ - пустотность крупного заполнителя, определяемая по формуле
Vпустщ = (1 - |
ρщ |
) ; |
(16) |
|
|||
|
ρщ |
|
α - коэффициент раздвижки зёрен, принимаемый по табл. 7.
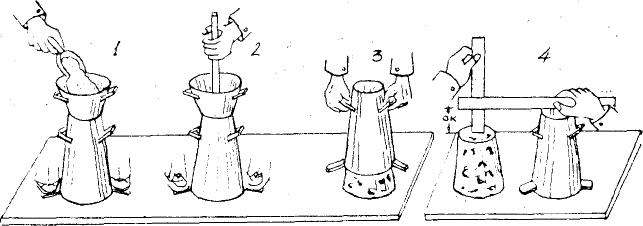
65
Т а б л и ц а 7
Значения коэффициента раздвижки зерен
Расход цемента, кг/м3 |
Коэффициент раздвижки зерен при В/Ц |
|
|||||
0,30 |
0,40 |
0,50 |
0,60 |
0,70 |
|
0,80 |
|
|
|
||||||
250 |
|
|
|
1,26 |
1,32 |
|
1,38 |
300 |
|
|
1,30 |
1,36 |
1,42 |
|
|
350 |
|
1,32 |
1,38 |
1,44 |
|
|
|
400 |
1,31 |
1,40 |
1,46 |
|
|
|
|
500 |
1,44 |
1,52 |
1,56 |
|
|
|
|
600 |
1,52 |
1,56 |
|
|
|
|
|
|
|
|
|
|
|
|
|
После определения расхода материалов на 1м3 бетонной смеси производят пересчёт состав на лабораторный замес (8 литров). У приготовленной бетонной смеси определяют фактическую подвижность (жёсткость) бетонной смеси.
Подвижность бетонной смеси (осадка конуса) бетонной смеси определяется в следующей последовательности (рис. 19).
Рис. 19. Определение подвижности бетонной смеси
Стандартный металлический конус устанавливают на гладком металлическом листе и плотно прижимают его к основанию. Наполнение формы производят через воронку тремя слоями одинаковой высоты, и каждый слой уплотняют 25 раз штыкованием. Затем воронку снимают, и избыток бетонной смеси срезают вровень с краями конуса, после чего конус поднимают строго вертикально вверх в течение 5-7с и устанавливают рядом с отформованной бетонной смесью. Бетонная смесь, освобожденная от конуса, под собственным весом дает осадку, которую замеряют металлическими линейками с точностью до 0,5 см.
В случае, если фактическая осадка конуса не соответствует проектной, производят корректирование состава бетонной смеси.
66
Прочность бетона контролируют путем испытания стандартных бетонных образцов-кубов размером 15x15x15 см в возрасте 28сут. Изготовленные образцы хранят при относительной влажности воздуха 95±5% и температуре 20±3° С. Методика определения предела прочности при сжатии представлена в главе 1 первого раздела настоящего пособия.
После того, как достигается соответствие фактических показателей проектным, производят производственный расчёт состава бетона (с учётом влажности заполнителей).
4. МЕТОДИКА СТАНДАРТНЫХ ИСПЫТАНИЙ КРУПНОГО ЗАПОЛНИТЕЛЯ ДЛЯ ТЯЖЕЛЫХ БЕТОНОВ
Важнейшими показателями качества крупного заполнителя для тяжёлых бетонов являются: зерновой состав; марка по дробимости при сжатии в цилиндре; средняя плотность и пустотность.
Определение зернового состава щебня (гравия) производится путём рассева пробы на стандартном наборе сит. Лабораторную пробу массой 10кг высушивают до постоянной массы и просеивают по частям через стандартный набор сит: 1,25; 2,5; 3; 5; 7,5; 10; 12,5; 15; 20; 25; 30; 40; 50; 60; 70; 80.
По результатам просеивания вычисляют частный остаток на каждом сите (аi) , затем определяют полные остатки на каждом сите (Аi), % по формулам:
а = |
mi |
×100 ,%, |
(17) |
|
|||
i |
m |
|
|
|
|
||
Ai = a80 + a70 + ... + ai , |
(18) |
где mi - масса остатка на данном сите; m - масса навески;
a80… аi - частные остатки на соответствующих ситах.
Определение марки по дробимости щебня (гравия) проводится с помощью специального стального цилиндра со съемным дном и плунжера. Щебень (гравий) рассеивается на стандартные фракции (5-10, 10-20,20-40мм), и испытывается отдельно каждая фракция.
Пробу щебня (гравия) насыпают в цилиндр с высоты так, чтобы после разравнивания верхний уровень материала примерно на 15мм не доходил до верхнего края цилиндра. В цилиндр вставляют плунжер. После в этого цилиндр помещают на плиту пресса. Повышая нагрузку, доводят ее до 200кН (20 тс).
После испытания пробу высыпают из цилиндра и взвешивают. Затем ее просеивают через сито с отверстиями размером в четыре раза меньше минимального размера фракции, взятой для испытания (например, 1,25 - для фйракции 5 - 10). Остаток на сите взвешивают.
Коэффициент дробимости – ( Др) вычисляют по формуле

67 |
|
|
|
Др = |
m - m1 |
, |
(19) |
|
|||
|
m |
|
где m - масса пробы щебня (гравия);
m1 - масса остатка на сите после просеивания раздробленной пробы щебня (гравия).
По показателю дробимости определяется марка щебня (гравия) по дробимости.
Определение средней плотности щебня (гравия). Из подготовленной высушенной пробы щебня (гравия) берут навеску 1000г и погружают ее в воду на 2ч. Затем вынимают из воды, удаляют влагу с поверхности зерен мягкой влажной тканью и сразу взвешивают сначала на настольных обычных, а затем на гидростатических весах (рис. 20).
Среднюю плотность щебня (гравия) вычисляют по формуле:
ρm |
= |
m × ρв |
, |
(20) |
|
||||
|
|
m1 - m2 |
|
где m - масса пробы в сухом состоянии, г; ρв - плотность воды, равная 1г/см3;
m1 - масса пробы в насыщенном водой состоянии на воздухе; m2 - масса пробы в насыщенном водой состоянии в воде.
Крупные заполнители для тяжелых бетонов должны иметь среднюю плотность зерен от 2000 до 2800кг/м3.
Определение насыпной плотности и пустотности щебня (гравия)
Высушенный щебень (гравий) насыпают в предварительно взвешенный мерный цилиндр объёмом 10л с высоты 10см до образования конуса, который снимают стальной линейкой вровень с краями без уплотнения, после чего цилиндр со щебнем (гравием) взвешивают.
Насыпную плотность щебня (гравия) ρн вычисляют по формуле:
ρн = |
m1 - m |
, |
(21) |
|
|||
|
V |
|
где m - масса мерного цилиндра;
m - масса мерного цилиндра со щебнем; V - объем мерного цилиндра.
Пустотность щебня (гравия) Vпуст определяют расчетным путем на основании предварительно установленных значений:
ρ
Vпуст = (1 - ρн ) (22)
щ
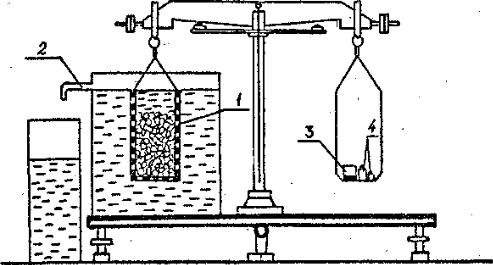
68
Рис.20. Весы для гидростатического взвешивания: 1 - сетчатый (перфорированный) стакан; 2 - сосуд со сливом для воды; 3 - стакан с дробью для уравновешивания массы
сетчатого стакана в воде; 4 - разновесы
69
Контрольные вопросы
1.Что такое строительные материалы? Их роль и значение в современном строительстве.
2.Перечислите основные физические и механические свойства строительных материалов.
3.Какие схемы испытаний используются для определения прочности материалов при сжатии и изгибе?
4.Укажите основные породообразующие минералы.
5.Назовите три группы горных пород по условиям их образования (по генетическому признаку).
6.Как добывают и обрабатывают природный камень?
7.Какие виды природных каменных материалов применяются в строительстве?
8.Назовите основные свойства глин, как сырья для производства керамических изделий.
9.Опишите общую технологию производства керамических изделий
10.Опишите методы производства керамических изделий. В чём их достоинства и недостатки?
11.Что является сырьем для производства стекла? Опишите технологию производства стекла и перечислите изделия из него.
12.Что такое ситаллы, шлакоситаллы и ситаллопласты? Опишите технологию их производства и область применения в строительстве.
13.Какими показателями характеризуются свойства металла и как они определяются?
14.Что такое сталь и чугун? Основные их виды. Область применения в строительстве.
15.Какие из цветных металлов имеют наибольшее применение в строительстве, каковы их свойства?
16.Назовите основные виды стальных конструкций и их первичных элементов.
17.Что такое стальная арматура? Её виды, свойства и область применения. 18.Сравните по химическому составу, структуре и технологии производства гипсовые вяжущие β-модификации и α-модификации; определите свойства и назовите применение разновидностей гипсовых вяжущих. 19.Технология производства извести, её разновидности и область
применения в строительстве