
8677
.pdf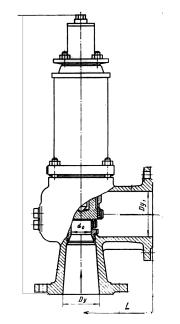
41
мых на паропроводах, должна быть больше или равняться пропускной способности паропровода.
Пропускную способность предохранительного клапана определяют по формуле:
G = 10 × B × α × F × (P1 + 0,1), кг/ч,
где F – расчетная площадь сечения клапана, равная наименьшей площади свободного сечения в проточной части, мм2;
α– коэффициент расхода пара, отнесенный к площади сечения клапана
иопределяемый в размере 90% от значения, полученного заводомизготовителем при испытании и указываемого в паспорте на клапан;
P1 – максимальное избыточное давление перед предохранительным клапаном, принимаемое равным 1,1 Рраб, МПа; В – коэффициент, тот же, что при расчете регулирующего клапана.
При известных пропускной способности установки, за которой устанав-
ливается клапан и давлении пара в защищаемом трубопроводе, расчет сводится к определению площади сечения проточной части клапана, по которой затем выбирается клапан соответствующего диаметра, имеющий площадь сечения проточной части не менее требуемой.
Пример – Подбор предохранительного клапана.
Требуется подобрать предохранительный клапан для установки на трубопроводе насыщенного пара пропускной способностью 400 кг/ч и рабочем давлении Р=0,3 МПа (избыточное)
Решение
Определяем требуемую площадь свободного сечения проточной части клапана
F = |
|
G |
|
, мм2 |
|
× B × α × (P1 + 0,1) |
|||
10 |
|
|||
Предварительно выбираем клапан предо- |
||||
хранительный полноподъемный |
пружинный |
Рис. 8. Предохранительный клапан

42
фланцевый 17с13нж, Ру = 1,6 МПа.
Для этого клапана α =1, следовательно, в формулу надо подставлять:
α = 0,9 × 1 = 0,9
Коэффициент В для пара насыщенного давлением Р1 = 0,3 МПа, равняется 0,5225 (по таблице из раздела «Подбор регулирующих клапанов).
F = |
|
400 |
|
= 213 мм |
|
× 0 ,5225 × 0 ,9 × ( 0 ,3 |
|
||
10 |
+ 0 ,1 ) |
По найденному значению площади свободного сечения проточной части выбираем типоразмер клапана Ду 50 мм, имеющий сечение проточной части
706мм2.
|
|
|
|
|
|
|
|
Таблица 5 |
|
|
Основные габаритные размеры и масса клапана 17с13нж |
|
|
||||||
|
|
|
|
|
|
|
|
|
|
Условный про- |
|
|
|
|
Cечение |
|
Масса, кг |
|
|
ход, мм |
|
|
|
|
проточной |
|
|
|
|
Dу |
Dу |
L, мм |
L1, мм |
Н, мм |
dс, мм |
части F, |
|
17с13нж |
|
|
|
|
|
мм2 |
|
17нж32ст |
|
||
50 |
80 |
130 |
155 |
550 |
30 |
706 |
|
27 |
|
|
|
|
|
|
|
|
|
|
|
80 |
100 |
150 |
175 |
635 |
40 |
1256 |
|
39 |
|
|
|
|
|
|
|
|
|
|
|
100 |
125 |
165 |
205 |
770 |
50 |
1962 |
|
55 |
|
|
|
|
|
|
|
|
|
|
|
150 |
200 |
205 |
250 |
955 |
72 |
4069 |
|
120 |
|
|
|
|
|
|
|
|
|
|
|
200 |
250 |
280 |
320 |
1200 |
142 |
15828 |
|
230 |
|
|
|
|
|
|
|
|
|
|
|
7.3. Расчет емкости конденсатных баков
Подобрать конденсатные баки для расхода конденсата G = 10,26 т/ч.
Решение
Суммарная емкость баков при 10-минутном запасе составит:
10,26 × 10 = 1,71 т (м3) 60
Принимаем конденсатные баки по ОСТ 34-42-561-82. Номинальный типоразмер бака – 2 м3 (11).
43
Поскольку часовой расход конденсата более 5 т/ч к установке следует принять два бака. Таким образом, суммарная емкость баков составит 4 м3, что соответствует примерно 23-минутному расходу конденсата, что не противоречит требованиям (6).
7.4. Подбор насосов для перекачки конденсата
Конденсатные насосы предназначаются для откачки конденсата из сборных баков по конденсатопроводам. Производительность их выбирается по максимальному часовому расходу конденсата. Напор конденсатных насосов определяется по формуле:
Н = Нк ± Z, м,
где Нк – потеря напора в конденсатопроводе на участке от сборного бака потребителя до сборного конденсатного бака источника теплоты;
Z – разность геодезических отметок баков источника теплоты и потребителя (при установке бака источника теплоты ниже бака потребителя Z имеет отрицательный знак).
Подбор насосов осуществляется по производительности и напору на основании заводских данных, приведенных в справочной литературе.
7.5. Подбор конденсатоотводчиков
Конденсатоотводчики применяются для автоматического бесшумного удаления конденсата с одновременным запиранием пара. Значение конденсатоотводчиков очень велико. Потери пара только за счет неудачной конструкции конденсатоотводчиков и неправильно поставленной эксплуатации могут достигать в среднем до 25% количества потребляемого пара.
Правильная расстановка, выбор типа и производительности конденсатоотводчиков по трассе паропроводов, тщательный монтаж и систематический контроль за их работой обеспечивают надежную и экономичную эксплуатацию
44
паропроводов. Если хотя бы одно из этих условий не выполнено, то возможны гидравлические удары, повышение гидравлического сопротивления из-за водяных мешков по трассе, нарушения соединений, парения и утечки.
8. Использование в тепловом балансе промышленных предприятий вторичных тепловых ресурсов.
8.1. Общие сведения.
Различные производственные процессы в ряде случаев сопровождаются тепловыми отходами в виде теплоты, пара, горячей воды или нагретыми технологическими продуктами, называемыми вторичными энергетическими (тепловыми) ресурсами.
Тепловые отходы по своим размерам могут быть весьма значительны. Отходящие горячие газы промышленных печей в среднем содержат около 3040% количества теплоты, поступающей в печи, а теплота, теряемая со сбросной нагретой водой, например, в сталеплавильных печах составляет 15-20 % теплоты расходуемого топлива.
Различают следующие основные группы вторичных энергоресурсов: Высокотемпературные, образующиеся при сжигании топлива непосред-
ственно в технологическом оборудовании, в т.ч.
1. Горячие газы (отходящие от печей, двигателей внутреннего сгорания и
др.)
2. Продукты технологического процесса (физическая теплота обрабатываемого материала и отходов, например, нагретых слитков, шлака, раскаленного кокса и т.п.)
Низкотемпературные вторичные энергоресурсы -
1.Пар, отработавший в двигателях и вторичный - после технологического процесса;
2.Горячая вода, получаемая от различных охлаждающих устройств, а также в виде производственного конденсата;
45
3. Производственные тепловыделения, являющиеся источником нагрева воздуха в помещениях.
Первые два вида энергоресурсов имеют температуру значительно более высокую.
Например, газы, отходящие от печей имеют температуру 500-1000 ° С, а выхлопные газы, отходящие из двигателей внутреннего сгорания, 350-600 ° С. Весьма высокую температуру имеют технологические продукты металлургической промышленности: стальные слитки 500-1000 ° С ; кокс, выдаваемый из кокосовой печи 1100 ° С; шлак плавильных печей 1200-1500 ° С.
Для второй группы энергоресурсов характерны низкие параметры тепло-
носителей: |
|
давление отработавшего пара двигателя, МПа |
0,12-0,3 |
температуры, ° С |
|
отработавшего пара двигателя |
100-130 |
производственного конденсата |
90-130 |
охлаждающей воды |
35-95 |
внутренних тепловыделений в производственных и |
|
других помещениях |
ниже 100. |
Важнейшей задачей при проектировании и эксплуатации теплового и технологического оборудования промпредприятий является максимальное сокращение выхода вторичных энергоресурсов, обеспечивающее прямую экономию топлива. Наиболее целесообразно использование вторичных энергоресурсов для технологических целей, т.е. для улучшения теплового баланса той установки, которая является источником тепловых отходов (например, использование теплоты горячих газов промышленных печей для подогрева воздуха, подаваемого в печь). При этом улучшается внутренняя регенерация теплоты в установке; отбросная теплота используется непрерывно, повышая технологический к.п.д. установки.
46
Использование вторичных энергоресурсов возможно также для увеличения располагаемой электрической мощности предприятия. Например, использование горячих газов для выработки пара с последующим производством электроэнергии.
И, наконец, использование вторичных энергоресурсов (пара или горячей воды) для теплоснабжения силовых, технологических и отопительновентиляционных процессов позволяет улучшить тепловой баланс промышленного предприятия в целом.
Подробная характеристика энергетических ресурсов промышленных предприятий по отдельным отраслям промышленности может быть получена из рассмотрения конкретных тепловых схем установки.
Так, в котельном цехе основными тепловыми отходами являются уходящие газы котлов с температурой 150-200град. Потери теплоты с уходящими газами составляют 10-15 % от теплоты сжигаемого топлива. При невозможности использовать уходящие газы на нагрев питательной воды и дутьевого воздуха котельного агрегата следует рассмотреть вопрос о применении теплофикационного экономайзера для подогрева сетевой воды. В тоже время, как известно, коэффициент теплопередачи от газов к воде невелик. Это потребует больших поверхностей экономайзера. Кроме того, из-за увеличения сопротивления газового тракта повышается расход электроэнергии дымососом. Поэтому применение теплофикационного экономайзера в ряде случаев экономически нецелесообразно.
Значительно меньше тепловых отходов содержится в дренажах, продувочной воде котлов. В турбинном цехе очень большие отходы теплоты имеют место с охлаждающей водой конденсаторов турбин (до 50% теплоты топлива, расходуемого на электростанциях). Однако ввиду низкой температуры охлаждающей воды (15-25 ° С) непосредственная утилизациях этих тепловых отходов невозможна. Отходы теплоты с охлаждающей водой масло- и воздухоохладителей турбогенераторов не превышает 1-2% энергии, вырабатываемой станцией.
47
Втепловых схемах паротурбинных ТЭС все чаще предусматривается использование внутри самой станции теплоты дренажей, продувочной воды котлов, охлаждающей воды масло- и воздухоохладителей для подогрева конденсата турбин, сырой воды в ХВО и т.д.
Взаключение следует отметить, что основным недостатком схем теплоснабжения, базирующихся лишь на тепловых отходах, является несоответствие графиков отпуска и потребления теплоты. Поэтому использовать полностью все тепловые отходы практически никогда не удается; используется только теплота, нужная потребителю. Если же теплопотребление имеет сезонный характер, то доля использования тепловых отходов в годовом разрезе еще меньше. Эти обстоятельства должны учитываться при разработке схемы использования тепловых отходов и в технико-экономических расчетах по обоснованию предлагаемой схемы.
8.2. Использование отработавшего и вторичного производственного пара
Паровой привод кузнечных молотов, прессов, штамповочных машин, насосов и других механизмов широко применяется на заводах металлургической, машиностроительной, химической, нефтеперерабатывающей, легкой и пищевой промышленности.
Паровые двигатели указанных механизмов, как правило, работают на выхлоп с противодавлением от 0,2 до 0,3 МПа.
Отходы теплоты с отработавшим паром весьма велики. Например, в агрегатах пластической обработки металлов применяется пар давлением 1,0-1,2 МПа в количестве 2-6 т на т поковки, а количество отработавшего пара составляет не менее 85-90% от соответствующего количества производственного пара, подаваемого в цех.
Энергетический К.П.Д. паровых машин, приводящих в движение молоты, прессы, очень низкий и составляет всего несколько процентов, а потеря
48
теплоты с отработавшим паром у паровых молотов достигает до 80% от его начальной энтальпии. На современных нефтеперерабатывающих заводах расходуется до 420 кг пара на 1т перерабатываемой нефти. В ряде отраслей промышленности производственные процессы, связанные с выпаркой технологического продукта, дают вторичный пар с давлением, близким к атмосферному.
Наконец, пар может быть получен при утилизации теплоты горячей воды. Это так называемый пар вторичного вскипания промышленного конденсата и пар в установках с испарительным охлаждением производственных агрегатов.
Использование отработавшего пара возможно в следующих направлени-
ях:
1)теплоснабжение потребителей;
2)выработка электроэнергии;
3)комбинированное использование пара полностью для теплоснабжения
ичастично на выработку электроэнергии, что обеспечивает круглогодовое потребление тепловых отходов.
Схема установки для использования отработавшего пара кузнечных молотов показана на рис. 9. В ней имеются все элементы, позволяющие использовать пар молотов как для теплоснабжения, так и для выработки электроэнергии.
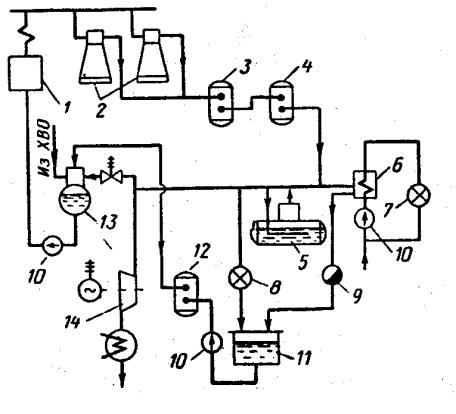
49
Рис. 9. Схема установки для использования отработавшего пара.
1- паровой котел; 2 - паровой молот; 3 - набивкоудалитель; 4- маслоотделитель; 5 - паровой аккумулятор; 6 - пароводяной подогреватель; 7 - потребители горячей воды; 8 - потребители пара; 9 - конденсатоотводчик; 10 - насос; 11 - конденсаторный бак; 12 - устройство для очистки конденсата; 13деаэратор; 14 - турбина низкого давления (мятого пара).
Отработавший в паровых молотах пар содержит хлопья сальниковой набивки и капли масла, поэтому при дальнейшем использовании его подвергают очистке в набивко- и маслоуловителях. В паровых системах теплоснабжения пар подается непосредственно к потребителям. Однако, в крупных и протяженных системах теплоснабжения транспортировка пара связана с большими затратами на сооружение коммуникаций. В этом случае, как правило, экономически целесообразнее применять водяную систему теплоснабжения. Теплоподготовительную установку размещают в непосредственной близости от места выхода отработавшего пара, а потребители получают теплоту с горячей водой, транспортируемой сетевыми насосом.
50
Как отмечалось выше, графики выхода отработавшего пара и расхода теплоты потребителями не совпадают. Для выравнивания графика поступления пара к потребителям (теплоприемники, турбины низкого давления) и устранения перебоев в их снабжении в схеме целесообразно устанавливать паровые аккумуляторы переменного давления.
В ряде случаев давление отработавшего или вторичного пара оказывается недостаточным для имеющегося теплового потребителя. Повышение давления пара можно осуществить в теплонасосных установках: механических, абсорбционных и струйных.
Для повышения давления отработавшего пара наибольшее распространение получили струйные теплонасосные установки, работающие по повысительной разомкнутой схеме, так называемые пароструйные компрессоры.
Применение струйных компрессоров позволяет уменьшить расходы острого пара и пара повышенного давления за счет частичного использования отработавшего пара.
На рис. 10 показаны различные схемы использования низкопотенциального пара с помощью пароструйных компрессоров.
При использовании отработавшего пара на цели теплоснабжения предпочтение следует отдавать круглогодичным потребителям теплоты на производственные нужды (подогрев воды, идущей на ХВО и питание котлов, нагрев промывочных, масляных и других ванн), а также на горячее водоснабжение (душевые и пр.)
Отработавший пар широко используется для покрытия отопительновентиляционной нагрузки предприятия, а в ряде случаев и заводских поселков, расположенных вблизи. Недостатком этого способа теплоснабжения является сезонность тепловой нагрузки, в связи с чем в летнее время резко ограничено использование отработавшего пара. Для устранения этого недостатка в летнее время можно использовать отработавший пар на выработку холода (в пароэжекторных или абсорбционных холодильных машинах), главным образом для