
10120
.pdf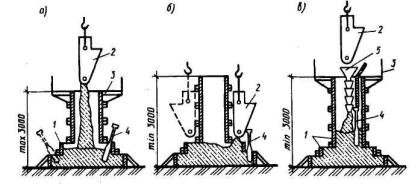
60
Укладка бетонной смеси в различные конструкции. Технологические приемы укладки бетонной смеси назначают в зависимости от типов конструкции и требований к ним, состава бетонной смеси, конструктивных особенностей опалубки, способов подачи бетонной смеси.
Вфундаменты и массивы в зависимости от принятой технологической схемы бетонную смесь подают в опалубку непосредственно с транспортного средства с применением эстакады, либо бетононасосами, либо бадьями с помощью кранов. Малоармированные фундаменты и массивы бетонируют смесью с осадкой конуса 1…3 см, а густоармированные – с осадкой конуса
4…6 см.
Вступенчатые фундаменты общей высотой до 3 м и площадью нижней ступени до 6 м2 смесь подают через верхний край опалубки (рис. 22, а). Внутренние вибраторы погружают в смесь через открытые грани нижней ступени. Аналогично ведут виброуплотнение второй и третьей ступени. В подколонник бетонную смесь можно подавать сразу же после окончания укладки в ступени через верх опалубки подколонника. Внутренние вибраторы для уплотнения бетона подколонника опускают сверху.
Рис. 22. Схема укладки бетонной смеси в ступенчатые фундаменты:
1 – опалубка фундамента; 2 – бункер с бетонной смесью; 3 – рабочий настил с ограждением; 4 – вибратор; 5 – звеньевой хобот
При высоте ступенчатых фундаментов более 3 м и площади нижней ступени более 6 м2 первые порции бетонной смеси поступают в нижнюю ступень по периметру (рис. 22, б). В последующем бетонную смесь подают через звеньевые хоботы (рис. 22, в); виброуплотнение бетонной смеси ведут аналогично предыдущему варианту.
В стены толщиной до 0,4 м укладывают подвижные бетонные смеси (ОК=6…8 см). Бетонную смесь подают в опалубку бетононасосом или бадьями с помощью крана в нескольких точках по длине участка (рис. 23). При высоте стен более 3 м используют звеньевые хоботы, при этом бетонную смесь укладывают слоями 0,3…0,4 м с вибрированием внутренними вибраторами.
В колонны высотой до 5 м сечением до 0,8х0,8 м, не имеющие перекрещивающихся хомутов, бетонную смесь укладывают сверху и уплотняют глубинными вибраторами, опускаемыми через верх опалубочного короба (рис. 24, а). При высоте колонн свыше 5 м смесь подают через воронки
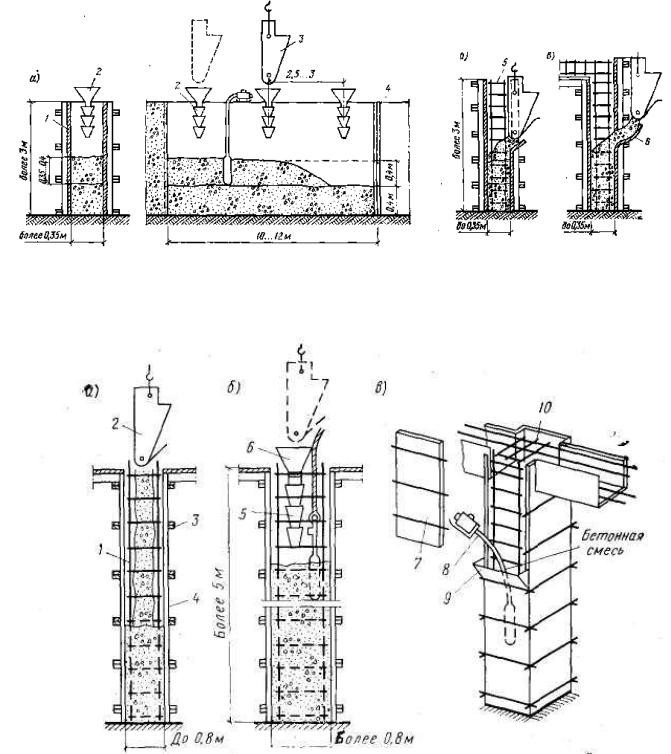
61
по звеньевым хоботам (рис. 24, б). В высокие и густоармированные колонны смесь укладывают ярусами через окна в опалубке (рис. 24, в).
Рис. 23. Укладка бетонной смеси в стены: а – послойное бетонирование; б – бетони-
рование высоких и густоармированных стен с наращиванием опалубки; в – бетонирование через карманы: 1 – опалубка; 2 – звеньевой хобот; 3 – бункер с бетонной смесью; 4 – разделительная опалубка в рабочем шве; 5 – арматурный каркас; 6 – карман
Рис. 24. Укладка бетонной смеси в колонны:
а – колонны высотой до 5 м; б – то же, высотой более 5 м; в – то же, с густой арматурой: 1 – арматура; 2 – бункер; 3 – хомуты; 4 – опалубка; 5 – звеньевой хобот; 6 – приемная воронка звеньевого хобота; 7 – съемный щит; 8 – вибратор с гибким валом; 9 – карман; 10 – арматура балки
62
В балки и плиты, монолитно связанные со стенами, бетонную смесь укладывают через 1…2 ч после укладки последнего слоя смеси в вертикальные конструкции, ввиду необходимости первоначальной осадки уложенной в них смеси. В балки (прогоны) и плиты ребристых перекрытий смесь укладывают, как правило, одновременно. В балки высотой более 80 см бетонную смесь укладывают слоями 30…40 см с уплотнением внутренними вибраторами, причем последний слой смеси должен быть на 3…5 см ниже уровня низа плиты перекрытия. В плиты перекрытия бетонная смесь подается сразу на всю ширину с уплотнением поверхностными вибраторами при их толщине до 0,25 м и внутренними – при большей толщине.
Уход за бетоном имеет целью создание оптимальных условий для его твердения в течение первых 3…7 суток. Для этого в летних условиях распластанные конструкции (полы, плиты и др.) сразу же после завершения бетонирования укрывают полиэтиленовой пленкой, засыпают слоем опилок и периодически (через 3…5 ч) поливают водой. Бетон, уложенный в фундаменты, колонны, стены также увлажняют, чтобы избежать быстрого его высыхания и растрескивания от больших усадочных напряжений.
4.1.5. Технология бетонирования в зимних условиях
Понятие «зимние условия» в технологии монолитного бетона и железобетона означает снижение среднесуточной температуры наружного воздуха до +5°С и падение температуры в течение суток ниже 0°С.
При отрицательных температурах содержащаяся в бетонной смеси вода замерзает, прекращается реакция гидратации цемента и, следовательно, бетон не твердеет. Одновременно в бетоне развиваются значительные силы внутреннего давления, вызванные увеличением (примерно на 9 %) объема воды при переходе ее в лед. При раннем замораживании бетона его неокрепшая структура разрушается под воздействием этих сил. Кроме того, замораживание свежеуложенного бетона сопровождается образованием вокруг арматуры и зерен заполнителя ледяных пленок, в результате чего ухудшается сцепление арматуры и заполнителя с цементным камнем. Все эти процессы значительно снижают прочность, плотность и долговечность бетона.
Если бетон до замерзания приобретает определенную начальную прочность, то упомянутые выше процессы не оказывают на него неблагоприятного воздействия. Минимальную прочность, при которой замораживание для бетона не опасно, называют критической. Величина нормируемой критической прочности зависит от класса бетона, вида и условий эксплуатации конструкции и составляет: для бетонных и железобетонных конструкций с ненапрягаемой арматурой – 50 % проектной прочности для бетонов класса В7,5…В10; 40 % – для В12,5…В25; 30 % – для В30 и выше; для конструкций с предварительно напрягаемой арматурой – 80 %; для конструкций, нагружаемых расчетной нагрузкой, – 100 % проектной прочности.
При бетонировании в зимних условиях необходимо создать и поддерживать такие температурно-влажностные условия, при которых бетон твердеет до приобретения критической прочности в минимальные сроки. Для
63
этого применяют специальные способы приготовления, подачи, укладки и выдерживания бетона.
При приготовлении бетонной смеси в зимних условиях ее температуру повышают до 35…40°С путем подогрева заполнителей и воды.
Состояние основания, на которое укладывают бетонную смесь, а также способ ее укладки должны исключать возможность ее замерзания в стыке с основанием. Для этого основание отогревают до положительной температуры. Опалубку и арматуру до бетонирования очищают от снега и наледи. Бетонирование следует вести непрерывно и высокими темпами.
Метод выдерживания бетона, уложенного в опалубку, выбирают в зависимости от вида и массивности конструкции, вида, состава и требуемой прочности бетона, энергетической оснащенности строительной площадки и т.д. Эти методы можно разделить на три группы: метод «термоса»; методы, основанные на искусственном прогреве бетона – электропрогрев, контактный, индукционный и инфракрасный нагрев, конвективный обогрев; методы, основанные на применении химических добавок, снижающих температуру замерзания воды и ускоряющих твердение бетона. Указанные методы можно комбинировать.
Технологическая суть метода «термоса» заключается в том, что имеющая положительную температуру (15…30°С) бетонная смесь укладывается в утепленную опалубку. В результате этого бетон конструкции набирает заданную прочность за счет начального теплосодержания и экзотермического тепловыделения цемента. При выборе метода «термоса» рекомендуется применять быстротвердеющие портландцементы, которые обладают наибольшей экзотермическим тепловыделением, то есть при твердении выделяют максимальное количество теплоты.
Эффективность метода «термоса» тем выше, чем массивнее бетонируемая конструкция. Степень массивности конструкции характеризуется модулем ее поверхности, представляющим собой отношение площади охлаждаемых поверхностей конструкции к ее объему: Мп= А/V. Для колонн, балок и других линейных конструкций Мп определяют отношением периметра к площади поперечного сечения. Метод «термоса» эффективен при выдерживании массивных конструкций с Мп ≤ 6 при укладке смесей на портландцементе и Мп ≤ 10 на быстротвердеющем портландцементе.
Сущность методов искусственного прогрева бетона заключается в повышении температуры уложенного бетона до максимально допустимой и поддержании ее в течение времени, за которое бетон набирает критическую прочность. Эти методы применяют при бетонировании немассивных конструкций с Мп ≥ 10, а также и более массивных, если в последних невозможно получить в установленные сроки заданную прочность бетона при выдерживании только методом «термоса».
Физическая сущность электропрогрева заключается в использовании теплоты, выделяемой в уложенном бетоне при пропуске через него электрического тока. Для подведения электрической энергии к бетону
64
используют различные электроды: пластинчатые, полосовые, стержневые и струнные; наиболее эффективно использование пластинчатых электродов.
Пластинчатые электроды представляют собой пластины из кровельного железа или стали, нашиваемые на внутреннюю, примыкающую к бетону поверхность опалубки и подключаемые к разноименным фазам питающей сети. В результате токообмена между противолежащими электродами весь объем конструкции нагревается. Электропрогрев ведут на пониженных напряжениях в пределах 50…127 В. Удельный расход электроэнергии в среднем составляет 60…80 кВт/ч на 1 м3 железобетона.
Контактный (кондуктивный) нагрев. При этом методе используют
греющую опалубку: она имеет палубу из металлического листа или водостойкой фанеры, с тыльной стороны которой расположены электрические нагревательные элементы – греющие провода, кабели, или сетчатые нагреватели. Нагреватели изолируют от палубы, а также с тыльной стороны опалубочного щита асбестовыми листами и покрывают теплоизоляцией.
При инфракрасном нагреве бетона в качестве генераторов инфракрасного излучения применяют трубчатые металлические и кварцевые излучатели. Для создания направленного лучистого потока излучатели заключают в плоские или параболические рефлекторы (обычно из алюминия).
При индукционном нагреве бетона используют теплоту, выделяемую в арматуре или стальной опалубке, находящихся в электромагнитном поле катушки-индуктора, по которой протекает переменный электрический ток. Для этого по наружной поверхности опалубки последовательными витками укладывается изолированный провод-индуктор. Переменный электрический ток, проходя через индуктор, создает переменное электромагнитное поле. Электромагнитная индукция вызывает в находящемся в этом поле металле (АРМатуре, стальной опалубке) вихревые токи, в результате чего арматура (стальная опалубка) нагревается и за счет контакта нагревает бетон. Индукционный метод наиболее эффективен при бетонировании конструкций, густо насыщенных арматурой, а также при использовании металлической опалубки.
При конвективном обогреве тепловая энергия бетону передается с помощью нагретой среды – теплым воздухом или паром. В этом случае бетон до приобретения им заданной прочности выдерживают в тепляках – временных ограждающих сооружениях. В настоящее время в качестве тепляков применяют надувные конструкции из синтетических материалов, которые представляют собой двухслойное ограждение с воздушной прослойкой. Тепляки применяют при возведении высотных сооружений в скользящей или объемно-переставной опалубке. Тепляки обогревают как правило, электрическими или паровыми калориферами.
Применение бетонов с противоморозными добавками. Противоморозные добавки – это химические соединения, вводимые в бетонную смесь в количестве 2…10 % массы цемента и способствующие твердению бетона при отрицательных температурах. Эти добавки оказывают различное воздействие на бетонную смесь: одни ускоряют процесс твердения бетона, другие снижают температуру замерзания воды и, следовательно, позволяют увеличить продолжительность твердения бетона до набора им критической прочности.
65
В качестве основных противоморозных добавок применяют хлорид кальция CaCl2 (ХК), хлорид натрия NaCl (ХН), поташ K2CO3 (П) и нитрит натрия NaNO2 (НН). Применяют также ряд комплексных соединений: нитрит кальция с мочевиной (НКМ), нитрат кальция + мочевина (НК+М) и др. Бетоны с добавками хлористых солей можно применять в неармированных конструкциях и в конструкциях, армированных конструктивной арматурой. Бетоны с противоморозными добавками нельзя применять в конструкциях, подверженных динамическим нагрузкам и в предварительно напряженных конструкциях.
4.2. Технологии строительства зданий из кирпича и других мелкоштучных материалов.
Каменные работы представляют собой поштучную укладку камня на растворе. Такую укладку выполняют при устройстве фундаментов, стен зданий и сооружений, колонн, столбов, арок и других строительных конструкций, работающих преимущественно на сжатие.
В зависимости от вида применяемых материалов каменную кладку подразделяют на кладку из искусственных и природных камней.
Кладку из искусственных каменных материалов выполняют из сплошного или пустотелого кирпича и из сплошных или пустотелых прямоугольных камней.
Кладку из естественных каменных материалов выполняют из камней правильной и неправильной формы. Кладку из камней неправильной формы называют бутовой. Разновидностью бутовой кладки является бутобетонная, в которой слои бутового камня втапливаются в слои бетонной смеси.
Камень, применяемый при возведении строительных конструкций, является штучным материалом, допускающим возможность ручной укладки. Его масса – от 3…5 кг и не превышает 35 кг. Искусственные каменные материалы подразделяют на кирпич керамический и силикатный полнотелый и пустотелый, керамические и силикатные камни пустотелые и камни бетонные стеновые. Кирпич имеет размеры: обычный – 250×120×65 мм, модульный (утолщенный) – 250×120×88 мм. По прочности кирпич разделяют на марки 300, 250, 200, 175, 150, 125, 100 и 75. Масса кирпича равна 3…5 кг.
Керамические и силикатные пустотелые камни изготовляют размерами: обычные – 250×120×38 мм и модульные – 288×138×138 мм. Поверхность граней у камней выполняется гладкой или рифленой. Камни бетонные стеновые выпускают сплошными и пустотелыми. Их изготовляют из тяжелых, облегченных и легких бетонов с максимальными размерами 390×190×188 мм массой до 35 кг.
Камни имеют опорные и боковые поверхности (рис. 25, а). Опорные поверхности – это постель камня, а боковые – тычок и ложок. Камни, уложенные ложками вдоль стены (рис. 25, б), называют ложковыми, а поперек
– тычковыми.
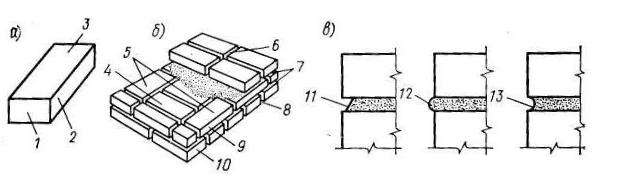
66
Крайние камни в стене называют верстовыми, а промежуточные между верстовыми – забуткой. Пространства между камнями в продольном и поперечном направлении, заполненные раствором, являются швами.
В зависимости от степени заполнения швов раствором различают кладку впустошовку и под расшивку (рис. 25, в). Первый вид применяют, если в последующем необходимо оштукатурить поверхность, для чего швы на глубину 10…15 мм не заполняют раствором. Это обеспечивает качественное сцепление наносимой штукатурки с каменной кладкой. При втором виде кладки швы заполняют раствором полностью, придавая им различную форму: выпуклую, вогнутую, прямоугольную и др.
Рис. 25. Элементы камня и каменной кладки:
а – камень; б – кладка; в – швы кладки; 1 – тычок; 2 – ложок; 3 – постель; 4 – забутка; 5 – верстовые камни (наружная и внутренняя версты); 6, 8 – вертикальные швы, продольный и поперечный; 7 – горизонтальный шов; 9 – ложковый ряд кладки; 10 - тычковый ряд кладки; 11 – неполный шов; 12 – выпуклый шов; 13 – вогнутый шов
Растворы для каменной кладки применяют с целью связывания отдельных камней в монолит, что обеспечивает равномерное распределение нагрузки и жесткую связь между камнями, предохраняет кладку от продувания и проникания воды. Применяют преимущественно смешанные растворы, в которых вяжущим является цемент, пластификатором – известь или глина, а заполнителем – песок. Цементные растворы применяют только для особо нагруженных конструкций, в армированной кладке и в кладке подземных конструкций. Для каменной кладки применяют растворы следующих устанавливаемых проектом марок: 4, 10, 25, 50, 75, 100, 150 и 200.
Растворы должны быть не только прочными, но и достаточно технологичными, т.е. они должны позволять укладывать их на основание (кирпич и т.п.) тонким однородным слоем с хорошим заполнением всех швов и пустот.
4.2.1. Кладка из камней правильной формы Виды кладок и системы перевязки швов. В зависимости от требований
по прочности, теплофизическим свойствам и архитектурной законченности кладку из керамических и силикатных камней правильной формы выполняют сплошной, сплошной с армированием, облегченной и с облицовкой
67
поверхностей. Раскладку кирпича и камней в слоях кладки и чередование слоев производят по определенной системе, которую называют системой перевязки кладки. Наиболее распространенными системами перевязки для стен и простенков являются однорядная и многорядная.
При однорядной (цепной) системе перевязки швов кладки каждый ложковый ряд чередуется с тычковым и, следовательно, все вертикальные поперечные и продольные ряды каждого ряда перекрываются кирпичами или камнями следующего ряда (рис. 26, а). С фасадной стороны стены вертикальные поперечные швы тычкового ряда смещены на ¼ кирпича относительно поперечных швов ложкового ряда и тем самым все кирпичи связаны между собой в единую цепь.
Многорядную систему перевязки выполняют чередованием одного тычкового и трех-пяти ложковых рядов кирпича (рис. 26, б). При такой кладке вертикальные поперечные швы во всех рядах, кроме тычкового и смежных с ним ложковых, перекрывают на ½ кирпича. Вертикальные продольные швы в трех-пяти смежных рядах по вертикали не перекрывают; перекрывают их только на 4-6-м ряду тычковыми верстовыми или забуточными кирпичами. Первый ряд такой кладки укладывают тычками. Второй ряд укладывают ложковыми так же, как и при однорядной кладке, а с 3-го по 6-й ряды укладывают одними ложками вдоль стены.
Последнее является преимуществом такой системы перевязки по отношению к однорядной, т.к. укладка кирпичей в забутку ложками проще и при такой перевязке меньше кирпичей приходится укладывать в верстовые ряды, а больше в забутку.
Достоинствами многорядной кладки являются: большая жесткость стены в продольном направлении, т.к. в ложковых рядах смежные поперечные швы смещены друг относительно друга на ½ кирпича; повышенная производительность труда каменщиков, т.к. они выполняют однотипные операции на высоте нескольких рядов, не меняя приемов кладки и системы перевязки швов (при однорядной кладке каменщик меняет приемы укладки кирпича через ряд, чередуя ложковые и тычковые ряды); меньшая трудоемкость вследствие укладки каменщиком низкой квалификации в забутку до 40 % общего количества потребляемого кирпича (при однорядной кладке в забутку укладывают около 25% кирпича); повышенные теплоизоляционные свойства кладки, т.к. на высоте нескольких рядов вертикальные продольные швы не заполняются раствором, а остаются пустыми и выполняют теплозащитные функции.
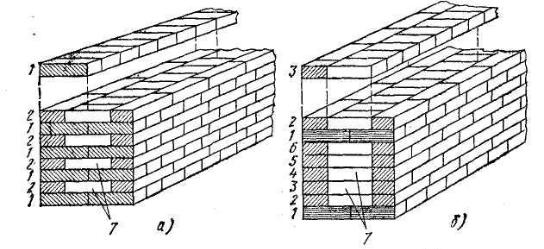
68
Рис. 26. Системы перевязки при кладке стен толщиной 2 кирпича:
а – однорядная перевязка; б – многорядная перевязка; 1 – тычковый ряд; 2,3,4,5,6 – ложковые ряды; 7 – забуточные кирпичи
Недостатки многорядной кладки: снижение несущей способности кладки примерно на 6 % по сравнению с однорядной; усложнение производства работ при отрицательных температурах. Обусловливается это тем, что замерзание раствора в продольных вертикальных швах может вызвать выпучивание наружных или внутренних верст толщиной в ½ кирпича, которые не имеют перевязки на высоте пяти рядов.
Независимо от принятой системы перевязки кладку всегда начинают с тычкового ряда и заканчивают вверху тоже тычковым рядом. Тычковые ряды также укладывают на уровне обрезов стен и столбов, в выступающих рядах кладки (карнизах, поясках), под опорными частями балок, прогонов, плит перекрытий и балконов.
Армированная кладка осуществляется с целью повышения несущей способности каменных конструкций. Для этого в горизонтальные швы укладывают металлические сетки. Толщина швов должна быть не менее чем на 4 мм больше суммы диаметров пересекающейся арматуры.
Для армирования кирпичной кладки, как правило, используют сварные или вязаные сетки с прямоугольным или зигзагообразным расположением проволок. В сетках с прямоугольным расположением проволок диаметр их не должен превышать 4 мм, т.к. проволоки накладывают друг на друга и увеличение их диаметра приведет к увеличению толщины шва, что вызовет снижение несущей способности кладки. При зигзагообразном расположении проволок диаметр их не более 8 мм. Расстояние между проволоками в сетках устанавливают в проекте, но, как правило, оно составляет 30…120 мм. По высоте столбов и простенков сетки укладывают в соответствии с растягивающими усилиями в кладке, но не реже чем через пять рядов кладки. Сетки с прямоугольным расположением укладывают по одной, а сетки с зигзагообразным расположением – с тем же интервалом, но попарно в двух смежных рядах с перпендикулярным расположением проволок. Для облегчения контроля укладки сеток их размещают таким образом, чтобы концы отдельных проволок выступали на 2…3 мм на одну из внутренних поверхностей выложенной конструкции.
69
При возведении конструкций, воспринимающих растягивающие усилия от изгиба, внецентренного сжатия, динамического воздействия, используют продольное армирование. В этом случае стержни располагают внутри или снаружи конструкции. При внутреннем расположении стержни располагают в вертикальных швах, при наружном – вне конструкции с последующей защитой штукатурным слоем.
Облегченные кладки применяют для уменьшения расхода кирпича и собственной массы зданий. Такие конструкции экономичны по стоимости и расходу материалов, однако применение облегченной кладки обусловливает ограничение высоты возводимого здания. Применение облегченных кладок позволяет в целом снизить стоимость 1 м2 стены по сравнению со сплошной на 20…30 %, а расход кирпича – на 30…40 %.
Кладку стен с облицовкой кирпичом и камнями правильной формы применяют с целью придания облику здания большей архитектурной выразительности. Для этих целей используют лицевой кирпич и керамические камни различной обработки и расцветки. Облицовку стен выполняют одновременно с кладкой, перевязывая облицовочный слой с основным массивом стены путем укладки тычковых рядов в облицовочном слое. Применяют различные варианты перевязки облицовочного слоя с кладкой массива стены, из которых наиболее употребительны многорядная и однорядная системы перевязки.
Инструмент, приспособления и инвентарь. Эффективное и качественное выполнение работ по возведению каменной кладки предусматривает использование специального инструмента, приспособлений и инвентаря.
Инструмент включает производственный инструмент каменщика, которым рабочие осуществляют необходимые технологические операции, и кон- трольно-измерительный инструмент, с помощью которого проверяют качество кладки (рис. 27). К основному производственному инструменту относятся кельма, молоток-кирочка, растворная лопата, расшивка. К контрольно-измери- тельному инструменту относятся порядовки, шнур-причалка, правило, уровень, отвес, угольник, складной метр металлический, рулетка измерительная.