
Современное здание. Конструкции и материалы (2006)
.pdf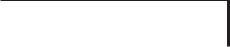
лнЦдгй а лЗЦнйикйбкДузхЦ игДлнада
В современном строительстве поликарбонат применяется в двух видах – в виде монолитных и структурированных листов различной толщины.
Монолитный поликарбонат редко используется в горизонтальных перекрытиях (он слишком дорог для этого), но является идеальным материалом, из которого путем горячего формования получают элементы криволинейной формы. Это различные купола с круглым, квадратным или прямоугольным основанием, протяженные модульные световые фонари с неограниченной длиной и отдельные секции огромных куполов, достигающие 8-10 м в диаметре (легко транспортируемые и собираемые).
Современные технологии позволяют изготавливать изделия из монолитного поликарбоната с ребрами жесткости, что делает их пригодными для самонесущих перекрытий. В этом случае необходимость в применении металлического каркаса отпадает, благодаря чему отсутствуют "мостики холода" и возможность появления конденсата.
Структурированные листы (порой именуемые сотовыми или ячеистыми) – это наиболее распространенный вид поликарбоната, применяемый в строительной индустрии сегодня, в основном, используемый в горизонтальных, либо арочных перекрытиях – крышах, навесах, зенитных фонарях и т.д.
Структурированные поликарбонатные листы производят методом экструзии, при этом происходит плавление гранул и выдавливание полученной массы через особое устройство, форма которого определяет строение и конструкцию листа.
К основным достоинствам структурированных поликарбонатных листов относятся:
•малый удельный вес (от 0,8 до 4,0 кг/м2), что позволяет проектировать легкие конструкции с большим количеством дизайнерских возможностей и удешевляет стоимость покрытия;
•высокие теплоизоляционные свойства (коэффициент приведенного сопротивления теплопередаче составляет 0,36 - 0,735 м2С/Вт);
•высокая ударная прочность (к примеру, в районе Флориды с сильными ветрами такие листы применяются для покрытия зданий и предохраняют их от летящих предметов);
•высокая несущая способность (до 250 кг/м2 при шаге обрешетки 1-2 м), которая сохраняется в температурном режиме от -40°С до +120°С;
•прозрачность;
•гибкость, позволяющая легко изготавливать арочные перекрытия;
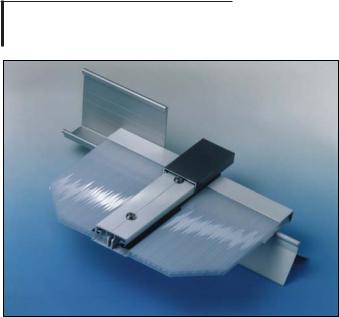
лнЦдгй а лЗЦнйикйбкДузхЦ игДлнада
êËÒ.3.5.8
дУМТЪ ЫНЪЛ‚М˚И ЫБВО (ФУ П‡ЪВ Л‡О‡П ЩЛ П˚ POLYGAL).
•высокая химическая стойкость;
•долговечность (гарантированный срок службы – 10-12 лет);
•низкая горючесть.
Уполикарбоната, как и у каждого материала, есть и некоторые недостатки, на которые необходимо обращать внимание при его использовании. Поликарбонат, как и любой пластический материал, подвержен температурному расширению в большей степени, чем материалы конструкций. Это свойство требует особого технического решения при проектировании, особенно в плоских покрытиях больших размеров. Возможны также механические повреждения поверхности листов, как и у стекла, например. Для решения этой проблемы поверхность листов можно обрабатывать специальным покрытием, а также сохранять защитное полиэтиленовое покрытие до окончания монтажа.
На отечественном рынке представлены поликарбонатные панели различных производителей. Общим для них (как уже упоминалось выше) является следующее: это прозрачные, легкообрабатываемые панели, обладающие малым удельным весом, высокими теплоизоляционными свойствами и исключительной ударной прочностью. Основной областью их применения являются арочные, горизонтальные
инаклонные (реже – вертикальные) светопропускающие перекрытия в различных, общественных и индустриальных и жилых зданиях и сооружениях. Поликарбонатные структурированные листы широко используются во всех развитых странах мира, в конструкциях спортивных и выставочных залов, крытых пешеходных переходов, заводских цехов и торговых комплексов.
За четверть века своего развития индустрия выработала ряд стандартов, в том числе и на толщину панелей: 4, 6, 8, 10, 16 и 25 мм. Выпускаются панели толщиной 32 мм, но на российском рынке они пока редкость. Стандартизованы
игоризонтальные размеры – подавляющее большинство предприятий выпускает листы шириной 2100 и длиной 6000 или 12 000 мм. Некоторые фирмы, впрочем, способны поставлять своим заказчикам листы гораздо большей длины.
Говоря о толщине панелей, необходимо заметить следующее: панели толщиной 4 и, ÷àcòî 6 мм не являются конструкционными материалами и не предназначены для использования в наружных конструкциях, особенно в регионах с высокими снеговыми либо ветровыми нагрузками. Основная область применения подобных панелей – рекламные щиты, световые короба, а также различного рода вывески и надписи. Для использования в архитектурных целях рекомендуются материалы от 8 до 16 мм, а там, где необходима особо высокая теплоизоляция, – 25 мм или толще.
Несколько отдельных слов следует сказать об ещс одной области применения структурированного поликарбоната – это аграрный сектор. Сочетание высокой прозрачности вкупе с достаточно высоким светорассеиванием (исключающим ожоги растений прямыми солнечными лучами), отличной теплоизоляцией и долговечностью делает поликарбонатные панели незаменимым материалом для изготовления крупных промышленных теплиц и парников. Хотя поликарбонат непроницаем для УФ - из лучения д о л я п р о н и к а ю щ е г о с к в о з ь н е г о с в е т а
достаточна для нормального развития растений. Оптимальными для такого использования следует признать панели толщиной 8 мм вследствие удачного сочетания цены, пропускающей способности и прочностных качеств. Особо хотелось бы отметить, что ряд ведущих фирм-изготовителей предлагает панели с покрытием "antifog", которое предотвращает образование капель воды на внутренней стороне панели, образуя пленку, способствующую повышению общего
уровенÿ освещенности внутри теплицы.
Если же попытаться понять, в чем состоят различия между поликарбонатными листами производства различных фирм, то здесь, в первую очередь, следует заметить разницу в поперечных сечениях панелей. Фирмы варьируют толщину наружных поверхностей и продольных перегородок, а также расстояние между ними. Для увеличения жесткости вводят в перегородки дополнительные диагональные или Х-образные элементы, разрабатывают свои собственные системы монтажа и крепления панелей (рис. 3.5.8).
Уникальная конструкция, например, разработана предприятием POLYGAL-TRIPLE-CLIP. Данная специальная алюминий-поликарбонатная система панелей и особых профилей позволяет с минимальными трудозатратами собрать гладкую, практически без стыков поверхность. Более того, применение подобной системы исключает для строителей и проектировщиков необходимость задумываться над проблемой компенсации линейного термического расширения поликарбоната – общей беды практически всех термопластиков. Особым образом сконструированные
элементы соединения поликарбонатных панелей исключают возможность деформации материала при при перепаде температур и обеcпечивают полную герметичность стыков. Имеются и другие различные системы для надежного монтажа поликарбонатных панелей.
Поликарбонатные панели, очевидно, не являются универсальными заменителями стекла или стеклопакетов в любых конструкциях, но, будучи грамотно применснными, безусловно, способны помочь архитекторам в разработке долговечных, комфортабельных, современных и пластически разнообразных проектов зданий и сооружений.
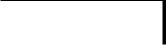
3.6 Бетоны
БЕТОНЫ
3.6.1 Основные сведения о бетоне
Бетонами называют искусственные каменные материалы, получаемые в результате затвердевания тщательно перемешанной и уплотненной смеси из минерального или органического вяжущего вещества с водой, мелкого и крупного заполнителей, взятых в определенных пропорциях. До затвердевания эту смесь называют бетонной смесью.
Встроительстве широко используют бетоны,
приготовленные на цементах или других неорганических вяжущих веществах. Эти бетоны обычно затворяют водой. Цемент и вода являются активными составляющими бетона; в результате реакции между ними образуется цементный камень, скрепляющий зерна заполнителей в единый монолит.
Между цементом и заполнителем обычно не происходит химического взаимодействия (за исключением силикатных бетонов, получаемых автоклавной обработкой), поэтому заполнители часто называют инертными материалами.
Однако они существенно влияют на структуру и свойства, изменяя его пористость, сроки затвердевания, поведения при воздействии нагрузки и внешней среды. Заполнители значительно уменьшают деформации бетона при твердении и тем самым обеспечивают получение больше размерных изделий и конструкций. В качестве заполнителей используют преимущественно местные горные породы и отходы производства (шлаки и др.). Применение этих дешевых заполнителей снижает стоимость бетона, так как заполнители и вода составляют 85... 90%, а цемент 4 10...15% от массы бетона.
В последние годы в строительстве широко используют легкие бетоны, получаемые на искусственных пористых заполнителях. Пористые заполнители снижают плотность бетона, улучшают его теплотехнические свойства.
Для регулирования свойств бетона и бетонной смеси в их состав вводят различные химические добавки, которые ускоряют или замедляют схватывание бетонной смеси, делают ее более пластичной и удобоукладываемой, ускоряют твердение бетона, повышают его прочность и морозостойкость, а также при необходимости изменяют и другие свойства бетона.
Бетоны на минеральных вяжущих веществах являются капилярно4пористыми телами, на структуру и свойства которых заметное влияние оказывают как внутренние процессы взаимодействия составляющих бетона, так и воздействие окружающей среды.
В течении длительного времени в бетонах происходит изменение поровой структуры, Наблюдается протекание структурообразующих,, а иногда и деструктивных процессов и как результат 4 изменение свойств материала. С увеличением возраста бетона повышается его прочность, плотность, стойкость к воздействию окружающей среды. Свойства бетона определяется не только его составом и качеством исходных материалов, но и технологией приготовления и укладки бетонной смеси в конструкцию, условиями твердения бетона. Все эти факторы учитывают при проектировании бетона и производстве конструкций на его основе.
На органических вяжущих веществах (битум, синтетические смолы и т.д.) бетонную смесь получают без введения воды, что обеспечивает высокую плотность и непроницаемость бетонов.
Многообразие вяжущих веществ, заполнителей, добавок и технологических приемов позволяет получать бетоны с самыми разнообразными свойствами.
Бетон является хрупким материалом: его прочность при сжатии в несколько раз выше в несколько раз выше прочности при растяжении. Для восприятия растягивающих напряжений бетон армируют стальными стержнями, получая железобетон. В железобетоне арматуру располагают так, чтобы она воспринимала растягивающие напряжения, а сжимающие напряжения передавались на бетон. Совместная работа арматуры и бетона обусловливается хорошим сцеплением между ними и
приблизительно одинаковыми температурными коэффициентами линейного расширения. Бетон предохраняет арматуру от коррозии. Бетонные и железобетонные конструкции изготовляют либо непосредственно на месте строительства 4 монолитный бетон и железобетон, либо на заводах и полигонах с последующем монтажом на строительной площадке 4 сборный бетон и железобетон.
3.6.2 Основные этапы развития технологии бетона
Бетон 4 один из древнейших строительных материалов. Из него построены галерей египетского лабиринта (3600 лет до н. э.), часть Великой Китайской стены (III в. до н. э.), ряд сооружений на территории Индии, Древнего Рима и в других местах.
Однако использование бетона и железобетона для массового строительства началось только во второй половине XIX в., после получения и организации промышленного выпуска портландцемента, ставшего основным вяжущем веществом для бетонных и железобетонных конструкций. Вначале бетон использовался для возведения монолитных конструкций и сооружений. Применялись жесткие и малоподвижные бетонные смеси, уплотнявшиеся трамбованием. С появлением железобетона, армированного каркасами, связанными из стальных стержней, начинают применять более подвижные и даже литые бетонные смеси, чтобы обеспечить их надлежащее распределение и уплотнение в бетонируемой конструкции. Однако применение подобных смесей затрудняло получение бетона высокой прочности, требовало повышенного расхода цемента. Поэтому большим достижением явилось появление в 304х годах способа уплотнения бетонной смеси вибрированием, что позволило обеспечить хорошее уплотнение малоподвижных и жестких бетонных смесей, снизить расход цемента в бетоне, повысить его прочность и долговечность.
В эти же годы был предложен способ предварительного напряжения арматуры в бетоне, способствовавший снижению расхода арматуры в железобетонных конструкциях, повышению их долговечности и трещиностойкости.
Проф. А.Р. Шуляченко в 804х годах прошлого века разработал теорию получения и твердения гидравлических вяжущих веществ и цементов и доказал, что на их основе могут быть получены долговечные бетонные конструкции. Под его руководством было организовано производство высококачественных цементов. Проф. Н.А. Белелюбский в 1891г. провел широкие испытания, результаты которых способствовали внедрению железобетонных конструкций в строительство. Проф. И.Г. Малюга в 1895 г. в своей работе "Составы и способы изготовления цементного раствора (бетона) для получения наибольшей крепости" обосновал основные законы прочности бетона В 1912 г. был издан капитальный труд Н.А. Житкевича "Бетон и бетонные работы".
В начале века появляются много работ по технологии бетона и за рубежом. Из них наиболее важными были работы Р. Фере (Франция), О. Графа (Германия), И. Боломе (Швейцария), Д. Абрамса (США).
Широкое развитие получила технология бетона в СССР со времени первых крупных гидротехнических строительств 4 Волховстроя (1924 г.) и Днепростроя (1930 г.). Профессора Н.М. Беляев и И.П. Александрии возглавили ленинградскую научную школу по бетону.
В 304е годы ученные московской школы бетона Б.Г. Скрамтаев, Н.А. Попов, С.А. Миронов, С.В. Шестоперов, П.М. Миклашевский и другие разработали методы зимнего бетонирования и тем самым обеспечили круглогодичное возведения бетонных и железобетонных конструкций, создали ряд новых видов бетона, разработали способы повышения долговечности бетона, основы технологии сборного железобетона. В послевоенные годы создаются новые виды вяжущих веществ и бетонов, начинают широко применятся химические добавки,
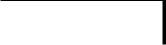
БЕТОНЫ
улучшающие свойства бетона, совершенствуются способы |
Полимерцементные бетоны получают на смешанном |
проектирования состава бетона и его технология. |
связующем, состоящем из цемента и полимерного вещества |
Ежегодно в строительстве применяются примерно 250 млн. куб. |
(водорастворимые смолы и латексы). |
метров бетона и железобетона, в том числе около 125 млн. куб. |
Специальные бетоны готовят с применением особых |
метров сборного железобетона. На предприятиях работает свыше |
вяжущих веществ. Для кислотоупорных и жаростойких бетонов |
25000 технологических линий по производству сборного |
применяют жидкое стекло с кремнефтористым натрием, фосфатное |
железобетона. |
связующее. В качестве специальных вяжущих используют |
|
шлаковые, нефелиновые и стеклощелочные, полученные из |
3.6.3 Классификация бетонов |
отходов промышленности. |
Внастоящее время в строительстве используют Бетоны применяют для различных видов конструкций, как
различные виды бетона. Разобраться в их многообразии помогает классификация бетонов. Бетоны классифицируют по средней плотности, виду вяжущего вещества и назначению.
Многие свойства бетона зависят от его плотности, на величину которой влияют плотность цементного камня, вид заполнителя и структура бетонов. По плотности бетоны делят на особо тяжелые с плотностью более 2500 кг/ куб. м.; тяжелые 4 1800...2500; легкие 4500... 1800; особо легкие 4 менее 500 кг/куб, м. Особо тяжелые бетоны приготовляют на тяжелых заполнителях 4 стальных опилках или стружках (сталебетон), железной руде (лимонитовый и магнетитовый бетоны) или барите (баритовый бетон).
Тяжелые бетоны с плотностью 2100...2500 кг/ куб. м. получают на плотных заполнителях из горных пород (гранит, известняк, диабаз). Облегченный бетон с плотностью 1800...2000 кг/ куб.м. получают на щебне из горных пород с плотностью 1600...1900 кг/куб, м.
Легкие бетоны изготовляют на пористых заполнителях (керамзит, аглопорит, вспученный шлак, пемза,туф).
К особо легким бетонам относятся ячеистые бетоны (газобетон, пенобетон), которые получают вспучиванием вяжущего, тонкомолотой добавки и воды с помощью специальных способов, и крупнопористый бетон на легких заполнителях.
Главной составляющей бетона, во многом определяющей его свойства, является вяжущее вещество, по виду которого различают бетоны цементные, силикатные, гипсовые, шлакощелочные, полимерцементные и специальные.
Цементные бетоны приготовляют на различных цементах
инаиболее широко применяют в строительстве. Среди них основное место занимают бетоны на цементе (портландцемент) и его разновидностях (около 65% от общего объема производства), успешно используют бетоны на шлакопортландцементе (20...25%)
ипуццолановом цементе. К разновидностям цементных бетонов относятся: декоративные бетоны, (на белом и цветных цементах), бетоны для самонапряженных конструкций (на напрягающем цементе), бетоны для специальных целей (на глиноземистом и безусадочном цементах).
Силикатные бетоны готовят на основе извести. Для производства изделий в этом случае применяют автоклавный способ твердения.
Гипсовые бетоны готовят на основе гипса. Гипсовые бетоны применяют для внутренних перегородок, подвесных потолков и элементов отделки зданий. Разновидностью этих бетонов являются гипсоцементные 4 пуццолановые бетоны, обладающие повышенной водостойкостью. Применение 4 объемные блоки санузлов, конструкции малоэтажных домов.
Шлакощелочные бетоны делают на молотых шлаках, затворенных щелочными растворами. Эти бетоны еще только начинают применяться в строительстве.
Полимербетоны изготовляют на различных видах полимерного связующего, основу которого составляют смолы (полиэфирные, эпоксидные, карбамидные) или мономеры (фурфуролацетоновый), отверждаемые в бетоне с помощью специальных добавок. Эти бетоны более пригодны для службы в агрессивных средах и особых условиях воздействия (истирание, кавитация).
изготовляемых на заводах сборного железобетона, так возводимых непосредственно на месте эксплуатации (в гидротехническом, дорожном строительстве).
В зависимости от области применения различают:
4обычный бетон для железобетонных конструкций (фундаментов, колон, балок перекрытий и мостовых конструкций);
4гидротехнический бетон для плотин, шлюзов, облицовки каналов, водопроводно4канализационных сооружений;
4бетон для ограждающих конструкций (легкий); бетон для полов, тротуаров, дорожных и аэродромных покрытий;
4бетоны специального назначения (жароупорный, кислотостойкий, для радиационной защиты).
Общие требования ко всем бетонам и бетонным смесям следующие: до затвердевания бетонные смеси должны легко перемешиваться, транспортироваться, укладываться (обладать подвижностью и удобоукладываемостью), не расслаиваться; бетоны должны иметь определенную скорость твердения в соответствии с заданными сроками распалубки и ввода конструкции в эксплуатацию; расход цемента и стоимость бетона должны быть минимальными.
3.6.3.1 Легкие бетоны
Для приготовления легких бетонов используют различные виды пористых заполнителей: искусственные 4 керамзит, аглопорит, перлит, шлаковую пемзу и естественные 4 туф, пемзу.
Легкие бетоны на пористых заполнителях применяют в ограждающих конструкциях и для снижения собственной массы несущих конструкций. Поэтому для этих бетонов наряду с прочностью очень важное значение имеет плотность бетона.
По плотности различают:
·особо легкие теплоизоляционные бетоны с плотностью в высушенном состоянии менее 500 кг/м3
·легкие бетоны с плотностью 500...1800 кг/м3.
Прочность особо легких бетонов редко бывает более 1,5 МПа, а прочность легкого бетона может изменяться в значительных пределах 4 от 2,5 до ЗО МПа и выше.
Обычно легкие бетоны подразделяются на:
·конструктивно4теплоизоляционные с плотностью 500 41400 кг/м3 и прочностью 2...10 МПа
·конструктивные с плотностью 1400...1800 кг/м3 и прочностью 10...30 МПа.
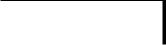
БЕТОНЫ
По структуре различают:
·плотные, или обычные, легкие бетоны, в которых раствор на тяжелом и легком песке полностью заполняет межзерновые пустоты крупного заполнителя,
·поризованные легкие бетоны, в которых не содержится и сохраняются межзерновые пустоты.
В строительстве используют главным образом легкие бетоны с крупностью пористого заполнителя до 20...40 мм, однако применяют и мелкозернистые легкие бетоны.
Легкие бетоны делятся на три вида:
1.Поризованный легкий бетон
2.Крупнопористый легкий бетон
3.Ячеистый бетон
4.Полистиролбетон
Поризованный легкий бетон
Для улучшения теплофизических свойств легкого бетона на пористом заполнителе применяют поризацию растворной части бетона или заменяют ее поризованным цементным камнем, т.е. готовят легкий бетон на крупном пористом заполнителе без песка. К поризованным легким бетонам относят бетоны, содержащие более 800 л/м3 легкого крупного заполнителя, у которых объем воздушных пор составляет 5...25%. Поризацию таких бетонов осуществляют либо предварительно приготовленной пеной, либо за счет введения газообразующих или воздухововлекающих добавок. Пеной поризуют только беспесчаные смеси, воздухововлекающими добавками 4 только смеси с песком, газообразующими добавками 4 смеси с песком и без песка. В зависимости от используемого заполнителя и способа поризации бетоны получают название: керамзитопенобетон, керамзитогазобетон, керамзитобетон с воздухововлекающими добавками.
Прочность поризованного бетона может быть 5...10 МПа, а плотность 4 700...1400 кг/м3. Прочность и плотность бетона зависят от его структуры. Для поризованного легкого бетона рационально применять цемент М400 и выше, керамзит марок: М50, 75, 100, 150, 200, 250. Оптимальный показатель OK = 546 см, оптимальный показатель Ж=30 4 90с. Расход керамзитового щебня или гравия не должен превышать 0,9 м3 на один куб бетона. Расход цемента в керамзитобетоне для неармированных конструкций должен быть не менее 120 кг/м3, для армированных не менее 200 кг/м3.
Крупнопористый легкий бетон
Крупнопористый конструктивно 4 теплоизоляционный бетон 4 это бетон на легких крупнопористых заполнителях (керамзитовый гравий, аглопорит, шлаковая пемза, природные крупнопористые и мелкопористые заполнители). Крупнопористые бетоны на легких заполнителях отличаются высокой жесткостью, поэтому при определении их состава контролируют нерасслаиваемость бетонной смеси.
Ячеистый бетон
Ячеистый бетон 4 это особо легкий бетон с большим количеством (до 85% от общего объема бетона) мелких и средних воздушных ячеек размером до 1... 1,5 мм.
Пористость ячеистым бетонам придается:
1. механическим путем, когда тесто, состоящее из вяжущего и воды, часто с добавкой мелкого песка, смешивают с отдельно приготовленной пеной; при твердении получается пористый
материал, называемый пенобетоном; 2. химическим путем, когда в вяжущее вводят специальные
газообразующие добавки; в результате в тесте вяжущего вещества происходит реакция газообразования, оно вспучивается и становится пористым. Затвердевший материал называют газобетоном.
Ячеистые бетоны по плотности и назначению делят на теплоизоляционные с плотностью З00...600 кг/м3 и прочностью 0,4... 1,2 МПа и конструктивные с плотностью 600...1200 кг/м3 (чаще всего около 800 кг/м3) и прочностью 2,5...15 МПа.
Широко развивается производство изделий из автоклавных ячеистых бетонов, т.е. твердеющих в автоклавах при пропаривании под давлением 0,8...1 МПа. Для автоклавного ячеистого бетона наиболее целесобразно использовать портландцемент совместно с известью 4 кипелкой в отношении 1:1 по массе.
Для приготовления автоклавных ячеистых бетонов применяют известь с содержанием активной оксида кальция не менее 70%, оксида магния не более 5%, высокоэкзотермическую с температурой гашения около 85 °C; тонкость помола должна быть не ниже 3500...4000 см2/г.
Для ячеистых бетонов неавтоклавного твердения применяют цементы не менее М400. В качестве кремнеземнистого компонента рекомендуется применять тонкомолотые кварцевые пески, содержащие не менее 90% кремнезема, не более 5% глины и 0,5% слюды. Песок в зависимости от плотности ячеистого бетона должен иметь удельную поверхность 1200...2000 см2/г.
Для образования ячеистой структуры бетона применяют пенообразователи и газообразователи. В качестве пенообразователей используют несколько видов ПАВ (клееканифольный, смолосапониновый, алюмосульфонатный и ГК). Расход пенообразователя для получения пены составляет соответственно 4 18...20%; 12...16%; 16...20% и 4...6%.
В качестве газообразователя применяют алюминиевую пудру, которую выпускают четырех марок. Для производства газобетона используют пудру марки ПАК43 или ПАК44 с содержанием активного алюминия 4 82% ц тонкостью помола 5000...6000 кв.см. Расход алюминиевой пудры зависит от плотности получаемого газобетона и составляет 0,25 4 0,6 кг/м3.
Пенобетон
Пенобетон изготавливается из цемента, песка, воды и пенообразователя1. Изделия из пенобетона отличают хорошие звуко4 и теплоизоляционные свойства, малый вес. Материал является негорючим и не разрушается от воздействия высокой температуры.
На свойства пенобетона оказывает большое влияние качество пенообразователя. В настоящее время в основном применяются синтетические пенобразователи на основе органических соединений как отечественного, так и импортного производства. Изменяя соотношение составляющих пенобетонной смеси, можно получать пенобетон различной плотности (400 4 1800 кг/м3).
Область применения пенобетона:
Заливка наклонной кровли (до 345 градусов). Общая схема утепления такой кровли предполагает использование двух слоёв монолитного пенобетона, одного, плотностью примерно 2504 300 кг/м3 для теплоизоляции, и второго, плотностью 600 для получения нужного угла наклона кровли и предохранения теплоизоляционного слоя.
Заливка кровли сложной формы или надстройка мансард. Вначале устанавливаются стропила, делается опалубка, для которой можно использовать ЦСП, фанеру либо другие материалы, затем в неё подаётся теплоизоляционный пенобетон плотностью 2004250 кг/м3, после застывания которого, верхняя
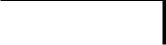
БЕТОНЫ
часть опалубки снимается, а поверхность пенобетона покрывается любым кровельным материалом.
Утепление стен выполняется теплоизолирующим пенобетоном плотностью 2004300 кг/м3 . Такой пенобетон имеет коэффициент теплопроводности 0,05740,065 Вт/м0С и при слое в 300 мм полностью удовлетворяет требованиям СНиП II43479. Несущими при этом могут быть кирпичные стены, бетонный несущий каркас, металлический каркас и т.д.
Изготовление строительных блоков различной плотности.
Тепло4звукоизоляция полов производится пенофибробетоном плотностью 6004800 кг/м3 . Пенобетон поглощает вибрацию и его сочетание с плитами из обычного бетона обеспечивает комплексную звукоизоляцию перекрытий.
Для получения пенобетона в строительстве применяются как стационарное оборудование, так и мобильные установки, легко перевозимые в машине типа "Газель". Причем мобильное оборудование позволяет получать пенобетон в большом диапазоне плотностей (от 200 до 1500 кг/м3) и дает возможность выполнять как заливки монолитного пенобетона, так и использовать его для получения пенобетонных строительных блоков.
Газобетон
Газобетон получают из вяжущего (цемента, извести) кварцевого песка, воды, с добавлением газообразующих веществ (благодаря чему мелкие воздушные поры распределяются равномерно). Именно поэтому строительные элементы из газобетона имеют малый вес и хорошие теплоизоляционные свойства.
Газобетон относится к конструкционно4 теплоизоляционным строительным материалам. Его применение для возведения ограждающих конструкций позволяет значительно уменьшить массу и толщину стен, что не только сокращает сроки и объем строительных работ, но и снижает стоимость строительства в связи с понижением массы здания и экономией на возведении фундамента. Конструкции из газобетона имеют высокие теплофизические показатели по сравнению с блоками из тяжелых бетонов, керамическими и силикатными штучными материалами. Газобетон обладает следующим свойством 4 он способен поглощать влагу из воздуха при повышенной влажности внутри помещения, а при пониженной влажности наоборот отдавать ее. Таким образом, применение газобетона благотворно влияет на обеспечение нормального влажностного режима в помещениях.
Газобетон является негорючим материалом и может быть применен для всех классов противопожарной безопасности. Он не разрушается от воздействия высокой температуры и препятствует распространению огня.
См. также подраздел "Камни (блоки) бетонные" в главе "Стены и фасадные системы"
Пенополистиролбетон
Полистиролбетон является композиционным материалом, и по своему функциональному назначению близок к ячеистым бетонам. Это легкий бетон на цементном вяжущем и вспученном (полистирольном) заполнителе.
Изготовление конструкций и изделий из полистиролбетона может осуществляться как в стационарных условиях, так и в условиях стройплощадки.
Полистиролбетон относится к трудногорючим материалам, имеет группу горючести Г1. Его плотность изменяется от Д150 до Д600 при марке по морозостойкости от F100 и более. Полистиролбетон имеет высокие прочностные характеристики, например, для класса В2,5 (Д5004Д600) предел прочности на растяжение соответствует классу В 12,5 для легких бетонов на пористом заполнителях. Коэффициент теплопроводности
изменяется в пределах от 0,55 (Д150) до 0,145 (Д600) при высокой водонепроницаемости.
Из полистиролбетона производятся следующие изделия:
·утепляющие плиты для фасадов;
·наружные стеновых блоков;
·внутренние перегородочные блоки;
·перегородочные панели;
·звукоизоляционные панели;
·утепляющие плиты для полов и кровель;
·плиты и панели другого назначения.
Широкое применение в строительстве имеет также и монолитный полистиролбетон:
·при утеплении фундаментных плит и фундаментных стен;
·вместо цементной стяжки, в качестве не только выравнивающего, но и тепло4 и звукоизолирующего слоя пола;
·в качестве элемента ограждающей конструкции;
·при устройстве плоских кровель.
См. также подраздел "Камни (блоки) бетонные" в главе "Стены и фасадные системы"
3.6.3.2 Особые виды бетона
Силикатный бетон
Силикатный бетон представляет собой бесцветный бетон автоклавного твердения. Вяжущим в нем является смесь извести с тонкомолотым кремнеземистым материалом. В процессе автоклавной обработки известь вступает с кремнеземистым компонентом в химическую реакцию, в результате которой образуются гидросиликаты кальция, скрепляющие зерна заполнителя в прочный монолит. В зависимости от вида кремнеземистого компонента различают следующие виды вяжущего вещества: известково4кремнеземистые (тонкомолотая известь и песок); известково4шлаковые (совместный помол металлургического или топливного шлака и извести); известково4 зольные (тонкомолотая известь и топливные золы); известково4 белитовые (тонкомолотые продукты низкотемпературного обжига 4 белитового шлама и песка), и известково4аглопоритрвые (известь и отходы производства искусственных пористых заполнителей). Соотношения извести и кремнеземистого компонента составляет от 30:70 до 50:50%. В качестве мелкого заполнителя применяют природные и дробленые пески, удовлетворяющие стандартным требованиям.
Для регулирования свойств вяжущего, бетонной смеси и бетона применяют специальные добавки: гипсовый камень для замедления гидратации извести: триэтаноламин для повышения помолоспособности компонентов вяжущего и пластификации бетонной смеси; кремнийорганические жидкости ГКЖ410 и ГКЖ411 для гидрофобизации и повышения долговечности бетона, суперпластификаторы.,
Прочность силикатного бетона меняется в широких пределах: 5410 МПа в легких силикатных бетонах, 20450 МПа в тяжелых бетонах и 804100 МПА в высокопрочных бетонах. Из силикатного бетона производят плиты перекрытий, колонны, ригели, балки, ограждающие панели и стеновые блоки.
Цементно'полимерный бетон
Цементно4полимерные бетоны 4 это цементные бетоны с добавками различных высокомолекулярных органических соединений в виде водной дисперсии полимеров 4 продуктов эмульсионной полимеризации различных полимеров: винилацетата, винилхлорида, стирола, латексов или водорастворимых коллоидов: поливинилового и фурилового спиртов, эпоксидных водорастворимых смол, полиамидных и
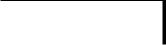
БЕТОНЫ
мочевиноформальдегидных смол. Добавки вводят в бетонную смесь при ее приготовлении. Полимеры и материалы на их основе применяют в виде добавок в бетонную смесь, в качестве вяжущего, для пропитки готовых бетонных и железобетонных изделий, для дисперсного армирования полимерными волокнами, в виде легких заполнителей и в качестве микронаполнителя.
Цементно4полимерные бетоны характеризуются наличием двух активных составляющих: минерального вяжущего и органического вещества. Вяжущее вещество с водой образует цементный камень, склеивающий частицы заполнителя в монолит. Полимер по мере удаления воды из бетона образует на поверхности пор, капилляров, зерен цемента и заполнителя тонкую пленку, которая обладает хорошей адгезией и способствует повышению сцепления между заполнителем и цементным камнем, улучшает монолитность бетона и работу минерального скелета под нагрузкой. В результате цементно4полимерный бетон приобретает особые свойства: повышенную по сравнению с обычным бетоном прочность на растяжение и изгиб, более высокую морозостойкость, хорошие адгезионные свойства, высокую износостойкость, непроницаемость. Наиболее распространенньми добавками полимеров в цементные бетоны являются ПВА, латексы и водорастворимые смолы.
Полимербетоны
Полимербетонами называют бетоны, в которых вяжущими служат различные полимерные смолы, а заполнителями 4 неорганические материалы (песок и щебень). Для экономии смолы и улучшения свойств полимербетонов в них иногда вводят тонкомолотые наполнители. Для ускорения твердения и улучшения свойств применяют отвердители, пластификаторы. Наиболее часто для полимербетонов используют термореактивные смолы: фурановые (ФА), эпоксидные (ЭД45,ЭД46) и полиэфирные (ПН41 и ПН43; МГ Ф49 и ТМГ Ф411). Фурановые смолы обычно получают конденсацией фурфурола и фурфурилового спирта с фенолами и кетонами. В строительстве наибольшее распостранение получил мономер ФА, получаемый при взаимодействии фурфурола и ацетона в щелочной среде. При нормальной температуре это жидкость желтовато4коричневого цвета плотностью 1,082г/куб.см с температурой кипения 160...240 градусов, нерастворимая в воде, но растворимая в эфирах и ацетоне. Мономер ФА отверждают бензосульфокислотами (20...30% массы ФА). Эпоксидные смолы 4 э то полимерные вещества линейного строения, содержащие эпоксигруппу. Для полимербетонов наиболее пригодны жидкие эпоксидные смолы ЭД45, ЭД46. Эпоксидные смолы отверждаются с помощью катализатора ионного типа (10...20% массы смолы). Полиэфирные смолы получают путем поликонденсации двух основных кислот (малеиновой и фталевой) и многоатомных спиртов. В качестве вяжущих для полимербетонов обычно используют ненасыщенные полиэфирные смолы: полиэфирмалеинаты ПН41 и ПН43, полиэфирокрмлаты МГФ49 и ТМГФ411, которые отверждаются при обычной температуре с помощью специальных катализаторов (перекиси бензоила, циклогексанона, метилэтилкатона). Усредненные характеристики полимербетонов: прочность на сжатие 4 20...100МПа; усадка линейная 4 0,2...1,5%; мера ползучести 4 0,3.,.0,5 кв.см/кг; пористость 4 1...2%; стойкость к нагреву 4 100...180 градусов по Цельсию: стойкость 4 к старению 4...6 баллов, к воде 4 6...8 баллов, к щелочам 4 2...10 баллов, к кислотам 4 б... 10 баллов.
3.6.3.3 Особо тяжелый бетон
Особо тяжелые бетоны применяют в специальных сооружениях для защиты от радиоактивных воздействий. К особо тяжелым относят бетоны с плотностью более 2500 кг/ куб. м.
Для особо тяжелых бетонов применяют портландцемент, пуццолановый портландцемент, шлакопортландцемент, глиноземистый цемент, гипсоглино4земистый расширяющийся цемент. В качестве заполнителей в особо тяжелых бетонах
используют материалы с высокой плотностью: магнетит, гематит, барит, металлический скрап.
К заполнителям особо тяжелых бетонов предъявляют следующие дополнительные требования:
·минимальная прочность на сжатие чугунного скрапа 4 200МПа, магнетита 4 200 МПа, лимонита или гематита 4 35 МПа, барита 440 МПа (испытания в цилиндрических образцах диаметром 50 мм, высотой 50 мм);
·содержание полуторных окислов в барите 4 не более 1% массы заполнителей,
·водопоглощение (% по массе) магнетита и барита 142, лимонита и гематита 9410.
3.6.3.4Тяжелый бетон
В строительстве наиболее широко используют обычный тяжелый бетон плотностью 1600 42500 кг/куб. м. на заполнителях из горных пород (граните, известняке, диабазе, щебне). Строительными нормами и правилами, установлены следующие марки тяжелых бетонов 4 М100, 150, 200,300, 400, 500, 600. Существуют различные виды тяжелого бетона:
1.Бетон для сборных железобетонных конструкций
2.Высокопрочный бетон
3.Быстротвердеющий бетон
4.Бетон на мелком песке
5.Бетон для гидротехнических сооружений
6.Бетон для дорожных и аэродромных покрытий
7.Бетон с тонкомолотыми добавками
8.Малощебеночный бетон
9.Литой бетон
10.Бетон с поверхностно 4 активными добавками
Бетон для сборных железобетонных конструкций
Для ускорения твердения бетона при изготовлении сборных железобетонных конструкций применяют тепловую обработку. Рост прочности бетона при тепловой обработке определяется не только активностью, но также минералогическим составом цемента, составом бетона, консистенцией бетонной смеси, режимом тепловой обработки и другими факторами. Для получения требуемой отпускной прочности применяют следующий оптимальный режим тепловой обработки, предварительная выдержка 41...2 ч, подъем температуры 42...3 ч, изотермическая выдержка 4 6...12 ч, остывание 4 3...4 ч.
Оптимальная температура изотермической выдержки 4 80 градусов.
Оптимальный состав бетона следующий: В = 140 л, Ц = 280 кг, Щ = 1415 кг, П = 590 кг.
Высокопрочный бетон
Высокопрочный бетон прочностью 60... 100 МПа получают на основе цемента высоких марок, промытого песка и щебня прочностью не ниже 100 МПа. Высокопрочный бетон приготовляют с низким В/Ц = 0,3... 0,35 и ниже (смеси жесткие или малоподвижные) в бетоносмесителях принудительного действия. Для укладки смесей и формования изделий используют интенсивное уплотнение: вибрирование с пригрузом, двойное вибрирование.
Для приготовления высокопрочного бетона применяют различные способы повышения активности цемента и качества бетонной смеси (домол и виброактивация цемента, виброперемешивание, применение суперпластификаторов) и принимают высокий расход цемента. Большие перспективы в получении высокопрочных бетонов связаны с применением вяжущего низкой водопотребности (ВНВ), которое получают совместным помолом высокомарочного цемента и суперрластификатора С43. При бетонировании массивных
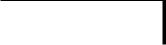
БЕТОНЫ
сооружений целесообразно применить цементы с пониженным содержанием алита (трех кальциевого силиката) и особенно целита (трех кальциевого алюмината), лучше всего белитовые (двух кальциевый силикат). Максимально допустимый расход белитового портландцемента составляет 450 кг/ куб.м. В качестве крупного заполнителя следует применять фракционированный щебень из плотных и прочных горных пород. Предел прочности при сжатии 4 у изверженных не менее ЮОМПа и у осадочных 80 Мпа. Песок для высокопрочных бетонов должен иметь пустотность менее 40%. Марки высокопрочных бетонов М 500 4 1000.
Быстротвердеющий бетон
Получение быстротвердеющего бетона, обладающего относительно высокой прочностью в раннем возрасте (1...3 сут.) при твердении в нормальных условиях, достигается применением быстротвердеющего цемента, а также различными способами ускорения твердения цемента (применение жесткой бетонной смеси с низким В/Ц, использование добавок4ускорителей твердения (хлористый кальций, хлористый водород, глиноземистый цемент), сухое или мокрое домалывание цемента с добавкой гипса (2...5% от массы цемента) или с применением комплексных специальных добавок, активация цементного раствора. Для получения качественного быстротвердеющего бетона используют алюминатный цемент марки М500, домолотого с 3% гипса, жесткой бетонной смеси с В/Ц = 0,35, добавки хлористого кальция в количестве 2% веса цемента и виброперемешивание. По результатам испытаний в первые сутки быстротвердеющий бетон набирает прочность при сжатии 300 4 500 кг/ кв.см.
Бетон на мелком песке
Ввиду широкого распространения в природе мелких песков и отсутствия в некоторых районах песков с удовлетворительным зерновым составом допускаются применять в бетоне мелкие и тонкие пески (с Мкр < 1,5) при условии соответствующего технике 4 экономического обоснования.
Мелкие пески по сравнению со средними и крупными характеризуются повышенной пустотностью и удельной поверхностью и худшим зерновым составом. Вследствие этого они несколько понижают прочность бетона и уменьшают подвижность бетонной смеси, что вызывает увеличение расхода цемента для получения равнопрочных и равноподвижных бетонов. Замена крупного песка мелким в большей степени сказывается на осадке конуса и меньшей 4 на удобоукладываемости бетонной смеси. Вместе с тем мелкий песок меньше раздвигает зерна крупного заполнителя и обладает лучшей водоудерживающей способностью, в результате чего уменьшается оптимальное содержание песка в бетоне и, следовательно, в меньшей мере заметно его влияние на водопотребность бетонной смеси.
Основные параметры: плотность бетонной смеси 4 2350 кг/ куб. м; состав бетона МЗОО 4В/Ц = 0,5, Ц= 370 кг/ куб. м, Щ = 1305 кг, П
= 490 кг, В = 185 л.
Бетон для гидротехнических сооружений
Бетон для гидротехнических сооружений должен обеспечивать длительную службу конструкций, постоянно или периодически омываемых водой. Поэтому в зависимости от условий службы к гидротехническому бетону помимо требований прочности предъявляют также требования по водонепроницаемости и морозостойкости. Выполнение этих дополнительных требований достигается правильным определением состава бетона. Эти требования дифференцированы в зависимости от характера конструкции и условий ее работы.
Гидротехнический бетон делят на следующие разновидности: подводный; постоянно находящийся в воде; расположенный в зоне переменного горизонта воды; надводный,
подвергающийся эпизодическому смыванию водой. Кроме того, различают массивный и немассивный бетон и бетон напорных и безнапорных конструкций. По прочности на сжатие в возрасте 180 суток гидротехнический бетон делят на классы В5, В7, В 10, В 15, В20, В25, ВЗО, В40.
По водонепроницаемости в 1804суточном возрасте на четыре марки: W2, W4, W6, W8. Бетон марки W2 при стандартном испытании не должен пропускать воду при давлении 0,2МПа, а бетон марок W4, W6 и W8 4 при давлении соответственно 0,4; 0,6 и 0,8 МПа.
По морозостойкости гидротехнический бетон делят на пять марок: F50, F100, F150, F200, F300. Максимальное допустимые значения В/Ц = 0,5...0,7. Допускается применение для Гидротехнического бетона портландцемента, пластифицированного и гидрофобного цементов, пуццоланового и шлакового, а в некоторых случаях сульфатостойкого цемента.
Бетоны для дорожных и аэродромных покрытий
В бетонных покрытиях дорог и аэродромов основными расчетными напряжениями являются напряжения от изгиба, так как покрытие работает на изгиб, как плита на упругом основании. Поэтому при расчете состава бетона надо установить такое соотношение между его составляющими, которое обеспечивает требуемую прочность бетона на растяжение при изгибе, а также достаточную прочность на сжатие и морозостойкосить. Проектную прочность дорожного бетона устанавливают в зависимости от назначения бетона: при изгибе 4 М 20, 25, 30, 35, 40, 45, 50, 55; при сжатии 4 М 100, 150, 200, 250, 300, 350, 400, 500.
Марки бетона по морозостойкости назначают в соответствии с климатическими условиями района строительства: F50, F100, F150, F200.
Требования к подвижности бетонной смеси: ОК = 1...3 см; Ж = 2...5с и Ж =10...15с, Чтобы обеспечить достаточную морозостойкость, и, следовательно, надежную защиту и эксплуатацию покрытий длительное время, В/Ц должно быть не более: для сурового климата 4 0,5, умеренного 4 0,53, мягкого 4 0,55. Для оснований бетонных дорог допускается использовать портландцемент не ниже МЗОО, Для бетона однослойных и двухслойных покрытий не ниже М400 с содержанием трех кальциевого алюмината менее 10%. В качестве крупного заполнителя используют щебень из прочных пород 4 изверженных (прочностью не менее 120 МПа) и осадочных пород (прочностью не менее 80 МПа); гравий только после промывки, при этом содержание в них загрязняющих частиц, не должно превышать 1,5 4 2% по массе. Наибольший размер зерен щебня и гравия не менее 20мм, 40мм, 70мм. В качестве ПАВ используют 4 пластификаторы (ССБ) и воздухововлекающие (мылонафт и Абиетат натрия); комплексные добавки 4 СДБ и мылонафт, СДБ и СНВ.
Оптимальный состав бетона: В = 155 л, Ц = 287 кг, Щ = 1340 кг, П = 655 кг.
Бетон с тонкомолотыми добавками
Применение тонкомолотых добавок (наполнителей) рационально в двух случаях:
1.когда по условию прочности можно допустить большее В/Ц, чем требуется по условию долговечности бетона.
2.когда прочность бетона можно обеспечить при меньшем расходе цемента, чем требуется по условию плотности.
Малощебеночной бетон
Малощебеночным называют бетон с пониженным содержанием щебня или гравия. При уменьшении содержания щебня в обычном бетоне повышается водопотребность бетонной смеси (так как возрастает удельная поверхность заполнителя), увеличивается воздухововлечение в бетонную смесь и вследствие этого несколько уменьшаются прочность бетона и модуль
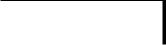
БЕТОНЫ
деформации, возрастают усадка и ползучесть. Соответственно при |
3.6.3.5 Мелкозернистый бетон |
||||
введении щебня в цементно 4песчаный бетон и увеличении его |
|
||||
содержания свойства бетона изменяются в противоположном |
Для изготовления тонкостенных железобетонных |
||||
направлении. Меняя содержание щебня в бетоне, можно |
конструкций применяют мелкозернистый бетон, не содержащий |
||||
регулировать его свойства. |
|
|
щебня. Армируя этот бетон стальными ткаными сетками, получают |
||
|
Малощебеночный бетон используют главным образом |
армоцемент 4 высокопрчный материал для тонкостенных |
|||
тогда, когда для железобетонных конструкций приходится |
конструкций. Мелкозернистый бетон можно также использовать |
||||
применять дорогостоящий привозной щебень. Оптимальная |
для изготовления железобетонных Конструкций в районах, где |
||||
плотность малощебеночного бетона составляет 4 2380 кг/куб, м. |
отсутствуют щебень и гравильно 4 песчаная смесь. Мелкозернистый |
||||
Оптимальный состав бетона на один куб : В = 150л, Ц = 280кг, Щ = |
цементно4песчаный бетон имеет некоторые особенности, |
||||
700кг, П = 1175кг. |
|
|
|
обусловленные его структурой, для которой характерны большая |
|
|
|
|
|
|
однородность и мелкозернистость, высокое содержание |
|
|
Литой бетон |
|
цементного камня, отсутствие жесткого каменного скелета, |
|
|
|
|
|
|
повышенные пористость и удельная поверхность твердой фазы. |
|
Литой бетон готовят при высоком расходе воды, что |
Для мелкозернистого бетона на мелком песке оптимальными |
|||
требует уделять особое внимание Предупреждению расслаивания |
оказываются составы 1:1 ... 1:1,5. Мелкозернистый бетон обладает |
||||
бетонной смеси. Для ее предотвращения осуществляют |
повышенной прочностью при изгибе Кизг = 2...20 МПа, |
||||
мероприятия, способствующие повышению водоудерживающей |
водонепроницаемостью и морозостойкостью. Поэтому его можно |
||||
способности смеси: |
|
|
|
использовать для дорожных покрытий в районах, где нет хорошего |
|
|
|
|
|
|
щебня, для труб и гидротехнических сооружений. |
1. |
используют |
цементы, |
обладающие |
достаточной |
Существует два вида мелкозернистого бетона: |
водоудерживающей способностью; |
|
|
|||
2. применяют суперпластификаторы, воздухововлекающие или |
1 вид 4 мелкозернистый бетон для армоцементных конструкций; |
||||
водоудерживающие добавки; |
|
|
|||
3. ограничивают значения В/Ц, чтобы избежать расслоения |
2 вид 4 мелкозернистый бетон с микронаполнителем (зола, |
||||
цементного теста; |
|
|
|
известняковая мука, молотый песок). |
|
4. увеличивают содержание песка в бетонной смеси, повышая |
|
||||
значения коэффициента раздвижки а. |
|
|
Для приготовления литых бетонов желательно использовать портландцемент и быстротвердеющий цемент. Такие цементы вследствие оптимального гранулометрического состава зерен и высокой точности помола обладают хорошей водоудерживающей способностью при высоких В/Ц. Кроме того быстрое схватывание цементного теста уменьшает возможность его расслаивания, так как Последнее может происходить только до момента затвердевания бетона. В строительстве используют литые бетоны с прочностью R = 20...60 МПа.
Бетон с поверхностно'активными добавками
В современном строительстве широко применяют поверхностно 4 активные добавки (ПАВ), вводимые в состав бетона для улучшения его свойств и экономии цемента ПАВ подразделяются на две группы:
1 группа 4 пластифицирующие добавки пептизирующего действия, способствующие диспергированию коллоидной системы цементного теста и тем самым улучшающие его текучесть, к ним относятся концентраты сульфитно4спиртовой барды (ССБ) и их производные, 2 группа 4 гидрофобизирующие добавки, вызывающие вовлечение
в бетонную смесь мельчайших пузырьков воздуха, что также улучшает подвижность бетонной смеси и, кроме того, повышает морозостойкость бетона и улучшает некоторые другие его свойства, к ним относятся омыленный древесный пек, мылонафт, омыленная абиетиновая смола (абиетат натрия), препарат ГК (пенообразователь на основе гидролизованной крови), микропенообразователь БС, получаемый из растительного сырья. Оптимальное содержание добавки составляет: ССБ 0,15...0,25%, абиената Натрия 0,01...0,25% (от веса цемента).
Эффективность применение добавки зависит от многих факторов: состава бетона, качества цемента и заполнителя, пластичности бетонной смеси.
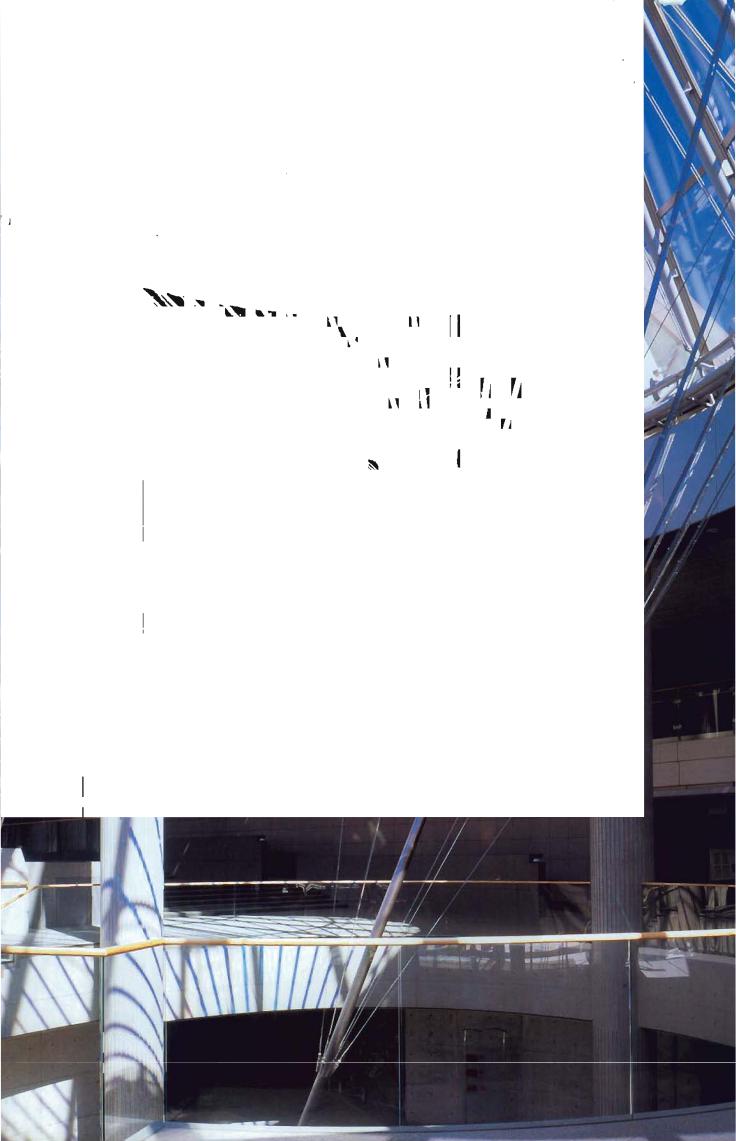